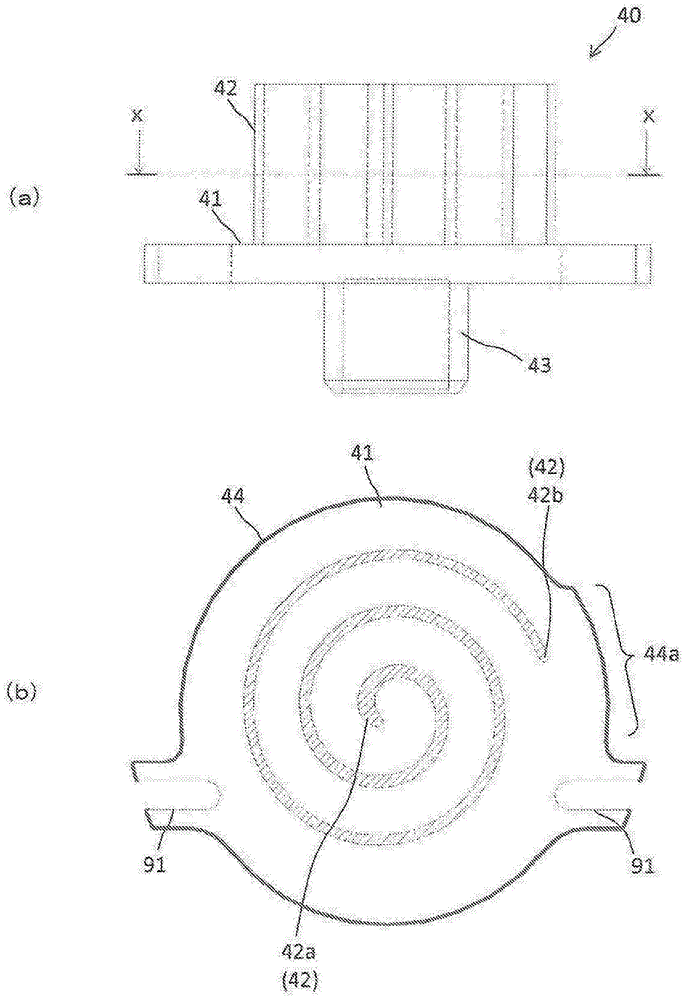
本发明涉及涡旋式压缩机。
背景技术:近年来,已知有一种密闭型涡旋式压缩机,其配置有:在压缩容器内设置分隔板,并且在由该分隔板分隔而成的低压侧的室内具有固定涡旋件和回旋涡旋件的压缩构件;和回旋驱动该回旋涡旋件的电动构件。提案有具有下述结构的装置:在该种密闭型涡旋式压缩机中,使固定涡旋件的凸台部嵌合在分隔板的保持孔中,将由压缩构件压缩后的制冷剂经由固定涡旋件的排出端口排出到由分隔板分隔出的高压侧的室内(例如参照专利文献1)。以专利文献1为代表的这种涡旋式压缩机,由于压缩构件的周围是低压空间,所以对回旋涡旋件和固定涡旋件施加使彼此远离的方向的力。因此,为了提高由回旋涡旋件和固定涡旋件形成的压缩室的密闭性,较多情况下使用片密封件(chipseal)。现有技术文献专利文献专利文献1:日本特开平11-182463号公报
技术实现要素:发明要解决的课题然而,为了进行高效率的运转,优选对回旋涡旋件或固定涡旋件施加背压。用于解决课题的方法因此,本发明提供一种涡旋式压缩机,固定涡旋件能够在分隔板与主轴承之间在轴向移动,通过对形成于分隔板与固定涡旋件之间的排出空间施加高压压力,能够将固定涡旋件按压于回旋涡旋件。此外,本发明提供一种涡旋式压缩机,其包括:形成于主轴承的上表面的轴承侧凹部;形成于固定涡旋件的下表面的涡旋件侧凹部;和下端部插入到轴承侧凹部、上端部插入到涡旋件侧凹部的柱状部件,柱状部件与轴承侧凹部及涡旋件侧凹部中的至少一者能够滑动。发明效果在本发明的涡旋式压缩机中,能够消除固定涡旋件和回旋涡旋件之间的间隙,能够进行高效率的运转。此外,在本发明的涡旋式压缩机中,利用涡旋件侧凹部、轴承侧凹部和柱状部件能够阻止固定涡旋件的旋转和半径方向上的移动,能够允许固定涡旋件向轴向的移动。附图说明图1是表示本发明的实施方式的密闭型涡旋式压缩机的结构的纵截面图。图2(a)是表示本实施方式的密闭型涡旋式压缩机的回旋涡旋件的侧视图,(b)是该图(a)的X-X线截面图。图3是表示本实施方式的密闭型涡旋式压缩机的固定涡旋件的底视图。图4是从底面观察该固定涡旋件的立体图。图5是从上面观察该固定涡旋件的立体图。图6是表示本实施方式的密闭型涡旋式压缩机的主轴承的立体图。图7是表示本实施方式的密闭型涡旋式压缩机的自转抑制部件的顶视图。图8是表示本实施方式的密闭型涡旋式压缩机的分隔板和固定涡旋件的主要部分截面图。图9是表示本实施方式的密闭型涡旋式压缩机的主要部分的部分截面立体图。图10是表示本实施方式的密闭型涡旋式压缩机的各旋转角度下的回旋涡旋件和固定涡旋件的相对位置的组合图。图11是表示本发明的第2实施方式的密闭型涡旋式压缩机的主要部分的部分截面立体图。具体实施方式本发明的第1方式的涡旋式压缩机,其包括:将密闭容器内划分成高压空间和低压空间的分隔板;与分隔板相邻的固定涡旋件;与固定涡旋件啮合而形成压缩室的回旋涡旋件;防止回旋涡旋件自转的自转抑制部件;和支承回旋涡旋件的主轴承,固定涡旋件、回旋涡旋件、自转抑制部件和主轴承配置于低压空间内,固定涡旋件和回旋涡旋件配置于分隔板与主轴承之间,其中涡旋式压缩机包括:形成于主轴承的上表面的轴承侧凹部;形成于固定涡旋件的下表面的涡旋件侧凹部;和下端部插入到轴承侧凹部、上端部插入到涡旋件侧凹部的柱状部件,柱状部件与轴承侧凹部和涡旋件侧凹部中的至少一者能够滑动,由此,固定涡旋件在分隔板与主轴承之间在轴向上移动。根据第1方式,利用涡旋件侧凹部、轴承侧凹部和柱状部件,能够阻止固定涡旋件的旋转和半径方向的移动,能够允许固定涡旋件向轴向的移动。本发明的第2方式是在第1方式中,柱状部件通过过盈配合或过渡配合插入到轴承侧凹部和固定涡旋件侧凹部中的任一者。根据第2方式,不需要用螺栓等固定柱状部件,能够削减部件数量,减少成本。本发明的第3方式是在第1方式中,柱状部件通过过盈配合或过渡配合插入到轴承侧凹部。根据第3方式,由于能够从上方将涡旋件侧凹部插入于被插入到轴承侧凹部的柱状部件,所以组装变得容易。本发明的第4方式是在第3方式中,柱状部件通过间隙配合插入到涡旋件侧凹部,在涡旋件侧凹部设置有与密闭容器内空间连通的连通孔。根据第4方式,通过设置连通孔,能够将润滑油或包含润滑油的制冷剂供给到涡旋件侧凹部与柱状部件之间,减少涡旋件侧凹部或柱状部件的磨损。本发明的第5方式是在第2方式中,在通过过盈配合或过渡配合插入有柱状部件的涡旋件侧凹部或轴承侧凹部,设置有与密闭容器内空间连通的连通孔。根据第5方式,通过设置连通孔,能够在抽真空时将轴承侧凹部内的空气可靠地抽掉,可靠性得到提高。本发明的第6方式是在第1方式~第5方式的任一方式中,轴承侧凹部与柱状部件的嵌合间隙和涡旋件侧凹部与柱状部件的嵌合间隙不同。根据第6方式,通过减小轴承侧凹部与柱状部件的嵌合间隙,能够防止柱状部件从轴承侧凹部脱落,可靠性得到提高。此外,通过增大涡旋件侧凹部与柱状部件的间隙,能够防止在柱状部件发生变形时涡旋件侧凹部与柱状部件的干扰,能够提高涡旋式压缩机的可靠性。本发明的第7方式是在第1方式~第6方式的任一方式中,设置有柱状部件没有插入到涡旋件侧凹部和轴承侧凹部的任一个中的区域。根据第7方式,通过设置没有插入到涡旋件侧凹部和轴承侧凹部的任一个中的区域,能够从该区域将润滑油或包含润滑油的制冷剂供给到柱状部件与涡旋件侧凹部或轴承侧凹部之间,所以能够减少柱状部件与涡旋件侧凹部或轴承侧凹部的磨损。本发明的第8方式是在第1方式~第7方式的任一方式中,至少设置2个以上的柱状部件,用2个以上的柱状部件限制主轴承与固定涡旋件的位置关系。根据第8方式,由于轴承侧凹部和柱状部件能够限制主轴承与固定涡旋件的位置关系,所以不需要另外设置位置限制用部件,能够减少成本。本发明的第9方式是在第1方式~第8方式的任一方式中,在轴承侧凹部的柱状部件的插入部设置有销孔,在销孔内设置有柱状部件的防脱落销。根据第9方式,能够防止柱状部件脱落,能够提高涡旋式压缩机的可靠性。本发明的第10方式是在第1方式~第9方式的任一方式中,用固定涡旋件和分隔板限制固定涡旋件向轴向的可动区域。根据第10方式,由于固定涡旋件在向轴向移动时与分隔板接触,所以第1密封部件的端面和第2密封部件的端面与固定涡旋件接触、发生变形。由此,不会导致密封性的下降,所以能够提高涡旋式压缩机的可靠性。本发明的第11方式是在第1方式~第10方式的任一方式中,包括:在分隔板与固定涡旋件之间配置于排出空间的外周的呈环状的第1密封部件;和在分隔板与固定涡旋件之间配置于第1密封部件的外周的呈环状的第2密封部件,使形成于第1密封部件与第2密封部件之间的中压空间比排出空间的压力低且比低压空间的压力高,利用封闭部件将第1密封部件和第2密封部件夹到分隔板。根据第11实施方式,在分隔板与固定涡旋件之间,通过在作为高压的排出空间以外形成中压空间,易于调整固定涡旋件对回旋涡旋件的按压力。此外,根据第11实施方式,由于用第1密封部件和第2密封部件形成排出空间和中压空间,所以能够减少制冷剂从作为高压的排出空间向中压空间的泄漏、以及制冷剂从中压空间向低压空间的泄漏。此外,根据第11实施方式,由于利用封闭部件将第1密封部件和第2密封部件夹到分隔板,所以在组装分隔板、第1密封部件、第2密封部件和封闭部件之后能够配置于密闭容器内,所以能够实现较少的部件数量,并且容易进行涡旋式压缩机的组装。本发明的第12方式是在第11方式中,在固定涡旋件中形成有将压缩室与中压空间连通的中压端口,并设置有能够封闭中压端口的中压单向阀。根据第12方式,在中压空间内利用压缩室的压力来容易地进行中压空间的压力调整。此外,根据第12方式,由于中压单向阀介于压缩室与中压空间之间,所以能够将中压空间的压力维持成恒定,能够稳定地进行固定涡旋件对回旋涡旋件的按压。本发明的第13方式是在第1~第12方式的任一方式中,固定涡旋件的固定涡旋齿的内壁和外壁的厚度、以及回旋涡旋件的回旋涡旋齿的内壁和外壁的厚度以从固定涡旋齿和回旋涡旋齿的涡旋始端至末端逐渐变薄的方式形成。根据第13方式,通过使厚度直至末端逐渐变薄,能够增大吸入气体的封闭容积,并且由于能够使涡旋齿轻量化,所以能够减小涡旋齿的回旋所产生的离心力。在第13方式的涡旋式压缩机中,为了通过排出空间的压力来确保固定涡旋件和回旋涡旋件的密闭性,不需要在涡旋齿前端设置片密封件。因此,由于设置片密封件而使涡旋齿的薄厚没有限制,所以如第13方式那样能够使涡旋齿变薄。下面,参照附图来说明本发明的第1实施方式。另外,本发明不限定于以下的实施方式。图1是表示本实施方式的密闭型涡旋式压缩机的结构的纵截面图。如图1所示,该密闭型涡旋式压缩机具有沿上下方向延伸的形成为圆筒状的密闭容器10。在密闭容器10内的上部设置有将密闭容器10内上下分隔的分隔板20。分隔板20将密闭容器10内划分成高压空间11和低压空间12。在密闭容器10设置有:将制冷剂导入至低压空间12的制冷剂吸入管13;和将压缩后的制冷剂从高压空间11排出的制冷剂排出管14。低压空间12的底部形成有贮存润滑油的油积存部15。在低压空间12设置有固定涡旋件30和回旋涡旋件40作为压缩机构。固定涡旋件30与分隔板20相邻。回旋涡旋件40与固定涡旋件30啮合而形成压缩室50。在固定涡旋件30和回旋涡旋件40的下方设置有支承回旋涡旋件40的主轴承60。在主轴承60的大致中央部形成有轴承部61和凸台收纳部62。在主轴承60形成有回流管63,其一端向凸台收纳部62开口、另一端向主轴承60的下表面开口。另外,回流管63的一端也可以在主轴承60的上表面开口。此外,回流管63的另一端也可以在主轴承60的侧面开口。轴承部61轴支承旋转轴70。旋转轴70被轴承部61和副轴承16支承。在旋转轴70的上端形成有相对于旋转轴70的轴心偏心的偏心轴71。在旋转轴70的内部形成有使润滑油通过的油路72。在旋转轴70的下端设置有润滑油的吸入口73。在吸入口73的上部形成有叶片(paddle)74。油路72与吸入口73、叶片74连通,形成于旋转轴70的轴向上。油路72具有向轴承部61供油的供油口75、向副轴承16供油的供油口76、向凸台收纳部62供油的供油口77。电动构件80包括:固定于密闭容器10的定子81;和配置于该定子81的内侧的转子82。转子82固定于旋转轴70。在旋转轴70,在转子82的上方和下方安装有平衡配重17a、17b。平衡配重17a和平衡配重17b配置于错开180°的位置。用由平衡配重17a、17b产生的离心力和通过回旋涡旋件40的公转运动产生的离心力来取平衡。另外,平衡配重17a、17b也可以固定于转子82。自转抑制部件(十字滑环)90防止回旋涡旋件40的自转。回旋涡旋件40经由自转抑制部件90支承于固定涡旋件30。由此,回旋涡旋件40相对于固定涡旋件30不自转地进行回旋运动。柱状部件100阻止固定涡旋件30的旋转和半径方向上的移动,允许固定涡旋件30在轴向上的移动。固定涡旋件30通过柱状部件100由主轴承60支承,在分隔板20与主轴承60之间能够沿轴向移动。固定涡旋件30、回旋涡旋件40、电动构件80、自转抑制部件90和主轴承60配置于低压空间12,固定涡旋件30和回旋涡旋件40配置于分隔板20与主轴承60之间。通过电动构件80的驱动,旋转轴70和偏心轴71与转子82一起旋转。回旋涡旋件40在自转抑制部件90的作用下不自转地回旋运动,在压缩室50内制冷剂被压缩。制冷剂从制冷剂吸入管13被导入到低压空间12。位于回旋涡旋件40外周的低压空间12内的制冷剂被引导至压缩室50。制冷剂在压缩室50被压缩之后,经由高压空间11,从制冷剂排出管14排出。通过旋转轴70的旋转,贮存于油积存部15的润滑油从吸入口73进入油路72,沿着该油路72的叶片74被汲取至上方。被汲取上来的润滑油从各供油口75、76、77供给至轴承部61、副轴承16和凸台收纳部62。被汲取至凸台收纳部62的润滑油被引导至主轴承60与回旋涡旋件40的滑动面,并且通过回流管63排出后重新返回油积存部15。图2(a)是表示本实施方式的密闭型涡旋式压缩机的回旋涡旋件的侧视图,图2(b)是该图(a)的X-X线截面图。回旋涡旋件40包括:圆板状的回旋涡旋件端板41;立设于该回旋涡旋件端板41的上表面的涡旋状的回旋涡旋齿42;和形成于涡旋件端板41的下表面大致中央的圆筒状的凸台43。回旋涡旋齿42的内壁和外壁的厚度形成为从回旋涡旋齿42的涡旋始端42a至末端42b逐渐变薄。这样,通过使回旋涡旋齿42直至末端42b逐渐变薄,能够增大吸入气体的封闭容积,并且由于能够使回旋涡旋齿42轻量化,所以能够减小回旋涡旋齿42的回旋所产生的离心力。在图2(b)中,用粗实线表示回旋涡旋件端板41的形成有回旋涡旋齿42的端面侧的边缘部44。在边缘部44形成有凸部44a。凸部44a设置在末端42b附近。在回旋涡旋件端板41形成有一对第1键槽91。图3是表示本实施方式的密闭型涡旋式压缩机的固定涡旋件的底视图,图4是从底面观察该固定涡旋件的立体图,图5是从上面观察该固定涡旋件的立体图。固定涡旋件30包括:圆板状的固定涡旋件端板31;立设于该固定涡旋件端板31的下表面的涡旋状的固定涡旋齿32;以包围该固定涡旋齿32的周围的方式立设的周壁33;和设置于该周壁33的周围的凸缘34。固定涡旋齿32的内壁和外壁的厚度形成为从固定涡旋齿32的涡旋始端32a至末端32b逐渐变薄。这里的末端32b是由内壁和外壁形成固定涡旋齿32的部分,固定涡旋齿32从末端32b至内壁最外周部32c为止还在内壁延长340°左右。这样,通过使固定涡旋齿32直至末端32b逐渐变薄,能够增大吸入气体的封闭容积,并且由于能够使固定涡旋齿32轻量化,所以能够减小固定涡旋齿32的回旋所产生的离心力。在固定涡旋件端板31的大致中心部形成有第1排出端口35。此外,在固定涡旋件端板31形成有旁通端口36和中压端口37。旁通端口36在第1排出端口35附近位于压缩快要完成时的高压压力区域。中压端口37位于压缩中途的中间压力区域。固定涡旋件端板31突出到比凸缘34靠上方的位置。在固定涡旋件30的周壁33和凸缘34形成有用于将制冷剂取入到压缩室50的吸入部38。在凸缘34形成有第2键槽92。此外,在凸缘34形成有供柱状部件100的上端部插入的涡旋件侧凹部101。如图5所示,在固定涡旋件30的上表面(分隔板20一侧的面),在中央形成有凸台部39。在凸台部39,排出空间30H由凹部形成,第1排出端口35和旁通端口36形成于该排出空间30H。此外,在固定涡旋件30的上表面,环状的凹部形成于周壁33与凸台部39之间。由该环状的凹部形成比排出空间30H的压力低且高于低压空间12的压力的中压空间30M。在中压空间30M形成有中压端口37。中压端口37以比回旋涡旋齿42的内壁和外壁的厚度小的直径构成。通过使中压端口37的直径小于回旋涡旋齿42的内壁和外壁的厚度,能够防止形成于回旋涡旋齿42的内壁侧的压缩室50和形成于回旋涡旋齿42的外壁侧的压缩室50的连通。在中压空间30M设置能够封闭中压端口37的中压单向阀111和中压单向阀挡112。中压单向阀111通过使用簧片阀能够降低高度。此外,中压单向阀111也能够由球阀和弹簧构成。在排出空间30H设置有自由封闭旁通端口36的旁通单向阀121和旁通单向阀挡122。旁通单向阀121通过使用簧片阀型单向阀能够降低高度。此外,旁通单向阀121通过使用成形为V字形的簧片阀型单向阀,用1个簧片阀就能够封闭与形成于回旋涡旋齿42的外壁侧的压缩室50连通的旁通端口36A、以及与形成于回旋涡旋齿42的内壁侧的压缩室50连通的旁通端口36B。另外,下面对图2所示的回旋涡旋件40的回旋涡旋齿42和图3所示的固定涡旋件30的固定涡旋齿32的形状进行说明。在设基础圆半径为a、渐开角为θ、回旋半径为ε、B和n为系数的情况下,该固定涡旋齿32和回旋涡旋齿42的内外壁曲线例如由下述式表示,并且,系数B满足B>0。xo=a·cosθ+(a·θ-B·θn)·sinθ(外壁X坐标)yo=a·sinθ-(a·θ-B·θn)·cosθ(外壁Y坐标)xi=a·cosθ+(a·(θ-π)-B·(θ-π)n+ε)·sinθ(内壁X坐标)yi=a·sinθ-(a·(θ-π)-B·(θ-π)n+ε)·cosθ(内壁Y坐标)根据这样的结构,能够减小固定涡旋齿32和回旋涡旋齿42的涡旋末端厚度,所以能够使固定涡旋件30和回旋涡旋件40轻量化。特别是,由于回旋涡旋件40因轻量化而产生的回旋驱动时的离心力下降的效果,所以能够减轻轴承部61的负荷。进而,由于能够实现设置于旋转轴70的平衡配重17a、17b的小型化,所以能够提高设计自由度。此外,由于能够将渐开角设计得比现有的涡旋齿形状的渐开角大,所以能够增大压缩比和容积。由此,能够进一步使涡旋式压缩机高效率化、小型化。进而,在本实施方式的涡旋式压缩机中,不需要为了通过排出空间30H的压力来确保固定涡旋件30和回旋涡旋件40的密闭性而在固定涡旋齿32和回旋涡旋齿42前端设置片密封件。因此,没有因设置片密封件而导致的对固定涡旋齿32和回旋涡旋齿42的薄厚的限制,所以能够使固定涡旋齿32和回旋涡旋齿42变薄。图6是表示本实施方式的密闭型涡旋式压缩机的主轴承的立体图。轴承部61和凸台收纳部62形成于主轴承60的大致中央。在主轴承60的外周部形成有供柱状部件100的下端部插入的轴承侧凹部102。轴承侧凹部102的底面优选与回流管63连通。在这种情况下,由回流管63向轴承侧凹部102供给润滑油,能够提高柱状部件100与涡旋件侧凹部101的嵌合、以及柱状部件100与轴承侧凹部102的嵌合的可靠性。图7是表示本实施方式的密闭型涡旋式压缩机的自转抑制部件的顶视图。在自转抑制部件(十字滑环)90形成有第1键93和第2键94。第1键93与回旋涡旋件40的第1键槽91卡合,第2键94与固定涡旋件30的第2键槽92卡合。因此,回旋涡旋件40能够相对于固定涡旋件30不自转地进行回旋运动。此外,如图1所示,在旋转轴70的轴向上从上方按顺序配置有固定涡旋件30、回旋涡旋件40、十字滑环90。由于按固定涡旋件30、回旋涡旋件40、十字滑环90的顺序配置,所以十字滑环90的第1键93和第2键94形成于环部95的同一平面上。因此,在加工十字滑环90时,能够从同一方向加工第1键93和第2键94,能够减少从加工装置装卸十字滑环90的次数,所以能够获得提高加工精度和削减加工费的效果。此外,关于十字滑环90,将连结一对第1键93彼此的中心的第1假想线与连结一对第2键94彼此的中心的第2假想线的假想交点O’相对于第2假想线的中点O(第2键94的半径方向最端部的中点)偏离距离L。通过采用这样的结构,如图2所示能够使回旋涡旋件40的第1键槽91从回旋涡旋件端板41的中心偏离,所以能够扩大第1键槽91与回旋涡旋齿42的距离。其结果,能够增加从回旋涡旋件端板41中心至回旋涡旋齿42的末端42b的距离,所以能够增大回旋涡旋齿42的的渐开角。因此,能够容易增大压缩比和容积,进一步使涡旋式压缩机高效率化、小型化。图8是表示本实施方式的密闭型涡旋式压缩机的分隔板和固定涡旋件的主要部分截面图。在分隔板20的中心部形成有第2排出端口21。在第2排出端口21设置有排出单向阀131和排出单向阀挡132。在分隔板20与固定涡旋件30之间形成有与第1排出端口35连通的排出空间30H。在第1排出端口35与排出空间30H之间没有设置单向阀。第2排出端口21将排出空间30H与高压空间11连通。排出单向阀131封闭第2排出端口21。根据本实施方式,通过对形成于分隔板20与固定涡旋件30之间的排出空间30H施加高压压力,将固定涡旋件30按压于回旋涡旋件40,所以能够消除固定涡旋件30与回旋涡旋件40的间隙,能够进行高效率的运转。由于对排出空间30H施加高压压力,所以重要的是能够尽可能地缩小排出空间30H的轴向投影面积,防止固定涡旋件30对回旋涡旋件40的过度按压,从而提高可靠性。然而,如果缩小排出空间30H的轴向投影面积,则难以在第1排出端口35和旁通端口36两者配置单向阀。特别是,在将第1排出端口35的单向阀和旁通端口36的单向阀配置于同一平面上的情况下,必须增大排出空间30H的轴向投影面积。因此,在本实施方式中,在第1排出端口35不配置单向阀,而在第2排出端口21配置有排出单向阀131。由此,能够缩小排出空间30H的轴向投影面积,能够防止将固定涡旋件30过度地按压于回旋涡旋件40。此外,根据本实施方式,另外由旁通端口36而不是第1排出端口35将压缩室50与排出空间30H连通,并且在旁通端口36设置旁通单向阀121,由此能够防止来自排出空间30H的制冷剂的逆流,并且能够在达到规定压力的时刻将其导向排出空间30H,所以能够在大运转范围内实现高效率。排出单向阀131的弹簧常数比旁通单向阀121的弹簧常数大。为了使排出单向阀131的弹簧常数比旁通单向阀121的弹簧常数大,例如使排出单向阀131的厚度构成得比旁通单向阀121的厚度厚。第2排出端口21的平均流路面积比第1排出端口35的平均流路面积大。由于通过了第1排出端口35的制冷剂和通过了旁通端口36的制冷剂流入第2排出端口21,所以通过使第2排出端口21的平均流路面积比第1排出端口35的平均流路面积大,能够降低排出压力的损失。此外,在第2排出端口21的排出空间30H一侧的端口入口设置倒角,通过在端口入口的端面形成倒角,能够降低排出压力的损失。本实施方式的密闭型涡旋式压缩机包括:在分隔板20与固定涡旋件30之间配置于排出空间30H的外周的呈环状的第1密封部件141;和在分隔板20与固定涡旋件30之间配置于第1密封部件141的外周的呈环状的第2密封部件142。对于第1密封部件141和第2密封部件142,例如作为氟树脂的聚四氟乙烯在密封性和组装性方面是适合的。此外,第1密封部件141和第2密封部件142通过在氟树脂中混合纤维材料来提高密封的可靠性。第1密封部件141和第2密封部件142被封闭部件150夹到分隔板20(第1密封部件141和第2密封部件142被夹在封闭部件150与分隔板20之间)。在封闭部件150通过使用铝材而能够进行分隔板20的铆接。在第1密封部件141与第2密封部件142之间形成有中压空间30M。中压空间30M通过中压端口37与位于压缩中途的中间压力区域的压缩室50连通,所以施加比排出空间30H的压力低且比低压空间12的压力高的压力。根据本实施方式,在分隔板20与固定涡旋件30之间,在作为高压的排出空间30H以外形成中压空间30M,由此易于调整固定涡旋件30对回旋涡旋件40的按压力。此外,根据本实施方式,由第1密封部件141和第2密封部件142形成排出空间30H和中压空间30M,所以能够减少制冷剂从作为高压的排出空间30H向中压空间30M的泄漏、以及制冷剂从中压空间30M向低压空间12的泄漏。此外,根据本实施方式,第1密封部件141和第2密封部件142被封闭部件150夹到分隔板20,所以能够在组装了分隔板20、第1密封部件141、第2密封部件142和封闭部件150之后配置在密闭容器10内,所以能够实现较少的部件数量,并且易于组装涡旋式压缩机。此外,根据本实施方式,在固定涡旋件30形成有将压缩室50与中压空间30M连通的中压端口37,并设置有能够封闭中压端口37的中压单向阀111,所以在中压空间30M内通过利用压缩室50的压力而易于进行中压空间30M的压力的调整。此外,根据本实施方式,由于使中压单向阀111介于压缩室50与中压空间30M之间,所以能够将中压空间30M的压力维持恒定,能够稳定地进行固定涡旋件30对回旋涡旋件40的按压。图9是表示本实施方式的密闭型涡旋式压缩机的主要部分的部分截面立体图。如图9所示,图8中说明的封闭部件150由环状部件151和形成于环状部件151的一个面的多个突出部152构成。第1密封部件141的外周部被环状部件151的内周侧上表面和分隔板20所夹。此外,第2密封部件142的内周部被环状部件151的外周侧上表面和分隔板20所夹。环状部件151在夹着第1密封部件141和第2密封部件142的状态下安装于分隔板20。将封闭部件150安装于分隔板20,即,在将突出部152插入至形成于分隔板20的孔22中,将环状部件151按压于分隔板20的下表面的状态下,通过铆接突出部152的端部来固定。在将封闭部件150安装于分隔板20的状态下,第1密封部件141的内周部向环状部件151的内周侧突出,第2密封部件142的外周部向环状部件151的外周侧突出。然后,通过将安装有封闭部件150的分隔板20安装于密闭容器10内,第1密封部件141的内周部被固定涡旋件30的凸台部39的外周面按压,第2密封部件142的外周部被固定涡旋件30的周壁33的内周面按压。在主轴承60的外周的上表面形成有轴承侧凹部102,在固定涡旋件30的外周下表面形成有涡旋件侧凹部101。柱状部件100的下端部插入至轴承侧凹部102中,上端部插入至涡旋件侧凹部101中。柱状部件100与轴承侧凹部102和涡旋件侧凹部101中的至少一者可自由滑动,固定涡旋件30能够在分隔板20与主轴承60之间沿轴向移动。轴承侧凹部102的底面通过回流管63与主轴承60的外部相通,涡旋件侧凹部101的底部通过连通孔101a与固定涡旋件30的外部相通。根据本实施方式,通过涡旋件侧凹部101、轴承侧凹部102和柱状部件100能够阻止固定涡旋件30的旋转和半径方向的移动,能够允许固定涡旋件30向轴向的移动。另外,偏心轴71通过摆动衬瓦78和回旋轴承79,可回旋驱动地插入至凸台43中。根据这样的结构,通过运转时的回旋运动的离心力的作用,摆动衬瓦(swingbush)78作为离心方向的柔顺(Compliance)机构发挥功能,回旋涡旋件40在离心方向上位移,由此回旋涡旋件40被固定涡旋件30按压,由此能够使回旋涡旋齿42和固定涡旋齿32之间的间隙最小化,减少制冷剂从该间隙泄漏。此外,由于具有旁通端口36,所以为了与压缩室50内的气体力相抵所需的离心方向上的力减少与使过度压缩下降对应的量。因此,能够设计成在大运转范围内回旋涡旋件40总是被固定涡旋件30按压。如果设计成假设即使压缩负荷较大的过度压缩的条件下回旋涡旋件40也被固定涡旋件30按压,则在压缩负荷较低的条件下回旋涡旋件40被固定涡旋件30过度地按压,所以导致机械损失的增加和可靠性的下降。然而,由于通过设置旁通端口36能够抑制过度压缩,所以能够缩小压缩负荷较大的条件下的离心方向上的力与压缩负荷较低的条件下的离心方向上的力之差,能够在大的运转范围内得到高效率和高可靠性。图10是表示本实施方式的密闭型涡旋式压缩机的各旋转角度下的回旋涡旋件和固定涡旋件的相对位置的组合图。压缩室50A由回旋涡旋件40的回旋涡旋齿42的外壁和固定涡旋件30的固定涡旋齿32的内壁形成。压缩室50B由回旋涡旋件40的回旋涡旋齿42的内壁和固定涡旋件30的固定涡旋齿32的外壁形成。图10(a)表示压缩室50A刚吸入封闭完成之后的状态。图10(b)表示从图10(a)进行了90°旋转之后的状态,图10(c)表示从图10(b)进行了90°旋转之后的状态,图10(d)表示从图10(c)进行了90°旋转之后的状态,从图10(d)进行了90°旋转之后返回至图10(a)的状态。图10(c)表示压缩室50B刚吸入封闭之后的状态。图10(a)中吸入封闭完成之后的压缩室50A如图10(b)、图10(c)、图10(d)所示,使容积减少并且向固定涡旋件30的中心移动,从进行了540°旋转之后的图10(c)至图10(d)为止与第1排出端口35连通。第1旁通端口36A,从图10(a)中吸入封闭完成之后的压缩室50A与第1排出端口35连通之前使压缩室50A与排出空间30H连通。因此,在压缩室50A内的压力成为将旁通单向阀121压上去的压力的情况下,在压缩室50A与第1排出端口35连通之前,压缩室50A内的制冷剂从第1旁通端口36A导出至排出空间30H。图10(c)中吸入封闭完成之后的压缩室50B如图10(d)、图10(a)、图10(b)所示,使容积减少并且向固定涡旋件30的中心移动,从进行了360°旋转之后的图10(c)至图10(d)为止与第1排出端口35连通。第2旁通端口36B,从图10(c)中吸入封闭完成之后的压缩室50B与第1排出端口35连通之前使压缩室50B与排出空间30H连通。因此,在压缩室50B内的压力成为将旁通单向阀121压上去的压力的情况下,在压缩室50B与第1排出端口35连通之前,压缩室50B内的制冷剂从第2旁通端口36B导出至排出空间30H。这样,另外由第1旁通端口36A、第2旁通端口36B而不是第1排出端口35将压缩室50A、50B与排出空间30H连通,并且在第1旁通端口36A、第2旁通端口36B设置旁通单向阀121,能够防止来自排出空间30H的制冷剂的逆流,并且能够在达到规定压力的时刻将其导向排出空间30H,所以能够在大运转范围内实现高效率。如图10(a)~(d)所示,中压端口37设置于与图10(a)中吸入封闭完成之后的压缩室50A、或图10(c)中吸入封闭完成之后的压缩室50B连通的位置。如图10(c)所示,在从10(a)旋转了180°之后的位置,回旋涡旋件40离吸入部38最远。在该位置上,回旋涡旋件40的边缘部44和固定涡旋件30的内壁最外周部32c最近。然而,根据本实施方式的涡旋式压缩机,以使回旋涡旋件40的回旋涡旋件端板41的部分外径向外径外侧扩展的方式设置凸部44a,由此在回旋涡旋件40回旋驱动的期间回旋涡旋件40的边缘部44从旋转轴70方向观察总是覆盖固定涡旋件30的内壁最外周部32c。即,回旋涡旋件40的回旋涡旋件端板41的边缘部44的轮廓线能够总是在外侧超越固定涡旋件30的内壁最外周部32c。因此,即使在运转时产生回旋涡旋件40的挠曲或倒伏的情况下,固定涡旋件30的内壁最外周部32c和回旋涡旋件40的边缘部44也不会偏离地抵接,而能够总是保持稳定的驱动状态,能够实现较高的可靠性。此外,凸部44a设置于与吸入部38在轴向上重叠的位置,由此能够使所需的凸部44a的区域为最小,所以能够获得进一步轻量化的效果。在本实施方式中,通过以使回旋涡旋件40的回旋涡旋件端板41的部分外径向外径外侧扩展的方式设置凸部44a,在回旋涡旋件40回旋驱动的期间回旋涡旋件40的边缘部44从旋转轴70方向观察能够总是覆盖固定涡旋件30的内壁最外周部32c。另外,在上述的结构以外,能够列举下述结构:缩小固定涡旋件30的内壁涡旋末端的渐开角,使内壁在固定涡旋件30的半径方向上更靠近端板中央部的位置结束。然而,在这种结构中,由于封闭容积减少,所以为了实现同等的容积而将固定涡旋齿32、回旋涡旋齿42的高度设计得较大。因此,可能产生因回旋涡旋齿42和固定涡旋齿32增高导致的涡旋齿可靠性下降、抗颠覆能力下降、加工性下降等。此外,由于压缩比也下降,所以容易引起压缩不足,也可能导致压缩机的效率下降。此外,即使增大回旋涡旋件40的回旋涡旋件端板41的外径整周,在回旋涡旋件40回旋驱动的期间回旋涡旋件40的边缘部44从旋转轴70方向观察能够总是覆盖固定涡旋件30的内壁最外周部32c。然而,回旋涡旋件40的回旋涡旋件端板41的最大外径仅在回旋涡旋件端板41与由主轴承60支承固定涡旋件30的柱状部件100不接触的范围内设计,为了增大回旋涡旋件40的回旋涡旋件端板41的外径,需要使柱状部件100变小。因此,可能导致在主轴承60支承固定涡旋件30的柱状部件100的刚性下降。基于这样的理由,通过本实施方式的涡旋式压缩机的结构,能够实现高可靠性和高效率。此外,在本实施方式中,通过将固定涡旋件30的固定涡旋齿32的内壁形成至回旋涡旋件40的回旋涡旋齿42的末端32b附近,使由固定涡旋齿32的内壁和回旋涡旋齿42的外壁形成的压缩室50A的封闭容积、与由固定涡旋齿32的外壁和回旋涡旋齿42的内壁形成的压缩室50B的封闭容积不同。根据本实施方式,通过确保最大限度的吸入气体的封闭容积,能够提高压缩比,所以能够使固定涡旋齿32和回旋涡旋齿42的高度下降。因此,固定涡旋件30能够在分隔板20与主轴承60之间沿轴向移动,通过排出空间30H的压力将固定涡旋件30按压于回旋涡旋件40,来确保固定涡旋件30与回旋涡旋件40的密闭性,在这样的涡旋式压缩机中,固定涡旋齿32和回旋涡旋齿42的高度较低的一方能够使固定涡旋件30稳定。此外,在本实施方式中,在吸入部38附近设置压缩室50A的吸入封闭位置和压缩室50B的吸入封闭位置,由此能够使吸入制冷剂通路最短化,能够降低受热损失。此外,如本实施方式那样,优选在吸入部38附近设置压缩室50A的吸入封闭位置和压缩室50B的吸入封闭位置的情况下,以使固定涡旋齿32和回旋涡旋齿42的高度在吸入部38一侧较高、随着远离吸入部38而逐渐降低的方式设置倾斜面。这样,通过在固定涡旋齿32和回旋涡旋齿42设置倾斜面,能够根据运转时的温度差实现间隙的最优化。固定涡旋齿32的倾斜量大于回旋涡旋齿42的倾斜量。固定涡旋齿32的温度比回旋涡旋齿42的温度高,所以通过使固定涡旋齿32的倾斜量大于回旋涡旋齿42的倾斜量,能够根据运转时的温度差实现间隙的最优化。另外,在固定涡旋齿32和回旋涡旋齿42设置倾斜面的情况下,在齿的最外周部形成至少1个平坦部在齿高度的管理方面是有效的。通过使固定涡旋齿32的最大高度比回旋涡旋齿42的最大高度大,能够防止回旋涡旋件40的一端接触。此外,在本实施方式的涡旋式压缩机中,至固定涡旋齿32和回旋涡旋齿42的涡旋末端,固定涡旋齿32和回旋涡旋齿42的厚度减小,所以固定涡旋齿32和回旋涡旋齿42的刚性下降,而通过在本实施方式这样的回旋涡旋件40形成凸部44a,能够防止回旋涡旋件40的边缘部44与固定涡旋件30的内壁最外周部32c的一端接触。因此,也不会因一端接触产生的异常振动等使固定涡旋齿32和回旋涡旋齿42的可靠性下降,其结果,能够兼顾高性能和高可靠性。在本实施方式中,优选柱状部件100通过过盈配合或过渡配合插入到轴承侧凹部102和涡旋件侧凹部101中的某一个中。将柱状部件100通过过盈配合或过渡配合插入到轴承侧凹部102和涡旋件侧凹部101中的某一个中,由此不需要用螺栓等固定柱状部件100,能够削减部件数量,减少成本。在将柱状部件100通过过盈配合或过渡配合插入到轴承侧凹部102中的情况下,能够从上方将涡旋件侧凹部101插入于被插入到轴承侧凹部102的柱状部件100,所以组装变得容易。此外,在本实施方式的涡旋式压缩机中,优选具有至少2个以上的柱状部件100。通过2个以上的柱状部件100,阻止固定涡旋件30的旋转和半径方向上的移动,限制主轴承60与固定涡旋件30的位置关系,由此不需要另外设置位置限制用部件,能够减少成本。此外,在本实施方式的涡旋式压缩机中,在将柱状部件100通过间隙配合插入到涡旋件侧凹部101中的情况下,在涡旋件侧凹部101设置连通孔101a,由此能够将润滑油或包含润滑油的制冷剂供给到涡旋件侧凹部101与柱状部件100之间,减少涡旋件侧凹部101或柱状部件100的磨损。此外,在本实施方式的涡旋式压缩机中,在将柱状部件100过盈配合或过渡配合插入到涡旋件侧凹部101中、通过间隙配合插入到轴承侧凹部102中的情况下,在轴承侧凹部102设置与密闭容器10内连通的连通孔102a,由此能够在抽真空时将轴承侧凹部102内的空气可靠地抽掉,能够提高可靠性。另外,在本实施方式的涡旋式压缩机中,如图9所示,连通孔102a经由回流管63与密闭容器10内连通。此外,在柱状部件100设置有没有插入到涡旋件侧凹部101和轴承侧凹部102中的任一个中的区域100x。通过设置柱状部件100的区域100x,在将柱状部件100通过间隙配合插入到涡旋件侧凹部101中的情况下,能够从区域100x将润滑油或包含润滑油的制冷剂供给到柱状部件100与涡旋件侧凹部101之间。此外,在将柱状部件100通过间隙配合插入到轴承侧凹部102中的情况下,能够从区域100x将润滑油或包含润滑油的制冷剂供给到柱状部件100与轴承侧凹部102之间。因此,能够减少柱状部件100与涡旋件侧凹部101或轴承侧凹部102的磨损。此外,由分隔板20限制固定涡旋件30向轴向的可动区域。由此,由于固定涡旋件30在向轴向移动时与分隔板20接触,所以第1密封部件141的端面和第2密封部件142的端面与固定涡旋件30接触、发生变形。由此,不会导致密封性的下降,所以能够提高涡旋式压缩机的可靠性。图11是表示本发明的第2实施方式的密闭型涡旋式压缩机的主要部分的部分截面立体图。本发明的第2实施方式与本发明的第1实施方式的不同之处仅在于以下说明的部分,其他结构与本发明的第1实施方式相同。另外,本发明不限定于以下的实施方式。在图11中,在轴承侧凹部102的柱状部件100的插入部设置有销孔,在销孔内设置有柱状部件100的防脱落销100a。由此,能够防止柱状部件100脱落,能够提高可靠性。由于防脱落销100a与密闭容器10的内壁接触,所以防脱落销100a自身不会脱落。产业上的可利用性本发明在能够利用于热水器、热水供暖装置、空气调节装置等的电气产品的制冷循环装置的压缩机中是有用的。附图标记说明10密闭容器11高压空间12低压空间20分隔板21第2排出端口30固定涡旋件30H排出空间30M中压空间31固定涡旋件端板32固定涡旋齿33周壁34凸缘35第1排出端口36旁通端口37中压端口38吸入部39凸台部40回旋涡旋件41回旋涡旋件端板42回旋涡旋齿43凸台44边缘部44a凸部50压缩室60主轴承61轴承部62凸台收纳部63回流管70旋转轴71偏心轴72油路73吸入口74叶片75供油口80电动构件90自转抑制部件(十字滑环)100柱状部件100a防脱落销101涡旋件侧凹部102轴承侧凹部111中压单向阀121旁通单向阀131排出单向阀141第1密封部件142第2密封部件150封闭部件