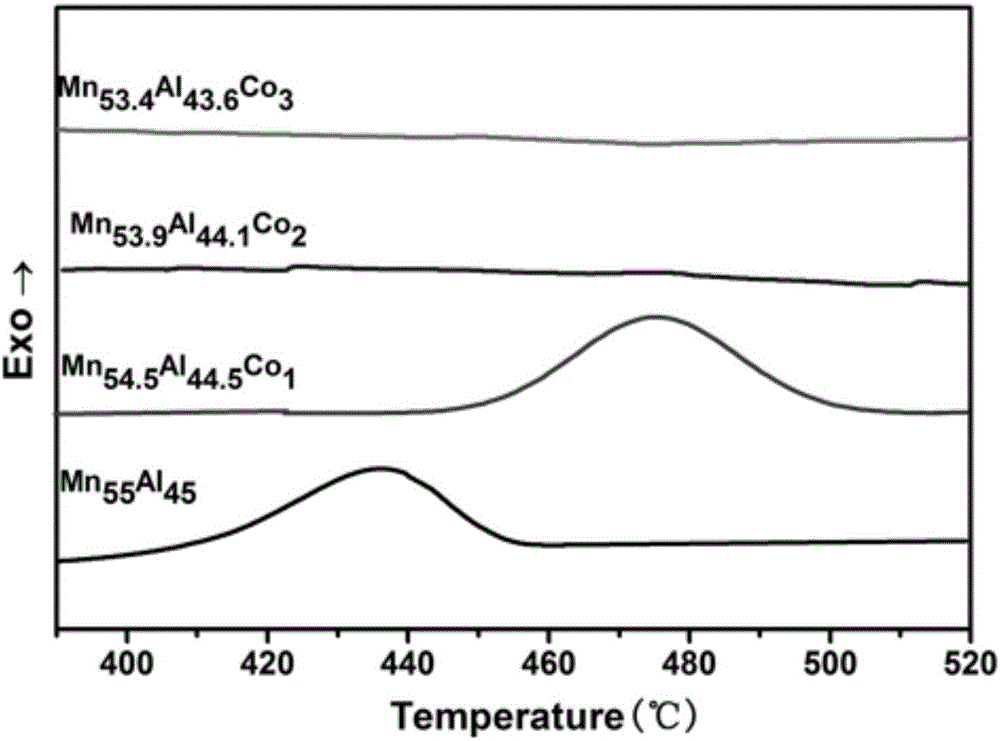
本发明涉一种磁性材料的制备方法,尤其是涉及一种MnAl合金磁性材料及其制备方法。
背景技术:随着磁性材料的发展,传统的稀土系永磁以其无以伦比的优异磁性能在磁性材料的研究与应用中占据了主导地位。当然其本身也存在一系列的问题,如烧结Nd2Fe14B永磁体在使用时存在明显的晶界腐蚀,而Sm-Co系永磁体在服役过程中脆性太大等,而目前限制稀土永磁的最大因素则是稀土资源的制约。此外在实际应用中也并非所有服役环境下都对永磁材料的性能要求十分苛刻,如果在这些服役条件下用无稀土永磁材料替代稀土系永磁则具有十分重要的现实意义。近年来新型无稀土永磁的研究与开发已成为磁性材料领域的研究热点。Mn基硬磁是无稀土永磁材料的一个重要分支,其中MnAl体系因其低密度、耐腐蚀、易成型且综合磁性能良好的特点使其成为极具前景的无稀土永磁材料。然而为使MnAl合金展现其优异的硬磁性能首先要解决磁性τ相的有序化转变问题。MnAl合金中的磁性相是一个亚稳相,通常是从高温的ε相冷却及后续退火得到。由Mn-Al合金二元相图可知,磁性相的母相ε利用传统工艺很难获得,因此磁性τ相的制备工艺也比较复杂。目前关于τ相的制备最常见的方法是先急冷后退火,其中急冷工艺可选择雾化法、熔体快淬法等,如国外学者Lee,Pasko等分别采用不同急冷工艺对磁性τ相进行研究。但是就其实验结果而言这些复杂工艺也并不能易得到较纯的磁性相。国内关于MnAl磁性相制备工艺的报道也大致如此。如胡元虎等(一种制造锰铝硬磁合金的方法,中国发明专利,CN101684527A,2010.03.31)其制备包括母合金熔炼、熔体快淬、薄带破碎、热加工等多步工艺,且物相图谱显示其最终的磁性τ相并不是很纯。凌敏等(一种无稀土MnAl永磁合金的制备方法,中国发明专利,CN104593625A,2015.01.06)通过熔体快淬以及后续的热处理在MnAl合金中获得了较纯的磁性相,但实际操作过程中探究最佳热处理工艺比较繁琐,且长时间的热处理对生产周期也有一定的影响。
技术实现要素:本发明的目的就是为了克服上述现有技术存在的缺陷而提供一种MnAl合金磁性材料及其制备方法。本发明的目的可以通过以下技术方案来实现:本发明第一方面提供一种MnAl合金磁性材料的制备方法,包括以下步骤:(1)母合金的原料配比与制备:将纯度为99.95%的锰、铝、钴按名义分子式(Mn0.55Al0.45)xCoy进行配比作为母合金的原料,其中0<y<3,x=100-y,将合金材料进行熔炼后随炉冷却最终得到成分均匀的(Mn0.55Al0.45)xCoy母合金铸锭;熔炼时采用电弧熔炼炉,熔炼的条件为:600mbar氩气气氛条件下正反熔炼4-6次。(2)母合金铸锭的快淬前预处理:将熔炼后得到的母合金铸锭破碎,清洗表面杂质,并烘干处理,得到破碎块体合金;具体方法为:具体方法为:将熔炼后得到的母合金铸锭用砂轮打磨以去除表层的氧化皮,然后对其进行机械破碎获得黄豆大小的块状合金,再将破碎后的合金交替放入酒精和丙酮中进行超声波清洗去除表面的杂质,最后取出烘干。(3)母合金铸锭的熔体快淬:将步骤(2)中得到的破碎块体合金放入石英管中,在真空条件下,在保护气氛下进行熔融处理,并使熔融态合金制成MnAl合金磁性薄带。母合金铸锭的熔体快淬具体方法如下:将步骤(2)中得到的破碎块体合金放入石英管中,同时保证铜辊表面光洁平整,熔体快淬设备腔体真空抽至10-3Pa以下后冲入50-100Pa保护气进行洗气,之后关闭真空阀再次冲入保护气维持气压0.6-0.8MPa,调节铜辊的线速度至30-40m/s,待转速稳定后调节感应电流,当合金恰好完全熔融时打开氩气阀使熔融态合金流到快速旋转的铜辊上,最终得到(Mn0.55Al0.45)xCoy体系的合金薄带。所述的保护气为氩气。对熔体快淬薄带进行研磨,利用X射线衍射仪检测其物相,扫描电子显微观察其表面形貌,磁性能利用振动样品磁强计检测。本发明另一方面提供:上述制备方法所制备的MnAl合金磁性材料。本发明通过研究发现钴元素的引进可以调控MnAl合金的相变过程。在(Mn0.55Al0.45)xCoy合金熔体急冷过程中,熔体会直接向亚稳磁性τ相转变,从而避免了MnAl二元合金体系中ε→ε’→τ的相变过程。这种转变将大大简化磁性相的制备工艺,可以明显缩短MnAl永磁材料的制备周期。同时研究表明Co的加入只有处在适当的范围才有利于熔体快淬时获得磁性相,其含量过少过多都不会出现τ相。当Co原子含量低于1%时,快淬合金薄带仍为高温母相ε相;而当Co原子含量高于3%时,MnAl合金体系将出现新的杂相进而不利于材料磁性能的提升。与现有技术相比,本发明主要利用Co元素掺杂改变合金体系热容,使其在熔体冷却时越过高温ε相区,直接进入亚稳磁性相区,从而在快淬薄带中直接出现磁性τ相。与传统的熔体快淬后续退火或机械合金化工艺相比,大大简化了操作流程。附图说明图1为(Mn0.55Al0.45)xCoy与Mn55Al45的快淬合金薄带物相对比图谱;图2为(Mn0.55Al0.45)xCoy与Mn55Al45的DSC曲线对比图;图3为Mn54.5Al44.5Co3快淬薄带的表面微观形貌图像;图4为Mn54.5Al44.5Co3快淬合金薄带的磁滞回线。具体实施方式下面结合附图和具体实施例对本发明进行详细说明。实施例1:将纯度为99.95%的锰、铝、钴按名义分子式Mn54.5Al44.5Co1进行配比作为母合金的原料。熔炼时采用电弧熔炼炉,原料在600mbar氩气气氛条件下正反熔炼3次后随炉冷却最终得到成分均匀的Mn54.5Al44.5Co1母合金铸锭。将熔炼后得到的母合金铸锭用砂轮打磨以去除表层的氧化皮,然后对其进行机械破碎获得黄豆大小的块状合金以便于在石英管中进行熔体快淬。在快淬前还把破碎后的合金交替放入酒精和丙酮中进行超声波清洗去除表面的杂质,最后取出烘干。将预处理后得到破碎块体合金放入石英管中,同时保证铜辊表面光洁平整。熔体快淬设备腔体真空抽至10-3Pa以下后充入氩气进行洗气,之后关闭真空阀再次冲入氩气维持气压0.6MPa左右。调节铜辊的线速度至35m/s,待转速稳定后调节感应电流,当合金恰好完全熔融时打开氩气阀使熔融态合金流到快速旋转的铜辊上,最终得到Mn54.5Al44.5Co1体系的合金薄带。从图1中Mn54.5Al44.5Co1与Mn55Al45的快淬合金薄带物相对比图谱可以看出该成分下的合金薄带物相并未出现磁性τ相,与未掺杂的Mn55Al45合金薄带物相一致,都为高温母相ε相。图2中的DSC曲线进一步表明其在470℃发生相变,即ε相转化为τ相。实施例2:将纯度为99.95%的锰、铝、钴按名义分子式Mn53.9Al44.1Co2进行配比作为母合金的原料。熔炼时采用电弧熔炼炉,原料在600mbar氩气气氛真空条件下正反熔炼3次后随炉冷却最终得到成分均匀的Mn53.9Al44.1Co2母合金铸锭。将熔炼后得到的母合金铸锭用砂轮打磨以去除表层的氧化皮,然后对其进行机械破碎获得黄豆大小的块状合金以便于在石英管中进行熔体快淬。在快淬前还把破碎后的合金交替放入酒精和丙酮中进行超声波清洗去除表面的杂质,最后取出烘干。将预处理后得到破碎块体合金放入石英管中,同时保证铜辊表面光洁平整。熔体快淬设备腔体真空抽至10-3Pa以下后充入氩气进行洗气,之后关闭真空阀再次冲入氩气维持气压0.6MPa左右。调节铜辊的线速度至35m/s,待转速稳定后调节感应电流,当合金恰好完全熔融时打开氩气阀使熔融态合金流到快速旋转的铜辊上,最终得到Mn53.9Al44.1Co2体系的合金薄带。从图1中Mn53.9Al44.1Co2与Mn55Al45的快淬合金薄带物相对比图谱可以看出该成分下的合金薄带物相已出现部分磁性τ相,而未掺杂的Mn55Al45合金薄带则全为高温母相ε相。图2中的DSC曲线已不存在明显的放热峰,也表明合金薄带中母相含量大量减少。实施例3:将纯度为99.95%的锰、铝、钴按名义分子式Mn53.4Al43.6Co3进行配比作为母合金的原料。熔炼时采用电弧熔炼炉,原料在600mbar氩气气氛条件下正反熔炼3次后随炉冷却最终得到成分均匀的Mn53.4Al43.6Co3母合金铸锭。将熔炼后得到的母合金铸锭用砂轮打磨以去除表层的氧化皮,然后对其进行机械破碎获得黄豆大小的块状合金以便于在石英管中进行熔体快淬。在快淬前还应把破碎后的合金交替放入酒精和丙酮中进行超声波清洗去除表面的杂质,最后取出烘干。将预处理后得到破碎块体合金放入石英管中,同时保证铜辊表面光洁平整。熔体快淬设备腔体真空抽至10-3Pa以下后冲入氩气进行洗气,之后关闭真空阀再次冲入氩气维持气压0.6MPa左右。调节铜辊的线速度至35m/s,待转速稳定后调节感应电流,当合金恰好完全熔融时打开氩气阀使熔融态合金流到快速旋转的铜辊上,最终得到Mn53.4Al43.6Co3体系的合金薄带。从图1中Mn53.4Al43.6Co3与Mn55Al45的快淬合金薄带物相对比图谱可以看出该成分下的合金薄带物相已全部转化为磁性τ相,而未掺杂的Mn55Al45合金薄带则全为高温母相ε相。图2中的DSC曲线已变为一条平滑的直线,表明母相已基本消失,此时合金薄带几乎全为磁性相。图3是快淬合金薄带的表面微观形貌图像。图4是快淬合金薄带的磁滞回线。上述的对实施例的描述是为便于该技术领域的普通技术人员能理解和使用发明。熟悉本领域技术的人员显然可以容易地对这些实施例做出各种修改,并把在此说明的一般原理应用到其他实施例中而不必经过创造性的劳动。因此,本发明不限于上述实施例,本领域技术人员根据本发明的揭示,不脱离本发明范畴所做出的改进和修改都应该在本发明的保护范围之内。