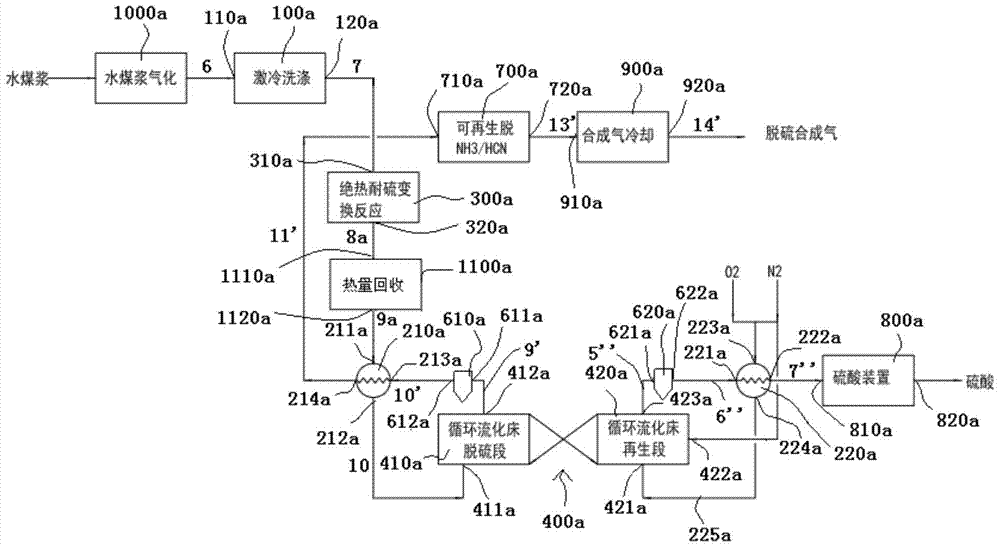
本发明涉及煤或其它含碳材料的气化产生的粗合成气中脱除杂质的净化技术领域,特别涉及一种结合耐硫变换和循环流化床热法脱硫的合成气净化方法及装置和应用。本发明除去合成气中含硫化合物、砷及其化合物、硒及其化合物、轻质芳烃和痕量的杂质,杂质例如氨、氰化物、汞、氯化氢,适用于该领域的新建或改造项目。
背景技术:在现有的技术和工业实践中,通常采用两种方法实现从合成气中除去酸性气体以及其他杂质。一种是使用溶剂进行物理或化学的液相吸收;一种是使用固体吸附剂在固定床中脱除。通过液相吸收脱除气体中的硫化合物,已经实现工业化有Linde和Lurgi许可的Rectisol以及上海国际化建工程咨询公司的分流式低温甲醇洗(专利号:ZL200910052424.1),该工艺采用甲醇为吸收溶剂,在极低的温度下操作,需消耗大量冷量,对设备材质的要求较高且工艺流程复杂,导致装置成本投资高。此外,其他实现液相吸收脱除气体中的硫化合物工业化还有Selexol工艺,该工艺中使用聚乙二醇二甲醚为溶剂,但该工艺对脱除合成气中的COS有一定的困难,如要将酸性气体中浓度高的COS除去,需增加COS水解单元,且溶剂的循环量大导致操作成本高。来自气化的高温合成气经过耐硫变换反应后,温度通常在270-450℃,而以上液相吸收法在这样的高温气体中是无效的,因为这些方法典型地需要在零度以下较低的温度下操作,因此合成气需要进行热回收、冷却处理,以满足液相吸收法除去杂质的低温条件。显而易见,这样的冷却、热回收和相关处理会导致下游合成气利用的热效率降低。通过使用固体吸附剂在固定床中脱除气体中的硫化合物的方法存在处理能力小,吸附剂再生困难的缺点。
技术实现要素:本发明所要解决的技术问题之一在于针对现有技术所存在的不足之处而提供一种结合耐硫变换和循环流化床热法脱硫的合成气净化方法。本发明所要解决的技术问题之二在于提供实现上述合成气净化方法的装置。本发明所要解决的技术问题之三在于提供上述合成气净化方法的应用。作为本发明第一方面的第一种结合耐硫变换和循环流化床热法脱硫的合成气净化方法,其是将经过煤或其它含碳材料的气化产生第一粗合成气送入一水激冷洗涤装置进行水激冷洗涤形成第二粗合成气送入耐硫变换反应系统;在所述耐硫变换反应系统内,第二粗合成气发生如下反应CO+H2O→CO2+H2形成第三粗合成气送出;送出的第三粗合成气进入热量回收装置进行降温形成第四粗合成气送出;送出的第四粗合成气进入第一换热器,与进入第一换热器的第一脱硫后的合成气换热后形成第五粗合成气送出;送出的第五粗合成气由循环流化床的吸附反应器中的提升管的底部进入到循环流化床的吸附反应器中的提升管内,与从循环流化床的再生反应器来的再生固体吸附剂在循环流化床的吸附反应器中的提升管内混合反应,混合反应过程中所述再生固体吸附剂中的活性金属氧化物MO与第五粗合成气中的含有硫杂质反应,产生载有硫的吸附剂MS,具体反应式如下:H2S+MO→MS+H2OCOS+MO→CO2+MS其中,M为存在于再生固体吸附剂中的金属;混合反应过程后形成的含固体吸附颗粒的第二脱硫后的合成气由循环流化床的吸附反应器中的旋风分离器上部进入到所述循环流化床的吸附反应器中的旋风分离器内进行旋风分离;经过所述循环流化床的吸附反应器中的旋风分离器分离后形成第三脱硫后的合成气,所述的第三脱硫后的合成气由所述循环流化床的吸附反应器中的旋风分离器的顶部送出,送出的第三脱硫后的合成气经过第一过滤器过滤后形成所述的第一脱硫后的合成气送入到第一换热器内,经过与进入第一换热器内的第四粗合成气换热后形成所述的第四脱硫后的合成气进入一可再生脱NH3/HCN装置中脱除第四脱硫后的合成气中的NH3/HCN形成第五脱硫后的合成气,所述第五脱硫后的合成气送入一冷却装置中进行冷却形成第六脱硫后的合成气送出;经过所述循环流化床的吸附反应器中的旋风分离器分离后的固体吸附颗粒一部分为活性金属氧化物MO,另一部分为载有硫的吸附剂MS,经过所述旋风分离器分离后的活性金属氧化物MO和载有硫的吸附剂MS通过所述循环流化床的吸附反应器中的下降管循环进入到循环流化床的吸附反应器中的提升管内,活性金属氧化物MO与循环流化床的吸附反应器中的提升管内的第五粗合成气中的含有硫杂质反应,产生载有硫的吸附剂MS;经过所述循环流化床的吸附反应器中的旋风分离器分离后的载有硫的吸附剂MS通过所述循环流化床的吸附反应器中的下降管进入到循环流化床的再生反应器中的提升管内,与进入循环流化床的再生反应器中的提升管内的再生空气或O2与N2的混合气体混合反应,使得载有硫的吸附剂MS得以再生形成所述的再生固体吸附剂,具体反应式如下:MS+3/2O2→MO+SO2;混合反应后形成的含有所述的再生固体吸附剂的第一富SO2的气体进入到循环流化床的再生反应器中的旋风分离器中进行旋风分离,循环流化床的再生反应器中的旋风分离器分离后的第二富SO2的气体由所述循环流化床的再生反应器中的旋风分离器的顶部送出,经过第二过滤器过滤后所形成的第三富SO2的气体送入第二换热器,与进入到所述第二换热器内的再生所需要的所述的再生空气或O2与N2的混合气体进行换热形成第四富SO2的气体送出至下游去生产硫酸或者单质硫;循环流化床的再生反应器中的旋风分离器分离后的所述的再生固体吸附剂通过所述循环流化床的再生反应器中的下降管送入到循环流化床的吸附反应器中的提升管内。在本发明第一种结合耐硫变换和循环流化床热法脱硫的合成气净化方法的一个优选实施例中,在所述可再生脱NH3/HCN装置与所述冷却装置之间增加一脱除汞和氯化物装置,以脱除所述第五脱硫后的合成气中的汞和氯化物,经过脱除汞和氯化物装置脱除汞和氯化物的第七脱硫后的合成气送入所述冷却装置中进行冷却形成第六脱硫后的合成气送出。在本发明第一种结合耐硫变换和循环流化床热法脱硫的合成气净化方法的一个优选实施例中,所述经过煤或其它含碳材料的气化产生第一粗合成气为水煤浆气化、粉煤气化或碎煤固定床气化产生第一粗合成气。在本发明第一种结合耐硫变换和循环流化床热法脱硫的合成气净化方法的一个优选实施例中,所述第二粗合成气的温度为180-250℃。在本发明第一种结合耐硫变换和循环流化床热法脱硫的合成气净化方法的一个优选实施例中,所述耐硫变换反应系统使用绝热耐硫变换反应器或等温耐硫变换反应器或本申请人申请的中国专利号ZL201210040295.6发明名称为带有支撑式槽孔板分布器的径向或轴径向固定床反应器;所述带有支撑式槽孔板分布器的径向或轴径向固定床反应器,包括承压壳体和设置在所述承压壳体内且与承压壳体同轴的催化剂外框和气体收集中心管,所述承压壳体上设置有气体进口和气体出口,所述催化剂外框由支撑在承压壳体内壁上的支撑式槽孔板分布器构成;所述支撑式槽孔板分布器有由规格一致的若干槽孔分布板相互搭接构成;所述的槽孔分布板采用角钢和支座支撑在承压壳体的内壁上,所述角钢与支座之间采用螺栓连接,所述支座固定在承压壳体的内壁上,所述槽孔分布板与承压壳体之间保留一定的弧形间隙;所述槽孔分布板为其上开设有密集槽孔的弧形长条板。在本发明第一种结合耐硫变换和循环流化床热法脱硫的合成气净化方法的一个优选实施例中,所述循环流化床的吸附反应器和循环流化床的再生反应器形成一流化催化裂化FCC工艺系统。在本发明第一种结合耐硫变换和循环流化床热法脱硫的合成气净化方法的一个优选实施例中,所述第三粗合成气的温度为270-450℃。在本发明第一种结合耐硫变换和循环流化床热法脱硫的合成气净化方法的一个优选实施例中,所述第四粗合成气的温度为75-200℃。在本发明第一种结合耐硫变换和循环流化床热法脱硫的合成气净化方法的一个优选实施例中,所述第五粗合成气的温度为300-550℃。在本发明第一种结合耐硫变换和循环流化床热法脱硫的合成气净化方法的一个优选实施例中,所述再生固体吸附剂中的活性金属氧化物MO与第五粗合成气中的含有硫杂质反应时的温度为320-580℃。在本发明第一种结合耐硫变换和循环流化床热法脱硫的合成气净化方法的一个优选实施例中,所述第三脱硫后的合成气中的硫含量低至0.5-5ppmv。在本发明第一种结合耐硫变换和循环流化床热法脱硫的合成气净化方法的一个优选实施例中,所述第四脱硫后的合成气的温度为170-230℃。在本发明第一种结合耐硫变换和循环流化床热法脱硫的合成气净化方法的一个优选实施例中,所述第六脱硫后的合成气送入下游的脱二氧化碳单元装置中,以脱除其中的二氧化碳。在本发明第一种结合耐硫变换和循环流化床热法脱硫的合成气净化方法的一个优选实施例中,所述脱二氧化碳单元装置为液相吸收脱二氧化碳单元装置或干法化学吸附脱二氧化碳单元装置。在本发明第一种结合耐硫变换和循环流化床热法脱硫的合成气净化方法的一个优选实施例中,所述可再生脱NH3/HCN装置为吸附床。在本发明第一种结合耐硫变换和循环流化床热法脱硫的合成气净化方法的一个优选实施例中,所述吸附床为固定式吸附床。在本发明第一种结合耐硫变换和循环流化床热法脱硫的合成气净化方法的一个优选实施例中,所述脱除汞和氯化物装置为保护床。在本发明第一种结合耐硫变换和循环流化床热法脱硫的合成气净化方法的一个优选实施例中,所述第一富SO2的气体的温度为650-750℃。在本发明第一种结合耐硫变换和循环流化床热法脱硫的合成气净化方法的一个优选实施例中,所述第四富SO2的气体的温度为330-530℃。在本发明第一种结合耐硫变换和循环流化床热法脱硫的合成气净化方法的一个优选实施例中,所述进入循环流化床的再生反应器中的提升管内的再生空气或O2与N2的混合气体的温度为450-550℃。在本发明第一种结合耐硫变换和循环流化床热法脱硫的合成气净化方法的一个优选实施例中,所述M为存在于再生固体吸附剂中的金属。例如Zn。作为本发明第一方面的实现上述第一种结合耐硫变换和循环流化床热法脱硫的合成气净化方法的装置,包括:一水激冷洗涤装置,所述水激冷洗涤装置具有一粗合成气输入口和粗合成气输出口,该水激冷洗涤装置的粗合成气输入口通过一第一粗合成气输送管线连接一煤气化装置;一耐硫变换反应系统,该耐硫变换反应系统具有一粗合成气输入口和粗合成气输出口,所述耐硫变换反应系统的粗合成气输入口通过一第二粗合成气输送管线连接所述水激冷洗涤装置的粗合成气输出口;一热量回收装置,该热量回收装置具有一粗合成气输入口和粗合成气输出口,所述热量回收装置的粗合成气输入口通过一第三粗合成气输送管线连接所述耐硫变换反应系统的粗合成气输出口;一第一换热器,所述第一换热器具有一粗合成气输入口、一粗合成气输出口、一脱硫后的合成气输入口和一脱硫后的合成气输出口,所述第一换热器的粗合成气输入口通过一第四粗合成气输送管线连接所述热量回收装置的粗合成气输出口;一循环流化床的吸附反应器,所述循环流化床的吸附反应器包括一提升管、一旋风分离器和一下降管,所述循环流化床的吸附反应器的提升管的底部具有一粗合成气输入口,所述循环流化床的吸附反应器的提升管的下部配置有再生吸附剂入口和循环吸附剂入口,所述循环流化床的吸附反应器的提升管的上部配置有含固体吸附颗粒的脱硫后的合成气出口;所述循环流化床的吸附反应器的旋风分离器的上部配置有含固体吸附颗粒的脱硫后的合成气入口,所述循环流化床的吸附反应器的旋风分离器的顶部配置有脱硫后的合成气输出口,所述循环流化床的吸附反应器的旋风分离器的下部配置有载有硫的吸附剂出口;所述循环流化床的吸附反应器的下降管的上部配置有载有硫的吸附剂入口,所述循环流化床的吸附反应器的下降管的下部配置有一载有硫的吸附剂循环出口和一载有硫的吸附剂待再生出口;所述循环流化床的吸附反应器的提升管底部的粗合成气输入口通过一第五粗合成气输送管线连接所述的第一换热器的粗合成气输出口;所述循环流化床的吸附反应器的提升管下部的循环吸附剂入口与所述循环流化床的吸附反应器的下降管的载有硫的吸附剂循环出口连接,所述循环流化床的吸附反应器的提升管上部的含固体吸附颗粒的脱硫后的合成气出口通过一含固体吸附颗粒的第二脱硫后的合成气输送管线与所述循环流化床的吸附反应器的旋风分离器上部的含固体吸附颗粒的脱硫后的合成气入口连接;一第一过滤器,所述第一过滤器具有一脱硫后的合成气输入口和一脱硫后的合成气输出口,所述第一过滤器的脱硫后的合成气输入口通过一第三脱硫后的合成气输送管线与所述循环流化床的吸附反应器的旋风分离器顶部的脱硫后的合成气输出口连接,所述第一过滤器的脱硫后的合成气输出口通过一第一脱硫后的合成气输送管线与所述第一换热器的脱硫后的合成气输入口连接;一循环流化床的再生反应器,所述循环流化床的再生反应器包括一提升管、一旋风分离器和一下降管,所述循环流化床的再生反应器的提升管的下部配置有载有硫的吸附剂待再生入口,所述循环流化床的再生反应器的提升管的底部配置有再生空气或O2与N2的混合气体入口,所述循环流化床的再生反应器的提升管的上部配置有含有再生固体吸附剂的富SO2的气体出口;所述循环流化床的再生反应器的旋风分离器的上部配置有含有再生固体吸附剂的富SO2的气体入口,所述循环流化床的再生反应器的旋风分离器的顶部配置有富SO2的气体出口,所述循环流化床的再生反应器的旋风分离器的下部配置有再生吸附剂出口;所述循环流化床的再生反应器的下降管的上部配置有再生吸附剂入口,所述循环流化床的再生反应器的下降管的下部配置有再生吸附剂出口;所述循环流化床的再生反应器的提升管下部的载有硫的吸附剂入口与所述循环流化床的吸附反应器的下降管的吸附剂待再生出口连接;所述循环流化床的再生反应器的旋风分离器上部的含有再生固体吸附剂的富SO2的气体入口通过一含有再生固体吸附剂的第一富SO2的气体输送管线与所述循环流化床的再生反应器的提升管上部的含有再生固体吸附剂的富SO2的气体出口连接;所述循环流化床的再生反应器的旋风分离器的下部的再生固体吸附剂出口与所述循环流化床的再生反应器的下降管的上部再生固体吸附剂入口连接;所述循环流化床的再生反应器的下降管的下部的再生吸附剂出口通过一再生吸附剂输送管线与所述循环流化床的吸附反应器的提升管下部的再生吸附剂入口连接;一第二过滤器,所述第二过滤器具有一富SO2的气体入口和富SO2的气体出口,所述第二过滤器的富SO2的气体入口与所述循环流化床的再生反应器的旋风分离器顶部的富SO2的气体出口通过一第二富SO2的气体输送管线连接;一第二换热器,所述第二换热器具有一富SO2的气体入口、富SO2的气体出口、再生空气或O2与N2的混合气体入口、再生空气或O2与N2的混合气体出口,所述第二换热器的富SO2的气体入口通过一第三富SO2的气体输送管线连接所述第二过滤器的富SO2的气体出口,所述第二换热器的再生空气或O2与N2的混合气体入口连接空气源或O2与N2的混合气体源;所述第二换热器的再生空气或O2与N2的混合气体出口通过再生空气或O2与N2的混合气体输送管线连接所述循环流化床的再生反应器的提升管底部的再生空气或O2与N2的混合气体入口;一可再生脱NH3/HCN装置,所述可再生脱NH3/HCN装置具有脱硫后的合成气入口和脱硫后的合成气出口,所述再生脱NH3/HCN装置的脱硫后的合成气入口通过一第四脱硫后的合成气输送管线与所述第一换热器的脱硫后的合成气输出口连接;一冷却装置,所述冷却装置具有脱硫后的合成气入口和脱硫后的合成气出口,所述冷却装置的脱硫后的合成气入口通过一第五脱硫后的合成气输送管线与所述可再生脱NH3/HCN装置的脱硫后的合成气出口连接,所述冷却装置的脱硫后的合成气出口通过一第六脱硫后的合成气输送管线与下游的脱二氧化碳单元装置连接。在本发明实现上述第一种结合耐硫变换和循环流化床热法脱硫的合成气净化方法的装置的一个优选实施例中,在所述可再生脱NH3/HCN装置与所述冷却装置之间增加一脱除汞和氯化物装置,所述脱除汞和氯化物装置具有脱硫后的合成气入口和脱硫后的合成气出口,所述脱除汞和氯化物装置的脱硫后的合成气入口通过一第五脱硫后的合成气输送管线与所述可再生脱NH3/HCN装置的脱硫后的合成气出口连接,所述脱除汞和氯化物装置的脱硫后的合成气出口通过一第七脱硫后的合成气输送管线与所述冷却装置的脱硫后的合成气入口连接。在本发明实现上述第一种结合耐硫变换和循环流化床热法脱硫的合成气净化方法的装置的一个优选实施例中,所述煤气化装置为水煤浆气化装置、粉煤气化装置或碎煤固定床气化装置。在本发明实现上述第一种结合耐硫变换和循环流化床热法脱硫的合成气净化方法的装置的一个优选实施例中,所述耐硫变换反应系统使用绝热耐硫变换反应器或等温耐硫变换反应器或本申请人申请的中国专利号ZL201210040295.6、发明名称为带有支撑式槽孔板分布器的径向或轴径向固定床反应器;所述带有支撑式槽孔板分布器的径向或轴径向固定床反应器,包括承压壳体和设置在所述承压壳体内且与承压壳体同轴的催化剂外框和气体收集中心管,所述承压壳体上设置有气体进口和气体出口,所述催化剂外框由支撑在承压壳体内壁上的支撑式槽孔板分布器构成;所述支撑式槽孔板分布器有由规格一致的若干槽孔分布板相互搭接构成;所述的槽孔分布板采用角钢和支座支撑在承压壳体的内壁上,所述角钢与支座之间采用螺栓连接,所述支座固定在承压壳体的内壁上,所述槽孔分布板与承压壳体之间保留一定的弧形间隙;所述槽孔分布板为其上开设有密集槽孔的弧形长条板。在本发明实现上述第一种结合耐硫变换和循环流化床热法脱硫的合成气净化方法的装置的一个优选实施例中,所述循环流化床的吸附反应器和循环流化床的再生反应器形成一流化催化裂化FCC工艺系统。在本发明实现上述第一种结合耐硫变换和循环流化床热法脱硫的合成气净化方法的装置的一个优选实施例中,所述脱二氧化碳单元装置为液相吸收脱二氧化碳单元装置或干法化学吸附脱二氧化碳单元装置。在本发明实现上述第一种结合耐硫变换和循环流化床热法脱硫的合成气净化方法的装置的一个优选实施例中,所述可再生脱NH3/HCN装置为吸附床。在本发明实现上述第一种结合耐硫变换和循环流化床热法脱硫的合成气净化方法的装置的一个优选实施例中,所述吸附床为固定式吸附床。在本发明实现上述第一种结合耐硫变换和循环流化床热法脱硫的合成气净化方法的装置的一个优选实施例中,所述脱除汞和氯化物装置为保护床。作为本发明第三方面的应用,本发明的第一种结合耐硫变换和循环流化床热法脱硫的合成气净化方法可以用于IGCC、合成氨、甲醇合成、F-T合成烃类油类产品、合成气制SNG、生产氢气、合成气制乙二醇的粗合成气的净化工艺。作为本发明第一方面的第二种结合耐硫变换和循环流化床热法脱硫的合成气净化方法,其是将经过煤或其它含碳材料的气化产生第六粗合成气送入一水激冷洗涤装置进行水激冷洗涤形成第七粗合成气送入到耐硫变换反应系统;在所述耐硫变换反应系统内,第七粗合成气发生如下反应CO+H2O→CO2+H2形成第八粗合成气送出;送出的第八粗合成气进入热量回收装置进行降温形成第九粗合成气送出;送出的第九粗合成气进入第三换热器,与进入第三换热器的第八脱硫后的合成气换热后形成第十粗合成气送出;送出的第十粗合成气进入到循环流化床脱硫系统的吸附反应脱硫段,与进入循环流化床脱硫系统的吸附反应脱硫段的再生固体吸附剂混合反应,混合反应过程中所述再生固体吸附剂中的活性金属氧化物MO与第十粗合成气中的含有硫杂质反应,产生载有硫的吸附剂MS,具体反应式如下:H2S+MO→MS+H2OCOS+MO→CO2+MS其中,M为存在于再生固体吸附剂中的金属;混合反应过程后形成的含固体吸附颗粒的脱硫后的合成气经过循环流化床脱硫系统的吸附反应脱硫段中的旋风分离器旋风分离后形成第九脱硫后的合成气,所述的第九脱硫后的合成气经过循环流化床脱硫系统的吸附反应脱硫段中的过滤器过滤后形成所述的第八脱硫后的合成气送入到第三换热器内,经过与进入第三换热器内的第九粗合成气换热后形成所述的第十脱硫后的合成气送入一可再生脱NH3/HCN装置中脱除第十脱硫后的合成气中的NH3/HCN形成第十一脱硫后的合成气,所述第十一脱硫后的合成气送入一冷却装置中进行冷却形成第十二脱硫后的合成气送出;经过循环流化床脱硫系统的吸附反应脱硫段中的旋风分离器旋风分离后的载有硫的吸附剂MS进入到循环流化床脱硫系统的再生段中,与进入循环流化床脱硫系统的再生段的再生空气或O2与N2的混合气体混合反应,使得载有硫的吸附剂MS得以再生形成所述的再生固体吸附剂,具体反应式如下:MS+3/2O2→MO+SO2;混合反应后形成的含有所述的再生固体吸附剂的第五富SO2的气体进入到循环流化床脱硫系统的再生段中的旋风分离器中进行旋风分离,旋风分离后的第六富SO2的气体经过循环流化床脱硫系统的再生段的过滤器过滤后所形成的第七富SO2的气体送入第四换热器,与进入到所述第四换热器内的再生所需要的所述的再生空气或O2与N2的混合气体进行换热形成第八富SO2的气体送出至下游去生产硫酸或者单质硫;旋风分离后的所述的再生固体吸附剂送入到循环流化床脱硫系统的吸附反应脱硫段中。在本发明第二种结合耐硫变换和循环流化床热法脱硫的合成气净化方法的一个优选实施例中,所述送出的第九粗合成气进入热量回收装置进行降温后再分出第十一粗合成气进行液相吸收脱硫脱碳后得到净化气。在本发明第二种结合耐硫变换和循环流化床热法脱硫的合成气净化方法的一个优选实施例中,所述净化气送入一提氢装置经过提氢后得到氢气送出。在本发明第二种结合耐硫变换和循环流化床热法脱硫的合成气净化方法的一个优选实施例中,所述冷却装置送出第十二脱硫后的合成气送入一PSA净化工段净化后得到氢气送出。在本发明第二种结合耐硫变换和循环流化床热法脱硫的合成气净化方法的一个优选实施例中,所述净化气送入一提氢装置经过提氢后得到氢气送出;所述冷却装置送出第十二脱硫后的合成气送入一PSA净化工段净化后得到氢气送出。在本发明第二种结合耐硫变换和循环流化床热法脱硫的合成气净化方法的一个优选实施例中,所述净化气送入一提氢装置经过提氢后得到氢气送出;所述冷却装置送出第十二脱硫后的合成气送入一PSA净化工段净化后得到氢气送出,两股氢气送入一合成氨装置中,补充N2得到产品氨。在本发明第二种结合耐硫变换和循环流化床热法脱硫的合成气净化方法的一个优选实施例中,所述经过煤或其它含碳材料的气化产生第六粗合成气为水煤浆气化、粉煤气化或碎煤固定床气化产生第六粗合成气。在本发明第二种结合耐硫变换和循环流化床热法脱硫的合成气净化方法的一个优选实施例中,所述第七粗合成气的温度为180-250℃。在本发明第二种结合耐硫变换和循环流化床热法脱硫的合成气净化方法的一个优选实施例中,所述耐硫变换反应系统使用绝热耐硫变换反应器或等温耐硫变换反应器或本申请人申请的中国专利号ZL201210040295.6、发明名称为带有支撑式槽孔板分布器的径向或轴径向固定床反应器或本申请人申请的中国专利号ZL201320176372.0、发明名称为一种将催化剂置于换热管之间的等温固定床反应器或本申请人申请的中国专利号ZL200910056432.4、发明名称为分流式等温耐硫变换工艺及其设备;所述带有支撑式槽孔板分布器的径向或轴径向固定床反应器,包括承压壳体和设置在所述承压壳体内且与承压壳体同轴的催化剂外框和气体收集中心管,所述承压壳体上设置有气体进口和气体出口,所述催化剂外框由支撑在承压壳体内壁上的支撑式槽孔板分布器构成;所述支撑式槽孔板分布器有由规格一致的若干槽孔分布板相互搭接构成;所述的槽孔分布板采用角钢和支座支撑在承压壳体的内壁上,所述角钢与支座之间采用螺栓连接,所述支座固定在承压壳体的内壁上,所述槽孔分布板与承压壳体之间保留一定的弧形间隙;所述槽孔分布板为其上开设有密集槽孔的弧形长条板;所述一种将催化剂装于换热管之间的等温固定床反应器,包括承压壳体、安装在承压壳体内的多个换热管;在所述承压壳体上设有气体进口、换热介质出口、气体出口、换热介质进口和催化剂卸料口;所述换热管的两端分别与所述换热介质出口和换热介质进口相连接;所述多个换热管之间存在空隙形成催化剂填充区,并且气体进口、换热管之间的空隙以及气体出口形成气体通道;所述分流式等温耐硫变换设备,至少包括一第一变换反应器和一锅炉给水预热器以及热回收冷却系统,第一变换反应器的第一变换气出口管与锅炉给水预热器进气口连接,锅炉给水预热器出气口与所述热回收冷却系统连接;第一变换反应器的原料气入口接原料煤气;所述的分流式等温耐硫变换设备还包括一汽包,所述第一变换反应器为等温变换反应器,所述第一变换反应器通过一由泵及管线构成的强制循环移热回路与汽包连接,所述锅炉给水预热器的锅炉给水管与汽包连接,向汽包输送预热后的锅炉给水;原料煤气配入过热蒸汽,将温度提高至200-300℃后通过第一变换反应器的原料气入口进入第一变换反应器进行变换反应,产出第一变换气,第一变换气通过第一变换气出口管送入所述锅炉给水预热器回收热量后,再送入所述热回收冷却系统分离出变换气和冷凝液;第一变换反应器副产中压饱和蒸汽,副产中压饱和蒸汽通过强制循环移热回路送入汽包进行分离,所述汽包分离出的中压饱和蒸汽通过汽包的蒸汽出口管送出;或者,所述分流式等温耐硫变换设备,至少包括一第一变换反应器和一锅炉给水预热器以及热回收冷却系统,第一变换反应器的第一变换气出口管与锅炉给水预热器进气口连接,锅炉给水预热器出气口与所述热回收冷却系统连接;第一变换反应器的原料气入口接原料煤气;所述的分流式等温耐硫变换设备还包括一第二变换反应器、一蒸汽过热器、一汽包,其中第一变换反应器为绝热变换反应器,第二变换反应器为等温变换反应器,其中第一变换反应器的第一变换气出口管与蒸汽过热器的第一变换气入口管直接,蒸汽过热器的第一变换气输送管与第二变换反应器的原料气入口连接,第二变换反应器的原料气入口还接原料煤气;所述第二变换反应器通过一由泵及管线构成的强制循环移热回路与汽包连接,第二变换反应器的第二变换气出口管与锅炉给水预热器进气口连接,所述锅炉给水预热器的锅炉给水管与汽包连接,向汽包输送预热后的锅炉给水;汽包的蒸汽出口管接蒸汽过热器的中压饱和蒸汽入口,蒸汽过热器的中压过热蒸汽出口管送出中压过热蒸汽;或者,所述分流式等温耐硫变换设备,至少包括一第一变换反应器和一锅炉给水预热器以及热回收冷却系统,第一变换反应器的第一变换气出口管与锅炉给水预热器进气口连接,锅炉给水预热器出气口与所述热回收冷却系统连接;第一变换反应器的原料气入口接原料煤气;所述的分流式等温耐硫变换设备还包括一第二变换反应器、一蒸汽过热器、一废热锅炉,其中第一变换反应器和第二变换反应器均为绝热变换反应器,其中第一变换反应器的第一变换气出口管与蒸汽过热器的第一变换气入口管直接,蒸汽过热器的第一变换气输送管与第二变换反应器的原料气入口连接,第二变换反应器的原料气入口还接原料煤气;所述第二变换反应器的第二变换气出口管与废热锅炉的第二变换气入口管直连,废热锅炉的第二变换气输送管与锅炉给水预热器进气口连接,所述锅炉给水预热器的锅炉给水管与废热锅炉的给水口连接,向废热锅炉输送预热后的锅炉给水;废热锅炉的蒸汽出口管接蒸汽过热器的中压饱和蒸汽入口,蒸汽过热器的中压过热蒸汽出口管送出中压过热蒸汽。在本发明第二种结合耐硫变换和循环流化床热法脱硫的合成气净化方法的一个优选实施例中,所述第八粗合成气的温度为270-450℃。在本发明第二种结合耐硫变换和循环流化床热法脱硫的合成气净化方法的一个优选实施例中,所述第九粗合成气的温度为75-200℃。在本发明第二种结合耐硫变换和循环流化床热法脱硫的合成气净化方法的一个优选实施例中,所述第十粗合成气的温度为300-550℃。在本发明第二种结合耐硫变换和循环流化床热法脱硫的合成气净化方法的一个优选实施例中,所述再生固体吸附剂中的活性金属氧化物MO与第十粗合成气中的含有硫杂质反应时的温度为320-580℃。在本发明第二种结合耐硫变换和循环流化床热法脱硫的合成气净化方法的一个优选实施例中,所述第九脱硫后的合成气中的硫含量低至0.5-5ppmv。在本发明第二种结合耐硫变换和循环流化床热法脱硫的合成气净化方法的一个优选实施例中,所述第十脱硫后的合成气的温度为170-230℃。在本发明第二种结合耐硫变换和循环流化床热法脱硫的合成气净化方法的一个优选实施例中,所述第十二脱硫后的合成气送入下游的脱二氧化碳单元装置中,以脱除其中的二氧化碳。在本发明第二种结合耐硫变换和循环流化床热法脱硫的合成气净化方法的一个优选实施例中,所述脱二氧化碳单元装置为液相吸收脱二氧化碳单元装置或干法化学吸附脱二氧化碳单元装置。在本发明第二种结合耐硫变换和循环流化床热法脱硫的合成气净化方法的一个优选实施例中,所述可再生脱NH3/HCN装置为吸附床。在本发明第二种结合耐硫变换和循环流化床热法脱硫的合成气净化方法的一个优选实施例中,所述吸附床为固定式吸附床。在本发明第二种结合耐硫变换和循环流化床热法脱硫的合成气净化方法的一个优选实施例中,所述第五富SO2的气体的温度为650-750℃。在本发明第二种结合耐硫变换和循环流化床热法脱硫的合成气净化方法的一个优选实施例中,所述第八富SO2的气体的温度为330-530℃。在本发明第二种结合耐硫变换和循环流化床热法脱硫的合成气净化方法的一个优选实施例中,所述进入所述循环流化床脱硫系统的再生段的再生空气或O2与N2的混合气体的温度为450-550℃。在本发明第二种结合耐硫变换和循环流化床热法脱硫的合成气净化方法的一个优选实施例中,所述第八富SO2的气体送出至下游的硫酸装置去生产硫酸。在本发明第二种结合耐硫变换和循环流化床热法脱硫的合成气净化方法的一个优选实施例中,所述第八富SO2的气体送出至下游的硫回收装置生产硫磺。在本发明第二种结合耐硫变换和循环流化床热法脱硫的合成气净化方法的一个优选实施例中,所述M为存在于再生固体吸附剂中的金属。例如Zn。作为本发明第一方面的实现上述第二种结合耐硫变换和循环流化床热法脱硫的合成气净化方法的装置,包括一水激冷洗涤装置,所述水激冷洗涤装置具有一粗合成气输入口和粗合成气输出口,该水激冷洗涤装置的粗合成气输入口通过一第六粗合成气输送管线连接一煤气化装置;一耐硫变换反应系统,该耐硫变换反应系统具有一粗合成气输入口和粗合成气输出口,所述耐硫变换反应系统的粗合成气输入口通过一第七粗合成气输送管线连接所述水激冷洗涤装置的粗合成气输出口;一热量回收装置,该热量回收装置具有一粗合成气输入口和粗合成气输出口,所述热量回收装置的粗合成气输入口通过一第八粗合成气输送管线连接所述耐硫变换反应系统的粗合成气输出口;一第三换热器,所述第三换热器具有一粗合成气输入口、一粗合成气输出口、一脱硫后的合成气输入口和一脱硫后的合成气输出口,所述第三换热器的粗合成气输入口通过一第九粗合成气输送管线连接所述热量回收装置的粗合成气输出口;一循环流化床,该循环流化床具有一循环流化床脱硫段和循环流化床再生段,所述循环流化床脱硫段具有一粗合成气输入口和脱硫后的合成气输出口;循环流化床再生段具有一再生空气或O2与N2的混合气体入口和一富SO2的气体出口,所述循环流化床脱硫段的粗合成气输入口通过一第十粗合成气输送管线连接所述的第三换热器的粗合成气输出口;所述循环流化床脱硫段的脱硫后的合成气输出口通过一第八脱硫后的合成气输送管线与所述第三换热器的脱硫后的合成气输入口连接;一第三过滤器,所述第三过滤器具有一脱硫后的合成气输入口和一脱硫后的合成气输出口,所述第三过滤器的脱硫后的合成气输入口通过一第九脱硫后的合成气输送管线与所述循环流化床的循环流化床脱硫段的脱硫后的合成气输出口连接,所述第三过滤器的脱硫后的合成气输出口通过一第八脱硫后的合成气输送管线与所述第三换热器的脱硫后的合成气输入口连接;一第四换热器,所述第四换热器具有一富SO2的气体入口、富SO2的气体出口、再生空气或O2与N2的混合气体入口、再生空气或O2与N2的混合气体出口,所述第四换热器的富SO2的气体入口通过一第七富SO2的气体输送管线连接所述循环流化床再生段的富SO2的气体出口,所述第四换热器的再生空气或O2与N2的混合气体入口连接空气源或O2与N2的混合气体源,所述第四换热器的再生空气或O2与N2的混合气体出口通过再生空气或O2与N2的混合气体输送管线连接所述循环流化床再生段的再生空气或O2与N2的混合气体入口;一硫酸装置或硫回收装置,所述硫酸装置或硫回收装置具有一富SO2的气体入口、一硫酸输出口或硫磺输出口,所述硫酸装置或硫回收装置的富SO2的气体入口通过第八富SO2的气体输送管线连接至所述第四换热器的富SO2的气体出口;所述硫酸装置或硫回收装置的硫酸输出口或硫磺输出口输出硫酸或硫磺;一可再生脱NH3/HCN装置,所述可再生脱NH3/HCN装置具有脱硫后的合成气入口和脱硫后的合成气出口,所述再生脱NH3/HCN装置的脱硫后的合成气入口通过一第十脱硫后的合成气输送管线与所述第三换热器的脱硫后的合成气输出口连接;一冷却装置,所述冷却装置具有脱硫后的合成气入口和脱硫后的合成气出口,所述冷却装置的脱硫后的合成气入口通过一第十一脱硫后的合成气输送管线与所述可再生脱NH3/HCN装置的脱硫后的合成气出口连接,所述冷却装置的脱硫后的合成气出口通过一第十二脱硫后的合成气输送管线与下游的脱二氧化碳单元装置连接。在本发明实现上述第二种结合耐硫变换和循环流化床热法脱硫的合成气净化方法的装置的一个优选实施例中,所述热量回收装置还具有另一粗合成气输出口并还包括一液相吸收脱硫脱碳装置,所述液相吸收脱硫脱碳装置具有粗合成气输入口和净化气输出口,所述液相吸收脱硫脱碳装置的粗合成气输入口通过一第十一粗合成气输送管线与所述热量回收装置的另一粗合成气输出口连接,所述液相吸收脱硫脱碳装置的净化气输出口送出净化合成气。在本发明实现上述第二种结合耐硫变换和循环流化床热法脱硫的合成气净化方法的装置一个优选实施例中,还包括一提氢装置,所述提氢装置具有一净化气输入口和一氢气出口,所述提氢装置的净化气输入口通过净化气输送管线与所述液相吸收脱硫脱碳装置的净化气输出口连接,所述提氢装置的氢气出口送出氢气。在本发明实现上述第二种结合耐硫变换和循环流化床热法脱硫的合成气净化方法的装置一个优选实施例中,还包括一PSA净化工段,所述PSA净化工段具有一脱硫后的合成气输入口和一氢气出口,所述PSA净化工段的脱硫后的合成气输入口通过所述第十二脱硫后的合成气输送管线与所述冷却装置的脱硫后的合成气出口连接,所述PSA净化工段的氢气出口送出氢气。在本发明实现上述第二种结合耐硫变换和循环流化床热法脱硫的合成气净化方法的装置一个优选实施例中,还包括一提氢装置、PSA净化工段和合成氨装置,所述提氢装置具有一净化气输入口和一氢气出口,所述PSA净化工段具有一脱硫后的合成气输入口和一氢气出口,所述合成氨装置具有两个氢气入口、一个N2补充口和一个产品氨输出口;其中所述提氢装置的净化气输入口通过净化气输送管线与所述液相吸收脱硫脱碳装置的净化气输出口连接,所述提氢装置的氢气出口通过一氢气输送管线与所述合成氨装置的一个氢气输入口连接;所述PSA净化工段的脱硫后的合成气输入口通过所述第十二脱硫后的合成气输送管线与所述冷却装置的脱硫后的合成气出口连接,所述PSA净化工段的氢气出口通过另一氢气输送管线与所述合成氨装置的另一个氢气输入口连接;所述合成氨装置的N2补充口通过N2输送管线连接N2气源;所述合成氨装置的产品氨输出口送出产品氨。在本发明实现上述第二种结合耐硫变换和循环流化床热法脱硫的合成气净化方法的装置的一个优选实施例中,所述煤气化装置为水煤浆气化装置、粉煤气化装置或碎煤固定床气化装置。在本发明实现上述第二种结合耐硫变换和循环流化床热法脱硫的合成气净化方法的装置的一个优选实施例中,所述耐硫变换反应系统使用绝热耐硫变换反应器或等温变换反应器或本申请人申请的中国专利号ZL201210040295.6、发明名称为带有支撑式槽孔板分布器的径向或轴径向固定床反应器或本申请人申请的中国专利号ZL201320176372.0、发明名称为一种将催化剂置于换热管之间的等温固定床反应器或本申请人申请的中国专利号ZL200910056432.4、发明名称为分流式等温耐硫变换工艺及其设备;所述带有支撑式槽孔板分布器的径向或轴径向固定床反应器,包括承压壳体和设置在所述承压壳体内且与承压壳体同轴的催化剂外框和气体收集中心管,所述承压壳体上设置有气体进口和气体出口,所述催化剂外框由支撑在承压壳体内壁上的支撑式槽孔板分布器构成;所述支撑式槽孔板分布器有由规格一致的若干槽孔分布板相互搭接构成;所述的槽孔分布板采用角钢和支座支撑在承压壳体的内壁上,所述角钢与支座之间采用螺栓连接,所述支座固定在承压壳体的内壁上,所述槽孔分布板与承压壳体之间保留一定的弧形间隙;所述槽孔分布板为其上开设有密集槽孔的弧形长条板;所述一种将催化剂装于换热管之间的等温固定床反应器,包括承压壳体、安装在承压壳体内的多个换热管;在所述承压壳体上设有气体进口、换热介质出口、气体出口、换热介质进口和催化剂卸料口;所述换热管的两端分别与所述换热介质出口和换热介质进口相连接;所述多个换热管之间存在空隙形成催化剂填充区,并且气体进口、换热管之间的空隙以及气体出口形成气体通道;所述分流式等温耐硫变换设备,至少包括一第一变换反应器和一锅炉给水预热器以及热回收冷却系统,第一变换反应器的第一变换气出口管与锅炉给水预热器进气口连接,锅炉给水预热器出气口与所述热回收冷却系统连接;第一变换反应器的原料气入口接原料煤气;所述的分流式等温耐硫变换设备还包括一汽包,所述第一变换反应器为等温变换反应器,所述第一变换反应器通过一由泵及管线构成的强制循环移热回路与汽包连接,所述锅炉给水预热器的锅炉给水管与汽包连接,向汽包输送预热后的锅炉给水;原料煤气配入过热蒸汽,将温度提高至200-300℃后通过第一变换反应器的原料气入口进入第一变换反应器进行变换反应,产出第一变换气,第一变换气通过第一变换气出口管送入所述锅炉给水预热器回收热量后,再送入所述热回收冷却系统分离出变换气和冷凝液;第一变换反应器副产中压饱和蒸汽,副产中压饱和蒸汽通过强制循环移热回路送入汽包进行分离,所述汽包分离出的中压饱和蒸汽通过汽包的蒸汽出口管送出;或者,所述分流式等温耐硫变换设备,至少包括一第一变换反应器和一锅炉给水预热器以及热回收冷却系统,第一变换反应器的第一变换气出口管与锅炉给水预热器进气口连接,锅炉给水预热器出气口与所述热回收冷却系统连接;第一变换反应器的原料气入口接原料煤气;所述的分流式等温耐硫变换设备还包括一第二变换反应器、一蒸汽过热器、一汽包,其中第一变换反应器为绝热变换反应器,第二变换反应器为等温变换反应器,其中第一变换反应器的第一变换气出口管与蒸汽过热器的第一变换气入口管直接,蒸汽过热器的第一变换气输送管与第二变换反应器的原料气入口连接,第二变换反应器的原料气入口还接原料煤气;所述第二变换反应器通过一由泵及管线构成的强制循环移热回路与汽包连接,第二变换反应器的第二变换气出口管与锅炉给水预热器进气口连接,所述锅炉给水预热器的锅炉给水管与汽包连接,向汽包输送预热后的锅炉给水;汽包的蒸汽出口管接蒸汽过热器的中压饱和蒸汽入口,蒸汽过热器的中压过热蒸汽出口管送出中压过热蒸汽;或者,所述分流式等温耐硫变换设备,至少包括一第一变换反应器和一锅炉给水预热器以及热回收冷却系统,第一变换反应器的第一变换气出口管与锅炉给水预热器进气口连接,锅炉给水预热器出气口与所述热回收冷却系统连接;第一变换反应器的原料气入口接原料煤气;所述的分流式等温耐硫变换设备还包括一第二变换反应器、一蒸汽过热器、一废热锅炉,其中第一变换反应器和第二变换反应器均为绝热变换反应器,其中第一变换反应器的第一变换气出口管与蒸汽过热器的第一变换气入口管直接,蒸汽过热器的第一变换气输送管与第二变换反应器的原料气入口连接,第二变换反应器的原料气入口还接原料煤气;所述第二变换反应器的第二变换气出口管与废热锅炉的第二变换气入口管直连,废热锅炉的第二变换气输送管与锅炉给水预热器进气口连接,所述锅炉给水预热器的锅炉给水管与废热锅炉的给水口连接,向废热锅炉输送预热后的锅炉给水;废热锅炉的蒸汽出口管接蒸汽过热器的中压饱和蒸汽入口,蒸汽过热器的中压过热蒸汽出口管送出中压过热蒸汽。在本发明实现上述第二种结合耐硫变换和循环流化床热法脱硫的合成气净化方法的装置的一个优选实施例中,所述脱二氧化碳单元装置为液相吸收脱二氧化碳单元装置或干法化学吸附脱二氧化碳单元装置。在本发明实现上述第二种结合耐硫变换和循环流化床热法脱硫的合成气净化方法的装置的一个优选实施例中,所述可再生脱NH3/HCN装置为吸附床。在本发明实现上述第二种结合耐硫变换和循环流化床热法脱硫的合成气净化方法的装置的一个优选实施例中,所述吸附床为固定式吸附床。本发明第二种结合耐硫变换和循环流化床热法脱硫的合成气净化方法可以用于IGCC、合成氨、甲醇合成、F-T合成烃类油类产品、合成气制SNG、生产氢气、合成气制乙二醇的粗合成气的净化工艺。由于采用了上述技术方案,本发明具有如下特点:(1)本发明可以适用于多种煤气化方式产的粗合成气的净化,例如水煤浆气化、粉煤气化、碎煤固定床气化。(2)本发明可以用来改造采用耐硫变换技术结合液相吸收法脱硫工艺净化粗合成气的增产工况,可以使得已有耐硫变换系统内的冷却装置和液相吸收法脱硫能够保持在原工况下操作,增产部分气体的提温和脱硫均可由新增循环流化床系统完成,做到改造对旧系统的影响最小,可大大减少改造的设备和降低投资费用,改造工作量最少最可靠。(3)本发明中的耐硫变换反应工艺,可以是全部变换或部分变换工艺,可以选择绝热变换流程,也可以选择等温变换流程。(4)本发明从合成气中脱二氧化碳的单元装置可使用液相吸收法或干法化学吸附,来进一步净化合成气。(5)本发明粗合成气经过一氧化碳耐硫变换反应,热量回收后不需要经过水冷和洗涤降低温度,而是以热状态进入循环流化床脱硫系统。(6)本发明经过循环流化床热法脱硫后的高温净化气可用来加热一氧化碳耐硫变换反应后的合成气,将粗合成气的温度提升至循环流化床脱硫入口所需的温度。(7)本发明经过循环流化床再生后的高温富SO2气体与再生空气或O2与N2的混合气换热,使得再生空气温度升高至再生反应所需要的温度,同时高温富SO2气体温度降低。(8)本发明使用循环流化床热法脱除合成气中的杂质,整个工艺过程在300-600℃,保持了煤气化产生的合成气的高位热值,避免了合成气下游利用再补充热量,有效提高了合成气的热效率。(9)本发明使用上述工艺过程脱除粗合成气中的杂质,粗合成气处理能力大。(10)本发明工艺流程简单,设备投资少。(11)本发明工艺过程不受到反应体系的压力影响,整个循环流化床脱硫体系压降低,动力损失少。(12)本发明工艺过程使用固体吸附剂脱除粗合成气中的含硫化合物、轻质芳烃、砷及其化合物、硒及其化合物、氰化物、氨,并可选地增加保护床除去合成气中的汞和氯化氢等其他微量杂质。整个工艺合成气脱除杂质流程比传统合成气净化过程中的水量消耗大幅度降低,同时减少了微量杂质组分对水的污染。(13)本发明工艺过程使用循环流化床进行热法脱粗合成气中的含硫杂质,例如H2S和COS,使合成气中的硫含量降低至0.5-5ppmv。(14)工艺过程中的循环流化床脱硫系统类似于流化催化裂化工艺系统,可使得固体吸附剂有效的再生循环。本发明通过耐硫变换与循环流化床热脱硫技术的合理配置,可以避免上述液相吸收法脱硫和固定床吸附剂脱硫的缺点,同时通过工艺参数和能量的合理优化,达到高温脱除粗合成气中含硫化合物、砷及其化合物、硒及其化合物、轻质芳烃的目的,通过固定床吸附剂脱除合成气中的氨和氰化物,也可选用保护床装置除去汞、氯化氢等杂质,最终实现粗合成气的干法净化。本发明旨在提供一种新的耐硫变换技术结合循环流化床热法脱硫技术工艺脱除合成气中的含硫化合物、砷及其化合物、硒及其化合物、轻质芳烃,通过固定床吸附剂脱除合成气中的氨和氰化物,通过可选地增加保护床装置脱除其他微量杂质,杂质可包括但不限于汞和氯化氢,实现粗合成气的净化。本发明可解决传统的耐硫变换工艺后配置液相吸收法脱硫工艺中存在的合成气热量利用率低的问题。本发明专利主要是通过耐硫变换技术结合循环流化床脱硫技术,合理配置变换反应与循环流化床脱硫系统的热量,脱除合成气中的含硫化合物、砷及其化合物、硒及其化合物、轻质芳烃,通过固定床吸附剂脱除合成气中的氨和氰化物,并可选地增加保护床装置除去合成气其他微量杂质如汞、氯化氢,实现合成气净化的目标。采用耐硫变换技术结合循环流化床脱硫技术脱除净化气的工艺,可以简化净化流程,减少设备,从而有效节省设备占地面积和降低合成气净化装置的投资成本。本发明的工艺方法和流程配置,通过耐硫变换技术与循环流化床热法脱硫技术的有效配置,并通过流程合理设计充分利用了上述反应的热量。最后可以使得净化后合成气的硫含量降低至0.5-5ppmv,并可脱除轻质芳烃、砷及其化合物、硒及其化合物,通过固定床吸附剂和可选择保护床,可以有效的脱除了合成气中氨、氰化物、汞、氯化氢等其他杂质。附图说明图1为本发明实施例1结合耐硫变换和循环流化床热法脱硫的合成气净化装置结构示意图。图2为本发明实施例2结合耐硫变换和循环流化床热法脱硫的合成气净化装置结构示意图。图3为本发明实施例3结合耐硫变换和循环流化床热法脱硫的合成气净化装置结构示意图。图4为本发明实施例4结合耐硫变换和循环流化床热法脱硫的合成气净化装置结构示意图。图5为本发明实施例5结合耐硫变换和循环流化床热法脱硫的合成气净化装置用于合成氨节能增产结构示意图。图6为本发明实施例6结合耐硫变换和循环流化床热法脱硫的合成气净化装置用于煤制氢节能增产结构示意图。图7为本发明实施例7结合耐硫变换和循环流化床热法脱硫的合成气净化装置用于新建煤制氢流程结构示意图。具体实施方式实施例1参见图1,图中给出了一种结合耐硫变换和循环流化床热法脱硫的合成气净化装置,包括水激冷洗涤装置100,换热器210、220,热量回收装置1100,耐硫变换反应系统300,循环流化床的吸附反应器400,循环流化床的再生反应器500,过滤器610、620,可再生脱NH3/HCN装置700,脱除汞和氯化物装置800,冷却装置900。水激冷洗涤装置100具有一粗合成气输入口110和粗合成气输出口120,水激冷洗涤装置100的粗合成气输入口110通过一粗合成气输送管线1连接一煤气化装置1000,煤气化装置1000为水煤浆气化装置、粉煤气化装置或碎煤固定床气化装置。耐硫变换反应系统300可使用绝热耐硫变换反应器或等温耐硫变换反应器或本申请人申请的中国专利号ZL201210040295.6、发明名称为带有支撑式槽孔板分布器的径向或轴径向固定床反应器。耐硫变换反应系统300具有一粗合成气输入口310和粗合成气输出口320。耐硫变换反应系统300的粗合成气输入口310通过一粗合成气输送管线2连接水激冷洗涤装置100的粗合成气输出口120。热量回收装置1100具有一粗合成气输入口1110和一粗合成气输出口1120。热量回收装置1100的粗合成气输入口1110通过一粗合成气输送管线3a连接耐硫变换反应系统300的粗合成气输出口320。热量回收装置1100的粗合成气输出口1120通过一粗合成气输送管线4a与换热器210的粗合成气输入口211连接。换热器210具有一粗合成气输入口211、一粗合成气输出口212、一脱硫后的合成气输入口213和一脱硫后的合成气输出口214,换热器210的粗合成气输入口211通过一粗合成气输送管线4a连接热量回收装置1100的粗合成气输出口1120。换热器210的脱硫后的合成气输出口214通过通过一脱硫后的合成气输送管线4′与再生脱NH3/HCN装置700的脱硫后的合成气入口710连接。循环流化床的吸附反应器400和循环流化床的再生反应器500形成一流化催化裂化FCC工艺系统。循环流化床的吸附反应器400包括一提升管410、一旋风分离器450和一下降管420,循环流化床的吸附反应器400的提升管410的底部具有一粗合成气输入口411,提升管410的下部配置有再生吸附剂入口412和再生吸附剂循环入口413,提升管410的上部配置有含固体吸附颗粒的脱硫后的合成气出口414。循环流化床的吸附反应器400的旋风分离器450的下部配置有载有硫的吸附剂出口451,旋风分离器450的上部配置有含固体吸附颗粒的脱硫后的合成气入口452,旋风分离器450的顶部配置有脱硫后的合成气输出口453。循环流化床的吸附反应器400的下降管420的下部配置有载有硫的吸附剂循环出口421和载有硫的吸附剂待再生出口422。提升管410底部的粗合成气输入口411通过一粗合成气输送管线5连接换热器210的粗合成气输出口212;提升管410下部的吸附剂循环入口通过一斜管430与下降管420下部的载有硫的吸附剂循环出口421连接,提升管410上部的含固体吸附颗粒的脱硫后的合成气出口414通过一含固体吸附颗粒的脱硫后的合成气输送管线2′与旋风分离器450上部的含固体吸附颗粒的脱硫后的合成气入口452连接。过滤器610具有一脱硫后的合成气输入口611和一脱硫后的合成气输出口612,过滤器610的脱硫后的合成气输入口611通过一脱硫后的合成气输送管线3′与旋风分离器450顶部的脱硫后的合成气输出口453连接,过滤器610的脱硫后的合成气输出口612通过一脱硫后的合成气输送管线1′与换热器210的脱硫后的合成气输入口213连接。循环流化床的再生反应器500包括一提升管510、一旋风分离器530和一下降管520。提升管510的下部具有一载有硫的吸附剂待再生入口511,底部配置有再生空气或O2与N2的混合气体入口512,提升管510的上部配置有含有再生固体吸附剂的富SO2的气体出口513。旋风分离器530的上部配置有含有再生固体吸附剂的富SO2的气体入口531,顶部配置有富SO2的气体出口532,底部配置有再生固体吸附剂出口533。下降管520的下部配置有再生吸附剂出口523。提升管510下部的载有硫的吸附剂入口511通过斜管440与下降管420下部的载有硫的吸附剂待再生出口422连接;旋风分离器530上部的含有再生固体吸附剂的富SO2的气体入口521通过一含有再生固体吸附剂的富SO2的气体输送管线1″与提升管510上部的含有再生固体吸附剂的富SO2的气体出口513连接;下降管520底部的再生吸附剂出口523通过一再生吸附剂输送管线(图中未示出)与循环流化床的吸附反应器400的提升管410下部的再生吸附剂入口412连接。过滤器620具有一富SO2的气体入口621和富SO2的气体出口622,过滤器620的富SO2的气体入口621与循环流化床的再生反应器500的旋风分离器520顶部的富SO2的气体出口522通过一富SO2的气体输送管线2″连接。换热器220具有一富SO2的气体入口221、富SO2的气体出口222、再生空气或O2与N2的混合气体入口223、再生空气或O2与N2的混合气体出口224,换热器220的富SO2的气体入口221通过一富SO2的气体输送管线3″连接过滤器620的富SO2的气体出口622,换热器220的再生空气或O2与N2的混合气体入口223连接空气源或O2与N2的混合气体源;换热器220的再生空气或O2与N2的混合气体出口224通过再生空气或O2与N2的混合气体输送管线225连接循环流化床的再生反应器500的提升管510底部的再生空气或O2与N2的混合气体入口512。可再生脱NH3/HCN装置700为固定式吸附床,具有脱硫后的合成气入口710和脱硫后的合成气出口720,再生脱NH3/HCN装置700的脱硫后的合成气入口710通过一脱硫后的合成气输送管线4′与换热器210的脱硫后的合成气输出口214连接。脱除汞和氯化物装置800为保护床,具有脱硫后的合成气入口810和脱硫后的合成气出口820,脱除汞和氯化物装置800的脱硫后的合成气入口810通过一脱硫后的合成气输送管线6′与可再生脱NH3/HCN装置700的脱硫后的合成气出口720连接。冷却装置900具有脱硫后的合成气入口910和脱硫后的合成气出口920,冷却装置900的脱硫后的合成气入口910通过一脱硫后的合成气输送管线8′与可再生脱NH3/HCN装置800的脱硫后的合成气出口820连接,冷却装置900的脱硫后的合成气出口920通过一脱硫后的合成气输送管线7′与下游的脱二氧化碳单元装置(图中未示出)连接。脱二氧化碳单元装置为液相吸收脱二氧化碳单元装置或干法化学吸附脱二氧化碳单元装置。经过煤或其它含碳材料的气化产生粗合成气,例如水煤浆气化、粉煤气化、碎煤固定床气化,该粗合成气通过粗合成气输送管线1送入到水激冷洗涤装置100中,经过水激冷洗涤装置100洗涤后,形成温度为180-250℃的粗合成气,该粗合成气有含硫化合物、氨、氰化物并可能含有轻质芳烃、砷及其化合物、硒及其化合物、汞、氯化物等杂质。温度为180-250℃的粗合成气通过粗合成气输送管线2进入耐硫变换反应系统300,耐硫变换反应系统300可采用全部变换或部分变换工艺,耐硫变换反应系统300可使用绝热耐硫变换反应器或等温耐硫变换反应器或本申请人申请的中国专利号ZL201210040295.6、发明名称为带有支撑式槽孔板分布器的径向或轴径向固定床反应器。在耐硫变换反应系统300中,粗合成气发生如下反应CO+H2O→CO2+H2,反应放出大量的热量,粗合成气的温度也随之升高至270-450℃。粗合成气...