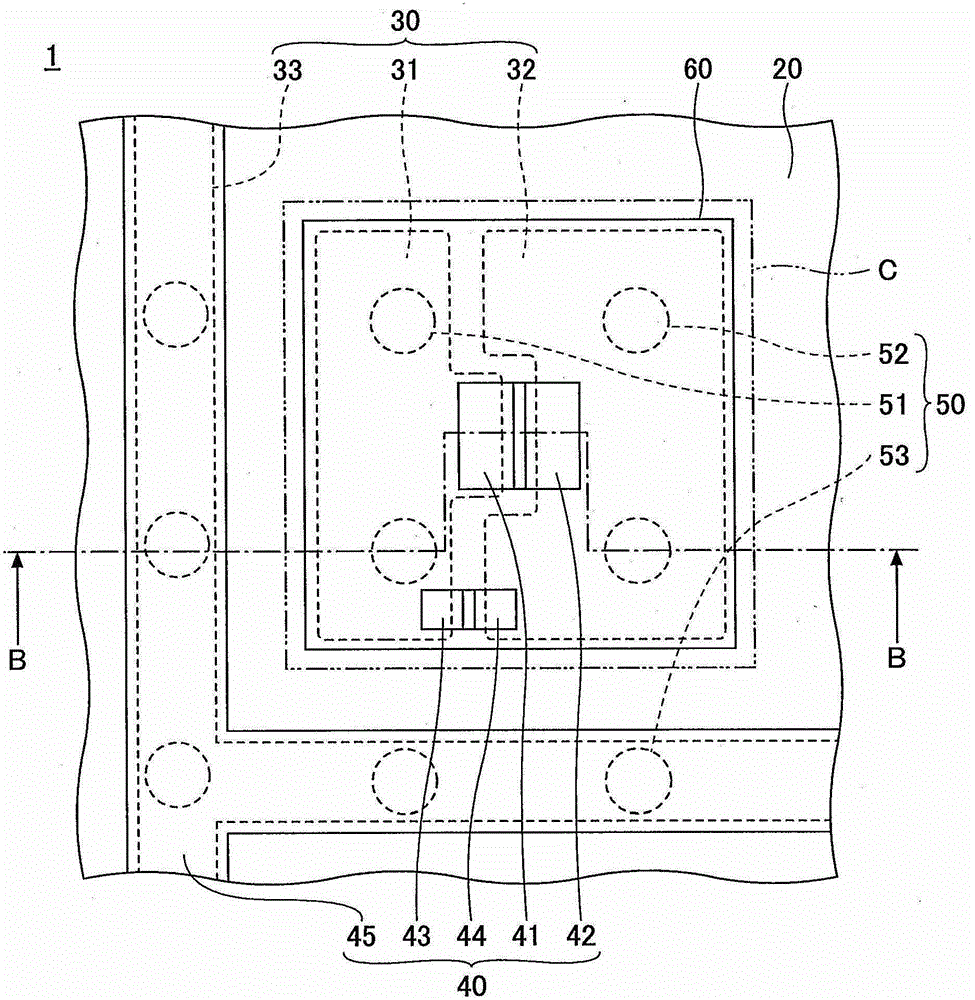
本文讨论的实施例涉及一种能够在其上安装发光元件的发光元件安装封装、发光元件安装封装的制造方法、以及通过将发光元件安装在发光元件安装封装上形成的发光元件封装。
背景技术:近些年来,提出了一种具有作为安装在发光元件封装上的发光元件的发光二极管(在下文中,称为“LED”)的发光元件封装。例如,所提出的发光元件封装等由多组LED形成,多组LED的每一组由安装在柔性基板的上表面的布线图案上的三个LED组成,并且多个散热器板通过接合剂(bond)而设置,以便覆盖与多组LED的安装位置对应的部分,如日本特开专利公开第2003-92011号所公开的。然而,上述发光元件封装通过在与该多组LED的安装位置对应的部分设置散热器板来散发由该多组LED发出的热量。因为从该多组LED到散热板的散热路径不充足,所以由该多组LED发出的热量不能被有效地传递到散热器板。
技术实现要素:考虑到以上几点,本发明的目的是要提供一种具有散热路径(其能够有效地将由发光元件产生的热量传递到设置在外部的散热器部)的发光元件安装封装、发光元件安装封装的制造方法、以及通过将发光元件安装在发光元件安装封装上形成的发光元件封装。根据实施例的一个方案,一种发光元件安装封装包括:第一布线,形成第一发光元件安装部,该第一发光元件安装部被设置在基板的一个表面上以安装发光元件;以及第一贯通布线,具有一端和另一端,该一端电连接至第一发光元件安装部以便能够进行热传递,以及该另一端从基板的另一个表面突出。根据实施例的另一个方案,一种发光元件封装包括:根据上述的发光元件安装封装;以及所述发光元件,安装在所述发光元件安装封装的相应的第一发光元件安装部、相应的第二发光元件安装部或相应的发光元件安装部。根据实施例的又一个方案,一种发光元件安装封装的制造方法包括:形成贯穿基板的通孔;在所述基板的一个表面上设置金属层;在所述通孔内部形成贯通布线,所述贯通布线包括一端和另一端,所述一端与所述金属层电连接,所述另一端从所述基板的另一个表面突出以形成连接端子;图案化所述金属层以形成包括发光元件安装部的布线并形成总线,发光元件将要安装在所述发光元件安装部上;以及使用包括所述总线的供电路径,通过电镀在所述发光元件安装部的表面上形成电镀膜。将凭借在所附权利要求中特别指出的元件和组合来实现和获得本发明的目的和优点。应当理解,前述的一般说明和下面的详细描述都是示例性和解释性的,并且不限制权利要求所要求保护的本发明。附图说明图1为第一实施例的发光元件安装封装的示例性平面图;图2A和图2B为示出图1的部分A的示例性放大图;图3为第一实施例的发光元件封装的示例性剖视图;图4A和图4B示出第一实施例的发光元件安装封装的示例性制造工艺;图5A至图5D示出第一实施例的发光元件安装封装的示例性制造工艺;图6A至图6D示出第一实施例的发光元件安装封装的示例性制造工艺;图7为第二实施例的发光元件安装封装的示例性剖视图;图8为第二实施例的发光元件封装的示例性剖视图;图9为第二实施例的变型实例的发光元件安装封装的示例性剖视图;图10为第二实施例的发光元件封装的示例性剖视图;图11为第三实施例的发光元件安装封装的示例性平面图;图12A和图12B为示出图11的部分A的示例性放大图;图13A和图13B示出第三实施例的发光元件安装封装的示例性制造工艺;图14A和图14B示出第三实施例的发光元件安装封装的示例性制造工艺;图15为第四实施例的发光元件安装封装的示例性平面图;图16A和图16B为示出图15的部分D的示例性放大图;图17为第四实施例的发光元件封装的示例性剖视图;图18A、图18B以及图18C示出第四实施例的发光元件安装封装的示例性制造工艺;图19为第四实施例的变型实例的发光元件安装封装的示例性剖视图;图20为第四实施例的变型实例1的发光元件封装的示例性剖视图;图21为第四实施例的变型实例2的发光元件安装封装的示例性剖视图;图22为第四实施例的变型实例2的发光元件封装的示例性剖视图;图23为第四实施例的变型实例3的发光元件安装封装的示例性平面图;图24为示出图23的部分D的示例性放大图;图25为第四实施例的变型实例3的发光元件封装的示例性剖视图;图26示出第四实施例的变型实例4的金属元件的示例性平面图;以及图27A和图27B示出悬挂部的其它示例性形状。具体实施方式将参考附图来说明本发明的优选实施例。其中相同的附图标记被附加于相同的部件,并省略对这些部件的重复说明。[a]第一实施例[第一实施例的发光元件安装封装的结构]将描述第一实施例的发光元件安装封装的结构。图1为第一实施例的发光元件安装封装的示例性平面图。图2A为图1的部分A的示例性放大平面图。图2B为沿图2A的线B-B的示例性剖视图。参照图1以及图2A和图2B,发光元件安装封装1包括:基板10;粘着层20;布线30(包括布线31和32以及总线33);电镀膜40(包括电镀膜41、42、43、44以及45);贯通布线50(包括贯通布线51、52以及53);以及绝缘层60。参照图2,由双点划线包围的区域C最终沿着该双点划线被切割,以便成为分离的发光元件安装封装的区域(在下文中,称为单独的封装区域C)。换句话说,发光元件安装封装1包括多个单独的封装区域C,每一个单独的封装区域C被形成以便安装一个发光元件。参照图1,发光元件安装封装1包括60个单独的封装区域C。然而,该数量不限于此数量。在发光元件安装封装1中,基板10为例如具有柔性的绝缘树脂膜。该绝缘树脂膜为例如由聚酰亚胺树脂构成的膜(聚酰亚胺带)、由环氧树脂构成的膜、由聚酯树脂构成的膜等。然而,基板10不限于具有柔性的绝缘树脂膜。例如,可以使用由阻燃剂4(FR4)的玻璃环氧树脂等构成的基板10。例如,基板10的厚度可以是大约50μm至75μm。粘着层20被接合至基板10的一个表面以将布线31和32以及总线33固定到基板10。粘着层20为例如由绝缘树脂构成的耐热性粘着剂(adhesionbond),例如,环氧树脂粘着剂或聚酰亚胺粘着剂。粘着层20的厚度为例如大约8μm至大约18μm。在基板10的两侧,以大体恒定的间隔沿预定方向连续地设置了多个齿孔(sprockethole)10x。当发光元件安装封装1被安装在用于安装发光元件的装置中以便使得发光元件被安装在发光元件安装封装1上时,齿孔10x为与链轮齿(其由电机等来驱动)啮合的通孔。可以确定沿与齿孔10x布置方向垂直的方向上基板10的宽度,以便与其上安装了发光元件安装封装1的装置对应。例如,基板10的宽度可以是大约40mm至大约90mm。另一方面,能够任意确定基板10的长度(齿孔10x的布置方向)。参照图1,单独的封装区域C的数量是10排。例如,如果具有柔性的绝缘树脂膜被用作基板10,则基板10可以进一步延长以便成为大约100排:其中呈带状的发光元件安装封装1被装在卷轴(reel)上运送。在基板10的一个端部的齿孔10x与基板10的另一个端部的齿孔10x之间,布置了表面被电镀膜45涂覆的总线33,以便包围所有单独的封装区域C,其中纵向及横向地布置总线33。总线33电连接至贯穿基板10和粘着层20的多个贯通布线53的一端。该多个贯通布线53的另一端通过从基板10的另一个表面突出而形成突出部。贯通布线53从基板10的另一个表面的突出量为例如大约20μm至大约50μm。总线33用来供应用于通过电镀在布线31和32上形成电镀膜40的电力。然而,总线33不直接连接至布线31和32。换句话说,在发光元件安装封装1内,总线33与形成发光元件安装部的布线31和32电独立。在后文描述使用总线33在布线30上形成电镀膜40的具体方法。在单独的封装区域C中,布线31和32经由粘着层20被设置在基板10的一个表面上。布线31电连接至贯穿基板10和粘着层20的多个贯通布线51的一端。布线32电连接至贯穿基板10和粘着层20的多个贯通布线52的一端。该多个贯通布线51和52的另一端通过从基板10的另一个表面突出而形成突出部。贯通布线51和52从基板10的另一个表面的突出量为例如大约20μm至大约50μm。两个贯通布线51连接至布线31。两个贯通布线52连接至布线32。如所描述的,从提高散热性能的视点来看,优选的是设置多个贯通布线51和52。然而,本实施例不限于此。为布线31和32的每一个设置至少一个贯通布线是足够的。然而,在单独的封装区域C在预定平面部分被切片并布置的情况下,从平衡的观点来看,优选为布线31和32的每一个设置两个或多个贯通布线51和52。例如,在单独的封装区域C的平面形状是矩形的情况下,贯通布线51和52(连接端子)被设置在单独的封装区域C的角部。如此,通过在将发光元件安装封装或发光元件封装安装在金属基板等上时设置贯通布线51和52,可以防止封装被倾斜地安装。为了方便起见,贯通布线51、52以及53被编上了不同的编号。然而,如后文描述的,贯通布线51、52以及53可以通过在相同的工艺中使用相同的材料来形成。在下文中,如果没有必要具体区分贯通布线51、52以及53,则贯通布线51、52以及53被通称为贯通布线50。另外,贯通布线51和52可以被称为第一贯通布线,贯通布线53可以被称为第二贯通布线。另外,贯通布线51和52的突出部可以被称为连接端子。贯通布线50的材料为例如铜(Cu)等。例如,贯通布线50的平面形状可以是圆形。这种情况下,其直径为例如大约0.5mm至1mm。然而,贯通布线50有助于电连接,并且还有助于散热。因此,如果要提高散热性能,则贯通布线50的直径可以是1mm或更大。贯通布线50的平面形状可以为例如椭圆形、矩形等。除区域C的一部分之外,由大体设置在单独的封装区域C的整个区域上的绝缘层60覆盖布线31和32。布线31和32的区域的该部分从绝缘层60暴露。电镀膜41、42、43以及44形成在布线31和32暴露于绝缘层60上的区域上。优选,设置绝缘层60以在相邻的单独封装区域C之间的边界界限(boundarydivision)暴露粘着层20的表面。通过设置绝缘层60,可以在每次发光元件安装封装1被切割成单独的封装区域C时防止绝缘层60外围的破裂或脱落。因此,能够防止绝缘层60的表面面积减小,从而防止绝缘层60的反射率的下降。另外,在这种情况下当发光元件安装封装1被切割成单独的封装区域C时,绝缘层60的外围被从基板10的外围向内安置。当绝缘层60等中没有破裂时,绝缘层60可以被设置在包括单独的封装区域C之间的边界界限的粘着层20的整个表面上。这种情况下,当发光元件安装封装1被切割成单独的封装区域C时,绝缘层60、基板10以及粘着层20的侧表面可以是大体平面的。为了方便起见,布线31、32以及33被编上了不同的编号。然而,如后文描述的,布线31、32以及33可以通过在相同的工艺中使用相同的材料来形成。当没有必要具体区分布线31和32以及总线33时,布线31和32以及总线33被通称为布线30。布线30的材料为例如铜(Cu)等。布线30的厚度可以是大约12μm至大约35μm。类似地,为了方便起见,电镀膜41、42、43、44以及45被编上了不同的编号。然而,如后文描述的,电镀膜41、42、43、44以及45可以通过在相同的工艺中使用相同的材料来形成。当没有必要具体区分电镀膜41、42、43、44以及45时,电镀膜41、42、43、44以及45被通称为电镀膜40。例如,电镀膜40由Ni或Ni合金/Au或Au合金膜、Ni或Ni合金/Pd或Pd合金/Au或Au合金膜、Ni或Ni合金/Pd或Pd合金/Ag或Ag合金/Au或Au合金膜、Ag或Ag合金膜、Ni或Ni合金/Ag或Ag合金膜、Ni或Ni合金/Pd或Pd合金/Ag或Ag合金膜等构成。在此,表达式“AA/BB”表示由AA构成的膜和由BB构成的膜以此顺序被叠置在对象部分上(当形成三个或多个膜时类似)。优选,电镀膜40中的Au或Au合金膜和Ag或Ag合金膜的厚度是0.1μm或更大。优选,电镀膜40中的Pd或Pd合金膜的厚度是0.005μm或更大。优选,电镀膜40中的Ni或Ni合金膜的厚度是0.5μm或更大。设置绝缘层60以增大由安装在单独的封装区域C中的发光元件照射的光的反射率和散热比。形成绝缘层60的材料可以通过将填充剂或颜料(例如,二氧化钛(TiO2)或硫酸钡(BaSO4))添加到例如环氧树脂或硅树脂(例如,有机聚硅氧烷)来获得。由该材料制成的白墨可以被用作绝缘层60的材料。在平面图中,布线31和32形成面向彼此的同时在其间插入有预定间隙的两个区域。该两个区域形成发光元件安装部。换句话说,该发光元件安装部由大体在单独的封装区域C中的基板10的整个表面上被设置成平面形状的金属层形成。该金属层通过设置在该金属层中的预定间隙(缝隙)而被分成面向彼此的两个区域(布线31和32)。同时,该预定间隙(缝隙)具有与发光元件的一个电极和另一个电极之间的间隙相对应的宽度。发光元件安装部的外围以从基板10的外围向基板10的内部的方式被向内设置。这是为了防止当发光元件安装封装1被切割成单独的封装区域C时发光元件安装部(布线31和32)的侧表面被暴露。这样,可以防止当使用发光元件安装封装1时发生短路。发光元件被安装在发光元件安装部上。形成在发光元件安装部的区域的一部分上的电镀膜41和42中的一个连接至发光元件的一个电极,发光元件的另一个电极连接至电镀膜41和42中的另一个。换句话说,布线31的形成电镀膜41的部分以及布线32的形成电镀膜42的部分形成为面向彼此,同时在其间插入有预定间隙。电镀膜41和42分别为发光元件的一个电极和另一个电极的连接部。作为发光元件安装部的贯通布线51连接在布线31的正下方。作为发光元件安装部的贯通布线52连接在布线32的正下方。由此,由发光元件产生的热量能够经由贯通布线51和52被有效地散发。另外,布线31的形成电镀膜43的部分和布线32的形成电镀膜44的部分形成为面向彼此,同时插入有预定间隔,从而使保护部件能够被安装在电镀膜43和44上。电镀膜43和44中的一个连接至保护部件的一个电极。电镀膜43和44中的另一个连接至保护部件的另一个电极。换句话说,电镀膜43和44分别是保护部件的一个电极和另一个电极的连接部。然而,可能并不总是安装该保护部件,而是可根据需要将其安装。该保护部件为例如齐纳二极管。在安装齐纳二极管的过程中,电镀膜43和44中具有较高电势的一个(即,发光元件的正电极)是阴极。同时,电镀膜43和44中具有较低电势的另一个(即,发光元件的负电极)是阳极。通过在电镀膜43和电镀膜44之间安装齐纳二极管,可以防止电镀膜43和44之间的电压变为预定电压(齐纳电压)或更大。布线31和32面向彼此,使得布线31的突出面向布线32的凹陷,同时在布线31和32之间插入预定间隔,并且在平面图中,该突出进入该凹陷中。布线31的突出是用于发光元件的一个电极的连接部。布线32的凹陷是用于发光元件的另一个电极的连接部。面向彼此的布线31和32的部分(除了布线31的突出和布线32的凹陷之外)变为与保护部件的电极连接的连接部。参照图2A,布线31的突出和布线32的凹陷被大体设置在布线31和32的面向部分的中心,同时插入有预定间隔。然而,该布置不限于上述布置。确定布线31和32的形状,以便将其中安装保护部件的部分与其中安装发光元件的部分分离得尽可能远。通过在发光元件的附近安装保护部件,光的一部分被保护部件所遮挡,从而可能降低照明强度。通过如图2A所示的布置,保护部件被安装得离发光元件尽可能远,从而防止保护部件被安装在紧邻发光元件旁边。这样,可以防止照明强度减小。然而,该形状不限于上述形状。图3为第一实施例的发光元件封装100的剖视图。参照图3,发光元件110被安装在切片后的发光元件安装封装1(单独的封装区域C的一部分)的发光元件安装部(布线31和32)上。然后,发光元件110由密封树脂120密封,并被进一步安装在金属基板125上。发光元件110可以是LED,在其相对侧形成有阳极电极和阴极电极。然而,发光元件110不限于LED。例如,可以使用表面发射激光器等。密封树脂120可以是包含荧光材料的环氧绝缘树脂或硅胶绝缘树脂等。在下文中,举例说明了这样的实例:其中发光元件110是LED,发光元件封装100是LED封装。(发光元件110可以被称为LED110,发光元件封装100可以被称为LED封装100。)安装在发光元件安装封装1上的LED110的规格尺寸(dimension)在其平面图中为例如:长度0.3mmx宽度0.3mm、长度1.0mmx宽度1.0mm、长度1.5mmx宽度1.5mm等。LED110具有作为一个电极的凸块111和作为另一个电极的凸块112。LED110的凸块111和112中的一个是阳极端子,LED110的凸块111和112中的另一个是阴极端子。凸块111和112通过倒装芯片接合被设置在电镀膜41和42上。电镀膜41和42之间的间隔被确定为与LED110的凸块111和112之间的间隔(例如,60μm)对应。在LED封装100中,在其上安装LED110的发光元件安装封装1被进一步安装在金属基板125上。金属基板125包括:金属板130,用作散热器部(散热器板);绝缘层140,形成在金属板130的一个表面上;布线层150,形成在绝缘层140上;以及阻焊剂层155,选择性地涂覆布线层150。开口155x和155y被设置在阻焊剂层155中。部分布线150从开口部155x和155y暴露。在下文中,暴露在开口部155x上的布线150和暴露在开口部155y上的布线150被分别称为外部连接焊盘150A和150B。金属板130的材料可以为例如具有优良导热性的铜(Cu)、铝(Al)等。金属板130的厚度可以为例如大约100μm至大约500μm。然而,尤其在需要散热性能的情况下,金属板的厚度可以是大约几毫米。绝缘层140的材料可以为例如环氧绝缘树脂、硅胶绝缘树脂等。布线层150的材料为例如铜(Cu)等。焊盘150A中的一个经由由焊料或导电浆料构成的结合部160电连接至贯通布线51的从基板10的另一个表面突出的突出部(连接端子)。换句话说,焊盘150A中的一个经由贯通布线51、布线31以及电镀膜41电连接至作为LED110的电极端子之一的凸块111。焊盘150A中的另一个经由由焊料或导电浆料构成的结合部160电连接至贯通布线52的从基板10的另一个表面突出的突出部(连接端子)。换句话说,焊盘150A中的另一个经由贯通布线52、布线32以及电镀膜42电连接至作为LED110的电极端子之一的凸块112。通过将外部连接焊盘150B连接至布置在发光元件封装100外部的电源、驱动电路等,并通过在LED110的凸块111和112之间施加预定电位差,LED110发光。LED110产生热量。由LED110产生的热量经由电镀膜41和布线31被传送到贯通布线51,并经由焊盘150A中的一个和绝缘层140被进一步传送到金属板130。类似地,由LED110产生的热量经由电镀膜42和布线32被传送到贯通布线52,并经由焊盘150A中的另一个和绝缘层140被进一步传送到金属板130。传递到金属板130的热量通过金属板130被散发。如所描述的,贯通布线51和52在安装在发光元件安装部上的LED110与主要有助于散热的金属基板125之间形成电连接路径,并且还形成用于将由LED110产生的热量传递到金属基板125的金属板130的散热路径。因为贯通布线51和52被布置在LED110的附近(例如,大体位于LED110下方),所以由LED110产生的热量能够被有效地传递到金属板130,使得热量从金属板130散发出去。[第一实施例的发光元件安装封装的制造方法]接下来,描述第一实施例的发光元件安装封装的制造方法。图4A至图6D示出第一实施例的发光元件安装封装1的制造工艺。在说明第一实施例的发光元件安装封装的制造工艺的过程中使用的剖视图与图2B对应。在图4所示的工艺内(图4A为平面图,图4B为与图2B对应的剖视图),呈卷轴形状(带状)的聚酰亚胺膜等被制备成基板10,并且粘着层20是通过在基板10的一个表面上涂覆环氧树脂粘着剂等来形成。代替环氧树脂粘着剂,可以通过粘着至基板10来贴附(attach)环氧树脂粘着膜。贯穿基板10和粘着层20的齿孔10x和通孔50x形成在基板10(其具有形成在基板10的一个表面上的粘着层20)上。齿孔10x沿着基板10的纵向方向(图4A中的左右方向)连续形成在横向边缘(图4A中的上下方向)上,同时插入大体恒定的间隔。通孔50x形成在预定位置(与图1所示的贯通布线50对应的位置)处,在该预定位置处在下文描述的工艺中形成布线30。齿孔10x和通孔50x通过例如冲压工艺形成。接下来,在图5A所示的工艺中,金属层30A形成在粘着层20上。粘着层20通过在预定温度加热被硬化。例如,金属层30A能够通过在粘着层20上叠置铜箔来形成。金属层30A的厚度可以是大约18μm至大约35μm。金属层30A通过稍后被图案化而变为布线30。接下来,在图5B所示的工艺中,通过将图5A所示的结构浸入用于湿蚀刻的溶液(例如,过氧化氢溶液)中,暴露在通孔50x中的金属层30A的下表面和金属层30A的上表面被蚀刻(所谓的微蚀刻)。通过该蚀刻工艺,存在于金属层30A的表面上的防锈剂被去除,并且金属层30A的表面的微少厚度可以被去除例如大约0.5μm至大约1μm。当优选要这样做时,可以执行该蚀刻工艺。参照图5C,遮蔽胶带(maskingtape)500被贴附到金属层30A的上表面。遮蔽胶带500是用来覆盖金属层30A的上表面,使得在以下图5D所示的工艺中通过电镀形成贯通布线50时电镀膜不会生长在金属层30A的上表面上。参照图5D,贯通布线50(贯通布线51、52以及53)通过使用金属层30A作为电源层进行电镀来形成。之后,去除图5C所示的遮蔽胶带500。贯通布线50使电镀金属在通孔50x的内部沉淀在金属层30A的下表面上。然后,电镀金属填充通孔50x的内部以便形成得类似柱状物(column)。贯通布线50在一端(图5D的上端)电连接至金属层30A。贯通布线50形成为在基板的另一端(图5D的下端)从基板10的另一个表面突出。贯通布线50从基板10的另一个表面的突出量为例如大约20μm至大约50μm。贯通布线50的材料为例如铜(Cu)等。接下来,参照图6A,金属层30A被图案化以形成包括布线31和32(发光元件安装部)以及总线33的布线30。具体而言,例如,抗蚀剂(未示出)被涂覆在金属层30A上。金属层30A被曝光以匹配布线30的形状。然后,布线30的形状被显影。然后,通过使用抗蚀剂进行蚀刻而通过图案化形成布线30。在此之后,去除抗蚀剂。参照图6B,绝缘层60形成在布线31和32的不形成电镀膜41和42的预定部分上。绝缘层60可以由白色材料构成。例如,绝缘层60可以通过丝网印刷方法等形成。在形成白墨等以便整体覆盖布线30之后,绝缘层60可以通过在白墨等上暴露将要形成电镀膜41和42的部分而形成。接下来,参照图6C,粘附有铜箔510的遮蔽胶带520被粘着至基板10的另一个表面。铜箔510接触贯通布线51、52以及53的下端(在突出部的顶端附近)。由此,贯通布线51和52的突出部(连接端子)以及贯通布线53的突出部接触作为导体的铜箔510,从而将贯通布线51和52(第一贯通布线)与贯通布线53(第二贯通布线)电连接。这样,基板的下表面完全被遮蔽胶带520覆盖。接下来,参照图6D,使用包括总线33、贯通布线53、铜箔510以及贯通布线51和52的供电路径执行电镀,从而在暴露于布线31和32的绝缘层60上的部分的表面上形成电镀膜41、42、43以及44。电镀膜45形成在总线33上。电镀膜41、42、43、44以及45的材料、厚度等如上所述。在图6D所示的工艺之后,粘附有铜箔510的遮蔽胶带520被去除,并通过沿与基板10的纵向方向垂直的方向切割被在预定位置处切片。完成图1和图2所示的发光元件安装封装1。图3所示的发光封装100能够形成如下。例如,发光元件安装封装1被安装在一装置中。然后,膏状焊料被涂覆在单独的封装区域C的每一个的电镀膜41和42上。每一个发光元件110的凸块111和112被布置在单独的封装区域C的每一个的电镀膜41和42的膏状焊料上。之后,发光元件封装100被带入回流熔炉,以熔化膏状焊料并将其硬化。之后,在利用密封树脂120密封发光元件安装封装1的上表面之后,每一个单独的封装区域C的部分沿着各自的边界界限被切割,以被切片成单独的封装区域C。或者,单独的封装区域C的部分被切片。然后,每一个单独的封装区域C的部分被密封树脂120密封。之后,每一个经切片的发光元件安装封装1被安装在包括金属板130、绝缘层140、布线层150等的金属基板125上。具体而言,通过将贯通布线51和52的突出部(连接端子)电连接至焊盘150A,完成图3所示的发光元件封装100。如所描述的,在发光元件安装封装1中,贯通布线51和52被用作将布线31和32电连接的路径,并且还被用作由发光元件110产生的热量的散热路径。由此,由发光元件110产生的热量能够被传递到散热器部(金属板130)以散发热量。此时,因为贯通布线51和52被布置在发光元件安装部(布线31和32)的正下方,所以由发光元件110产生的热量能够被有效地传递到散热器部(金属板130)以散发热量。另外,因为贯通布线51和52被布置在发光元件安装部的正下方从而提高散热性能,所以该布线可以不必像传统技术中为了提高散热性能那样被加厚。结果是,可以使用厚度为大约12μm至大约35μm的相对较薄的铜箔作为布线30。这样,可以将布线31和32之间的间隔缩窄为例如60μm。另外,由于发光元件和散热器板的热膨胀系数的失配,因而在传统发光元件封装中,可能降低发光元件与发光元件安装部之间的连接可靠性。另一方面,在发光元件封装100中,包括具有柔性的树脂作为主要成分的基板10被布置在发光元件110和用作散热器板的金属板130之间。因此,发光元件110与发光元件安装部之间的连接可靠性能够通过缓和发光元件110和金属板130的热膨胀系数之间的失配而得到提高。[b]第二实施例在第二实施例内,描述与第一实施例不同的发光元件安装封装的示例性制造方法。在第二实施例中,省略与第一实施例的上述说明中描述的相同的构成元件的说明。图7为第二实施例的发光元件安装封装1A的示例性剖视图。图8为第二实施例的发光元件封装100A的剖视图。参照图7,发光元件安装封装1A的示意性结构与第一实施例的发光元件安装封装1(参见图1和图2)类似。然而,在发光元件安装封装1A中,布线32的上表面的面积和电镀膜42的上表面的面积大于布线31的上表面的面积和电镀膜41的上表面的面积。另外,贯通布线52的截面面积大于贯通布线51的截面面积。这是因为发光元件110A通过导线接合被安装在发光元件安装封装1A中,如图8中所示的发光元件封装100A。换句话说,在经切片后的发光元件安装封装1A中,发光元件110A经由粘着层170被安装在电镀膜42上(发光元件110A的下表面通过粘着层170被粘着在电镀膜42上)。另外,设置在发光元件110A的上表面上的电极113经由由金(Au)、铜(Cu)等构成的金属线180(接合线)电连接至电镀膜41。另外,设置在发光元件110A的上表面上的另一个电极114经由由金(Au)、铜(Cu)等构成的金属线180(接合线)电连接至电镀膜42。发光元件110A和金属线180由密封树脂120来密封。粘着层170可以是绝缘粘着剂、粘着膜(例如,芯片贴附膜(dieattachfilm))等。然而,当发光元件110A的下表面与电极113和114以及作为发光元件110A的主要组件的芯片部分(未示出)绝缘时,由银膏等构成的导电粘着剂可以被用作粘着层170。如所描述的,在第二实施例内,当上表面的面积等被设计成适当的尺寸时,发光元件安装封装1A能够使所安装的发光元件110A通过导线接合而被电连接。在发光元件安装封装1A中,设置在与发光元件110A的背面对应的位置处的贯通布线52的截面面积能够被设计为较大。这样,能够提高散热效率。换句话说,由发光元件110A产生的热量从发光元件110A的背面经由电镀膜42和布线32被传递到贯通布线52。另外,热量被有效地从面积较大的贯通布线52传递到焊盘150A、绝缘层140以及金属板130。然后,热量通过金属板130被散发。(第二实施例的变型实例)在第二实施例的变型实例内,描述与第二实施例不同的发光元件安装封装的示例性结构。在第二实施例的变型实例中,省略与第一实施例和第二实施例的上述说明中描述的相同的构成元件的说明。图9为第二实施例的变型实例的发光元件安装封装1B的示例性剖视图。图10为第二实施例的变型实例的发光元件封装100B的剖视图。参照图9,发光元件安装封装1B的示意性结构与第二实施例的发光元件安装封装1A(参见图7)类似。然而,在发光元件安装封装1B中,电镀膜42的上表面的面积小于发光元件安装封装1A中的面积。这是因为发光元件110B的仅一个电极通过导线接合连接至发光元件安装封装1B,如图10中的发光元件封装100B所示。因此,没有设置通过导线接合连接发光元件110B的另一个电极的面积。在发光元件封装100B中,一个电极113被设置在发光元件110B的上表面上。另一个电极115被设置在发光元件110B的下表面上。在发光元件安装封装1B中,发光元件110B经由由例如银膏等构成的导电粘着层190被安装在电镀膜42上。由此,另一个电极115经由导电粘着层190电连接至电镀膜42。发光元件110B的电极113以类似于第二实施例的方式经由金属线180电连接至电镀膜41。发光元件110B和金属线180以类似于第二实施例的方式由密封树脂120来密封。如此,电极115被设置在发光元件110B的下表面上,从而经由导电粘着层190将电极115与电镀膜42电连接。这样,能够获得与第二实施例类似的效果。[c]第三实施例在第三实施例内,举例说明了与第一实施例不同的发光元件安装封装的示例性制造方法。在第三实施例中,省略与上述实施例中的描述相同的构成元件的说明。[第三实施例的发光元件安装封装的结构]描述第三实施例的发光元件安装封装的结构。图11为第三实施例的发光元件安装封装的示例性平面图。图12A为图11的部分A(由虚线包围)的示例性放大平面图。图12B为沿图12A的线B-B的示例性剖视图。参照图11以及图12A和图12B,发光元件安装封装1C与发光元件安装封装1(参见图1、图2A和图2B)不同的一点是贯通布线53没有被设置在总线33中。在该发光元件安装封装的制造方法的说明中描述了没有设置贯通布线53的原因。经切片后的发光元件安装封装1C的封装结构与发光元件安装封装1的类似。[第三实施例的发光元件安装封装的制造方法]接下来,描述第三实施例的发光元件安装封装的制造方法。图13A、图13B、图14A以及图14B示出第三实施例的发光元件安装封装的制造工艺。图13A和图14A为示例性平面图,图13B和图14B为示例性剖视图。参照图13B,实施与图4A至图6A所示的第一实施例中类似的工艺。然而,在与图4A和图4B对应的工艺中,通孔50没有形成在与总线33对应的区域中。在与图6A对应的工艺中,布线30从金属层30A形成,并同时形成多个连接部35。形成连接部35以将总线33与互相相邻的布线31或32、相邻的布线31、相邻的布线32、以及相邻的布线31和32电连接。由此,仅在基板10的一侧,所有的布线31和32电连接至总线33。如所描述的,因为总线33仅在基板10的一侧与布线31和32电连接,所以在基板10的另一个表面上没有使用导体。这样,没有设置贯通布线53。参照图14A和图14B,实施与图6B至图6D所示的第一实施例类似的工艺,从而在暴露于绝缘层60上的布线31和32的表面上形成电镀膜41、42、43以及44。电镀膜45形成在总线33上。接下来,参照图6C,未粘附有铜箔510的遮蔽胶带520被粘着至基板10的另一个表面。遮蔽胶带520的一个表面接触贯通布线50的下端(在突出部的顶端附近)。这样,基板10的另一个表面完全被遮蔽胶带520覆盖。在与图6D对应的工艺中,电力经由总线33和连接部35被供应到布线31和32,从而形成电镀膜41、42、43以及44。此时,遮蔽胶带被粘附在连接部35上,从而防止电镀膜形成在连接部35上。这是因为容易去除连接部35。在图14A和图14B所示的工艺之后,去除图14B所示的连接部35,并进一步去除遮蔽胶带520。通过在预定位置沿与纵向方向垂直的方向将基板10切割成片,完成图11和图12所示的发光元件安装封装1C。例如,能够通过掩盖除连接部35之外的区域并湿蚀刻或干蚀刻连接部35,来去除连接部35。或者,连接部35可以通过鼓风(blasting)来去除。如所描述的,在第三实施例内,设置连接部35以在基板10的一个表面上将总线33与布线31和32连接。另外,电镀膜41、42、43以及44形成在布线31和32上。在如上述制造的发光元件安装封装1C中能够获得与第一实施例类似的效果。另外,连接部35通过在将发光元件安装封装1C切片之前进行蚀刻来去除,从而防止连接部残留在切割成片的部分处,以获得发光元件安装封装1C。因为布线30的边缘没有暴露在通过进行切片获得的发光元件安装封装1C的端部上,所以不会发生诸如短路、生锈等问题。[d]第四实施例在第四实施例内,举例说明了与第一实施例不同的发光元件安装封装的另一个示例性结构。在第四实施例中,省略与上述实施例中的描述相同的构成元件的说明。[第四实施例的发光元件安装封装的结构]描述第四实施例的发光元件安装封装的结构。图15为第四实施例的发光元件安装封装的示例性平面图。图16A和图16B为图15的部分D(由虚线包围)的示例性放大图。图16A为平面图。图16B为沿图16A的线B-B的剖视图。为了方便起见,金属元件80通过图16A中的点而被图案化。参照图15以及图16A和图16B,发光元件安装封装1D与发光元件安装封装1(参见图1、图2A以及图2B)主要不同的点是金属元件80代替绝缘层60被设置在发光元件安装封装1D的表面上。在发光元件安装封装1D中,形成电镀膜41以覆盖布线31的上表面和侧表面。另外,形成电镀膜41以覆盖布线32的上表面和侧表面。以类似于第一实施例的方式,形成电镀膜45以覆盖总线33的上表面和侧表面。在第一实施例中形成电镀膜43和44的区域上,在第四实施例中形成电镀膜41和42。因此,在第四实施例中,电镀膜43和44不存在。金属元件80经由粘着层70被粘着在电镀膜40(电镀膜41、42以及45)上。例如,粘着层70是由绝缘树脂构成的粘着剂(例如,环氧树脂粘着剂、硅胶粘着剂或聚酰亚胺粘着剂)。当需要时,绝缘耐热性粘着剂可以被用作粘着层70。粘着层70的厚度为例如大约8μm至大约18μm。粘着层70可以是与粘着层20相同类型的粘着剂或与粘着层20不同类型的粘着剂。在发光元件安装封装1D中,由于进行切片而将变成单独的发光元件安装封装的多个单独的封装区域C被纵向和横向布置在基板10上。金属元件80包括:多个反射板81,纵向和横向布置,同时插入有预定间隔;框架部82,完全包围反射板81;以及悬挂部(hungportion)83,连接反射板81、框架部82以及悬挂部83。反射板81被布置在每一个单独的封装区域C内的每一个发光元件安装部上。反射板81、框架部82以及悬挂部83整体形成。在第四实施例中,可以仅沿一个方向(图16A的纵向方向)设置悬挂部83。可以仅沿图16A上的横向方向或者沿图16A上的纵向方向和横向方向来设置该悬挂部。以类似于齿孔10x的方式运作的齿孔80x被设置在金属元件80的框架部82中。设置开口部81x以在金属元件80的反射板81上暴露电镀膜41和42的每一个的一部分。暴露在每一个开口部81x上的电镀膜41和42用作发光元件的一个电极的连接部以及发光元件的另一个电极的连接部。开口部81x的内壁是倾斜表面,其形状像喇叭以向着上表面扩展(widen)。当发光元件被安装在暴露在开口部81内部的电镀膜41和42上时,该内壁用来沿预定方向反射由发光元件发出的光。能够相对于电镀膜40的上表面适当地设定开口部81x的内壁表面的倾斜角度。该倾斜角度是大约20°至大约50°。然而,开口部81x的内壁的截面形状不限于线性形状,而可以包括弯曲部。从提高反射率的角度来看,开口部81x的平面形状优选较小。开口部81x在其平面图中是圆形。例如,该开口部的直径可以是大约几毫米。然而,开口部81x的平面形状不限于圆形,而可以是椭圆形、矩形等。例如,金属体80的厚度可以是大约0.5mm。金属元件80的材料是铜、铝、铜和铝的合金等。此时,通过抛光金属元件80的表面来给予该表面进一步的光泽度(gloss),当发光元件被安装并发出光时,开口部81x的内壁表面内的反射率变得尤为高。通过在金属元件80的表面上设置镀金、镀银等,可以进一步增强光泽度。此时,优选的是选择对于从发光元件发出的光的发射波长具有高反射率的电镀材料。可以为整个金属元件80或仅限定区域(例如,仅开口部81x的内壁表面)提供抛光或电镀。与开口部81x不同的另一个开口部可以被设置在其中形成电镀膜43和44的区域中。然后,另一个开口部具有暴露在该另一个开口部上的电镀膜41和42,以使得能够在电镀膜41和42上安装保护部件(例如,齐纳二极管)。图17为第四实施例的发光元件封装的剖视图。参照图17,发光元件110被安装在经切片后的发光元件安装封装1D(单独的封装区域C的一部分)的发光元件安装部(布线31和32)上。然后,发光元件110由密封树脂120密封,并被进一步安装在金属基板125上。密封树脂120被设置在反射板81的开口部81x的内部。在第四实施例内,因为开口部81x的内壁表面是倾斜表面,所以可以有效地将从发光元件110发出的光反射到预定方向(提高反射率)。[第四实施例的发光元件安装封装的制造方法]接下来,描述第四实施例的发光元件安装封装的制造方法。图18A至图18C示出第四实施例的发光元件安装封装的制造工艺。图18A至图18C与图16对应。首先,实施类似于第一实施例的图4A至图6A所示的工艺。在图18A所示的工艺中,在类似于图6D所示的工艺中形成电镀膜41、42以及45。然而,因为没有形成绝缘层60,所以形成电镀膜41以便覆盖布线31的上表面和侧表面。另外,形成电镀膜42以便覆盖布线32的上表面和侧表面。在图18B所示的工艺中,在去除图18A所示的粘附有铜箔510的遮蔽胶带520之后,环氧树脂粘着剂等被涂覆在电镀膜41、42以及45的预定区域,从而形成粘着层70。代替环氧树脂粘着剂,可以粘着环氧树脂粘着膜以形成粘着层70。该预定区域是除暴露在反射板81的开口部81x内部的部分之外的区域。接下来,在图18C所示的工艺中,具有开口部81x和悬挂部83的金属元件80被制备,并经由粘着层70粘着在电镀膜41、42以及45上。包括开口部81x和悬挂部83的金属元件80可以通过压印(stamping)或蚀刻金属板来形成。利用该工艺,金属元件80的反射板81被纵向和横向布置,以便被安置在单独的封装区域C内部。其中安装发光元件的电镀膜41和42被暴露在反射板81的开口部81x的内部。通过在预定位置将该结构切割成片,完成图15、图16A以及图16B所示的发光元件安装封装1D。在对该结构进行切片时,切割悬挂部83。如所描述的,通过将包括反射板的金属元件粘着在发光元件安装封装的表面上,提高了发光元件安装封装的刚度以减少偏斜,并且发光元件安装封装的制造工艺以及装运之后的处理变得容易。同时,在如第一实施例的由白墨等构成的绝缘层60形成的情况下,绝缘层60的厚度具有特定值(大约40μm至大约50μm),以提高反射率。然而,因为通过一个印刷工艺不能获得该厚度,所以执行多个印刷工艺。另一方面,通过将反射板的开口部的内壁表面形成为倾斜表面,使得能够在该倾斜表面有效地反射光。因此,可以去除白墨等的印刷工艺。这样,能够简化发光元件安装封装的制造工艺。例如,在第一实施例中为了当在发光元件封装100的制造工艺中形成密封树脂时防止密封树脂流出,存在环形坝(annulardam)形成在发光元件安装封装1的单独封装区域的绝缘层60上的情况。在第四实施例内,反射板的开口部的内壁表面用作当在发光元件封装的制造工艺中形成密封树脂时防止密封树脂流出的坝。因此,没有专门设置用作坝的元件,从而简化了发光元件安装封装或发光元件封装的制造工艺。同时,因为由发光元件产生的热量能够从反射板散发,所以能够提高发光元件封装的散热性能。如果在散热性能方面寻求更大的改善,则优选的是将具有高导热性的金属(铜等)用作反射板的材料。如果更为寻求轻重量,则优选的是将具有低比重的金属(铝等)用作反射板的材料。<第四实施例的变型实例1>在第四实施例的变型实例1内,描述在反射板的表面上设置反射膜的实例。在第四实施例的变型实例1中,省略与前述实施例的上述说明中的描述相同的零部件的说明。图19示出第四实施例的变型实例1的发光元件安装封装的剖视图。图19与图16对应。图20示出第四实施例的变型实例1的发光元件封装的剖视图。图20与图17对应。像图19所示的发光元件安装封装1E以及图20所示的发光元件封装100E一样,反射膜61可以形成在反射板81的上表面以及开口部81x的内壁表面上。然而,形成有反射膜61的区域可以仅为开口部81x的内壁表面。形成反射膜61的材料可以通过将填充剂或颜料(例如,二氧化钛(TiO2)或硫酸钡(BaSO4))添加到例如环氧树脂或硅树脂(例如,有机聚硅氧烷)来获得。由上述材料构成的白墨可以被用作反射膜61的材料。反射膜61可以通过将丝网印刷方法等应用于其中形成开口部81x和悬挂部83的金属元件80来形成。另外,反射膜61可以形成在金属元件80的下表面上。在将反射膜61布置在电镀膜40上之后,将反射膜61硬化。这样,金属元件80能够被粘着在电镀膜40上,而不必使用粘着层70。换句话说,形成在金属元件80的下表面上的反射膜61用作粘着层70。因为反射膜61形成在金属元件80上,所以与第一实施例的绝缘层60相比,反射膜61可以是薄的。反射膜61的厚度可以为例如大约50μm。因为反射膜61可以较薄,所以与如第一实施例中所述形成绝缘层60的情况相比,能够减少印刷的次数。如此,通过将反射膜61设置在反射板81的上表面以及开口部81x的内壁表面上(或仅设置在开口部的内壁表面上),实现了由发光元件发出的光的高反射率。虽然在第四实施例的变型实例1中没有描述在框架部82的上表面上形成反射膜61,然而反射膜61可以形成在框架部82的上表面上,以省略掩蔽框架部82等的工艺。<第四实施例的变型实例2>在第四实施例的变型实例2内,第四实施例中的用于形成电镀膜41和42的区域被减小。在第四实施例的变型实例2中,省略与前述实施例的上述说明中的描述相同的零部件的说明。图21示出第四实施例的变型实例2的发光元件安装封装的剖视图。图21与图16B对应。图22示出第四实施例的变型实例2的发光元件封装的剖视图。图22与图17对应。除如图21中示出的发光元件安装封装1F以及图22中示出的发光元件封装100F所示的区域的一部分之外,布线31和32可以被阻焊剂层62覆盖。形成阻焊剂层62以覆盖除了安置在开口部81x内部的部分之外的布线31和32的上表面和侧表面。形成电镀膜41以覆盖布线31的上表面和侧表面的位于开口部81x内部的部分。形成电镀膜42以覆盖布线32的上表面和侧表面的位于开口部81x内部的部分。代替绝缘层60,阻焊剂层62可以在图6B所示的工艺中形成。具体而言,阻焊剂层62能够通过涂布液状或膏状感光环氧绝缘树脂等形成,以通过丝网印刷方法覆盖布线31和32。或者,膜状感光环氧绝缘树脂等可以被叠置在粘着层20上,以便覆盖布线31和32,从而形成阻焊剂层62。通过将涂覆或叠置的绝缘树脂曝光并显影,形成具有与开口部81x对应的形状的开口部62x(光刻)。开口部62x可以通过激光处理或鼓风来形成。因为阻焊剂层62不会有助于反射,所以阻焊剂层62的颜色能够是除白色以外的颜色。如所描述的,通过形成阻焊剂层62以便覆盖除安置在反射板81的开口部81x内部的部分之外的布线31和32的上表面和侧表面,能够减小用于形成电镀膜41和42的区域。因此,能够减小制造成本。另外,在第四实施例内,反射板81与电镀膜41和42(布线31和32)仅通过粘着层70来绝缘。另一方面,在第四实施例内,反射板81以及布线31和32通过阻焊剂层62和粘着层70来绝缘,从而安全可靠地将反射板81与布线31和32绝缘。<第四实施例的变型实例3>在第四实施例的变型实例3内,在通过导线接合在发光元件安装封装上安装发光元件的模式中,反射板被设置在发光元件安装封装中。在第四实施例的变型实例3中,省略与上述实施例的上述说明中的描述相同的零部件的说明。图23为第四实施例的变型实例3的发光元件安装封装的示例性平面图。图24为图23的部分D(由虚线包围的部分)的示例性放大剖视图。图24示出与图16B对应的剖视图。图25示出第四实施例的变型实例3的发光元件封装100G的剖视图。图25与图17对应。金属元件90可以将发光元件安装在其上的模式被设置在发光元件安装封装1G中,并以类似于图23和图24所示的发光元件安装封装1G以及图25所示的发光元件封装100G的方式被设置在发光元件封装中。在发光元件安装封装1G中,基板10、粘着层20、布线30以及贯通布线50具有与发光元件安装封装1A类似的结构(参见图7)。然而,发光元件安装封装1G包括阻焊剂层63,而不是绝缘层60。阻焊剂层63包括用于在阻焊剂层63上暴露布线31和32的部分的开口部63x。电镀膜41和42形成在暴露于开口部63x内部的布线31和32上。在发光元件封装100G中,金属线180(接合线)连接至电镀膜41和42。阻焊剂层63以类似于第四实施例的变型实例2中描述的阻焊剂层62的方式形成。如所描述的,通过形成阻焊剂层63(其在与金属线连接的部分处是开口的),能够减小形成有电镀膜41和42的部分的面积。因此,能够减少发光元件安装封装1G的制造成本。在发光元件安装封装1G中,由于进行切片而将变成单独的发光元件安装封装的多个单独封装区域C被纵向和横向布置在基板10上。金属元件90包括:多个反射板91,纵向和横向布置,同时插入有预定间隔;框架部92,完全包围反射板91;以及悬挂部93,连接框架部92与相邻于框架部92的反射板91,及互相相邻的反射板91。反射板91被布置在每一个单独的封装区域C内部的每一个发光元件安装部上。反射板91、框架部92以及悬挂部93整体形成。在第四实施例中,可以仅沿一个方向(图23的纵向方向)来设置悬挂部93。可以仅沿图23的横向方向或者沿图23的纵向方向和横向方向来设置该悬挂部。以类似于齿孔10x的方式运作的齿孔90x被设置在金属元件90的框架部92中。其中安装发光元件110A的区域以及用于暴露与金属线180(接合线)连接的电镀膜41和42的开口部91x被设置在金属元件90的每一个反射板91上。例如,开口部91x的形状是矩形。金属元件90形成得比金属元件80薄。每一个反射板91的开口部91x的内壁表面不是倾斜表面。在第四实施例内,当安装在开口部91x内部的发光元件110A发出光时,由发光元件110A发出的光在反射板91的上表面上反射。因为反射板91的开口部91x的内壁表面不是倾斜表面,所以金属元件90能够比金属元件80薄。例如,金属元件90的厚度是大约70μm。发光元件110A被安装在经切片后的发光元件安装封装1G(单独的封装区域C的一部分)的发光元件安装部(布线31和32)上。然后,发光元件110A由密封树脂120来密封,并被进一步安装在金属基板125上。密封树脂120被设置在反射板91的开口部91x的内部。反射板91的开口部91x的内壁表面用作防止密封树脂120流出的坝。如所描述的,即使反射板以通过导线接合安装发光元件的模式被设置在发光元件安装封装中,也能获得与第四实施例类似的效果。然而,在第四实施例的变型实例3内,因为每一个反射板的开口部的内壁表面不是倾斜表面,所以由发光元件发出的光在反射板的上表面上反射。<第四实施例的变型实例4>在第四实施例的变型实例4中描述金属元件的变化。在第四实施例的变型实例4中,省略与上述实施例的上述说明中的描述相同的零部件的说明。图26示出第四实施例的变型实例4的金属元件的示例性平面图。如图26所示,金属元件80A可以处于这样的模式:其中多个金属元件80经由连接部85连接。待连接的金属元件80的数量不限于三个,而可以是两个或四个或更多。包括许多单独的封装区域C的发光元件安装封装通过形成基板10、布线30等来实现,以便与金属元件80A对应。至于金属元件90(参见图23),多个金属元件可以类似于金属元件80的方式连接。在金属元件80A中,形成一个金属元件80的多个单独的封装区域C是第四实施例的第一部分的典型实例。形成与该一个金属元件分离布置的另一个金属元件80的多个单独的封装区域C是第四实施例的第二部分的典型实例。图27A和图27B示出悬挂部的其它示例性形状。在金属元件80中,悬挂部83可以由图27A所示的悬挂部83A来代替。悬挂部83A处于这样的模式:其中框架部82和相邻于框架部82的反射板81以及互相相邻的反射板81被布置,同时插入有预定间隔。可以采用这样的模式:其中框架部82通过布置有预定间隙的3个或多个部分(portionsequalto3ormore)连接至相邻于框架部82的反射板81,并且互相相邻的反射板81通过布置有预定间隙的3个或多个部分连接。在金属元件80中,悬挂部83可以由图27B所示的悬挂部83B来代替。悬挂部83B处于这样的模式:其中框架部82通过布置有预定间隙的2个部分连接至相邻于框架部82的反射板81,并且以类似于悬挂部83A的方式,互相相邻的反射板81通过布置有预定间隙的2个部分连接。然而,所布置的同时插入有预定间隙的两个部分弯曲得不同于悬挂部83A。因此,悬挂部可以是除了线性形状之外的其它形状。在使用悬挂部83B的情况下,开口部由插入有预定间隙的所述两个部分的内部形成。然而,本实施例不限于此模式。例如,布置有预定间隙的两个部分可以具有两个弯曲位置,以便形成八角形的开口部。例如,布置有预定间隙的两个部分可以弯曲,以形成椭圆形的开口部。至于金属元件80A和90,悬挂部83A或83B可适用。当悬挂部83、83A以及83B的上表面的一部分以及悬挂部83、83A以及83B的下表面的一部分被去除以进行薄化时,优选将单独的封装区域C切割成片。例如,代替经由粘着层20将金属层30A粘着到基板10,能够使用以下方法。作为聚酰亚胺树脂膜(聚酰亚胺带)等的基板10被制备,以使用无电镀、溅射、电镀等在基板10(未设置粘着层20)的一个表面上直接形成由铜(Cu)构成的金属层。然后,代替金属层30A,使用该形成的金属层以执行与金属层30A类似的功能。这种情况下,通孔50x通过激光处理方法等仅形成在基板10中。换句话说,每一个通孔50x的一侧由形成在基板10上的金属层来填充(填满)。如另一个实例,基板10可以通过在金属箔(例如,铜箔)上涂覆绝缘树脂(例如聚酰亚胺)等来形成。同样在这种情况下,通孔50x通过激光处理方法等仅形成在基板10中。换句话说,每一个通孔50x的一侧由形成在基板10上的金属箔来填充(填满)。由例如镍(Ni)或金(Au)构成的电镀膜可以形成在贯通布线51或52的突出部(连接端子)上。贯通布线51或52的突出部(连接端子)可以通过例如有机可焊性保护(OSP)工艺来进行抗氧化。可以适当地将实施例和实施例的变型实例结合。例如,在发光元件安装封装1G中,反射膜61(白色反射膜)位于反射板91的上表面上。可选择地,反射膜61可以形成在反射板91的上表面以及开口部91x的内壁表面上。另外,在发光元件安装封装1G中,代替金属元件90,可以使用具有为倾斜表面的内壁表面的金属元件80。根据公开内容,提供一种具有散热路径(其能够有效地将由发光元件产生的热量传递到设置在外部的散热器部)的发光元件安装封装、发光元件安装封装的制造方法、以及通过将发光元件安装在发光元件安装封装上形成的发光元件封装。本文所述的全部示例和条件性语言是为了教示性的目的,试图帮助读者理解本发明的原理以及发明人为了促进技术而贡献的概念,并应解释为不限制于这些具体描述的示例和条件,说明书中这些示例的组织也不是为了显示本发明的优劣。尽管已详细描述了本发明的实施例,然而应当理解,在不脱离本发明的精神和范围的前提下可以进行各种变化、替换以及更动。