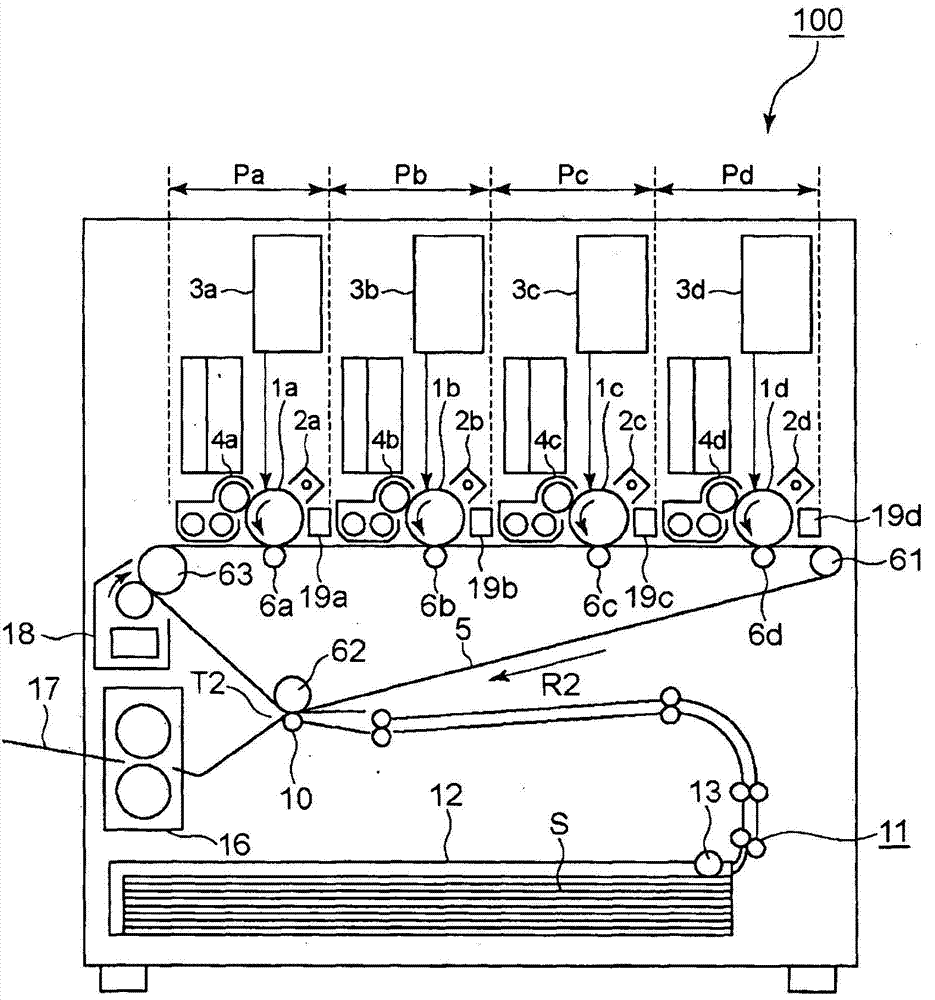
本发明涉及一种显影设备(装置),所述显影设备应用于成像设备例如复印机、打印机、记录图像显示设备、传真机等,目的是为了利用电子照相方法、静电记录方法等将形成在图像承载构件上的静电潜像显影为可视图像。特别地,本发明涉及一种显影设备(装置)的显影剂承载构件,所述显影设备使用由调色剂和磁性载体构成的双组分显影剂。
背景技术:
:使用电子照相成像方法的成像设备例如复印机将显影剂附着至形成在其图像承载构件例如感光鼓上的静电潜像,目的是为了将静电潜像显影为可视图像。根据现有技术的一些显影装置已知使用由调色剂和磁性载体构成的双组分显影剂。这些显影装置还已知使用一种方法,所述方法在保持双组分显影剂磁性地附着至显影剂承载构件的同时,通过利用其可旋转的显影剂承载构件(在下文中可以简称为显影套筒)将显影剂运送至紧邻图像承载构件的位置,使用双组分显影剂中的调色剂将图像承载构件(感光鼓)上的静电潜像显影为可视图像。通常,这些显影装置设置有显影套筒、固定的磁体和显影剂管控刮板(在下文中可以简称为管控刮板)。固定的磁体被安置在显影套筒中,以将显影剂磁性地保持到显影套筒的外周表面。管控刮板定位在显影套筒附近,其中在管控刮板自身和显影套筒的外周表面之间存在预定大小的间隙。因此,双组分显影剂能够承载在显影套筒上,并且在将其数量管控至预定值的同时被运送到紧邻感光构件的位置处。一般地,常见的做法是使用显影套筒,所述显影套筒的外周表面具有通过利用微观粒子的喷射(喷砂)形成的微观峰谷或者平行于显影套筒的旋转轴线延伸的多个微观槽,目的是为了确保显影剂被可靠地运送到感光构件的外周表面附近。然而,外周表面具有通过喷砂形成的微观峰谷的显影套筒的问题在于,如果微观峰谷的尺寸小于特定值,那么在显影剂运送方面的性能就有所不足。另一方面,如果为了提高显影套筒的显影剂运送性能而需要增大显影套筒在其外周表面上的峰谷的尺寸,那就必须增加对显影套筒的外周表面进行的喷砂处理的强度,由此在显影套筒的外周表面上喷射喷砂颗粒,这样做的问题在于喷砂处理可能会使显影套筒变形。因此,通常,目前使用的喷砂式显影套筒在其外周表面上的峰谷尺寸相对较小。然而,在显影套筒的外周表面上的峰谷尺寸较小的情况下,与在其外周表面上具有相对较大的峰谷的显影辊相比,在显影套筒被用于相当长时间的显影时,显影套筒的峰谷会因摩擦而相对快速地磨损,因此问题在于显影剂的运送性能不够稳定。这个问题可能会成为显影装置的使用寿命过早缩短的原因之一。近年来,开始要求复印机和打印机具有极高水平的图像质量、可靠性和稳定性。从满足这些要求的角度看,保持由显影套筒运送的显影剂的数量稳定非常重要。因此,已经提出了一种显影套筒,所述显影套筒具有平行于其轴线延伸的多个槽。在公开号为H02-50182的日本专利申请(专利文献1)中公开了一种这样的显影套筒。与利用喷砂使得显影套筒的外周表面设置有微观峰谷的方法不同,通过使显影套筒穿过模具而在显影套筒的外周表面中形成上述的槽能够使显影套筒的外周表面设置有相对较大的槽(峰和谷),而不会导致显影套筒变形。因此,与外周表面经受喷砂处理的显影套筒相比,利用模具使外周表面设置有微观槽的显影套筒受到摩擦影响的可能性更小,因此显影剂运送性能也更加稳定。外周表面设置有槽的显影套筒的显影剂运送性能稳定,但是其问题在于因下面的原因而要求显影套筒和上述的显影剂管控刮板之间的间隙相对较小。也就是说,即使显影辊的具有槽的外周表面能够使得显影套筒的显影剂运送性能稳定,但是其也会使得显影套筒的显影剂运送性能过度。因此,可能需要将显影套筒和管控刮板之间的间隙加工成相对较小,以补偿由显影套筒运送的过量的显影剂,这是因为除非减小间隙,否则显影辊上的显影剂的数量就会变得过多。此外,近年来,开始要求成像设备具有极高水平的图像质量。因此,为了尽可能地防止成像设备因显影套筒上的显影剂和形成在感光构件的外周表面上的调色剂图像之间的摩擦而在粒状性方面变差,存在减少由显影装置的显影套筒的外周表面承载的显影剂的数量的趋势。具体地,从使成像设备保持在所形成的图像中的粒状性水平良好的角度看,相对于显影套筒的旋转方向,在显影剂管控刮板的下游侧,显影套筒的每单位面积的外周表面上的显影剂量理想地被设定为处于(0.3±0.2)mg/mm2(=(30±20)mg/cm2)的范围内的值。更准确地说,优选的是按照标准比重G(显影剂涂层的表观厚度)来设定在管控刮板的下游侧保持涂布在显影套筒的外周表面上的显影剂的数量。也就是说,按照比重G,显影套筒的外周表面上的显影剂涂层的表观厚度M/S理想地处于0.029-0.14mm((30±20)mg/cm2)/3.48mg/mm3)(M/S[mg/mm2]/比重(密度)G[mg/mm3])=0.029-0.14mm((30±20)mg/cm2)/3.48mg/mm3)的范围内。尽管要求显影设备(装置)的显影套筒上的显影剂的厚度较小,但是仍然存在进一步减小显影装置的显影套筒和管控刮板之间的间隙的趋势。如果显影套筒和管控刮板之间的间隙表现为小于特定值,则易于引发这样的问题,即,异物等滞留在管控刮板附近并且干扰显影套筒上的显影剂涂层。因此,显影套筒和管控刮板之间的间隙的理想值是不小于0.2mm,优选地不小于0.3mm。另一方面,通过贸然地减小显影套筒的槽深度以为了允许加宽显影套筒和管控刮板之间的间隙而降低显影套筒的显影剂运送性能,可能会造成显影剂涂层不稳定,或者导致显影剂未能涂布显影套筒。因此,这是不理想的。技术实现要素:因此,本发明的主要目标是提供一种显影装置,所述显影装置使用显影剂承载构件,所述显影剂承载构件的外周表面设置有槽,所述显影装置构造成在显影剂承载构件的外周表面上形成足够薄的显影剂层以获得非常高质量的图像,所述显影装置不会遭遇因显影剂承载构件的显影剂运送性能过度或不足而造成的问题,所述问题包括:显影剂不符合预期地涂布显影剂承载构件,和/或异物堵塞在显影装置的显影剂承载构件的外周表面和显影装置的显影剂管控刮板之间的间隙中。【问题的解决方案】根据本发明的一方面,提供了一种显影设备,所述显影设备包括:显影剂承载构件,用于承载包括调色剂和磁性载体的显影剂,以使形成在图像承载构件上的潜像显影,所述显影剂承载构件包括这样的表面,所述表面具有沿着纵向方向延伸的多个槽;磁体,所述磁体设置在所述显影剂承载构件内部,用于吸引所述显影剂承载构件的表面上的显影剂;非磁性管控构件,所述非磁性管控构件设置成与所述显影剂承载构件间隔开,用于管控所述显影剂承载构件上承载的显影剂的数量,其中,在经过所述管控构件之后的单位面积的所述显影剂承载构件上承载的显影剂的数量M/S(mg/mm2)、所述管控构件的自由端部和所述显影剂承载构件之间的间隙SB(mm)、显影剂的密度G(mg/mm3)以及槽比率α即所述显影剂承载构件的表面中的槽的比率满足:0.1≤M/S(mg/mm2)≤0.5,0.2≤SB(mm),并且M/S(mg/mm2)×1/4≤α×{SB(mm)+D(mm)}×G(mg/mm3)<M/S(mg/mm2)通过结合附图考虑以下对本发明优选实施例的说明,本发明的各种目标、特征和优点将变得更加显而易见。附图说明图1是本发明的第一和第二实施例中的成像设备的示意性截面图,并且示出了设备的整体结构。图2是本发明涉及的典型显影装置在垂直于显影装置的显影套筒的轴线的平面上的示意性截面图。图3是本发明涉及的显影套筒和感光鼓之间的界面区域的放大截面图。图4是本发明涉及的显影装置的显影套筒的其中一个槽的放大的示意性截面图,并且用于图解槽的形状。图5是本发明涉及的显影装置的显影套筒的其中一个槽的放大的示意性截面图,并且用于图解槽的形状。图6是本发明涉及的显影装置的显影套筒的其中一个槽的放大的示意性截面图,并且用于图解槽的形状。图7是本发明涉及的显影装置的显影套筒和显影装置的管控刮板之间的间隙的放大的示意性截面图,并且用于图解间隙。图8是本发明涉及的显影装置的显影套筒和显影装置的管控刮板之间的其中一个间隙的放大的示意性截面图,并且用于图解显影套筒的槽节距和管控刮板的厚度B之间的关系。图9是示出了本发明的第一实施例中的显影装置以及比较性的显影装置的管控刮板和显影套筒之间的槽比率α和间隙SB之间的关系的表格。图10是根据本发明的显影装置的示意性截面图,所述显影装置的结构与本发明的第一实施例中的显影装置的结构不同。具体实施方式(实施例1)在下文中,将参照附图详细介绍本发明的实施例。然而,本发明还可以应用于多种显影装置,这些显影装置的结构部分地或者完全地不同于以下实施例中的显影装置的结构,只要这些显影装置装有形状和结构与以下实施例相同的显影套筒即可。也就是说,本发明不仅能够应用于其中的显影室和显影剂搅拌室串联地水平排列的显影装置,而且本发明还能够应用于其中的显影室和显影剂搅拌室串联地竖直排列的显影装置。此外,无论成像设备是串联型还是单鼓型、无论成像设备是中间转印型还是直接转印型,根据本发明的显影装置均可与成像设备相兼容。此外,在根据本发明的显影装置的以下介绍中,仅介绍了显影装置中的对于本发明来说必不可少的部分。然而,除了装置、设备、框架等以外,将在下文介绍的本发明实施例中的显影装置的各个部分可以用作打印机、复印机、传真机以及多功能机器的一部分。顺便提及,在上述专利文献1中公开的成像设备的整体结构在附图中并未示出,目的是为了不再重复相同的介绍。【成像设备】图1是用于介绍与本发明兼容的典型成像设备的整体结构的示图。参照图1,成像设备100是串联型并且也是中间转印型的全色打印机。也就是说,成像设备100具有:一一对应地形成黄色、品红色、青色和黑色调色剂图像的成像工作站Pa、Pb、Pc和Pd;以及中间转印带5,成像工作站Pa、Pb、Pc和Pd沿着中间转印带5串联排列。中间转印带5通过辊61、62和63被悬置并且能够沿着由箭头标记R2指示的方向运动。在成像工作站Pa中,黄色调色剂图像形成在感光鼓1a上并且被转印到中间转印带5上。在成像工作站Pb中,品红色调色剂图像形成在感光鼓1b上并且被转印到中间转印带5上。在成像工作站Pc和Pd中,青色调色剂图像和黑色调色剂图像分别形成在感光鼓1c和1d上并且被转印到中间转印带5上。在将颜色不同的四种调色剂图像转印到中间转印带5上之后,调色剂图像被运送到二次转印工作站T2,在二次转印工作站T2中,四种调色剂图像被转印到记录介质片材S上。与此同时,在记录介质盒12中的记录介质片材S由拾取辊13从盒12中取出,同时与盒12内其余的记录介质片材逐一分离,然后被运送到对齐辊对,所述对齐辊对以每张片材S与中间转印带5上的调色剂图像同时抵达二次转印工作站T2这样的定时将片材S送至二次转印工作站T2。在将调色剂图像转印到片材S上之后,片材S在定影装置16中经受加热和加压,使得调色剂图像被定影至片材S的表面。在将调色剂图像定影至片材S之后,片材S被排出到输送托盘17中。尽管成像工作站Pa、Pb、Pc和Pd所使用的调色剂的颜色不同,但是它们的结构大体相同。因此,在下文中,将仅介绍成像工作站P。除了表示成像工作站所使用的调色剂颜色的附图标记的后缀(b、c或d)不同之外,成像工作站Pb、Pc和Pd的介绍与成像工作站P相同。成像工作站P具有感光鼓1a。成像工作站P还具有电晕型的充电装置2a、曝光装置3a、显影装置4a、一次转印辊6a和鼓清洁装置19a,这些装置位于感光鼓1a的外周表面附近。感光鼓1a由铝制圆筒和形成在感光鼓1a的外周表面上的、能够以负极性充电的感光层构成。感光鼓1a以预定的处理速度沿着由箭头标记指示的方向旋转。电晕型充电装置2a用于将感光鼓1a的外周表面地均匀充电至预定的负极性VD(其对应于调色剂图像的未曝光区域的电势水平)。曝光装置3a通过利用激光束扫描感光1a的外周表面的均匀充电部分将待形成图像的静电图像写到感光鼓1a的外周表面的均匀充电部分上,在发射激光束的同时利用曝光装置的旋转镜使得激光束偏转。显影装置4a利用显影剂使得感光鼓1a的外周表面上的静电图像显影为调色剂图像,所述显影剂是调色剂和载体的混合物。一次转印辊6a通过被按压到中间转印带5的内表面上而在感光鼓1a和中间转印带5之间形成转印工作站。在向一次转印辊6a施加正DC电压(正直流电压)时,感光鼓1a上的带负电的调色剂图像被转印(一次转印)到中间转印带5上。鼓清洁装置19a回收转印残留的调色剂也就是未能转印到记录介质片材S上并因此保留在感光鼓1a的外周表面上的调色剂。在本实施例中用作图像承载构件的感光鼓1a是鼓形式的普通的有机感光构件。然而,本发明也可以与由例如非晶硅这样的感光物质形成的无机感光构件相兼容。此外,本发明还可以与带形式的感光构件相兼容。换言之,本发明的以下实施例并不旨在限制本发明的范围。也就是说,本发明还可以与多种成像设备相兼容,这些成像设备与本发明的以下实施例在充电方法、显影方法、转印方法、清洁方法和定影方法等方面有所不同。【显影装置】接下来,参照图2,详细介绍本实施例中的显影装置4。图2是本实施例中的显影装置在垂直于装置的长度方向的平面上的示意性截面图。该图用于介绍装置的结构。参照图2,显影装置4a具有作为显影剂承载构件的显影套筒28,以使感光鼓1a上的静电图像显影,所述显影套筒28承载由调色剂和磁性载体构成的显影剂。感光鼓1a以273mm/秒的处理速度(圆周速度)沿着由箭头标记R1指示的方向旋转。显影装置4a使用双组分显影剂,所述双组分显影剂是非磁性调色剂和磁性载体的混合物。显影装置4a的显影设施容器22具有:显影室23,用于为显影套筒28供应显影剂;以及搅拌室24,用于从显影套筒28上回收显影剂。两室23和24串联地并排定位。显影套筒28能够旋转地定位在显影设施容器的与感光鼓1a相对的区域中。显影室23和显影剂搅拌室24构成环路,在搅拌显影剂的同时运送显影剂通过该环路,所述的显影室23和显影剂搅拌室24是通过用分隔壁27划分显影设施容器而构建的两个室。两个室23和24并排定位,并且分别设置有可旋转的显影螺杆25和搅拌螺杆26。显影螺杆25和搅拌螺杆26通过沿着彼此相反的方向运送显影剂而使显影剂在显影设施容器22中循环运动。显影套筒28由非磁性物质例如铝或不锈钢制成。感光鼓1a的直径为80mm。显影套筒28和感光鼓1a之间在显影工作站中的最小距离为大约300μm。也就是说,显影装置构造成使得当显影剂被运送到显影工作站时,显影剂成为以刷(磁刷)的形式位于顶部,所述显影剂与感光鼓1a的外周表面相接触,由此使得能够显影感光鼓1a的外周表面上的静电图像。显影套筒28的外周表面设置有沿着显影套筒28的纵向方向延伸的槽,从而增加了能够由显影套筒28运送的显影剂的数量(在下文中这可以简称为“显影剂运送性能”)。在显影工作站中,显影套筒28沿着与感光鼓1a的外周表面的运动方向相同的方向(由图1中的箭头标记R28指示)旋转。显影套筒28相对于感光鼓1a的圆周速度比为1.75。显影套筒28相对于感光鼓1a的圆周速度比越大,显影效率就越高。然而,如果所述圆周速度比过大,则易于使得调色剂分散并且还易于发生显影剂退化等问题。因此,显影套筒28相对于感光鼓1a的圆周速度比理想地处于0.5-2.0的范围内。在使用双组分磁刷的显影方法的情况下,双组分显影剂中的磁性载体通过受到磁辊29的磁通量的约束而被保持到显影套筒28的外周表面。带负电的调色剂静电附着到显影套筒28的外周表面上的带正电的载体上。由此,“磁刷”作用在显影套筒28的外周表面上。因此,通过在向显影套筒28施加的DC电压和感光鼓1a的外周表面上的静电潜像之间提供预定量的电势差而使得感光鼓1a的外周表面上的潜像显影为可视图像。为了提高显影装置的显影效率(附着至静电图像的调色剂的比率),将-500V的DC电压和峰值电压为1,300V(Vpp=1,300V)且频率为12kHz(f=12,000Hz)的AC电压的组合作为显影电压施加到显影套筒28。一般来说,向显影套筒施加AC电压提高了显影套筒的显影效率,这使得成像设备能够输出更高质量的图像。然而,这样可能会导致调色剂附着到静电潜像的未曝光部分;这可能会导致成像设备输出模糊的图像。因此,在施加到显影套筒28的DC电压和感光鼓1a的外周表面充电所达到的电势(对应于图像的背景部分(白色区域))之间设置一定量的电势差,目的是为了防止调色剂附着到潜像的未曝光部分。顺便提及,本实施例并不旨在向显影套筒28施加的DC电压和AC电压的组合方面限制本发明。<调色剂>本实施例中的显影装置所使用的显影剂是由介电非磁性调色剂和磁性颗粒(载体)构成的双组分显影剂。非磁性调色剂的加权平均粒径理想地不小于10μm。本实施例中使用的非磁性调色剂是彩色复印机调色剂,所述彩色复印机调色剂的加权平均粒径为8μm。在此假设调色剂的加权平均粒径为M,且调色剂粒径为r。为了形成尽可能逼真的彩色图像,理想的是不小于90%权重的调色剂满足不等式:1/2M<r<2/3M,并且不小于99%权重的调色剂满足不等式:0<r<2M。作为用作调色剂所用材料的粘合树脂的示例,例如有苯乙烯共聚物譬如苯乙烯丙烯酸酯树脂和苯乙烯甲基丙烯酸酯树脂或聚酯树脂。然而,考虑到在对未定影的彩色图像进行定影时发生的彩色调色剂的定影,聚酯树脂因其理想的熔点而是优选的。利用干燥型的自动密度计更具体地说是AccuPyc1330(Shimazu有限责任公司的产品)来测量调色剂的真实比重。用于测量调色剂真实比重的方法与用于测量载体真实比重的方法(将随后介绍)相同。<磁性载体>关于磁性载体,理想的是基于体积分布标准的平均粒径在25-50μm的范围内(50%的粒径:D50)。在本实施例中使用的磁性载体的体积平均粒径为35μm。作为这样的载体,纯铁氧体颗粒(最大磁化量约为230emu的铜锌(Cu-Zn)铁氧体)或薄薄地涂覆有树脂的纯铁氧体颗粒是理想的。将在下文介绍利用多图像分析仪(Beckman-Caulter有限责任公司的产品)测量基于体积分布标准的平均粒径(50%的粒径:D50)。利用激光衍射/激光散射类型的粒径分布测量设备更具体地说是MicrotrackMT3300EX(Nikkiso有限责任公司的产品)获得粒径分布,所述粒径分布测量设备装配有干燥型的样本供应装置更具体地说是干燥型的一次性样本调节器Turbotrack(Nikkiso有限责任公司的产品)。用于将磁性载体供给Turbotrack的真空源是集尘器,所述集尘器的风量设定为大约33升/秒并且压力为17kPa。所述集尘器通过软件自动控制。获得的粒径为50%的粒径(D50),这是基于体积分布的累积值。通过设备自带的软件(版本为10.3.3-203D)来控制设备,并且通过设备自带的软件对测量结果进行分析。以下为测量颗粒尺寸时所处的条件细节:置零时间:10秒测量时长:10秒测量次数:1次颗粒折射率:1.81颗粒形状:非球形测量上限:1208μm测量下限:0.243μm环境:正常温度和正常湿度(23℃,50%RH)。利用干燥型的自动密度计更具体地说是AccuPyc1330(Shimazu有限责任公司的产品)测量磁性载体的真实比重。首先,将磁性载体样本无人值守地放置在温度为23℃且相对湿度为50%的环境中24小时。然后,精确地测量5g样本,并且将这5g样本放到测量单元(10cm3)中,随后将测量单元插入到密度计的主组件的样本室中。然后,启动密度计。在启动密度计时,自动测量样本的真实比重。在启动密度计时,用氦气清除样本室中的空气十次,所述氦气的压力被调节为20.000psig(2.392×102kPa)。然后,重复地清除氦气,直到样本室的内部压力的变动稳定在0.005psig/分钟(3.447×102kPa/分钟)为止。然后,测量样本室的内部压力。测试样本的体积能够根据样本室的内部压力的变化获得,这在样本室的内部压力处于平衡状态时进行(Voil定律)。能够利用以下的公式计算测试样本的真实比重:测试样本的真实比重(g/cm3)=测试样本的质量(g)/测试样本的体积(cm3)。关于载体的选择,可以使用树脂性的磁性载体,所述树脂性的磁性载体由粘合树脂和磁性或非磁性金属的氧化物构成。树脂性的磁性载体的特征之一是其最大磁化量约为190emu/cm3,小于铁氧体颗粒的的最大磁化量。因此,当树脂性的磁性载体被用作磁性载体时,相邻磁刷之间的磁干扰小于当使用铁氧体颗粒时的磁干扰。因此,显影装置的磁刷密度较高且磁刷高度较低。因此,与铁氧体颗粒相比,树脂性的磁性载体能够使得成像设备输出纹理更均匀和更精细并且分辨率更高的图像。【显影剂承载构件(显影套筒)】接下来,将详细介绍显影套筒28。显影装置设置有不可旋转的磁辊29,该不可旋转的磁辊29定位在显影套筒28的中空部中。磁辊29的外周表面设置有多个(本实施例中为四个)磁极N1、S1、S2和N3。在显影工作站中,磁辊29定位成使其磁极S2与感光鼓1a相对;磁极S1与作为显影层厚度管控构件的管控刮板30相对;磁极N2定位在磁极S1和S2之间;并且磁极N1和N3分别面向显影室23和搅拌室24。每一个磁极的磁通密度均处于40mT-70mT的范围内。然而,用于显影的磁极S2的磁通密度可以设定为100mT。显影套筒28沿着由箭头标记R28指示的方向旋转。用于管控显影套筒28上的显影剂层厚度的管控刮板30定位在显影区域的上游侧,在所述显影区域中显影套筒28与感光鼓1a相对。管控刮板30通过修正显影套筒28的外周表面上的磁刷的末端部分来管控显影套筒28上的显影剂层的厚度。管控刮板30是长且窄的非磁性金属板件(铝板),所述管控刮板30定位成使其长度方向平行于显影套筒28的长度方向。在被显影套筒28承载之后,显影剂被运送通过管控刮板30的管控边缘和显影套筒28的外周表面之间的间隙。本实施例中的管控刮板30的厚度为1.2mm。能够通过调节管控刮板30的管控边缘和显影套筒28的外周表面之间的间隙来调节通过显影套筒28的旋转而运送的承载在显影套筒28上的显影剂的数量。在本实施例中,允许保持涂布在显影套筒28的每单位面积的外周表面上的显影剂的数量被调节为0.3mg/mm2(=30mg/cm2)。从图像粒状性的角度看,相对于显影套筒28的旋转方向,在管控刮板30的下游侧,显影套筒28的每单位面积的外周表面上的显影剂的数量理想地处于(0.3±0.2)mg/mm2(=30±20mg/cm2)的范围内。实际上,允许保持涂布在显影套筒28的外周表面上的显影剂的数量要受到显影剂的比重G(mg/cm3)的影响。因此,为了准确地表示管控刮板的下游侧的显影套筒28上的显影剂的数量,应当用显影剂层的表观厚度(mm)(厚度(mm)=M/S(mg/mm2)/(比重G(mg/mm3))来表示显影剂的数量。在本实施例中,从图像粒状性的角度看,允许保持涂布在显影套筒28的外周表面上的显影剂的表观厚度(mm)理想地设定为处于29-140μm的范围内,优选地处于43-129μm范围内的值。换言之,间隙SB理想地设定为这样的值,使得在管控刮板30的下游侧,显影套筒的每单位面积的外周表面上的显影剂的数量M/S将处于(0.3±0.15)mg/mm2(=(30±15)mg/cm2):(M/S=(0.3±0.15)mg/mm2(30±15)mg/cm2)范围内。如果间隙SB不大于上述给定范围中的下限值,那么保持涂布在显影套筒28的外周表面上的显影剂的数量(M/S)就太少,并且因此显影剂涂层的厚度的不均匀性易于在图像质量的均匀性方面影响显影装置(成像设备)。另一方面,如果间隙SB不小于上限,那么显影装置(成像设备)就易于输出受到粒状性影响的图像,所述粒状性归因于由磁刷的末端部分对感光鼓1a的外周表面的摩擦。如果必须要提高显影装置的显影效率,那么显影装置必须增大间隙SB也就是显影套筒28和感光鼓1a之间的间隙。然而,如果简单地减小间隙SB,那么感光鼓1a的外周表面在显影工作站中会被磁刷摩擦。因此,也有可能输出粒状性可接受的图像。因此,减小显影装置中允许保持涂布在显影套筒28上的显影剂的数量M/S。随着数量M/S逐渐变小,即使显影套筒28和感光鼓1a之间的间隙SB被减小以提高显影装置的显影效率,显影套筒28的外周表面上的磁刷也不易于摩擦感光鼓1a上的调色剂图像。因此,显影装置(成像设备)易于输出高质量的图像。关于管控刮板30和显影套筒28之间的间隙,理想的是不超过0.2mm,这是因为如果管控刮板30和显影套筒28之间的间隙较小(不大于0.2mm),则异物等易于被堵塞在间隙中,并且影响显影装置(成像设备)的图像质量,正如在关于现有技术的先前段落中所述的那样。然而,装配有在外周表面设置槽的显影套筒的显影装置能够具有更高的显影剂运送性能。因此,显影装置的管控刮板30和显影套筒28之间的间隙能够加工得更小。另一方面,如果减小显影装置中的槽的深度以降低显影剂运送性能,则能够增大显影装置中的显影刮板30和显影套筒28之间的间隙。然而,如果轻率地减小了管控刮板30和显影套筒28之间的间隙,则显影套筒28上的显影剂涂层易于变得不稳定。因此,显影装置必须在将其显影套筒28的显影剂运送性能保持在适当水平的同时增大管控刮板30和显影套筒28之间的间隙。显影剂层厚度管控刮板30可以是仅由磁性板制成的磁性刮板,或者是非磁性板和磁性板的粘接组合。然而,在只是磁性刮板被用作管控刮板30的情况下,显影剂因磁性板的作用而倾向于收集在管控刮板30的附近。因此,显影套筒28的显影剂运送性能降低,这相应地使得可以增大管控刮板30和显影套筒28之间的间隙。然而,随着显影剂收集在磁性板(管控刮板)附近,显影剂会趋于退化。这是为何需要管控刮板30和显影套筒28之间留有间隙、而且仅由磁性板制成的刮板或者非磁性和磁性板的组合不被用作管控刮板30的原因所在。因此,本发明的发明人研究显影套筒28的显影剂运送性能和显影套筒28的外周表面上所具有的槽的形状之间的相关性。研究结果如下所述:发明人的研究揭示,在显影套筒28的显影剂运送性能和槽比率α之间存在强相关性,所述槽比率α是“显影套筒28的外周表面中被槽占据的部分相对于显影套筒28的整个外周表面的比率”。在槽平行于显影套筒28的长度方向的情况下,槽比率α能够表达为在垂直于显影套筒28的轴线的平面上的所有槽的宽度的总和与显影套筒28的周长的比率。特别地,参照图3,在显影套筒28的外周表面上的槽被设置成横截面形状相同并且间距(预定的周期性P)一致的情况下,槽比率α能够表达为以下公式的形式,其中,W代表槽宽度,P代表给定槽的中心和紧邻的槽的中心之间的距离。槽比率α=W/P…(1)当显影套筒28的半径为r,并且显影套筒28的外周表面上的槽的数量给定为N时,槽间距P能够表达为2πr/N(P=2πr/N)。显影套筒28的显影剂运送性能和槽比率α之间的强相关性意味着显影套筒28的外周表面中被槽占据的部分有助于显影剂运送并且显影套筒28的外周表面中未被槽占据的部分对显影剂运送几乎没什么帮助。换言之,只要槽是能够捕获并保留一定量的显影剂更具体地说是磁性颗粒的这种形状,那么槽就与槽的深度或类似性质无关地有助于显影剂的运送。因此,可以说显影套筒28的显影剂运送性能与槽宽度W具有强相关性,而与槽的横截面、槽的深度都不具有强相关性。然而,作为上述相关性保持成立的先决条件,槽必须使其能够捕获并保留一定量的显影剂。为了让槽能够捕获并保留显影剂,槽必须能够捕获并保留一定量的磁性载体即调色剂的载体。为了让槽能够捕获并保留一定量的磁性载体,槽宽度W必须大于磁性载体颗粒的直径2R,如图4(a)所示。如果槽宽度W小于磁性载体颗粒直径2R,则磁性载体颗粒无法装入槽中,并且因此,与槽深度D无关地,槽不能捕获并保留磁性载体(颗粒)。此外,如图5(a)所示,槽深度D至少必须大于磁性载体颗粒的半径R。接下来,参照图5(b),如果槽深度D小于磁性载体颗粒的半径R,则磁性载体颗粒就无法足够深地装入以供槽捕获并保留磁性颗粒,并且因此也易于滑移。因此,槽宽度W、槽深度D、磁性载体颗粒直径2R和磁性载体颗粒半径R之间的关系必须满足以下的不等式2和3。此外,槽宽度W理想的是不大于磁性载体直径(2R)的十倍(20R)。如果槽宽度W大于20R,则对于载体颗粒而言不易于保持被捕获在槽中。因此,有不能无法充分实现槽对显影套筒28的显影剂运送性能的作用。20R>W>2R…(2)D>R…(3)只要槽深度D大于磁性载体颗粒半径R,就能确保由槽捕获的磁性载体颗粒保留在槽中。然而,如果槽深度D如图6所示被加工为大于磁性载体颗粒直径2R,则整个磁性载体颗粒都装入槽中,使得磁性载体颗粒基本不可能滑出槽。因此,优选的是将槽加工为使其深度D大于磁性载体颗粒直径2R(D>2R)。关于显影套筒28的外周表面的无槽部分,理想的是显影套筒28的外周表面包括有槽部分,这是因为如果无槽部分粗糙,那么就显影剂运送性能而言在有槽部分和无槽部分之间并无明显差异,这就降低了本发明的有效性。因此,显影套筒28的外周表面的无槽部分的表面粗糙度(中心线平均粗糙度)理想的是不大于0.5(Ra≤0.5),优选地不大于0.25(Ra<0.25)。在JISB0601中给出了中心线平均粗糙度Ra的定义。利用接触型的表面粗糙度测量仪更具体地说是SurfcorderSE-3300(KosakaLaboratory有限责任公司的产品)来测量显影套筒28的外周表面的表面粗糙度Ra。测量表面粗糙度Ra所采用的条件是截断值为0.8mm、测量长度为2.5mm、运送速度为1.0mm/秒并且放大率为5,000倍。显影套筒28的显影剂运送性能和槽比率α之间存在相关性的先决条件是能够以通过磁性载体颗粒的磁力使得磁性载体颗粒形成磁性载体颗粒的磁穗(链条)这样的方式在显影套筒28的外周表面上形成磁刷,所述磁穗从被显影套筒28的槽捕获并保留在槽中的磁性颗粒延伸。通过如上所述的磁刷的形成,整个磁刷都在磁性载体颗粒处于槽中的情况下运送,由此增强了显影套筒28的显影剂运送性能。如上所述形成磁刷的必要条件是磁辊29例如像本实施例中所述位于显影套筒28的中空部中。由于在显影套筒28的中空部中存在磁辊29,因此通过磁辊29的磁场引发磁性载体中的磁性。然而,如果磁辊29的磁通密度|B|(=(Br2+Bθ2+Bz2)1/2)小于特定值,那就不能形成磁刷。因此管控刮板30和显影套筒28之间的区域的磁通密度|B|必须大于特定值。只要管控刮板30和显影套筒28之间的区域的磁通密度不小于10mT,即可形成磁刷。因此得以实现将在下文介绍的本发明的效果。只要满足上述条件,则由显影套筒28的槽捕获磁刷的基部部分。因此,随着显影套筒28的旋转,运送整个磁刷。也就是说,只要满足上述条件,则显影套筒28的外周表面的有槽部分有助于显影剂运送。显影套筒28是否运送磁刷取决于磁刷的基部部分是否被槽捕获并保持被槽捕获。也就是说,必要的是满足上述条件,即,相对于磁性载体颗粒半径R,槽的深度对于被槽捕获并保持被槽捕获的磁性载体颗粒而言足够深。换言之,并不意味着简单地增加槽的深度就能确保提高显影套筒28的显影剂运送性能。另一方面,增加槽的宽度增加了被槽捕获并保持被槽捕获的磁刷的数量。因此,显影套筒28提高了显影剂运送性能。换言之,这些发现与本发明的发明人获得的结论一致,也就是说,结论是显影套筒28的显影剂运送性能与槽比率α具有强相关性,与槽的深度D或槽的横截面不具有强相关性,所述槽比率α能够表达为显影套筒28的外周表面中被槽占据的部分相对于显影套筒28的整个外周表面的比率α的形式。因此,能够反推出可以通过调节显影套筒28的槽比率α来控制显影套筒28的显影剂运送性能。也就是说,通过在确保槽仍然能够捕获并保留磁性载体颗粒的同时调节显影套筒28的槽深度D,即可调节显影套筒28的显影剂运送性能且不会导致显影套筒28上的显影剂涂层变得不稳定。接下来,在考虑上述发现和结论的同时介绍本发明,本发明的目标是提供一种显影装置,所述显影装置的管控刮板30和显影套筒之间的间隙比介绍过的常规显影装置更宽。如上所述,在显影套筒28的显影剂运送性能和槽比率α之间存在强相关性意味着与显影套筒28的外周表面的无槽部分相比,显影套筒28的外周表面的有槽部分对显影剂运送性能的贡献更大;显影套筒28的无槽部分在显影剂运送性能方面的贡献不如有槽部分高。如果假设仅通过有槽部分运送显影剂,则被运送通过管控刮板30和显影套筒28之间的间隙的显影剂在每单位面积(10mm×10mm)上的估算最大量可以表达为以下的数学公式(公式4)的形式。“仅通过有槽部分运送显影剂”是指只有显影套筒的外周表面上的构成磁刷的显影剂部分28k才通过显影套筒28运送。此外,“估算最大量”表示当显影套筒28的外周表面的有槽部分和管控刮板30之间的空间充满显影剂时由显影套筒28运送的显影剂的数量。实际上,可以认为在有槽部分运动通过管控刮板30的同时由显影套筒28的有槽部分运送的显影剂并不是占据显影套筒28的有槽部分和管控刮板30之间的空间的全部显影剂。也就是说,可以认为占据上述空间的显影剂中的一部分不是通过有槽部分运送的显影剂。然而,在本实施例中,假设通过有槽部分运送上述空间中的全部显影剂,由此估算能够由显影套筒28运送的显影剂在每单位面积上的最大量。10mm×10mm×α×{SB(mm)+D(mm)}×G(mg/mm3)…(4)在此,槽比率α是显影套筒28的外周表面的有槽部分的总和相对于显影套筒28的整个外周表面的比率。因此,每单位面积(10mm×10mm)上有槽部分的比率是10mm×10mm×α。参照图7(a),“SB”代表管控刮板30和显影套筒28之间的间隙,更准确地说是代表管控刮板30的管控侧和显影套筒28的外周表面的无槽部分之间的间隙。接下来,参照图7(b),在管控刮板30的管控侧相对于显影套筒28的外周表面倾斜的情况下,“SB”代表管控刮板30的管控侧的更接近的边缘和显影套筒28之间的间隙。“D”代表槽深度。因此,显影套筒28的外周表面的有槽部分和管控刮板30之间的空间的高度表达为(SB+D)。因此,如果假设仅通过显影套筒28的外周表面的有槽部分运送显影剂,那么运动通过管控刮板30和显影套筒28之间的间隙SB的显影剂在每单位面积上的体积表达为10mm×10mm×α×(SB+D))。高度(SB+D)主要是影响槽的形状。因此,在此假设槽的横截面是矩形。然而,即使槽是V形、U形或者是不同于V形或U形的其它形状,只要(SB+D)被用作上述空间的高度,那就不会出现低估高度的情况,确定无疑的是应略微地高估由显影套筒28运送的显影剂的数量。在此,理想的是估算由显影套筒28运送的显影剂的数量。因此,与槽的形状无关地,高度可以表达为(SB+D)。“G”代表显影剂的比重。由此,通过将上述体积乘以G而获得的值是由显影套筒28运送的显影剂的数量。因此,能够利用上述的公式4计算由显影套筒28运送的显影剂的数量。因为本实施例中的显影剂主要是调色剂和磁性载体的混合物,所以能够用以下的公式5的形式表示显影剂的比重G,其中,“C”和“T”分别代表磁性载体和调色剂的比重,并且“P”和“(1-P)”分别代表调色剂和磁性载体在显影剂中的重量比:G=1/{(1-P)/C+P/T}…(5)能够由公式4获得的值是能够由显影套筒28的外周表面的有槽部分运送的显影剂的估算最大量。这些公式、方程和不等式符合将在下文介绍的实验的结果。实际上,在管控刮板30的下游侧,每单位面积(10mm×10mm)上实际的显影剂数量M/S有时会大于由公式4获得的值。也就是说,存在满足以下的不等式6的情况。也就是存在这样的情况,仅由有槽部分运送的显影剂的数量小于由显影套筒28运送的显影剂的实际数量:10mm×10mm×α×{SB(mm)+D(mm)}×G(mg/mm3)<M/S(mg/mm2)×10mm×10mm…(6)不等式6的左侧是由显影套筒28的外周表面的有槽部分运送的显影剂的估算最大量。因此,在满足不等式6的情况下,由显影套筒28的槽部分运送的显影剂的数量小于在管控刮板30的下游侧的显影套筒28上的显影剂的数量M/S。也就是说,无槽部分也有助于显影剂运送。因此,在满足不等式6的情况下,显影套筒28和管控刮板30之间的间隙能够增加的量等于由无槽部分运送的显影剂的数量,无槽部分的显影剂运送性能小于有槽部分的显影剂运送性能。相比而言,在不满足不等式6的情况下,能够由显影套筒28的有槽部分运送的显影剂的数量与显影套筒28上的显影剂数量M/S相匹配。在这种情况下,显影套筒28的有槽部分的显影剂运送性能相当高。因此,主要由显影套筒28的槽部分运送的显影剂的数量与显影套筒28上的显影剂的数量M/S相匹配。因此,可能必须要大幅度减小显影套筒28和管控刮板30之间的间隙。可以用不等式6'替代不等式6:α×﹛SB+D﹜×G<M/S…(6')使用以下方法获得显影套筒28的每单位面积(10mm×10mm)的外周表面上的显影剂数量的值M/S。也就是说,首先制备罩,所述罩匹配显影套筒28的外周表面的曲率并且具有预定尺寸(在由本发明的发明人实施的实验的情况下为50mm×10mm)的开口。然后,在保持罩围绕显影套筒28的同时通过罩的开口回收显影套筒28的外周表面上的显影剂。然后,测量回收的显影剂的重量。然后,通过将获得的已回收显影剂的重量转换成每单位面积(10mm×10mm)上的显影剂的数量而获得M/S的值(在本发明的发明人的情况下,通过用已回收的显影剂的重量除以5来获得M/S的值)。本发明的要旨是调节槽比率α满足不等式6,目的是为了使得显影套筒28和管控刮板30之间的间隙SB不必过窄,更具体地说是不必减小至不大于0.2mm。<实施例>接下来,参照本发明以下实施例中的显影装置以及比较性的显影装置具体地介绍本发明。表1中示出了在多种条件下实施的实验的结果,所述实验用于发现显影套筒的外周表面中的槽的规格特别是槽的形状与显影套筒的性能之间的关系。参照表1,在实验中使用的每一个显影套筒28都设置有多个槽,所述多个槽是V形截面并且沿着显影套筒28的长度方向延伸,其中,相对于显影套筒的圆周方向设置成预定的间隔(槽节距),如图3所示。表1在实验中使用的显影剂是如上所述的调色剂和由铁氧体制成的磁性载体的混合物。调色剂的重量比(P)和磁性载体的重量比(1-P)分别是0.1(=P)和0.9(=1-P)。调色剂的比重是1.0mg/mm3,磁性载体的比重是4.8mg/mm3。因此,利用公式5获得的显影剂的比重G是3.48。此外,磁性载体的粒径为35μm。显影装置设置成使得在管控刮板30的下游侧,显影套筒28的外周表面上的显影剂的数量M/S为0.3mg/mm2(=30mg/cm2)(M/S=0.3mg/mm2(=30mg/cm2))。然后就显影套筒28和管控刮板30之间的间隙(=SB)的数量能够如何设置来研究表1中的每个显影套筒。不允许将间隙SB设置成不小于0.2mm的显影套筒被记为“N”,而允许将间隙SB设置成不小于0.2mm的显影套筒被记为“G”。此外,允许将间隙SB设置成不小于0.3mm的显影套筒被记为“E”。在每一次实验中,用裸眼检查显影套筒28上的显影剂涂层的状况。具有均匀显影剂涂层的显影套筒被记为“E”,而所具有的显影剂涂层不均匀到足以有助于形成令人不满意的图像的显影套筒被记为“N”。其上的显影剂涂层略有不均匀但还不足以有助于形成令人不满意的图像的显影套筒被记为“G”。实施例1:第一实施例中的槽比率α为0.08(α=0.080)的显影套筒允许将间隙SB设置为0.45mm。如果间隙(SB)为0.45mm,则通过将0.45(=SB)代入公式4(=不等式6的左侧)获得的值为13.9,该值小于每单位面积(10mm×10mm)上的理想数量M/S(=不等式6的右侧)30(=0.3×10×10)的一半。因此,满足不等式6。也就是说,与由槽部分运送通过管控刮板30的显影剂的数量相比,由无槽部分运送通过管控刮板30的显影剂的数量可观。因此,可以将间隙SB设置为大约0.45mm。可以合理的假设这就是为何可以将间隙SB设置为大约0.45mm的原因所在。实施例2:当使用第二实施例中槽比率α为0.096(α=0.096)的显影套筒时,可以将间隙SB设定为0.35mm。因此,通过用0.35代入公式4(=不等式6的左侧)中的SB而获得的值为13.6,该值小于每单位面积(10mm×10mm)上的量M/S(=不等式6的右侧)30(=0.3×10×10)的一半。因此,满足不等式6。也就是说,与由槽部分运送通过管控刮板30的显影剂的数量相比,由无槽部分运送通过管控刮板30的显影剂的数量可观。这看起来就是为何可以将间隙SB设置为大约0.35mm的原因所在。实施例3:当使用第三实施例中槽比率α为0.143(α=0.143)的显影套筒时,间隙SB可以被设定为0.3mm。因此,通过用0.3代入公式4(=不等式6的左侧)中的SB而获得的值是19.4,该值小于显影套筒28的每单位面积(10mm×10mm)上的显影剂数量M/S的理想值30(=0.3×10×10)。因此满足不等式6。基于这一事实,可以合理地认为不仅由槽部分运送显影剂,而且也由无槽部分运送显影剂。因此,可以将间隙SB设置为0.2mm或更大。然而,与第一和第二实施例中的显影套筒相比,本实施例中的显影套筒的由槽部分运送的显影剂的数量较大,也就是说,由无槽部分运送的显影剂的数量较小。因此,即使可以将间隙SB设置为大约0.3mm,其也明显地大于0.2mm。实施例4:当使用第四实施例中的槽比率α为0.229(α=0.229)的显影套筒时,间隙SB可以被设定为0.2mm。因此,通过用0.2代入公式4(=不等式6的左侧)中的SB而获得的值是23.1,该值小于显影套筒28的每单位面积(10mm×10mm)上的显影剂数量M/S的理想值30(=0.3×10×10),并且因此满足不等式6。因此,可以合理地认为不仅利用槽部分运送显影剂,而且也利用无槽部分运送显影剂,并且因此可以将间隙SB设定为0.2mm或更大。然而,与第一、第二和第三实施例中的显影套筒相比,本实施例中的显影套筒的由槽部分运送的显影剂的数量明显更大。这看起来就是为何间隙SB必须设置为相对较小的值0.2mm的原因所在。在第四实施例中的显影套筒的情况下必须将间隙SB设置得较小的另一个原因是该显影套筒的槽节距P相对于管控刮板30的厚度而言较小。更具体地,第四实施例中的显影套筒的槽节距P是0.785mm(P=0.785mm),而管控刮板30的厚度B是1.2mm(B=1.2mm)。即,槽节距P(0.785mm)小于管控刮板30的厚度B(1.2mm)。在槽节距P小于管控刮板30的厚度B的情况下,有时两个或更多个有槽部分会同时运动经过管控刮板30,由此形成由从有槽部分延伸的两个磁刷夹持的空间,如图8(b)所示。位于由两个磁刷形成的空间中的显影剂没有释放的空间,且因此易于承受由磁刷施加的机械力和磁力。因此,即使是无槽部分也易于提高显影剂运送性能。因此,理想的是将槽节距P加工为大于管控刮板30的厚度,如图8(a)所示,目的是为了防止两个或更多个有槽部分同时运动经过管控刮板30。参照8(c),即使在管控刮板30的面向显影套筒28的表面相对于显影套筒28的外周表面以角度θ倾斜的情况下,只要槽节距P大于管控刮板30的面向显影套筒28的表面在显影套筒28的外周表面上的投影的长度(Bcosθ),就能获得与上述效果相类似的效果。比较性的显影套筒1:在槽比率α为0.389(α=0.389)的第一比较性显影套筒的情况下,间隙(SB)不能被设置为0.2mm或更大。通过用0.2mm代入公式4(不等式6的左侧)中的SB而获得的值为44.3,该值大于显影套筒28的每单位面积(10mm×10mm)上的显影剂数量M/S的理想值30(=0.3×10×10)。因此,为了满足不等式6,间隙SB必须不大于0.2mm。实际上,如果M/S是30,则间隙SB是0.17mm。因此,通过用0.17代入SB获得公式4(=不等式6的左侧)的值为40.2,该值大于显影套筒28的每单位面积(10mm×10mm)上的显影剂数量M/S的理想值(=不等式右侧)30(=0.3×10×10),并且因此,不满足不等式6。比较性的显影套筒2:在槽比率α为0.382(α=0.382)的第二比较性显影套筒的情况下,间隙SB不能被设置为0.2mm或更大。通过用0.2mm代入公式4(不等式6的左侧)中的SB而获得的值为34.6,该值大于显影套筒28的每单位面积(10mm×10mm)上的显影剂数量M/S的理想值30(=0.3×10×10)。因此,为了满足不等式6,间隙SB必须不大于0.2mm。实际上,如果M/S是30,则间隙SB是0.18mm。因此,通过用0.18代入SB获得公式4(=不等式6的左侧)的值为31.9,该值大于显影套筒28的每单位面积(10mm×10mm)上的显影剂数量M/S的理想值(=不等式右侧)30(=0.3×10×10),并且因此,不满足不等式6。图9是示出了在使用本发明实施例中的显影套筒和比较性显影套筒时的槽比率α和SB之间的关系的曲线图。在M/S设置为0.30的情况下,横轴代表槽比率α,纵轴代表SB。由该曲线图显而易见的是,槽比率α和SB之间存在强相关性。概括地说,减小槽比率α就允许将间隙SB设置得更宽。特别地,将槽比率α设置为0.229或更小就允许间隙SB明显加大。我们认为这一点可行是因为0.229大致上就是能够满足不等式6和不能满足不等式6之间的界线值。实际上,参照槽比率α是0.229的情况,在图9的右侧也就是在槽比率大于0.229时,不能满足不等式6,而参照槽比率α是0.229的情况,也就是参照槽比率α是0.229的情况,在图9的左侧也就是在槽比率小于0.229时,满足不等式6。在不满足不等式6的情况下,主要由有槽部分运送显影剂。因此,通过改变间隙SB来改变量M/S。因此,如果尝试通过减小槽比率α而减小M/S来增加SB,则在略微增宽SB时,M/S便恢复到原始值。也就是说,不能大幅增宽SB。实际上,在槽比率α相对较大的图9的右侧表示通过增加槽比率α不允许大幅增加SB。另一方面,在满足不等式6的情况下,无槽部分积极地有助于显影剂的运送。因此,通过改变SB不会显著地影响M/S。因此,即使尝试通过减小槽比率α而减小M/S来实现增宽SB,M/S也不会恢复到原始值,除非SB大幅增宽。因此,可以增宽SB。实际上,参照槽比率α是0.229的情况,图9的曲线图中的左侧也就是满足不等式6时表示通过减小槽比率α允许大幅增宽SB。也就是说,在本实施例中,槽比率α理想地不大于0.229(α≤0.229)。可以合理地推导出以下内容:只要公式4的值小于M/S即在管控刮板30相对于显影套筒28的旋转方向的下游侧的显影套筒28的外周表面上的显影剂的数量,也就是只要槽比率α设置成使得满足不等式6,则无槽部分就明显地有助于显影剂运送。因此,即使M/S较小,也可以将SB设置为不小于0.2mm。用于显影装置的理想的结构布置如下:首先,为了确保不仅由有槽部分而且也由无槽部分运送显影剂,公式4的值理想的不大于在管控刮板30的下游侧的显影套筒28的一部分外周表面上的显影剂的数量M/S(在本实施例中为30mm/cm2)的23/30。即,参照图9,在第四实施例中(槽比率α=23/30),公式4的值不超过M/S的理想值(在本实施例中为30)的23/30(第三实施例:19.4/30)。因此,能够由无槽部分运送至少7/30,从而确保能够增宽SB。关于SB的更加理想的范围,在公式4的值相对于管控刮板的下游侧的显影套筒28的外周表面上的显影剂的数量M/S而言不超过19/30的情况下,不仅确保显影装置处在无槽部分也有助于显影剂运送的状态下,而且能够进一步增加无槽部分在显影剂运送性能方面所占的比率。结果,能够进一步增宽SB。因此,理想的是,由无槽部分以及有槽部分来运送显影剂。本实施例等价于α≤0.143的情况。只要槽比率α处于该范围内,就能够理想地增强上述效果。此外,参照图9,在槽比率α不大于0.12(α≤0.12)的情况下,本实施例能够使得SB大致为第一和第二比较性显影套筒的SB的两倍宽。因此,理想的是槽比率α不大于0.12。换言之,只要将槽比率α设置成使得公式4的值相对于在管控刮板30的下游侧的显影套筒28的一部分外周表面上的显影剂的理想数量M/S而言不大于16/30,就能够获得与上述效果大体类似的理想效果。在此情况下,能够令人满意地增加显影装置的由无槽部分运送显影剂的比率。进一步地介绍,在第一和第二实施例的情况下,公式4的值不大于在管控刮板30的下游侧的显影套筒28上的显影剂数量M/S(在本实施例中为30)的一半(15/30),如公式7所示。因此,可以进一步增宽SB。这看起来就是为何显影装置能够相对于有槽部分增加由无槽部分运送的显影剂的比率的原因,也就是说,无槽部分能够更加积极地用于显影剂运送。10mm×10mm×α{SB(mm)+D(mm)}×G(mg/mm3)<M/S(mg/mm2)×10mm×10mm/2…(7)还研究了第五实施例中的显影套筒的实验结果,第五实施例中的显影套筒的直径与前述显影套筒的直径不同。实验结果表明能够与显影套筒28的直径无关地获得相同的结果。实施例5:在使用第五实施例中的槽比率α为0.078(α=0.078)的显影套筒的情况下,能够将间隙SB设置为0.40mm。通过用0.4代入SB获得公式4(=不等式6的左侧)的值为12.5,该值小于显影套筒28的每单位面积(10mm×10mm)上的显影剂的数量M/S的理想值30(0.3×10×10)的一半,并且因此满足不等式6。因此,可以合理地认定在运送显影剂通过管控刮板30和显影套筒28之间的间隙SB的同时,由无槽部分运送不少于一半的显影剂。因此,可以合理地认为这就是为何能够将间隙SB设置为大约0.4mm的原因所在。此外,还研究了显影套筒的槽比率α更小的情况(实施例6和7)。实施例6:在使用第六实施例中的槽比率α为0.040(α=0.040)的显影套筒的情况下,能够将间隙SB设置为0.5mm(SB=0.5)。用0.5代入公式4中的SB获得公式4(=不等式6的左侧)的值为7.61,该值小于每单位面积(10mm×10mm)上的理想的取值或显影剂数量M/S(=30)。因此,满足不等式6(7)。可以合理地认为这就是为何能够将间隙SB设置为大约0.5mm的原因所在。实施例7:在使用第七实施例中的槽比率α为0.032(α=0.032)的显影套筒的情况下,能够将间隙SB设定为0.6mm(SB=0.6)。用0.6代入公式4中的SB获得公式4(=不等式6的左侧)的值为7.23,该值小于30(0.3×10×10)或者每单位面积(10mm×10mm)上的显影剂数量M/S的理想值(不等式6的右侧)。因此,满足不等式6(7)。可以合理地认为这就是为何能够将间隙SB设定为大约0.6mm的原因所在。然而,在第七实施例的情况下,显影套筒28的显影剂运送性能处于不会造成问题的水平。但是,显影剂涂层却略有不均。造成该问题的原因看起来是由有槽部分运送的显影剂的比率为7.23/30=0.241,该值小于由显影套筒28运送的全部显影剂的1/4。因此,可以合理地认为由无槽部分运送的显影剂的比率过高,并且因此影响了显影套筒28的显影剂运送性能。因此,公式4的值理想的是不小于显影剂数量M/S的理想值的1/4,如不等式8所示:10mm×10mm×α×{SB+D}×G≥M/S/4…(8)在表2中给出了实验结果,在所述实验中,利用显影套筒研究了显影套筒28的外周表面中的槽的形状对显影套筒28的显影剂运送性能的影响,所述显影套筒的槽深度D和槽宽度W以及槽形状与第一实施例中有所不同。表2套筒直径(mm)No.P(mm)W(mm)D(mm)W/PSB涂层状态实施例820501.2560.100.040.080EE实施例920501.2560.100.030.080EG比较示例320501.2560.100.010.080EN比较示例420501.2560.030.040.016EN在实验中使用的显影剂与在表1中给出结果的实验所用的显影剂相同。也就是说,显影剂的比重G为3.48(G=3.48),并且磁性载体的粒径为35μm。与在表1中给出结果的实验中使用的显影套筒相同,用于这些实验的显影装置设定为使得在管控刮板30的下游侧,显影套筒28的外周表面上的显影剂数量M/S为0.3mg/mm2(=30mg/cm2)。然后,针对表2中列出的每一个显影套筒28研究显影套筒28和管控刮板30之间的间隙SB能够设定的值。此外,还检查了显影剂涂层的状态。实施例8:在使用第八实施例中的槽比率α为0.080(α=0.080)的显影套筒的情况下,能够将间隙SB设置为0.45mm(SB=0.45)。用0.45代入公式4(=不等式6的左侧)中的SB获得公式4的值为13.6,该值小于显影套筒28的每单位面积(10mm×10mm)上的显影剂数量M/S的理想值30(=0.3×10×10)的一半,并且因此满足不等式6(7和8)。因此,可以合理地认为无槽部分的贡献不小于由显影套筒28运送通过管控刮板30的显影剂的数量的一半,并且因此可以将间隙SB设定为大约0.45mm。实施例9:在使用第九实施例中的槽比率α为0.080(α=0.080)的显影套筒的情况下,能够将间隙SB设置为0.50mm(SB=0.50)。用0.50代入公式4(=不等式6的左侧)中的SB获得公式4的值为14.7,该值小于显影套筒28的每单位面积(10mm×10mm)上的显影剂数量M/S的理想值30(=0.3×10×10)的一半,并且因此,满足不等式6。因此,可以合理地认为在运送显影剂通过管控刮板30和显影套筒28之间的间隙的同时,由无槽部分运送的显影剂不少于一半,并且因此可以将间隙SB设定为大约0.50mm。然而,在第九实施例的情况下,虽然不存在关于显影套筒28的显影剂运送性能方面的问题,但是在显影剂涂层上能够检测到少量的不均匀性。造成这种现象的原因看起来是归因于以下的事实:因为显影套筒28的槽的深度D为30μm,该深度小于磁性载体颗粒的直径2R,所以这对于磁性载体颗粒而言略微地不易于被槽捕获并保持被捕获在槽中,这就影响了显影套筒28的显影剂运送性能。因此,理想的是槽宽度W大于磁性载体的粒径2R,正如先前由不等式2表示的那样。比较性显影套筒3:在使用槽比率α为0.080(α=0.080)的第三比较性显影套筒28的情况下,能够将间隙SB设置为0.6mm,但是显影套筒上的显影剂涂层不稳定。这种现象看起来表明:因为槽深度D为10μm,该深度小于磁性载体颗粒的半径,所以槽的捕获并保留磁性载体颗粒的能力太小,这就影响了显影套筒28的显影剂运送性能。因此,理想的是槽深度D大于磁性载体颗粒的半径R,正如先前由不等式3表示的那样。比较性显影套筒4:在使用槽比率α为0.016(α=0.016)的第四比较显影套筒的情况下,能够将间隙SB设置为0.8mm,但是显影套筒上的显影剂涂层不稳定。该问题看起来归因于以下事实:与第三比较性显影套筒不同,第四比较性显影套筒的槽深度D为40μm,该深度大于磁性载体颗粒的直径2R,但是槽宽度W为30μm,该宽度小于磁性载体颗粒的直径2R。因此,磁性载体颗粒不能完全装入槽中。因此,槽不易于捕获和保留磁性载体颗粒,磁性载体颗粒不易于附着至槽,这就影响了显影套筒28的显影剂运送性能。因此,理想的是槽宽度W大于磁性载体颗粒的直径2R。到目前为止,已经介绍了在管控刮板30的下游侧,显影套筒的每单位面积的外周表面上的显影剂数量M/S是0.3mg/mm2(=30mg/cm2)的情况。然而,即使显影剂数量M/S不是0.3mg/mm2(=30mg/cm2),前述情况的介绍也依然成立。如上所述,从显影套筒显影的图像的粒状性的角度看,显影套筒的每单位面积的外周表面上的显影剂数量M/S理想地设定为(0.3±0.2)mg/mm2(=(30±20)mg/cm2)。更精确地,理想的是通过根据比重标准化在管控刮板30的下游侧涂布在显影套筒上的显影剂的数量而获得的值(显影剂涂层的表观厚度)=(M/S(mg/mm2)/比重G(mg/mm3))处于29-140μm的范围内。在将M/S设定为处于上述范围内的值的情况下,能够利用不等式6如下所述地估算可用于将间隙SB设定为0.2mm或更宽的槽比率α的值。由于显影剂数量M/S的值越小,就越难以满足不等式6。因此,假设M/S=0.1mg/mm2,并且SB=200μm,计算槽比率α。此外,关于标准化的槽深度D和槽宽度W,假设D=0.06mm且G=3.5mg/mm3。因此,不等式6变成:10×10×α×(0.20+0.06)×3.5<0.1×10×10因此,α<0.1099。因此,即使考虑到槽深度和显影剂比重的偏差,在将M/S设定为处于(30±20)mg/cm2范围内的值时也能够满足不等式6。此外,在为了更好的图像质量而将M/S和SB分别设定为0.15mg/mm2和200μm的情况下,不等式6变成:10×10×α×(0.20+0.06)×3.5<0.15×10×10因此α<0.1648。因此,即使考虑到槽深度的偏差和显影剂的比重的偏差,只要显影套筒被加工为槽比率小于0.16(α<0.16),那么即使在将M/S设定为处于(30±15)mg/cm2的范围内的值的情况下,也能够满足不等式6(这从防止形成令人不满意的粒状性和/或令人不满意的低密度的图像的角度看是有利的)。此外,在为了更好的图像质量而将M/S设定为0.15mg/mm2并且SB增宽为300μm(M/S=0.15mg/mm2,SB=300μm)的情况下,不等式6变成:10×10×α×(0.30+0.06)×3.5<0.15×10×10因此α<0.119。因此,即使考虑到槽深度和显影剂比重的偏差,但是即使在将M/S设定为处于(30±15)mg/cm2的范围内的值且间隙SB增宽至300μm或更宽的情况下也能够满足不等式6。因此,可以说将M/S设定为0.15mg/mm2更为理想。基于测试第六和第七实施例的实验结果,槽比率α理想地不小于0.04。如果槽比率α不大于0.04,也就是说如果槽比率α过小,则显影套筒的显影剂运送性能不足,这就相应地使得显影套筒上的显影剂涂层不稳定。关于槽比率α的最小值,槽比率α理想的不小于0.06,优选地不小于0.08,目的是为了确保显影套筒的显影剂运送性能令人满意。此外,本发明的上述实施例中的显影套筒设置有V形槽。然而,如上所述,这些实施例并不是为了在槽的形状这方面限制本发明。即,本发明能够跟显影装置的显影套筒的槽形状无关地与如上所述构造的显影装置兼容。例如,只要显影装置被如上所述地构造,则本发明就与多种显影装置兼容,所述显影装置的显影套筒的横截面形状为字母U形、矩形或复杂的形状。然而,在显影套筒的槽比率α相对较低的情况下,存在难以形成横截面为U形或矩形的槽的问题。此外,参照显影装置所用的显影套筒的数量仅设置为一个的情况介绍了本发明的前述实施例。然而,本发明还可以应用于设置有两个或更多个显影套筒(例如,显影套筒28和31,磁辊29和32分别定位在显影套筒28和31中,如图10所示)的显影装置。即,与针对显影装置仅具有一个显影套筒的情况相类似的说明内容也可以应用于例如图10中示出的显影装置,至少可以应用于其显影套筒28,管控刮板就定位在所述显影套筒28的外周表面附近。(实施例2)在本发明的第一实施例中,磁性载体是由纯铁氧体制成的载体。然而,即使满足不等式6的程度与常规的磁性载体相同,由于以下的原因,与常规的铁氧体载体相比,使用树脂比率更大而磁化量更小的树脂性的磁性载体也能够使得显影装置输出在涉及粒状性方面的性质更加优越的图像。也就是说,如果磁性载体的磁化量较小,则相邻的两个磁刷之间的磁相互作用力(排斥力)较小。因此,由磁性载体在显影套筒的外周表面上形成的磁刷更短且密度更高,从而允许显影装置输出纹理均匀且分辨率更高的图像。磁刷长度约等于表观厚度(=M/S(mg/mm2)/比重G(mg/mm3)),这已在第一实施例的说明内容中提及。然而,实际上,两者之间存在因显影剂密度引起的少量差异,这是因为由密度较高的显影剂形成的磁刷的表观长度(高度)可能会大于由密度较低的显影剂形成的磁刷的表观长度(高度)。因此,前者不如后者,原因在于前者比后者更易于导致形成不理想的粒状图像。更具体地,在使用密度更小的显影剂的情况下,由显影剂形成的磁刷更短,即表观长度(高度)更小,且密度更高。因此,能够形成分辨率更高且粒状性更小的图像。因此,在本实施例中,通过将磁性金属氧化物(例如磁铁矿)和非磁性金属氧化物(例如赤铁矿)散布在粘合树脂中形成的树脂性的磁性载体被用作用于显影剂的载体。更具体地,在本实施例中,使用的树脂性的磁性载体的最大磁化量为大约190emu/cm3,因此,该值小于铁氧体颗粒的最大磁化量(280emu/cm3)。这种树脂性的磁性载体的比重G是4.0mg/mm3,该值小于第一实施例中的磁性载体的比重G。在本实施例中使用的调色剂与在第一实施例中使用的调色剂相同。此外,调色剂和树脂性的磁性载体之间的重量比与第一实施例中的调色剂和常规磁性载体之间的重量比相同且为1:9。因此,根据公式5能够获得本实施例中的显影剂的比重G为3.08(G=3.08)。利用与在表1中用于第一实施例的显影套筒相同的显影套筒来研究这种载体。实施例10:在使用第一实施例中的槽比率α为0.080的显影套筒的情况下,能够将间隙SB设定为0.50mm。通过用0.50代入公式4中的SB获得的值为13.6,该值小于显影剂数量M/S的理想值(30)的一半。因此,满足不等式6。也就是说,与槽部分相比,无槽部分更加有助于运送显影剂通过管控刮板30。可以认为这就是为何能够将间隙SB设定为大约0.50mm的原因所在。此外,就关于粒状性的图像质量而言,本实施例中的树脂性的磁性载体优于第一实施例中的仅由铁氧体颗粒形成的常规磁性载体。本实施例并非是要在就磁性载体的选择方面限制本发明。即,本发明不仅与本实施例中的通过将磁性和非磁性金属氧化物散布在粘合树脂中形成的非树脂性的磁性载体相兼容,而且还与通过将树脂分散在多孔的载体颗粒之间的间隙中以使得树脂比率更高的这种树脂性的磁性载体相兼容。为了使得本发明尽可能的有效,载体的磁化量理想地不小于210emu/cm3。关于计算磁化量所用的方法,利用振荡磁场类型的自动磁性性质记录设备(RikenInstrumentation有限公司的产品)来获得载体的磁性性质。更具体地,测量封装在圆筒形容器中并置于外部磁场中的构成1KOe(kiloelsted)的载体的磁化强度。然后,将获得的载体的磁化强度乘以载体的真实比重以计算载体的磁化量(emu/cm3)。根据本发明,在使用了显影剂承载构件的显影装置中,能够提供这样的显影装置,所述显影剂承载构件的外周表面设置有槽并且构造成在所述显影剂承载构件的外周表面上形成足够薄的显影剂层,以得到非常高质量的图像,所述显影装置抑制产生由于显影剂承载构件的显影剂运送性能的过度或不充分而使得显影剂令人不满意地涂布在显影剂承载构件上和/或异物堵塞在显影装置的显影剂承载构件的外周表面和显影装置的显影剂管控构件之间的间隙中这样的问题。尽管已经参照在此公开的结构介绍了本发明,但是本发明并不局限于所阐述的细节,并且本申请旨在涵盖能够落在改进目的或所附权利要求的保护范围内的这些变型或修改。【工业应用性】本发明提供了一种显影装置,所述显影装置抑制由于显影剂承载构件的显影剂运送性能的过度或不充分而使得显影剂令人不满意地涂布在显影剂承载构件上和/或异物堵塞在显影装置的显影剂承载构件的外周表面和显影装置的显影剂管控构件之间的间隙中这样的问题。当前第1页1 2 3