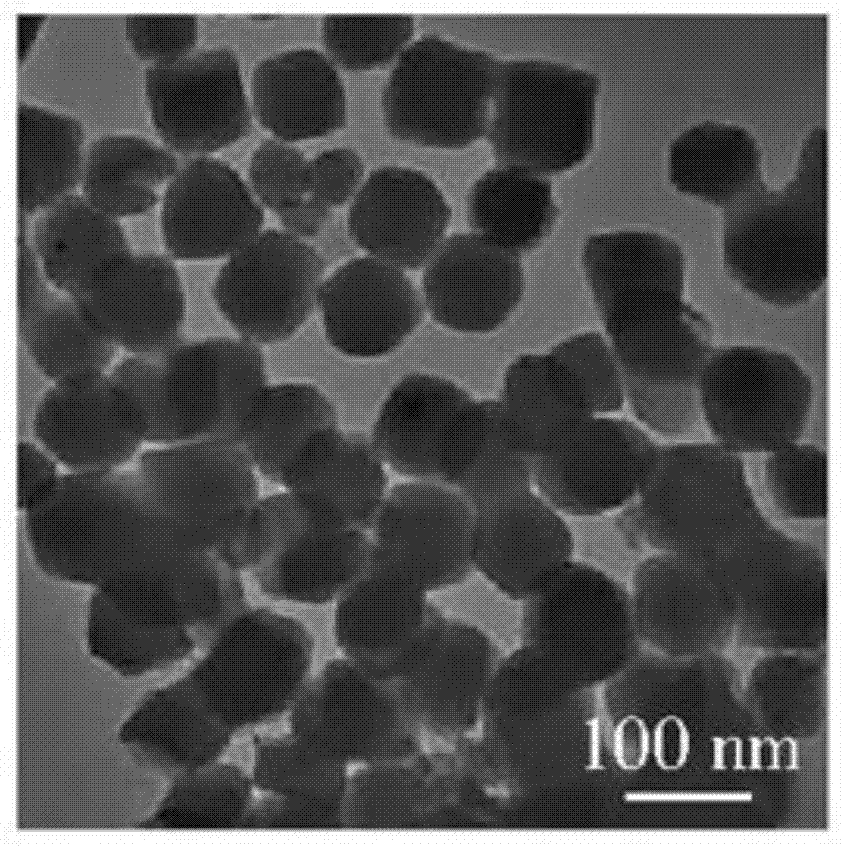
本发明属于医药化学
技术领域:
,具体涉及一种治疗运动障碍用药物中间体的制备方法。
背景技术:
帕金森病是一种慢性、渐进性、运动功能减退的神经变性疾病,其特征在于受损的自主运动。帕金森病至少作为中脑黑质中的多巴胺-生产神经元死亡的结果。多巴胺是神经递质或化学信使,将信号传送至大脑控制运动开始和协调的部位。大脑中多巴胺的丢失与多种原发症状相关,包括,手、手臂、腿、颚和脸的颤动;四肢和躯干的僵化或强直;运动徐缓或运动缓慢;运动障碍;和姿势不稳定或受损的平衡和协调。多巴胺前体l-dopa(l-3,4-二羟基苯丙氨酸;左旋多巴)的给药作为最有效的且最常用的帕金森病治疗,因为其比多巴胺激动剂更有效地逆转了与帕金森病相关的运动缺陷。不幸地,l-dopa可能引起使人虚弱的副作用,包括严重的恶心、呕吐和精神病。此外,随着使用时间的延长,患者常常经受其他副作用,如许多患者中的运动障碍。艾托拉嗪作为5-ht1a/5-ht1b受体激动剂,具有预防和治疗左旋多巴(l-dopa)诱发的迟发性运动障碍(lid)、注意力不足过动症等功效;另外艾托拉嗪也是s-15535(施维雅公司研发代码)药物和lecozotan药物的前体。5-氨基-1,4-苯并二噁烷是制备艾托拉嗪的关键中间体,该化合物由其对应的硝基物5-硝基-1,4-苯并二噁烷还原所得,反应方程式如scheme1所示:目前5-硝基-1,4-苯并二噁烷还原的方法主要是采用贵金属pd/c进行还原,根据还原剂的不同分为以下几种方法:一、以甲酸铵为氢源进行pd/c催化转氢工艺2002年cn1084619c中报道以规格为10wt%pd/c为催化剂、采用甲酸铵为氢源、甲醇为溶剂进行反应,反应结束后经过乙腈研磨、柱层析纯化得目标产物,收率为74%,且pd/c用量为过多(生产1.51g目标产物需要加入1.44gpd/c)。二、以水合肼为氢源进行pd/c催化转氢工艺2009年湘潭大学林原斌等人(化学研究与应用,2009,21(3):419-422,艾托拉嗪的合成)中采用pd/c为催化剂、水合肼为氢源、乙醇为溶剂回流反应,反应结束后采用硅胶色谱柱进行纯化,收率为88.32%;采用水合肼作为氢源进行转氢反应,降低了pd/c的使用量且收率较甲酸铵体系大大提高;但后处理过程中产物仍然需要柱层析进行纯化不宜后期车间生产放大。三、pd/c催化加氢在2015年公告的cn102093364b中,北京赛林泰医药技术有限公司采用pd/c为催化剂、在氢气的氛围下加氢,收率高达97%,但反应时间长、pd/c用量大,且后处理同样需要进行硅胶柱层析纯化。以上方法中均采用贵金属pd/c作为催化剂,但无论是转氢反应体系还是加氢反应体系,均具有较多副产物生成,后处理需要采用柱层析进行纯化;pd/c作为一种常见的硝基还原催化剂在医药化工中得到广泛应用,但是在医药原料药及其制剂中pd的含量通常在1-20ppm级别(根据制剂中不同药品的最大日服计量有所区别),5-氨基-1,4-苯并二噁烷与二(2-氯乙基)胺一步反应即制备出最终原料药,所以5-氨基-1,4-苯并二噁烷制备过程中的pd残留量会直接影响原料药中pd的含量。所以开发一种高收率、后处理简便、环境友好的方法来制备5-氨基-1,4-苯并二噁烷对于治疗运动障碍用药物艾托拉嗪具有重要的意义。技术实现要素:本发明的目的是克服现有技术中5-硝基-1,4-苯并二噁烷还原制备治疗运动障碍用药物中间体5-氨基-1,4-苯并二噁烷中需要采用大量pd/c还原、且后处理繁琐需要柱层析纯化导致难以实现车间生产放大的缺陷,提供一种绿色催化还原方法制备5-氨基-1,4-苯并二噁烷;本发明以2-甲基咪唑为有机配体、以二水合醋酸锌为锌源,在十六烷基三甲基溴化铵存在下水热反应制备出纳米级沸石咪唑骨架材料(zif-8);然后将硫酸亚铁沉积到纳米级沸石咪唑骨架材料(zif-8)孔隙和表面上,最后采用四丁基硼氢化铵还原制备出沸石咪唑骨架负载的铁材料(简写为zif-8@fe);本发明制备的zif-8@fe可高效催化5-硝基-1,4-苯并二噁烷还原制备5-氨基-1,4-苯并二噁烷,解决了pd残留及其后处理繁琐的缺陷,具备工业化应用前景。根据本发明的一个方面,本发明提供了一种沸石咪唑骨架负载的铁材料的制备方法,包括如下步骤:1)制备纳米级沸石咪唑骨架材料:8.2g2-甲基咪唑溶于100ml甲醇的水溶液中,滴加50ml浓度为20mmol/l的二水合醋酸锌水溶液在40-60℃下搅拌,滴加结束后搅拌3-5min加入10ml浓度为5.0wt的十六烷基三甲基溴化铵,保温搅拌12h后过滤、滤饼采用无水甲醇洗涤后在60-70℃下干燥至恒重得纳米级沸石咪唑骨架材料,所述纳米级沸石咪唑骨架材料简写为zif-8;以2-甲基咪唑为有机配体、以醋酸锌为金属离子制备出沸石咪唑骨架材料(zif-8),制备过程中加入适量十六烷基三甲基溴化铵使制备出的沸石咪唑骨架材料大小均匀,无纳米粒子积聚现象;2)制备沸石咪唑骨架负载的铁材料:500mgzif-8超声分散在40ml甲醇中,然后滴加浓度为2mol/l的硫酸亚铁的甲醇溶液,滴加结束后搅拌10-20min,然后滴加50ml浓度为0.2mol/l的四丁基硼氢化铵的甲醇溶液,滴加结束后在40-50℃保温反应2-3h,然后降温至室温离心、滤饼采用甲醇淋洗后干燥得沸石咪唑骨架负载的铁材料;所述沸石咪唑骨架负载的铁材料简写为zif-8@fe;本发明制备的沸石咪唑骨架材料(zif-8)属于金属有机骨架材料,具有微孔隙、高比表面积和孔道结构规整等优点,本发明采用沉积法在沸石咪唑骨架材料(zif-8)孔隙和表面沉积亚铁离子,经过四丁基硼氢化铵还原将亚铁离子和沸石咪唑骨架材料(zif-8)中的锌离子原位还原形成活性物种制备成催化剂。优选的,步骤2)中2mol/l的硫酸亚铁的甲醇溶液的滴加量为3-10ml;通过控制硫酸亚铁的滴加量从而调节zif-8@fe中铁的负载量,进一步优选为8ml;根据本发明的另一个方面,本发明提供了一种沸石咪唑骨架负载的铁材料的用途,在水合肼和溶剂的存在下,用于催化5-硝基-1,4-苯并二噁烷进行还原反应制备治疗运动障碍用药物中间体5-氨基-1,4-苯并二噁烷。优选的,所述还原反应中还包括有机碱,所述有机碱的摩尔用量为5-硝基-1,4-苯并二噁烷摩尔量的0.1-0.3倍;所述有机碱为氮氮二甲基甲酰胺(dmf)、三乙胺(tea)或二异丙基乙基胺(dipea);本发明在试验过程中发现,加入有机碱可以缩短反应时间,本领域技术人员也可以采用其它有机碱来使反应体系维持在在一定碱性条件下,从而加快反应进行。优选的,所述溶剂为甲醇、乙醇、乙二醇或四氢呋喃;优选的,所述沸石咪唑骨架负载的铁材料的用量为5-硝基-1,4-苯并二噁烷重量的5wt%-30wt%;优选的,所述水合肼的摩尔用量为5-硝基-1,4-苯并二噁烷的1.1-2.0倍。本发明首次在沸石咪唑骨架材料(zif-8)上负载活性铁用于催化还原5-硝基-1,4-苯并二噁烷制备5-氨基-1,4-苯并二噁烷,与现有技术相比,本发明技术方案具有如下优点:1)本发明制备的沸石咪唑骨架负载的铁材料比表面积大,为催化反应提供了大量活性位点;2)本发明制备的沸石咪唑骨架负载的铁材料可用于催化5-硝基-1,4-苯并二噁烷制备5-氨基-1,4-苯并二噁烷,与现有技术报道的pd/c相比不仅反应速率加快、而且后处理简便,且与贵金属pd相比,催化成本大大降低;另外,与传统的fe粉催化还原相比,杜绝了铁泥产生和含铁废水的产生;3)本发明通过优化反应过程,在有机碱的存在下1h内实现完全转化,提高了生产效率;4)本发明制备的沸石咪唑骨架负载的铁材料可通过二氧化硅进行包覆,避免活性组分在反应过程中流失,实现催化剂的回收套用。附图说明图1为本发明制备的zif-8@fe的透射电镜图(tem);图2为本发明zif-8@fe催化制备的间氨基苯腈的1h-nmr;图3为本发明zif-8@fe催化制备的对溴苯胺的1h-nmr;图4为本发明zif-8@fe催化制备的对碘基苯胺的1h-nmr。具体实施方式为使本发明的目的、技术方案和优点更加清楚明了,下面结合具体实施方式,对本发明进一步详细说明。应该理解,这些描述只是示例性的,而并非要限制本发明的范围。实施例中所用原料5-硝基-1,4-苯并二噁烷是根据现有技术(化学研究与应用,2009,21(3):419-422,艾托拉嗪的合成)中的教导自制,柱层析后采用反溶剂结晶(乙酸乙酯在50℃溶解后滴加正庚烷析晶)提纯所得,最终hplc纯度为99.86%。hplc分析方法:色谱柱agilentc18;体积比流动相a/b=38/62,流动相a为ph=5.8的磷酸盐水溶液,流动相b为乙腈,分析时间为40min;检测波长为230nm,流速为1.0ml/min。实施例1制备沸石咪唑骨架负载的铁材料:1)制备纳米级沸石咪唑骨架材料:8.2g2-甲基咪唑溶于100ml甲醇的水溶液中,滴加50ml浓度为20mmol/l的二水合醋酸锌水溶液在40-60℃下搅拌,滴加结束后搅拌3-5min加入10ml浓度为5.0wt的十六烷基三甲基溴化铵,保温搅拌12h后过滤、滤饼采用无水甲醇洗涤后在60-70℃下干燥至恒重得纳米级沸石咪唑骨架材料,所述纳米级沸石咪唑骨架材料简写为zif-8(比表面积sbet=1453m2/g);2)制备沸石咪唑骨架负载的铁材料:500mgzif-8超声分散在40ml甲醇中,然后滴加浓度为2mol/l的硫酸亚铁的甲醇溶液,滴加结束后搅拌10-20min,然后滴加50ml浓度为0.2mol/l的四丁基硼氢化铵的甲醇溶液,滴加结束后在40-50℃保温反应2-3h,然后降温至室温离心、滤饼采用甲醇淋洗后干燥得沸石咪唑骨架负载的铁材料;所述沸石咪唑骨架负载的铁材料简写为zif-8@fe。本发明考察了不同硫酸亚铁的滴加量对制备出的zif-8@fe影响,采用不同硫酸亚铁的滴加量制备出的zif-8@fe作为催化剂催化5-硝基-1,4-苯并二噁烷的效果,方法如下:具磁力搅拌器的100ml双层玻璃三口烧瓶中加入20ml乙醇、5-硝基-1,4-苯并二噁烷(10mmol,1.81g)、氢源(30mmol,3.0eq)、不同硫酸亚铁的滴加量制备出的zif-8@fe催化剂(0.18g,10wt%)在氮气保护下于30-40℃下反应,hplc检测反应液中5-硝基-1,4-苯并二噁烷浓度不再减少且产物含量不再增加时,统计各反应体系的反应时间、原料5-硝基-1,4-苯并二噁烷的转化率、产物5-氨基-1,4-苯并二噁烷的选择性,结果如表1所示:表1不同硫酸亚铁的滴加量对zif-8@fe催化性能影响序列feso4滴加量/ml氢源反应时间/h转化率/%选择性/%15nh4cl1611.7—25hcoonh4188.2—35nh2nh2·h2o2490.699.840nh2nh2·h2o24<1.0—53nh2nh2·h2o2486.899.867nh2nh2·h2o2090.999.8710nh2nh2·h2o1990.999.8注:“—”是指未对选择性进行统计。试验结果表明,1)zif-8采用硫酸亚铁处理后制备出的zif-8@fe可有效催化水合肼催化5-硝基-1,4-苯并二噁烷进行硝基还原,氯化铵、甲酸铵等氢源无法被zif-8@fe催化利用进行硝基还原(序列1-3对比);2)随着硫酸亚铁滴加量的增加,底物5-硝基-1,4-苯并二噁烷的转化率逐步增加,但是最高转化率仅为90.9%,后期无法通过继续增加硫酸亚铁滴加量来使底物完全转化;表1序列6中制备的zif-8@fe材料的tem图如图1所示,由图1可以看出本发明制备的zif-8@fe为纳米级,且形貌规整,未出现纳米粒子的积聚现象。实施例1-a为了研究硫酸亚铁和zif-8的相互作用,本发明分别以硫酸亚铁、铁粉、锌粉和zif-8作为催化剂按照实施例1中的方法进行硝基还原,具体方法如下:具磁力搅拌器的100ml双层玻璃三口烧瓶中加入20ml乙醇、5-硝基-1,4-苯并二噁烷(10mmol,1.81g)、水合肼(30mmol,3.0eq)、催化剂(0.18g,10wt%)在氮气保护下于30-40℃下反应,hplc检测反应液中5-硝基-1,4-苯并二噁烷浓度不再减少且产物含量不再增加时,统计各反应体系的反应时间、原料5-硝基-1,4-苯并二噁烷的转化率、产物5-硝基-1,4-苯并二噁烷的选择性,结果见表2所示:表2硫酸亚铁和zif-8的催化效果序列催化剂反应时间/h转化率/%1feso4240.22fe粉241.63锌粉243.44zif-8(实施例1制备)240试验结果表明,以水合肼为氢源单纯采用催化量的铁粉、锌粉、硫酸亚铁及其zif-8均无法有效催化水合肼对5-硝基-1,4-苯并二噁烷进行硝基还原。实施例2本发明以实施例1中表1序列6中的方法制备的zif-8@fe作为催化剂、以水合肼作为氢源,本发明进一步对反应溶剂、催化剂用量及其水合肼用量对反应的影响,优化方法如下:平行合成仪中加入20ml溶剂、5-硝基-1,4-苯并二噁烷(10mmol,1.81g)、水合肼(11-40mmol,1.1-4.0eq)、zif-8@fe(18mg-905mg,1.0-50wt%以底物5-硝基-1,4-苯并二噁烷为计算基准)在氮气保护下于30-40℃下反应,hplc检测反应液中5-硝基-1,4-苯并二噁烷浓度不再减少且产物含量不再增加时,统计各反应体系的反应时间、原料5-硝基-1,4-苯并二噁烷的转化率、产物5-氨基-1,4-苯并二噁烷的选择性,结果见表3所示:表3反应体系优化试验结果表明采用乙二醇作为反应溶剂,反应24-36h可以实现底物的完全转化,几乎定量的生成目标产物。实施例3采用本发明制备的zif-8@fe催化剂催化5-硝基-1,4-苯并二噁烷可以定量的催化硝基还原反应,但是反应周期过长,本发明通过采用增加反应温度(乙二醇沸点高)和添加助剂以期缩短反应周期,优化方法如下:平行合成仪中加入20ml乙二醇、5-硝基-1,4-苯并二噁烷(10mmol,1.81g)、水合肼(15mmol,1.5eq)、zif-8@fe(0.362g,20wt%以底物5-硝基-1,4-苯并二噁烷为计算基准)、添加剂(2mmol,0.2eq)在氮气保护下于30-130℃下反应,hplc检测反应液中5-硝基-1,4-苯并二噁烷浓度不再减少且产物含量不再增加时,统计各反应体系的反应时间、原料5-硝基-1,4-苯并二噁烷的转化率、产物5-氨基-1,4-苯并二噁烷的选择性,结果见表4所示:表4反应温度和助剂对反应时间的影响序列温度/℃助剂反应时间/h转化率/%选择性/%150na2610099.8280na2410099.83120na1210099.84130na1010099.65120硝酸锂1110099.76120硝酸铜1210099.77120硝酸钙1289.799.88120硝酸镁1010099.19120醋酸2489.899.810120三乙胺210099.811120二异丙基乙基胺110099.812120氮氮二甲基甲酰胺610099.813100二异丙基乙基胺110099.81480二异丙基乙基胺210099.81540二异丙基乙基胺510099.8注:na是指未添加任何助剂。试验结果表明,在不添加助剂的情况下随着反应温度的升高能在一定程度上缩短反应时间,但温度超过120℃后目标产物的选择性会出现下降趋势,且反应时间仍长达12h;本发明尝试在反应体系中添加酸、碱或金属盐作为添加剂,实验人员惊奇的发现无机碱可加快反应速率,缩短反应周期,尤其是二异丙基乙基胺作为添加剂,可以在40℃下5h内即可完成反应。实施例4在5l具四氟机械搅拌桨的双层玻璃反应釜中加入1.5l乙二醇,开启搅拌然后加入5-硝基-1,4-苯并二噁烷(1mol,181g)、65wt%水合肼(1.5mol,1.5eq)、zif-8@fe(36.2g,20wt%)、二异丙基乙基胺(0.2mol,0.2eq)在氮气保护下于80-90℃下反应,2h后取反应液进行hplc检测(面积百分比:5-硝基-1,4-苯并二噁烷0.08%,5-氨基-1,4-苯并二噁烷99.76%,未知杂质0.16%);反应降温至室温,过滤去除催化剂zif-8@fe,将滤液转移至萃取反应釜中加入1.5l纯化水和2l乙酸乙酯搅拌萃取分液,水相采取乙酸乙酯萃取两次,每次乙酸乙酯用量为2l,合并所有乙酸乙酯相在45-50℃下减压脱溶得5-氨基-1,4-苯并二噁烷143.0g,收率为94.6%,hplc纯度为99.93%;1hnmr(400mhz,cdci3)δppm8.62-8.65(t,1h),6.31-6.33(dt,2h),4.23-4.26(m,4h),3.76(s,2h);esi-ms:m/z=152[m+h]+。采用实施例4中的方法能够实现百克级的放大,且后处理方便仅仅通过过滤、萃取、浓缩即可实现产品的分离纯化;为进一步为生产放大提供研发数据,本发明对回收后的催化剂进行了套用研究(底物5-硝基-1,4-苯并二噁烷批量为10.0g),统计了zif-8@fe的回收率及其催化效果,结果如表5所示:表5zif-8@fe的回收率及其催化效果套用次数1234回收率/%86.779.270.468.6转化率/%99.899.699.799.6选择性/%99.999.899.899.8试验结果表明,本发明制备的zif-8@fe材料可以实现催化剂的回收套用,套用次数的增加不会影响催化剂的催化性能,但zif-8@fe的回收率低,本发明采用二氧化硅进行负载能够解决zif-8@fe回收率低的问题,方法如下:将1.0gzif-8@fe超声分散在100ml甲醇中,然后依次加入5.0ml浓度为5.0wt%的氯化十六烷基三甲基铵的水溶液、2.0ml正硅酸乙酯搅拌溶解均匀后滴加浓氨水调节ph至11.0,室温搅拌2-3h后过滤、甲醇淋洗、干燥得二氧化硅负载的zif-8@fe。按照实施例4催化反应条件采用二氧化硅负载的zif-8@fe作为催化剂催化5-硝基-1,4-苯并二噁烷反应(底物5-硝基-1,4-苯并二噁烷批量为100g),6h后反应达到平衡,底物转化率为99.8%,选择性为99.9%,除了反应时间由2h延长至6h外,与未采用二氧化硅负载前相比转化率和选择性均未改变,可能是由于采用二氧化硅负载后zif-8@fe活性位点减少导致反应时间延长,但是二氧化硅负载的zif-8@fe的回收率达到了98.5%,可以使催化剂充分得到回收。实施例5为了拓展本发明制备的zif-8@fe的应用范围,本发明采用不同取代基团的硝基苯作为底物,考察催化效果,方法如下:100ml三口烧瓶中加入乙二醇20ml、硝基苯衍生物(10mmol),催化剂zif-8@fe(0.2g)、65wt%水合肼(20mmol,2.0eq)和1ml二异丙基乙基胺在60-70℃下反应,lc-ms检测反应液中硝基苯衍生物浓度不再变化时停止反应,过滤去除zif-8@fe,滤液加入20ml纯化水搅拌均匀后采用乙酸乙酯萃取浓缩得氨基苯衍生物;不同底物的反应情况如表6所示:表6zif-8@fe对不同底物的催化效果试验结果表明,本发明制备的zif-8@fe可有效催化其它硝基苯衍生物,在含有氰基、卤代基取代的硝基苯中基本未发生氰基还原和脱卤副产物的发生,为催化剂提供了广阔的应用前景。尽管已经详细描述了本发明的实施方式,但是应该理解的是,在不偏离本发明的精神和范围的情况下,可以对本发明的实施方式做出各种改变、替换和变更。当前第1页12