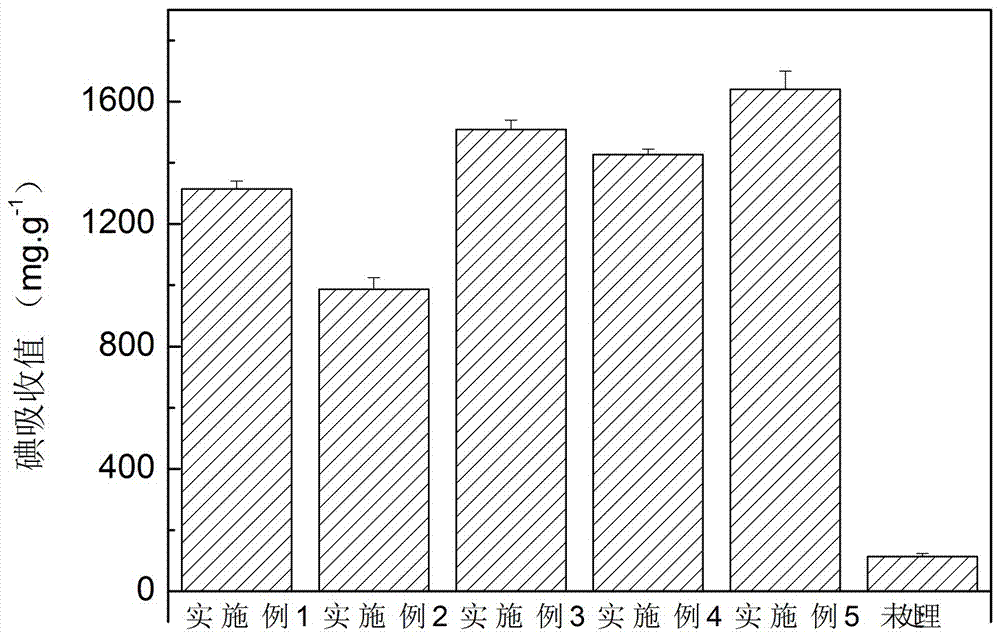
本发明属于新型环境材料及其应用
技术领域:
,主要涉及植物基生物炭材料的纯化,降低植物基生物炭灰分含量的方法,提高植物基生物炭材料的吸附能力。
背景技术:
:生物炭是有机物在缺氧或限氧条件下,高温热裂解形成的稳定芳香性物质。生物炭作为一种新型碳素材料,在气候变化、水体净化、重金属吸附和土壤改良方面为全球热点问题提供解决方案。不同于活性炭材料主要依靠巨大比表面积产生的物理性吸附,生物炭表面广泛分布的含氧官能团,能够与污染物产生新的化学键,从而产生更为稳定的化学吸附作用。因此,作为一种新型高效吸附剂,生物炭材料在重金属和有机污染物的去除方面发挥着重要作用。一般来说,生物炭的制备原料来源主要分为植物基和固体废物基2大类,即以植物的有机残体为制备来源的称之为植物基生物炭,以有机固体废物为制备来源的称之为固体废物基生物炭。然而,不论是植物基生物炭还是固体废物基生物炭,在制备过程中,除了生物炭产品之外,还可以产生无机盐、焦油以及其他气体产物,这些副产物连同制备原料携带的矿物成分,作为灰分留存在生物炭表面和空隙结构中,灰分一方面能够掩蔽生物炭表面功能官能团的作用,另一方面由于这些物质化学性质比较活跃,可以影响生物炭的吸附效率。因此,脱灰处理成为提高生物炭材料吸附性能的关键。目前,脱灰处理主要有前期脱灰、中期脱灰和后期脱灰3种工艺。相比较而言,后期脱灰成本最低、污染最少,成为最常采用的脱灰工艺。中国专利申请号200810049457.6采用漂洗工艺,在漂洗液中添加聚丙烯酰胺或聚氯化铝絮凝剂,将灰分含量控制在1.5%以下。专利中国申请号201210455610.1采用浓硫酸酸洗工艺,产品灰分小于0.5%。上述2个专利工艺虽然能够较好脱灰,但产品灰分依然较高。中国专利申请号201110386303.8采用水热后处理工艺,经过水热碱洗、水热酸洗、热水洗后,灰分虽然能够控制在0.1%以下,但工艺需要加温加压,工艺设备昂贵,投资成本大。为了提高植物基生物炭材料的吸附性能,最大程度降低灰分含量,本发明在常温常压条件下,采用多段酸洗后处理工艺对植物基生物炭进行脱灰处理,产品灰分含量降低至0.1%以下。该脱灰工艺操作简单,成本低廉,脱灰效果好。技术实现要素:本发明为了降低植物基生物炭灰分含量,提高生物炭的吸附性能,发明了一种多段酸洗后处理工艺,对植物基生物炭进行彻底脱灰。本发明是通过以下技术方案实现的,包括如下步骤:常温常压条件下,在振荡反应器中,将植物基生物炭预先在碱性溶液中浸泡6小时,洗涤至中性后,进入第一阶段盐酸处理,重复3次,进入后加入第二阶段磷酸处理,重复3次,过滤后进入第三阶段氢氟酸处理,重复3次,过滤洗涤干燥后储存。多阶段酸洗工艺中植物基生物炭浓度为1-25%(w/v),优选为5-20%(w/v),更优选为10%(w/v),每阶段处理时间为0.5-5小时,优选为1-4小时,更优选为3小时。振荡反应器振荡频率为100-300rpm,优选为150-250rpm,更优选为200rpm。上述工艺中碱性溶液为氢氧化钠、氢氧化钾、氢氧化钙、碳酸钠、碳酸氢钠、氨水中的一种或这些物质的混合物,碱液的使用浓度为0.01-2mol.l-1之间,优选为0.5-1.5mol.l-1之间,更优选为1mol.l-1。工艺中第一段酸洗中盐酸的使用浓度在0.1-5mol.l-1之间,优选为0.5-2mol.l-1之间,更优选为1mol.l-1。工艺中第二段酸洗中磷酸的使用浓度在1-20%之间,优选为5-15%之间,更优选为10%。工艺中第三段酸洗中氢氟酸的使用浓度在0.1-40%之间,优选为1-20%之间,更优选为20%。上述酸洗后处理的植物基生物炭包括以农作物秸秆、果实、枝叶、树木或其他植物类有机部分,经过限氧或无氧条件下热裂解后产物。制备的植物基生物炭过50目筛,灰分含量为15%-35%之间。上述工艺中使用的振荡反应器内衬材料为耐酸碱腐蚀的聚四氟乙烯材料。上述工艺中的一种具体方案如下:植物基生物炭用碱液在浸泡6小时,过滤洗涤后,常温常压下,在振荡反应器中,振动频率200rpm条件下,将洗涤后的生物炭材料置入振荡反应器中,加入1mol.l-1的盐酸,生物炭的浓度为10%(w/v),振荡3小时,重复3次,固液分离。然后在振荡反应器中添加10%的磷酸,生物炭的浓度为10%(w/v),振荡3小时,重复3次,固液分离。在振荡反应器中添加20%的氢氟酸,生物炭的浓度为10%(w/v),振荡3小时,重复3次,过滤后用去离子水洗涤至中性。在120℃烘箱中烘至恒重后,包装后置于干燥器中备用。工艺处理中所用的酸碱液体可以重复使用。本发明的原理是碱液与生物炭材料中的硅酸盐和硅铝酸盐无机盐分反应,生成可溶性的硅酸钠或酸溶性的硅铝酸钠。生物炭材料中的碳酸盐类、金属氧化物以及难溶性的硅酸盐类物质在经过盐酸、磷酸和氢氟酸作用下,逐渐彻底溶解进入液相,再通过过滤洗涤后,与生物炭中的芳香性固态物质分离,从而得到超低灰分含量的植物基生物炭材料。通过本技术工艺处理的植物基生物炭,在经过第一段盐酸处理后,灰分含量可降低至10%左右,经过第二段磷酸处理,灰分可降至1%左右,经过第三段氢氟酸处理后,其中的灰分含量可以降低至0.1%以下。本发明成本低廉,操作简便,对设备要求低,制备的生物炭材料灰分超低,可以用于制备超低灰分植物基生物炭,提高植物基生物炭的吸附性能。附图说明图1是多段酸洗后处理工艺制备超低灰分植物基生物炭流程示意图。图2是实施例与未进行脱灰处理的生物炭最大碘吸附值比较图。具体实施方式下面结合具体实施方式对本发明作进一步描述。本发明工艺中典型流程如下:植物基生物炭→碱液浸泡→盐酸酸洗→磷酸酸洗→氢氟酸酸洗→固液分离→干燥→储藏实施例1植物基生物炭用碱液在浸泡6小时,过滤洗涤后,常温常压下,在振荡反应器中,振动频率200rpm条件下,将洗涤后的生物炭材料置入振荡反应器中,加入1mol.l-1的盐酸,生物炭的浓度为10%(w/v),振荡3小时,重复3次,固液分离。然后在振荡反应器中添加10%的磷酸,生物炭的浓度为10%(w/v),振荡3小时,重复3次,固液分离。在振荡反应器中添加20%的氢氟酸,生物炭的浓度为10%(w/v),振荡3小时,重复3次,过滤后用去离子水洗涤至中性。在120℃烘箱中烘至恒重后,包装后置于干燥器中备用。实施例2植物基生物炭用碱液在浸泡6小时,过滤洗涤后,常温常压下,在振荡反应器中,振动频率100rpm条件下,将洗涤后的生物炭材料置入振荡反应器中,加入0.5mol.l-1的盐酸,生物炭的浓度为20%(w/v),振荡3小时,重复3次,固液分离。然后在振荡反应器中添加1%的磷酸,生物炭的浓度为20%(w/v),振荡3小时,重复3次,固液分离。在振荡反应器中添加5%的氢氟酸,生物炭的浓度为20%(w/v),振荡3小时,重复3次,过滤后用去离子水洗涤至中性。在120℃烘箱中烘至恒重后,包装后置于干燥器中备用。实施例3植物基生物炭用碱液在浸泡6小时,过滤洗涤后,常温常压下,在振荡反应器中,振动频率300rpm条件下,将洗涤后的生物炭材料置入振荡反应器中,加入1mol.l-1的盐酸,生物炭的浓度为5%(w/v),振荡2小时,重复3次,固液分离。然后在振荡反应器中添加10%的磷酸,生物炭的浓度为5%(w/v),振荡2小时,重复3次,固液分离。在振荡反应器中添加20%的氢氟酸,生物炭的浓度为5%(w/v),振荡2小时,重复3次,过滤后用去离子水洗涤至中性。在120℃烘箱中烘至恒重后,包装后置于干燥器中备用。实施例4植物基生物炭用碱液在浸泡6小时,过滤洗涤后,常温常压下,在振荡反应器中,振动频率300rpm条件下,将洗涤后的生物炭材料置入振荡反应器中,加入2mol.l-1的盐酸,生物炭的浓度为5%(w/v),振荡4小时,重复3次,固液分离。然后在振荡反应器中添加15%的磷酸,生物炭的浓度为5%(w/v),振荡4小时,重复3次,固液分离。在振荡反应器中添加30%的氢氟酸,生物炭的浓度为5%(w/v),振荡4小时,重复3次,过滤后用去离子水洗涤至中性。在120℃烘箱中烘至恒重后,包装后置于干燥器中备用。实施例5植物基生物炭用碱液在浸泡6小时,过滤洗涤后,常温常压下,在振荡反应器中,振动频率300rpm条件下,将洗涤后的生物炭材料置入振荡反应器中,加入2mol.l-1的盐酸,生物炭的浓度为10%(w/v),振荡1小时,重复3次,固液分离。然后在振荡反应器中添加20%的磷酸,生物炭的浓度为10%(w/v),振荡1小时,重复3次,固液分离。在振荡反应器中添加40%的氢氟酸,生物炭的浓度为10%(w/v),振荡1小时,重复3次,过滤后用去离子水洗涤至中性。在120℃烘箱中烘至恒重后,包装后置于干燥器中备用。表1实施例与未进行脱灰处理的生物炭中灰分的检测结果处理实施例1实施例2实施例3实施例4实施例5未处理灰分(%)0.08±0.0010.23±0.0020.09±0.0030.07±0.0020.06±0.00224.15±0.03从表1结果可以观察到,采用多段酸洗后处理工艺使得植物基生物炭的灰分含量显著降低,不同实施例之间灰分含量相差不大,通过提高振荡器振动频率和提高三种酸的使用浓度处理获得的生物炭灰分含量最低,脱灰效果最好。在考量生产成本前提下,实施例1的生产工艺为最优选。图2为采用实施例1-5和未进行脱灰处理的生物炭最大碘吸附值比较图,可以看出采用本发明脱灰工艺后,可以有效提高植物基生物炭的吸附性能。当前第1页12