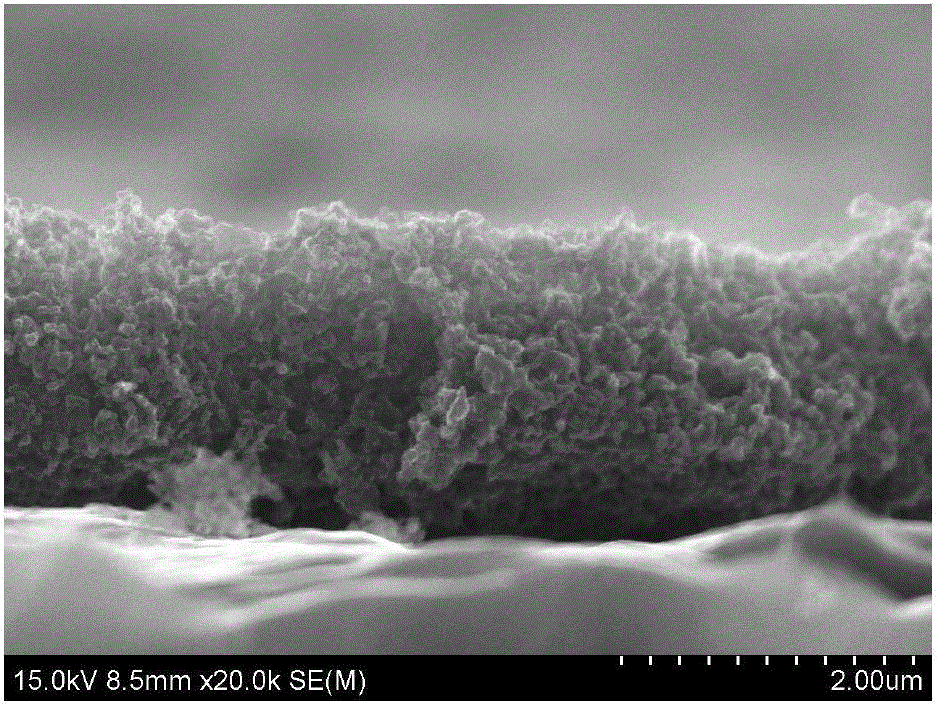
本发明涉及锂离子电池功能性导电集流体的制备方法,具体涉及一种锂离子电池用水系底涂集流体及其制备方法和应用。
背景技术:
:典型的电化学电池具有参与电化学反应的阴极和阳极。为制造电极,可以将电极活性材料(electroactivematerial)涂覆到集流体上,其可以充当电池的正负极材料。保持电极活性材料与导电集流体之间的电接触对于电化学电池的有效运作至关重要。已知地,涂覆在电极活性材料和集流体之间的过渡层,称为“底涂料”或者“底涂层”,可以粘合在电极活性材料和集流体之间,并且提供电极活性材料和集流体之间的电导通,进而降低活性物质与集流体之间的接触电阻。目前,现在已有底涂浆料出现,但许多现有底涂料不能在提供层间良好的电接触的同时也提高电极活性材料和集流体的良好粘合。技术实现要素:有鉴于此,本发明提供了一种锂离子电池用水系底涂集流体,可以在提高集流体和电极活性材料之间良好导电能力的同时,还可以提高电极活性材料在涂覆有水系底涂浆料的集流体(即得到的水系底涂集流体)上的粘结性,进而提高电池的压实密度、能量密度等性能。第一方面,本发明提供了一种水系底涂集流体的制备方法,包括如下步骤:(1)将水系分散剂和水混合,搅拌均匀,得到混合物A;(2)将片状导电碳和球形导电碳加入到所述混合物A中,搅拌均匀后并进行砂磨直至所述片状导电碳和球形导电碳的D50为20~90μm,得到混合物B;(3)向所述混合物B中加入水系粘结剂,搅拌得到锂离子电池用水系底涂浆料,所述水系底涂浆料中,水系分散剂的质量分数为0.5-10%,片状导电碳的质量分数为5-25%,球形导电碳的质量分数为5-50%,水系粘结剂的质量分数为2-10%;(4)取集流体基材,将所述水系底涂浆料涂覆在所述集流体基材表面,干燥后形成一底涂层,得到水系底涂集流体。优选地,所述水系底涂浆料的粘度为0.05~8Pa·s。优选地,所述水系底涂浆料中,水的质量分数为30-80%。进一步优选为40-70%。优选地,步骤(1)中,所述搅拌的时间为0.5-4h小时。优选地,步骤(2)中,所述搅拌的时间为0.5-4h小时。优选地,步骤(3)中,所述搅拌的速度为3000~5000r/min。本发明中,在制备底涂浆料的过程中,同时采用片状导电碳和球形导电碳作为导电剂,其中,片状导电碳能够有效降低界面电阻,而球状导电碳可有效能够增强导电性,增强粗糙度,可以借由片状和球形导电碳的相互作用,共同形成导电网络结构(可以是片状导电碳形成导电网络框架,球形导电碳穿插在片状导电碳的层面之间,避免片状导电碳的团聚,或者是球形导电碳充分分散在片状导电碳分子之间)。在将所述底涂浆料涂布到集流体上时,利于集流体和电极活性物质之间导电性的提高,更利于形成大面积的具有凹凸不平的粗糙表面的底涂层,有助于电极活性材料在集流体上的粘附,并承载更多的电极活性材料,从而提高电池的能量密度,减少电池内阻。此外,在制备底涂浆料的过程中,先将水系分散剂与水进行混合,再加入导电剂,最后加入水系粘结剂,这样可以避免先加入水系粘结剂所造成的浆料粘度增大,影响后加入的片状和球形导电碳的分散,延长搅拌时间。本发明中主要控制片状导电碳和球形导电碳在水系底涂浆料中的质量分数分别为5-25%、5-50%,并基于水系分散剂、粘结剂、水的协同作用,使得所述底涂层的粗糙度合适,空隙合适,便于电极活性材料在水系底涂集流体的底涂层上稳定、高附着量的承载。球形导电碳与片状导电碳在浆料中的质量分数应控制在一定范围,若球性导电碳太多,片状导电碳太少,则球形导电碳自身可能在底涂层表面形成密堆积,影响电极活性材料在水系底涂集流体上的附着量,进而影响电池的能量密度;若片状导电碳太多,球形导电碳太少,则形成的整体结构中空隙太大,底涂层的粗糙度不够,电极活性材料在水系底涂集流体上的附着不稳定。优选地,所述片状导电碳在油系底涂浆料中的质量分数为4-15%。优选地,所述球形导电碳在油系底涂浆料中的质量分数为10-25%。进一步优选为12-23%。本发明中,所述球形导电碳与所述片状导电碳的质量比为(0.2-10):1。优选地,所述球形导电碳与所述片状导电碳的质量比为(1-5):1。本申请的步骤(2)中,采用研磨至D50为20~90μm的片状导电碳和球形导电碳作为构成所述水系底涂浆料的主要成分,这样粒径范围的导电剂,可以在所述水系底涂浆料中较好的分散,浆料的底涂性能较优良,可以避免粒径范围太大影响涂布的厚度,还可以避免粒径太小,使得形成的底涂层的粗糙度不够。优选地,所述片状导电碳选自石墨烯、鳞片石墨、膨胀石墨和KS-6中的一种或多种。优选地,所述球形导电碳为SupperP、科琴黑、乙炔黑、350G等炭黑导电剂(SP)中的一种或多种。本发明中,所述石墨烯包括单层的石墨烯或两层以上且一百层以下的多层石墨烯。所述单层的石墨烯是指具有sp2键的1原子层的碳分子片。优选地,所述石墨烯为2-10层的多层石墨烯。优选地,所述石墨烯的直径为5~10μm,厚度为10~20nm。在本发明一实施方式中,所述片状导电碳为石墨烯,所述球形导电碳为350G。在本发明一实施方式中,所述片状导电碳为KS-6,所述球形导电碳为科琴黑。在本发明一实施方式中,所述片状导电碳为石墨烯和膨胀石墨,所述球形导电碳为乙炔黑和科琴黑。在本发明一实施方式中,所述片状导电碳为鳞片石墨和KS-6,所述球形导电碳为乙炔黑和350G。优选地,所述水系分散剂为乙醇、十二烷基硫酸钠(SDS)、十二烷基苯磺酸钠(SDBS)、辛基苯基聚氧乙烯醚(曲拉通X-100)、聚乙烯吡咯烷酮(PVP)和聚乙二醇(PEG)中的一种或多种。本发明一实施方式中,所述PEG的分子量为1-5万。优选地,所述水系粘结剂包括羧甲基纤维素钠(CMC)、聚乙烯醇(简写为PVA)和LA系列水性粘结剂(如LA133、LA132、LA135)中的一种或多种,但不限于此。进一步优选地,所述水系粘结剂在水系底涂浆料中的质量分数为2-6%。更优选为3-5%。本发明一实施方式中,所述PVA的分子量为5-30万。优选地,所述水系底涂浆料中,还包括表面活性剂,消泡剂,稳定剂中的一种或多种。优选地,所述底涂层的厚度为0.2-10μm。进一步优选为0.5-2μm。优选地,所述底涂层的剥离强度为0.05-1N。所述剥离强度是采用万能力学试验机进行测量,此仪器将剥离力从零开始逐渐增大,增大到将涂层和集流体基体分离时所用的力即为该涂层的剥离力。优选地,所述集流体基材为铜箔或铝箔。进一步优选为铝箔。本发明第一方面提供的所述水系底涂集流体的制备方法,简单易操作,底涂浆料的制备时间短,易得到搅拌均匀的底涂浆料。第二方面,本发明提供了一种水系底涂集流体,所述水系底涂集流体采用本发明第一方面所述的方法制得。其中,所述水系底涂集流体包括集流体基材和形成在所述集流体基材上的底涂层。其中,所述底涂层包括水系分散剂、片状导电碳、球形导电碳和水系粘结剂。本申请中,片状导电碳、球形导电碳均匀分散在构成底涂层浆料的水系分散剂和水系粘结剂中,干燥后形成的所述底涂层具有凹凸不平的粗糙表面。本发明第二方面提供的水系底涂集流体具有凹凸不平的粗糙表面,当电极活性物质涂覆在该水系底涂集流体表面时,除了保证活性物质和水系底涂集流体之间具有良好的导电能力外,还可以增加后续活性物质和水系底涂集流体之间的粘粘性和剥离强度(约提高50%以上)。第三方面,本发明提供了一种电极极片,所述电池极片包括水系底涂集流体和电极活性物质层,所述水系底涂集流体包括集流体基材和形成在所述集流体基材上的底涂层,所述底涂层上设置有所述电极活性物质层。其中,所述电极活性物质层包括正极活性材料、导电剂和溶剂。所述电极活性物质层中还可以包括粘结剂等。其中,所述电极活性物质层包括负极活性材料、导电剂和溶剂。所述电极活性物质层中还可以包括粘结剂等。所述正极活性材料包括磷酸铁锂、磷酸锰铁锂、镍钴铝酸锂等常见的正极材料。所述负极活性材料包括石墨等。第四方面,本发明还提供了一种锂离子电池,在上述水系底涂集流体上涂覆正极或负极活性物质,通过涂覆,制片,注液,化成,分容,得到锂离子电池。集流体基材与活性物质的内阻较大,影响锂离子的迁移速率,进而影响锂离子电池的性能。与单纯的集流体基材相比,本发明提供的所述水系底涂集流体,基于所述底涂层的作用,可以减少集流体基材与活性物质之间的电子迁移阻力,可使电池极片的方块电阻降低85%以上,可使形成的半电池的交流阻抗降低40%以上,使全电池的内在降低30%以上。更重要的是,所述水系底涂集流体中底涂层的特殊表面结构可以明显增加活性物质和水系底涂集流体之间的粘结性和剥离强度(约提高50%以上),还可大大增加活性物质在水系底涂集流体上的负载程度,提高电池的压实密度,增加电池的能量密度,为电池动力续航提供可能。本发明提供的所述水系底涂集流体,可使电池(如磷酸铁锂为正极材料)的压实密度从2.2-2.3g/cm3提高到2.4-2.6g/cm3,使电池的能量密度从115-125wh/kg上升到130-140wh/kg。本发明的优点将会在下面的说明书中部分阐明,一部分根据说明书是显而易见的,或者可以通过本发明实施例的实施而获知。附图说明图1为本发明实施例1提供的一种水系底涂集流体的结构示意图;图2为本发明实施例1中所得水系底涂集流体上底涂层的扫描电镜(SEM)照片;图3为本发明实施例1提供的一种电池正极极片的结构示意图。具体实施方式以下所述是本发明的优选实施方式,应当指出,对于本
技术领域:
的普通技术人员来说,在不脱离本发明原理的前提下,还可以做出若干改进和润饰,这些改进和润饰也视为本发明的保护范围。实施例1一种水系底涂集流体的制备方法,包括以下步骤:1.将60gPEG加入1400g的去离子水中,在分散罐中搅拌30min,使其完全溶解;2.向上述分散罐中加入180g石墨烯(片状)及435g的350G(球形)搅拌30min,待分散均匀后,采用砂磨机进行砂磨4-5遍,直至混合物的粒度D50为20μm即可,停止砂磨;3.向步骤2的分散罐中加入80g的CMC,进行搅拌,得到粘度为4mPa·s左右的水系底涂浆料;4.将所得到的水系底涂浆料采用刮刀技术涂覆在铝箔集流体基材的表面,干燥后形成厚度为1微米的一底涂层,得到水系底涂集流体。图1为本发明实施例1中所得水系底涂集流体的结构示意图。图1中,10为铜箔集流体基材,20为底涂层,层叠在10上的20与10共同构成所述水系底涂集流体。此外,该底涂层的剥离强度为0.07N。图2为本实施例中底涂层的扫描电镜(SEM)照片,从图2中可以看到,底涂层中凹凸不平、粗糙度较高,且具有一定的空隙,可便于后续电极活性材料的粘附、嵌入。应用1:在本实施例1得到的水系底涂集流体上涂覆正极活性物质(包括取5g粒径为0.1微米的磷酸铁锂(LFP)、3g的去离子水中、7.8g的导电液混合形成正极活性物质),并先于100℃干燥5min,再在120℃干燥2min,裁片后得到电池正极极片。使用的导电液为CN-1N/CN-1F德方纳米科技股份有限公司。应用2:半电池的制作:在本实施例1得到的水系底涂集流体上涂覆正极活性物质(包括取5g粒径为0.1微米的LFP、3g的去离子水中、7.8g的导电液混合形成正极活性物质),经烘干,辊压,冲片得到正极极片,将得到的正极片粘黏在正极壳上,负极使用锂片,并压成纽扣电池,制得半电池。应用3:全电池的制作:将上述制得的正极片和石墨构成的负极片与和隔膜进行层叠和卷绕,得到电芯,隔膜设置在正极片和负极片之间,将电芯装入壳体的收容空间内,注入电解液,密封后制得锂离子电池(即为全电池,如常见的18650电池或者说软包电池)图3为本发明实施例1中所得电池正极极片的结构示意图。图3中,10为铜箔集流体基材,20为底涂层,层叠在10上的20与10共同构成所述水系底涂集流体100,30为正极活性位置。从图3中明显可以看出,活性物质能够充分嵌入到水系底涂集流体中的底涂层中,并借由凹凸不平、粗糙度较高的底涂层,实现其在水系底涂集流体中的牢固粘附,增大了水系底涂集流体和活性物质之间的剥离强度和剥离难度。为突出本发明的技术效果,通过以下对比实施例1:取普通的铜箔集流体,在其表面涂覆同样的正极活性物质,制成电池正极极片,并测试其性能,结果如下表1所示。表1本发明例1和对比例1的性能对比其中,上述表1中,剥离力、方块电阻、压实密度是针对电极正极极片的测试;内阻、交流阻抗是针对半电池的测试,能量密度是针对电池的测试。由表1可以明显看出,本发明提供的所述水系底涂浆料形成的底涂层,可以很好地修饰集流体基材,得到表面粗糙度较高的水系底涂集流体,该水系底涂集流体可以提高水系底涂集流体和电极活性物之间的导电能力,还可以提供两者之间的粘粘性,提高电池的压实密度和能量密度,为电池动力续航提供可能。为突出本发明的技术效果,还针对实施例1设置了以下2个对比实施例:对比实施例2一种水系底涂集流体的制备方法,包括以下步骤:1.将:60g的PEG加入215g的去离子水中,在分散罐中搅拌30min,使其完全溶解;2.向上述分散罐中加入600g石墨烯(片状)及1200g的350G(球形)搅拌30min,待分散均匀后,采用砂磨机进行砂磨4-5遍,直至混合物的粒度D50为20μm即可,停止砂磨;3.向步骤2的分散罐中加入80g的CMC,进行搅拌,得到水系底涂浆料;4.将所得到的水系底涂浆料采用刮刀技术涂覆在铝箔集流体基材的表面,干燥后形成一底涂层,得到水系底涂集流体。对比实施例3一种水系底涂集流体的制备方法,包括以下步骤:1.将:60g的PEG加入1855g的去离子水中,在分散罐中搅拌30min,使其完全溶解;2.向上述分散罐中加入75g石墨烯(片状)及85g的350G(球形)搅拌30min,待分散均匀后,采用砂磨机进行砂磨4-5遍,直至混合物的粒度D50为20μm即可,停止砂磨;3.向步骤2的分散罐中加入80g的CMC,进行搅拌,得到水系底涂浆料;4.将所得到的水系底涂浆料采用刮刀技术涂覆在铝箔集流体基材的表面,干燥后形成一底涂层,得到水系底涂集流体。采用与实施例1相同的方法,将对比实施例2、3制得的水系底涂集流体分别制成电池正极极片、半电池、电池,并测试相关性能,结果如下表2所示:表2本发明例1和对比例2、3的性能对比性能对比例2对比例3例1剥离力(N)0.38210.29910.581方块电阻(Ω)10210.103内阻(mΩ)2137,69交流阻抗(1000Hz)(Ω)14.6259.27压实密度(g/cm3)2.322.282.32能量密度(wh/kg)121118132实施例1中,片状导电碳的质量分数为8.35%,球形导电碳的质量分数为20%,而对比例2中,片状导电碳的质量分数为27.8%,球形导电碳的质量分数为55.6%,对比例3中,片状导电碳的质量分数为3.4%,球形导电碳的质量分数为4%。由上表2可知,当水系底涂浆料中,片状导电碳的质量分数超出25%或低于5%时,球形导电碳的质量分数超出50%或低于5%时所得底涂层的剥离力均较低,电池极片的压实密度也较低,这说明水系底涂浆料中,片状导电碳和球形导电碳应该控制在一定的含量范围,才可使得所得水系底涂集流体的各项性能更优越。实施例2一种水系底涂集流体的制备方法,包括以下步骤:1.将72g的曲拉通X-100加入1485g的去离子水中,在分散罐中搅拌60min,使其完全溶解;2.向上述分散罐中加入及115g的KS-6(片状)及500g科琴黑(球形)搅拌2h,待分散均匀后,采用砂磨机进行砂磨4-5遍,直至混合物的粒度D50为20~90μm即可,停止砂磨;3.向步骤2的分散罐中加入90g的LA132,进行搅拌,得到粘度为3mPa·s左右的水系底涂浆料;4.将所得到的水系底涂浆料采用刮刀技术涂覆在铜箔集流体基材的表面,干燥后形成一底涂层,得到水系底涂集流体。将本实施例2得到的水系底涂集流体的底涂层上涂覆正极活性物质(包括粒径为0.2微米的LFP、蒸馏水还有导电液构成的混合浆料),干燥后得到电池正极极片。实施例3一种水系底涂集流体的制备方法,包括以下步骤:1.将65g的聚乙烯吡咯烷酮PVP加入1480g的去离子水中,在分散罐中搅拌45min,使其完全溶解;2.向上述分散罐中加入250g的鳞片石墨(片状)及350g的乙炔黑(球形)搅拌2h,待分散均匀后,采用砂磨机进行砂磨4-5遍,直至混合物的粒度D50为20~90μm即可,停止砂磨;3.向步骤2的分散罐中加入70g的水系粘结剂LA133,进行搅拌,得到粘度为8Pa·s左右的水系底涂浆料;4.将所得到的水系底涂浆料采用刮刀技术涂覆在铜箔集流体基材的表面,干燥后形成一底涂层,得到水系底涂集流体。以上所述仅为本发明的较佳实施例而已,并不用以限制本发明,凡在本发明的精神和原则之内所作的任何修改、等同替换和改进等,均应包含在本发明的保护范围之内。当前第1页1 2 3