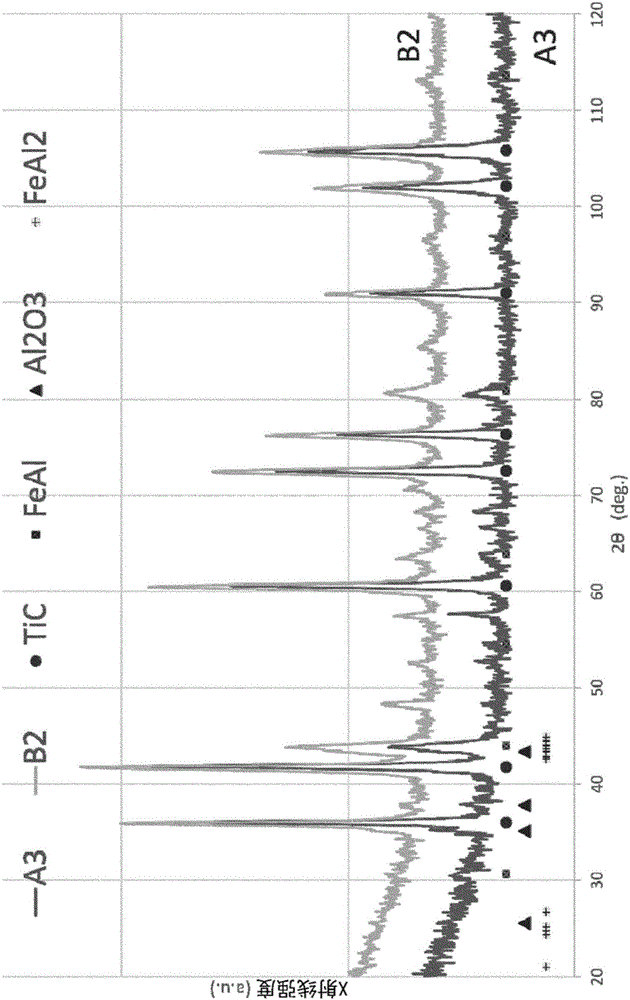
本发明涉及最适于不重磨刀片等切削工具、耐磨用工具、耐腐蚀性部件以及高温用构件等的硬质烧结材料。具体而言,涉及通过使微细的氧化铝均匀地分散在不含有稀有金属的金属结合相内来提高高温耐氧化性、硬度等的便宜的硬质烧结体及其制造方法。
背景技术:
:以往,作为切削工具、模具和耐热耐磨部件等要求耐磨性、强度和耐热性的材料,广泛采用使用钴、镍等对碳化钨粉末进行烧结而成的超硬合金(WC-Co合金等)。如果在大气中600℃以上的高温状态下使用该超硬合金,则氧化急速地进行,因此,该超硬合金必须在低于该温度的温度条件下使用。然而,由于加工技术的进步,逐渐需要在高温状态下进行切削加工、模具加工,因此,寻求一种能够在更高的温度条件下使用的硬质材料。另一方面,由于作为碳化钨原料的钨矿山不均匀地分布在一部分地域,所以钨是担负国家风险的稀有金属。因此,采用使用钴、镍等对碳化钛粉末、碳氮化钛粉末进行烧结而成的金属陶瓷代替碳化钨。金属陶瓷的硬度比超硬合金高,耐氧化性优异。然而,钴、镍也是由资源枯竭的担忧的稀有金属。另外,对于钴而言,其被指定为污染物释放与转移登记(PollutantReleaseandTransferRegister,PRTR)法的第一种指定化学物质、劳动安全卫生法的特定化学物质的第二类物质,从成本、环境融合的观点出发,尽量不要使用。根据以上情况,希望开发一种稳定供给资源、不含有稀有金属的便宜的工具用材料。作为稀有金属的对策之一,已知具有由Fe和Al中的一种或两种构成的结合相的超硬合金代替钴(例如,专利文献1)。如果将硬质相中具有碳化钛(TiC)、碳氮化钛(TiCN)的金属陶瓷的结合相由钴、镍置换成铁铝等金属间化合物,则成为不含有稀有金属的硬质材料。在使铁铝形成结合相的复合材料的制备方法中,将Fe、Al和硬质粒子混合,在烧结时存在使Fe和Al反应而生成FeAl的情况,但由于结晶粒难以微细化,所以难以提高抗弯强度(例如,专利文献1、2)。另外,在将通过燃烧合成等将Fe和Al预先合成并粉碎而成的FeAl粉末(プリアロイ)、硬质粒子与添加物一同混合粉碎后进行烧结而成的复合材料的制备方法(例如,专利文献3)中,通过延长混合粉碎时间提高复合材料的硬度。然而,如果延长混合粉碎时间,则在结晶粒微细化进行的同时,混合粉末的氧化也在进行。其结果是,硬度等材料特性提高,但由于在烧结时已氧化了的FeAl混合粉末暴露在高温中,所以存在吸附在FeAl和混合粉末表面的氧通过下述化学反应式(1)所示的反应分离成Fe和Al2O3,耐氧化性降低的问题。4FeAl+3O2→4Fe+2Al2O3(1)另外,在由硬质粒子形成预制体,熔渗FeAl而成的复合材料的制备方法中,存在复合材料难以致密化、复合材料的硬度、抗弯强度降低的问题。现有技术文献专利文献专利文献1:日本专利第2611177号公报;专利文献2:日本特表平10-511071号公报;专利文献3:日本特表2002-501983号公报。技术实现要素:发明所要解决的问题本发明是鉴于上述情况而完成的,其课题在于,提供一种不使用稀有金属、具有能够作为工具使用的抗弯强度、高温耐氧化性优异、在高温条件下的硬度高且便宜的硬质烧结体及其制造方法。解决问题的技术方案为了实现上述课题,本发明由以下技术方案构成。本发明的硬质烧结体,含有8.8~34.4mol%的结合相,剩余部分由硬质相和不可避免的杂质所构成,结合相含有以FeAl为主要成分的铁铝以及分散在铁铝中的粒径为1μm以下的氧化铝,硬质相由选自周期表的第四族金属、第五族金属和第六族金属的碳化物、氮化物、碳氮化物、硼化物以及这些物质的固溶体中的至少一种构成。本发明的硬质烧结体的制造方法具有:将含有由选自FeAl2、Fe2Al5和FeAl3中的至少一种构成的铁铝粉末的结合粒子粉末、以及由选自周期表的第四族金属、第五族金属和第六族金属的碳化物、氮化物、碳氮化物和硼化物中的至少一种构成的硬质粒子粉末混合并粉碎,得到混合粉末的混合粉碎工序;以及对混合粉末进行烧结的烧结工序。本发明的切削用或耐磨用工具将本发明的硬质烧结体作为原料。发明效果根据本发明,能够得到高温耐氧化性优异、在高温条件下的硬度高的便宜的硬质烧结体。附图说明图1是实施例A3的硬质烧结体的高温氧化试验后的剖面观察和各元素的能量分散型X射线分光测定的分析结果。图2是实施例A3的硬质烧结体和比较例B2的硬质烧结体的X射线衍射图案。图3是通过扫描电子显微镜观察实施例A2的硬质烧结体的图像。图4是通过扫描电子显微镜观察实施例A3的硬质烧结体的图像。图5是通过扫描电子显微镜观察实施例A4的硬质烧结体的图像。图6是通过扫描电子显微镜观察实施例A5的硬质烧结体的图像。图7是通过扫描电子显微镜观察实施例A10的硬质烧结体的图像。图8是通过扫描电子显微镜观察比较例B2的硬质烧结体的图像。图9是表示实施例A1~A3、A10、A17和A20的硬质烧结体和比较例B1和B3的硬质烧结体的400~800℃高温硬度试验结果的图表。具体实施方式下面,一边参照表和附图一边基于实施方式和实施例对本发明的硬质烧结体、该硬质烧结体的制造方法以及以该硬质烧结体为原材料的工具进行详细地说明。需要说明的是,适当地省略重复说明。另外,在两个数值之间记作“~”来表示数值范围的情况下,设为这两个数值也被包含在数值范围中。本发明的实施方式的硬质烧结体由结合相、硬质相和不可避免的杂质所构成。优选硬质烧结体中的结合相的含量为2.4~53mol%。通过设为该含量,可得到取得抗弯强度、高温耐氧化性、硬度和断裂韧性的平衡的硬质烧结体。如果硬质烧结体中结合相的含量小于2.4mol%,则虽然硬度高,但抗弯强度和高温耐氧化性差。如果硬质烧结体中结合相的含量大于53mol%,则硬度差。结合相含有铁铝和氧化铝。铁铝以FeAl为主要成分。氧化铝的粒径为1μm以下,分散在该铁铝中。硬质相由选自周期表的第四族金属、第五族金属和第六族金属的碳化物、氮化物、碳氮化物、硼化物以及这些物质的固溶体中的至少一种构成。周期表的第四族金属为Ti、Zr、Hf,第五族元素为V、Nb、Ta,第六族元素为Cr、Mo、W。其中,优选硬质相由选自Ti的碳化物、氮化物、碳氮化物、硼化物以及这些物质的固溶体中的至少一种或碳化钨及其固溶体中的至少一种构成。根据本实施方式的硬质烧结体的组成,出于提高高温特性、硬度等的目的,在结合相中可以含有选自硼、硅、铬、铌和钼中的至少一种(以下,有时称为“添加物”)。通过使结合相含有添加物,提高烧结性,能够期待致密化、高温蠕变特性的提高、抗氧化特性的提高。优选硬质烧结体中添加物的含量大于0mol%且为25mol%以下。这是因为如果硬质烧结体中的添加物的含量过多,则成为抑制烧结的主要原因,硬质烧结体的各种特性降低。更优选硬质烧结体中的结合相的含量为8.8~34.4mol%。通过设为该含量,可得到高硬度且断裂韧性、抗弯强度和高温耐氧化性优异的硬质烧结体。如果硬质烧结体中的结合相的含量少,则虽然硬度高,但抗弯强度和高温耐氧化性差。如果硬质烧结体中的结合相的含量过多,则硬度差。而且,优选结合相中的氧化铝的含量为24.2~50.0mol%。这是因为如果结合相中的氧化铝的含量少,则硬质烧结体的耐热性降低。如果结合相中的氧化铝的含量过多,则难以得到致密的硬质烧结体。另外,优选结合相中的铁铝的铝含量为24.6~57.7。如果铝含量比上述范围多,则断裂韧性值降低,如果铝含量比上述范围少,则高温耐氧化性降低。本发明的硬质烧结体的制造方法具有混合粉碎工序和烧结工序。在混合粉碎工序中,将结合粒子粉末和硬质粒子粉末混合并粉碎,得到混合粉末。其中,结合粒子粉末是由铁和相对于铁过量存在的铝构成的铁铝粉末,含有由选自例如FeAl2、Fe2Al5和FeAl3中的至少一种构成的铁铝粉末。该铁铝粉末为结合相用材料。硬质粒子粉末由选自周期表的第四族金属、第五族金属和第六族金属的碳化物、氮化物、碳氮化物、硼化物中的至少一种粉末构成。其中,优选硬质粒子粉末由选自Ti的碳化物、氮化物、碳氮化物和硼化物中的至少一种或碳化钨粉末构成。在烧结工序中,对混合粉碎工序中得到的混合粉末进行烧结。经由混合粉碎工序和烧结工序,从而得到具有包含以Fe3Al或FeAl为主要成分的铁铝和分散在该铁铝中的粒径为1μm以下的氧化铝的结合相的硬质烧结体。通过使结合相含有稳固的Fe3Al或FeAl为主要成分,硬质烧结体成为不使用稀有金属、具有能够作为工具使用的抗弯强度、优异的高温耐氧化性和高温硬度的便宜的硬质材料。由于本实施方式的硬质烧结体由结合相和硬质相构成,所以为了提高机械特性等,期望将结合相和硬质相的原料粉末均匀地混合。另外,由于硬质相和结合相的结晶微细化对提高硬度等有效,所以优选采用干式法或湿式法进行混合粉碎,得到原料粉末。通过混合粉碎工序中的微细化,各结合相和硬质相的原料粉末产生新表面,氧气分子等附着在该新表面上。因此,如果已进行微细粉碎的混合粉末暴露在大气中,则该混合粉末一定会被氧化,只是存在氧化程度的不同。在本实施方式中,作为结合相用材料的铁铝粉末,使用选自FeAl2、Fe2Al5和FeAl3中的至少一种代替现有的Fe3Al或FeAl。在烧结时,吸附于通过混合粉碎已进行微细化的混合粉末的氧和相对于铁铝中的铁过量存在的铝在高温条件下发生下述化学反应式(2)~(4)所示的反应,形成氧化铝和以稳固的FeAl的铁铝为主要成分的结合相。该氧化铝形成微细结晶粒,分散并存在于结合相中。4FeAl2+3O2→4FeAl+2Al2O3(2)4Fe2Al5+9O2→8FeAl2+2Al2O3+6O2→8FeAl+6Al2O3(3)4FeAl3+6O2→4FeAl2+2Al2O3+3O2→4FeAl+4Al2O3(4)为了分散并混合亚微米级粉末,需要长时间的混合,需要添加分散剂等。然而,作为本实施方式的硬质烧结体,与现有的超硬合金、金属陶瓷同样地对作为结合相用材料的铁铝粉末和硬质相用材料粉末进行混合、成型、烧结,从而能够制造。作为结合相材料的结合粒子粉末和硬质相材料的硬质粒子粉末的混合方法,无论干式法或湿式法均可。另外,对结合粒子粉末和硬质粒子粉末的粉碎方法没有特别的限制。在本实施方式中,由于必须控制混合粉末的含氧量,因此,通过实验等预先求出混合粉碎时间与得到的混合粉末中含有的氧量的关系,进行粉碎混合直至形成含有规定氧量的目标混合粉末。在混合粉碎工序中,当通过滚动式球磨机、行星式球磨机或立式球磨机等湿式混合粉碎机制备含有规定氧量的混合粉末时,可以使用有机溶剂对结合粒子粉末和硬质粒子粉末进行湿式混合粉碎,得到混合粉末。另外,当通过滚动式球磨机、行星式球磨机或立式球磨机等干式混合粉碎机制备含有规定氧量的混合粉末时,在真空研磨容器内或用氩气或氮气置换的研磨容器内,对结合粒子粉末和硬质粒子粉末进行干式混合粉碎后,暴露在大气中,从而也能够得到混合粉末。在本实施方式中,将对结合粒子粉末和硬质粒子粉末进行混合粉碎而得到的含有规定氧量的混合粉末填充在模具中,进行加压成型后,进行烧结,制造硬质烧结体。烧结优选在真空环境、氩气环境、氮气环境或氢气环境下进行。代替该方法,可以将对结合粒子粉末和硬质粒子粉末进行混合粉碎而得到的含有规定氧量的混合粉末填充到加压通电烧结装置用模型中,对模型进行加压,同时,通过通电加热在真空环境、氩气环境、氮气环境或氢气环境下进行烧结。进一步地,根据需要,也可以对得到的这些烧结体进行热等静压(HotIsostaticPressing,HIP)处理。如此制造的本实施方式的硬质烧结体的结合相是分散有微细氧化铝的稳固的FeAl相。因此,在高温氧化环境中,硬质烧结体的FeAl相接触大气的表面重新被氧化,在硬质烧结体表面形成氧化铝膜。该氧化铝膜覆盖硬质烧结体的表面,防止氧向硬质烧结体的内部扩散。因此,本实施方式的硬质烧结体表现出非常优异的高温耐氧化性。另外,由于氧化铝也有助于提高硬度,所以本实施方式的硬质烧结体在高温条件下的硬度高。实施例下面,基于实施例具体地说明本发明,但本发明并不受以下实施例的任何限定。首先,将市售的平均粒径为1.7μm的TiC粉末(日本新金属株式会社制)、平均粒径为1.4μm的TiCN粉末(日本新金属株式会社制,TiC07N03)、平均粒径为0.73μm的WC粉末(日本新金属株式会社制)、平均粒径为0.92μm的WC粉末(日本联合材料株式会社(アライドマテリアル社)制)、平均粒径为1.3μm的TiN粉末(日本新金属株式会社制)、平均粒径为10μm的FeAl粉末(日本共立材料株式会社(協立マテリアル社)制(Fe:40mol%;Al:60mol%))、粒径为300μm以下的铁铝粉末(正荣商会株式会社制(Fe:33mol%;Al:67mol%))、粒径为3~5μm的Fe粉末(高纯度化学研究所株式会社制)、平均粒径为5.5μm的Ni粉末(高纯度化学研究所株式会社制)、平均粒径为0.3μm的α-Al2O3粉末(高纯度化学研究所株式会社制)、平均粒径为1.8μm的Mo2C粉末(高纯度化学研究所株式会社制)、粒径为63~90μm的Cr粉末(高纯度化学研究所株式会社制)、平均粒径为63μm的FeB粉末(新日本电工株式会社制)、平均粒径位45μm的B粉末(高纯度化学研究所株式会社制)作为原料,按照表1所示的配合组成将各原料粉末进行混合。A1~A23为本发明的实施例,B1~B3为比较例。表1然后,通过滚动式球磨机对A1~A23、B1和B3的混合粉末进行以丙酮为溶剂的湿式混合粉碎。对于湿式混合粉碎而言,在A5和A14的情况下,进行120小时,在A17和A21的情况下,进行108小时,在B1的情况下,进行48小时,在其他情况下,进行72小时。在B2的情况下,进行1小时的干式混合粉碎。并且,在湿式混合粉碎的情况下,对粉末进行干燥,得到混合粉末,在干式混合粉碎物的情况下,直接得到混合粉末。然后,将得到的A1~A23、B2和B3的混合粉末分别填充到石墨模型中。将填充有粉末的石墨模型置于电脉冲烧结炉内,对石墨模型施加40MPa的压力,同时,在大致1150℃至1300℃的温度条件下保持10分钟至20分钟,进行烧结。另外,对于B1的混合粉末而言,将混合粉末填充到模具中,用手压机对模具施加100MPa的压力,从而进行压制成型,然后使用真空烧结炉在1415℃的温度条件下烧结2小时。并且,对得到的硬质烧结体的平面进行磨削后,研磨至表面成为镜面,分别测定密度、维氏硬度(HV30)、断裂韧性、抗弯强度。将测定结果示于表2。另外,通过根据JISZ2244的方法测定维式硬度,基于下述Shetty式算出断裂韧性。其中,Hv为维氏硬度(GPa),P为压入载荷(N),C为平均裂纹长度(μm)。表2然后,在大气中、800℃的条件下对A2~A4、A7、A9~A13、A15和B1~B3的硬质烧结体进行高温抗氧化试验。每经过一定时间将样品冷却至室温,进行重量测定,再升温到800℃。将累计氧化增量(单位:g/m2)示于表3。表3单位:g/m2样品4小时后8小时后12小时后16小时后24小时后48小时后72小时后A22.553.634.314.775.526.977.99A32.192.722.893.233.594.294.76A42.423.494.044.414.805.746.18A74.385.926.847.308.8411.4113.66A94.085.305.976.326.988.219.06A101.912.572.632.823.063.684.00A114.995.405.726.257.6013.1216.30A128.4911.8413.9615.8818.9625.2230.16A134.557.739.8211.7614.3415.1016.64A152.925.076.667.809.7913.9918.65B14.516.287.678.8410.2813.6515.76B210.1620.1127.5235.3546.7071.1694.12B38.8412.2414.3016.0618.3023.4126.55比较例的B1(金属陶瓷)作为高温耐氧化性优异的材料而为人所知。与B1的累计氧化增量相比,A2~A4的累计氧化增量约为30~60%,A10的累计氧化增量为25.4%以下,这些样品表现出非常优异的高温耐氧化性。另外,在大气中、800℃的条件下对A10和A17进行连续72小时的抗氧化试验后,对于氧化增量(单位:g/m2)而言,A10为3.3,A17为4.0,表现出优异的耐氧化性。对高温氧化试验后的样品的剖面进行能量分散型X射线分光测定。图1是A3的硬质烧结体进行高温氧化试验后的剖面观察(扫描电子显微镜(ScanningElectronMicroscope,SEM))和各元素(Ti、Fe、Al、O)的能量分散型X射线分光测定的分析结果(表示元素分布)。图像左侧是暴露在大气的一面,根据SEM图像可知氧化导致结合相的铁铝表面形成厚度约为2μm的氧化铝膜。另外,观察Al和O的分析图像,结果由图像左侧的曲线围绕的部分的浓度高。这表示在高温氧化试验中,在A3的表面形成氧化铝膜,由此难以向内部发生氧化。另一方面,将A3的硬质烧结体和组成被调整成与A3的硬质烧结体相同的比较例的B2的硬质烧结体的高温耐氧化性作比较,结果A3的硬质烧结体更优异。于是,为了将A3和B2的各硬质烧结体作比较,通过X射线衍射对构成相进行分析,通过扫描电子显微镜(SEM)进行观察。将A3和B2的各硬质烧结体的X射线衍射图案示于图2。作为结合相的原料,在A3中,使用FeAl2,在B3中,分别使用FeAl和Al2O3,但在A3和B2两种硬质烧结体中,存在TiC、FeAl、Al2O3峰,不存在FeAl2峰。即,可知在A3和B2的构成相中含有TiC、FeAl和Al2O3,不含有FeAl2。由此,表示出通过本发明的制造硬质烧结体的方法,在A3中由FeAl2生成了FeAl和Al2O3。图3至图8是在5000倍条件下观察A2~A5、A10和B2的硬质烧结体时的SEM图像。在右下位置示出直径为1μm的圆。图中白色大小的点为Al2O3。如图4所示,在A3的硬质烧结体中每个白点的外径均为1μm以下,相对于此,如图8所示,在B2的硬质烧结体中,到处可观察到外径为1μm以上的白点。由于作为B2原料的Al2O3粉末的粒径为0.3μm,因此,认为B2的硬质烧结体在烧结工序中由Al2O3粉末凝集等导致粗大化。然后,对高温耐氧化性试验结果优异的样品测定高温条件下的硬度(单位:kgfmm-2)。通过根据JISZ2244的方法测定硬度。即,将各样品加热至800℃,接着待温度稳定后,使维氏压头接触样品表面,将压头温度加热至试样温度后,在10kgf的试验载荷下压下15秒,进行测定。测定数个点后,将温度下降100℃,与上次同样地测定硬度,重复进行直至试样温度达到400℃。将上述测定结果示于表4和图9。表4单位:kgfmm-2样品400℃500℃600℃700℃800℃A11627149212881069900A2154914081206894618A3145213371080835582A10128211401064953894A1716581439128811231010A2018001682156113661196B111061076963913808B311571003828677593在全部温度条件下,结合相少的A1的硬质烧结体、A10和A17的硬质烧结体以及以碳化钨为主要成分的A20的硬质烧结体的高温硬度均高于比较例B1的硬质烧结体(金属陶瓷)的硬度。另外,在600℃以下,A2和A3的硬质烧结体的硬度高于金属陶瓷的硬度。另外,将结合相的量相等的A3和B3的硬质烧结体的硬度作比较,结果在800℃下两者硬度相同,而在700℃以下,A3的硬质烧结体的硬度高于B3的硬质烧结体的硬度。进一步地,将结合相的量相等的A10以及A17与B3的硬质烧结体的硬度作比较,结果其硬度在全部温度下均高于B3的硬质烧结体。将根据各样品的硬质烧结体的氧量的实测值和混合粉末的配合组成算出的各样品的硬质烧结体和结合相的组成的理论计算值示于表5。使用氧氮分析装置(美国力可公司(LECO)制,TC-436)对硬质烧结体的氧量进行测定。例如,如下所述地计算A2的硬质烧结体的组成和结合相的组成。根据表5,100g的A2的硬质烧结体由95.94g混合粉末和4.06g氧构成。如果将氧的原子量设为AtmO,则100g硬质烧结体中含有的氧的物质的量MolO为,MolO=4.06/AtmO[mol]由于硬质烧结体中的氧全部是Al2O3中的氧,硬质烧结体中的Al2O3的物质的量是硬质烧结体中氧的物质的量的1/3,因此,100g硬质烧结体中含有的Al2O3的物质的量MolAl2O3为,MolAl2O3=1/3×(4.06/AtmO)[mol]另一方面,如果将TiC的式量设为AtmTiC,将FeAl2的式量设为AtmFeAl2,则根据表1,95.94g混合粉末中含有的TiC的质量即100g硬质烧结体中含有的TiC的质量为,100g硬质烧结体中的TiC的质量=95.94×0.892×AtmTiC/(0.892×AtmTiC+0.108×AtmFeAl2)[g]因此,100g硬质烧结体中含有的TiC的物质的量即MolTiC是用100g硬质烧结体中的TiC的质量除以TiC的式量AtmTiC而得到的值,因此,MolTiC=95.94×0.892/(0.892×AtmTiC+0.108×AtmFeAl2)[mol]另外,如上述化学反应式(2)所示,100g硬质烧结体中含有的FeAl的物质的量即MolFeAl与95.94g混合粉末中含有的FeAl2的物质的量即MolFeAl2相同,与计算MolTiC同样地,MolFeAl=95.94×0.108/(0.892×AtmTiC+0.108×AtmFeAl2)[mol]硬质烧结体的TiC摩尔分数、FeAl摩尔分数以及Al2O3摩尔分数分别为:硬质烧结体的TiC摩尔分数=MolTiC/(MolTiC+MolFeAl+MolAl2O3)硬质烧结体的FeAl摩尔分数=MolFeAl/(MolTiC+MolFeAl+MolAl2O3)硬质烧结体的Al2O3摩尔分数=MolAl2O3/(MolTiC+MolFeAl+MolAl2O3)。将由前述式算出的MolTiC、MolFeAl、MolAl2O3的值代入上述式,算出TiC摩尔分数、FeAl摩尔分数和Al2O3摩尔分数。另外,由于100g硬质烧结体中含有的Al2O3中的Al的物质的量即MolAl@Al2O3是100g硬质烧结体中含有的Al2O3的物质的量MolAl2O3的2倍,因此,MolAl@Al2O3=2×MolAl2O3[mol]。如果100g硬质烧结体中含有的铁铝中的Al的物质的量即100g硬质烧结体中含有的、除Al2O3中的Al以外的Al的物质的量即MolAl@FeAl使用95.94g混合粉末中含有的FeAl2中的Al的物质的量即MolAl@FeAl2,则MolAl@FeAl=2×MolAl@FeAl2-MolAl@Al2O3=2×MolAl@FeAl2-2×MolAl2O3[mol]。其中,根据MolAl@FeAl2=2×MolFeAl2[mol],将由前述式算出的MolAl2O3与混合粉末配合时的MolFeAl2的值代入上述式,算出MolAl@FeAl。而且,100g硬质烧结体中的铁铝中的Al摩尔分数即结合相中铁铝中的Al摩尔分数是100g用硬质烧结体中的铁铝中的Al的物质的量除以100g硬质烧结体中的铁铝的物质的量即95.94g混合粉末中含有的FeAl2的物质的量与100g硬质烧结体中的铁铝中的Al的物质的量之和而得的值,因此,结合相中的铁铝中的Al摩尔分数=MolAl@FeAl/(MolAl@FeAl+MolFeAl2)。将由前述式算出的MolAl@FeAl和混合粉末配合时的MolFeAl2的值代入上述式,算出结合相中的铁铝中的Al摩尔分数。另外,100g硬质烧结体中的结合相中的Al2O3的摩尔系数即结合相中的Al2O3的摩尔系数是用100g硬质烧结体中含有的Al2O3的物质的量MolAl2O3除以100g硬质烧结体中含有的铁铝的物质的量即95.94g混合粉末中含有的FeAl2的物质的量与100g硬质烧结体中含有的Al2O3的物质的量MolAl2O3之和而得到的值,因此,结合相中的Al2O3的摩尔系数=MolAl2O3/(MolFeAl2+MolAl2O3)。将由前述式算出的MolAl2O3和混合粉末配合时的MolFeAl2的值代入上述式,算出结合相中的Al2O3的摩尔分数。同样地也算出A3、A4、A10、A14和B2的硬质烧结体以及结合相的组成。另外,根据图1所示的能量分散型X射线分光测定结果和图2所示的X射线衍射图案的结果,认为实测的氧与Al结合。表5由于B2采用干式法对结合粒子粉末和硬质粒子粉末进行混合粉碎,所以混合粉碎工序后的混合粉末不受氧化的影响。虽然B2的硬质烧结体的组成的理论计算值与B2的混合粉末的配合组成存在一定的差异,但表现出了基本相同的倾向。如表5所示,铁铝中的Al的含量为9.56~57.68%,结合相中的Al2O3的含量为24.16~60.91mol%。以往,铁铝和硬质材料在混合粉碎工艺中发生的氧化产生了不良影响,但本发明通过积极地利用该氧化,得到具有非常优异的高温耐氧化性和高温硬度的硬质烧结体。工业实用性本发明的硬质烧结体能够用作以往使用超硬合金、金属陶瓷等的切削工具、耐磨工具、耐腐蚀性构件和高温用构件等的原材料。具体而言,能够合适地用作暴露在高温中的难切削材料的加工、高温锻造等切削工具用材料、耐磨工具用材料。当前第1页1 2 3