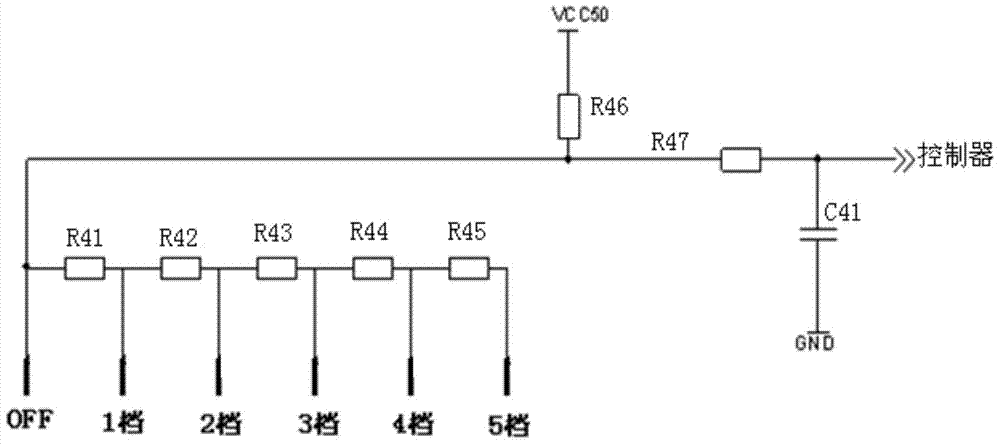
本发明涉及一种汽车空调控制系统,具体涉及一种用于小型乘用车上的一款空调控制系统,该系统具有操作简单,自动化程度高,可靠性强等优点。
背景技术:随着汽车工业和微电子技术的发展,汽车作为一种便捷的交通工具已进入千家万户,汽车空调的应用已越来越广泛。而人们对于车内乘车环境也越来越高。现代大小客车都要求有舒适的车内环境,主要是控制车内温度。而空调负荷随车内外环境、温度变化而变化,当汽车发动机作空调动力时,还要受车速变化的影响。因此,对汽车空调的控制是特别有意义的,也是十分重要的。传统的汽车空调系统包括控制器,电源模块,蒸发器温控传感器,压缩机,内外循环模式执行器,鼓风机,模式执行器,温度执行器,后除霜执行器,背景灯开关电路等;该系统通过控制器输出信号对内外循环模式、后除霜、压缩机进行控制。而对于鼓风机、模式执行器(模式电机)和温度执行器(冷暖电机),都是通过手动旋钮开关来进行操作,通过机械结构对鼓风机风速、模式电机的转动、冷暖电机的转动进行档位调整,该手动方式操作存在可靠性低,生产工艺复杂,一致性和舒适性差,控制不精确,调节滞后等问题。
技术实现要素:本发明要解决的技术问题是提供一种汽车空调控制系统,该系统采用可调电阻电路调节输入控制器的电压,从而使控制器根据采集的电压信号相应调整输出的控制信号,对冷暖电机进行档位控制,极大提高了空调系统的冷暖电机控制精度和使用效率;利用电机供电过流保护电路在电机短路情况下对控制系统进行保护,提高了系统的稳定性。为了解决上述技术问题,本发明的汽车空调控制系统包括控制器,电源模块,蒸发器温度传感器,内外循环模式执行器,压缩机,温度执行器,模式执行器,鼓风机;所述电源模块为整个控制系统供电,蒸发器温度传感器与控制器连接;控制器通过驱动芯片与内外循环模式执行器,压缩机,温度执行器,模式执行器连接,通过脉冲调速模块与鼓风机连接;其特征在于还包括温度调整信号采集电路;温度调整信号采集电路与控制器连接,用于采集温度调整信号;温度调整信号采集电路包括第一支路分压电阻,第一支路输出电阻,第一支路滤波电容,第二支路分压电阻,第二支路输出电阻,第二支路滤波电容,由多个电阻串联组成的温度调整分压变阻器;第一支路分压电阻与温度调整分压变阻器之间的电位通过第一支路输出电阻连接控制器,第一支路滤波电容连接在控制器输入端与电源地之间;第二支路分压电阻与温度调整分压变阻器之间的电位通过第二支路输出电阻连接控制器,第二支路滤波电容连接在控制器输入端与电源地之间。温度调整信号采集电路具有两个电压输出,当外部温度调整旋钮的金手指铜箔在不同档位输入端滑动时,温度调整信号采集电路输出的两个电压之间的差值发生变化,控制器根据该电压差值输出不同控制信号驱动温度执行器工作,以调整空调工作温度。温度在控制的过程中平稳变化,使能量利用率大大提高,达到了节能的目的,提了高舒适性,运转平稳。特别是温度调整信号采集电路中温度调整分压变阻器连接在两个分压支路电阻之间,当外部温度调整旋钮的金手指铜箔在不同档位输入端滑动时,控制器采集的电压一路减小,另一路增大,提高了两档位之间输入电压的差,从而进一步提高了温度控制精度。进一步,本发明还包括电机供电过流保护电路;所述电机供电过流保护电路包括由第一、第二过流保护三极管、第一电阻、第二电阻组成的过流保护电路,保险丝,由开关管和第三、第四、第五电阻组成的开关电路,由第六、第七、第八电阻组成的电压反馈电路,输出滤波电容;第一、第二过流保护三极管为PNP型三极管,开关管为NPN型三极管;电源模块的输出通过第一电阻连接第二过流保护三极管的发射极,第二过流保护三极管的集电极通过保险丝连接控制系统中的各执行器,通过第一电阻、第二过流保护三极管为各执行器供电;第一过流保护三极管的基极接第二过流保护三极管的发射极,发射极接电源模块的输出,集电极接第二过流保护三极管的基极;第二电阻跨接在第一过流保护三极管的发射极与集电极之间;第二过流保护三极管的基极通过第五电阻和开关管接地;开关管的基极通过电阻接控制器输出,第四电阻连接在开关管的基极与地之间;第六、第八电阻串接在电机供电过流保护电路的输出与地之间,第六、第八电阻之间的电位通过第七电阻接控制器的输入;输出滤波电容连接在电机供电过流保护电路的输出与地之间。电机供电过流保护电路中由第一电阻、第二电阻、第一过流保护三极管、第二过流保护三极管构成过流保护电路,当电机对地短路时,能够起到过流保护作用。保险丝也是起到过流保护的作用,它的反应速度比三极管快,当瞬间电流很大时,就会熔断,对整个电流起到保护作用。控制器通过第七电阻采集反馈电压,对输出给执行器的电压进行监测,若输出电压较大时,说明电路正常工作;当输出电压很小时,说明电路短路,控制器输出低电平控制开关管关闭,隔一段时间再打开开关管,再对电压进行监测,直到输出电压正常。提高了系统的稳定性。本发明还包括风量调节信号采集电路;所述风量调节信号采集电路包括风量调节分压电阻和由多个电组串联组成的风量调节分压变阻器,风量调节输出端电阻及滤波电容;风量调节分压电阻与风量调节分压变阻器之间的电位通过风量调节输出端电阻连接控制器;滤波电容连接在控制器输入端与电源地之间。风量调节分压变阻器中各电阻之间的具有档位信号输入端,当外部风量旋钮的金手指铜箔在不同档位输入端滑动时,风量调节信号采集电路输出的电压不同,控制器根据该电压输出不同占空比的PWM信号,以调整输出风量的大小,提高了空调系统的风量控制精度和使用效率。本发明还包括模式调整信号采集电路;所述模式调整信号采集电路包括模式调整分压电阻、模式调整分压变阻器、模式调整输出端电阻及滤波电容;模式调整分压电阻与模式调整分压变阻器之间的电位通过模式调整输出端电阻连接控制器;滤波电容连接在控制器输入端与电源地之间。模式调整分压变阻器中各电阻之间的具有档位信号输入端,当外部模式旋钮的金手指铜箔在不同档位输入端滑动时,模式调整信号采集电路输出的电压不同,控制器根据该电压输出不同控制信号,使模式执行器分别工作在吹脸、吹脸吹脚、吹脚、吹脚除霜、除霜模式;温度调整分压变阻器中各电阻之间的具有档位信号输入端。模式调整信号采集电路采集外部控制旋钮的位置信号并将其转换为电压信号,使得控制器能够根据输入的信号电压输出不同控制信号,以调整模式执行器工作模式,提高了空调系统的控制精度和使用效率。所述电源模块包括两个在电路板上垂直放置的滤波电容,快恢复二极管,瞬态抑制二极管,小容值陶瓷电容,大容值电解电容,稳压器,陶瓷滤波电容,电解滤波电容;所述快恢复二极管正向连接于直流电源的正极与稳压器的输入之间,稳压器的输出接控制器;两个滤波电容串联在直流电源BAT的正极与电源地之间;瞬态抑制二极管反向连接于稳压器的输入与地之间;小容值陶瓷电容和大容值电解电容并联构成的滤波电路连接于稳压器的输入Vin与电源地之间,陶瓷滤波电容与电解滤波电容并联构成的滤波电路连接于稳压器的输出Vout与电源地之间。电源模块采用两个垂直放置的滤波电容防止静电,可以防止应力,避免两个电容同时损坏。快恢复二极管正向连接于直流电源正极与稳压器输入之间,可以防止电源接反,保护控制器,在直流电源接反的情况下也不会被烧坏。瞬态抑制二极管反向连接于稳压器的输入与电源地之间,能够防止控制器因瞬间的脉冲损坏。在两个滤波电路中,采用大容值的电解电容滤除高频信号,用小容值的陶瓷电容保护大容值的电解电容,能够防止其在高频下发热。稳压器采用一个DCDC电压转换芯片,能够将不稳定的输入电压转换成稳定的输出电压。整个电源模块为控制器和各执行器提供非常稳定的输出电压。所述稳压器LDC采用一个可编程的小功率DCDC电路,该电路包括输入端滤波电容,电感,DCDC稳压芯片,二极管,由反馈电阻和可编程电阻构成的反馈电路,反馈电路滤波电容,输出端滤波电容;电感和二极管串接在整个稳压器的输入端和输出端之间,二极管正向连接在电感和稳压器输出端之间;滤波电容连接在稳压器输入与电源地之间;整个稳压器的输出端通过相互并联的导线与反馈电路滤波电容连接到反馈电阻,反馈电阻的另一端通过可编程反馈电阻接电源地;DCDC稳压芯片的电压输入端Vin连接到稳压器的输入端,开关信号输入端SW连接在二极管的正极,反馈信号输入端连接在反馈电阻与可编程电阻之间;输出端滤波电容连接在稳压器输出端与电源地之间。所述可编程电阻采用可编程电阻器AD5245,通过改变其电阻可精确控制输出电压。所述脉冲调速模块包括第一级放大器、第二级放大器、滤波网络、反馈电路;所述第一级放大器和第二级放大器构成PI控制器,滤波网络包括两个电阻和滤波;反馈电路包括串接在一起的反馈电阻和反馈电容;控制器的PWM信号输出端通过滤波网络与第二级放大器的正相输入端连接,第二级放大器的输出端通过反馈电阻和反馈电容连接到第一级放大器的正相输入端、电源模块的输出及鼓风机,第一级放大器的反相输入端连接到鼓风机的反馈信号输出端,第一级放大器的输出连接到第二级放大器的反相输入端。控制器输出不同占空比的PWM控制信号,该PWM控制信号经过脉冲调速模块输出至鼓风机,对鼓风机进行PI控制,以调整输出风量的大小。附图说明下面结合附图和具体实施方式对本发明作进一步详细说明。图1为本发明的汽车空调控制系统结构框图;图2为风量调节信号采集电路图;图3为模式调整信号采集电路图;图4为温度调节信号采集电路图;图5为电源模块电路图;图6为稳压器LDC电路图;图7为电机供电过流保护电路;图8为脉冲调试模块电路图。具体实施方式如图1所示,本发明的汽车空调控制系统包括控制器,电源模块,蒸发器温度传感器,内外循环模式执行器,压缩机,温度执行器,模式执行器,鼓风机;其特征在于还包括风量调节信号采集电路,模式调整信号采集电路,温度调整信号采集电路,电机供电过流保护电路;所述电源模块为整个控制系统供电;蒸发器温度传感器、风量调节信号采集电路、模式调整信号采集电路和温度调整信号采集电路与控制器连接,用于采集蒸发器温度、风量调节信号、模式调整信号和温度调整信号;控制器通过驱动芯片与内外循环模式执行器,压缩机,温度执行器,模式执行器连接,通过脉冲调速模块与鼓风机连接;电源模块与控制器连接,并通过电机供电过流保护电路与内外循环模式执行器、压缩机、温度执行器、模式执行器、鼓风机连接。其中蒸发器温控传感器温度采集,压缩机控制,以及内外循环模式控制均为已有技术,这里不再累述。如图2所示,所述风量调节信号采集电路包括风量调节分压电阻R46,风量调节分压变阻器,风量调节输出端电阻R47及滤波电容C41;风量调节分压变阻器由电阻R41、R42、R43、R44、R45串联组成;风量调节分压电阻R46与风量调节分压变阻器之间的电位通过风量调节输出端电阻R47连接控制器。风量调节分压变阻器中各电阻之间的具有档位信号输入端,当外部风量旋钮的金手指铜箔在不同档位输入端滑动时,分压电阻不同,导致风量调节信号采集电路输出的电压不同,控制器根据该电压输出不同占空比的PWM信号,通过脉冲调速模块控制鼓风机使其调整输出风量的大小。如图3所示,所述模式调整信号采集电路包括模式调整分压电阻R51,模式调整分压变阻器,模式调整输出端电阻R52及滤波电容C51;模式调整分压变阻器由电阻R53、R54、R55、R56串联组成;模式调整分压电阻R51与模式调整分压变阻器之间的电位通过模式调整输出端电阻R52连接控制器。模式调整分压变阻器中各电阻之间的具有档位信号输入端,当外部模式旋钮的金手指铜箔在不同档位输入端滑动时,分压电阻不同,导致模式调整信号采集电路输出的电压不同,控制器根据该电压输出不同控制信号,通过驱动芯片驱动模式执行器使其分别工作在吹脸、吹脸吹脚、吹脚、吹脚除霜、除霜模式。如图4所示,温度调整信号采集电路包括第一支路分压电阻R61,第一支路输出电阻R62,第一支路滤波电容C61,第二支路分压电阻R64,第二支路输出电阻R63,第二支路滤波电容C62,温度调整分压变阻器;所述温度调整分压变阻器由n个电阻R601、R602、R603……R60n串联组成;第一支路分压电阻R61与温度调整分压变阻器之间的电位通过第一支路输出电阻R62连接控制器;第二支路分压电阻R64与温度调整分压变阻器之间的电位通过第二支路输出电阻R63连接控制器。温度调整分压变阻器中各电阻之间的具有档位信号输入端。温度调整信号采集电路具有两个电压输出,控制器根据该两个电压之间的差值输出控制信号,通过驱动芯片驱动温度执行器工作。当外部温度调整旋钮的金手指铜箔在不同档位输入端滑动时,温度调整信号采集电路输出的两个电压之间的差值发生变化,控制器根据该电压差值输出不同控制信号驱动温度执行器工作,以调整空调工作温度。如图5所示,电源模块包括两个在电路板上垂直放置的滤波电容C11和C12,快恢复二极管D11,瞬态抑制二极管D12,小容值陶瓷电容C13,大容值电解电容C14,稳压器LDO,陶瓷滤波电容C15,电解滤波电容C16;所述快恢复二极管D11正向连接于直流电源BAT的正极与稳压器LDO的输入之间,稳压器LDO的输出接控制器;滤波电容C11和C12串联在直流电源BAT的正极与电源地之间;瞬态抑制二极管D12反向连接于稳压器LDO的输入与地之间;小容值陶瓷电容C13和大容值电解电容C14并联构成的滤波电路连接于稳压器LDO的输入Vin与电源地之间,陶瓷滤波电容C15与电解滤波电容C16并联构成的滤波电路连接于稳压器LDO的输出Vout与电源地之间。外部直流电源BAT输入的12V~24V电压,经过两个垂直放置的滤波电容C11和C12,起到防止静电的作用,两个滤波电容C11和C12在电路板上垂直摆放,可以防止应力,避免两个电容同时损坏。快恢复二极管D11正向连接于直流电源BAT正极与稳压器LDO输入之间,可以防止电源接反,保护控制器,在直流电源BAT接反的情况下也不会被烧坏。瞬态抑制二极管D12反向连接于稳压器LDO的输入与电源地之间,当瞬时电压超过电路正常工作电压后,瞬态抑制二极管D12便产生雪崩,提供给瞬时电流一个超低电阻通路,其结果是瞬时电流通过二极管被引开,并且在电压恢复正常值之前使被保护回路一直保持截止电压。当瞬时脉冲结束以后,瞬态抑制二极管D12自动回复高阻状态,整个回路进入正常电压,从而防止控制器因瞬间的脉冲损坏。小容值陶瓷电容C13和大容值电解电容C14并联构成的滤波电路中,大容值电解电容C14的作用是滤除高频信号,小容值陶瓷电容C13用于保护大容值电解电容C14,防止其在高频下发热。稳压器LDO采用一个DCDC电压转换芯片,其主要功能是提供稳压,即能够将不稳定的输入电压转换成稳定的输出电压,输出电压不随输入电压或输出电流的变化而改变。在陶瓷滤波电容C15与电解滤波电容C16构成的滤波电路中,电解滤波电容C16的作用是滤除高频信号,陶瓷滤波电容C15用于保护电解滤波电容C16,防止其在高频下发热。整个电源模块为控制器和各执行器提供非常稳定的输出电压。如图6所示,所述LDC电路采用一个可编程的小功率DCDC电路,该电路包括输入端滤波电容C21,电感L21,DCDC稳压芯片,二极管D21,由反馈电阻R21和可编程电阻R22构成的反馈电路,反馈电路滤波电容C23,输出端滤波电容C22;电感L21和二极管D21串接在整个LDC电路的输入端和输出端之间,二极管D21正向连接在电感L21和LDC输出端之间;滤波电容C21连接在LDC输入与电源地之间;整个LDC电路的输出端通过相互并联的导线与反馈电路滤波电容C23连接到反馈电阻R21,反馈电阻R21的另一端通过可编程反馈电阻R22接电源地;DCDC稳压芯片的电压输入端Vin连接到LDC电路的输入端,开关信号输入端SW连接在二极管L21的正极,反馈信号输入端连接在反馈电阻R21与可编程电阻R22之间;输出端滤波电容C22连接在LDC输出端与电源地之间。稳压器LDC的输入电压Vin经过电容C21滤波,再经过DCDC稳压芯片后,得到一个输出电压,通过反馈电阻R21和可编程反馈电阻R22反馈给DCDC稳压芯片,从而达到控制输出电压Vout的目的。所述可编程电阻R22采用可编程电阻器AD5245,通过改变其电阻可精确控制输出电压。如图7所示,所述电机供电过流保护电路包括由第一、第二过流保护三极管Q31、Q32、第一电阻R31、第二电阻R32组成的过流保护电路,保险丝F31,由开关管Q33和第三、第四、第五电阻R33、R34、R35组成的开关电路,由第六、第七、第八电阻R36、R37、R38组成的电压反馈电路,输出滤波电容C37;第一、第二过流保护三极管Q31、Q32为PNP型三极管,开关Q33为NPN型三极管;LDC电路的输出通过第一电阻R31连接第二过流保护三极管Q32的发射极,第二过流保护三极管Q32的集电极通过保险丝F31连接控制系统中的各执行器,通过第一电阻R31、第二过流保护三极管Q32为各执行器(电机)供电;第一过流保护三极管Q31的基极接第二过流保护三极管Q32的发射极,发射极接LDC电路的输出,集电极接第二过流保护三极管Q32的基极;第二电阻R32跨接在第一过流保护三极管Q31的发射极与集电极之间;第二过流保护三极管Q32的基极通过第五电阻R35和开关管Q33接地;开关管Q33的基极通过电阻R33接控制器输出,第四电阻R34连接在开关管Q33的基极与地之间;第六、第八电阻R36、R38串接在电机供电过流保护电路的输出与地之间,第六、第八电阻R36、R38之间的电位通过第七电阻R37接控制器的输入。输出滤波电容C37连接在电机供电过流保护电路的输出与地之间。当电机对地短路时,流过第一电阻R31的电流瞬间增大,使得加载在第一电阻R31两端的电压超过第一过流保护三极管Q31的开启电压。此时,第一过流保护三极管Q31打开,第二过流保护三极管Q32的基极电压接近于稳压器LDC的输出电压,第二过流保护三极管Q32打开;随后第二过流保护三极管Q32因其基极与发射极之间电压降至低于开启电压而关闭,由此起到过流保护作用。保险丝F31也是起到过流保护的作用,它的反应速度比三极管快,当瞬间电流很大时,就会熔断,对整个电流起到保护作用。当控制器通过I/O口输出高电平信号给开关管Q33时,开关管Q33接通,稳压器LDC输出电压经过过流保护电路和保险丝F31提供给各执行器。当控制器输出低电平时,关闭开关管Q33,稳压器LDC无输出。控制器通过第七电阻R37采集反馈电压,对输出给执行器的电压进行监测,若输出电压较大时,说明电路正常工作;当输出电压很小时,说明电路短路,控制器输出低电平控制开关管Q33关闭,隔一段时间再打开开关管Q33,再对电压进行监测,直到输出电压正常。如图8所示,所述脉冲调速模块包括第一级放大器、第二级放大器、滤波网络、反馈电路;所述第一级放大器和第二级放大器构成PI控制器,滤波网络包括电阻R706、R702和滤波C701;反馈电路包括串接在一起的反馈电阻R703和反馈电容C702;控制器的PWM信号输出端通过滤波网络与第二级放大器的正相输入端连接,第二级放大器的输出端通过反馈电阻R703和反馈电容C702连接到第一级放大器的正相输入端、电源模块的输出及鼓风机,第一级放大器的反相输入端连接到鼓风机的反馈信号输出端,第一级放大器的输出连接到第二级放大器的反相输入端。控制器输出不同占空比的PWM控制信号,该PWM控制信号经过脉冲调速模块输出至鼓风机,对鼓风机进行PI控制,以调整输出风量的大小。