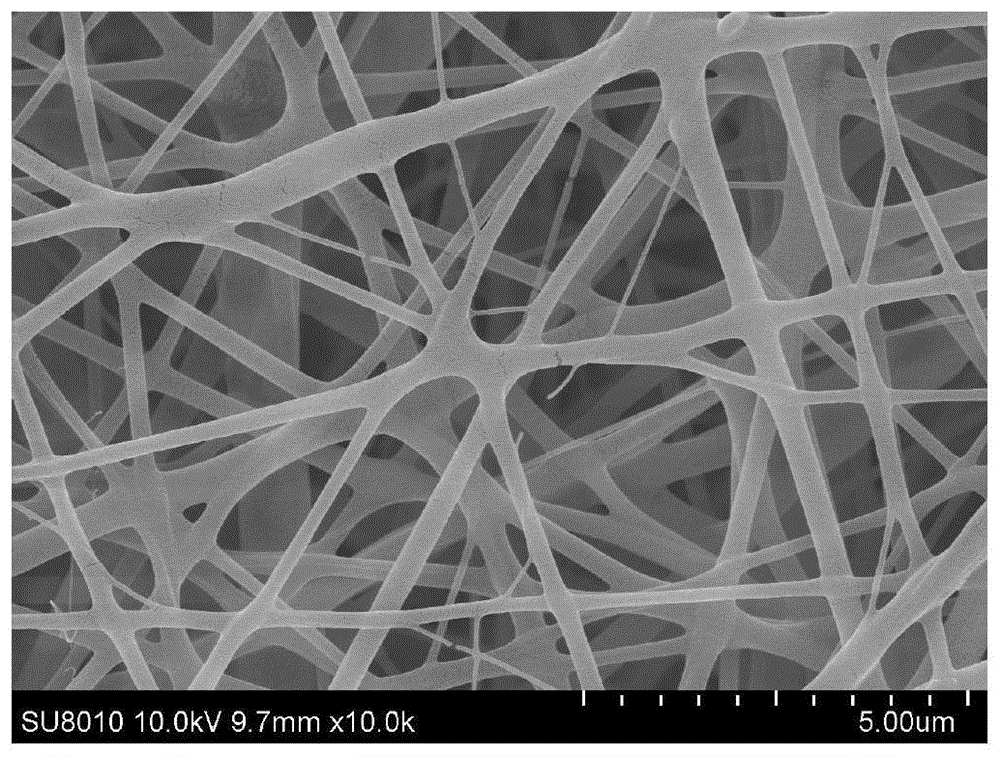
本发明涉及一种纳米含能复合纤维及其制备方法,具体涉及一种以硝化棉(nc)和聚叠氮缩水甘油醚(gap)为载体、负载纳米三氨基三硝基苯(nano-tatb)的纳米含能复合纤维及其制备方法,属于含能材料制备
技术领域:
。
背景技术:
:纳米含能复合纤维的各组分之间接触距离短,纤维的传热和传质效率高,临界直径小,体系能量的释放速率高,放热量大,燃烧性能和爆炸性能优异,摩擦和撞击感度低,长脉冲冲击波感度低、短脉冲冲击波感度高,同时还可以有效避免单一纳米炸药粒子的团聚,所以可以应用于多个领域,例如:(1)应用于推进剂中时,可以显著提高固体推进剂力学性能和延伸率,改善燃烧和爆炸性能,降低感度;(2)应用于起爆器件中时,能够降低起爆能量,提高使用安全性、起爆灵敏度、起爆精确度和稳定性;(3)应用于传爆药中时,既可降低摩擦感度、撞击感度、长脉冲冲击波感度,又可增大能量输出。但是,由于纳米含能粒子具有小尺寸效应、表面效应和高表面自由能,所以使得纳米颗粒存在易团聚的缺陷,进而限制了纳米含能复合纤维的应用。可见,防止纳米含能粒子团聚,从而改善纳米含能复合纤维的性能,是我们亟待解决的问题。近年来,随着纳米技术的不断发展,静电纺丝技术又一次引起了广泛关注,并被应用于了聚合物纳米纤维的制备工艺中。采用静电纺丝技术制备得到的纳米含能复合纤维力学性能好,具有较高的比表面积和孔隙率,在生物医学、过滤材料、催化载体等领域都具有重要用途,当其作为载体使用时,可以均匀分散纳米炸药粒子,有效防止纳米炸药粒子团聚,同时还可以发挥聚合物载体的柔韧性和易操作性。中国专利cn101880915a通过静电纺丝技术制备得到了一种硝化棉纤维,该硝化棉纤维有效提高了炸药的燃烧速率。但是,该技术使用的是混合溶剂(水和有机溶剂混合),纳米金属粒子活性高,极不稳定,极易与水发生反应,从而降低活性位点以及金属纳米粒子的热力学性能,使纳米金属粒子燃烧时放热量大幅度减少,进而对固体推进剂的燃烧速率和燃烧效率造成影响。另外,水在室温下不易挥发,在纺丝过程中,极易造成纤维的坍塌和静电力对纤维的拉伸作用力不充足,从而导致纳米金属粒子分布不均匀和团聚,影响纤维的力学性能和燃烧爆炸性能。中国专利cn102634861a采用静电纺丝技术制备得到了一种mic/硝化棉微纤维,该微纤维有效提高了硝化棉的能量密度。但是,该技术选择将硝化棉作为载体,单独的硝化棉溶液粘度相对较大,会给纺丝过程带来极大困难,同时还会使纤维直径分布不均匀,导致制备的纤维纳米炸药粒子负载量低。另外,制备以单纯的硝化棉为基体的纤维时,需要的纺丝电压较高,当纺丝电压超过20kv时,会在注射器针头产生电火花,这会带来极大的安全隐患。技术实现要素:为解决现有技术的不足,本发明的目的在于提供一种既能降低纺丝难度,又能提高纳米炸药粒子负载量,同时还能杜绝安全隐患的纳米含能复合纤维的制备方法以及由该制备方法制备得到的纳米含能复合纤维。为了实现上述目标,本发明采用如下的技术方案:一种纳米含能复合纤维的制备方法,其特征在于,包括以下步骤:step1:配制纺丝溶液将硝化棉、聚叠氮缩水甘油醚和纳米三氨基三硝基苯加入到有机溶剂中,配制成质量浓度为8~20%的纺丝溶液,其中,纳米三氨基三硝基苯与硝化棉和聚叠氮缩水甘油醚总质量的质量比为1:1~6;step2:静电纺丝使用静电纺丝设备进行静电纺丝,设置纺丝电压12~18kv,挤出速度1~6ml/h,接收距离6~20cm,环境相对湿度35~60%。前述的纳米含能复合纤维的制备方法,其特征在于,在前述纺丝溶液中,硝化棉与聚叠氮缩水甘油醚的质量比为1:0.5~3。前述的纳米含能复合纤维的制备方法,其特征在于,前述有机溶剂为丙酮或乙酸乙酯。一种纳米含能复合纤维,其特征在于,以硝化棉和聚叠氮缩水甘油醚为载体、负载纳米三氨基三硝基苯,具体采用前述的制备方法制备而成。本发明的有益之处在于:(1)用聚叠氮缩水甘油醚取代部分硝化棉,降低了纺丝溶液的粘度,不仅有利于增加纳米炸药粒子的负载量,提高纤维放热量和爆热等燃烧爆炸性能,更有利于降低纺丝电压和纺丝难度,提高实验的安全性,保障实验人员和实验室的安全;(2)硝化棉和聚叠氮甘油醚基体与负载的纳米含能粒子之间存在协同作用,使得纳米含能复合纤维的热分解温度降低,反应活性提高;(3)使用丙酮或乙酸乙酯作为纺丝溶液的溶剂,不掺水,不仅可以避免因溶剂挥发慢造成的纤维坍塌和静电力对纤维的拉伸作用力不充足,而且还可以避免因纳米含能粒子与水发生反应造成的活性位点以及金属纳米粒子的热力学性能降低;(4)采用本发明提供的制备方法制备得到的纳米含能复合纤维孔隙率高、长径比大、均一度高,为纳米含能粒子提供了大量的负载位点,能够有效防止纳米含能粒子团聚。附图说明图1是实施例1中的nc/gap纤维的扫描电镜图;图2是实施例1中的nc/gap纤维的dsc图图3是实施例2中的nc/gap/nano-tatb纤维的扫描电镜图;图4是实施例2中的nc/gap/nano-tatb纤维的dsc图;图5是实施例3中的nc/gap/nano-tatb纤维的扫描电镜图;图6是实施例3中的nc/gap/nano-tatb纤维的dsc图;图7是实施例4中的nc/gap/nano-tatb纤维的扫描电镜图;图8是实施例4中的nc/gap/nano-tatb纤维的dsc图。具体实施方式以下结合附图和具体实施例对本发明作具体的介绍。第一部分:制备复合纤维实施例1:制备nc/gap纤维step1:配制纺丝溶液在室温条件下,将硝化棉和聚叠氮缩水甘油醚加入到有机溶剂丙酮中,配制成质量浓度为18%的纺丝溶液,其中:硝化棉与聚叠氮缩水甘油醚的质量比为2:1。step2:静电纺丝使用静电纺丝设备进行静电纺丝,环境湿度控制在50%。首先将纺丝溶液装入注射器内,然后将注射器安装在注射泵上,再将注射器的针头与电源的正极相连,最后将电源的负极与接收器相连,注射器的针头与接收器之间形成静电场。调节注射器的针头与接收器之间的接收距离为10cm,设置注射泵的挤出速度为3ml/h,打开高压电源,设置纺丝电压为15kv。在静电纺丝过程中,具有一定静电压的射流从注射器的针头向接收器运动的过程中,会在电场力的作用下产生加速现象,射流在电场中被进一步拉伸,最后被接收器收集,完成nc/gap纤维的制备。采用上述制备方法制备得到的nc/gap纤维的扫描电镜图如图1所示。从图1中可以看到:nc/gap纤维表面光滑、纤维尺寸分布均匀。采用上述制备方法制备得到的nc/gap纤维的dsc图谱如图2所示。从图2中可以发现:在179℃处有一个放热峰,这说明在制备nc/gap纤维的过程中nc和gap分子链凝聚缠结,两种含能高分子材料具有优异的相容性。实施例2:制备nc/gap/nano-tatb纤维step1:配制纺丝溶液在室温条件下,将硝化棉、聚叠氮缩水甘油醚和纳米三氨基三硝基苯加入到有机溶剂丙酮中,配制成质量浓度为18%的纺丝溶液,其中:硝化棉与聚叠氮缩水甘油醚的质量比为2:1;纳米三氨基三硝基苯与硝化棉和聚叠氮缩水甘油醚总质量的质量比为1:1。step2:静电纺丝使用静电纺丝设备进行静电纺丝,环境湿度控制在50%。首先将纺丝溶液装入注射器内,然后将注射器安装在注射泵上,再将注射器的针头与电源的正极相连,最后将电源的负极与接收器相连,注射器的针头与接收器之间形成静电场。调节注射器的针头与接收器之间的接收距离为15cm,设置注射泵的挤出速度为3ml/h,打开高压电源,设置纺丝电压为18kv。在静电纺丝过程中,具有一定静电压的射流从注射器的针头向接收器运动的过程中,会在电场力的作用下产生加速现象,射流在电场中被进一步拉伸,最后被接收器收集,完成纳米含能复合纤维的制备。采用上述制备方法制备得到的nc/gap/nano-tatb纤维的扫描电镜图如图3所示。从图3中可以看到:nc/gap/nano-tatb纤维表面粗糙、纤维尺寸分布均匀,与nc/gap纤维相比,直径增大明显。采用上述制备方法制备得到的nc/gap/nano-tatb纤维的dsc图谱如图4所示。从图4中可以发现:加入tatb后,放热峰后移,在热分解过程中仍然只有一个放热峰存在,这说明tatb的加入不会影响nc和gap的相容性,三种组分相互协同,纳米含能复合纤维的分解温度较低、反应活性较高。实施例3:制备nc/gap/nano-tatb纤维step1:配制纺丝溶液在室温条件下,将硝化棉、聚叠氮缩水甘油醚和纳米三氨基三硝基苯加入到有机溶剂丙酮中,配制成质量浓度为18%的纺丝溶液,其中:硝化棉与聚叠氮缩水甘油醚的质量比为1:2;纳米三氨基三硝基苯与硝化棉和聚叠氮缩水甘油醚总质量的质量比为1:4。step2:静电纺丝使用静电纺丝设备进行静电纺丝,环境湿度控制在50%。首先将纺丝溶液装入注射器内,然后将注射器安装在注射泵上,再将注射器的针头与电源的正极相连,最后将电源的负极与接收器相连,注射器的针头与接收器之间形成静电场。调节注射器的针头与接收器之间的接收距离为15cm,设置注射泵的挤出速度为3ml/h,打开高压电源,设置纺丝电压为16kv。在静电纺丝过程中,具有一定静电压的射流从注射器的针头向接收器运动的过程中,会在电场力的作用下产生加速现象,射流在电场中被进一步拉伸,最后被接收器收集,完成纳米含能复合纤维的制备。采用上述制备方法制备得到的nc/gap/nano-tatb纤维的扫描电镜图如图5所示。从图5中可以看到:nc/gap/nano-tatb纤维表面粗糙、纤维尺寸分布均匀,与实施例2中的nc/gap/nano-tatb纤维相比,纤维尺寸变细,nano-tatb在nc/gap表面负载的不太均匀。采用上述制备方法制备得到的nc/gap/nano-tatb纤维的dsc图谱如图6所示。从图6中可以发现:复合纤维中tatb比例较低时,放热峰温降低。实施例4:制备nc/gap/nano-tatb纤维step1:配制纺丝溶液在室温条件下,将硝化棉、聚叠氮缩水甘油醚和纳米三氨基三硝基苯加入到有机溶剂乙酸乙酯中,配制成质量浓度为16%的纺丝溶液,其中:硝化棉与聚叠氮缩水甘油醚的质量比为1:2;纳米三氨基三硝基苯与硝化棉和聚叠氮缩水甘油醚总质量的质量比为1:4。step2:静电纺丝使用静电纺丝设备进行静电纺丝,环境湿度控制在50%。首先将纺丝溶液装入注射器内,然后将注射器安装在注射泵上,再将注射器的针头与电源的正极相连,最后将电源的负极与接收器相连,注射器的针头与接收器之间形成静电场。调节注射器的针头与接收器之间的接收距离为15cm,设置注射泵的挤出速度为3ml/h,打开高压电源,设置纺丝电压为18kv。在静电纺丝过程中,具有一定静电压的射流从注射器的针头向接收器运动的过程中,会在电场力的作用下产生加速现象,射流在电场中被进一步拉伸,最后被接收器收集,完成纳米含能复合纤维的制备。采用上述制备方法制备得到的nc/gap/nano-tatb纤维的扫描电镜图如图7所示。从图7中可以看到:nc/gap/nano-tatb纤维表面粗糙、纤维尺寸分布均匀。采用上述制备方法制备得到的nc/gap/nano-tatb纤维的dsc图谱如图8所示。从图8中可以发现:放热峰温与实施例3中的放热峰温相接近,这说明纺丝浓度对热分解的过程影响较小。聚叠氮缩水甘油醚(gap)是一种具有低粘度和高能量的含能预聚体,(与nc相比)它具有较低的玻璃化温度和较高的密度。用gap取代部分nc来降低纺丝溶液的粘度,不仅有利于增加纳米炸药粒子的负载量,提高纤维放热量和爆热等燃烧爆炸性能,更有利于降低纺丝电压和纺丝难度,提高实验的安全性,保障实验人员和实验室的安全。使用丙酮或乙酸乙酯作为纺丝溶液的溶剂,不掺水,不仅可以避免因溶剂挥发慢造成的纤维坍塌和静电力对纤维的拉伸作用力不充足,而且还可以避免因纳米含能粒子与水发生反应造成的活性位点以及金属纳米粒子的热力学性能降低。采用本发明提供的制备方法制备得到的纳米含能复合纤维孔隙率高、长径比大、均一度高,为纳米含能粒子提供了大量的负载位点,能够有效防止纳米含能粒子团聚。第二部分:复合纤维的性能评价1、爆热计算利用爆热的经验计算法—阿瓦克扬法计算nc以及实施例1至实施例4中的复合纤维的爆热,计算结果见下表:产品爆热nc4.058mj/kgnc/gap(实施例1)4.265mj/kgnc/gap/nano-tatb(实施例2)8.557mj/kgnc/gap/nano-tatb(实施例3)5.074mj/kgnc/gap/nano-tatb(实施例4)5.074mj/kg从上表可知:实施例1中的nc/gap和实施例2至实施例4中的nc/gap/nano-tatb纤维的爆热都显著高于nc;实施例2中的nc/gap/nano-tatb纤维的tatb比例较大,其爆热明显高于实施例3和实施例4。2、感度测量利用撞击感度仪测量实施例2至实施例4中的nc/gap/nano-tatb纤维的撞击感度,撞击感度仪选用1kg落锤。测量结果见下表:撞击感度nc/gap/nano-tatb(实施例2)79.8nc/gap/nano-tatb(实施例3)78.4nc/gap/nano-tatb(实施例4)78.2从上表可知:实施例2至实施例4中的nc/gap/nano-tatb纤维的感度很低。需要说明的是,上述实施例不以任何形式限制本发明,凡采用等同替换或等效变换的方式所获得的技术方案,均落在本发明的保护范围内。当前第1页12