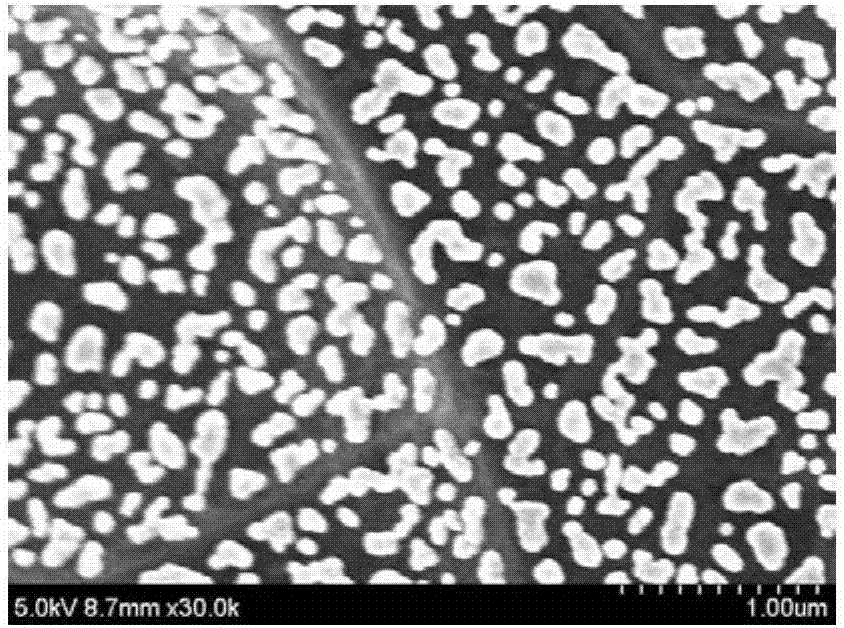
本发明涉及一种晶体硅太阳能电池的绒面结构的制备方法,属于太阳能电池技术领域。
背景技术:随着太阳能电池组件的广泛应用,光伏发电在新能源中越来越占有重要比例,获得了飞速发展。目前商业化的太阳电池产品中,晶体硅(单晶和多晶)太阳电池的市场份额最大,一直保持85%以上的市场占有率。目前,在太阳电池的生产工艺中,硅片表面的绒面结构可以有效地降低太阳电池的表面反射率,是影响太阳电池光电转换效率的重要因素之一。为了在晶体硅太阳能电池表面获得好的绒面结构,以达到较好的减反射效果,人们尝试了许多方法,常用的包括机械刻槽法、激光刻蚀法、反应离子刻蚀法(RIE)、化学腐蚀法(即湿法腐蚀)等。其中,机械刻槽方法可以得到较低的表面反射率,但是该方法造成硅片表面的机械损伤比较严重,而且其成品率相对较低,故而在工业生产中使用较少。对于激光刻蚀法,是用激光制作不同的刻槽花样,条纹状和倒金字塔形状的表面都已经被制作出来,其反射率可以低至8.3%,但是由其制得的电池的效率都比较低,不能有效地用于生产。RIE方法可以利用不同的模版来进行刻蚀,刻蚀一般是干法刻蚀,可以在硅片表面形成所谓的“黑硅”结构,其反射率可以低至7.9%,甚至可以达到4%,但是由于设备昂贵,生产成本较高,因此在工业成产中使用较少。而化学腐蚀法具有工艺简单、廉价优质、和现有工艺好兼容等特点,成为了现有工业中使用最多的方法。目前,采用湿法腐蚀的晶体硅太阳能电池的绒面结构一般呈微米级。目前的常规做法仍是进一步降低其表面反射率。发明专利申请WO2014120830(A1)公开了一种晶体硅纳米绒面的制备方法,通过退火的方式来实现纳米绒面形貌的控制,但是该方法工艺复杂,不利于工业化生产的需要。此外,现有技术中还出现了金属离子腐蚀的方法,比如中国专利CN101573801B,具体包括如下步骤:(1)将硅片放入含有氧化剂以及金属盐的氢氟酸溶液中,形成多孔质层结构;(2)然后用第一化学腐蚀液进行表面刻蚀;所述第一化学腐蚀液为氢氟酸和硝酸的混合溶液;(3)然后将上述硅片放入第二化学腐蚀液中进行浸渍,形成绒面结构;所述第二化学腐蚀液为碱液。其中,步骤(1)亦可以分成2步,即先将硅片放入含有金属离子的溶液中浸泡,使硅片表面涂覆一层金属纳米颗粒,然后再用化学腐蚀液腐蚀硅片表面,形成多孔质层结构。然而,实际应用中发现,上述方法存在如下问题:当溶液中的金属离子的浓度较低时,附着的金属纳米颗粒大小不均,不同位置附着的密度差异也较大,从而导致制备的纳米微结构大小不均,开口迥异,最终导致较低的电性能。因此,开发一种新的晶体硅太阳能电池的绒面结构的制备方法,以保障绒面结构的稳定性和均匀性、并进一步提高电池片的光电转化效率,显然具有积极的现实意义。
技术实现要素:本发明的发明目的是提供一种晶体硅太阳能电池的绒面结构的制备方法。为达到上述发明目的,本发明采用的技术方案是:一种晶体硅太阳能电池的绒面结构的制备方法,包括如下步骤:(1)将硅片放入含有金属离子的溶液中浸泡,使硅片表面涂覆一层金属纳米颗粒;(2)使上述步骤(1)中硅片表面涂覆的金属纳米颗粒形成团簇;(3)用第一化学腐蚀液腐蚀硅片表面,形成多孔质层结构;所述第一化学腐蚀液为HF和氧化剂的混合溶液;即可得到晶体硅太阳能电池的绒面结构。上文中,所述步骤(2)中金属纳米颗粒团簇是指金属纳米颗粒团聚变大;通常情况下,使用的金属纳米颗粒大小为100nm以下,团聚后形成50~500nm的金属纳米颗粒。上述技术方案中,将步骤(1)中的溶液进行加热,使硅片表面涂覆的金属纳米颗粒形成团簇;或者,将步骤(1)中的表面涂覆有金属纳米颗粒的硅片置于惰性气体气氛中加热使硅片表面涂覆的金属纳米颗粒形成团簇。所述步骤(2)包含2种并列的方法,一是直接加热含有金属离子的溶液,使溶液温度保持在50~1000℃,并持续5~500秒;优选的,使溶液温度保持在500~800℃,并持续10~100秒;更优选的,使溶液温度保持在550~650℃,并持续25~60秒。第二种方法是直接加热硅片,即将硅片置于惰性气体气氛中加热处理5~500秒,惰性气体气氛的温度为50~1000℃;优选的,使惰性气体气氛的温度保持在200~500℃,并持续10~100秒;更优选的,使惰性气体气氛的温度保持在250~350℃,并持续25~60秒。所述惰性气体气氛可以是氩气气氛、氦气气氛等等。优选的,所述步骤(2)中,采用油浴的加热方法使溶液温度保持在50~1000℃。也可以在含有金属离子的溶液中直接设置电热丝等加热设备,直接加热该溶液。优选的,所述步骤(2)中,采用红外加热方法使惰性气体气氛的温度达到50~1000℃。当然,加热惰性气体气氛的方法有很多,除了上述红外加热方法,还可以采用电加热的方法等。上文中,所述金属离子可从现有技术的金属离子中选用,比如金、银、铜、镍中的一种或几种。上文中,所述多孔质层结构包括多孔硅结构、纳米线结构等。优选的,所述步骤(1)中含有金属离子的溶液中还包含HF。优选的,所述步骤(1)中,所述溶液中金属离子浓度小于等于1E-3mol/L,或者,溶液中金属离子浓度大于1E-3mol/L的同时HF的浓度小于等于1E-2mol/L。这是为了使相邻两个金属纳米颗粒的间距大于纳米颗粒尺寸的2倍。从而形成上述类似倒金字塔的微结构。上述技术方案中,所述步骤(3)中,所述第一化学腐蚀液中,HF的浓度为1~15mol/L,氧化剂的浓度为0.05~0.5mol/L,腐蚀温度为25~90℃,时间为1~10min。所述氧化剂可以是硝酸、双氧水、铬酸或高锰酸钾溶液。上述技术方案中,所述步骤(3)之后,还包括如下步骤:(4)采用第一清洗液去除残留金属颗粒;所述第一清洗液选自以下4种溶液中的一种:盐酸和双氧水的混合液、氨水和双氧水的混合液、硝酸、氨水;所述硝酸的质量浓度为5~69%;所述氨水的体积浓度为1~30%;所述第一清洗液的温度为20~80℃;(5)然后用第二化学腐蚀液进行表面刻蚀;所述第二化学腐蚀液为氢氟酸和硝酸,其中氢氟酸的浓度为1~15mol/L,硝酸的浓度为0.05~0.5mol/L;或者所述第二化学腐蚀液为碱液,所述碱液选自氢氧化钠溶液、氢氧化钾溶液、氨水或四甲基氢氧化铵的任意一种或多种;(6)然后将上述硅片放入第二清洗液中进行清洗;所述第二清洗液为盐酸和双氧水的混合液、氨水和双氧水的混合液中的任意一种混合液;(7)然后将上述硅片放入氢氟酸溶液中浸渍。上述技术方案中,步骤(5)的作用是用来去除表面多孔硅,步骤(6)去除残留的金属粒子,步骤(7)去除表层氧化硅层,实际的方案可以根据具体的需求进行选择。优选的,所述步骤(5)、(6)、(7)之前以及步骤(7)之后,还均设有水洗步骤。本发明同时请求保护由上述方法制备得到的晶体硅太阳能电池的绒面结构。本发明的工作原理是:通过新增的步骤(2)的加热处理,使金属纳米颗粒形成团簇,且通过调整加热温度和持续时间来调整金属纳米颗粒团簇的形状和大小,有利于纳米微结构形貌的控制;本发明制备的纳米微结构开口较大(本发明微结构的尺寸为400~800nm,现有技术为200~300nm),有利于纳米微结构表面的钝化;此外,本发明制备的微结构整齐且均匀性好。由于上述技术方案运用,本发明与现有技术相比具有下列优点:1、本发明开发了一种新的晶体硅太阳能电池的绒面结构的制备方法,通过新增的步骤(2)的加热处理,使金属纳米颗粒形成团簇,且通过调整加热温度和持续时间来调整金属纳米颗粒团簇的形状和大小,有利于纳米微结构形貌的控制;实验证明:相对于现有技术,本发明的电池片的转换效率可提高0.20~0.22%左右,取得了意想不到的效果;2、本发明制备的纳米微结构开口较大,其尺寸为400~800nm,有利于纳米微结构表面的钝化;此外,本发明制备的微结构整齐且均匀性好;3、本发明的制备方法简单易行,与现有工业化生产工艺兼容性较好,可以快速移植到工业化生产中,适于推广应用。附图说明图1是本发明实施例一中硅片表面沉积金属纳米颗粒并加热后的SEM图。(放大倍数为50k)图2是本发明实施例一中硅片表面沉积金属纳米颗粒并加热后的SEM图。(放大倍数为30k)图3是本发明实施例一中硅片绒面的SEM扫描图。(放大倍数为30k)图4是本发明实施例二中硅片表面沉积金属纳米颗粒并加热后的SEM图。(放大倍数为50k)图5是本发明实施例二中硅片表面沉积金属纳米颗粒并加热后的SEM图。(放大倍数为30k)图6是本发明实施例二中硅片绒面的SEM扫描图。(放大倍数为30k)图7是本发明对比例一中硅片表面沉积金属纳米颗粒并加热后的SEM图。(放大倍数为50k)图8是本发明对比例一中硅片表面沉积金属纳米颗粒并加热后的SEM图。(放大倍数为30k)图9是本发明对比例一中硅片绒面的SEM扫描图。(放大倍数为30k)。具体实施方式下面结合实施例对本发明进一步描述。实施例一:参见图1~3所示,一种晶体硅太阳能电池绒面结构的制备方法,包括如下步骤:(1)将硅片放入含有金属离子的溶液中浸泡,使硅片表面涂覆一层金属纳米颗粒;(2)将上述步骤(1)中的表面涂覆有金属纳米颗粒的硅片置于惰性气体气氛中加热处理50秒,惰性气体气氛的温度为300℃,使硅片表面涂覆的金属纳米颗粒形成团簇;这里采用的是红外加热的方法,惰性气体气氛为氩气气氛;(3)用第一化学腐蚀液腐蚀硅片表面,形成多孔质层结构;温度为590℃,时间为2~10min;所述第一化学腐蚀液为HF和氧化剂的混合溶液;(4)水洗;然后采用第一清洗液去除残留金属颗粒;所述第一清洗液选自硝酸、氨水、盐酸和双氧水的混合液、氨水和双氧水的混合液中的任意一种混合液;(5)水洗;然后用第二化学腐蚀液进行表面刻蚀;所述第二化学腐蚀液为氢氟酸和硝酸的混合溶液;温度为40℃,时间为5~250s;(6)水洗;然后将上述硅片放入第三化学腐蚀液中进行浸渍,形成绒面结构;所述第三化学腐蚀液为碱液;所述碱液选自氢氧化钾,碱液的浓度为0.05~0.5mol/L;浸渍时间为5~250s;(7)水洗;然后将上述硅片放入第二清洗液中进行清洗,去除残留的金属颗粒;所述第二清洗液为氨水和双氧水的混合液;所述清洗液的温度为30℃;所述氨水的体积浓度为10%,双氧水的体积浓度为10%;(8)水洗;然后将上述硅片放入氢氟酸溶液中浸渍;水洗,即可得到晶体硅太阳能电池的绒面结构。图1是硅片表面沉积金属纳米颗粒并加热后(即步骤(2)后)的SEM图,其放大倍数为50k;图2也是其SEM图,其放大倍数为30k。图3是硅片绒面的SEM扫描图。实施例二:参见图4~6所示,一种晶体硅太阳能电池绒面结构的制备方法,包括如下步骤:(1)将硅片放入含有金属离子的溶液中浸泡,使硅片表面涂覆一层金属纳米颗粒;(2)加热上述步骤(1)中的含有金属离子的溶液,使溶液温度保持在600℃,并持续30秒,使硅片表面涂覆的金属纳米颗粒形成团簇;这里可以采用在溶液中设置电热丝的加热方式;(3)用第一化学腐蚀液腐蚀硅片表面,形成多孔质层结构;温度为590℃,时间为2~10min;所述第一化学腐蚀液为HF和氧化剂的混合溶液;(4)水洗;然后采用第一清洗液去除残留金属颗粒;所述第一清洗液选自硝酸、氨水、盐酸和双氧水的混合液、氨水和双氧水的混合液中的任意一种混合液;(5)水洗;然后用第二化学腐蚀液进行表面刻蚀;所述第二化学腐蚀液为氢氟酸和硝酸的混合溶液;温度为40℃,时间为5~250s;(6)水洗;然后将上述硅片放入第三化学腐蚀液中进行浸渍,形成绒面结构;所述第三化学腐蚀液为碱液;所述碱液选自氢氧化钾,碱液的浓度为0.05~0.5mol/L;浸渍时间为5~250s;(7)水洗;然后将上述硅片放入第二清洗液中进行清洗,去除残留的金属颗粒;所述第二清洗液为氨水和双氧水的混合液;所述清洗液的温度为30℃;所述氨水的体积浓度为10%,双氧水的体积浓度为10%;(8)水洗;然后将上述硅片放入氢氟酸溶液中浸渍;水洗,即可得到晶体硅太阳能电池的绒面结构。图4是硅片表面沉积金属纳米颗粒并加热后(即步骤(2)后)的SEM图,其放大倍数为50k;图5也是其SEM图,其放大倍数为30k。图6是硅片绒面的SEM扫描图。对比例一:参见图7~9所示,一种晶体硅太阳能电池绒面结构的制备方法,包括如下步骤:(1)将硅片放入含有金属离子的溶液中浸泡,使硅片表面涂覆一层金属纳米颗粒;(2)用第一化学腐蚀液腐蚀硅片表面,形成多孔质层结构;温度为590℃,时间为2~10min;所述第一化学腐蚀液为HF和氧化剂的混合溶液;(3)水洗;然后采用第一清洗液去除残留金属颗粒;所述第一清洗液选自硝酸、氨水、盐酸和双氧水的混合液、氨水和双氧水的混合液中的任意一种混合液;(4)水洗;然后用第二化学腐蚀液进行表面刻蚀;所述第二化学腐蚀液为氢氟酸和硝酸的混合溶液;温度为40℃,时间为5~250s;(5)水洗;然后将上述硅片放入第三化学腐蚀液中进行浸渍,形成绒面结构;所述第三化学腐蚀液为碱液;所述碱液选自氢氧化钾,碱液的浓度为0.05~0.5mol/L;浸渍时间为5~250s;(6)水洗;然后将上述硅片放入第二清洗液中进行清洗,去除残留的金属颗粒;所述第二清洗液为氨水和双氧水的混合液;所述清洗液的温度为30℃;所述氨水的体积浓度为10%,双氧水的体积浓度为10%;(7)水洗;然后将上述硅片放入氢氟酸溶液中浸渍;水洗,即可得到晶体硅太阳能电池的绒面结构。图7是硅片表面沉积金属纳米颗粒并加热后(即步骤(2)后)的SEM图,其放大倍数为50k;图8也是其SEM图,其放大倍数为30k。图9是硅片绒面的SEM扫描图。对比图1、4和7,以及图2、5和8,可以看出,采用本发明的加热步骤之后,实施例中硅片表面涂覆的金属纳米颗粒形成团簇,而对比例则没有发生团簇。再比较图3、6和9,可以看出,与对比例相比,实施例制得的微结构更大、更整齐且均匀性好。然后,按照现有技术制成电池片,测试实施例和对比例的电性能,对比结果如下:Uoc(mV)Jsc(mA/cm2)FF(%)EFF对比例一634.88.93179.7918.59%实施例一636.88.97979.9718.79%实施例二636.88.98280.0318.81%由上可见,相对于对比例,本发明的电池片Uoc有明显的提升,形成团簇后制备的绒面钝化效果更好,转换效率可提高0.20~0.22%左右,取得了意想不到的效果。