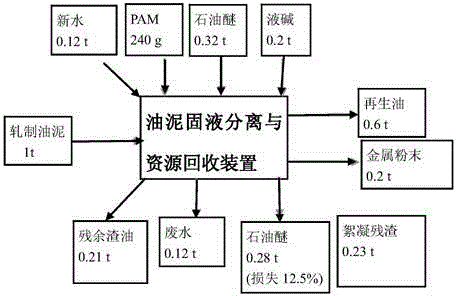
本发明属于工业危险废物处理与资源化利用的
技术领域:
,涉及轧制油泥固液分离与资源回收的方法和装置。
背景技术:
:在钢材轧制过程中,为追求高速、高效、高质,降低动力消耗,减少轧辊磨损,确保冷却效果,避免锈垢混入,稳定轧制负荷,需选用合适的润滑油。轧制油的润滑系统对轧机的生产能力和产品质量有直接影响。为提高润滑油的使用率,确保轧制产品质量,现代新建的用于多辊轧机的润滑系统均采用具有自动反冲洗功能的过滤系统。以法国DMS产森吉米尔不锈钢板带二十辊轧机为例,其过滤原理是利用可反冲洗的滤芯过滤。轧制油经轧机轧制使用后流入脏油箱,经一次泵打入主过滤器过滤后流入净油箱,污物留在滤芯之外,净油箱油泵再打入轧机循环使用。当主过滤器压差过大时,进入主滤芯反冲洗状态。反冲洗产生的废油进入污油箱自然沉降,其上部油液继而进入二级过滤器。二级过滤器也具有反冲洗功能,二级过滤后清液打入脏油箱,污物进入污油箱。根据生产需要,污油箱底部油泥(轧制油泥)需定期排出,吨钢产量约2kg。目前,企业通常将其作为危险废物委外处置,不仅代价高昂,且有资源浪费和污染转移的隐患。从工艺流程可见,轧制油泥在排出润滑系统之前,将反复经历轧制、过滤、反冲洗、自然沉降等过程,并受到温度、压力、空气、灰尘、金属接触等多重作用,直至形成无法继续回用的废弃轧制油泥。经分析,这部分轧制油泥与常规的废润滑油(如废机油、动力油、液压油、齿轮油,轴承油、真空泵油、透平油等)的主要区别如下:(1)固相含量高达5~15%、多为极细的金属、炭黑、胶质、沥青等杂质;(2)固相颗粒与油液高度乳化、自然沉降难度大,1个月的自然沉降高度小于10%;(3)色泽墨黑,颗粒细粘,不适宜离心分离和膜分离;(4)因轧制温度不高,润滑油氧化程度不太严重,有效成分变化较小,经 固液分离和细微颗粒去除后,上清油液返回利用价值大。针对此类轧制油泥,国内外未有回收利用的相关报道,而含固量很低的常规废润滑油的再生工艺,目前已有数十种,主要包括酸洗、少酸洗、无酸洗、加氢精制等过程(戴钧樑,废润滑油再生,2009,中国石化出版社)。早期的硫酸一白土法工艺简单,可生产出合格的基础油,但白土用量大、设备腐蚀严重、酸渣和废气污染环境,已成为国家明令禁止的方法(CN102657959A,CN102295982A等);经过改进的蒸馏一酸洗一白土精制法,减少了硫酸用量,但基础油收率不高(CN102746884A,CN102304414A等);白土高温接触无酸工艺再生油质量好,但白土用量大于10%,废油回收率小于80%,设备腐蚀严重、炉管堵塞,操作条件苛刻,因此适用性不强(CN101597541A,CN87105043等);蒸馏一溶剂抽提一白土精制法,该工艺不用硫酸,收率较高,但对废油选择性好的溶剂难以选择,而且溶剂回收工艺较复杂(CN101033433,CN1044487,CN102517154A等);分子精馏工艺作为目前较新的废油再生工艺,利用了分子蒸馏器高真空、低温操作的有点,避免了油品氧化,但不能处置氧化变质、乳化严重、酸值偏高的废油,且存在异味难去除、再生油颜色较深的问题(CN101092585A,CN101319166A,CN102373108A等);加氢精制工艺不产生污染环境的酸渣、酸水,具有环保、回收率高、产品质量好等优点,但反应条件要求比较苛刻,再生装置投资较高,仅适合大规模处理(CN101041789A,CN1539936,CN102433212A等)。以上这些专利,对废油再生后产生的残渣底泥,如何资源化处置或回收,也未明确具体途径。根据《废矿物油回收利用污染控制技术规范》(HJ607-2011),废矿物油的再生处理宜采用沉降、过滤、蒸馏、精制、催化裂解工艺,可根据废矿物油污染程度、再生产品质量要求选择,鼓励采用无酸废油再生技术,不得使用硫酸—白土法再生废矿物油。借鉴常规废润滑油的各种再生工艺,轧制油泥的固液分离和资源回收,应朝工艺过程环保、操作条件温和、废油回收率高、处理成本较低的方向发展。若能采用物理、化学或物理-化学联合手段,强化轧制油泥的固液分离过程和胶质颗粒的去除,并将上清油液和底泥分离后,分别回收利用,这对于回收废 油、节省处置费用、实现冷轧机组废旧油的闭路循环和危险废物的妥善处置,都具有积极意义。技术实现要素:针对常规废润滑油再生工艺操作条件苛刻、投资和运行成本高、工艺流程长、再生过程存在酸渣碱渣二次污染等问题,结合钢铁工业轧制机组废弃油泥的特性,提出一种轧制油泥的固液分离和资源回收方法和装置,其技术特征在于,先采取板框压滤实现油泥固液两相初步分离;再采取絮凝沉降、板框压滤、减压蒸馏的方式实现废油再生;最后利用既有设备,采取溶剂萃取、板框压滤、常压蒸馏的方式进一步实现废油再生和金属底泥回收,从而最终实现轧制油泥的固液分离、废油再生和金属资源的有效回收。所涉及的设备主要有:油泥贮槽、螺杆泵、板框压滤机、中间槽、油泵、三合一反应釜、清油灌、冷凝器、蒸馏塔、真空泵、管道、仪表、阀门等。本套方法操作简单、工艺可靠、一线多能、一机多用,占地小、投资低,废油再生率高,可有效实现轧制油泥的固液分离、废油再生和金属资源的有效回收。为了实现上述目的,本发明的技术方案如下:一种用于轧制油泥固液分离与资源回收的装置,其包括:油泥储槽、螺杆泵、板框压滤机、中间槽、油泵、三合一反应釜、蒸馏塔、冷凝器、清油罐和真空泵,所述油泥储槽分别与螺杆泵和三合一反应釜的底部连通,所述螺杆泵与板框压滤机连通,所述板框压滤机与中间槽连通,所述中间槽与油泵连通,所述油泵与三合一反应釜的顶部连通,所述三合一反应釜的顶部还设有蒸馏塔,所述蒸馏塔与精油罐通过冷凝器相连通,所述精油罐的底部与真空泵相连通。作为优选方案,所述油泥储槽中设有油泥储槽搅拌器以及油泥储槽液位计。作为优选方案,所述中间槽的侧壁和底部分别固设有中间槽液位计和中间槽排料阀。作为优选方案,所述三合一反应釜的釜体顶部、内部、外侧壁以及底部分 别设有温度计、反应釜搅拌器、换热夹层和反应釜排放阀。作为优选方案,所述蒸馏塔的顶部设有蒸馏塔温度计和蒸馏塔压力计。作为优选方案,所述精油罐的顶部、内部以及侧壁上分别设有精油罐压力表、精油罐液位计以及精油罐排料阀。一种基于本发明所述的装置的轧制油泥固液分离与资源回收方法,其包括如下步骤:a、收集轧制油泥,置于油泥储槽中,在5~20r/min搅拌速率下缓慢搅拌,使油泥保持均匀流动状态;b、待所述油泥升至超过油泥储槽有效储液高度三分之一的液位后,启动螺杆泵,将油泥输送至板框压滤机中,进行固液两相的初步分离,得到固相的油泥饼和液相的废油,将所述油泥饼取出,进行清理后装回板框压滤机,将所述废油排入中间槽后,用油泵打入三合一反应釜中;c、在三合一反应釜中,所述废油在5~20r/min速率的搅拌下先后加入絮凝剂和碱液后,将搅拌速率提高至20~40r/min,持续搅拌20~50min;d、打开螺杆泵将三合一反应釜内得到的絮凝物输送至板框压滤机,压滤后得到絮凝后上清液和和絮凝泥饼,打开板框压滤机将絮凝泥饼取出,进行专门处理;e、将所述絮凝后的上清液输送至中间槽,静置后,分离出废水和油液,打开中间槽的底阀,将废水放出;f、用油泵将所述油液打入三合一反应釜内,在釜体换热夹层中通入冷凝水,进行减压蒸馏1~3h后,得到渣油和经“压滤-絮凝-减压蒸馏”处理后的再生油;g、将所述油泥饼与萃取剂在中间槽内混合均匀后,输送至板框压滤机内,压滤后得到固相金属粉末和液相溶剂,将所述液相溶剂通过中间槽进入三合一反应釜中进行常压蒸馏,回收萃取剂和再生油。作为优选方案,所述絮凝剂为无机絮凝剂、有机絮凝剂和复合絮凝剂中的至少一种,所述无机絮凝剂为三氯化铁、硫酸铁、聚合硫酸铁、绿矾、聚合氯化铝、硫酸铝、明矾、聚合硫酸铝铁中的至少一种;所述有机絮凝剂为聚丙烯 酰胺。作为优选方案,所述所述碱液的加入量按照碱液中的纯碱物质占所述处理的废油质量的1~20%计算,所述碱液为5~30wt%的氢氧化钠或氢氧化钾溶液。作为优选方案,步骤f中所述的减压蒸馏中,收集塔底温度160~320℃,塔顶温度180~280℃,真空度5mmHg的组分;步骤g中,所述的萃取剂与油泥饼的质量比控制为1~5:1,所述萃取剂包括石油醚、正己烷、辛烷、四氯化碳、丙酮、甲苯中的一种,常压蒸馏收集60~90℃的组分。本发明的有益效果主要体现在:(1)工艺简单可靠:借助于板框压滤、絮凝沉降和减/常压蒸馏三种常规物理化学-手段,通过一线多能、一机多用,以较低的成本实现了废弃油泥中液相油、固相金属物质的回收;再生油可返回车间重新使用,固体金属粉料可生产高附加值产品。(2)操作简便:本发明涉及的装置都是常规的化工设备,容易操作和维护。(3)针对性强:针对于轧制机组废弃油泥间歇排放、定期收集处置的特点,开发的这套装置,通过功能切换间歇进料设计,既降低了设备投资和运行成本,充分挖掘了设备的潜力,又节约了占地。(4)安全环保:与传统硫酸-白土工艺相比,本发明属无酸操作,无有害气体释出,对环境的影响小。(5)适宜推广:本发明操作简单、投资少、成本低,基础油回收率高,可直接回用,适用于其他各类废润滑油的再生处理,具有推广价值。附图说明图1为本发明的用于轧制油泥固液分离与资源回收的装置的结构示意图。图2为轧制油泥固液分离与资源回收的物料平衡图;图3为轧制油泥固液分离与资源回收的物料平衡图;图4为轧制油泥固液分离与资源回收的物料平衡图;图5为轧制油泥固液分离与资源回收的物料平衡图;图1中:1、油泥储槽;11、油泥储槽搅拌器;12、油泥储槽液位计;2、螺杆泵;3、板框压滤机;4、中间槽;41、中间槽液位计;42、中间槽排料阀;5、油泵;6、三合一反应釜;61釜体;62、换热夹层;63、反应釜搅拌器;64、反应釜排放阀;65、温度计;7、蒸馏塔;71、蒸馏塔温度计;72、蒸馏塔压力计;8、冷凝器;9、清油罐;91、清油罐液位计;92、清油罐压力表;93、清油罐排料阀;10、真空泵。具体实施方式本发明提供的一种用于轧制油泥固液分离与资源回收的装置的结构如图1所示,其包括:油泥储槽1、螺杆泵2、板框压滤机3、中间槽4、油泵5、三合一反应釜6、蒸馏塔7、冷凝器8、清油罐9和真空泵10,油泥储槽1分别与螺杆泵2和三合一反应釜6的底部连通,螺杆泵2与板框压滤机3连通,板框压滤机3与中间槽4连通,中间槽4与油泵5连通,油泵5与三合一反应釜6的顶部连通,三合一反应釜6的顶部还设有蒸馏塔7,蒸馏塔7与精油罐9通过冷凝器8相连通,精油罐9的底部与真空泵10相连通。油泥储槽1的顶部和侧壁分别设有油泥储槽搅拌器11以及油泥储槽液位计12。中间槽4的侧壁和底部分别固设有中间槽液位计41和中间槽排料阀42。三合一反应釜6的釜体61顶部、内部、外侧壁以及底部分别设有温度计65、反应釜搅拌器63、换热夹层和62反应釜排放阀64。蒸馏塔7的顶部设有蒸馏塔温度计71和蒸馏塔压力计72。精油罐9的顶部、侧壁以及底部分别设有精油罐压力表92、精油罐液位计91以及精油罐排料阀93。油泥储槽1为间歇收集油泥的装置,通过油泥储槽搅拌器11的转动,避免油泥沉积;通过液位计12控制其贮油高度,待贮油升至一定高度后,进入油泥固液分离和资源回收程序。螺杆泵2为油泥/油液输送装置。在固液分离操作中,螺杆泵2前与油泥储槽1、后与板框压滤机3相连;在絮凝沉降+压滤操作中,螺杆泵2前与三合一反应釜6、后与板框压滤机3相连。板框压滤机3的功能是实现固液分离,其关键部件是滤布,具体型号选择、 安装更换,以及板框压滤操作,属于通识技术和设备。中间槽4承接板框压滤后的上清油液,为进入三合一反应釜6做好准备。中间槽装设有液位计41,指示液位;底部设置排料阀42,以排出油水分离产生的废水,此部分废水可在配制碱液中得到回收利用。油泵5为油液输送装置。三合一反应釜6,由釜体61、外置换热夹层62、搅拌器63、排放阀64、温度计65等部件组成,在釜内可实现废油絮凝-沉降、油品减压蒸馏、固相物萃取-常压蒸馏三种功能,三个功能可以切换使用。蒸馏塔7的功能是实现油品常减压蒸馏,为节省空间,该蒸馏塔置于三合一反应釜6的上部,为一体式设计,同时配备指示仪表温度计71,压力计72。冷凝器8的功能是蒸馏后油品的冷凝回收。清油罐9在减压蒸馏中回收清油,在常压蒸馏中回收萃取剂。同时配备液位计91,压力计92和排料阀93。真空泵10的功能是辅助反应釜6、蒸馏塔7、冷凝器8、清油罐9,实现减压蒸馏功能。一种基于本发明所述的装置的轧制油泥固液分离与资源回收方法,其包括如下步骤:a、收集轧制油泥,置于油泥储槽中,在5~20r/min搅拌速率下缓慢搅拌,使油泥保持均匀流动状态;b、待所述油泥升至超过油泥储槽有效储液高度三分之一的液位后,启动螺杆泵,将油泥输送至板框压滤机中,进行固液两相的初步分离,得到固相的油泥饼和液相的废油,将所述油泥饼取出,进行清理后装回板框压滤机,将所述废油排入中间槽后,用油泵打入三合一反应釜中;c、在三合一反应釜中,所述废油在5~20r/min速率的搅拌下先后加入絮凝剂和碱液后,将搅拌速率提高至20~40r/min,持续搅拌20~50min;d、打开螺杆泵将三合一反应釜内得到的絮凝物输送至板框压滤机,压滤后得到絮凝后上清液和和絮凝泥饼,打开板框压滤机将絮凝泥饼取出,进行专门处理;e、将所述絮凝后的上清液输送至中间槽,静置后,分离出废水和油液,打开中间槽的底阀,将废水放出;f、用油泵将所述油液打入三合一反应釜内,在釜体换热夹层中通入冷凝 水,进行减压蒸馏1~3h后,得到渣油和经“压滤-絮凝-减压蒸馏”处理后的再生油;g、将所述油泥饼与萃取剂在中间槽内混合均匀后,输送至板框压滤机内,压滤后得到固相金属粉末和液相溶剂,将所述液相溶剂通过中间槽进入三合一反应釜中进行常压蒸馏,回收萃取剂和再生油。作为优选方案,所述絮凝剂为无机絮凝剂、有机絮凝剂和复合絮凝剂中的至少一种,所述无机絮凝剂为三氯化铁、硫酸铁、聚合硫酸铁、绿矾、聚合氯化铝、硫酸铝、明矾、聚合硫酸铝铁中的至少一种;所述有机絮凝剂为聚丙烯酰胺。作为优选方案,所述所述碱液的加入量按照碱液中的纯碱物质占所述处理的废油质量的1~20%计算,所述碱液为5~30wt%的氢氧化钠或氢氧化钾溶液。作为优选方案,步骤f中所述的减压蒸馏中,收集塔底温度160~320℃,塔顶温度180~280℃,真空度5mmHg的组分;步骤g中,所述的萃取剂与油泥饼的质量比控制为1~5:1,所述萃取剂包括石油醚、正己烷、辛烷、四氯化碳、丙酮、甲苯中的一种,常压蒸馏收集60~90℃的组分。实施例1轧制油泥取自某钢企冷轧厂DMS20辊可逆式冷轧机组,色泽墨黑,底泥粘稠,经分析,主要含有两部分物质:液态的油和固态的泥,其中液相80%,固相20%,油泥经干化,发现干基成分以Fe、Cr、Ni、Mn、Si、Ca为主(含量之和约60%),并含有微量Mg、Zn、Pb、P等(含量之和小于1%)。此外,在预实验中发现,轧制油泥从沉降性差,1个月的自然沉降高度仅为10%,且底部的“固相”乳化“液相”性能好,固液分离十分困难。取此轧制油泥2t,按前述的分离方法,进行油泥的固液分离和资源回收,主要过程为:先采取板框压滤实现初步固液分离;再采取絮凝沉降、板框压滤、减压蒸馏的方式实现废油再生;最后利用既有设备,采取溶剂萃取、板框压滤、常压蒸馏的方式进一步实现废油再生和金属底泥回收,从而最终实现轧制油泥的固液分离、废油再生和金属资源的有效回收。具体为:1、轧制油泥固液分离收集轧制油泥2t,置于油泥贮槽1中,在搅拌器11的缓慢作用下,保持内部均匀流动状态;待油泥升至一定液位计12限值时,启动螺杆泵2,将油泥输送至板框压滤机3,实现固液分离,得到固相的油泥饼约0.4t和液相的废油(滤液)约1.6t;打开板框压滤机3取出0.4t油泥饼备用,1.6t废油(滤液)进入中间槽4。2、废油再生将中间槽3中废油(滤液)用油泵5打入三合一反应釜6中,开动反应釜6搅拌器6-3缓慢搅拌(速度10r/min),先加入大约0.32t质量分数为0.05%阳离子PAM絮凝剂溶液(PAM为废油的质量百分比为1%),搅拌过程中再加入0.4t质量分数为20%的氢氧化钠溶液(氢氧化钠为废油的质量百分比的5%),变频调节搅拌速率升至20r/min,持续搅拌30min停止搅拌;打开螺杆泵2将絮凝物输送至板框压滤机3,压滤后得到大约2.15t絮凝处理物和大约0.17t絮凝底泥,打开板框压滤机将底泥取出,进行专门处理。将2.15t的絮凝处理物进入中间槽4,打开中间槽底部排放阀4-2将废水放出,得到大约1.4t絮凝处理油;用油泵5将絮凝处理油打入三合一反应釜6,打开釜体换热夹层62,先后启动蒸馏塔7、冷凝器8、真空泵10,进行减压蒸馏,收集塔底温度160~320℃,塔顶温度180~280℃,真空度5mmHg的组分,约2h后蒸馏完毕;打开清油罐底阀,放出蒸馏处理后清油,即得到经“压滤-絮凝-减压蒸馏”处理后的再生油约1t;打开反应釜6底部排放阀,放出底部渣油,进行专门处理;3、固相组分回收将步骤“1、轧制油泥固液分离”中得到的0.4t油泥与0.8t石油醚加入三合一反应釜6中,启动搅拌器63,调节搅拌速率为85r/min,搅拌30min,打开螺杆泵2,将1.2t油泥与萃取剂混合物通过板框压滤机3打入中间槽4,在中间槽4中得到约0.9t剂油混合物,打开板框压滤机,即得到大约0.3t金属固体粉末;打开油泵5将0.9t剂油混合物打入三合一反应釜6,常压蒸馏收集60~80℃的馏分约0.72t,即为回收的石油醚(回收率75%),由清油罐9排放阀93放出;打开三合一反应釜6底部排放阀64,回收废油大约0.1t,参照废 油再生对其进行处理。综上,2t轧制油泥,经固液分离、废油再生和油泥萃取后,可回收得到至少1.1t再生油(废油蒸馏回收1t+油泥萃取回收0.1t),0.3t金属固体粉末,消耗石油醚约0.04t,消耗阳离子PAM絮凝剂160g,消耗液碱0.21t,消耗水约0.063t,产生残余渣油约0.35t及絮凝残渣约0.5t。物料平衡如图2所示。4、废油再生效果和回收固相金属物料成分如表1所示,为油泥净化前、净化后以及轧制新油的关键指标对比。可见,经本工艺净化后,油品理化指标有较大改善,固相颗粒等杂质几近去除,色泽由墨黑转淡黄,基本上达到或接近该级别基础油标准,可返回轧制生产线继续使用。如表2所示,为固相金属物料经萃取后的成分分析。可见,除表面残留的部分油品外,轧制油底泥成分以铁、铬、镍、锰的单质金属元素及其氧化物为主,这四种主要元素含量合计在70%以上,其余杂质为硅、钠、硫、钙、镁等微量成分。通过高温氧化,松散的金属粉料中有机成分可有效去除,固体成分即可氧化为金属化球团。此类球团金属化率高、杂质含量少,可在钢铁长流程工序中资源化利用(如返回炼钢等)。表1轧制油泥净化前、净化后及轧制新油关键指标对比(mg/L)表2轧制油底泥固相物料化学成分项目实施例1实施例2实施例3实施例4Pb<0.05<0.05<0.05<0.05Zn<0.05<0.05<0.050.1SiO20.61.20.60.7Al2O3<0.1<0.1<0.1<0.1CaO<0.1<0.10.10.1MgO<0.1<0.1<0.1<0.1MnO3.04.12.54.2Na2O2.02.52.51.2T.Fe49.450.551.249.8Cr2O317.616.518.114.5NiO5.04.23.66.1Co3O40.2<0.1<0.1<0.1CuO0.5<0.1<0.10.1实施例2轧制油泥固液分离和资源回收装置、方法及实施过程与实施例1相同。所不同点是轧制油泥处理量、絮凝剂、液碱、石油醚的加入量不同。物料平衡如图3所示。实施例3轧制油泥固液分离和资源回收装置、方法及实施过程与实施例1相同。所不同点是轧制油泥处理量、絮凝剂、液碱、石油醚的加入量不同。物料平衡如图4所示。实施例4轧制油泥固液分离和资源回收装置、方法及实施过程与实施例1相同。所不同点是轧制油泥处理量、絮凝剂、液碱、石油醚的加入量不同。物料平衡如图5所示。下面再举出以下实施例2~实施例4来进一步说明本发明的上述方法,具体工艺参数如表3所示:表3实施例1~实施例4的工艺参数综上所述,仅为本发明的较佳实施例而已,并非用来限定本发明实施的范围,凡依本发明权利要求范围所述的形状、构造、特征及精神所为的均等变化与修饰,均应包括于本发明的权利要求范围内。当前第1页1 2 3