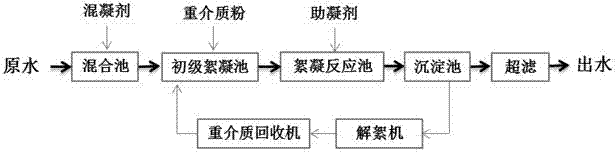
本发明涉及水处理
技术领域:
,尤其适用于污水处理和自来水处理的物化处理领域,具体涉及一种用于水处理的重介质粉的配方、制备方法及使用方法。
背景技术:
:近年来,随着各地水环境污染情况日趋严重,社会大众对水处理技术及其效果的要求也日益提高。无论是新建的污水处理厂或自来水厂,也无论是对现有污水处理厂或自来水厂的提标改造,都需要高效、紧凑型的新技术、新工艺。混凝沉淀是一种水处理领域里广泛应用的工艺方法。该工艺采用在待处理的原水中投加具有凝聚能力的药剂(混凝剂/助凝剂)的方法,通过吸附架桥等机理作用使水中的细微悬浮粒子、胶体粒子等杂质或污染物形成絮团,并沉淀,从而达到净水效果。专利号为201180030555.5的发明专利提出通过实施天然絮凝剂的压载絮凝来处理水的方法,选择利用粒径60至300微米的微砂参与压载絮凝,以提高絮凝效率。由于微砂的密度约为2.5g/cm3,尽管比水的密度大,但其密度还不足够大,而且在实际生产过程中细小的含砂絮体常常还没有能完全沉淀即已随水流漂到下道工序,俗称“跑砂”,造成后道工序中管道的堵塞、水泵叶轮的损坏、超滤膜丝的损坏等不好影响。重介质混凝沉淀工艺是近些年刚刚发展起来、在上述传统的水处理工艺基础上开发的一种极速混凝沉淀技术(专利号:201620549866.2,201520658253.8等),该技术在向水中投加常规凝聚剂和/或絮凝剂的同时,投加微米级的惰性高密度软磁性重介质微粒作为絮凝核,在较优水力条件下快速形成高浓度、大密度的复合絮体,该复合絮体可以在极短时间内完成沉淀过程,并使水体迅速得到净化。为降低水处理系统运行成本并减少重介质粉对水处理后道工序的影响,重介质混凝沉淀工艺通过重介质粉絮体解絮机(专利号201520658318.9,201520561702.7)对絮体进行解絮后,再通过重介质粉分离机(专利号201520059633.x)利用重介质粉的软磁性对重介质粉进行回收,实现重介质粉的循环利用。上述微米级的惰性高密度软磁性重介质微粒,简称重介质或重介质粉。与传统的水处理混凝沉淀工艺以及微砂混凝沉淀工艺相比,重介质混凝沉淀工艺可以减少20%至50%的沉淀时间和沉淀池土地占用面积,进一步地,在同等水处理规模下也大幅减少了建设成本,或者在同等土地占用面积下也大幅提高了水处理厂的处理能力。因此,市场上急需适用于自来水和污水处理、比微砂密度更大且更易于回收利用、对后续工序影响更小的新的重介质粉产品;同时这种产品能够降低投资、运行成本,提高水处理效率。技术实现要素:本发明的目的在于针对现有技术的不足,提供一种适用于自来水和污水处理、比微砂密度更大且更易于回收利用、对后续工序影响更小的用于水处理的重介质粉的配方、制备方法及使用方法。为解决上述技术问题,本发明采用的技术方案为:一种用于水处理的重介质粉的配方,所述重介质粉中粒径范围为200目-300目占重介质粉总体积的75%以上,其创新点在于:包括主要物质和配料:所述主要物质为fe3o4,所述fe3o4占总质量的85%-99.5%;所述配料包括mno、sio2、zno、tio2、cuo、al2o3、cao、mgo、bi2o3中的一种或多种,所述配料中的每种成分占总质量的0.01%-8%。本发明的还有一个目的是提供一种用于水处理的重介质粉的制备方法,其创新点在于:具体包括以下步骤:(1)称取原料:按配方比例称取主要物质fe3o4;(2)研磨:将称取好的主要原料放入研磨设备中,进行混合和研磨;获得粒径<200目的初级粉末;(3)一次磁选:将研磨后符合初步粒径要求的粉末送入磁选机进行一次磁选,去除其中的非磁性物质;(4)烘干:对去除非磁性物质后的粉末进行脱水和烘干,去除粉末中的水分;(5)焙烧:将烘干后的干燥粉末,与mno、zno、al2o3、cao、mgo、bi2o3、sio2、tio2、cuo中的一种或多种按照配方中的比例一起送入回转焙烧炉中,边混合边焙烧;(6)筛分:对焙烧完毕后的半成品逐渐降温到常温后,进行筛分,筛分出符合粒径要求300目-200目的半成品,将粒径大于200目的半成品重新进行步骤(2)的研磨;将小于300目的半成品,进行造粒处理后,重新进行步骤(2)的研磨;(7)二次磁选:对经筛分后符合粒径要求的半成品二次磁选,再次去除非磁性物质,产出重介质粉的成品;所述重介质粉中的磁性物质含量>90%,粒径范围为200目-300目占重介质粉总体积的75%以上,真密度为3.5-5.5g/cm3。进一步的,所述步骤(2)中的研磨工序采用球磨机或气流磨机;选用球磨机时,选用钢球干磨、陶瓷球干磨或使用蒸馏水或去离子水作为弥散剂进行湿磨中的一种。进一步的,所述步骤(4)中的烘干工序,烘干温度为90-100℃,烘干时间为1-3h。进一步的,所述步骤(5)中的焙烧工序,焙烧时将氧气浓度设置为0.0%-4.5%,温升时间为1-3h,焙烧温度为600℃-850℃,焙烧时间为3-4h。进一步的,所述步骤(6)中的降温至常温所用时间为1-3h,降温时的氧气浓度设置为焙烧时的氧气浓度,进行气氛保护;所述步骤(6)中筛分工序选用双层筛分机,对于超出粒径要求300目-200目范围的颗粒进行分离。进一步的,所述步骤(6)中的造粒工艺采用喷雾造粒,造粒时,将浆料温度设置为40℃-50℃,加入聚乙烯醇(pva)或甲基纤维素(cmc)作为黏合剂,形成直径在50目-200目的颗粒。本发明还有一个目的是提供一种用于水处理的重介质粉的使用方法,其创新点在于:包括以下步骤:所述待处理的原水需依次流经混合池、初级絮凝池、絮凝反应池、沉淀池和超滤膜池后出水;a.将待处理的原水通过泵入或重力流进入混合池中,在混合池中加入混凝剂;开启搅拌机进行搅拌,搅拌速率为200-350s-1,搅拌时间为2-5min;使得混凝剂与待处理原水充分混合;b.添加有混凝剂的原水进入初级絮凝池,在初级絮凝池中加入重介质粉;开启搅拌机进行搅拌,搅拌速率为150-300s-1,搅拌时间为2-6min;c.添加混凝剂和重介质粉的水进入絮凝反应池,在絮凝反应池中加入助凝剂,开启搅拌机进行搅拌,搅拌速率为40-150s-1,搅拌时间为2-6min;使得原水中的污泥杂质逐步凝聚成絮体;d.絮凝反应池中含有絮体的水进入沉淀池中进行沉淀;e.沉淀池上层的清水进入超滤膜池,进行超滤膜过滤处理,再进一步进行消毒处理,形成饮用自来水出厂;f.将沉淀池底部的絮体沉淀物泵入解絮机,使用解絮机将污泥絮体打碎,使得污泥杂质与重介质粉絮核分离,随后,将解絮后的污泥、重介质粉、水等物质送入重介质回收机对其中的重介质粉进行回收,回收后的重介质粉再次投入到初级絮凝池中继续参与絮凝反应,实现重介质粉的循环利用。进一步的,所述步骤f中解絮机的电机转速为900-3000r/min;所述重介质回收机的滚筒表面的磁感应强度即磁通量>150mt。进一步的,所述步骤a中混凝剂的添加量为10-20mg/l;所述步骤b中重介质粉的添加量为8-12mg/l;所述步骤c中助凝剂的添加量为0.1-0.2mg/l。本发明的有益效果如下:1.本发明的用于水处理的重介质粉的制备方法所生产的重介质粉适用于自来水和污水处理、比微砂密度更大且更易于回收利用、对后续工序影响更小,同时这种产品能够降低投资成本,提高饮用水处理效率。2.本发明的用于水处理的重介质粉的制备方法所生产的重介质粉中磁性物含量>90%、成品密度大,其为絮核形成的絮体比微砂为核形成的絮体更容易沉淀,磁性含量更高,比微砂更容易回收并循环利用。3.本发明的用于水处理的重介质粉的制备方法中,在焙烧阶段加入了mno、zno、al2o3、cao、mgo、bi2o3、sio2、tio2、cuo中的一种或多种,既可以有效保证重介质粉的温度性能特性,使得重介质粉在一年四季不同环境下经由重介质回收机的回收效率高;同时还使得重介质粉微粒表面充分钝化,避免极少量的悬浮重介质粉絮体在随水流流失进入后续超滤工艺阶段,对超滤膜表面形成伤害,有效延缓了超滤膜的使用寿命。4.本发明的用于水处理的重介质粉的使用方法中,在初级絮凝池中加入适量的重介质粉,经搅拌均匀后,重介质粉随着水流流入絮凝反应池,在初级絮凝池和絮凝反应池中,重介质粉作为絮核逐步参与絮凝反应,加快了絮凝反应速度,缩短了絮体形成时间,提高了絮体的质量密度,以至于絮体进入沉淀池后也加快了絮体沉降速度,提高了处理效果。5.本发明的用于水处理的重介质粉的使用方法中,使用解絮机将来自沉淀池的污泥絮团打碎,使得污泥杂质与重介质絮核分离,随后立即进入重介质回收机对重介质粉进行回收,回收率达到98%以上,再将回收后的重介质粉重新加入到初级絮凝池中,实现重介质粉的重复循环利用。附图说明图1为本发明的一种用于水处理的重介质粉的制备方法的工艺流程图。图2为本发明的一种用于水处理的重介质粉的使用方法的工艺流程图。具体实施方式以下由特定的具体实施例说明本发明的实施方式,熟悉此技术的人士可由本说明书所揭露的内容轻易地了解本发明的其他优点及功效。一种用于水处理的重介质粉的配方,重介质中粒径范围为200目-300目占重介质粉总体积的75%以上,配方包括主要物质和配料:所述主要物质为fe3o4,fe3o4占总质量的85%-99.5%;配料包括mno、sio2、zno、tio2、cuo、al2o3、cao、mgo、bi2o3中的一种或多种,配料中的每种成分占总质量的0.01%-8%。如图1所示,一种用于水处理的重介质粉的制备方法,具体包括以下步骤:(1)称取原料:按配方比例称取具有软磁性的主要物质fe3o4;(2)研磨:将称取好的主要物质放入研磨设备中,进行混合和研磨;获得粒径<200目的初级粉末;研磨工序采用滚筒球磨机或气流磨机;选用滚筒球磨机时,可以使用钢球干磨、陶瓷球干磨或使用蒸馏水或去离子水作为弥散剂进行湿磨中的一种。钢球湿磨时,粉料与钢球、水的级配比例为m(料):m(钢球):m(水)=1:(2~3.2):(0.7~0.9)。(3)一次磁选:将研磨后符合初步粒径要求的粉末送入磁选机进行一次磁选,去除其中的非磁性物质;(4)烘干:对去除非磁性物质后的粉末进行脱水和烘干,去除粉末中的水分;烘干工序,烘干温度为90-100℃,烘干时间为1-3h。(5)焙烧:将烘干后的干燥粉末,与mno、zno、al2o3、cao、mgo、bi2o3、sio2、tio2、cuo中的一种或多种按照配方中的比例一起送入回转焙烧炉中,边混合边焙烧;焙烧工序,焙烧时将氧气浓度设置为0.0%-4.5%,温升时间为1-3h,焙烧温度为600℃-850℃,焙烧时间为3-4h。本发明的用于水处理的重介质粉的制备方法中,在焙烧阶段,原料中的少量可能对水质产生二次污染的挥发性的杂质得以去除,同时,在此阶段,加入了mno、zno、al2o3、cao、mgo、bi2o3、sio2、tio2、cuo中的一种或多种配料,其助熔作用,或使得原料、配料中不同的金属氧化物之间发生的固相反应,既可以有效保证重介质粉的温度性能特性,使得重介质粉在一年四季不同温度环境下经由重介质回收机的回收效率高;同时还使得重介质粉微粒表面充分钝化,避免极少量的悬浮重介质粉絮体在随水流流失进入后续超滤工艺阶段,对超滤膜表面形成伤害,有效延缓了超滤膜的使用寿命。(6)筛分:对焙烧完毕后的半成品逐渐降温到常温后,进行筛分,筛分出符合粒径范围要求为300目-200目的半成品。同时,将粒径大于200目的半成品重新进行步骤(2)的研磨;将小于300目的半成品,进行造粒处理后,重新进行步骤(2)的研磨;其中,降温至常温所用时间为1-3h,降温时的氧气浓度设置为焙烧时的氧气浓度,进行气氛保护;其中,筛分工序选用双层筛分机,对于超出粒径要求200目-300目的颗粒进行分离,并使得粒径分布为200目-300目大于75%。造粒处理采用喷雾造粒工艺,造粒时,将浆料温度设置为40℃-50℃,加入聚乙烯醇(pva)或甲基纤维素(cmc)等粘合剂,形成直径在50目-200目的颗粒。(7)二次磁选:对经筛分后符合粒径要求的半成品二次磁选,再次去除非磁性物质,产出重介质粉的成品;所述重介质粉成品中的磁性物质含量>90%,粒径为200目-300目占重介质粉总体积的75%以上,真密度为3.5-5.5g/cm3。本发明的用于水处理的重介质粉的制备方法所生产的重介质粉中磁性物含量>90%、成品密度大,其为絮核形成的絮体比砂更容易沉淀,磁性含量更高,比砂更容易回收并循环利用。如图2所示,一种用于水处理的重介质粉的使用方法,包括以下步骤:待处理的原水需依次流经混合池、初级絮凝池、絮凝反应池、沉淀池和超滤膜池后出水;a.将待处理的原水泵入或经重力流流入混合池中,在混合池中加入混凝剂;混凝剂的添加量为10-20mg/l;开启搅拌机进行搅拌,搅拌速率为200-350s-1,搅拌时间为2-5min;使得混凝剂与待处理原水充分混合;b.添加有混凝剂的原水自流进入初级絮凝池,在初级絮凝池中加入重介质粉;重介质粉的添加量为50-200mg/l;开启搅拌机进行搅拌,搅拌速率为150-300s-1,搅拌时间为2-6min;c.添加有混凝剂和重介质粉的水自流进入絮凝反应池,在絮凝反应池中加入助凝剂,助凝剂的添加量为0.1-0.2mg/l;开启搅拌机进行搅拌,搅拌速率为40-150s-1,搅拌时间为2-6min;使得原水中的细微悬浮粒子、胶体粒子等污泥杂质逐步凝聚成絮体;d.絮凝反应池中含有絮体的水自流进入沉淀池中进行沉淀;e.沉淀池上层的清水自流进入超滤膜池,进行超滤膜过滤处理,再进一步进行消毒处理,形成饮用自来水出厂;f.将沉淀池底部的絮体沉淀物泵入解絮机,使用解絮机将絮体打碎,使得污泥杂质与重介质絮核分离,随后,解絮后的物质进入重介质回收机对重介质粉进行回收,回收后的重介质粉投入到初级絮凝池中继续参与絮凝反应,实现重介质粉的循环利用。其中,解絮机的电机转速为900-3000r/min;所述重介质回收机的滚筒表面的磁感应强度(磁通量)>150mt。本发明的用于水处理的重介质粉的使用方法中,在初级絮凝池中加入适量的重介质粉,经搅拌均匀后,重介质粉随着水流流入絮凝反应池,在初级絮凝池和絮凝反应池中,重介质粉作为絮核逐步参与絮凝反应,加快了絮凝反应速度,缩短了絮体形成时间,提高了絮体的质量密度,以至于絮体进入沉淀池后也加快了絮体沉降速度,提高了处理效果。本发明的用于水处理的重介质粉的使用方法中,使用解絮机将来自沉淀池的污泥絮团打碎,使得污泥杂质与重介质絮核分离,随后立即进入重介质回收机对重介质粉进行回收,实现了重介质粉的回收利用,回收率达到98%以上,再将重介质粉加入初级絮凝池中,实现重介质粉的重复循环利用。本发明的用于水处理的重介质粉的制备方法所生产的重介质粉适用于自来水和污水处理、比微砂密度更大且更易于回收利用、对后续工序影响更小,同时这种产品能够降低投资成本,提高饮用水处理效率。选取三份等量长江下游某段江水作为待处理的原水,其浊度为55~60ntu、cod为3~5mg/l,依次流经混合池、初级絮凝池、絮凝反应池、沉淀池后,经超滤膜过滤后出水;实施例1在混合池中加入10mg/l混凝剂,在初级絮凝池中加入100mg/l的重介质粉,在絮凝反应池中加入0.1mg/l助凝剂,混合池、初级絮凝池、絮凝反应池中的搅拌机分别按一定的速度进行搅拌,设计g值分别为350s-1、300s-1、150s-1,设计搅拌时间分别为2min、2min、2min,使加入待处理水的混凝剂和助凝剂与水充分搅拌混合,这样,在反应池中,原水中的污泥、胶体杂质等污染物在初级絮凝池和絮凝反应池中逐步凝聚形成絮体后,在沉淀池实现絮体沉淀,沉淀池停留时间为10min,设计上向流流速20m/h,取沉淀池出水、超滤出水进行分析。平行试验3次。实施例2在混合池中加入10mg/l混凝剂,在初级絮凝池中加入100mg/l、200目-300目(75%以上)粒径的微砂,在絮凝反应池中加入0.1mg/l助凝剂,混合池、初级絮凝池、絮凝反应池中的搅拌机分别按一定的速度进行搅拌,设计g值分别为350s-1、300s-1、150s-1,设计搅拌时间分别为2min、2min、2min,使加入待处理水的混凝剂和助凝剂与水充分搅拌混合,这样,在反应池中,原水中的污泥杂质等污染物在初级絮凝池和絮凝反应池中逐步凝聚形成絮体后,在沉淀池实现絮体沉淀,沉淀池停留时间均为15min,设计上向流流速20m/h,取沉淀池出水、超滤出水进行分析。平行试验3次。实施例3在混合池中加入10mg/l混凝剂,在初级絮凝池中不加入重介质微粒或微砂,在絮凝反应池中加入0.1mg/l助凝剂,混合池、初级絮凝池、絮凝反应池中的搅拌机分别按一定的速度进行搅拌,设计g值分别为350s-1、300s-1、150s-1,设计搅拌时间分别为2min、2min、2min,使加入待处理水的混凝剂和助凝剂与水充分搅拌混合,这样,在反应池中,原水中的污泥杂质等污染物在初级絮凝池和絮凝反应池中逐步凝聚形成絮体后,在沉淀池实现絮体沉淀,沉淀池停留时间均为90min,设计上向流流速20m/h,取沉淀池出水、超滤出水进行分析。平行试验3次。对比实施例1、实施例2和实施例3,本发明的用于水处理重介质粉使用方法用于水处理过程中,对水体中浊度和cod的影响如下表所示:性能指标沉淀出水浊度(ntu)沉淀出水cod(mg/l)超滤出水浊度(ntu)实施例1-重介质1.0-1.52.0-2.20.02-0.04实施例2-微砂3.9-4.82.3-2.50.03-0.07实施例3-传统絮凝19.5-21.42.4-2.90.06-0.15对比上表可知,实施例1、实施例2和实施例3相对于微砂絮凝和传统混凝沉淀,采用本发明中提供重介质微粒进行的重介质混凝沉淀用于水处理时,具有更快捷、更好的水处理效果、对后续工序影响更小,将能有效提高饮用水处理效率。本发明所提供的一种用于水处理的重介质粉,当应用于自来水处理时,必须通过对本配方的恰当把控,使重介质粉在实际应用时不存在对人体有害的重金属离子在水中渗析,或者重介质粉在水中重金属离子的渗析程度满足于《生活饮用水卫生标准》gb5749-2006的要求。上述实施例只是本发明的较佳实施例,并不是对本发明技术方案的限制,只要是不经过创造性劳动即可在上述实施例的基础上实现的技术方案,均应视为落入本发明专利的权利保护范围内。当前第1页12