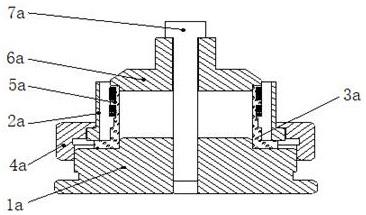
1.本实用新型涉及力矩器技术领域,具体涉及一种力矩器定圈组件的灌胶模具。
背景技术:2.力矩器将电信号(电流或电流脉冲)转换为力矩(或力),是陀螺仪和加速度计中非常重要的一个元件。在陀螺仪中,力矩器将力矩施加到陀螺仪的输出轴上,使陀螺仪产生有规律的进动,以保持转子轴在特定的方向上,如平行于当地垂线或当地子午线方向。在摆式加速度计中,也需要对惯性质量摆施加平衡力矩,以使它维持在平衡位置。
3.挠性陀螺仪的力矩器骨架一般采用强度大、耐候性和耐久性优良的可加工陶瓷制成。但受挠性陀螺仪体积及力矩器工作空间限制,力矩器定圈组件的可加工陶瓷骨架为中空的薄壁件,外侧采用胶液将工作线圈固定在可加工陶瓷骨架上。
4.参见图1,现有的力矩器灌胶模具包括胶膜底座1a和胶模外圈2a,胶膜外圈2a位于力矩器骨架3a外侧,并通过锁紧螺母4a与胶膜底座固定。线圈5a绕设在力矩器骨架3a外侧。胶模外圈2a与力矩器骨架3a之间即为灌胶通道。为避免胶液进入力矩器骨架内侧,需要额外设置固定压块6a。固定压块6a置于力矩器骨架3a的上侧,并通过锁紧螺钉7a将固定压块6a和胶膜底座1a固定将力矩器骨架3a的内部封闭。固定压块6a的设置增加了制造灌胶模具的安装步骤,并且增加了灌胶的成本。此外,现有的灌胶结构在灌胶时存在不易排出通道底部的气体的缺陷,胶液内部以及胶液与力矩器骨架之间的气体不易排出,在力矩器定圈组件加工完成后骨架易开裂,成品合格率低。
技术实现要素:5.针对现有技术存在的上述不足,本实用新型的目的在于解决现有的力矩器灌胶结构复杂,灌胶成本高,且在灌胶时不易排出气体,使得力矩器定圈组件加工完成后骨架易开裂,成品合格率低的问题,提供一种力矩器定圈组件的灌胶模具,能够排出灌胶通道内的气泡,便于灌胶,使力矩器定圈组件加工完成后性能可靠,合格率高。
6.为了解决上述技术问题,本实用新型采用如下技术方案:
7.一种力矩器定圈组件的灌胶模具,包括模具本体,所述模具本体为下端封闭的圆筒结构,所述模具本体的底部成型有一定位凸台,该定位凸台的轴心线与模具本体的轴心线重合;模具本体的上端向外侧倾斜并延伸形成导流台。
8.通过设置定位凸台,定位凸台的轴心线与模具本体的轴心线重合,这样,将力矩器骨架倒置并将其上端插入灌胶模具中并通过凸台对力矩器骨架进行限位,结构简单且安装方便。在模具本体的上端向外侧倾斜并延伸形成导流台,这样,胶水通过导流台向下灌入,便于将位于通道底部的气体排出,使得胶液与力矩器骨架之间不易开裂,提高成品的合格率。
9.进一步,所述定位凸台的直径与力矩器骨架的内径一致,这样,定位凸台的定位更加准确。
10.进一步,还包括一压板,所述压板通过一锁紧螺栓与模具本体的底部相连;其中,压板的中部具有一通孔,在定位凸台的中部开设有锁紧螺孔,该锁紧螺孔沿模具本体的轴心线贯穿模具本体的底部;锁紧螺栓穿过通孔后与螺孔相连。通过压板使力矩器骨架位置固定,方便灌胶操作。
11.与现有技术相比,本实用新型具有如下优点:
12.通过设置定位凸台,定位凸台的轴心线与模具本体的轴心线重合,这样,将力矩器骨架倒置并将其上端插入灌胶模具中并通过凸台对力矩器骨架进行限位,结构简单且安装方便。在模具本体的上端向外侧倾斜并延伸形成导流台,这样,胶水通过导流台向下灌入,便于将位于通道底部的气体排出,使得胶液与力矩器骨架之间不易开裂,提高成品的合格率。
附图说明
13.图1为现有的力矩器灌胶示意图。
14.图2为本实用新型中一种力矩器定圈组件的灌胶模具的灌胶示意图。
15.图3为本实用新型中一种力矩器定圈组件的力矩器骨架示意图。
16.图中:
17.胶膜底座1a、胶模外圈2a,力矩器骨架3a、锁紧螺母4a、线圈5a、固定压块6a、锁紧螺钉7a。
18.模具本体1、定位凸台11、导流台12、力矩器骨架2、第一安装凸台21、第二安装凸台22、线圈3。
具体实施方式
19.下面将结合附图及实施例对本实用新型作进一步说明。
20.实施例:
21.参见图2和3,一种力矩器定圈组件的灌胶模具,包括模具本体1,所述模具本体1为下端封闭的圆筒结构,所述模具本体1的底部成型有一定位凸台11,该定位凸台11的轴心线与模具本体1的轴心线重合。模具本体1的上端向外侧倾斜并延伸形成导流台12。具体实施时,所述定位凸台11的直径与力矩器骨架2的内径一致,这样,定位凸台11的定位更加准确。还包括一压板,所述压板通过一锁紧螺栓与模具本体1的底部相连。力矩器定圈组件中的力矩器骨架2具有一法兰盘,加工时,该压板的直径大于该法兰盘的内径且小于等于该法兰盘的外径,使该压板能够压在力矩器骨架2的法兰盘上并且不会阻碍灌胶。其中,压板的中部具有一通孔,在定位凸台11的中部开设有锁紧螺孔,该锁紧螺孔沿模具本体1的轴心线贯穿模具本体1的底部。锁紧螺栓穿过通孔后与螺孔相连。通过压板使力矩器骨架2位置固定,方便灌胶操作。
22.使用时,具体包括如下步骤:
23.s1、将线圈3组件安装于力矩器骨架2上,再将安装有线圈3的力矩器骨架2倒置后伸入灌胶模具内,并通过定位凸台11进行限位,使力矩器骨架2、线圈3组件与灌胶模具之间形成灌胶通道。具体实施时,所述线圈3组件包括数个矩形环状结构的线圈3,所述线圈3的中心具有一矩形孔;在力矩器骨架2的外侧绕其一周设有与每个线圈3的矩形孔对应的第一
安装凸台21,所述线圈3组件套设在第一安装凸台21上。这样,便于安装线圈3组件。在相邻两个第一安装凸台21之间,沿力矩器骨架2的轴向设有一第二安装凸台22,所述第二安装凸台22位于两第一安装凸台21的中心位置,且当线圈3安装后,该第二安装凸台22能够与相邻的两线圈3抵接并对两线圈3进行限位。通过设置第二安装凸台22,线圈3之间的间隙变小,线圈3两端都与一定位凸台11接触定位,使得线圈3正交提升。
24.s2、调配胶液,并将胶液抽真空。实施时,在胶液抽真空前将胶液加热至60℃并保温30min。这样,胶液的流动性达到最佳状态,确保后期灌注时胶液与线圈组件接触良好。
25.s3、保持胶液在60
±
5℃下进行灌胶,将抽真空后的胶液注入灌胶通道内使胶液淹没线圈3,然后将力矩器定圈组件和灌胶模具放入真空环境中,以0.5~1 l/s的速率抽真空30s,这样,能够将胶液中的气体抽出,若时间延长,则灌入的胶液开始凝固,达不到抽真空的目的。
26.s4、将力矩器定圈组件和灌胶模具从真空环境中移出,再次向灌胶通道内注入胶液,将整个灌胶通道填满,为了保证胶液的流动性达到最佳状态,确保后期灌注时胶液与线圈组件接触良好,保持胶液在60
±
5℃下进行灌胶。
27.s5、将灌胶结构定型烘干后脱模、精加工,得到力矩器定圈组件。
28.在灌胶过程中,先将胶液抽真空,然后将抽真空后的胶液灌入使胶液淹没线圈后,再将灌胶后的力矩器定圈组件和灌胶模具抽真空,通过两次抽真空使胶液中的气体排出,胶层内无气泡;胶液与力矩器骨架和线圈之前的结合紧密,胶层稳定性高,从而提高力矩器定圈组件的合格率。由于采用了上述力矩器定圈组件的灌胶模具,使得胶液与力矩器骨架之间不易开裂,提高成品的合格率,还具有胶液灌注方便,工装简单,脱模方便的优点。
29.最后需要说明的是,以上实施例仅用以说明本实用新型的技术方案而非限制技术方案,本领域的普通技术人员应当理解,那些对本实用新型的技术方案进行修改或者等同替换,而不脱离本技术方案的宗旨和范围,均应涵盖在本实用新型的权利要求范围当中。