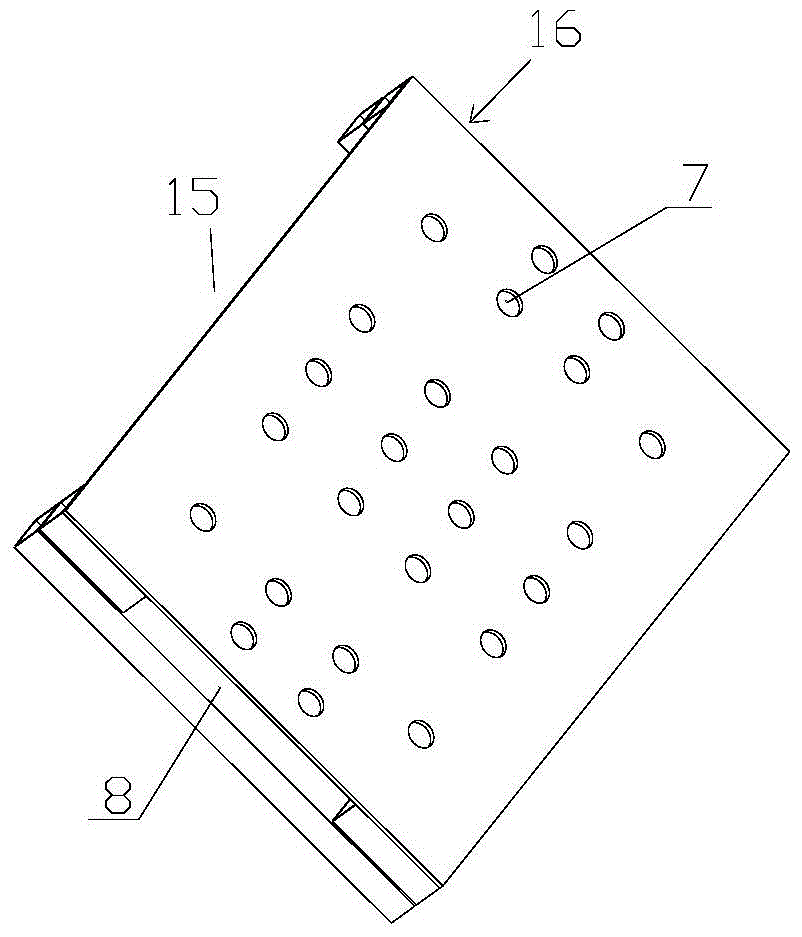
本发明涉及一种用于3D打印砂芯的托盘、以及转运3D打印砂芯的方法。
背景技术:平托盘是一种铸造车间里常用的一种工装,常被用来放置、盛放、转运砂芯或者其他物品。通常采用木质、塑料、碳素钢材质。3D打印技术被应用于铸造领域,由于其无模铸造的特性,通常会被选定用来生产多品种、小批量的产品,另外,由于基于3DP技术的3D打印机打印出来的砂芯无芯铁、无芯鼻,而且在清砂前、流涂后需要用热风烘干,所以3D打印砂芯只能使用托盘转运。对于3D打印整个铸造工艺流程主要包括:3D打印、取芯、转运、预表干、清砂、流涂、烘干、组芯、芯包转运、造型填背砂、浇注等工序。可见整个流程比较长,根据物流行业的经验“搬运作业的重大原则就是作业量最少原则,即当货物移动时尽量减少“二次搬运”和“临时停放”,使搬运次数尽可能减少。"为了提高转运效率,技术人员、操作者当然希望尽可能地减少转载作业,所以要设计一种能兼顾整个3DP铸造工艺流程的托盘,在浇注前的流程中砂芯不需要下托盘。现有技术中,申请号为201410436654.9的中国专利,公开了一种喷墨3D打印设备及打印方法。但是其没有涉及如何兼顾整个3DP铸造工艺流程的托盘的任何技术手段。
技术实现要素:为了克服现有技术中普通托盘转运3D打印砂芯实现预表干、水基涂料流涂烘干、组芯、芯包转运等工艺流程,需要不断倒换不同型号(材质)的托盘或者其他工装,效率低下的问题,本发明的目的在于提供一种用于3D打印砂芯的托盘,以能够兼顾3D打印砂芯的取芯、转运、预表干、清砂、流涂、烘干、组芯、芯包转运、造型填背砂的全流程;还提供一种转运3D打印砂芯的方法,以消除现有技术转运3D打印砂芯方法需要在上述全流程需要更换托盘的缺陷。为实现上述目的,根据本发明第一方面,本发明提供一种用于3D打印砂芯的托盘,托盘为钢制件,并且具有由面板、以及在所述面板的同一侧相对布置的第一侧部和第二侧部形成的凹槽结构,其中,所述面板的与所述第一侧部和第二侧部相反的一侧为平整面,且在所述面板上形成有贯通所述面板的多个通孔,其中,沿着从所述第一侧部指向第二侧部的方向,形成有贯通所述第一侧部和第二侧部的贯通口。优选地,所述面板的所述平整面的平整度为2mm。优选地,所述第一侧部和第二侧部均为双层结构,每个所述双层结构由固定于所述面板的第一层支脚、及固定于所述第一层支脚上的第二层支脚构成,其中,每个第一层支脚由间隔开的第一支脚和第二支脚构成,每个第二层支脚为覆盖所述间隔的单个支脚,其中,所有第二层支脚的底面处于同一平面并且与所述面板的平整面相互平行,由所述第二层支脚覆盖的所述间隔构成所述贯通口,其中,相对布置的所述第一侧部和第二侧部之间间隔所形成的空挡,作为液压叉车和柴油叉车的操作空间。优选地,所述面板为钢制长方形平板,每个所述第一层支脚、以及每个所述第二层支脚均为方形钢管,每个方形钢管平行于所述长方形平板的宽度方向,在所述面板的与所述平整面相反的一侧固定有钢制加强筋,所述面板上的所述多个通孔与所述加强筋相互错开,其中,每个所述加强筋相对于所述平整面的最大高度,小于所述第一层支脚与第二层支脚的相接面相对于所述平整面的高度。优选地,每个所述方形钢管为80mmx80mm的方形钢管,每个加强筋的厚度为25mm,所述面板的厚度为10mm。优选地,所述第一侧部和第二侧部之间的所述空档为90-120mm。优选地,所述第一层支脚中的第一支脚和第二支脚、及所述加强筋都焊接在所述面板的与所述平整面相反的一侧上,所述第二层支脚焊在所述第一支脚和第二支脚的底面上,所述多个通孔均为冲孔。优选地,托盘的长度为1000-1200mm,宽度为800-1000mm。优选地,托盘的材质为Q235钢。根据本发明第二方面,本发明提供一种转运3D打印砂芯的方法,该方法包括:在3D打印铸造的取芯、转运、预表干、清砂、流涂、烘干、组芯、芯包转运直至造型填背砂的整个工序(或者称之为整个流程)中转运3D打印砂芯,在所述整个工序中,始终采用本发明前述第一方面所述的任意一种托盘转运3D打印砂芯而不更换托盘。本发明的有益效果至少在于以下(1)-(2),更详细的效果在具体实施方式描述:(1)本发明托盘能够兼顾3D打印砂芯的取芯、转运、预表干、清砂、流涂、烘干、组芯、芯包转运、造型填背砂的全流程,而不用更换托盘。(2)消除了现有技术转运3D打印砂芯方法需要在上述全流程需要更换托盘的缺陷。附图说明图1是本发明用于3D打印砂芯的托盘的一个示例的一个等轴测视图;图2是图1所示托盘的另一个等轴测视图;图3是图1所示托盘的俯视图;图4是图1所示托盘的主视图。在图中,各部分的编号如下:1-面板,2-宽度方向加强筋,3-长度方向加强筋,4-第二层支脚,5-三角加强筋,6-第一层支脚,7-通孔,8-贯通口,10-第一侧部,11-第二侧部,12-第一支脚,13-第二支脚。具体实施方式以下参见附图描述本发明的具体实施方式。具体地,参见图1和2所示的本发明的用于3D打印砂芯的托盘的一个示例,因为3D打印砂芯在清砂前要进行预表干,需要用130-150℃的烘干温度保温20-30min,塑料托盘、木质托盘因为是易燃物,有变形甚至着火风险,不适用于3D打印铸造工艺流程。另外,因为组芯后芯包最重可达到1.5-2T,塑料托盘、木质托盘有效载荷较低,易变形,不能满足组芯、芯包转运的需要,故本发明的用于3D打印砂芯的托盘为钢制件。优选地,本发明的托盘的材质选择Q235钢。根据使用环境,本发明的托盘16需同时通用柴油叉车、液压叉车,所以本发明托盘16设计为双向进叉的单面托盘。具体而言,如图1所示,本发明托盘16整体呈凹槽结构。面板1、以及在面板1的同一侧相对布置的第一侧部10和第二侧部11一起构成所述凹槽结构。由于所述凹槽结构,显然第一侧部10和第二侧部11之间的间隔可以形成空挡15(参见图4),该空挡15优选为90mm-120mm,该空挡15可以用作液压叉车和柴油叉车的操作空间。从而,此时托盘16构造为前述的双向进叉的单面托盘。3D打印砂芯需要在箱式烘干窑里进行预表干、烘干,所以本发明的托盘16上设有良好的热风通道进行通风。具体而言,从图1可看出,沿着从第一侧部10指向第二侧部11的方向,托盘16形成有贯通第一侧部10和第二侧部11的贯通口8,该贯通口8可以用作热风通道。另外,清砂过程中、流涂后烘干时要能将砂子、多余的涂料及时排走,所以要留有足够数量、面积的漏砂或涂料的孔。为此,如图2和3所示,本发明托盘16在面板1上设有贯通面板1的多个通孔7,该多个通孔7可以用作前述的漏砂或涂料的孔。通孔7可为两个以上,具体数量可以调整。考虑到还要在托盘16上面进行组芯,所以托盘16的顶面要求较高的平整度。为此,面板1的与第一侧部10和第二侧部11相反的一侧为平整面(即,托盘16的顶面),优选地,该平整面的平整度为2mm。考虑配套3D打印机(1800mm*1000mm)打印尺寸、箱式烘干窑、造型使用的砂箱尺寸(1000mm*800mm或者1200mm*900mm),本发明的托盘16尺寸可以优选为长1000mm-1200mm,宽800mm-1000mm,从而可以满足所有的3D打印砂芯、芯包转运的需要。参见图1、图2、图4,对于托盘16呈凹槽结构的情形而言,凹槽结构的第一侧部10和第二侧部11均构造为双层结构。每个双层结构由固定于面板1的第一层支脚6、及固定于第一层支脚6上的第二层支脚4构成。例如,对于第一侧部10中的第一层支脚6由相互间隔开的第一支脚12和第二支脚13构成,第一侧部10中的第二层支脚4为单个支脚并覆盖第一支脚12与第二支脚13之间的间隔。对于第二侧部11而言,其与第一侧部10具有相同的情形,所以不再赘述。在第一侧部10中,第一支脚12和第二支脚13之间的间隔由第二层支脚4覆盖;在第二侧部11中,同样地,第一支脚12和第二支脚13之间的间隔由第二层支脚4覆盖;这两个由第二层支脚4覆盖的间隔构成了:前述的用作热风通道的贯通口8的一个实施例。作为一个示例,以下结合附图1-4描述本发明托盘的具体连接方式、以及制造过程:本发明的托盘16共涉及三种型材:80方钢(80mmx80mm)、25mm厚钢板、10mm厚钢板;按照图纸要求将80方钢、25mm、10mm钢板切成合适尺寸,其中10mm钢板需要按照图纸上要求的数量、尺寸冲孔(形成图1中通孔7),作为漏砂通道和热风通道。在平整的工作台或者地面上将冲完孔的10mm钢板作为焊接基准找平,平面度控制在2mm以内以形成面板1。按照从上到下的顺序焊接托盘工作面1、宽度方向加强筋2、长度方向加强筋3、三角加强筋5、第一层支脚6和第二层支脚4,要求焊接时满焊,焊接后去除焊渣,焊接后不能有应力变形。换而言之,第一层支脚6的第一支脚12和第二支脚13、以及加强筋2、3、5都焊接在面板1的与其平整面相反的一侧上,第二层支脚4焊接在第一支脚12和第二支脚13的底面上。面板1是由10mm钢板制成的长方形平板,其上设置有用于漏砂或涂料的通孔7,所述平板的宽度方向上对称设置有贯通口8(根据其用途可以称为热风口),第一层支脚6的第一和第二支脚12和13间隔开形成长方形通道,该长方形通道的底面由第二层支脚4覆盖以形成所述贯通口8;长度方向加强筋3是由25mm钢板制成;宽度方向加强筋2是由25mm钢板制成;第二层支脚4是由80方钢制成,共计两段,其中一段为第一侧部10的构件,而另一段为第二侧部11的构件;三角加强筋5由25mm钢板制成,共计四块;每个第一层支脚4由间隔开的第一支脚12(由80方钢制成)和第二支脚13(由80方钢制成)形成,所有第一支脚12连同所有第二支脚13总共4段。另外,从图1中可以看出,每个方钢(方形钢管)平行于长方形平板的宽度方向。以上80方钢、25mm厚钢板、10mm厚钢板仅是示例,本发明不局限于此,具体尺寸可以变化。例如,第一层支脚和第二层支脚不局限于上述方钢,而可以是其他形状的热轧型材。从图1还可以看出,面板1上的所述多个通孔7与加强筋2、3、5相互错开,每个加强筋2、3、5相对于面板1平整面的最大高度小于第一层支脚6与第二层支脚4的相接面相对于所述平整面的高度。本发明托盘16从3D打印机取芯时开始投入,柴油叉车、液压叉车可以沿长度方向的空档15插入,升起托盘16及托盘16上的砂芯,经过取芯、转运、预表干、清砂、流涂、烘干、组芯、芯包转运至造型填背砂工序回收,再次投入3D打印机取芯工序。预表干、流涂后的烘干工序,热风能够从托盘16宽度方向两侧的设置的热风口(图2处贯通口8)处吹入,经过漏砂孔(图2中通孔7)往上吹,从而使烘干热风无法直接吹到的砂芯下底面,此时可以理解,通孔7连同贯通口8都可以用作热风通道。组芯时将托盘16放在平整的地面上,第二层支脚4下只要没有异物即可保证整个托盘水平,组芯时无需再专门校平基准。为此,本发明中托盘的所有第二层支脚4的底面处于同一平面并且与所述面板1的平整面相互平行。清砂过程中、流涂后,将砂子、多余的涂料及时从漏砂孔(见图2中通孔7)中排走,即要及时清理漏砂孔中的杂物。本发明的托盘16能够兼顾3D打印砂芯的取芯、转运、预表干、清砂、流涂、烘干、组芯、芯包转运、造型填背砂的全流程,在清砂前预表干、流涂后烘干、组芯、转运芯包等3D打印铸造关键工艺流程中减少转载、二次搬运、临时停放等不必要的动作提高生产效率40%以上,可以稳定控制现场在制在3天以内。综上所述,本发明通过将托盘设置为双向进叉的单面托盘,提高了托盘的通用性,可适用于柴油叉车、液压叉车的各类叉车。通过在托盘的面板上设置了可以用作漏砂孔的通孔,不仅方便了清砂和流涂,也更有利于砂芯的干燥。通过专门设置的可以用作热风口的贯通口,使得更多的热风能够进入砂芯内部,加速砂芯的烘干,提高生产效率。整个托盘结构设置为钢制结构,一方面保证了托盘的刚度,从而保证了砂型不会变形,因为3D打印出来的砂芯是尚未完全硬化的,需要加热来进一步硬化;另一方面,提高了托盘的重复利用率,降低了生产成本。焊接时要求满焊,不能有应力变形,是为了保证所述托盘的刚度及工作面的平整性。另一方面,本发明还提供一种转运3D打印砂芯的方法,包括:在3D打印铸造的取芯、转运、预表干、清砂、流涂、烘干、组芯、芯包转运直至造型填背砂的整个工序(可以称为全流程)中转运3D打印砂芯,在所述整个工序中,始终采用本发明托盘16而不更换托盘。从而消除了现有技术转运3D打印`砂芯方法需要在上述全流程过程中需要更换托盘的缺陷。本发明转运3D打印砂芯的方法由于在上述全流程中不需要更换托盘,所以减少转载、二次搬运、临时停放等不必要的动作提高生产效率约40%以上,可以稳定控制现场在制在约3天以内。