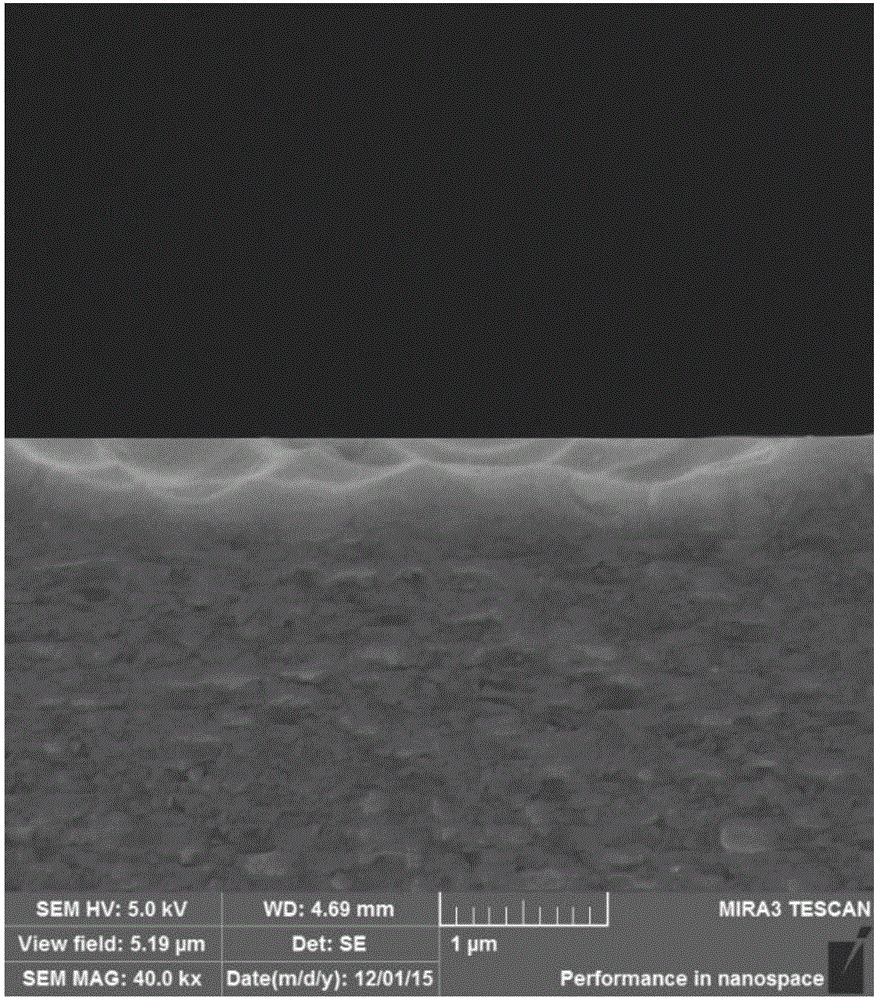
本发明涉及镀膜
技术领域:
,尤其涉及一种玻璃基板和玻璃表面的镀膜方法。
背景技术:
:玻璃材料具有良好的光学、电学、机械和化学稳定性能,因此玻璃基板在光学器件、微波器件、建筑方面以及汽车方面等具有广泛的应用。在玻璃表面镀金属、合金或金属氧化物膜,可以赋予玻璃新的功能,通常被广泛地应用于建筑、光伏、电子等领域。现有玻璃镀膜技术主要包括磁控溅射法、溶胶-凝胶技术、化学气相沉积技术、真空蒸发镀膜技术等,其中,膜与玻璃之间的粘附性很大程度上决定了薄膜在实际应用中的可靠性和稳定性。公开号为CN103613289A的中国专利文献公开了一种在玻璃基板上化学镀铜的方法,该方法包括:在玻璃基板上涂覆一层有机薄膜,晾干后再采用传统化学镀铜工艺方法沉积铜层;其中有机薄膜制备方法包括以下步骤:(1)将有机薄膜材料以0.1%~20%的体积百分比溶解于易挥发有机溶剂中;(2)将所述有机溶剂以旋涂、喷涂、浸泡或涂刷方法涂覆于玻璃基板上;(3)待涂覆了所述有机溶剂的玻璃基板烘干或晾干;(4)将玻璃基板采用有机薄膜材料的特性进行亚胺化或高温固化。上述方法主要通过在玻璃基板表面涂覆一层有机薄膜,再采用传统镀铜的方法进行镀膜,这可以一定程度上提高薄膜和玻璃基板之间的结合力。但由于玻璃本体与膜材料的异质性,以及界面主要是由物理作用、化学作用来结合,因此,还需要有更多可行的方法来进一步增强膜与玻璃的结合力,从而改善膜功能的稳定性和可靠性。技术实现要素:有鉴于此,本申请提供一种玻璃基板和玻璃表面的镀膜方法,采用本发明提供的玻璃基板进行镀膜,能提高薄膜和基体、以及膜层之间的结合力。本发明提供一种玻璃基板,其由玻璃经反胶束微球微乳液表面处理得到;所述反胶束微球微乳液包括非极性溶剂和表面活性剂包裹的化学腐蚀液;所述玻璃基板具有微米级孔坑。优选地,所述非极性溶剂选自直链烷烃、取代直链烷烃、支链烷烃和芳香烃中的一种或几种。优选地,所述表面活性剂选自烷基苯磺酸钠、烷基磺酸钠、脂肪醇硫酸钠、脂肪醇聚氧乙烯醚硫酸钠、烷基磺酸钠等、十二烷基三甲基溴化铵、十六烷基三甲基溴化铵、十六烷基三甲氯化铵、十二烷基二甲基苄基氯化铵、十六烷基三甲基杂多酸铵盐、十二烷基甜菜碱、N-酰胺丙基二甲基羧甲基铵甜菜碱、多元醇型非离子表面活性剂、聚氧乙烯型非离子表面活性剂和聚氧乙烯-聚氧丙烯型非离子表面活性剂中的一种或几种。优选地,所述化学腐蚀液选自酸类腐蚀液或碱类腐蚀液。优选地,所述反胶束微球微乳液还包括醇。本发明提供一种玻璃表面的镀膜方法,包括以下步骤:A)采用反胶束微球微乳液对玻璃进行表面处理,得到具有微米级孔坑的玻璃基板;所述反胶束微球微乳液包括非极性溶剂和表面活性剂包裹的化学腐蚀液;B)在所述玻璃基板表面上镀膜,得到镀膜后的玻璃材料。优选地,所述步骤A)中,所述非极性溶剂自直链烷烃、取代直链烷烃、支链烷烃和芳香烃中的一种或几种;所述化学腐蚀液选自酸类腐蚀液或碱类腐蚀液。优选地,所述步骤A)中,所述表面处理的时间为0.5h~10h,所述表面处理的温度为10℃~120℃。优选地,所述步骤B)中,所述镀膜的方式为磁控溅射法或化学气相沉积法。优选地,所述步骤A)之前还包括:采用清洗液对玻璃进行洗涤,得到洗涤后的玻璃;所述清洗液包括水溶液或无水溶剂;所述步骤A)为:采用反胶束微球微乳液对洗涤后的玻璃进行表面处理,经清洗,得到具有微米级孔坑的玻璃基板。与现有技术相比,本发明应用反胶束微球腐蚀玻璃表面,形成微米级孔坑的结构;所得玻璃基板为微米级孔坑玻璃,其呈现多孔结构,表面积大,结构稳定,耐磨。并且,本发明在所述微米级孔坑玻璃表面进行镀膜,膜能嵌入到玻璃孔里,可以得到切面呈波浪形的三维膜结构。因此,利用本发明提供的玻璃基板的镀膜方法不仅提高了薄膜和基板之间的结合力,而且提高了膜层之间的结合力,从而改善膜功能的稳定性和可靠性,利于应用。附图说明图1为实施例1制备得到的微米级孔坑玻璃的表面SEM图;图2为实施例1制备得到的微米级孔坑玻璃的断面SEM图;图3为实施例1制备得到的微米级孔坑玻璃的表面原子力显微镜3D图;图4为实施例1制备得到的微米级孔坑玻璃的表面激光显微镜3D图;图5为实施例1在玻璃微米级孔坑上镀膜的表面SEM图;图6为实施例1在玻璃微米级孔坑上镀膜的断面SEM图;图7为原片玻璃表面上AZO薄膜的划痕试验图;图8为本发明多孔玻璃表面上AZO薄膜的划痕试验图。具体实施方式下面对本发明实施例中的技术方案进行清楚、完整地描述,显然,所描述的实施例仅仅是本发明一部分实施例,而不是全部的实施例。基于本发明中的实施例,本领域普通技术人员在没有做出创造性劳动前提下所获得的所有其他实施例,都属于本发明保护的范围。本发明提供了一种玻璃基板,其由玻璃经反胶束微球微乳液表面处理得到;所述反胶束微球微乳液包括非极性溶剂和表面活性剂包裹的化学腐蚀液;所述玻璃基板具有微米级孔坑。本发明提供的玻璃基板为微米级孔坑玻璃,其呈现多孔结构,表面积大,结构稳定,耐磨,利于镀膜。本发明实施例提供的玻璃基板表面具有孔坑形貌,其中,坑深可为100nm~600nm,坑口宽可为1μm~3μm,即具有微米级孔坑。所述玻璃基板由玻璃经过反胶束微球微乳液的表面处理得到,其中,所述玻璃为本领域常用的基板或基片材料,本发明没有特殊限制。在本发明实施例中,可将玻璃切割成所需尺寸进行后续处理。本发明优选采用洗涤后的玻璃进行表面处理;所述洗涤后的玻璃可采用清洗液洗涤得到。在本发明的实施例中,所述清洗液包括水溶液或无水溶剂,能把玻璃表面的杂质清洗干净,但没有使其表面结构产生变化。其中,所述水溶液如水、酸溶液、碱溶液或洗涤剂水溶液等;所述无水溶剂如乙醇、丙酮或乳化液等。所述清洗液优选为蒸馏水、稀盐酸、稀硫酸、氨水、无水乙醇、蒸馏水和丙酮中的两种或两种以上。此处,当清洗液为两种或两种以上物质时,即采用这两种或两种以上物质分别清洗玻璃。所述清洗液更优选为稀盐酸、稀硫酸、氨水、无水乙醇、蒸馏水和丙酮;其中,稀盐酸和稀硫酸的质量浓度可为5%~20%,如7%。在本发明的实施例中,采用清洗液洗涤玻璃时,稀盐酸、稀硫酸、氨水、无水乙醇、蒸馏水和丙酮的体积比优选为(1~2):(1~2):(1~2):(10~20):(10~20):(10~20),更优选为(1~1.8):(1~1.8):(1~1.8):(12~18):(12~18):(12~18)。此处,所述体积比表示相互之间的体积比例关系,对使用顺序和种类没有限制。本发明可按顺序依次将清洗液对玻璃进行洗涤;在本发明的一些实施例中,所述清洗液依次为稀盐酸、丙酮、蒸馏水。在本发明的一些实施例中,所述清洗液依次为丙酮、乙醇、蒸馏水。在本发明的另一些实施例中,所述清洗液依次为稀盐酸、蒸馏水。在本发明的另一些实施例中,所述清洗液依次为氨水、丙酮、蒸馏水。在本发明的另一些实施例中,所述清洗液依次为稀硫酸、无水乙醇、蒸馏水。在这些实施例中,所用物质的比例均满足上述体积比。本发明应用反胶束微球微乳液腐蚀玻璃表面,形成微米级孔坑的结构以及提高表面积。所述反胶束微球微乳液也称反胶束微球液、反胶束微球乳液等,其包括非极性溶剂。所述非极性溶剂优选自直链烷烃、取代直链烷烃、支链烷烃和芳香烃中的一种或几种,如正己烷、正庚烷、正辛烷、正壬烷、正癸烷等直链烷烃,异戊烷、新戊烷、3-甲基-5乙基辛烷、2,3-二甲基丁烷、5-丙基-4-异丙基壬烷等支链烷烃,苯或烷基苯等芳香烃,以及四氯化碳、二氯化碳等取代直链烷烃。所述非极性溶剂更优选自直链烷烃和支链烷烃中的一种或几种;在本发明的一些实施例中,所述非极性溶剂为正己烷和3-甲基-5-乙基辛烷。在本发明的一些实施例中,所述非极性溶剂为正戊烷。在本发明的另一些实施例中,所述非极性溶剂为正庚烷和异戊烷。在本发明的另一些实施例中,所述非极性溶剂为正癸烷和5-丙基-4-异丙基壬烷。在本发明的另一些实施例中,所述正极性溶剂为异戊烷和3-甲基-5-乙基辛烷。当所述非极性溶剂为两种物质时,两者的体积比可为1:1。在本发明中,所述反胶束微球微乳液包括表面活性剂包裹的化学腐蚀液。其中,所述表面活性剂包括阳离子表面活性剂、阴离子表面活性剂、两性表面活性剂、非离子表面活性剂等,优选为阳离子表面活性剂或阴离子表面活性剂。所述表面活性剂更优选自烷基苯磺酸钠、烷基磺酸钠、脂肪醇硫酸钠、脂肪醇聚氧乙烯醚硫酸钠、烷基磺酸钠等阴离子表面活性剂,十二烷基三甲基溴化铵、十六烷基三甲基溴化铵、十六烷基三甲氯化铵、十二烷基二甲基苄基氯化铵、十六烷基三甲基杂多酸铵盐等阳离子表面活性剂,十二烷基甜菜碱、N-酰胺丙基二甲基羧甲基铵甜菜碱等两性表面活性剂,多元醇型、聚氧乙烯型和聚氧乙烯-聚氧丙烯型等非离子表面活性剂;所选表面活性剂优选为其中的一种或几种。在本发明中,所述表面活性剂包裹水性的化学腐蚀液。所述化学腐蚀液优选自酸类腐蚀液或碱类腐蚀液,如HCl、H2SO4、HNO3、HF、HPO3、H2CO3、CH3COOH溶液等酸类腐蚀液,NaOH、KOH、NaHCO3、Na2HPO4、NH4OH溶液等碱类腐蚀液,所选化学腐蚀液为其中的一种或几种。所述化学腐蚀液更优选自HCl、H2SO4、HNO3、HF、H2CO3、CH3COOH、NaOH、KOH、NaHCO3、Na2HPO4和NH4OH中的两种或两种以上溶液;其中,H2SO4的质量浓度可为98%,HF的质量浓度可为40%,HCl的质量浓度可为37%,碱类腐蚀液的浓度优选为0.1M~1M。在本发明的一些实施例中,所述化学腐蚀液包括H2SO4和HF。在本发明的一些实施例中,所述化学腐蚀液包括H2SO4、HF和HCl。在本发明的另一些实施例中,所述化学腐蚀液包括KOH和NaHCO3。在本发明的另一些实施例中,所述化学腐蚀液包括。NaOH和Na2HPO4。在本发明的另一些实施例中,所述化学腐蚀液为HF。其中,HCl、H2SO4、HNO3、HF、H2CO3、CH3COOH、NaOH、KOH、NaHCO3、Na2HPO4、NH4OH的摩尔比优选为(2~5):(0.2~5):(0.2~5):(2~20):(2~5):(0.2~5):(0.2~5):(2~20):(2~5):(0.2~5):(0.2~5):(2~20),更优选为(2~5):(0.3~5):(0.3~5):(2~18):(2~5):(0.3~5):(0.3~5):(2~18):(2~5):(0.3~5):(0.3~5):(2~18)。此处,所述摩尔比表示相互之间的物质的量的比例关系,对种类没有限制。当上述水性的化学腐蚀液选取两种或三种溶液时,均满足上述摩尔比例。在本发明中,所述反胶束微球微乳液优选还包括醇,更优选包括C2~C12的醇。所述醇包括但不限于正丙醇、丙三醇、正丁醇、1,4-丁二醇、正戊醇、正己醇、正庚醇、正辛醇、异丙醇、异戊醇,优选为丙三醇、正丁醇、1,4-丁二醇或异戊醇。在本发明中,所述反胶束微球微乳液可简称为乳液、微乳液、反应液。在本发明一些实施例中,所述反应液优选包括正己烷、正庚烷、正辛烷、正壬烷、正癸烷、异戊烷、新戊烷、3-甲基-5-乙基辛烷、2,3-二甲基丁烷、5-丙基-4-异丙基壬烷、苯或烷基苯、四氯化碳、二氯化碳中的一种或几种非极性溶剂与醇的组合,更优选为正己烷、正庚烷、正辛烷、正壬烷、正癸烷、异戊烷、新戊烷、3-甲基-5乙基辛烷、2,3-二甲基丁烷、5-丙基-4-异丙基壬烷、苯或烷基苯、四氯化碳、二氯化碳中的一种与醇的组合。此时,所述正己烷、正庚烷、正辛烷、正壬烷、正癸烷、异戊烷、新戊烷、3-甲基-5乙基辛烷、2,3-二甲基丁烷、5-丙基-4-异丙基壬烷、苯或烷基苯、四氯化碳、二氯化碳中的一种与醇的摩尔比优选为(1~3):(0.1~1)。本发明对所述反胶束微球微乳液的来源没有特殊限制,优选按照以下方法配制得到:将非极性溶剂和醇在水中混合,加入表面活性剂,得到油相;将化学腐蚀液加入所述油相,混合,得到反胶束微球微乳液。其中,两步混合的温度均优选为室温,更优选为20℃~50℃。两步混合的时间均优选为2h~20h,更优选为5~20h。本发明对所述反胶束微球微乳液的用量也没有特殊限制,能浸没或覆盖玻璃表面即可。本发明还提供了一种玻璃表面的镀膜方法,包括以下步骤:A)采用反胶束微球微乳液对玻璃进行表面处理,得到具有微米级孔坑的玻璃基板;所述反胶束微球微乳液包括非极性溶剂和表面活性剂包裹的化学腐蚀液;B)在所述玻璃基板表面上镀膜,得到镀膜后的玻璃材料。本发明提供的玻璃表面镀膜方法是一种三维镀膜技术,能提高薄膜和玻璃基板、以及膜层之间的结合力。本发明实施例可将玻璃切割成所需尺寸,进行后续处理。所述玻璃为本领域常用的基板或基片材料,本发明没有特殊限制。本发明优选还包括:采用清洗液对玻璃进行洗涤,得到洗涤后的玻璃。本发明实施例在表面处理前,将玻璃放入清洗液中进行洗涤或清洗,把玻璃表面的杂质清洗干净,而玻璃表面的结构没有产生变化,利于后续处理。所述清洗液优选包括水溶液或无水溶剂,其内容与前文所述的相应内容一致,在此不再一一赘述。在本发明的实施例中,所述洗涤的方式优选超声清洗;可超声清洗1min~120min,优选为10min~100min。得到清洗液处理后的玻璃后,本发明实施例将其在反胶束微球微乳液中,在一定温度范围进行表面处理,处理一段时间后,得到微米级孔坑玻璃,也就是具有微米级孔坑的玻璃基板。在本发明中,所述反胶束微球微乳液包括非极性溶剂和表面活性剂包裹的化学腐蚀液。本发明采用反胶束微球微乳液对玻璃进行表面处理,在处理过程中,该乳液与玻璃表面进行反应,在玻璃表面造微米级孔坑结构。该反应为水热反应,能腐蚀玻璃表面。经过所述反应处理,可得表面具有微米级孔坑的玻璃,即为上述所述的玻璃基板。其中,所述反胶束微球微乳液的内容如前文所述,在此不再一一赘述。作为优选,待反胶束微球微乳液澄清时,再将玻璃放入其中进行表面处理。所述表面处理的时间优选为0.5h~10h,更优选为1h~10h,最优选为1h~9h。所述表面处理的温度优选为10℃~120℃,更优选为20℃~120℃,最优选为30℃~100℃。得到反应处理后的玻璃后,本发明优选还包括将其进行清洗,得到具有微米级孔坑的玻璃基板。在本发明中,所述水热反应后优选还包括将玻璃放入清洗液中清洗5min~100min,更优选为清洗10min~90min,最优选为清洗15min~60min。所述清洗液优选自稀盐酸、稀硫酸、无水乙醇、蒸馏水和丙酮中的一种或几种,更优选为稀盐酸、稀硫酸、无水乙醇、蒸馏水和丙酮中的两种或两种以上。此处,当清洗液为两种或两种以上物质时,即采用这两种或两种以上物质分别清洗玻璃。所述清洗液最优选为稀盐酸、稀硫酸、无水乙醇、蒸馏水和丙酮;本发明实施例采用清洗液清洗玻璃时,稀盐酸、稀硫酸、氨水、无水乙醇、蒸馏水和丙酮的体积比优选为(1~2):(1~2):(1~2):(10~20):(10~20):(10~20),更优选为(1~1.8):(1~1.8):(1~1.8):(12~18):(12~18):(12~18)。此处,所述体积比表示相互之间的体积比例关系,对使用顺序和种类没有限制。本发明可按顺序依次将清洗液对玻璃进行清洗;在本发明的一些实施例中,所述清洗液优选为蒸馏水。为便于区分,可将表面处理前所用的清洗液称为第一清洗液,表面处理后所用的清洗液称为第二清洗液。在本发明中,上述清洗的方式优选为超声清洗。上述超声清洗之后优选为风干,本发明对所述风干的方式不进行限定,采用本领域技术人员熟知的风干的方式即可,可以为氮气吹干或热风吹干等。本发明的玻璃经过上述处理后,表面呈现较为规则的“多坑”状形貌,其尺寸为微米级。本发明在这样的玻璃基板的表面上进行镀膜,得到镀膜后的玻璃材料,其表面具有切面呈波浪状的三维膜结构。在本发明的实施例中,所述镀膜的方式可为磁控溅射法或化学气相沉积法(CVD)。本发明对磁控溅射法镀膜没有特殊限制,可以镀一层膜或多层膜;可以镀掺铝氧化锌膜(AZO膜)、氧化铟锡薄膜(ITO薄膜)、二氧化钛薄膜、类金刚石薄膜(DLC薄膜)、SiCO硅碳氧膜中的一种或多种。本发明对化学气相沉积法镀制薄膜也没有特殊限制,优选采用常压CVD法镀膜;可以镀制SnO2:F(FTO)薄膜、SnO2:F/SnO2:Sb(SUN-E)薄膜等。综上所述,本发明不仅提高了薄膜和基板、以及膜层之间的结合面积,同时膜嵌入到玻璃孔里,都提高了薄膜和基板、以及膜层之间的结合力,从而改善膜功能的稳定性和可靠性,利于应用。为了进一步理解本申请,下面结合实施例对本申请提供的玻璃基板和玻璃表面的镀膜方法进行具体地描述。以下实施例中,所涉及的溶液浓度均为质量浓度。所用玻璃购自海南中航三鑫公司,其为普通浮法钠钙硅玻璃,厚度为3mm,成分参见表1,表1为本发明实施例所用玻璃的成分。表1本发明实施例所用玻璃的成分实施例1将玻璃切割成所需尺寸。将玻璃放入清洗液中超声清洗10min:按1:10:10的比例量取稀盐酸(7%)、丙酮、蒸馏水,即量取10mL稀盐酸,100mL丙酮,100mL蒸馏水,按顺序依次将清洗液对玻璃进行清洗。将清洗液处理后的玻璃放入反胶束微球液中,进行反应处理。反胶束微球液的具体配制方法包括:按10:10:1的比例,量取正己烷(30mL)、3-甲基-5-乙基辛烷(30mL)和丙三醇(3mL)于盛有蒸馏水的聚四氟乙烯密封容器中,加入表面活性剂十二烷基三甲基溴化铵3g,量取1mLH2SO4(98%)和1mLHF(40%)于上述盛有油相的聚四氟乙烯密封容器中,将上述试剂混合,搅拌均匀后,配制成反胶束微球液。搅拌,待反胶束微球液澄清后,将上述洗涤后的玻璃基片放入该乳液中,在温度为60℃的条件下表面处理5h。将反应处理之后的玻璃放入蒸馏水中超声清洗10min,得到表面具有微米级孔坑的玻璃,即微米级孔坑玻璃。对所得微米级孔坑玻璃进行形貌观察、分析,图1为实施例1制备得到的微米级孔坑玻璃的表面SEM图,图2为实施例1制备得到的微米级孔坑玻璃的截面SEM图,图3为实施例1制备得到的微米级孔坑玻璃的原子力显微镜3D图,图4为实施例1制备得到的微米级孔坑玻璃的表面激光显微镜3D图。从图1和图2可清楚地看出,表面处理后的玻璃表面具有孔坑形貌,坑深为100nm~600nm,坑口宽为1μm~3μm。并且,图3测试范围为25*25微米,扫描速率为1Hz;图4激光显微镜测试范围为95*70微米。从图3和图4进一步可视表面处理后的玻璃表面具有微米级孔坑。实施例2将玻璃切割成所需尺寸。将玻璃放入清洗液中超声清洗10min:按3:3:2的比例量取丙酮、乙醇、蒸馏水,即量取60mL丙酮,60mL乙醇,40mL蒸馏水,按顺序依次将清洗液对玻璃进行清洗。将清洗液处理后的玻璃放入反胶束微球液中,进行反应处理。反胶束微球液的具体配制方法包括:按10:1的比例,量取正戊烷(60mL)和正丁醇(6mL)于盛有蒸馏水的聚四氟乙烯密封容器中,加入表面活性剂烷基苯磺酸钠和十二烷基三甲基溴化铵3g,量取1mLH2SO4(98%)、0.5mLHF(40%)和0.5mLHCl(37%)于上述盛有油相的聚四氟乙烯密封容器中,混合均匀后,配制成反胶束微球液。搅拌,待反胶束微球液澄清后,将上述洗涤后的玻璃基片放入该乳液中,在温度为90℃的条件下表面处理1h。将反应处理之后的玻璃放入蒸馏水中超声清洗10min,得到表面具有微米级孔坑的玻璃。实施例3将玻璃切割成所需尺寸。将玻璃放入清洗液中超声清洗10min:按1:15的比例量取稀盐酸(7%)、蒸馏水,即量取10mL稀盐酸,150mL蒸馏水,按顺序依次将清洗液对玻璃进行清洗。将清洗液处理后的玻璃放入反胶束微球液中,进行反应处理。反胶束微球液的具体配制方法包括:按10:10:1的比例,量取正庚烷(30mL)、异戊烷(30mL)和丙三醇(3mL)于盛有蒸馏水的聚四氟乙烯密封容器中,加入表面活性剂十二烷基三甲基溴化铵3g,量取1mLKOH溶液、1mLNaHCO3溶液于上述盛有油相的聚四氟乙烯密封容器中,KOH和NaHCO3浓度分别为0.7M、0.3M。混合均匀后,配制成反胶束微球液。搅拌,待反胶束微球液澄清后,将上述洗涤后的玻璃基片放入该乳液中,在温度为70℃的条件下表面处理3h。将反应处理之后的玻璃放入蒸馏水中超声清洗30min,得到表面具有微米级孔坑的玻璃。实施例4将玻璃切割成所需尺寸。将玻璃放入清洗液中超声清洗10min:按1:15:15的比例量取氨水、丙酮、蒸馏水,即量取10mL氨水,150mL丙酮,150mL蒸馏水,按顺序依次将清洗液对玻璃进行清洗。将清洗液处理后的玻璃放入反胶束微球液中,进行反应处理。反胶束微球液的具体配制方法包括:按10:10:1的比例,量取正癸烷(30mL)、5-丙基-4-异丙基壬烷(30mL)和1,4-丁二醇(3mL)于盛有蒸馏水的聚四氟乙烯密封容器中,加入表面活性剂烷基苯磺酸钠3g,量取1mLNaOH溶液和1mLNa2HPO4溶液于上述盛有油相的聚四氟乙烯密封容器中,NaOH溶液和Na2HPO4溶液的浓度分别为0.8M、0.2M,混合均匀后,配制成反胶束微球液。搅拌,待反胶束微球液澄清后,将上述洗涤后的玻璃基片放入该乳液中,在温度为40℃的条件下表面处理6h。将反应处理之后的玻璃放入蒸馏水中超声清洗20min,得到表面具有微米级孔坑的玻璃。实施例5将玻璃切割成所需尺寸。将玻璃放入清洗液中超声清洗10min:按1:10:10的比例量取稀硫酸(7%)、无水乙醇、蒸馏水,即量取10mL稀硫酸(7%),100mL无水乙醇,100mL蒸馏水,按顺序依次将清洗液对玻璃基板进行清洗。将清洗液处理后的玻璃放入反胶束微球液中,进行反应处理。反胶束微球液的具体配制方法包括:按15:15:2的比例,量取异戊烷(30mL)、3-甲基-5乙基辛烷(30mL)和异戊醇(4mL)于盛有蒸馏水的聚四氟乙烯密封容器中,加入表面活性剂十二烷基三甲基溴化铵1.5g和十六烷基三甲氯化铵1.5g,量取2mlHF(40%)于上述盛有油相的聚四氟乙烯密封容器中,混合均匀后,配制成反胶束微球液。搅拌,待反胶束微球液澄清后,将上述洗涤后的玻璃基片放入该乳液中,在常温下表面处理9h。将反应处理之后的玻璃放入蒸馏水中超声清洗30min,得到表面具有微米级孔坑的玻璃。实施例6磁控溅射镀AZO膜在磁控溅射过程中,进行参数的设定。选用氧化锌和氧化铝质量比例为98:2的AZO靶,固定靶基距为50mm、工作气压为0.5Pa、溅射功率为300W,氩气气体流量为60sccm,溅射时间为40min,选取普通玻璃(原片玻璃)与实施例1所得微米级孔坑玻璃各一片同时进行溅射,分别得到镀膜后的玻璃材料。普通玻璃购自海南中航三鑫公司,其为普通浮法钠钙硅玻璃,厚度为3mm,成分参见表1。对磁控溅射在两种玻璃表面镀单层AZO薄膜的影响进行研究,本发明实施例6中,多孔玻璃表面上AZO膜的扫描电镜图如图5和图6所示,图5为实施例1在玻璃微米级孔坑上镀膜的表面SEM图,图6为实施例1在玻璃微米级孔坑上镀膜的断面SEM图。通过纳米力学系统仪器按照公知方法测试划痕,本发明实施例6中,两种玻璃表面上AZO薄膜的划痕试验测试如图7和图8所示,图7为原片玻璃表面上AZO薄膜的划痕试验图,图8为本发明多孔玻璃表面上AZO薄膜的划痕试验图,数据见表2,表2为本发明多孔玻璃和原片玻璃表面上AZO薄膜的划痕试验对比结果。由表2可知,与在表面为平面的玻璃基片相比,在多孔玻璃表面上薄膜和基板之间,以及膜层之间的结合力比较增大十倍以上。表2本发明多孔玻璃和原片玻璃表面上AZO薄膜的划痕试验对比结果临界值原片玻璃4.85mN微米级孔坑玻璃(多孔玻璃)50.04mN实施例7磁控溅射镀ITO薄膜在磁控溅射过程中,进行参数的设定。选取ITO为溅射靶材,打开所需气体,固定靶基距为50mm、工作气压为1.0Pa、溅射功率为200W,氩气气体流量为50sccm,溅射时间为20min,选取普通玻璃与微米级孔坑玻璃各一片进行同时溅射,分别得到镀膜后的玻璃材料。对磁控溅射在两种玻璃表面镀单层ITO薄膜的影响进行研究:通过对实施例7中两种玻璃表面上的ITO薄膜进行划痕试验测试,与在表面为平面的玻璃基片相比,在多孔玻璃表面上薄膜和基板之间,以及膜层之间的结合力比较增大十五倍以上。实施例8磁控溅射镀二氧化钛薄膜在磁控溅射过程中,进行参数的设定。选取二氧化钛为靶材,打开所需气体,固定靶基距为50mm、工作气压为0.5Pa、溅射功率为200W,氩气气体流量为60sccm,溅射时间为40min,选取普通玻璃与微米级孔坑玻璃各一片进行同时溅射,分别得到镀膜后的玻璃材料。对磁控溅射在两种玻璃表面镀单层二氧化钛薄膜的影响进行研究,通过对实施例8中两种玻璃表面上的二氧化钛薄膜进行划痕试验测试,与在表面为平面的玻璃基片相比,在多孔玻璃表面上薄膜和基板之间,以及膜层之间的结合力比较增大十三倍以上。实施例9磁控溅射镀双薄膜:SiCO和DLC薄膜在磁控溅射过程中,进行参数的设定。选用SiCO靶和DLC靶,打开所需气体,固定靶基距为50mm、工作气压为0.5Pa,DLC靶材溅射功率为200W,SiCO靶材溅射功率为150W,氩气气体流量为80sccm,温度设定为200℃,溅射时间各为20min,选取普通玻璃与微米级孔坑玻璃各一片进行同时溅射,分别得到镀膜后的玻璃材料。对磁控溅射在两种玻璃表面镀双层SiCO和DLC薄膜的影响进行研究:通过对实施例9中两种玻璃表面上的双层SiCO和DLC薄膜进行划痕试验测试,数据与在表面为平面的玻璃基片相比,在多孔玻璃表面上薄膜和基板之间,以及膜层之间的结合力比较增大九倍以上。实施例10常压CVD法镀制SnO2:F(FTO)薄膜常压CVD镀膜过程中,主要参数设置如下:选取单丁基三氯化锡和三氟乙酸和水为原料,本实验所用载气主要为干燥空气(可直接作为载气和氧化剂),载气流量为20L/min,镀膜器喷嘴距离基板为6mm,基板温度设置为400℃~600℃,基座移动速率为6mm/s,镀膜时间为105s,各组分经150℃的蒸发器气化后随着载气从镀膜器出口喷向玻璃基板表面,所有操作环境均在常压下进行,选取普通玻璃与微米级孔坑玻璃各一片进行薄膜镀制,分别得到镀膜后的玻璃材料。对常压化学气相沉积在两种玻璃表面镀单层SnO2:F薄膜的影响进行研究:通过对实施例10中两种玻璃表面上的SnO2:F薄膜进行划痕试验测试,与在表面为平面的玻璃基片相比,在多孔玻璃表面上薄膜和基板之间,以及膜层之间的结合力比较增大十二倍以上。实施例11常压CVD法镀制SnO2:F/SnO2:Sb(SUN-E)薄膜常压CVD镀膜过程中,主要参数设置如下:选用单丁基三氯化锡和三氟乙酸和水为顶膜,单丁基三氯化锡和三氯化锑和水为底膜。本实验所用载气主要为干燥空气(可直接作为载气和氧化剂),底膜和顶膜载气流量为25L/min,镀膜器喷嘴距离基板为6mm,基板温度设置为300℃~500℃,基座移动速率为5mm/s,两镀膜喷嘴之间距离为100mm,镀膜时间为225s,底膜和顶膜分别进入相应的管道,蒸发管温度均为150℃,所有操作环境均在常压下进行,选取普通玻璃与微米级孔坑玻璃各一片进行薄膜镀制,分别得到镀膜后的玻璃材料。对常压化学气相沉积在两种玻璃表面镀双层SnO2:F/SnO2:Sb薄膜的影响进行研究:通过对实施例11中两种玻璃表面上的双层SnO2:F/SnO2:Sb薄膜进行划痕试验测试,与在表面为平面的玻璃基片相比,在多孔玻璃表面上薄膜和基板之间,以及膜层之间的结合力比较增大十八倍以上。由以上实施例可知,本发明应用反胶束微球腐蚀玻璃表面,形成微米级孔坑的结构;所得玻璃基板为微米级孔坑玻璃,其呈现多孔结构,表面积大,结构稳定,耐磨。并且,本发明在所述微米级孔坑玻璃表面进行镀膜,膜能嵌入到玻璃孔里,可以得到切面呈波浪形的三维膜结构。因此,利用本发明提供的玻璃基板的镀膜方法不仅提高了薄膜和基板之间的结合力,而且提高了膜层之间的结合力,从而改善膜功能的稳定性和可靠性,利于应用。以上所述仅是本发明的优选实施方式,应当指出,对于使本
技术领域:
的专业技术人员,在不脱离本发明技术原理的前提下,是能够实现对这些实施例的多种修改的,而这些修改也应视为本发明应该保护的范围。当前第1页1 2 3