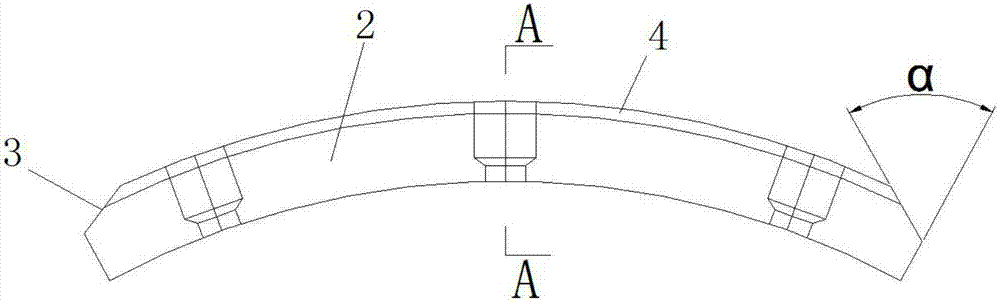
本实用新型涉及制动器辅助设备
技术领域:
,具体涉及一种汽车用鼓式制动器的制动蹄结构。
背景技术:
:整车制造下线时需要试车,试车时其中一项是测试汽车在制动时是否出现跑偏。由于新车处于磨合初期,制动时摩擦片与制动鼓接触面积不均匀,经常出现车辆跑偏问题,需要对制动器的摩擦片进行返工处理,这就造成了新车不能及时下线,影响效率。经过调查发现,若摩擦片与制动鼓贴合面积不好,易出现制动蹄上下蹄铁与制动鼓距离不一致等情况。新车装车时,由于各部件尺寸精度、制动间隙、装配配合等各方面原因,部分车辆会出现制动器系统各部件配合相对较差情况:如汽车制动时摩擦片仅有某一侧边与制动鼓接触,另一边没有接触;或者摩擦片与制动鼓接触位置不好,影响制动力灵敏性,导致车辆两侧的车轮制动力的不一致,车辆制动时,制动接触面好的其中一轮已经完全制动,基础面差,制动差的另一轮还在继续向前滑行,于是车辆向一个方向侧滑,出现跑偏并影响制动效果。出现上述情况时,汽车厂一般处理方式是将制动器打开,对摩擦片两侧边处理,使摩擦片尽量中部接触制动鼓,避免再次跑偏。这种处理方式耽误了工期,影响了生产效率。因此,有必要对现有技术进行改进。技术实现要素:本实用新型的目的在于,针对现有技术的不足,提供一种贴合度高、避免车辆跑偏的汽车用鼓式制动器的制动蹄结构。本实用新型采用的技术方案为:一种汽车用鼓式制动器的制动蹄结构,包括制动蹄和摩擦片,所述摩擦片固定安装于制动蹄上,摩擦片的内周面与制动蹄的外周面紧贴,摩擦片的外周面形成制动面,制动面可与制动器的制动鼓内周面贴紧;所述摩擦片的两端端面与制动面之间均分别设有过渡的第一倒角面。按上述方案,所述摩擦片的两侧侧面与制动面之间均分别设有过渡的第二倒角面,第一倒角面的两端分别与第二倒角面相交,第二倒角面的上沿和下沿均为与摩擦片的外周面轮廓相对应的弧线。按上述方案,第一倒角面与摩擦片端面的夹角α为25°~60°。按上述方案,两个第二倒角面对称布置。按上述方案,第二倒角面与摩擦片侧面的夹角β为70°~86°。按上述方案,所述第一倒角面的下边与摩擦片内周面的距离为摩擦片高度的按上述方案,所述第二倒角面的下边与摩擦片内周面的距离为摩擦片高度的按上述方案,所述摩擦片通过铆钉固定安装于制动蹄上。本实用新型的有益效果为:(1)本实用新型摩擦片的两端端面及两侧侧面均设有与制动面过渡的倒角面,制动时,摩擦片与制动鼓的接触面集中在摩擦片的中间部位(非倒角面),不会出现摩擦片某一侧边与制动鼓接触,而另一侧边不与制动鼓接触的情况,大大减少了制动不均匀现象的发生,解决了汽车制动跑偏的问题,继而降低了返工率,减少了汽车下线的磨合时间,提高了生产效率;(2)摩擦片倒角面的倒角较小,可以较快磨合到位,实验室模拟整车惯性台架试验制动约2000次,相当于汽车行驶约2000公里就能够将倒角磨损完毕,即汽车在自磨合阶段就可以,不影响制动鼓使用。附图说明图1为本实用新型一个具体实施例的结构示意图。图2为图1中摩擦片的主视图。图3为图1中摩擦片的俯视图。图4为图2中的A-A剖视图。图5为实施例的主视图。图6为实施例的俯视图。图7为实施例的B-B剖视图。其中:1、制动蹄;2、摩擦片;3、第一倒角面;4、第二倒角面;5、铆钉;6、制动面。具体实施方式为了更好地理解本实用新型,下面结合附图和具体实施例对本实用新型作进一步地描述。如图1所示的一种汽车用鼓式制动器的制动蹄结构,包括制动蹄1和摩擦片2,所述摩擦片2通过铆钉5固定安装于制动蹄1上,摩擦片2的内周面与制动蹄1的外周面紧贴,摩擦片2的外周面形成制动面6,制动面6可与制动器的制动鼓内周面贴紧。如图2~4所示,所述摩擦片2的两端端面(沿长度方向上的两端端面)与制动面6之间均分别设有过渡的第一倒角面3;所述摩擦片2的两侧侧面(沿宽度方向上的两侧侧面)与制动面6之间均分别设有过渡的第二倒角面4,第一倒角面3的两端分别与第二倒角面4相交,第二倒角面4的上沿和下沿均为与摩擦片2的外周面轮廓相对应的弧线。优选地,所述第一倒角面3与摩擦片2端面的夹角α为25°~60°。优选地,两个第二倒角面4对称布置,第二倒角面4与摩擦片2侧面的夹角β为70°~86°。优选地,所述第一倒角面3的下边与摩擦片2内周面的距离为摩擦片2高度的优选地,所述第二倒角面2的下边与摩擦片2内周面的距离为摩擦片2高度的摩擦片2沿弧面双侧边倒角后,摩擦片2与制动鼓的接触面集中于摩擦片2制动面6的中间部位,不会出现摩擦片2某一侧边与制动鼓接触、另一侧边未与制动鼓接触的情况,解决了摩擦片2侧边接触不平现象;同时,第一倒角面3和第二倒角面4的倒角较小,可以较快磨合到位,制动不均匀现象大幅度减少。根据某试车场的数据分析,该设计能够解决绝大部分汽车下线跑偏问题,将目前的汽车新车下线率由20%左右下降到5%以下。以下以宽度为180mm、厚度为18mm的摩擦片2为例进行说明。如图5~图7所示,自摩擦片2的底部11mm高度的端面开始形成第一倒角面3,第一倒角面3与摩擦片2的制动面6交汇形成第一倒角面3的上沿;自摩擦片2的底部16.5mm高度的侧面开始形成第二倒角面4,第二倒角面4与摩擦片2的制动面交汇形成第二倒角面4的上沿,第二倒角面4的宽度为20mm。以下对本实施例所述带有倒角面的摩擦片2进行试验,验证该摩擦片2的制动效果和磨损。1、进行惯性台架试验,验证制动力矩:常规摩擦片(无倒角面)与本实施例所述带有倒角面的摩擦片2两者制动力矩如表1所示。表1常规摩擦片与本实施例所述摩擦片的制动力矩从表1中可看出,带倒角面的摩擦片2与常规摩擦片相比,其制动力矩变化很小,能够达到制动要求。2、在一定制动次数的情况下,制动鼓和摩擦片2的磨损:实验室模拟整车惯性台架试验制动约3000次,即相当于汽车行驶约2000公里就能够将摩擦片2的倒角磨损完毕;倒角面的倾斜度较小时,通过车辆的自磨合可将倒角磨去,不影响摩擦片2和制动鼓的使用。本实施例所述带有倒角面的摩擦片2制动约3000次的磨损情况如表2所示(表2用于说明带倒角的摩擦片在使用时不存在接触面积不够及制动力不够等问题):带倒角面的摩擦片2及制动鼓表面的磨损如表3所示,采用3D坐标仪测量制动鼓的磨损。表2带倒角面的摩擦片的磨损表3带倒角面的摩擦片及制动鼓表面的磨损制动鼓的磨损位置实测制动鼓半径mm鼓边沿未磨到的原始位204.985鼓外沿相对摩擦片倒角位205.05鼓中部相对无倒角位205.162鼓内沿相对摩擦片倒角位205.12相对原始鼓的最大磨损(半径mm)0.177中部和两边最大磨损差异(半径mm)0.112从表2和表3可知,实验室模拟整车惯性台架试验制动约3000次,能够通过整车的自磨合较快的将倒角磨去,而此时与带倒角面的摩擦片2配合的制动鼓表面侧边部位光滑,没有出现印痕台阶,不影响制动鼓的使用。最后应说明的是,以上仅为本实用新型的优选实施例而已,并不用于限制本实用新型,尽管参照实施例对本实用新型进行了详细的说明,对于本领域的技术人员来说,其依然可以对前述各实施例所记载的技术方案进行修改,或者对其中部分技术特征进行等同替换,但是凡在本实用新型的精神和原则之内,所作的任何修改、等同替换、改进等,均应包含在本实用新型的保护范围之内。当前第1页1 2 3