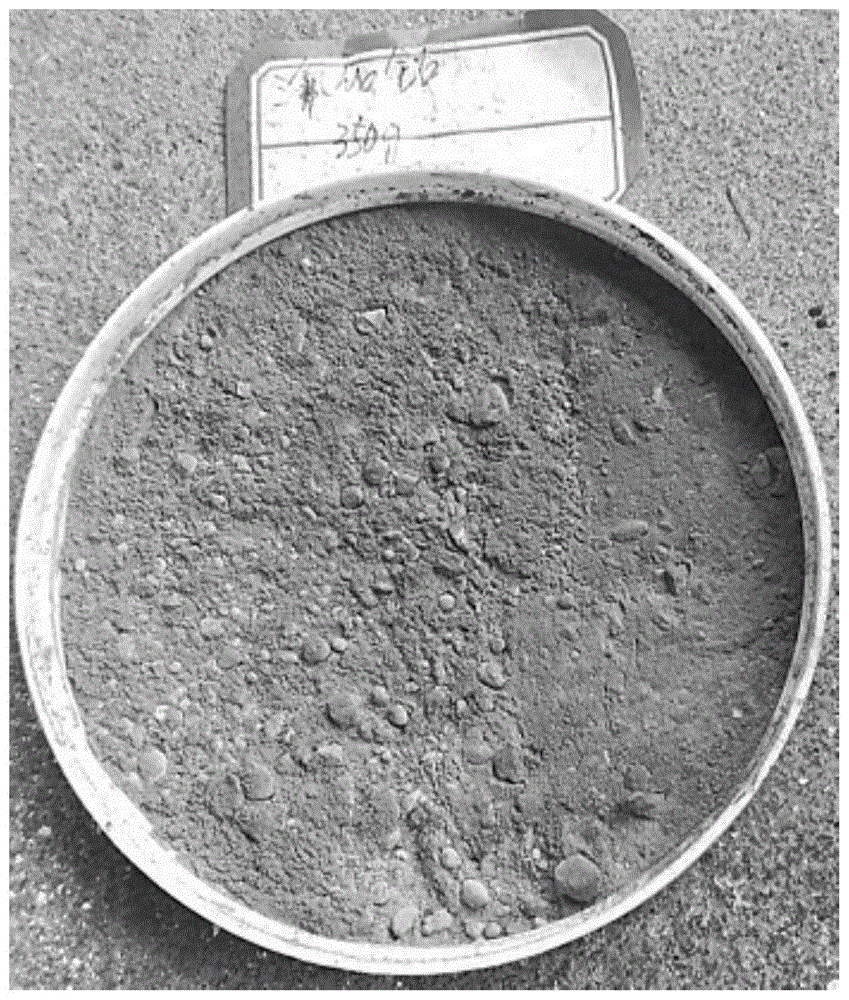
本发明涉及锂电池材料
技术领域:
,尤其涉及一种三氟化钴的制备方法。
背景技术:
:三氟化钴(化学式:cof3),室温下为不稳定的浅棕色易潮解固体,密度为3.88g/ml(25℃),溶于水放出氧气,是很常用的氟化剂。在co2气流中加热到250℃时,开始放出f2,在350℃时,则完全转变为cof2。三氟化钴可以与许多金属或非金属单质反应生成相应的氟化物,自身被还原为二氟化钴。三氟化钴也有水合物,cof3·3.5h2o,但结构尚不清楚。用三氟化钴氟化有机化合物时,首先用二氟化钴与氟气在300℃左右反应生成三氟化钴,然后引入有机反应物与三氟化钴反应。三氟化钴被还原后生成的二氟化钴可以循环使用。三氟化钴的制备方法很多,一般采用二氯化钴或者二氟化钴与氟气直接高温反应,此外,用三氟化氯来氟化金属钴或一氧化钴与氟气反应也可得到三氟化钴。其中比较常用的是二氟化钴直接氟化法,即在高温下直接向装有二氟化钴的反应釜内通入氟气,二者反应生成三氟化钴。实际操作中,由于二氟化钴为固体堆叠,内部的二氟化钴不容易反应到,使得即使消耗了很多氟气,但最终的产品中通常仍少量的二氟化钴存在。即氟气消耗量大,且三氟化钴在最终产品中的含量低。技术实现要素:本发明的目的在于克服现有技术中的缺陷,提供一种三氟化钴的制备方法,降低了氟气消耗量,并提高了三氟化钴在最终产品中的含量。本发明是这样实现的:本发明提供了一种三氟化钴的制备方法,所述方法包括如下步骤:步骤1、将二氟化钴,与铵盐混合;所述二氟化钴与铵盐的重量比为20~60:1;步骤2、转入反应釜内,通入氟气进行氟化生产。优选地,所述步骤1中,所述铵盐包括氯化铵或氟化铵中的任意一种。更为优选地,所述铵盐为氯化铵。优选地,所述二氟化钴与铵盐的重量比为40:1。优选地,所述氟化生产的反应温度为190~210℃。更为优选地,所述氟化生产的反应温度为200℃。优选地,所述步骤2中氟化生产的具体步骤为:所述氟化生产的具体步骤为:s1、先升温至50℃,开始通入纯氟气至釜内压力为1.8~2.2公斤,升温至190~210℃开始反应,5~15min后排空釜内压力;s2、然后继续通入氟气至1.8~2.2公斤压力,继续在190~210℃反应,5~15min后排空釜内压力;s3、再继续步骤s2多次直至反应完毕,即再继续通入氟气至1.8~2.2公斤压力,继续在190~210℃反应,5~15min后排空釜内压力。本发明具有的有益效果是:本发明提供的一种三氟化钴的制备方法,在进行氟化生产之前先将二氟化钴与铵盐混合再转入反应釜内;从而降低了氟气消耗量,并提高了三氟化钴在最终产品中的含量。其原理为:二氟化钴与铵盐混合后,当在适当温度下烘干加热时,其内混合的铵盐(氯化铵或氟化铵)会进一步分解,使得待反应二氟化钴变得更加疏松多孔,这样在后续的二氟化钴氟化反应时,可以最大程度的保证内外反应均匀,氟化效果好。处理完毕后,将二氟化钴加入氟化碳反应釜,在190-210℃条件下间歇性的通入氟气进行氟化反应,使得二氟化钴内部的氟化反应完全,用该法所生产的三氟化钴产品中三氟化钴的含量可以达到95.81%,二氟化钴含量不超过5%。附图说明图1为实施例1制备得到的三氟化钴成品图片;图2为实施例1制备得到的三氟化钴成品检测报告图。具体实施方式下面结合实施例,进一步阐明本发明。这些实施例应理解为仅用于说明本发明而不是用于限制本发明的保护范围。在阅读了本发明记载的内容之后,本领域技术人员可以对本发明作各种改动或修改,这些等效变化和修饰同样落入本发明权利要求书所限定的范围。实施例1一种三氟化钴的制备方法,所述方法包括如下步骤:步骤1、将2000g焦炭粉碎完毕,与50g的氯化铵混合;步骤2、转入反应釜内,进行氟化生产。反应釜有加热装置,反应釜尾气排放处装有干燥装置,尾气通入氢氧化钾水溶液进行吸收。开始加热装置升温至50℃后,开始通入氟气至釜内压力为2公斤,继续升温至200℃开始反应,20分钟后排空釜内压力。继续通入氟气至2公斤压力,继续反应。整个反应过程期间釜内温度控制在200℃左右。直至反应完毕,消耗氟气1200g。共制备三氟化钴混合产品2370g,其中三氟化钴含量为95.81%。实施例2一种三氟化钴的制备方法,所述方法包括如下步骤:步骤1、将2100g焦炭粉碎完毕,与35g的氯化铵混合;步骤2、转入反应釜内,进行氟化生产。反应釜有加热装置,反应釜尾气排放处装有干燥装置,尾气通入氢氧化钾水溶液进行吸收。开始加热装置升温至50℃后,开始通入氟气至釜内压力为1.8公斤,继续升温至190℃开始反应,20分钟后排空釜内压力。继续通入氟气至1.8公斤压力,继续反应。整个反应过程期间釜内温度控制在190℃左右。直至反应完毕,消耗氟气1280g。共制备三氟化钴混合产品2361g,其中三氟化钴含量为93.65%。实施例3一种三氟化钴的制备方法,所述方法包括如下步骤:步骤1、将2000g焦炭粉碎完毕,与100g的氯化铵混合;步骤2、转入反应釜内,进行氟化生产。反应釜有加热装置,反应釜尾气排放处装有干燥装置,尾气通入氢氧化钾水溶液进行吸收。开始加热装置升温至50℃后,开始通入氟气至釜内压力为2.2公斤,继续升温至210℃开始反应,20分钟后排空釜内压力。继续通入氟气至2.2公斤压力,继续反应。整个反应过程期间釜内温度控制在210℃左右。直至反应完毕,消耗氟气1210g。共制备三氟化钴混合产品2369g,其中三氟化钴含量为95.35%。实施例4一种三氟化钴的制备方法,所述方法包括如下步骤:步骤1、将2000g焦炭粉碎完毕,与50g的氟化铵混合;步骤2、转入反应釜内,进行氟化生产。反应釜有加热装置,反应釜尾气排放处装有干燥装置,尾气通入氢氧化钾水溶液进行吸收。开始加热装置升温至50℃后,开始通入氟气至釜内压力为2公斤,继续升温至200℃开始反应,20分钟后排空釜内压力。继续通入氟气至2公斤压力,继续反应。整个反应过程期间釜内温度控制在200℃左右。直至反应完毕,消耗氟气1190g。共制备三氟化钴混合产品2367g,其中三氟化钴含量为94.92%。实施例5一种三氟化钴的制备方法,所述方法包括如下步骤:步骤1、将2100g焦炭粉碎完毕,与35g的氟化铵混合;步骤2、转入反应釜内,进行氟化生产。反应釜有加热装置,反应釜尾气排放处装有干燥装置,尾气通入氢氧化钾水溶液进行吸收。开始加热装置升温至50℃后,开始通入氟气至釜内压力为1.8公斤,继续升温至190℃开始反应,20分钟后排空釜内压力。继续通入氟气至1.8公斤压力,继续反应。整个反应过程期间釜内温度控制在190℃左右。直至反应完毕,消耗氟气1275g。共制备三氟化钴混合产品2355g,其中三氟化钴含量为93.36%。实施例6一种三氟化钴的制备方法,所述方法包括如下步骤:步骤1、将2000g焦炭粉碎完毕,与100g的氟化铵混合;步骤2、转入反应釜内,进行氟化生产。反应釜有加热装置,反应釜尾气排放处装有干燥装置,尾气通入氢氧化钾水溶液进行吸收。开始加热装置升温至50℃后,开始通入氟气至釜内压力为2.2公斤,继续升温至210℃开始反应,20分钟后排空釜内压力。继续通入氟气至2.2公斤压力,继续反应。整个反应过程期间釜内温度控制在210℃左右。直至反应完毕,消耗氟气1260g。共制备三氟化钴混合产品2369g,其中三氟化钴含量为95.45%。对比例1向10升不锈钢高温高压反应釜内加入2公斤二氟化钴,当升温至50℃后,开始通入氟气至釜内压力为2公斤,继续升温直至开始反应,20分钟后排空釜内压力。继续通入氟气至2公斤压力,继续反应。整个反应过程期间釜内温度控制在190-210℃范围内。直至反应完毕,消耗氟气2公斤。共制备三氟化钴混合产品2.31公斤,其中三氟化钴含量为84.25%。实验例统计实施例1~6以及对比例1最后得到三氟化钴混合产品重量,氟气消耗量,三氟化钴在最终产品中的含量,如表1和表2所示。表1三氟化钴氯化铵产物总量三氟化钴含量氟气消耗量实施例12000g50g2370g95.81%1200g实施例22100g35g2361g93.65%1280g实施例32000g100g2369g95.35%1210g对比例12000g/2310g84.25%2000g表2三氟化钴氟化铵产物总量三氟化钴含量氟气消耗量实施例12000g50g2367g94.92%1190g实施例22100g35g2355g92.36%1275g实施例32000g100g2369g95.45%1260g对比例12000g/2310g84.25%2000g由表1和表2可知,与对比例1相比,实施例1-实施例6均降低了氟气消耗量,并提高了三氟化钴在最终产品中的含量;其中氟气消耗量从对比例1的2000g降低至1200g~2000g;三氟化钴在最终产品中的含量从对比例1的84.25%升高至95.81%。以上所述仅为本发明的较佳实施例而已,并不用以限制本发明,凡在本发明的精神和原则之内,所作的任何修改、等同替换、改进等,均应包含在本发明的保护范围之内。当前第1页12