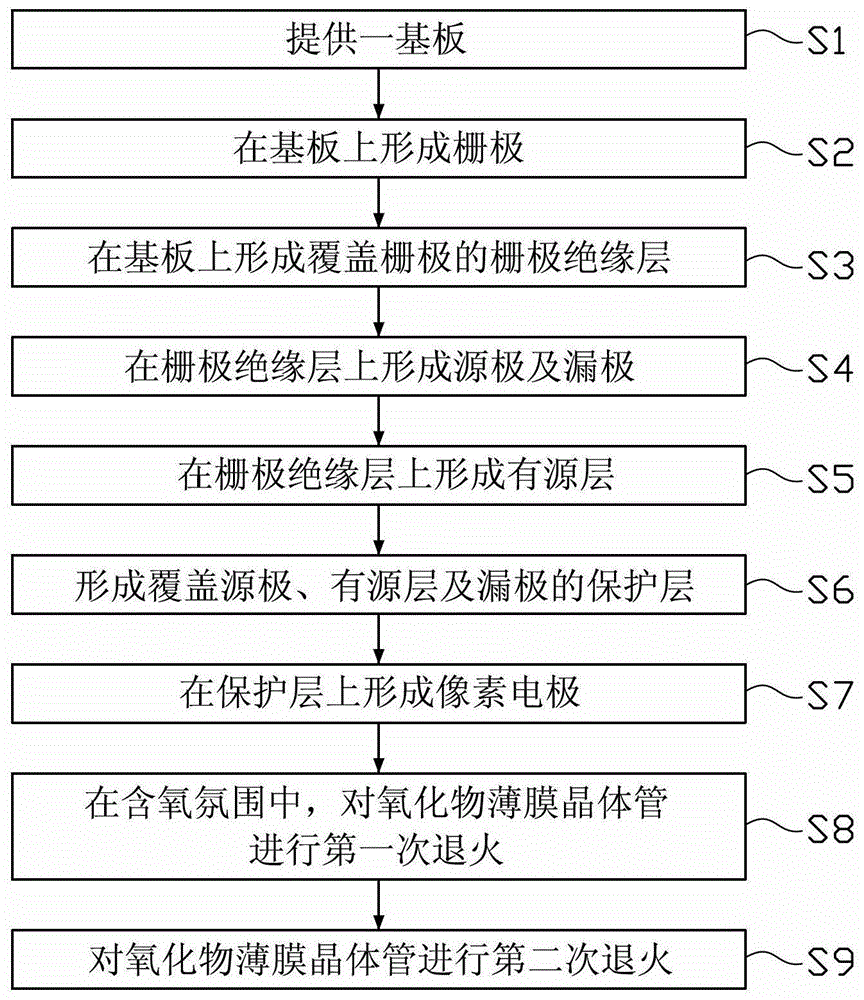
本发明涉及半导体器件的制造领域,且特别涉及一种氧化物薄膜晶体管的制造方法。
背景技术:氧化物薄膜晶体管是场效应晶体管的一种,其包括栅极、漏极、源极、有源层、保护层等膜层。氧化物薄膜晶体管因其具有省电、成本低、工艺灵活等优点,而被作为驱动元件广泛应用于显示装置中。在氧化物薄膜晶体管的制造过程中,为了改善氧化物薄膜晶体管的性能,通常需要对氧化物薄膜晶体管进行退火处理。对氧化物薄膜晶体管进行退火处理的目的有两个:(1)使退火环境中的氧原子扩散进入有源层,进而中和因保护层成膜时产生的大量氧空位(载流子的主要来源);(2)降低氧化物薄膜晶体管的所有膜层(含界面)的应力和缺陷态。在对氧化物薄膜晶体管进行退火处理时,较高的退火温度有利于氧原子扩散进入有源层,但不利于膜层界面特性的改善;反之,较低的退火温度虽然有利于降低膜层界面特性中的应力和缺陷态,但氧原子因为能量较低无法充分地透过保护层而扩散进入有源层。然而,现有技术中的氧化物薄膜晶体管的退火工艺只采用单一温度对氧化物薄膜晶体管进行退火处理,从而导致现有的氧化物薄膜晶体管的制造方法不能兼顾上述两方面的效果。
技术实现要素:本发明的目的在于,提供一种氧化物薄膜晶体管的制造方法,其既可以有利于氧原子扩散进入有源层,又可以改善氧化物薄膜晶体管的膜层特性。一种氧化物薄膜晶体管的制造方法,包括以下步骤:在有氧氛围内,将所述氧化物薄膜晶体管置于退火炉中进行第一次退火,其中,第一次退火时退火炉中的温度T1的范围为200℃-400℃;以及在第一次退火完成后,将所述氧化物薄膜晶体管置于退火炉中进行第二次退火,其中,第二次退火时退火炉中的温度T2的范围为150℃-250℃,并且所述第二次退火时退火炉中的温度T2低于所述第一次退火时退火炉中的温度T1。在本发明的一个具体实施方案中,所述有氧氛围中的氧气含量按体积比例计算为21%-100%。在本发明的一个具体实施方案中,在退火炉中对所述氧化物薄膜晶体管进行所述第一次退火时,所述第一次退火的时间至少为40分钟。在本发明的一个具体实施方案中,所述第二次退火的时间为至少为60分钟。在本发明的一个具体实施方案中,所述有氧氛围为空气或者纯氧气或者氧气与氮气的混合气体。在本发明的一个具体实施方案中,所述第二次退火是在无氧氛围内进行。在本发明的一个具体实施方案中,在对氧化物薄膜晶体管进行第一次退火之前还包括以下步骤:提供一基板;在所述基板上形成栅极;在所述基板上形成覆盖所述栅极的栅极绝缘层,其中所述栅极绝缘层具有第一区域、第二区域以及第三区域,其中所述第二区域位于所述栅极的正上方,所述第一区域与所述第三区域分别位于所述第二区域的两侧;在所述栅极绝缘层的第一区域及第三区域分别形成漏极及源极;在所述栅极绝缘层的第二区域上形成有源层;以及在所述漏极、所述有源层及所述源极上形成覆盖它们的保护层。在本发明的一个具体实施方案中,在所述漏极、所述有源层及所述源极上形成保护层的步骤与对氧化物薄膜晶体管进行第一次退火的步骤之间还包括以下步骤:在所述保护层的位于所述漏极一侧的区域上方形成像素电极。在本发明的一个具体实施方案中,所述保护层正对所述漏极的区域形成有接触孔,所述像素电极通过所述接触孔与所述漏极连接。在本发明的一个具体实施方案中,所述漏极及所述源极与所述有源层连接。本发明有益效果是,本发明的氧化物薄膜晶体管的制造方法通过采用两段式退火工艺,即在高温含氧的环境中对氧化物薄膜晶体管进行第一次退火,在低温环境中对氧化薄膜晶体管进行第二次退火,以对氧化物薄膜晶体管进行退火处理,从而使本发明的氧化物薄膜晶体管的制造方法既有利于氧原子扩散进入有源层,又有利于改善氧化物薄膜晶体管的所有膜层的特性。上述说明仅是本发明技术方案的概述,为了能够更清楚了解本发明的技术手段,而可依照说明书的内容予以实施,并且为了让本发明的上述和其他目的、特征和优点能够更明显易懂,以下特举较佳实施例,并配合附图,详细说明如下。附图说明图1是本发明一实施例的氧化物薄膜晶体管的结构示意图。图2是本发明一实施例的氧化物薄膜晶体管的制造方法的流程图。图3是氧化物薄膜晶体管A在单一的高温条件下退火后的转移特性曲线图。图4是氧化物薄膜晶体管B在单一的低温条件下退火后的转移特性曲线图。图5是氧化物薄膜晶体管C采用两段式退火工艺后的转移特性曲线图。图6是由图3-图5中的氧化物薄膜晶体管的转移特性曲线得到的氧化物薄膜晶体管的特性参数表。具体本实施例为更进一步阐述本发明为达成预定发明目的所采取的技术手段及功效,以下结合附图及较佳实施例,对本发明的具体实施例、结构、特征及其功效,详细说明如后。图1是本发明一实施例的氧化物薄膜晶体管的结构示意图。请参考图1,本发明的氧化物薄膜晶体管被用作例如液晶显示器的驱动元件,其包括基板11、栅极12、栅极绝缘层13、漏极14、源极15、有源层17、保护层18以及像素电极19。基板11为透明基板,其可由玻璃、石英或透明高分子材料等制成。栅极12设置在基板11上。在本实施例中,栅极12是通过采用磁控溅射法在基板11上形成第一导电膜,然后再通过光刻工艺来图案化该第一导电膜而形成的。第一导电膜即栅极12的材料只要导电性良好即可,可根据需要选择,例如可以为Ti(钛)、Al(铝)、Pt(铂)、Au(金)等金属单质或包含其中至少一种的合金或包含其中至少一种的金属氧化物。栅极绝缘层13是为了将栅极12绝缘设置,以覆盖栅极12的方式形成在基板11上。在本实施例中,栅极绝缘层13是通过采用等离子体化学气相沉积法(PlasmaEnhancedChemicalVaporDeposition,PECVD)在基板11上形成覆盖栅极12的第一绝缘膜而形成的。第一绝缘膜的材料即栅极绝缘层13的材料只要绝缘性出色即可,第一绝缘膜能够使用例如硅氧化膜(SiO2)、硅氮化膜(SiN)、氧化铝膜(Al2O3)等。栅极绝缘层13包括第一区域131、第二区域132及第三区域133。其中,第二区域132位于栅极12的正上方,第一区域131与第三区域133分别位于第二区域132的两侧。漏极14设置在栅极绝缘层13的第一区域131的正上方。源极15设置在栅极绝缘层13的第三区域133的正上方。在本实施例中,漏极14和源极15是通过采用磁控溅射法在栅极绝缘层13上形成第二导电膜,然后再通过光刻工艺来图案化该第二导电膜而形成,并使得形成的漏极14和源极15分别位于栅极绝缘层13的第一区域131及第三区域133的上方。第二导电膜即漏极14和源极15的材料只要导电性良好即可,可根据需要选择,例如为为Ti(钛)、Al(铝)、Pt(铂)、Au(金)等金属单质或包含其中至少一种的合金或包含其中至少一种的金属氧化物。有源层17为设置在栅极绝缘层13的第二区域132上方的氧化物半导体层,其隔着栅极绝缘层13与栅极12相对设置,并且有源层17与漏极14及源极15连接。需要说明的是,在本实施例中,有源层17是通过采用磁控溅射法在栅极绝缘层13上形成氧化物半导体膜,然后再通过光刻工艺来图案化该氧化物半导体膜而形成。氧化物半导体膜即有源层17的材料例如为含有In(铟)、Ga(镓)、Zn(锌)的非晶态的金属氧化物半导体。保护层18以覆盖漏极14、源极15及有源层17的方式形成于漏极14、源极15、有源层17以及栅极绝缘层13之上。在本实施例中,保护层18是通过采用磁控溅射法形成覆盖漏极14、源极15及有源层17的第二绝缘膜,然后再通过光刻工艺来图案化该第二绝缘膜,使该第二绝缘膜在正对漏极14的区域形成有接触孔181,从而形成保护层18。在其他实施例中,在保护层18的制备过程中,还可以采用等离子体化学气相沉积法形成覆盖漏极14、源极15及有源层17的第二绝缘膜。第二绝缘膜即保护层18的材料只要绝缘性出色即可,第二绝缘膜能够使用例如硅氧化膜(SiO2)、硅氮化膜(SiN)、氧化铝膜(Al2O3)等。像素电极19形成于保护层18的位于漏极14一侧的区域上方。在本实施例中,像素电极19是通过采用磁控溅射法在保护层18的位于漏极14一侧的区域上方形成第三导电膜,然后再通过光刻工艺图案化该第三导电膜而形成。像素电极19通过保护层18上的接触孔181与漏极14连接。需要说明的是,像素电极19为透明电极,例如可以由氧化铟锡(ITO)制成。请参照图2,本发明的氧化物薄膜晶体管的制造方法包括以下步骤:步骤S1:提供一基板11。步骤S2:在基板11上形成栅极12。具体的,首先采用磁控溅射法在基板11上形成第一导电膜,然后通过光刻工艺来图案化该第一导电膜,从而形成栅极12。步骤S3:在基板11上形成覆盖栅极12的栅极绝缘层13。具体的,采用等离子体化学气相沉积法在基板11上形成覆盖栅极12的第一绝缘膜,而形成栅极绝缘层13。需要说明的是,栅极绝缘层13具有第一区域131、第二区域132及第三区域133,并且第二区域132位于栅极12的正上方,第一区域131与第三区域133分别位于第二区域132的两侧。步骤S4:在栅极绝缘层13上形成漏极14及源极15。具体的,首先采用磁控溅射法在栅极绝缘层13上形成第二导电膜,然后通过光刻工艺来图案化该第二导电膜,而在栅极绝缘层13的第一区域131及第三区域上形成漏极14及源极15。步骤S5:在栅极绝缘层13上形成有源层17。具体的,首先采用磁控溅射法在栅极绝缘层13的第二区域132形成氧化物半导体膜,然后通过光刻工艺来图案化该氧化物半导体膜,从而形成有源层17。需要说明的是,有源层17分别与漏极14及源极15连接。步骤S6:在漏极14、有源层17及源极15上形成覆盖它们的保护层18。具体的,在本实施方式中,首先采用磁控溅射方法形成覆盖漏极14、有源层17及源极15的第二绝缘膜,然后通过光刻工艺来图案化该第二绝缘膜,使该第二绝缘膜正对漏极14的区域形成有接触孔181,从而形成覆盖漏极14、有源层17及源极15的保护层18。在其他实施方式中,还可以通过等离子体化学气相沉积法形成覆盖漏极14、有源层17及源极15的第二绝缘膜。步骤S7:在保护层18上形成像素电极19。具体的,首先采用磁控溅射法在保护层18的位于漏极14一侧的区域上方形成第三导电膜,然后通过光刻工艺来图案化该第三导电膜,形成像素电极19,从而得到氧化物薄膜晶体管。需要说明的是,像素电极19通过保护层18上的接触孔181与漏极14连接。步骤S8:在有氧氛围中,对氧化物薄膜晶体管进行第一次退火。在氧化物薄膜晶体管的制造过程中,形成保护层18时,由于等离子体放电会在有源层17上造成氧空位的浓度显著增加,即造成载流子的浓度显著增加,影响氧化物薄膜晶体管的操作特性,例如会降低氧化物薄膜晶体管的开关电流比和阈值电压等。因此,在有氧氛围中,对氧化物薄膜晶体管进行第一次退火,可以使氧氛围中的氧原子扩散进入有源层17,进而中和因保护层18成膜时产生的大量氧空位,从而改善氧化物薄膜晶体管的开关电流比和阈值电压。具体的,首先将氧化物薄膜晶体管置于退火炉中,然后向退火炉中通入含有氧气的气体进而形成有氧氛围,并在T1温度下对氧化物薄膜晶体管进行第一次退火,第一次退火的时间为t1。需要说明的是,第一次退火时退火炉中的温度T1需保证含氧氛围中的氧原子具有足够的活动能力穿透氧化物薄膜晶体管的保护层18进入氧化物薄膜晶体管内部,可以理解的是,第一次退火时退火炉中的温度T1越高含氧氛围中的氧原子的活动能力越强,但过高的退火温度又不利于膜层膜质和界面特性的改善,特别是高温退火很容易在器件膜层内引起热应力,本发明的实施方式中,第一次退火时退火炉中的温度T1在200℃-400℃之间;第一退火的含氧氛围中的氧气含量按照体积比计算例如为21%-100%,第一退火时通入的气体例如为空气、纯氧气或氧气与氮气的混合气体等,可以理解的是,含氧氛围中的氧气含量越高,第一次退火的效果越明显;第一次退火的时间t1与第一次退火时退火炉中的温度T1及第一次退火的氧气含量有关系,即第一次退火时退火炉中的温度T1越高,第一次退火的氧气含量越高,第一次退火的时间t1就越少,但是为了保证在第一次退火时,含氧氛围中的氧原子能够充分进入氧化物薄膜晶体管内部,使氧化物薄膜晶体管达到第一次退火效果即使氧空位达到特定的中和百分比,在退火炉中对氧化物薄膜晶体管进行第一退火的时间t1至少为40分钟。可以理解的是,第一次退火不限于在退火炉中进行,在其他实施方式中,第一次退火还可以采用快速退火(RTP)、激光退火等瞬态高温加热手段,这样可减少第一次退火的时间t1。步骤S9:对氧化物薄膜晶体管进行第二次退火。由于氧化物薄膜晶体管的有源层17内的点缺陷、位错和面缺陷等缺陷态以及氧化物薄膜晶体管的所有膜层的应力(含界面)的存在,会降低氧化物薄膜晶体管的操作性能,例如会降低氧化物薄膜晶体管的开关电流比、阈值电压、场效应迁移率以及亚阈值摆幅。因此,对氧化物薄膜晶体管进行第二次退火,可以降低氧化物薄膜晶体管所有膜层(含界面)的应力和有源层17的缺陷态,从而可以改善氧化物薄膜晶体管的开关电流比、阈值电压、场效应迁移率以及亚阈值摆幅。具体的,在第一次退火结束后,在T2温度下对氧化物薄膜晶体管进行第二次退火,第二次退火的时间为t2,并且第二次退火时退火炉中的温度T2小于第一次退火时退火炉中的温度T1。更具体的,为了保证氧化物薄膜晶体管内的氧原子有效扩散且各膜层内的应力和缺陷态能有效降低,第二次退火时退火炉中的温度T2例如为150℃-250℃,并且第二次退火时退火炉中的温度T2低于第一次退火时退火炉中的温度T1,第二次退火的时间t2至少为60分钟。另,第二次退火的时间t2和第二次退火时退火炉中的温度T2有关系,第二次退火时退火炉中的温度T2越高,第二次退火的时间t2也越少,但为了使氧化物薄膜晶体管达到第二次退火效果即充分消除所有膜层应力和缺陷态,第二次退火的时间t2至少为60分钟。需要进一步说明的是,在对氧化物薄膜晶体管进行第二次退火时,可以先将氧化物薄膜晶体管从退火炉内取出冷却后,再将氧化物薄膜晶体管放入退火炉中进行第二次退火,也可以在第一次退火后,稍事冷却即马上进行第二次退火,而无需在第一退火后由退火炉内取出氧化物薄膜晶体管。还需要说明的是,在对氧化物薄膜晶体管进行第二次退火时,最好在稳定性气体氛围内退火,例如可以在无氧氛围例如氮气氛围等气氛中进行,可以理解的是,第二次退火也可以在含氧氛围例如空气氛围、氧气氛围等氛围中进行。当第二次退火在含氧氛围中进行时,由于第二次退火时退火炉中的温度较低,因此,含氧氛围中的氧原子难以穿过保护层18进入到有源层17中而影响到有源层中的氧空位(载流子的来源)的含量,因此,含氧氛围不会影响载流子的浓度。下面以具体的实施例来说明本发明采用两段式退火的优异性。图3是氧化物薄膜晶体管A在单一的高温条件下退火后的转移特性曲线图。图4是氧化物薄膜晶体管B在单一的低温条件下退火后的转移特性曲线图。图5是氧化物薄膜晶体管C采用两段式退火工艺后的转移特性曲线图。具体的,图3为氧化物薄膜晶体管A在退火炉内、空气氛围中、260℃的温度下退火2小时后形成的转移特性曲线。图4为氧化物薄膜晶体管B在退火炉内、空气氛围中、170℃的温度下退火2小时后形成的转移特性曲线。图5为氧化物薄膜晶体管C在退火炉内、空气氛围中、260℃的温度下退火1小时,然后在退火炉内、空气氛围中、170℃的温度下退火1小时后形成的转移特性曲线。图6是由图3-图5中的氧化物薄膜晶体管的转移特性曲线得到的氧化物薄膜晶体管的特性参数表。请参照图3-图6,从实验结果可以看到,在退火炉内、空气氛围中、260℃的温度下退火2小时后的氧化物薄膜晶体管A具有较好的场效应迁移率和亚阈值摆幅,但氧化物薄膜晶体管A的开关电流比较小,且阈值电压的负值程度太大;在退火炉内、空气氛围中、170℃的温度下退火2小时后的氧化物薄膜晶体管B具有较好的阈值电压,但其它特性指标则较差;相比较而言,在退火炉内、空气氛围中、260℃的温度下退火1小时,然后在退火炉内、空气氛围中、170℃的温度下退火1小时后的氧化物薄膜晶体管C具有最好的综合特性,其具有最高的开关电流比以及较好的场效应迁移率、亚阈值摆幅和阈值电压。本实验结果证明采用合适的两段退火条件可以有效地改善氧化物薄膜晶体管的器件特性。综上所述,本发明的氧化物薄膜晶体管的制造方法通过采用两段式退火工艺,即在高温含氧的环境中对氧化物薄膜晶体管进行第一次退火,在低温环境中对氧化薄膜晶体管进行第二次退火,以对氧化物薄膜晶体管进行退火处理,从而使本发明的氧化物薄膜晶体管的制造方法既有利于氧原子扩散进入有源层,又有利于改善氧化物薄膜晶体管的所有膜层的特性。以上所述,仅是本发明的较佳实施例而已,并非对本发明作任何形式上的限制,虽然本发明已以较佳实施例揭露如上,然而并非用以限定本发明,任何熟悉本专业的技术人员,在不脱离本发明技术方案范围内,当可利用上述揭示的技术内容作出些许更动或修饰为等同变化的等效实施例,但凡是未脱离本发明技术方案内容,依据本发明的技术实质对以上实施例所作的任何简单修改、等同变化与修饰,均仍属于本发明技术方案的范围内。