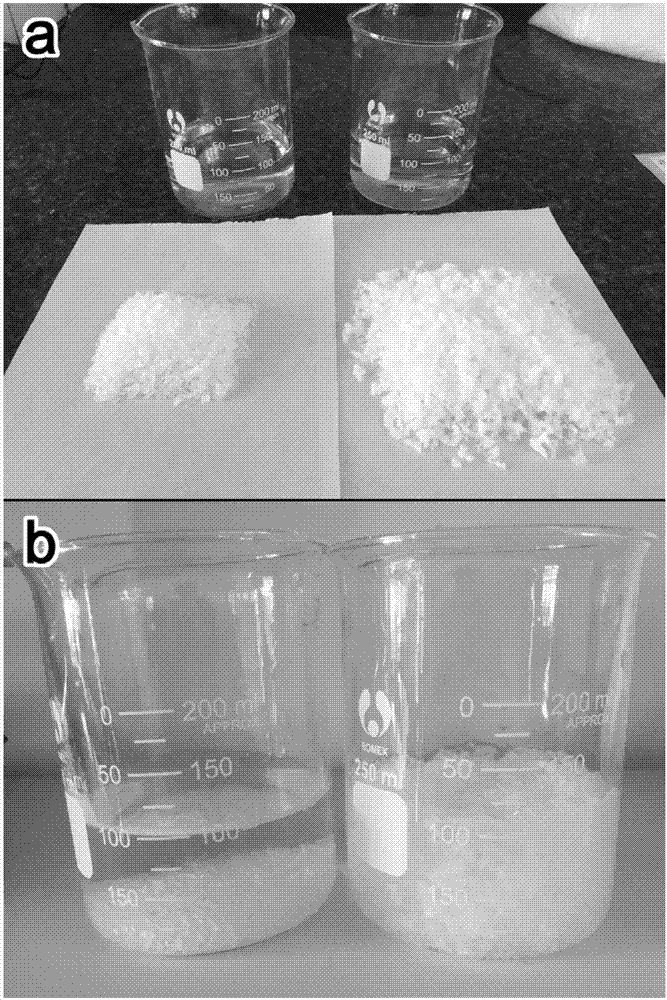
本发明涉及化工
技术领域:
,具体指一种聚乙烯醇熟化预处理方法。
背景技术:
:聚乙烯醇是重要的化工原料,用于制造聚乙烯醇缩醛、耐汽油管道和维尼纶合成纤维、织物处理剂、乳化剂、纸张涂层、粘合剂、胶水等。现有技术中,由不同生产工艺可以得到不完全醇解和完全醇解的聚乙烯醇产品,其作用和性能不同。不完全醇解的聚乙烯醇是冷水可溶的,而完全醇解的聚乙烯醇则需要沸水溶解。国标产品的100-40和100-50型号(国标)的聚乙烯醇是经过完全醇解工艺处理的,其颗粒聚乙烯醇的6%水溶液需要沸水搅拌2小时才能完全溶解,费时且能源消耗大。技术实现要素:本发明的目的在于克服现有完全醇解的聚乙烯醇产品需要高温溶解,且耗时长的缺陷,提供一种简单、高效的聚乙烯醇熟化预处理方法,以降低完全醇解聚乙烯醇产品的溶解温度,缩短溶解时间。为实现上述目的,本发明所设计的聚乙烯醇熟化预处理方法,包括以下步骤:1)取完全醇解的聚乙烯醇、水、偶联剂按照1:0.5~1:0.01~0.05的重量比配置成混合物,所述偶联剂为3-氨丙基甲基二乙氧硅烷和/或3-缩水甘油醚氧基三甲氧基硅烷;2)然后按照重量比再向混合物中添加0.01%的醋酸甲脂和丙三醇的混合物;3)对所述混合物进行加温物理挤压捏合,挤压时间为50分钟~2小时,温度为75~85℃;4)对挤压捏合后的混合物进行粉碎,即得到完全醇解的改性聚乙烯醇。优选地,所述偶联剂为3-氨丙基甲基二乙氧硅烷和3-缩水甘油醚氧基三甲氧基硅烷的混合偶联剂。更优选地,所述所述偶联剂为3-氨丙基甲基二乙氧硅烷和3-缩水甘油醚氧基三甲氧基硅烷的重量比为1:1.75的混合偶联剂。可选地,所述醋酸甲脂和丙三醇的混合物中醋酸甲脂和丙三醇的重量比为1:1。本发明原理:通过在完全醇解的聚乙烯醇中加入偶联剂偶联后增大其分子量,再加入有机溶剂醋酸甲酯和丙三醇稀释,渗透聚乙烯醇使其溶胀,最后再用物理方法升温挤压使其膨胀、干燥。因此获得了能够在更低温度下速溶的改性聚乙烯醇。本发明的有益效果:通过本发明方法对聚乙烯醇进行预处理,可以使其熟化,降低了完全醇解聚乙烯醇的溶解温度,并且大幅缩短了溶解时间,产物在95℃水中30分钟可完全溶解,或者置于沸水中20分钟完全溶解;该方法大幅的提高了聚乙烯醇的使用效率,节约能源和耗时,具有较好的经济效益,且操作方法简单,处理时间短,实用性强。附图说明图1为同等重量下,未改性的聚乙烯醇和经过本发明方法改性的聚乙烯醇体积对比图。图2为图1所示等量的聚乙烯醇投入水中的状态对比图。具体实施方式下面结合附图和具体实施例对本发明作进一步的详细说明,以下实施例是对本发明的解释而本发明并不局限于以下实施例。以下实施例中采用的完全醇解聚乙烯醇原料为市售的安徽皖维20-99片状聚乙烯醇对应国标(100-40)。实施例1聚乙烯醇熟化预处理方法,包括以下步骤:1)取完全醇解的聚乙烯醇、水、偶联剂按照1:0.5:0.01的重量比配置成混合物,所述偶联剂为3-氨丙基甲基二乙氧硅烷;2)然后按照重量比再向混合物中添加0.01%的醋酸甲脂和丙三醇的混合物,其中醋酸甲脂和丙三醇的重量比为1:1;3)对所述混合物进行加温物理挤压捏合,挤压时间为50分钟~2小时,温度为75~85℃;4)对挤压捏合后的混合物进行粉碎,即得到完全醇解的改性聚乙烯醇。实施例2聚乙烯醇熟化预处理方法,包括以下步骤:1)取完全醇解的聚乙烯醇、水、偶联剂按照1:0.5:0.01的重量比配置成混合物,所述偶联剂为3-缩水甘油醚氧基三甲氧基硅烷;2)然后按照重量比再向混合物中添加0.01%的醋酸甲脂和丙三醇的混合物,其中醋酸甲脂和丙三醇的重量比为1:1;3)对所述混合物进行加温物理挤压捏合,挤压时间为50分钟~2小时,温度为75~85℃;4)对挤压捏合后的混合物进行粉碎,即得到易低温溶解的完全醇解的改性聚乙烯醇。实施例3聚乙烯醇熟化预处理方法,包括以下步骤:1)取完全醇解的聚乙烯醇、水、偶联剂按照1:1:0.03的重量比配置成混合物,所述偶联剂为3-缩水甘油醚氧基三甲氧基硅烷;2)然后按照重量比再向混合物中添加0.01%的醋酸甲脂和丙三醇的混合物,其中醋酸甲脂和丙三醇的重量比为1:1;3)对所述混合物进行加温物理挤压捏合,挤压时间为50分钟~2小时,温度为75~85℃;4)对挤压捏合后的混合物进行粉碎,即得到易低温溶解的完全醇解的改性聚乙烯醇。实施例41)取完全醇解的聚乙烯醇、水、偶联剂按照1:1:0.03的重量比配置成混合物,所述偶联剂为3-氨丙基甲基二乙氧硅烷和3-缩水甘油醚氧基三甲氧基硅烷的重量比为1:1的混合偶联剂;2)然后按照重量比再向混合物中添加0.01%的醋酸甲脂和丙三醇的混合物,其中醋酸甲脂和丙三醇的重量比为1:1;3)对所述混合物进行加温物理挤压捏合,挤压时间为50分钟~2小时,温度为75~85℃;4)对挤压捏合后的混合物进行粉碎,即得到完全醇解的改性聚乙烯醇。实施例51)取完全醇解的聚乙烯醇、水、偶联剂按照1:1:0.05的重量比配置成混合物,所述偶联剂为3-氨丙基甲基二乙氧硅烷和3-缩水甘油醚氧基三甲氧基硅烷的重量比为1:1的混合偶联剂;2)然后按照重量比再向混合物中添加0.01%的醋酸甲脂和丙三醇的混合物,其中醋酸甲脂和丙三醇的重量比为1:1;3)对所述混合物进行加温物理挤压捏合,挤压时间为50分钟~2小时,温度为75~85℃;4)对挤压捏合后的混合物进行粉碎,即得到易低温溶解的完全醇解的改性聚乙烯醇。实施例61)取完全醇解的聚乙烯醇、水、偶联剂按照1:1:0.03的重量比配置成混合物,所述偶联剂为3-氨丙基甲基二乙氧硅烷和3-缩水甘油醚氧基三甲氧基硅烷的重量比为1:1.75的混合偶联剂;2)然后按照重量比再向混合物中添加0.01%的醋酸甲脂和丙三醇的混合物,其中醋酸甲脂和丙三醇的重量比为1:1;3)对所述混合物进行加温物理挤压捏合,挤压时间为50分钟~2小时,温度为75~85℃;4)对挤压捏合后的混合物进行粉碎,即得到易低温溶解的完全醇解的改性聚乙烯醇。实施例71)取完全醇解的聚乙烯醇、水、偶联剂按照1:0.8:0.03的重量比配置成混合物,所述偶联剂为3-氨丙基甲基二乙氧硅烷和3-缩水甘油醚氧基三甲氧基硅烷的重量比为1:1.75的混合偶联剂;2)然后按照重量比再向混合物中添加0.01%的醋酸甲脂和丙三醇的混合物,其中醋酸甲脂和丙三醇的重量比为1:1;3)对所述混合物进行加温物理挤压捏合,挤压时间为50分钟~2小时,温度为75~85℃;4)对挤压捏合后的混合物进行粉碎,即得到易低温溶解的完全醇解的改性聚乙烯醇。试验例1对上述实施例1~7所获得的改性聚乙烯醇进行粘度检测试验,以验证其效果。本试验例为按聚乙烯醇国标方法检测所得的絮状聚乙烯醇粘度,检测样品来自实施例1~7,对照例为原料的安徽皖维20-99片状聚乙烯醇。1、分别取每个实施例的聚乙烯醇13克,纯水287克,4%固含量混合,浸泡15分钟,升温至95℃,达到95℃后开始计时,已获得每个实施例所得完全醇解聚乙烯醇的溶解时间,并且在聚乙烯醇完全溶解后继续保持95℃至1小时,得到聚乙烯醇的澄清水溶液;再降温至25摄氏度,用旋转粘度计ndj-1检测粘度。2、取原料皖维20-99片状聚乙烯醇采用同步骤1的方法溶解,区别在于溶解温度为100℃,持续时间为2小时,使其完全溶解。结果显示,原料皖维20-99片状聚乙烯醇溶解后溶液粘度实测38mpa.s,实施例1~7的改性聚乙烯醇溶解液实测38mpa.s,同样固含量,水溶液的粘度没有变化。上述步骤1中各实施例聚乙烯醇的完全溶解时间见下表。编号完全溶解时间实施例149min55s实施例246min13s实施例338min44s实施例434min32s实施例535min0s实施例630min22s实施例730min25s上述结果说明,改性的聚乙烯醇明显溶解时间要短于未改性的,且需要的溶解温度也有所降低;其中单独使用某一种偶联剂的效果不如两者联用,且进一步优化偶联剂配比后,能够在30分钟左右速溶。试验例2取实施例7的改性聚乙烯醇和原料安徽皖维20-99片状聚乙烯醇进行理化性质检测。1)分别称取10g上述产品,如图1a、1b所示,未改性的聚乙烯醇(图1左侧)为片状,而改性的聚乙烯醇为絮状,改性的聚乙烯醇(图1右侧)相较于未改性的体积膨胀了3~4倍。由于图片为灰度模式无法显示,实际上未改性的聚乙烯醇为淡黄色片状固体,而改性的聚乙烯醇为白色絮状固体。2)将称取的10g产品分别投入等体积的100ml常温水中。如图2a、2b所示,试验中可以看到,未改性的聚乙烯醇(图2左侧)迅速沉底,因此用户在溶解未改性的获取未改性的聚乙烯醇水溶液时,需要高强度高频率搅拌,使得片状聚乙烯醇不沉底,才能充分的溶胀,溶解,否则会有明显的塌锅,糊锅的现象发生。而改性的聚乙烯醇(图2右侧)呈絮状,均匀的悬浮在水里且有明显的自吸水现象,那么用户在溶解它时只需要低速搅拌或者不搅拌就能充分的溶胀、溶解,杜绝了塌锅,糊锅的现象,大量节约了搅拌所需要的能源消耗,并且充分自吸水后,会大量的节约溶解过程中蒸汽消耗。3)步骤2)中对改性的聚乙烯醇和水的混合物加温至100℃,试验观察到20分钟后溶液澄清,完全溶解。上述对比试验说明,改性的聚乙烯醇在密度上有所降低,吸水性有所增加,本发明方法先通过偶联剂处理聚乙烯醇,使其轻度偶联,再利用高温物理挤压使其体积膨胀1~3倍,从而改变聚乙烯醇的分子结构,增加其溶解度。本发明具体实施方式为了方便对照采用的均为应国标(100-40)片状聚乙烯醇,实际上基于同样的原理,其他标准的完全醇解聚乙烯醇也能够采用该方法进行改性处理,能够达到一样的增溶效果。当前第1页12