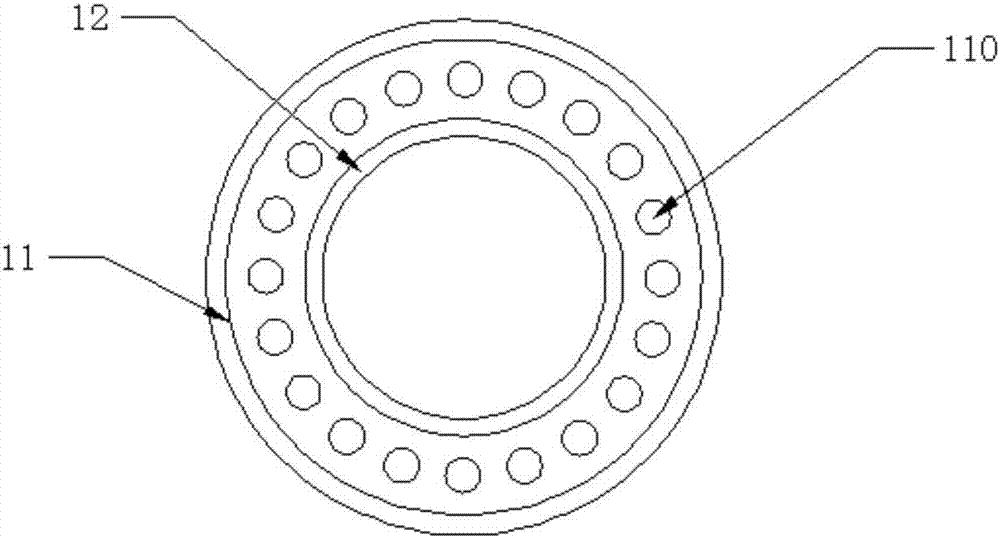
本发明涉及光学镜片加工设备领域,尤其涉及适用于非球面镜片加工的真空吸附定位工装及镜片加工方法。
背景技术:
:主反射镜主要用于经典的卡塞格林系统中。主反射镜为非球面反射镜。主反射镜的技术指标主要包括非球面精度、离轴角和非球面的顶角角度。现有的真空吸附盘中,吸附孔开设在吸附盘的中间,通过抽取工件底面与吸附盘之间的空气实现吸附。主反射镜的镜片中心需要开设通孔,因此现有的真空吸附盘不适合在主反射镜加工过程中使用。现有的加工过程中,开孔完成后在进行铣磨离轴角和顶角角度时,将工件通过机械夹具定位后进行离轴角铣磨;然后,将工件再次定位,用微分表进行了精密测量确认后,然后进行顶角铣磨。这两个工序传统的加工方式都是通过手工操作来完成的。由于主反射面的一面是平面,另一面是非球面,因此手工操作的质量差。此外,工件需要重复装夹定位,导致精度也下降。技术实现要素:为解决上述现有技术中的问题,本发明提供的技术方案如下:适用于非球面镜片加工的真空吸附定位工装,包括吸附工装盘,所述吸附工装盘的顶部开设装配凹台,在所述装配凹台的底部开设多个边缘吸附孔,所述装配凹台的内部设置辅助支撑环,使所述边缘吸附孔位于所述辅助支撑环的外壁与所述装配凹台的内壁之间内。工件放置在吸附工装盘上,根据加工的离轴角角度,调整工件与装配凹台之间的角度。工件的底面、装配凹台的内侧壁以及辅助支撑环的外侧壁之间形成密闭空间。通过边缘吸附孔抽真空,即可将工件的边缘固定在吸附工装盘上。在完成工件装夹之后,通过工具依次对工件进行精密打孔、铣磨离轴角和顶角三个工序。由于工件打孔的位置位于工件的中心,即辅助支撑环的内部。开设通孔的工件依然能够通过工件的边缘与装配凹台、辅助支撑环形成密闭空间,使工件仍能够稳定地固定在吸附工装盘上。一次工装即可完成三道工序,避免了重复装夹定位,既提高了生产效率,实现了批量化生产同,时也保证了加工的良品率。在一种优选的实施方式中,所述辅助支撑环的高度低于所述装配凹台的深度。在一种优选的实施方式中,所述辅助支撑环的顶部边缘套置密封圈,所述装配凹台的顶部边缘套置密封圈。在一种优选的实施方式中,在所述装配凹台的底部还开设中心吸附孔,所述中心吸附孔位于所述辅助支撑环内。在一种优选的实施方式中,所述吸附工装盘的外侧壁下方设置固定底座,所述固定底座上开设装配孔。本发明还提供一种非球面镜片加工方法,使用上述的真空吸附定位工装,在工件进行抛光后,还包括以下的步骤:S501,将抛光后的工件放置在吸附工装盘上,启动真空装置,使工件的边缘部被吸附在辅助支撑环与装配凹台之间。S502,采用超声波方式对工件的中心打孔。现有的加工顺序为铣磨、打孔、抛光。但是,先打孔再抛光将无法测量零件的非球面面形,从而导致抛光的精度低。本发明中,将工件的打孔工序设置在抛光工序之后完成,一方面保证抛光的加工精度,另一方面还能使打孔、离轴角和顶角三道工序能够一并完成,减少重复夹装。S503,采用超声波方式对工件的离轴角进行铣磨。S504,采用超声波方式对工件的顶角进行铣磨。在一种优选的实施方式中,在步骤S501之前还包括以下的步骤:S101,对工件进行球面铣磨;S201,对工件的球面进行非球面铣磨,使工件的非球面的表面面形至少达到Rt<1.5μm,表面粗糙度达到Ra<0.3μm;S301,对工件进行抛光,使工件的非球面的表面面形至少达到Rt<0.5μm,表面粗糙度达到Ra<0.1μm;S401,对工件进行定心磨边。在一种优选的实施方式中,在步骤S201中,工件的转速为15-20r/min,工具轴的转速为6000r/min。在一种优选的实施方式中,在步骤S301中,工件的转速为25-30r/min,工具轴的转速为8000r/min。本发明的有益效果为:本发明的吸附工装盘中,装配凹台的内部设置辅助支撑环,辅助支撑环的外壁与装配凹台的内壁之间的底部设置边缘吸附孔。固定工件时,工件的底面、装配凹台的内侧壁以及辅助支撑环的外侧壁之间形成密闭空间。通过边缘吸附孔抽真空,即可将工件的边缘固定在吸附工装盘上。在完成工件装夹之后,通过工具依次对工件进行精密打孔、铣磨离轴角和顶角三个工序。避免了重复装夹定位,既提高了生产效率,实现了批量化生产同,时也保证了加工的良品率。由于工件打孔的位置位于工件的中心,即辅助支撑环的内部,因此,开设通孔的工件仍能够稳定地固定在吸附工装盘上。本发明的非球面镜片加工方法中,将工件的打孔工序设置在抛光工序之后完成,一方面保证抛光的加工精度,另一方面还能使打孔、离轴角和顶角三道工序能够一并完成,减少重复夹装。附图说明为了更清楚地说明本发明实施例或现有技术中的技术方案,下面将对实施例或现有技术描述中所需要使用的附图作简单地介绍,显而易见地,下面描述中的附图仅仅是本发明的一些实施例,对于本领域普通技术人员来讲,在不付出创造性劳动的前提下,还可以根据这些附图获得其他的附图。图1是吸附工装盘一种实施方式的剖视图;图2是吸附工装盘一种实施方式的俯视图;图3是吸附工装盘另一种实施方式的剖视图;图4是吸附工装盘又一种实施方式的剖视图;图5是真空吸附定位工装一种实施方式的剖视图。具体实施方式下面将结合本发明的附图,将对本发明的技术方案进行清楚、完整地描述,显然,所描述的实施例仅仅是本发明一部分实施例,而不是全部的实施例。基于本发明中的实施例,本领域普通技术人员在没有作出创造性劳动前提下所获得的所有其他实施例,都属于本发明保护的范围。结合图1-2,本实施例提供的适用于非球面镜片加工的真空吸附定位工装,包括吸附工装盘1。吸附工装盘1的顶部开设装配凹台11,装配凹台11的内径与磨边后的工件圆周半径匹配。装配凹台11的内部设置辅助支撑环12。辅助支撑环12的轴线与装配凹台11的轴线平行。在装配凹台11的底部开设多个边缘吸附孔110。边缘吸附孔110的底部通过气管连接至真空发生装置。边缘吸附孔110沿着装配凹台11的边缘均匀分布,处于装配凹台11内壁与辅助支撑环12的外壁之间。优选地,辅助支撑环12的轴线与装配凹台11的轴线重叠,以使工件的底面在固定时受力均匀。在固定工件时,根据加工的离轴角角度,调整工件与装配凹台之间的角度。工件的底面、装配凹台11的内侧壁以及辅助支撑环12的外侧壁之间形成密闭空间。启动真空发送装置,抽取密闭空间内的空气,使工件的边缘受到大气压力,将工件固定在装配凹台11内。在完成工件装夹之后,采用铣磨工具依次对工件进行精密打孔、离轴角铣磨和顶角铣磨三个工序。当工件打孔完成后,开设通孔的工件依然能够通过工件的边缘与装配凹台、辅助支撑环形成密闭空间,使工件仍能够稳定地固定在吸附工装盘上,无需重新定位装夹,就能够继续进行离轴角铣磨以及顶角铣磨的工序。为了保证工件与装配凹台11之间能够紧密连接,在一种实施方式中,如图3,辅助支撑环12的高度低于装配凹台11的深度,使工件能够置于装配凹台11内,同时工件的弧形底面能够与辅助支撑环顶面紧密接触。装配凹台11的边缘套置环形密封圈13,辅助支撑环12的边缘套置环形密封圈14。工件置入装配凹台11内,使工件的边缘与密封圈13紧密连接,工件的底面与环形密封圈14紧密连接,以提高工件与装配凹台11、辅助支撑环12的紧密性,以提高吸附的稳定性。如图4,在装配凹台11的底部还开设中心吸附孔111,中心吸附孔111位于辅助支撑环12内。工件底面的中部与辅助支撑环的内壁之间形成密闭空间。中心吸附孔111通过气管连接至真空发生装置。在工件未打孔时,边缘吸附孔110以及中心吸附孔111分别抽取真空,使工件的中间部位吸附在辅助支撑环内,边缘部位吸附在辅助支撑环与装配凹台之间。在打孔过程中,要求的定位准确性较高,且不能出现划痕或破边,因此采用两种吸附孔同时对工件的中心以及边缘进行固定,保证加工的准确性。为了方便将真空吸附定位工装固定在工作台上,如图5,在吸附工装盘1外侧壁的下部焊接固定底座2,固定底座2上开设装配孔20。使用上述实施例中真空吸附定位工装的非球面镜片加工方法,在工件进行抛光后,还包括以下的加工步骤:S501,将抛光后的工件放置在装配凹台内,启动真空装置,使工件的边缘部被吸附在辅助支撑环与装配凹台之间,工件的中部被吸附在辅助支撑环内。S502,采用超声波方式对工件的中心打孔。启动超声波发生器,换能器将超声频电振荡转变为超声机械振动,通过变幅杆使工具产生超声波振动,控制变幅杆的位置对准工件的中心,使磨料悬浮液高速地不断撞击、抛磨工件表面,将工件中心开设通孔。S503,采用超声波方式对工件的离轴角进行铣磨。控制变幅杆的位置,通过变幅杆铣磨离轴角,使工件的非球面光轴与工件的几何光轴保持18′50″的离轴角。S504,采用超声波方式对工件的顶角进行铣磨。控制变幅杆的位置,使变幅杆在工件离轴角的最高点上磨出5.9×15°倾斜面。在一种优选的实施方式中,在步骤S501之前还包括以下的步骤:S101,对工件进行球面铣磨;S201,对工件的球面进行非球面铣磨,使工件的非球面的表面面形至少达到Rt<1.5μm,表面粗糙度达到Ra<0.3μm;工件的转速为15-20r/min,工具轴的转速为6000r/min。S301,对工件进行抛光,使工件的非球面的表面面形至少达到Rt<0.5μm,表面粗糙度达到Ra<0.1μm;工件的转速为25-30r/min,工具轴的转速为8000r/min。S401,对工件进行定心磨边。对上述加工方法制成的镜片进行检测,主要测量打孔精度、打孔效率、离轴角加工精度、良品率等方面。将上述镜片的测量数据与传统的铣磨打孔、手工离轴角打磨出的镜片进行对比,具体的测量结果如表1和表2。从表格可知,本发明中的加工方式极大地提高了镜片加工的良品率,而且加工精度大大提高,加工效率也为传统方式的数倍。表1传统打孔与超声波精密打孔的对比打孔方式打孔精度破边打孔效率良品率铣磨±0.10.3-130分/件70%-80%超声振动±0.03≤0.310分/件≥90%表2传统离轴角加工与数控加工的对比加工方式控制指标加工精度加工效率良品率手工加工等厚差3′15-20件/天70%-80%超声振动角度误差30″>100件/天≥90%以上所述,仅为本发明的具体实施方式,但本发明的保护范围并不局限于此,任何熟悉本
技术领域:
的技术人员在本发明揭露的技术范围内,可轻易想到变化或替换,都应涵盖在本发明的保护范围之内。因此,本发明的保护范围应以所述权利要求的保护范围为准。当前第1页1 2 3