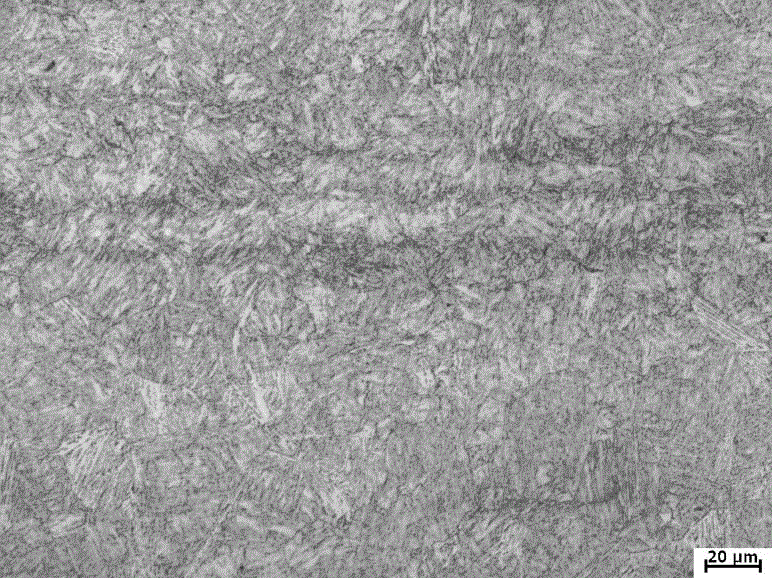
本发明属于钢铁
技术领域:
,涉及一种高强钢材生产方法,具体的说是一种超低碳当量大厚度Q690D高强钢生产方法。
背景技术:
:高强度钢是一种资源节约型同时也是一种技术含量高、附加值高的产品。大型建筑尤其是高层建筑,为了保证高层建筑整体安全的需要,要求结构件不仅具有较高的强度和焊接性,还要有较高的横纵向冲击韧性和优良的耐磨性。随着国内大型工程的大力发展,Q690D及以上等级的高强钢在工程机械、矿山开采、起重矿车、海洋平台等方面得到了大力应用。其特点是:结构简单,自重轻,安全性高,能够承载较大的动、静态载荷,服役时间较长。然而,由于国内铸坯受厚度影响,大厚度结构件目前只能采用常规Q345-Q550系列低合金结构钢代替,而此类结构钢因为强度低,在苛刻的服役条件下,使用强度不高,易出现工程事故。为此,针对大型工程结构钢件,国内企业只能花高价进口大厚度的高强钢。国内很多钢厂均在研究大厚度的Q690及以上高强钢的生产工艺,但对于100mm大厚度Q690D高强钢低碳当量研究较少,目前尚未有实质性的报道,已公布的专利文献内容中产品在实际工程应用更是微乎其微。公开号为:CN201310560500.6,一种调质高强钢Q690D特厚钢板的生产方法,通过合理的成分设计,经过在线淬火+离线调质,得到合理的性能,但该专利从公布的厚度为100mm所有的坯料化学成分来说,添加了0.03%Nb+0.046%V+0.47%Cr合金,且生产工艺采用两级淬火工艺,增加了生产工序,生产成本不经济;同时力学性能只做了横向冲击,对于纵向冲击值如何未公布。公开号为:CN201410221530.9,厚规格Q690D高强度高韧性钢板及其生产方法,采用合理的成分设计,通过在线TMCP+离线QT工艺,得到合理的性能,但该专利公布的生产方法只适合50mm-80mm厚度Q690D生产方法。公开号为:CN201410467565.0,一种特厚规格Q690高强度结构钢板及其制造方法,采用合理的成分设计,通过在线DQ+缓冷+回火工艺,得到合理的性能,但该专利公布的生产方法中的化学成分,添加了0.89%Ni+0.57%Mo等贵重的合金,且缓冷工序特别长,在大生产中不适合,且160mm-180mm冲击质量等级仅达到0℃即C级水平,且冲击功值均在70J以下。技术实现要素:本发明所要解决的技术问题是,如何使纵向冲击性能最优的100mm大厚度Q690D高强度结构钢板不仅具有较高的强度和韧性,还具有良好的焊接性能,且所有的要求均要易于生产且成本较低。为了解决以上技术问题,本发明针对100mm大厚度Q690D高强度钢板的化学成分和生产工艺进行了研究,提出了一种超低碳当量大厚度Q690D高强钢的生产方法,技术方案具体为:一种超低碳当量大厚度Q690D高强钢的生产方法,包括以下步骤:㈠炼钢成分设计:其化学成分按重量百分比计包括:C:0.14-0.16%,Si:0.2-0.3%,Mn:1.0-1.1%,P≤0.013%,S≤0.0015%,Cr:0.22-0.3%,Ni:0.5-0.6%,Mo:0.42-0.5%,Nb:0.012-0.02%,Ti:0.013-0.02%,V:0.03-0.04%,B≤0.0017%,Alt:0.035-0.055%,余量为Fe及不可避免的杂质,Ceq=C+Mn/6+(Cr+Mo+V)/5+(Cu+Ni)/15≤0.56;㈡出炉轧制工艺:出钢温度为1180-1200℃,在炉时间为300-400分钟,二阶段开轧温度≤880℃,成品厚度为100mm,待温坯厚度控制在≥150mm,二阶段终轧温度840-860℃,轧后空冷;㈢热处理工艺:淬火温度:900-920℃,升温速率:1.5±0.1min/mm,在炉时间为220-235min;回火温度:600-620℃,升温速率:2.2±0.1min/mm,在炉时间为270-320min;钢板热处理后力学性能达到以下水平:屈服强度≥800MPa,抗拉强度≥860MPa,延伸率≥16%,-20℃,纵向Akv冲击功值≥160J;显微组织为回火贝氏体组织,晶粒尺寸控制在10μm-12μm,晶粒度控制在10级。本发明通过中碳加少量的铬、镍、钼合金及Nb、V、Ti、B微合金化成份设计,配合合理的轧制、调质热处理工艺生产厚度达到100mm厚度的Q690D高强钢,且力学性能达到国标GB/T16270-2009标准要求,其实际水平达到:屈服强度≥800MPa,抗拉强度≥860MPa,延伸率≥16%,-20℃,纵向Akv冲击功值≥160J。该方法成功解决了100mm大厚度高强钢强度高低塑性、低压缩比纵向冲击功值差异大以及焊接性不稳定的技术难点。本发明的有益效果是:⑴通过中碳加少量的铬、镍、钼合金、Nb+Ti+V+B微合金化成份设计,设计碳当量ceq≤0.56,实际碳当量ceq=0.50-0.51,生产工序流程短,成本低;⑵本方法采用合理的弱控轧工艺生产厚度达到100mm的超高强钢,通过最优的调质热处理工艺,各力学性能指标均达到国标GB/T16270-2009标准要求,其实际的生产水平达到:屈服强度≥800MPa,抗拉强度≥860MPa,延伸率≥16%,-20℃,纵向Akv冲击功值≥160J;⑶该发明方法成功解决了100mm的大厚度Q690D高强钢的高强度低塑性、低压缩比纵向冲击功值差以及高碳当量对焊接性能影响的技术难点。⑷该发明方法成功解决了在四辊可逆的5000mm轧机生产线能够生产高强度、高韧性大厚度Q690D高强钢。本发明的低碳当量大厚度Q690D高强钢生产方法,通过中碳、低锰、Cr+Ni+Mo合金化、Nb+V+Ti微合金化成份设计生产大厚度Q690D超高强钢,设计碳当量ceq≤0.56,实际碳当量ceq=0.50-0.51。经过调质热处理后,力学性能达到国标GB/T16270-2009的性能标准要求,应用到国内大型工程机械设备,大大降低了依赖进口高成本费用。随着国内大型工程的发展需求,大厚度Q690D及以上等级的高强钢在工程机械、矿山开采、起重矿车、海洋平台等方面将有更大的应用前景。附图说明图1是本发明实施例3的1/4厚度处金相组织图。图2是本发明实施例3的1/2厚度处金相组织图。具体实施方式实施例本发明实施例为超低碳当量大厚度Q690D高强钢的生产方法,包括在的工序为:铁水脱硫预处理→转炉冶炼→LF+RH精炼→连铸→铸坯堆垛缓冷→铸坯检验→铸坯判定→铸坯验收→铸坯加热→除鳞→轧制→空冷→(探伤)→抛丸→淬火→回火→矫直→切割、取样→喷印标识→检验→入库。其中:⑴100mm厚度规格Q690D超高强钢化学成分实际重量百分比实例1化学成分实例2化学成分实例3化学成分由于100mm厚度钢板因轧制需要采用高温大压下,钢板轧后板形较差,需要在790-830℃进行预矫,保证原始板形。在坚持低成本生产要求的基础上,确保淬火能淬透,在成分设计中采用中碳加少量的提高淬透性的Cr、Mo、B元素从而可以提高冷速设计思路解决生产需高等级设备要求。⑵加热工艺由于实验钢强度高,100mm钢板采用高温大压下模式进行控轧,受铸坯厚度发展影响,本专利方法采用压缩比3.2倍,即选用320mm厚度坯料,且均热温度控制在1225℃左右,考虑合金溶解需要时间,在炉时间适当延长,确保坯料钢温整体均匀,避免出现“红黑”相间的钢温。⑶控轧工艺由于成品厚度为100mm,在轧制过程中为避免出现心部偏析,影响强度和和冲击韧性值,故采用二阶段展宽轧制方法,且一阶段轧制形变率≥53%,二阶段总形变率≥33%,确保表面到心部组织足够细小。⑷淬火工艺实例成品厚(mm)淬火温度(℃)升温速率(min/mm)总加热时间(min)11009151.522721009121.522831009181.5231⑸回火工艺实例成品厚(mm)回火温度(℃)升温速率(min/mm)总加热时间(min)11006072.329921006082.129131006052.2280各实施例高强钢的力学性能为:以上实施例通过中碳和少量铬、镍、钼合金、铌+钒+钛+硼微合金化的成份设计,配合合理的弱控轧工艺、调质热处理工艺,开发出100mm厚度的Q690D高强度钢。经过控轧、调质热处理后,其力学性能中屈服强度≥800MPa,抗拉强度≥860MPa,延伸率≥16%,-20℃,纵向Akv冲击功值≥160J;本专利所获得的这些强度、塑性及纵向冲击韧性指标均达到国标要求同时也满足了国内某大型企业工程机械其力学性能的设计标准。由于强度高,厚度大,在实际工业生产过程中,对轧制设备和淬火机冷却能力要求较高,为避免在生产过程中不能满足大压下轧制要求,易造成原始晶粒尺寸粗大,甚至出现混晶现象,从而严重影响强度和低温冲击韧性相匹配的力学性能。通过中碳加淬透性较高的合金元素成分设计,利用横纵向展宽轧制坯料设计方法,从而弥补了满足常规轧制生产线因装备能力有限不能够生产高强度、高韧性、高焊接稳定性的Q690D高强钢的缺陷,同时采用高温结束轧制,使得高温态强度较低,充分发挥轧制设备能力。图1为回火加热温度:605℃,升温速率:2.2min/mm,加热时间为:280min,回火后的金相组织,从图中的组织可以看出,从1/4厚度处到心部均为回火贝氏体组织,且晶粒尺寸控制在10μm-12μm,晶粒度达到10级。除上述实施例外,本发明还可以有其他实施方式。凡采用等同替换或等效变换形成的技术方案,均落在本发明要求的保护范围。当前第1页1 2 3