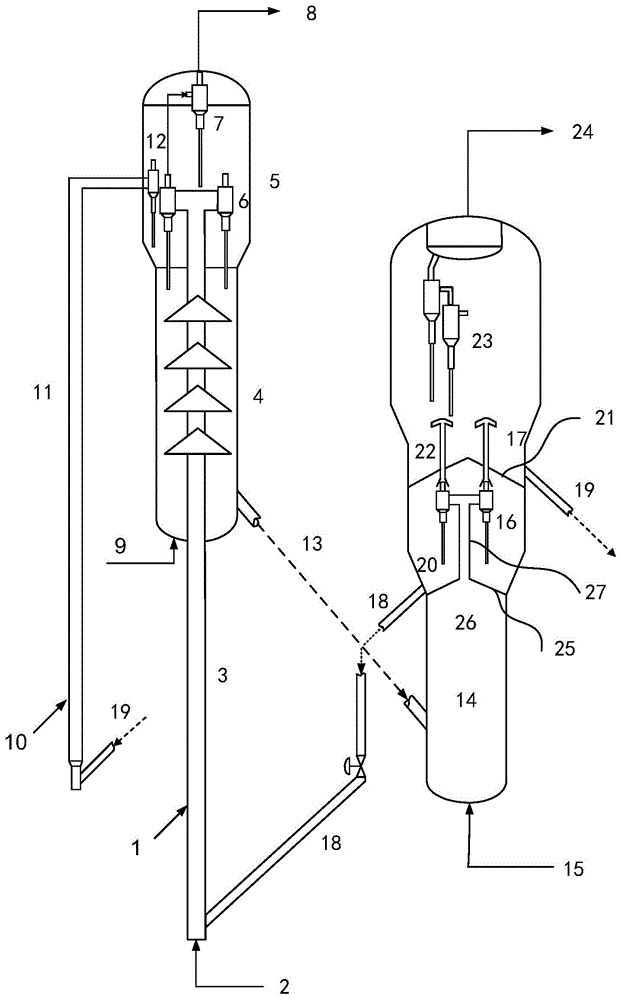
本发明涉及石油化工领域,具体的说,本发明涉及一种双催化剂分区催化裂化方法及装置。
背景技术:
:催化裂化工艺是炼油技术中的核心工艺,不仅是重油加工的主要手段,生产轻质油组分的主要来源,而且在提供轻质烯烃和石油化工一体化技术方面,具有不可取代的地位。催化裂化是典型平行顺序反应,有一次反应及二次反应,其中,一次反应主要是重组分的裂化反应,生成轻烃及烯烃产物,二次反应主要是轻烃裂化及烯烃的进一步反应,如汽、柴油馏分的继续裂化及烯烃的氢转移反应、异构化反应、烷基化反应等。研究发现,催化裂化中一次反应和二次反应所需的工艺条件及催化剂性质存在较大的差别。热力学结果表明大分子重油裂化只需较低的活化能,而较小分子(汽油)裂化需要较高的活化能,因此重油的一次裂化需要较低的温度,而一次裂化产品如汽油的二次裂化应在较高的温度下进行,同时,二次反应需要较长的反应时间。为了兼顾一次反应和二次反应对反应温度和反应时间的不同需求,已经开发了催化裂化分区控制工艺技术,通过设置不同反应区,控制不同反应区的温度及反应时间,以满足一次反应及二次反应的不同热力学特性。如dcc-plus工艺。dcc-plus工艺采用提升管反应器+流化床反应器的形式,使用提升管反应器与流化床反应器串联,实现一次反应和二次反应对反应时间的不同需求,此外,该工艺通过向流化床反应器内部补充热的再生催化剂的技术实现分区控制,改变了流化床反应器的催化剂活性分布及反应温度,同时可以在保持流化床反应器温度一定的情况下,降低提升管反应器的温度和剂油比,以满足重质原料的一次裂解反应和轻质原料的二次裂解反应对催化剂活性和反应条件的各自要求。结果表明,提升管反应器与流化床反应器串联使用及补充再生催化剂至流化床反应器,可改变油气在不同反应区的停留时间,增加重油的裂化、提高低碳烯烃的产率和改善汽油性质,降低提升管出口温度和提升管入口油剂混合温度,可明显降低干气和焦炭产率。cn201610917106.7公开了一种生产低碳烯烃和轻芳烃的催化裂化方法,重质原料在第一反应器(提升管反应器ⅰ)与第一部分催化裂解催化剂接触进行反应,富含饱和烃的轻质原料和富含烯烃的轻质原料在第二反应器(提升管反应器ⅱ)和第三反应器(流化床反应器)与第二部分催化裂解催化剂接触进行反应,以增产低碳烯烃和轻芳烃。该方法设置了三个反应器,相当于三个反应区,实现了原料的分区裂化转化,但是使用的是同一种催化剂,虽然第一反应器和第二反应器都使用的是再生后的催化剂,但是没有针对原料转化性质差异匹配不同催化剂,没有实现催化剂的分区,不能使原料、催化剂及工艺条件三者高度匹配。cn98101765.7公开了一种同时制取低碳烯烃和高芳烃汽油的方法,使重质石油烃和水蒸气在一个由提升管和密相流化床组成的复合反应器的下部,即提升管下部,与含沸石催化剂接触,使轻质石油烃进入复合反应器的上部,即密相流化床底部,与来自提升管的含沸石催化剂接触。该方法设置了两个反应区,实现了原料的分区裂化转化,但使用的是一种催化剂,且第二反应区(密相流化床)的催化剂为来自第一反应区(提升管反应器)的催化剂,没有实现催化剂的分区,催化剂活性、催化剂与原料转化性能之间不能高度匹配。另外,催化裂化是单分子吸热反应,在强酸位发生,而氢转移反应是双分子放热反应,在弱酸位发生,且要求较高的酸密度。异构化是单分子放热,在较强酸位上发生。而且,催化剂的孔径不同,异构化性能也存在差异,如随着沸石孔径的减小,沸石的异构化性能逐渐降低。使用稀土或磷对y分子筛改性后,y分子筛的异构化性能增强。重油大分子的裂化需要的催化剂孔径较大,而轻油小分子的裂化需要的催化剂孔径较小。而对于同一种催化剂,要想同时兼顾以上各种性能是很难做到的,常常顾此失彼。为了弥补同一种催化剂不能兼顾多种性能的缺陷,目前的做法是使用两种催化剂,如usy和zsm系列催化剂的混合使用,通过加入zsm系列催化剂来增强小分子的二次反应,以增产低碳烯烃。cn200410006189.1公开了一种生产低碳烯烃和芳烃的化工型炼油方法,其中催化裂化催化剂为中孔zsm系列催化剂和大孔y系列催化剂的混合物。存在的问题是,重油的一次裂化及缩合反应同样可以在zsm系列催化剂的表面发生,使zsm系列催化剂表面及孔道入口被焦炭覆盖,阻碍了小分子进入zsm系列催化剂孔道继续反应,严重降低了zsm系列的催化活性,导致轻油在zsm系列催化剂上二次反应较少。技术实现要素:为了解决以上问题,本发明提出催化剂分区的催化裂化方法和装置,使用两种不同性质的催化剂,以满足同一种催化剂无法兼顾多种性能的要求。同时将再生后的两种催化剂通过催化剂初旋分离器进行分离富集,然后将两种催化剂输送到不同的反应区,在各反应区匹配不同的原料,同时根据热力学性质匹配不同的工艺条件,以达到催化剂与原料及工艺条件三者的高度匹配,强化了每种催化剂的催化性能,使催化剂的催化性能得到充分发挥。避免了催化剂混合使用时,一种催化剂对另一种催化剂的影响。本发明的一个目的在于提供一种双催化剂分区催化裂化装置;本发明的另一目的在于提供一种双催化剂分区催化裂化方法。为达上述目的,一方面,本发明提供了一种双催化剂分区催化裂化装置,其中,所述装置包括用于重质原料油催化裂化反应的主反应器3、用于轻质原料油催化裂化反应的副反应器11、以及再生器14,再生器14中段内部设置第一隔板21和第二隔板25,以将再生器分隔为上部的b催化剂贮藏室22、中部的a催化剂贮藏室20、以及下部的催化剂再生室26,a催化剂贮藏室20内部设置a催化剂初旋分离器16,a催化剂初旋分离器16入口通过管路穿过第二隔板25与催化剂再生室26连通,a催化剂初旋分离器16底部设置开口与a催化剂贮藏室20连通,b催化剂贮藏室22内部设置b催化剂初旋分离器17,b催化剂初旋分离器17底部通过管路穿过第一隔板21与a催化剂初旋分离器16顶部连接,b催化剂初旋分离器17顶部设置水平开口与b催化剂贮藏室22连通,a催化剂贮藏室20底部通过管路与主反应器3连接,b催化剂贮藏室22底部通过管路与副反应器11连接。根据本发明一些具体实施方案,其中,所述主反应器和副反应器的型式分别是各自独立的提升管反应器、输送床反应器、提升管+快速床反应器、湍流床+快速床反应器中的一种或多种的组合。催化剂初旋分离器是用于催化剂初步分离的旋风分离器,旋风分离器是已知产品,是化工领域常见的分离设备。而根据本发明一些具体实施方案,其中,a催化剂初旋分离器为能够实现a催化剂分离50~100wt%的旋风分离器,其进气口开在上方或中间位置。本领域技术人员可以根据本发明所述的分离指标来选择合适尺寸的初旋分离器。其中a催化剂的参数为:催化剂堆密度为0.8-1.5g/cm3,优选为0.9-1.2g/cm3;平均粒径80-140um,优选为90-120um;粒径分布:大于80um粒径的颗粒占催化剂a总重量的60~100wt%,优选为80~100wt%根据本发明一些具体实施方案,其中,所述b催化剂初旋分离器为能够实现b催化剂分离50~100wt%的旋风分离器,其进气口开在上方或中间位置。其中b催化剂的参数为:催化剂堆密度为0.4-0.7g/cm3,优选为0.5-0.65g/cm3;平均粒径20-80um,优选为40-60um;粒径分布:30~50um粒径的颗粒占催化剂b总重量的60~100wt%,优选为80~100wt%。根据本发明一些具体实施方案,其中,所述a催化剂贮藏室20底部通过第一再生斜管18与主反应器3连接,b催化剂储罐22底部通过第二再生斜管19与副反应器11连接;a催化剂初旋分离器16通过催化剂立管27与催化剂再生室26连通。根据本发明一些具体实施方案,其中,所述主反应器3和副反应器11分别为提升管反应器;主反应器3顶部与汽提器4底部连接并贯穿汽提器4进入到沉降器5,汽提器4顶部与沉降器5底部连接,副反应器11顶部与沉降器5连接;主反应器3底部通过第一再生斜管18与a催化剂贮藏室20底部连接;副反应器11底部通过第二再生斜管19与b催化剂贮藏室22底部连接;汽提器4下端通过待生斜管13与催化剂再生室26下端连接。根据本发明一些具体实施方案,其中,所述沉降器5内设置第一初旋分离器12,副反应器11顶部与第一初旋分离器12连接。根据本发明一些具体实施方案,其中,沉降器5内还设置与主反应器3连接的第二初旋分离器6,并在沉降器5顶部设置二级旋分器7,二级旋分器7顶部穿过沉降器5顶部与外界连通。根据本发明一些具体实施方案,其中,再生器14内上部设置旋风分离器23,旋风分离器23顶部通过管路穿过再生器14顶部与外界连通。上述催化裂化反应装置在原有dcc-plus装置的再生器中增加一套催化剂初旋分离系统,用于a、b催化剂的分离富集,并设置隔板,避免富集后的催化剂混合,并将a、b催化剂分区到主、副反应器中,并匹配裂化性质差异较大的原料,该初旋分离系统由串联的两个旋分或粗旋或旋流头构成。另一方面,本发明还提供了一种双催化剂分区催化裂化方法,其中,所述方法包括在石油烃催化裂化反应中使用两种不同的催化剂,包括在重质原料油催化裂化反应中使用a催化剂,并在轻质原料油催化裂化反应中使用b催化剂。根据本发明一些具体实施方案,其中,a催化剂堆密度为0.8-1.5g/cm3,平均粒径80-140um,粒径分布:大于80um粒径的颗粒占催化剂a总重量的60~100wt%。根据本发明一些具体实施方案,其中,a催化剂堆密度为0.9-1.2g/cm3。根据本发明一些具体实施方案,其中,a催化剂平均粒径90-120um。根据本发明一些具体实施方案,其中,a催化剂粒径分布:大于80um粒径的颗粒占催化剂a总重量的80~100wt%。根据本发明一些具体实施方案,其中,b催化剂堆密度为0.4-0.7g/cm3,平均粒径20-80um,粒径分布:30~50um粒径的颗粒占催化剂b总重量的60~100wt%。根据本发明一些具体实施方案,其中,b催化剂堆密度为0.5-0.65g/cm3。根据本发明一些具体实施方案,其中,b催化剂平均粒径40-60um。a催化剂具有高的重质原料裂化性能、高的基质裂化活性;b催化剂具有高的烯烃选择性、低的氢转移活性、强的轻质油二次转化能力。本发明所用的a催化剂可以是适用于重质原料油催化裂化过程的任何催化剂。而根据本发明一些具体实施方案,其中,a催化剂以重量百分比计包含以下组分:15~40%的天然矿物质,10~35%的zsm-5分子筛或改性zsm-5分子筛,50~75%的y型分子筛。所述的天然矿物质选自高岭土、多水高岭土、蒙脱土、硅藻土、凸凹棒石、海泡石、埃洛石、水滑石、膨润土、累托土中的至少一种。所述的y型分子筛选自dasy分子筛、含稀土的dasy分子筛、usy分子筛、含稀土的usy分子筛、rey分子筛、rehy分子筛、hy分子筛中的至少一种。本发明所使用的催化剂b可以是适合轻质原料油催化裂化的任何催化剂。而根据本发明一些具体实施方案,其中,b催化剂以重量百分比计包含以下组分:15~40%的天然矿物质,50~75%的zsm-5分子筛或改性zsm-5分子筛,10~35%的y型分子筛。所述的天然矿物质选自高岭土、多水高岭土、蒙脱土、硅藻土、凸凹棒石、海泡石、埃洛石、水滑石、膨润土、累托土中的至少一种。所述的y型分子筛选自dasy分子筛、含稀土的dasy分子筛、usy分子筛、含稀土的usy分子筛、rey分子筛、rehy分子筛、hy分子筛中的至少一种。根据本发明一些具体实施方案,其中,b催化剂粒径分布:30~50um粒径的颗粒占催化剂b总重量的80~100wt%。根据本发明一些具体实施方案,其中,所述方法还包括将经过反应后失活催化剂进行再生,并将再生后的催化剂经过两次分离富集,分别得到富含a催化剂的再生a催化剂、以及富含b催化剂的再生b催化剂,然后将再生a催化剂输送用于重质原料油催化裂化反应,将再生b催化剂输送用于轻质原料油催化裂化反应。根据本发明一些具体实施方案,其中,被输送用于重质原料油催化裂化反应的再生a催化剂中a催化剂和b催化剂的重量比为7:3至9:1;被输送用于轻质原料油催化裂化反应的再生b催化剂中b催化剂和a催化剂的重量比为7:3至9:1。根据本发明一些具体实施方案,其中,被输送用于重质原料油催化裂化反应的再生a催化剂中a催化剂和b催化剂的重量比为8:2。根据本发明一些具体实施方案,其中,被输送用于轻质原料油催化裂化反应的再生b催化剂中b催化剂和a催化剂的重量比为8:2。根据本发明一些具体实施方案,其中,在石油烃催化裂化反应系统中,a催化剂和b催化剂的重量比为6:4至9:1。根据本发明一些具体实施方案,其中,在石油烃催化裂化反应系统中,a催化剂和b催化剂的重量比为7:3至8:2。根据本发明一些具体实施方案,其中,所述的轻质原料油包括富含c4、c5、c6中的一种或多种的烃馏分、汽油馏分、和柴油馏分的一种或多种的混合物;所述的重质原料油包括石油烃类、油砂沥青、矿物油、合成油、动物油脂、和植物油脂中的一种或多种的混合物。其中汽、柴油馏分可以是来自反应得到的部分汽、柴油馏分,也可以是催化裂化、热裂解、焦化汽、柴油馏分、直馏汽、柴油馏分中的一种或一种以上的混合物。本发明通过将催化剂分区实现烃类分区转化,将不同性质的混合催化剂富集后输送到不同反应区中,同时匹配不同的原料,提高了催化剂与原料的匹配度,弥补了同一催化剂不能兼顾多种性质原料的缺陷,大大提高了催化剂的效率,同时,可以定向控制烃类的转化(如裂化、芳构化、异构化、叠合等反应),提高目的产物选择性。另外,通过工艺参数调整,可以大幅度减少副反应的发生。如在主反应器反应中,降低反应温度,适度裂化重质原料,而在副反应器中提高反应温度,使轻质原料充分反应,以减少干气及焦炭产率。根据本发明一些具体实施方案,其中,重质原料油催化裂化反应的反应条件包括:重质原料油预热温度为160~350℃,反应温度为460~550℃,剂油比为4~12,催化剂微反活性50~70,反应时间1.0~7.0s,反应压力为0.1~0.4mpa;轻质原料油催化裂化反应的反应条件包括:轻质原料油预热温度为40~200℃,反应温度为460~600℃,剂油比为4~15,催化剂微反活性50~80,反应时间0.3~7s,反应压力为0.1~0.4mpa。根据本发明一些具体实施方案,其中,重质原料油催化裂化反应的反应条件包括:重质原料油预热温度为180~280℃。根据本发明一些具体实施方案,其中,重质原料油催化裂化反应的反应条件包括:反应温度为490~530℃。根据本发明一些具体实施方案,其中,重质原料油催化裂化反应的反应条件包括:剂油比为6~9。根据本发明一些具体实施方案,其中,重质原料油催化裂化反应的反应条件包括:催化剂微反活性58~65。根据本发明一些具体实施方案,其中,重质原料油催化裂化反应的反应条件包括:反应时间1.5~4.5s。根据本发明一些具体实施方案,其中,轻质原料油催化裂化反应的反应条件包括:轻质原料油预热温度为60~150℃。根据本发明一些具体实施方案,其中,轻质原料油催化裂化反应的反应条件包括:反应温度为500~580℃。根据本发明一些具体实施方案,其中,轻质原料油催化裂化反应的反应条件包括:剂油比为6~9。根据本发明一些具体实施方案,其中,轻质原料油催化裂化反应的反应条件包括:催化剂微反活性60~75。根据本发明一些具体实施方案,其中,轻质原料油催化裂化反应的反应条件包括:反应时间1~6s。根据本发明一些具体实施方案,其中,所述方法包括使用本发明前面任意一项所述的装置进行催化裂化反应。根据本发明一些具体实施方案,其中,所述a催化剂初旋分离器限定入口气速6~12m/s;所述b催化剂初旋分离器限定入口气速12~22m/s,b催化剂初旋分离器入口气速比a催化剂初选分离器入口气速高6~10m/s。根据本发明一些具体实施方案,其中,所述方法包括将再生后的催化剂(a催化剂和b催化剂的混合物)由催化剂立管从再生器引出,首先通过a催化剂初旋分离器对a催化剂富集分离,富含a催化剂的再生a催化剂进入a催化剂贮罐,经第一再生斜管输送到主反应器底端与重质原料油反应;未分离下来的富含b催化剂的催化剂混合物,经b催化剂初旋分离器使颗粒较小的b催化剂分离富集,富含b催化剂的再生b催化剂进入b催化剂贮罐,再由第二再生斜管输送至副反应器底部与轻质原料油接触反应。根据本发明一些具体实施方案,其中,;经b催化剂初旋分离器未分离下来的细小粉末进入再生器顶部,经再生器顶端旋风分离器分离后,烟气排出,细小催化剂粉末进入b催化剂贮藏室。综上所述,本发明提供了一种双催化剂分区催化裂化方法及装置。本发明的方法具有如下优点:本发明的工艺技术优点在于根据原料的性质及生产目的,定向匹配使用两种催化剂,再生后将a、b催化剂分别富集,并输送到不同反应器中,与不同性质的原料接触反应,通过催化剂的分区与分区的原料实现催化剂与原料的高度定向匹配。并根据不同区催化反应的特性,匹配优化的工艺条件,实现催化剂、原料及工艺条件三方面的高度匹配,以提高原料定向转化效率和催化剂定向催化效率,从而加强催化裂化能力,强化了每种催化剂的催化性能,使催化剂的催化性能得到充分发挥。避免了催化剂混合使用时,一种催化剂对另一种催化剂的影响,减少副产物产生,提高目的产物收率。附图说明图1为本发明实施例1的装置的示意图。具体实施方式以下通过具体实施例详细说明本发明的实施过程和产生的有益效果,旨在帮助阅读者更好地理解本发明的实质和特点,不作为对本案可实施范围的限定。各实施例的设备连接关系如图1所示。该方法为首先在常规双提升管催化裂化装置的再生器14中部设置两个隔板:第一隔板21和第二隔板25,第一隔板21和第二隔板25将再生器分隔为上部的b催化剂贮藏室22、中部的a催化剂贮藏室20、以及下部的催化剂再生室26。a催化剂初旋分离器16位于第一隔板21下面,b催化剂初旋分离器17位于第一隔板21上面,将a、b催化剂初旋分离器串联的管路穿过第一隔板21。a催化剂初旋分离器16置于由第一隔板21、第二隔板25及再生器周围筒壁构成的a催化剂贮藏室20中,b催化剂初旋分离器置于第一隔板21及再生器上部分筒壁构成的b催化剂贮藏室22中。a催化剂贮藏室20下部设置第一再生斜管18与主反应器3底端相连。b催化剂贮藏室22下部设置第二再生斜管19与副反应器11相连。其工艺过程为将预热的重质原料油1从主反应器3的下部进入,与来自a催化剂贮藏室20富含a催化剂的再生a催化剂在预提升蒸汽2的提升作用下,边上升边反应,反应后的油气及失活的a催化剂在初旋分离器6的作用下油气分离,油气继续上升,经二级旋分器7后得到油气8,油气8进入冷却分离系统,进行冷却分离。旋分下来的催化剂在汽提段4经汽提蒸汽9汽提后,经待生斜管13输送到再生器14的催化剂再生室26中再生。将预热的轻质原料油10在副反应器11下部引入,与来自b催化剂贮藏室22的富含b的再生b催化剂在副反应器11中反应,反应后油气及失活催化剂在初旋分离器12中初步分离,再经二级旋分器7分离后得到油气排出,失活催化剂经沉降器5进入汽提段4,经汽提蒸汽9汽提后,再经待生斜管13输送到再生器14的催化剂再生室26中再生。进入再生器14的失活催化剂在再生空气15的作用下再生,再生后的再生催化剂混合物经过催化剂立管27进入a催化剂初旋分离器16进行a催化剂的富集分离,得到的富含a催化剂的再生a催化剂进入a催化剂贮藏室20,再由第一再生斜管18输送至主反应器底部与重质原料油反应。未分离下来的再生催化剂混合物进入b催化剂初旋分离器17中,对b催化剂富集分离,分离下来的富含b催化剂的再生b催化剂进入b催化剂贮藏室22,再经第二再生斜管19输送至副反应器11底部与轻质原料油反应。经b催化剂初旋分离器未分离下来的催化剂粉末及烟气继续上升经旋风分离器23分离后,催化剂粉末下降,烟气24由再生器14顶部烟气管道排出。重质原料油性质如表1所示,轻质原料油为重质原料油一次裂化生成的汽油馏分及c4烃。表1重质原料性质项目数据项目数据密度(20℃)kg/m3914氮含量,wt%0.02残炭,wt%0.24烃族组成分析元素分析饱和烃,wt%69.8氢含量,wt%12.57芳烃,wt%23.7碳含量,wt%86.67胶质,wt%6.1硫含量,wt%0.33沥青质,wt%<0.4实施例1主反应器为提升管反应器,副反应器为提升管+床层反应器。a、b催化剂的性质如表2所示,输送到主反应器催化剂组成:70wt%a+30wt%b,输送到副反应器催化剂组成:70wt%b+30wt%a,主要工艺条件如表3所示,反应结果如表4所示。表2催化剂性质表3主要工艺条件表4产品分布实施例1对比例(dcc-plus工艺)产物收率,重wt%干气5.337.54液化气39.4040.16c5+汽油33.7630.17柴油11.4611.25油浆3.693.07焦炭5.987.23转化率,wt%84.4685.68总烯烃产率,wt%37.6833.76乙烯5.163.86丙烯17.7917.16丁烯14.7312.74实施例2主反应器为提升管反应器,副反应器为提升管+床层反应器。a、b催化剂的性质如表5所示,输送到主反应器催化剂组成:80wt%a+20wt%b,输送到副反应器催化剂组成:80wt%b+20wt%a,主要工艺条件如表6所示,反应结果如表7所示。表5催化剂性质表6主要工艺条件重质原料油预热温度,℃240轻质原料油预热温度,℃100主反应器反应温度,℃515副反应器反应温度,℃560主反应器的剂油比8副反应器的剂油比7主反应器反应时间,s8副反应器反应时间,s5主反应器反应压力,mpa0.3副反应器反应压力,mpa0.3催化剂微反活性a:60b:70再生温度,℃680表7产品分布实施例2对比例(dcc-plus工艺)产物收率,重wt%干气5.617.54液化气42.4740.16c5+汽油32.4630.17柴油10.4211.25油浆2.793.07焦炭5.867.23转化率,wt%87.6285.68总烯烃产率,wt%39.7633.76乙烯5.463.86丙烯19.6617.16丁烯14.6412.74实施例3主反应器为提升管反应器,副反应器为提升管+床层反应器。a、b催化剂的性质如表8所示,输送到主反应器催化剂组成:90wt%a+10wt%b,输送到副反应器催化剂组成:90wt%b+10wt%a,主要工艺条件如表9所示,反应结果如表10所示。表8催化剂性质表9主要工艺条件重质原料预热温度,℃240轻质原料的预热温度,℃100主反应器反应温度,℃530副反应器反应温度,℃580主反应器的剂油比9副反应器的剂油比8主反应器反应时间,s9副反应器反应时间,s6主反应器反应压力,mpa0.3副反应器反应压力,mpa0.3催化剂微反活性a:70b:75再生温度,℃680表10产品分布实施例3对比例(dcc-plus工艺)产物收率,重wt%干气5.897.54液化气43.5440.16c5+汽油31.5230.17柴油10.0411.25油浆2.333.07焦炭6.157.23转化率,wt%87.1185.68总烯烃产率,wt%38.8433.76乙烯5.613.86丙烯19.1117.16丁烯14.1212.74通过表中数据可以看出,采用本专利双催化剂分区的催化裂化工艺和装置,目标产物的产率明显提高,如低碳烯烃产率提高3.92wt%~5.08wt%,而副产物收率明显降低,如干气和焦炭的产率分别降低1.65wt%~2.21wt%和1.08wt%~1.37wt%。当前第1页12