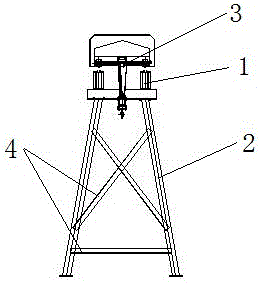
本实用新型属于公路桥梁设备
技术领域:
,具体涉及一种大吨位大跨径箱梁提升设备。
背景技术:
:近年来,国家对高速公路的大力投入,促使新建高速公路跨线桥梁、跨河桥建设越来越多。高速公路桥梁绝大多数为预制梁,很多项目部在预制梁施工中,梁场设置门式起重机,这样在架梁施工时只有用吊车将砼梁起吊,不论是用门式起重机还是用吊车,其费用都是非常的高。技术实现要素:本实用新型的目的是为了节约成本、解决传统提梁设备的弊端。为此,本实用新型提供了一种大吨位大跨径箱梁提升设备,包括主梁、支腿和起重天车,支腿支撑起主梁,起重天车活动坐落在主梁上,所述的主梁包括两条平行的作为起重天车轨道的工字钢,主梁的四角位置分别连接着一条支腿,位于主梁一端的两条支腿之间连接着平联件,位于主梁一侧的两条支腿之间连接着钢拉杆,每一条支腿和主梁之间还连接有一个斜撑。所述的斜撑一端连接在支腿上,钢拉杆的一端依次穿过支腿和斜撑将两者固定。所述的钢拉杆的端部套有槽钢,槽钢外端设置螺母,螺母套在钢拉杆的外端进行锁紧。所述的主梁与支腿之间以及主梁与斜撑之间均通过法兰板用高强螺栓连接。所述的法兰板下表面上焊接有多个与支腿或斜撑侧壁连接的加劲板。所述的位于主梁一端的两条支腿呈八字形连接在主梁下部,这两条支腿之间的平联件包括水平平联件和交叉型平联件。所述的起重天车为电动卷扬机。所述的支腿底部装有万向载重轮。所述的主梁为45a型工字钢,主梁长9m;所述的支腿、平联件与斜撑均为φ245×10mm钢管,支腿高度为6.0m,位于主梁两端的支腿间的跨径为8.24m,该大吨位大跨径箱梁提升设备承受重量为80t。本实用新型的有益效果:本实用新型提供的这种大吨位大跨径箱梁提升设备,大大解决了梁场的提梁转运问题,本设备具有自重轻,安全好,耗电量小,效率高,结构简单,操作方便,适应性强等优点,且不需要专业安装操作人员,也不需要通过质量技术监督部门的验收,就可以投入使用,安全可靠,提高了施工功效、降低了施工成本,特别适用于场地少、梁座少的施工现场。附图说明以下将结合附图对本实用新型做进一步详细说明。图1是本实用新型的主视结构示意图。图2是本实用新型的侧视结构示意图。图3是支腿连接结构示意图。图4是法兰板结构示意图。图5是加劲板结构示意图。附图标记说明:1、主梁;2、支腿;3、起重天车;4、平联件;5、钢拉杆;6、斜撑;7、法兰板;8、加劲板。具体实施方式架梁施工时只有用吊车将砼梁起吊,不论是用门式起重机还是用吊车,其费用都是非常的高,为控制施工成本,不在梁场设置门式起重机,而是选择一种简单快捷,安全方便,投资少的简易提梁门架设备。实施例1:本实施例提供一种大吨位大跨径箱梁提升设备,如图1和图2所示,包括主梁1、支腿2和起重天车3,支腿2支撑起主梁1,起重天车3活动坐落在主梁1上,所述的主梁1包括两条平行的作为起重天车3轨道的工字钢,主梁1的四角位置分别连接着一条支腿2,位于主梁1一端的两条支腿2之间连接着平联件4,位于主梁1一侧的两条支腿2之间连接着钢拉杆5,每一条支腿2和主梁1之间还连接有一个斜撑6。大吨位大跨径箱梁简易提升设备的应用,大大解决了梁场的提梁转运问题,本设备具有自重轻,安全好,耗电量小,效率高,结构简单,操作方便,适应性强等优点,且不需要专业安装操作人员,也不需要通过质量技术监督部门的验收,就可以投入使用,安全可靠,提高了施工功效、降低了施工成本,特别适用于场地少、梁座少的施工现场。实施例2:本实施例在实施例1的基础上进一步进行说明,如图3所示,本实施例中,斜撑6一端连接在支腿2上,钢拉杆5的一端依次穿过支腿2和斜撑6将两者固定。钢拉杆5的端部套有槽钢,槽钢外端设置螺母,螺母套在钢拉杆5的外端进行锁紧。上述结构,在主梁1和支腿2最不利的受压弯曲变形点增加了精轧螺纹钢对拉措施,提梁设备充分考虑箱梁制梁台座横移至运梁车的应有宽度空间、提升至运梁车后梁面距离精轧螺纹钢之前的应有高度空间。实施例3:结合图3所示,主梁1与支腿2之间以及主梁1与斜撑6之间均通过如图4所示的法兰板7用高强螺栓连接。法兰板7下表面上焊接有多个与支腿2或斜撑6侧壁连接的加劲板8(结合图3和图5所示)。主梁1与支腿2采用刚性连接,法兰螺栓连接要求螺栓孔位置偏差不得大于2mm,法兰接触面要平整配对。根据现场施工情况,采用拓印法进行施工,即支腿法制作完成后,每组法兰与主梁配装,配装时两个接触面要平整、中间无杂物,配装结束后用型钢等将每组支腿法兰刚性连接并移植到支腿上,然后进行支腿的制作;加劲板8的设置使得结构更加稳固,整体结构承受力更强。实施例4:为了结构更加稳固,本实施例中,除了上述几个实施例的结构外,位于主梁1一端的两条支腿2呈八字形连接在主梁1下部,这两条支腿2之间的平联件4包括水平平联件和交叉型平联件。本实施例的起重天车3为电动卷扬机,采用旧有架桥机进行改造,桁架主梁1自行加工制作。为了方便整体设备的移动,本实施例中,支腿2底部装有万向载重轮,依靠万向载重轮可以实现整体箱梁提升设备的移动。实施例5:在上述几个实施例的基础上,本实施例提供一种具体尺寸的箱梁提升设备,主梁1为45a型工字钢,主梁1长9m;所述的支腿2、平联件4与斜撑6均为φ245×10mm钢管,支腿2高度为6.0m,位于主梁1两端的支腿2间的跨径为8.24m,该大吨位大跨径箱梁提升设备承受重量为80t。1.新型提梁设备验算流程如下:1)常规验算新型提梁设备设计荷载包括:恒载(桁架自重及电动卷扬机重量)、起吊荷载(箱梁重量)、风荷载,此外考虑1.4的活载系数。新型提梁设备最大工作风速不超过6级,超过此风速时停止工作。设计考虑各项荷载:(1)恒载(桁架自重及电动卷扬机重量)P1=11.4t;(2)起吊荷载P2=80t;(3)大临结构设计验算风速按30年一遇基本风速29.3m/s计算,风荷载标准值Wk=1.2kN/m2。荷载组合:1.2×P1+1.2×P2+1.4×Wk。采取两种工况进行计算:工况一:电动卷扬机移动至跨中部位。工况二:电动卷扬机移动至左侧或右侧部位。计算结果如下表1-1所示:表1-1主梁材料参数表(普工45a)截面上下对称截面面积A=10200mm2抗弯惯性矩I=322000000mm4自重W=0.785kN/m抗弯模量W=1431111mm3面积矩S=829582mm3塑性发展系数γ=1.05结论:工况一荷载位置距左端4.0m。工况二荷载位置距左端0.0m。计算得出结论:在第二跨最大挠度1.72mm,最大挠跨比1/2092≤1/400。最大应力σ=Mmax/γ/W=142.5MPa≤f=205MPa。满足要求。2)Midas模型验算为了确保设计结构安全可靠性,利用Midas建立模型验算。验算结果见下表1-2所示,新型提梁设备各杆件的强度满足规范要求,其结构变形满足要求。表1-2Midas设计验算结果统计分析表通过以上的计算结果可知,吊架各杆件的强度满足要求,其结构变形也满足要求。2.新型提梁设备制作流程如下:1)放样号料:根据施工图纸要求,对新型提梁设备各部分进行加工并预留加工余量,然后在板材上标出基准线和孔的规划线标号。2)切割:新型提梁设备加工均采用火焰切割,根据现在的工艺要求,为了避免较大的切割变形,尽量采用数控切割机。钢板应置于专用的切割平台上,以保证钢板平直。切割前应将钢材表面距切割线50mm范围内清理干净。3)矫正、弯曲及表面加工:零件的矫正应采用平板机和型材矫直机进行,如用锤击其表面不得有明显的凹面和损伤,表面划痕深度不得大于0.5mm。4)制孔、组对及安装:本工程主要节点采用10.9级摩擦型高度螺栓进行连接,节点板等连接螺栓孔制孔应用钻床,制孔的位置应准确,孔距允许偏差控制在允许范围内。5)组对与焊接:构件组装前应对连接表面及焊缝边缘30-50mm范围内进行清理,应将铁锈、毛刺和油污等清除干净。多层焊应连续施焊,其中每一层焊道焊完之后应及时清理,如发现有影响焊接质量的缺陷,必须清除后再焊接。6)设备拼装:主梁与支腿之间采用高强螺栓法兰连接,属刚性连接,法兰螺栓连接要求螺栓孔位置偏差不得大于2mm,法兰接触面要平整配对。根据现场施工情况,采用拓印法进行施工。即支腿法制作完成后,每组法兰与主梁配装,配装时两个接触面要平整、中间无杂物,配装结束后用型钢等将每组支腿法兰刚性连接并移植到支腿上,然后进行支腿的制作。7)吊装试验:①静载试验:起升额定荷载,再逐步加载到额定荷载的1.25倍,制动应平稳可靠,主要检查有无永久变形。②动载试验:以110%的额定荷载,同时启动、起升、运行。反复运转,试验时间大于1小时,主要检查起吊系统的起升、制动性能及运行状态是否正常,检查验收合格后再进行箱梁吊装工作。大吨位大跨径箱梁简易提升设备的操作方式与普通提升设备方式一致,这里不一一叙述。综上所述,本实用新型的这种大吨位大跨径箱梁简易提升设备,充分考虑设计箱梁混凝土超方加重、提梁支撑点受力不均、型钢材料锈蚀及焊缝质量折减系数等因素,节约了成本、解决了传统提梁设备的弊端。以上例举仅仅是对本实用新型的举例说明,并不构成对本实用新型的保护范围的限制,凡是与本实用新型相同或相似的设计均属于本发明的保护范围之内。当前第1页1 2 3