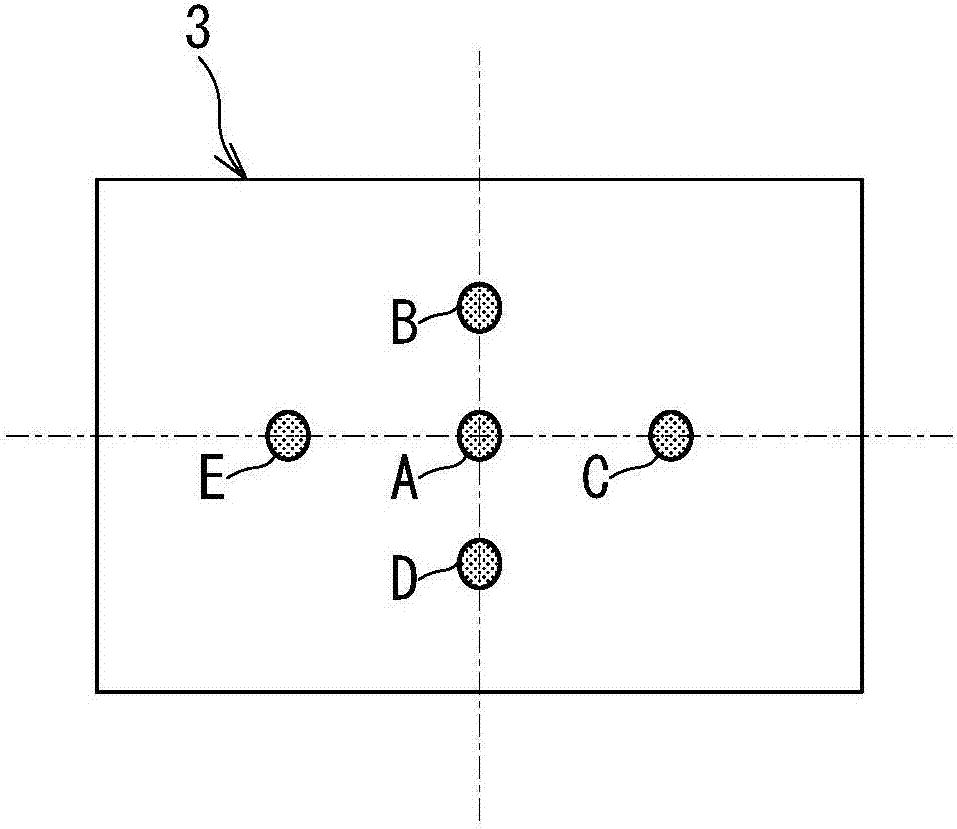
本申请是国际申请日为2011年2月10日国际申请号为pct/jp2011/052910、中国国家申请号为20118009729.x,名称为“耐磨元件以及制造该耐磨元件的方法”的申请的分案申请。本发明涉及一种耐磨(耐磨损)元件以及制造该元件的方法,并且更具体地涉及一种包含主要由氮化硅所形成的陶瓷烧结体的耐磨元件,以及制造该耐磨元件的方法。
背景技术:
:陶瓷烧结体具有轻、高硬度、高耐磨性、高耐腐蚀性和低热膨胀系数的性能,使得陶瓷烧结体广泛地作为元件用于构成精制的装置。具体地,从优异的高硬度和耐磨性的观点来说,陶瓷烧结体已经被优选作为耐磨元件用于构成轴承。在不同的陶瓷烧结体中,氮化硅(si3n4)烧结体具有高硬度和优异的耐磨性,使得氮化硅烧结体优选作为元件用于构成轴承等。关于这种氮化硅烧结体,为了改进作为构成轴承等的耐磨元件的可靠性,一段时间以来已经进一步改进了性能。例如,已经提出了一种制造氮化硅烧结体的方法,包含步骤:通过将钇氧化物、尖晶石、氧化铝和/或氮化铝以规定的金属元素的预定摩尔比和预定的含量比加入到氮化硅材料粉末,来制备材料粉末混合物;制备由该材料粉末混合物所形成的压实体(模制体);在1400-1500℃的温度烧结该压实体;在1500-1650℃的温度进一步烧结该压实体,由此来获得相对密度为大约98%的烧结体;和在10atm或者更大的氮气氛中,在1400-1650℃的温度对该烧结体进行次级烧结(主烧结)操作,由此来将相对密度提高到大约99%,以便能够制造强度优异,并且在强度性能方面具有较低分散的氮化硅烧结体(例如参考专利文献1)。另外,作为用于制造这种类型的氮化硅烧结体所用的氮化硅原料粉末,通常已知的是优选使用高纯材料粉末。例如,通过酰亚胺热分解方法所合成的高纯度材料粉末是适用的。但是,这种高纯度材料粉末是非常昂贵的,并且因此所制造的氮化硅烧结体的机械强度和断裂韧性值倾向于变得过大,因此产生了这样的问题,即,所形成的烧结体的可加工性是不足的。为了解决这个问题,已经论述了一种通过使用廉价的氮化硅原料粉末来制造氮化硅烧结体的方法,该氮化硅原料粉末是通过将金属si直接氮化的直接氮化方法来制造的。该通过直接氮化方法所制造的氮化硅原料粉末具有相对大的fe和ca含量。但是,已知的是当将稀土元素、铝成分和碳化硅等的含量控制到预定的范围内时,可以获得机械强度、耐磨性和滚动寿命性能等于或者大于常规烧结体的烧结体,并且所形成的烧结体的可加工性也是优异的(例如参见专利文献2)。如上所述,当由该含有氮化硅原料粉末的材料粉末的混合物所形成的压实体(模制体)进行初级烧结时,获得了相对密度为大约98%的烧结体。其后,将所形成的烧结体进一步在压力为10atm或者更大的氮气氛中进行次级烧结操作,从而获得相对密度高于98%、优选99%或者更大的烧结体,由此来制造强度优异,并且强度性能分散较小的氮化硅烧结体。但是,为了在初级烧结操作获得大约98%的相对密度,必须严格的控制该制造方法,因此产生了这样的问题,即,制造氮化硅烧结体所需的生产成本不利地增加了。如上所述,通过直接氮化方法所制造的氮化硅材料粉末的成本是相对低的。此外,当将包含在氮化硅材料粉末中的稀土元素、铝成分和碳化硅等的量控制到预定的范围内时,可以制造这样的氮化硅烧结体,其具有优异的机械强度、耐磨性和滚动寿命(rollinglife)性能等,特别是优异的加工性。现有技术文献专利文献专利文献1:日本专利申请(公开)no.06-080470专利文献2:国际专利申请(公开)no.wo2005/030674技术实现要素:本发明所要解决的技术问题但是,因此所制造的氮化硅烧结体表现出它特性的离差(分散性),因此当这些氮化硅烧结体在更苛刻的条件下用作耐磨元件时,产生了这样的问题,即,一些烧结体具有不足的特性。此外,因为存在上述特性的离差(dispersion),当烧结体加工成耐磨元件时,一些烧结体在加工过程等期间易于损坏,因此产生了在耐磨元件制造加工时,产率降低的严重问题。此外,在氮化硅烧结体用作耐磨元件的情况中,研磨加工是一个基本方法。但是,因为高密度的氮化硅烧结体是一种硬质材料,其难以进行研磨加工,因此研磨加工的负荷很大,因此需要大量的人工-小时和加工时间。本发明已经解决了上述问题。因此,本发明的一个目标是提供一种耐磨(磨损)元件,其包含能够以低成本制造和同时能够抑制特性的离差的氮化硅烧结体。具体的,本发明的目标是提供一种能够降低其研磨加工的负荷的耐磨元件。本发明的另一目标是提供一种有效制造这样的耐磨元件的方法。解决问题的手段为了实现上述目标,本发明的一种实施方案提供了一种由主要由氮化硅烧结体组成的陶瓷烧结体所形成的耐磨元件,该陶瓷烧结体含有10-3500ppm的按照fe元素计的fe成分,大于1000ppm至2000ppm的按照ca元素计的ca成分,和1-2000ppm的按照mg元素计的mg成分,其中氮化硅晶粒的β-相比是95%或者更大,氮化硅晶粒的最大长径是40μm或者更低,通过xrd(x射线衍射方法)没有检测出存在于晶界相中的ca成分,并且该耐磨元件内部的维氏(vicker)硬度、断裂韧性和密度中每个的离差处于±10%的范围。优选的是通过xrd没有检测出存在于该陶瓷烧结体的晶界相中的mg成分。此外,还优选的是该陶瓷烧结体包含0.1-5质量%的选自下面的至少一种元素:ti,zr,hf,w,mo,ta,nb和cr。此外,还优选的是前述陶瓷烧结体包含1-5质量%的以稀土元素计的稀土成分,和1-5质量%的以al元素计的al成分。另外,还优选的是该陶瓷烧结体的维氏硬度是1400或者更大。此外,还优选的是定义为构成耐磨元件的氮化硅晶粒的各长径比的平均值的平均长径比是2或者更大。此外,还优选的是该陶瓷烧结体包含表面粗糙度(ra)是1μm或者更低的研磨的表面。根据本发明的另外一种实施方案,这里提供了一种制造由主要由氮化硅形成的陶瓷烧结体所形成的耐磨元件的方法,该方法包含步骤:制备一种材料粉末混合物,其含有氮化硅材料粉末、烧结剂粉末、10-3500ppm的按照fe元素计的fe成分、大于1000ppm至2000ppm的按照ca元素计的ca成分、和1-2000ppm的按照mg元素计的mg成分;模制该材料粉末混合物,由此来形成模制体;在1600-1950℃的烧结温度对该模制体进行初级烧结操作,由此来获得相对密度为80%或者更高且小于98%的初级烧结体;冷却该初级烧结体,其中在烧结温度到1400℃的温度范围内,将冷却速率控制到100℃/小时或者更大;在1600-1900℃的烧结温度对该初级烧结体进行次级烧结操作,由此来获得相对密度为98%或者更大的次级烧结体;和冷却该次级烧结体,其中在烧结温度到1400℃的温度范围内,将冷却速率控制到100℃/小时或者更大。此外,还优选的是该次级烧结操作是通过对初级烧结体进行高温等静压(hip)方法来实施。此外,还优选的是该陶瓷烧结体包含1-5质量%的以稀土元素计的稀土成分和1-5质量%的以al元素计的al成分作为烧结剂。仍然的另外,还优选的是该方法进一步包含研磨该陶瓷烧结体的步骤,从而将该陶瓷烧结体的表面粗糙度ra控制到1μm或者更低。本发明的效果根据本发明由主要由氮化硅烧结体组成的陶瓷烧结体所形成的耐磨元件,该陶瓷烧结体含有10-3500ppm的按照fe元素计的fe成分、大于1000ppm至2000ppm或者更低的按照ca元素计的ca成分、和1-2000ppm的按照mg元素计的mg成分,来提供耐磨元件,在其中将该耐磨元件的密度、硬度和断裂韧性中每个的离差抑制到±10%的范围,并且该耐磨元件还具有优异的可靠性和低成本性。此外,根据本发明,可以获得烧结的表面(烧结完成面),其是易于研磨的。另外,根据该制造耐磨元件的方法,该耐磨元件是如下来制造的:制备一种材料粉末混合物,其含有氮化硅材料粉末、烧结剂粉末、10-3500ppm的按照fe元素计的fe成分、大于1000ppm至2000ppm的按照ca元素计的ca成分、和1-2000ppm的按照mg元素计的mg成分;模制该材料粉末混合物,由此来形成模制体;对该模制体进行初级烧结操作,由此来获得相对密度为80%或者更高且小于98%的初级烧结体;对该初级烧结体进行次级烧结操作,由此来获得相对密度为98%或者更大的次级烧结体,以使得能够容易地制造这样的耐磨元件,其含有10-3500ppm的fe成分、大于1000ppm至2000ppm的ca成分、和1-2000ppm的mg成分,并且具有抑制到±10%的范围的密度、硬度和断裂韧性的离差。附图说明图1是一横截面图,表示在球形耐磨元件的情况中本发明的一种实施方案的耐磨元件,并且表示出测量该耐磨元件的维氏硬度、断裂韧性和密度的点。图2是一平面图,表示了在矩形耐磨元件的情况中本发明的另外一种实施方案的耐磨元件,并且表示出测量该耐磨元件的维氏硬度、断裂韧性和密度的点。图3是一横截面图,表示用于测量本发明的耐磨(磨损)元件的滚动寿命特性的推力(thrust)类型滚动磨损(磨损)测试设备的结构。具体实施方式接下来,在下面解释根据本发明一种实施方案的耐磨(磨损)元件的实施方案。该实施方案提供了一种由主要由氮化硅组成的陶瓷烧结体所形成的耐磨元件,该陶瓷烧结体的特征在于含有10-3500ppm的按照fe元素计的fe成分、大于1000ppm至2000ppm的按照ca元素计的ca成分、和1-2000ppm的按照mg元素计的mg成分,其中氮化硅晶粒的β-相比是95%或者更大,氮化硅晶粒的最大长径是40μm或者更低,通过xrd(x射线衍射方法)没有检测出存在于晶界相中的ca成分,并且该耐磨元件内部的维氏硬度、断裂韧性和密度中每个的离差处于±10%的范围。在耐磨元件的fe成分、ca成分或者mg成分的含量超过上述范围的情况中,不利的产生了作为破裂起始点的脆性隔离部分,因此容易降低耐磨元件的特性例如硬度、断裂韧性等。所以,当该耐磨元件进行表面加工来制造耐磨装置或者当该耐磨元件实际上用作耐磨元件时,易于发生脱落和破裂。另一方面,在fe成分、ca成分和mg成分小于上述范围的情况中,必需使用高纯度的氮化硅材料粉末来制造该耐磨元件,这样材料成本大幅升高,因此在经济上是不利的。为了提高后述的易磨性(研磨加工的容易性),优选的是将fe成分的含量设定到以fe元素计100-2000ppm的范围内、ca成分的含量设定到以ca元素计为1100ppm-1600ppm的范围内、和mg成分的含量设定到以mg元素计为100ppm-1000ppm的范围内。就此而言,在本发明中“ppm”的单位表示“质量%”。即,在本发明中,因为杂质含量例如fe成分、ca成分和mg成分被控制到上述范围内,因此可以使用廉价的氮化硅原料粉末,其含有相对大量的fe成分、ca成分和mg成分作为杂质。该廉价的氮化硅原料粉末是通过将金属si直接氮化的直接氮化方法来制造的。使用这样的低成本原料是非常有利的,结果是极大地降低了耐磨元件的制造成本。另外,在本发明中,虽然耐磨元件中包含了作为杂质的大量的fe成分、ca成分和mg成分,但是硬度、断裂韧性和密度的离差被抑制到±10%的范围内。所以,甚至在该耐磨元件长期使用的情况中,引起脱落或者破裂的耐磨元件的数量很小,因此可以获得具有优异可靠性的耐磨元件。此外,即使该陶瓷烧结体包含大于1000ppm且2000ppm或者更小的量的ca,当进行xrd分析时,没有检测出ca的化合物。“通过xrd分析没有检测出ca的化合物”表示没有检测到ca的化合物的峰,并且ca的化合物基本上变成无定形相。上述ca的化合物的例子可以包括单物质的ca、ca的氧化物、ca和烧结剂的反应产物等。此外,该xrd分析是在使用cu靶(cukα)的条件下进行的,x射线管电压是40kv,x射线管电流是100ma。此外,ca成分含量可以通过icp分析(诱导性偶合的等离子体质谱法)来检测。因为ca的化合物变成了无定形相,因此能够降低耐磨元件的研磨加工负荷。因为该研磨加工的负荷能够降低至很小,因此容易获得平的研磨的表面,该表面的表面粗糙度ra是1μm或者更低,进一步的0.1μmra或者更低。此外,优选的是通过xrd分析也没有检测出在陶瓷烧结体的晶界相中存在着mg成分的峰。特征“通过xrd分析没有检测出mg的化合物的峰”表示mg的化合物基本变成了无定形相。此外,上述mg的化合物的例子可以包括单物质mg、mg的氧化物,mg和烧结剂的反应产物,和mg和ca的反应产物等。因为mg的化合物变成了无定形相,因此耐磨元件的研磨加工负荷可以进一步降低到很小。晶界相中是否存在ca的化合物和mg的化合物可以通过epma(电子探针微分析)方法,使用彩色成图(colormapping)技术来确认。此外,必需将上述陶瓷烧结体(氮化硅烧结体)的氮化硅晶粒的β-相比设定到95%或者更大。该β-相类型氮化硅晶粒具有三角系晶体,因为能够提高耐磨元件的高温强度。当上述氮化硅晶粒的β-相比小于95%时,陶瓷烧结体的强度不利地降低了。在本发明中,耐磨元件中的氮化硅晶粒的最大长径优选设定为40μm或者更小。换句话说,优选的是在该耐磨元件中不存在长径超过40μm的粗氮化硅晶粒。在其中在该耐磨元件中存在长径超过40μm的粗氮化硅晶粒的情况中,该粗氮化硅晶粒充当了破裂的开始点,因此烧结体的断裂韧性极大降低,并且机械强度也降低了,因此确实不是优选的。就此而言,氮化硅晶粒的最大长径是通过下面的方式来测量的。即,将该耐磨元件切割,并且对切割表面进行镜面抛光。随后,将该镜面抛光的表面进行蚀刻处理,由此除去晶界成分。然后,通过×5000或者更大放大倍率的扫描型电子显微镜(sem)对单位面积(100μm×100μm)进行照相,该单位面积任意选自蚀刻的表面。氮化硅晶粒的最大长径是在照片上所观察的各晶粒的最长直径。因此,当在该耐磨元件的照片上没有观察到长径超过40μm的粗氮化硅晶粒时,实现了本发明的要求。此外,在本发明的耐磨元件中,同样优选的是定义为氮化硅晶粒各长径比的平均值的平均长径比是2或者更大。在长径比小于2的情况中,耐磨元件的微结构将不是其中氮化硅晶粒是以复杂的方式形成的并且彼此复杂缠绕的结构,因此耐磨元件的机械强度等易于变成不足的。就此而言,氮化硅晶粒的长径比(=长径/短径)是通过与上述用于测量氮化硅晶粒的最大长径的相同方法来获得的。即,将该耐磨元件切割,并且对切割表面进行镜面抛光。随后,将该镜面抛光的表面进行蚀刻处理,由此除去晶界成分。然后,通过扫描型电子显微镜(sem)对单位面积表面进行照相。测量在照片上所观察的氮化硅晶粒的长径和短径。结果,长径比是作为长直径与短直径之比来获得的。另外,平均长径比是通过将照片上所显示的在单位面积(100μm×100μm)中所观察的全部氮化硅晶粒的各长径比的平均而获得的。此外,还优选的是该陶瓷烧结体包含1-5质量%的以稀土计的稀土成分和1-5质量%的以al元素计的al成分作为烧结剂。由于烧结剂的存在,可以获得具有高密度的烧结体。稀土元素化合物的例子可以包括稀土氧化物,具体地,钇氧化物、铒氧化物、镱氧化物等。此外,作为al成分,使用氧化铝、氮化铝等。这些成分在陶瓷烧结体中与氮化硅等反应,由此来产生稀土元素-si-al-o-n类型化合物等作为构成晶界相的成分而存在。稀土成分和al成分的量是通过分析各元素的含量来获得的。此外,还优选的是该陶瓷烧结体包含0.1-5质量%的选自下面的至少一种元素:ti、zr、hf、w、mo、ta、nb和cr。这些元素能够有效增强晶界相。在这些元素中,hf是最优选的。hf与稀土元素反应,由此来形成晶体化合物,因此hf能够有效增强晶界相。hf和稀土元素的结晶化合物可以通过xrd分析来鉴定和检测。由于增强的晶界相,能够进一步提高烧结体的硬度和断裂韧性。此外,本发明的耐磨元件具有优异的性能,因此维氏硬度(hv)是1400或者更大,断裂韧性是5.5mpa·m1/2或者更大。在这些耐磨元件具有高硬度和/或高断裂韧性的情况中,各特性的离差受到抑制。此外,即使将维氏硬度(hv)设定为1430或者更高和将断裂韧性设定为6.0mpa·m1/2或者更大,也可以抑制各特性的离差。就此而言,维氏硬度(hv)或者断裂韧性或者密度的离差是按照如下方式来计算的。图1是一横截面图,表示了球形耐磨元件的一个例子,和图2是一平面图,表示了矩形板状耐磨元件的另一例子。在图1所示的球形耐磨元件4的情况中,横截面的中心部分表示为a点,而直线的中间四个点(每个点连接到耐磨元件4的中心点a和周边端点)分别表示为b点、c点、d点和e点。维氏硬度(hv)、断裂韧性和密度是分别在a-e点5个点测量的。将该测量值平均来获得各平均值。另一方面,在图2所示的矩形板状耐磨元件3的情况中,平面的中心部分表示为a点,而直线的中间四个点(每个点连接到耐磨元件3的中心点a和周边端点)分别表示为b点、c点、d点和e点。维氏硬度(hv)、断裂韧性和密度是分别在a-e点5个点测量的。然后将该测量值平均来计算维氏硬度(hv)、断裂韧性和密度的平均值。此外,在许多测量值中,在数字上偏离平均值最大(距离平均值最大的最远值)的最远值定义为“最大偏离值”。然后,将测量平均值和最大偏离值代入下文中的计算式(1)中,由此来计算各离差。离差[%]=[(平均值–最大偏离值)/平均值]×100---(1)就此而言,维氏硬度是根据日本工业标准(jisr1610)所规定的方法来测量的。另外,断裂韧性是通过规定于日本工业标准(jisr1607)中的if方法测量的。此外,密度的离差是按照下面的方式来测量的。即,首先,从5个点(a-e点)上切割下试样。然后,对于各试样,基于阿基米德原理来测量密度,并且对测量值进行平均,由此来获得平均密度。然后,按照与硬度和断裂韧性相同的方式,基于计算式(1)来计算离差(%)。在本发明中,耐磨元件密度的离差也设定为±10%内。就此而言,优选的是该陶瓷烧结体的密度是3.18g/cm3或者更大。此外,更优选的是该陶瓷烧结体的密度是3.25g/cm3或者更大。本发明的这些耐磨元件不仅可以用作构成轴承等的滚珠,而且还可以用作需要耐磨(磨损)性的不同应用所用的结构元件。不同应用的例子可以包括切割工具、旋转夹具(rollingjig)、阀门的检查球(checkball)、发动机零件、各种夹具和工具、各种围栏和各种辊子。具体的,本发明的耐磨元件能够适用于直径为3mm或者更大,进一步的10mm或者更大的大球形(球)体,和短边长度为30mm或者更大,进一步的100mm或者更大的大尺寸元件。本发明可以提供一种耐磨装置。本发明的耐磨装置包含上述耐磨元件,特别是包含许多上述本发明的耐磨元件。具体的,本发明的耐磨装置包含例如使用该耐磨元件作为滚珠的轴承,或者包含这种轴承的装置。在这些耐磨装置中,因为耐磨元件的硬度和断裂韧性的离差被限定到±10%的范围内,因此造成损坏例如脱落或者破裂等的耐磨元件的量是非常小的,因此能够长期抑制振动等的产生,并且该耐磨元件具有优异的可靠性。此外,根据本发明的耐磨装置,可以使用前述相对廉价的含有大量fe成分、ca成分和mg成分的氮化硅材料粉末用于构建耐磨元件,以使得该耐磨装置的成本能够降低到相对廉价。换句话说,可以使用廉价的氮化硅材料粉末和烧结剂粉末(各个含有大量fe成分、ca成分和mg成分作为杂质),来获得进一步的成本降低效应。此外,在本发明中,当进行研磨加工来获得表面粗糙度为1μmra或者更低,进一步的0.1μmra或者更低的陶瓷烧结体时,可以降低研磨加工的负荷,即,当进行研磨加工来获得表面粗糙度为1μmra或者更低的氮化硅烧结体时,通常进行使用金刚石磨石(磨光粉)的研磨加工。在这种情况中,在本发明的耐磨元件中,存在于晶界相中的ca的化合物是作为无定形化合物而存在的,其比结晶化合物软。ca成分在烧结步骤后易于浸泡出到陶瓷烧结体表面上。所以,当ca的化合物的无定形化合物形成于陶瓷烧结体表面上时,该表面能够容易地进行研磨。为此原因,金刚石磨石的损坏是很小的,并且可以减少氮化硅烧结体本身的研磨量(研磨余量)。换句话说,本发明适用于具有研磨的表面的耐磨元件。本发明的耐磨元件可以例如是具有几乎板形状的一种实施方案的耐磨元件,并且该耐磨元件的测试表面进行研磨加工来获得镜面。然后,这样的板形耐磨元件连接到图3所示的滚动磨损测试设备1上。将三个suj2钢滚珠4(每个直径是9.35mm和五级或者更高级的表面状态)置于直径40mm的轨道上,该轨道布置在板形耐磨元件3的顶表面上。当这些钢滚球4以1200rpm的转速如下的条件下旋转时,即,施加负荷来对该滚珠施加最大接触应力5.9gpa的条件下旋转时,优选的是滚动寿命是优选至少2×107,该滚动寿命定义为当板形耐磨元件3脱落时,所发生的旋转数。本发明的耐磨元件例如是滚动寿命为至少2×107的元件,其等于或者长于常规的耐磨元件的滚动寿命。本发明的耐磨元件也可以例如用作球形元件例如滚珠(轴承珠),而非前述的板形元件。在其中本发明的耐磨元件用作滚珠的情况中,对于滚珠的尺寸没有具体限制,例如,可以合适的使用直径为3mm或者更大的滚珠。此外,当直径设定到10mm或者更大,进一步20mm或者更大时,与通过常规方法所制造的常规耐磨元件的这些相比,特性例如滚动寿命等能够明显改进。此外,当该耐磨元件的直径设定到相对高时,与通过使用昂贵的氮化硅材料粉末(通过常规的酰亚胺热分解方法合成)所制造的球形耐磨元件相比,制造的主要成本的差异变得更明显。此外,形成本发明的耐磨元件来提供球形体,其每个的直径是9.35mm。该球形体进行了研磨加工。然后,将这样的球形体连接到图3所示的滚动磨损测试设备上。当将三个球形耐磨元件(滚珠)4(每个的表面状态是5级或者更大)置于直径为40mm的轨道上,该轨道布置在suj2钢板的顶表面上,其测试表面被镜面抛光。然后,当球形耐磨元件4以1200rpm的转速这样的条件下旋转时,即,施加负荷来对该球形耐磨元件4施加最大接触应力5.9gpa的条件下旋转时,优选的是滚动寿命是优选至少400小时,该滚动寿命定义为当球形耐磨元件4的表面脱落时的持续时间。本发明的耐磨元件具有上述至少400小时的滚动寿命,其等于或者长于常规耐磨元件(滚珠)的寿命。接下来,在下文中解释本发明的制造耐磨元件的方法。本发明提供了一种制造由主要由氮化硅组成的陶瓷烧结体所形成的耐磨元件的方法,该方法包含下面的步骤:制备一种材料粉末混合物,其含有氮化硅材料粉末、烧结剂粉末、10-3500ppm的按照fe元素计的fe成分、大于1000ppm至2000ppm的按照ca计的ca成分、和1-2000ppm的按照mg元素计的mg成分;模制该材料粉末混合物,由此来形成模制体;在1600-1950℃的烧结温度对该模制体进行初级烧结操作,由此来获得相对密度为80%或者更高且小于98%的初级烧结体;冷却该初级烧结体,其中在烧结温度到1400℃的温度范围内,将冷却速率控制到100℃/小时或者更大;在1600-1900℃的烧结温度对该初级烧结体进行次级烧结操作,由此来获得相对密度为98%或者更大的次级烧结体;和冷却该次级烧结体,其中在烧结温度到1400℃的温度范围内,将冷却速率控制到100℃/小时或者更大。与使用常规的初级和次级烧结步骤的方法相比,本发明的方法采用其中烧结体的相对密度控制到相对低的80-小于98%的初级烧结步骤,和采用了其中将烧结体的相对密度进一步提高到98%或者更大的次级烧结步骤(致密化的烧结步骤)。当进行上述初级和次级烧结步骤时,甚至在其中材料粉末混合物中的fe成分,ca成分和mg成分的量相对大的情况中,也能够容易地制造耐磨元件,其具有优异的硬度和断裂韧性,并且将硬度和断裂韧性的离差抑制到±10%的范围中。此外,在初级和次级烧结步骤之后,将该烧结体以100℃/h或者更大的冷却速率快速冷却,直到该烧结体的温度低到1400℃,以使得可以防止ca的化合物变成结晶化合物。作为用于制造上述耐磨元件的氮化硅原料粉末,例如优选使用这样的氮化硅原料粉末,其含有10-3500ppm的按照fe元素计的fe成分、大于1000ppm至2000ppm的按照ca计的ca成分、和1-2000ppm的按照mg元素计的mg成分。作为含有处于上述范围内的fe成分、ca成分和mg成分的氮化硅材料粉末,例如合适的可以使用廉价的通过金属氮化方法所制造的氮化硅原料粉末。此外,作为该氮化硅材料粉末,考虑到烧结特性例如弯曲强度和断裂韧性等,优选可以使用这样的氮化硅材料粉末,其含有至少80质量%,优选90-97质量%的α-氮化硅,该α-氮化硅含有1.5质量%或者更低的,优选0.9%-1.2质量%的氧,并且平均粒径是1.2μm或者更低,优选大约0.6-大约1.0μm。就此而言,已知的是氮化硅原料粉末具有α-相类型和β-相类型。由β-相类型氮化硅粉末制成的氮化硅烧结体倾向于具有不足的强度。相反,在烧结操作之后,α-相类型氮化硅材料粉末变成β-相类型氮化硅晶粒,因此这里能够提供高强度的烧结体,其中该具有高长径比的氮化硅晶粒是高度缠绕的。在α-相类型和β-相类型氮化硅材料粉末总量中,当在本发明的方法中将α-相类型氮化硅材料粉末的混合比控制到至少80质量%时,能够改进该耐磨元件的弯曲强度、断裂韧性和滚动寿命。另一方面,考虑到烧结特性,将α-相类型氮化硅材料粉末的混合比限制到97质量%或者更低。优选α-相类型氮化硅材料粉末的量是90-95质量%。此外,作为氮化硅材料粉末,具体的,使用平均粒径为0.8μm或者更低的细原料粉末能够提供孔隙率为2%或者更低的致密烧结体,甚至使用较少量的烧结剂时也是如此,因此是优选的。这种烧结体的孔隙率可以根据阿基米德原理来容易的测量和确定。优选的是将稀土元素加入到该氮化硅原料粉末中作为烧结助剂(烧结剂)。作为稀土元素,优选的是将选自y、ho、er、yb、la、sc、pr、ce、nd、dy、sm和gd等的至少一种元素加入到该氮化硅原料粉末中。这些稀土元素与氮化硅原料粉末反应来产生液相,因此充当了烧结促进剂(烧结剂)。优选的是将稀土元素的添加量控制到相对于包含氮化硅材料粉末和其他烧结助剂的整个材料粉末混合物(下文简称为“材料粉末混合物”)为1-5质量%。当稀土元素的添加量小于1质量%时,所形成的耐磨元件具有不足的密度和强度。具体的,当该稀土元素具有高原子重量的镧系元素时,耐磨元件见具有相对低的强度。另一方面,当烧结助剂的添加量超过5质量%时,产生了过量的晶界相。这能够提高耐磨元件的孔数或者降低强度。此外,还优选的是将铝成分加入到氮化硅原料粉末中。这种铝成分优选作为氧化铝(a12o3)或者氮化铝(aln)来加入。此外,优选的是将这些铝成分的总添加量设定到相对于整个材料粉末混合物为1-5质量%(以al元素计)的范围内。加入氧化铝(al2o3)来提高稀土元素作为烧结促进剂的功能,这允许在低的烧结温度时提高密度,控制晶体结构中的晶粒的生长,和提高机械强度,例如耐磨元件的弯曲强度和断裂韧性等。优选的是在其中氧化铝与aln一起协同使用的情况中,将氧化铝的添加量控制到相对于整个材料粉末混合物为4质量%或者更低的范围内。当氧化铝的添加量大于4质量%时,烧结体中的氧含量升高。该升高的氧含量引起了晶界相中存在的成分不均匀的分布和耐磨元件滚动寿命的降低,因此不是优选的。相反,当氧化铝(al2o3)的添加量小于2质量%时,由于添加al2o3所形成的效应是不足的,因此优选的是将氧化铝的添加量控制到2质量%或者更大。由于上述观点,氧化铝(al2o3)的添加量更优选设定到2质量%至3.5质量%或者更低的范围。另一方面,将氮化铝(aln)理想的以相对于整个材料粉末混合物为3质量%或者更低来加入,来防止或者降低烧结操作过程中氮化硅成分的蒸发,和提高稀土元素作为烧结促进剂的功能。但是,大于3质量%的添加量的aln降低了耐磨元件的机械强度和滚动寿命,因此不是优选的。相反,当氮化铝(aln)的添加量小于1质量%时,通过加入aln引起的上述作用是不足的。因此,aln的添加量优选控制到1质量%或者更大。就此而言,将2-4质量%的al2o3和1-3质量%的aln二者加入到氮化硅材料粉末能够更有效的改进耐磨元件的机械特性。但是,过量的al2o3和aln的总量降低了耐磨(磨损)元件的滚动寿命。因此,将铝成分在原料粉末混合物中的总量优选设定到6质量%或者更低(氧化物当量)。另一方面,优选的是将选自ti、hf、zr、w、mo、ta、nb和cr的氧化物、碳化物、氮化物、硅化物和硼化物中的至少一种化合物加入到氮化硅原料粉末中。这些化合物提高了稀土氧化物等作为烧结促进剂的功能,促进了结晶结构的离差,和改进了包含烧结的氮化硅的耐磨元件的机械强度和滚动寿命。在这些化合物中,ti、mo和hf的化合物是特别优选的。当例如ti等的这些化合物相对于整个材料粉末混合物的添加量按照其元素计小于0.1质量%时,通过加入所述化合物带来的功能是不足的。另一方面,当添加量超过5质量%时,该耐磨元件的机械强度和滚动寿命降低。因此,将该化合物的添加量限制到0.1-5质量%的范围。更理想的,将该化合物的量具体限制到0.5-2质量%的范围。此外,碳化硅(sic)也可以加入到该氮化硅原料粉末中。碳化硅(sic)是作为单个粒子分散在晶体结构中,并且明显改进了耐磨元件的滚动寿命。当碳化硅相对于整个材料粉末混合物的添加量小于2质量%时,通过加入碳化硅所带来的作用是不足的。另一方面,当添加量超过7质量%时,该烧结体导致了不足的致密化和耐磨元件弯曲强度的降低。因此,将碳化硅的量优选限制到2-7质量%的范围。顺便说一下,碳化硅可以分成α-类型和β-类型,其二者都表现出相同的操作作用,因此可以加入任一类型的碳化硅。本发明的耐磨元件是通过例如下面的方法来制造的。即,上述原料粉末混合物是如下来制备的:将预定量的所需添加剂例如烧结助剂(其包含稀土元素,如果需要,包含铝成分例如氧化铝(al2o3)和/或氮化铝(aln),和任选存在的化合物例如ti等)加入到如上所述的氮化硅细粉末中。此外,将有机粘合剂成分加入到这种原料粉末混合物中,由此来制备粒状粉末。同时,在原料粉末混合物中没有预先包含预定量的fe成分、ca成分和mg成分的情况中,通过补足各个成分不足的量来制备该原料粉末混合物。因此,将因此获得的粒状粉末模制成具有预定形状的压实体(模制体)。作为模制粒状粉末的方法,合适的是使用通用的模制压模方法和cip(冷等静压)方法等。在通过模制压模方法和cip(冷等静压)方法形成压实体(模制体)的情况中,该粒状粉末优选在120mpa或者更大的压力下模制来形成晶界相,其中特别是在烧结操作之后,很难形成孔和空穴。当模制压力小于120mpa时,容易形成由稀土元素化合物形成的粘着部分(cohesiveportion)(隔离部分),其主要形成了晶界相。另外,所形成的模制体具有不足的密度,并且该耐磨元件易于产生许多裂纹。另一方面,当模制压力设定超过200mpa时,模制模具的耐久性降低,因此生产率不好。因此,模制压力优选设定为120-200mpa。随后,将模制体(模制压实体)在非氧化性气氛中在600℃-800℃的温度加热或者在空气中在400℃-500℃的温度加热1-2小时,来充分除去有机粘合剂成分,并且使该模制体脱脂。然后,将该脱脂的模制体在惰性气体例如氮气的非氧化性气氛中进行初级烧结步骤,由此将所形成的初级烧结体的相对密度控制到80%或者更高且小于98%。其后,将所形成的初级烧结体进一步在非氧化性气氛中进行次级烧结步骤,以使得所形成的次级烧结体的相对密度控制到98%或者更大,由此来形成氮化硅烧结体(耐磨元件)。就此而言,烧结体的相对密度定义为基于阿基米德原理所测量的实际密度相对于氮化硅烧结体理论密度的比率(%)。作为获得理论密度的方法,该理论密度可以简单地通过下面的简化方法来获得。例如,根据理化词典(physical-chemistrydictionary)等,氮化硅所述的理论密度是3.185g/cm3,钇氧化物(y2o3)是5.03g/cm3,氧化铝(al2o3)是4.0g/cm3,和氧化镁(mgo)是3.58g/cm3。氮化硅烧结体的理论密度还可以通过将y含量转化成钇氧化物,将al成分转化成氧化铝,将mg成分转化成氧化镁,如下来计算。氮化硅烧结体的理论密度=(氮化硅的质量×理论密度+钇氧化物的质量×理论密度+…)例如,当假定各成分的含量是92质量%的氮化硅,5质量%的钇氧化物和3质量%的氧化铝时,具有上述组成的氮化硅烧结体的理论密度是通过下面的计算式来计算的。(氮化硅的质量:0.92×3.185+钇氧化物的质量:0.05×5.03+氧化铝的质量:0.03×4.0)=3.3017g/cm3如上所述,根据本发明,将模制体在初级烧结步骤中烧结,来获得80-98%或者更低的相对密度,其低于通过常规制造方法所制造的烧结体的密度。其后,将该烧结体进一步在次级烧结步骤中烧结,来主要提高烧结体的相对密度。结果,可以将氮化硅烧结体(耐磨元件)的硬度和断裂韧性的离差抑制到±10%的范围内。此外,在初级和次级烧结步骤之后,进行冷却步骤。在冷却步骤中,将该烧结体以100℃/h或者更大的冷却速率快速冷却,直到烧结体的温度降低到1400℃。当该快速冷却步骤是以100℃/h或者更大的冷却速率进行时,晶界相会变成无定形相。当晶界相变成无定形相时,它可以防止ca的化合物变成结晶化合物。对上述冷却速率的上限没有特别的限制,但是,500℃/h或者更低的冷却速率是优选的。烧结温度是1600℃/h或者更大,以使得如果冷却步骤是以超过500℃的冷却速率进行的,则用于冷却设备的负荷变大。将要控制的温度范围设定到烧结温度到1400℃的原因如下。即,当稀土元素化合物和al成分用作烧结剂时,这些成分一度形成了液相。其后,直到1400℃的温度,该液相凝固,由此来完全变成晶界相。就此而言,在1400℃或者更低的温度范围不需要对冷却速率进行特别的控制。此外,当控制这样的冷却速率时,不仅能够形成均匀的晶界相,而且还降低了密度的离差。此外,这里可以获得优异的特性,例如维氏硬度是1400或者更大,和断裂韧性是5.5mpa·m1/2或者更大,优选该维氏硬度是1430或者更大,和该断裂韧性是6.0mpa·m1/2或者更大。另外,硬度或者断裂韧性的离差可以抑制到±10%的范围内。即,当在初级烧结步骤中相对密度设定到小于80%或者大于98%时,难以将氮化硅烧结体(耐磨元件)的维氏硬度和断裂韧性的离差设定到±10%的范围,即使在次级烧结步骤中将相对密度设定为98%或者更大也是如此。在本发明中,从在前述的次级烧结步骤完成时将氮化硅烧结体的密度设定到高密度和将氮化硅烧结体的硬度和断裂韧性的离差抑制到±10%范围的观点来说,优选的是烧结体的密度应当在初级烧结步骤的阶段设定到85%-小于98%的范围内。为了实现初级烧结步骤完成后烧结体的相对密度为80-小于98%,应当在例如1600℃-1950℃的温度进行常压烧结操作或者压力烧结操作2–8小时,更优选在1700℃-1850℃进行2–6小时。当初级烧结步骤的上述烧结温度低于上述温度范围的下限或者当初级烧结步骤的烧结时间小于上述时间范围的下限,则难以在初级烧结步骤完成的阶段将初级烧结体的密度设定到80%或者更大。此外,在其中初级烧结步骤的烧结温度超过上述温度范围上限或者其中初级烧结步骤的烧结时间超过上述时间范围上限的情况中,烧结在初级烧结步骤过度进行,以至于这里会恐怕所形成的初级烧结体的密度超过98%。此外,该次级烧结步骤优选是通过例如进行高温等静压(hip)处理来进行的,在其中将初级烧结体在其中对初级烧结体施加70mpa或者更大优选100mpa或者更大的压力的状态在1600-1900℃的温度进一步烧结0.5-2小时。当次级烧结步骤的上述烧结温度低于上述温度范围的下限或者当压力低于上述范围时,或者当次级烧结步骤的烧结时间小于上述时间范围的下限时,恐怕在次级烧结步骤完成阶段所形成的氮化硅烧结体(次级烧结体)的相对密度将不是98%或者更大的高密度。另外,这里还恐怕难以将氮化硅次级烧结体的硬度,断裂韧性和密度的离差抑制到±10%的范围内。另一方面,当烧结温度超过上述温度范围的上限时,恐怕氮化硅成分易于蒸发和分解。此外,在其中烧结时间超过上述时间范围的上限时,恐怕相对密度无法进一步提高和致密化效应是饱和的,因此增加了制造时间(加工时间),因此不是优选的。此外,当初级和次级烧结操作的时间设定到1600℃或者更高的高温时,烧结剂变成了液体成分,并且例如氮化硅粉末中所包含的ca成分浸泡出到液相中,因此会形成其中ca的化合物存在于烧结体的烧结的表面上的状态。如上所述,根据本发明的制造耐磨元件的方法,当使用含有10-3500ppm的fe成分、大于1000ppm至2000ppm或者更低的ca成分和1-2000ppm的mg成分的材料粉末混合物时,进一步的该烧结操作是分别在两个阶段中进行的,可以制造其中将该氮化硅烧结体的硬度和断裂韧性的离差抑制到±10%的范围内的氮化硅烧结体(耐磨元件)。此外,根据本发明的制造耐磨元件的方法,例如这里可以制造其中氮化硅晶粒长径是40μm或者更低,和平均长径比是2或者更大,优选4或者更大的这样的氮化硅烧结体(耐磨元件)。此外,如果需要,将因此获得的陶瓷烧结体进行研磨加工。在其中将陶瓷烧结体用作耐磨元件的情况中,优选的是进行镜面研磨加工,来获得表面粗糙度ra为1μm或者更低,进一步的0.1μm或者更低。该研磨加工是使用金刚石磨石来进行的。此时,当ca的化合物存在于陶瓷烧结体的烧结的表面时,该烧结的表面的硬度可以稍降低一些。所以,研磨时间可以缩短,并且还会降低金刚石磨石的损伤,因此能够降低研磨加工的负荷。此外,当ca的化合物被配置到存在于烧结的表面上时,研磨余量(待研磨的烧结体的量)会降低。所以,在其中进行镜面研磨加工来获得表面粗糙度ra为1μm或者更低,进一步的0.1μm或者更低的情况中,研磨余量比常规的烧结体小,因此能够获得镜面抛光表面,而不排出废料。此外,根据本发明的制造耐磨元件的方法,在其中耐磨元件具有板形的情况中,可以制造滚动寿命为2×107或者更大的板形耐磨元件,该滚动寿命是通过预定的操作来定义的。此外,在其中耐磨元件为球形的情况中,可以制造球形耐磨元件,其滚动寿命是400小时或者更大,该滚动寿命是通过预定的操作来定义的。实施方案接下来,将参考下述的实施例和对比例来详细具体的解释本发明的实施方案。(实施例1-7和对比例1-4)这里制备了多种si3n4(氮化硅)材料粉末,其是通过金属氮化方法来制造的,并且每个材料粉末包含下表1所示的不同量的fe成分(以fe元素计为10–3500ppm)、ca成分(以ca元素计为50–2000ppm)和mg成分(以ca元素计为10–2000ppm)。将这些氮化硅材料粉末与作为烧结促进剂(烧结剂)的y2o3(钇氧化物)粉末、al2o3(氧化铝)粉末、aln(氮化铝)粉末和hfo2(二氧化铪)粉末进行混合,由此来制备各自含有表1所示量的fe成分、ca成分和mg成分的材料粉末混合物。就此而言,在其中氮化硅材料粉末中的fe,ca和mg的量不足的情况中,通过进一步加入氧化物到氮化硅材料粉末中来控制所述量从而获得表1所示的含量值。就此而言,使用各自具有平均粒径为0.3-1.5μm的氮化硅材料粉末和烧结促进剂粉末。此外,在该材料粉末混合物中,y2o3的含量是3质量%,aln的含量是2质量%,hfo2是1质量%,并且补足量是氮化硅材料粉末。例如,非氮化硅材料粉末的材料粉末,即,y2o3粉末、al2o3粉末、aln粉末和hfo2粉末中的每种作为烧结促进剂,其包含10ppm或者更低量的fe成分、ca成分和mg成分。将每种材料粉末混合物在乙醇中使用氮化硅球作为研磨介质进行湿磨(共混和研磨)48小时,然后干燥来制备均匀的材料粉末混合物。此外,将有机粘合剂加入到每种均匀的材料粉末混合物中,由此来制备共混的粒状粉末。[表1]接下来,将每个共混的粒状粉末以150mpa的模压力进行压模,由此来制备多个模制体。随后,将这些模制体在温度450℃的空气流动气氛中脱脂4小时。其后,将每个脱脂的模制体在表2所示的烧结条件下、在压力0.7mpa的氮气氛下进行初级烧结步骤(操作),由此来形成各初级烧结体。此外,将每个初级烧结体然后在表2所示的烧结条件下进行次级烧结步骤,由此来制造各次级烧结体和来提供由氮化硅烧结体组成的各耐磨性元件。就此而言,上述的次级烧结步骤是作为其中在氮气氛中对该初级烧结体施加了100mpa的压力的高温等静压(hip)方法来进行的。测量了在初级烧结步骤之后烧结体的密度(相对密度)和次级烧结步骤之后烧结体的密度(相对密度)。各测量结果表示在下面的表2中。就此而言,每个烧结体的密度(相对密度)(%)是作为通过阿基米德原理所测量的实际的密度相对于氮化硅烧结体的理论密度比率(%)来测量的。[表2]就此而言,烧结体的密度(其是通过阿基米德原理测量的)是3.10g/cm3-3.26g/cm3。具体的,烧结体实际测量值如下。在实施例1中,初级烧结体的密度是3.24g/cm3,而次级烧结体的密度是3.26g/cm3。在实施例1中,初级烧结体的密度是3.24g/cm3,而次级烧结体的密度是3.26g/cm3。在实施例2中,初级烧结体的密度是3.24g/cm3,而次级烧结体的密度是3.26g/cm3。在实施例3中,初级烧结体的密度是3.24g/cm3,而次级烧结体的密度是3.26g/cm3。在实施例4中,初级烧结体的密度是3.16g/cm3,而次级烧结体的密度是3.18g/cm3。在实施例5中,初级烧结体的密度是3.23g/cm3,而次级烧结体的密度是3.25g/cm3。在实施例6中,初级烧结体的密度是3.25g/cm3,而次级烧结体的密度是3.28g/cm3。在实施例7中,初级烧结体的密度是3.14g/cm3,而次级烧结体的密度是3.16g/cm3。在对比例1中,初级烧结体的密度是3.12g/cm3,而次级烧结体的密度是3.15g/cm3。在对比例2中,初级烧结体的密度是3.12g/cm3,而次级烧结体的密度是3.13g/cm3。在对比例3中,初级烧结体的密度是3.10g/cm3,而次级烧结体的密度是3.14g/cm3。在对比例4中,初级烧结体的密度是3.10g/cm3,而次级烧结体的密度是3.15g/cm3。此外,在实施例1-7和对比例1–2的氮化硅烧结体中,氮化硅晶粒的β-相比是95-98%。另一方面,在对比例3–4的氮化硅烧结体中,氮化硅晶粒的β-相比是90-92%。接下来,对于因此根据每个实施例和对比例所制造的耐磨元件,测量了维氏硬度、断裂韧性值,及其平均值、其离差、和滚动寿命。就此而言,维氏硬度是根据日本工业标准(jis-r-1610)规定的方法测量的。根据每个实施例和对比例的耐磨元件3的维氏硬度的平均值是通过对在图2所示的a-e五个测量点上测量的五个测量值进行平均来获得的。此外,维氏硬度的离差是通过下面的方式来获得的。即,在所测量的5个值中,将在数字上与平均值偏离最大的最远值(远离平均值最大的最远值)定义为“最大偏离值”。然后,将所测量的平均值和最大偏离值代入下面的计算式中,由此来计算维氏硬度的离差。离差[%]=[(平均值–最大偏离值)/平均值]×100另外,断裂韧性是根据日本工业标准(jis-r-1607)规定的if方法来测量的。此外,通过与维氏硬度的这些相同的方法来获得平均值和断裂韧性的离差。各耐磨(磨损)元件中每个的滚动寿命是通过使用图3所示的推力类型滚动磨损(磨损)测试设备1来测量的。该推力类型滚动磨损测试设备1配置为包含:布置在测试设备1的主体2上的板形耐磨(磨损)元件3;布置在耐磨元件3上表面上的三个钢滚珠4;布置在钢滚珠4上的导板5;连接到导板5上的驱动轴6;和用于限定各钢滚珠4之间的间隔的支持架(固定器)7。主体2填充有润滑油8,用于润滑滚动部分。在这种测量操作中,作为用于推力类型滚动磨损(磨损)测试设备1的板形耐磨(磨损)元件3,使用了这样的测试样品,其是通过将实施例和对比例的每个耐磨元件加工成尺寸为70mm×70mm×3mm(厚度)的样品而形成的。此时,将板形元件(耐磨元件)3的表面粗糙度(ra)设定为0.01μm。此外,作为用于推力类型滚动磨损(磨损)测试设备1的滚珠4,使用了每个由suj2构成并且直径是9.35mm的球形珠。在这种推力类型滚动磨损测试设备中,对suj2滚珠4施加一定的负荷,来施加5.9gpa的最大接触应力。在这个条件下,这些滚珠4以1200rpm的速度旋转。然后,当由耐磨元件构成的板形元件3的表面脱落时,测量随时间所发生的旋转数。就此而言,通过将作为最大旋转数的上限设定到3×107来测量旋转数。表3表示了测量结果。[表3]从上表3所示的结果中很显然,在各实施例1–7的耐磨元件中,其中进行初级烧结步骤来获得80-小于98%的相对密度,和进行次级烧结步骤来获得98%或者更大的相对密度,证实了将维氏硬度和断裂韧性二者的离差控制到±10%的范围内。此外,还证实了实施例1–7的每个板形耐磨元件的全部的滚动寿命超过了3×107圈,并且该耐磨元件还具有优异的滚动寿命。接下来,对于因此根据每个实施例和对比例所制造的耐磨元件来说,测量了氮化硅晶粒的长径的最大值,同时计算了氮化硅晶粒的平均长径比。氮化硅晶粒的长径的最大值是通过下面的方式来测量的。即,切割所述的耐磨元件。随后,通过×5000或者更大的放大倍率的扫描类型的电子显微镜(sem),对任选自切割表面的单位面积(100μm×100μm)进行照相。观察照片上该单位面积内所选择的具有最大长径的氮化硅晶粒,并且测量所选择的氮化硅晶粒的长径,使得所测量的长径定义为长径的最大值。此外,平均长径比是通过下面的方式来计算的。即,对于存在于所观察的照片中上述单位面积内的全部的氮化硅晶粒,测量长径和短径,由此从每个氮化硅晶粒的长径和短径来获得长径比。结果,平均长径比是通过将各长径比平均来计算的。表4表示了测量结果。[表4]从上表4所示的结果中很显然,在各实施例1–7的耐磨元件中,其中进行初级烧结步骤来获得80-小于98%的相对密度,和进行次级烧结步骤来获得98%或者更大的相对密度,证实了长径的氮化硅晶粒的最大值是40μm或者更低,和在该耐磨元件的结构中没有产生长径超过40μm的任何粗的氮化硅晶粒。此外,在各实施例1–7的每个耐磨元件中,氮化硅晶粒的平均长径比是2或者更大,并且证实了该耐磨元件形成了其中柱形氮化硅晶粒彼此复杂缠绕的微观结构。接下来,制备了与各实施例1–7和对比例1的耐磨元件相同的氮化硅烧结体。对于各氮化硅烧结体的烧结的表面和研磨的表面,进行了xrd分析,来证实是否检测到ca的化合物或者mg的化合物的结晶峰。另外,当每个氮化硅元件进行了研磨加工来获得1μm或者0.1μm的表面粗糙度ra时,测量了研磨加工的负荷。就此而言,通过假定对比例1的研磨时间是100作为比率基准,将该研磨加工的负荷表示为研磨时间的比率。表5表示了测量结果。[表5]从上表5所示的结果中很显然,作为对各实施例的陶瓷烧结体进行xrd分析的结果,在各陶瓷烧结体的烧结的表面和研磨的表面二者的全部都没有检测出ca的化合物或者mg的化合物的结晶峰。结果,证实了结晶ca的化合物或者mg的化合物没有存在于各耐磨元件中。另外,还证实了目标的研磨的表面能够以比对比例1更短的研磨加工时间来获得。相反在对比例1中,检测到y-hf-o类型结晶化合物的衍射峰。(实施例8-11和对比例5)接下来,在其中制造了作为一种耐磨元件的滚珠(轴承珠)的情况中,将评价因此所制造的滚珠的特性。制备了用于各实施例8-11和对比例5的多种材料粉末混合物,从而具有下表6所示的组成。[表6]接下来,将该材料粉末混合物模制,由此来形成具有表6所示的上述组成的轴承珠模制体。然后,将该轴承珠模制体在表8所示的条件下进行初级烧结操作和次级烧结操作,由此来制造具有表7所示直径的各轴承珠。[表7]样品no.轴承珠直径(mm)实施例83实施例910实施例1015实施例1120对比例53[表8]接下来,对于图1所示的因此获得的各自轴承珠的横截面上设的五个测量点a–e来说,测量了其维氏硬度、断裂韧性、密度和离差。要注意的是,该测量方法与实施例1所用的方法相同。此外,还测量了该轴承珠的滚动寿命。使用图3所示的前述推力类型滚动磨损(研磨)测试设备1,测量作为耐磨元件的滚珠的滚动寿命。就此而言,在前述的用于测量板形耐磨元件的滚动寿命而提出的方法中,图3所示的板形元件3由耐磨元件构成,而滚珠4由suj2构成。但是,与前述情况相比,在本发明的测量方法中,将由suj2构成的板形元件用作板元件3,同时使用了滚珠4(表面粗糙度ra为0.01μm),其是通过加工实施例8-11和对比例5的耐磨元件来形成。在这种使用推力类型的滚动磨损测试设备1的测量操作中,对滚珠4(每个由耐磨元件构成)施加负荷,来接收最大5.9gpa的接触应力。在这种条件下,驱动轴6和这些滚珠4是以1200rpm的转速来旋转的。然后,测量当由耐磨元件构成的滚珠4的表面脱落时的时间作为滚动寿命。就此而言,通过设定上限400小时作为最大旋转时间(小时)来测量旋转时间。表9表示了测量结果。[表9]从上表9所示的结果中很显然,在每个由各实施例8–11的耐磨元件构成的滚珠中,证实了维氏硬度、断裂韧性值和密度全部的离差都是小的。此外,氮化硅晶粒的最大长径全部是0.01μm或者更小,和长径比是2或者更大。另外,因此获得的各轴承珠的每个的密度是3.18g/cm3或者更大。另一方面,在轴承珠是对比例5的耐磨元件的情况中,断裂韧性的离差是大的。此外,对由各实施例8-11和对比例5的氮化硅烧结体构成的轴承珠的烧结的表面和研磨的表面进行xrd分析,由此来确定能否检测出ca的化合物的结晶峰。此外,测量了研磨加工的负荷。通过假定对比例5中的研磨时间是100来作为比率基准,将研磨加工的负荷表示为研磨时间的比率。表10表示了测量结果。[表10]从表10所示的结果中很显然,与其中检测出ca的化合物晶体的对比例5的轴承珠相比,在每个由其中没有检测出ca的化合物的各实施例8–11的耐磨元件构成的轴承珠的情况中,很显然能够明显缩短研磨时间,因此它还证实了能够明显降低加工成本。即,本发明实施例的轴承珠能够通过400小时的研磨测试,进一步的能够降低研磨加工的负荷。此外,同样很显然通过更短的研磨时间能够获得相同的表面粗糙度。所以,该耐磨元件的制造成本能够明显降低和改进。工业应用性如上所述,根据本发明的由主要由氮化硅烧结体组成的陶瓷烧结体所形成的耐磨元件,该陶瓷烧结体含有10-3500ppm的按照fe元素计的fe成分、大于1000ppm至2000ppm或者更低的按照ca元素计的ca成分、和1-2000ppm的按照mg元素计的mg成分,以使得这里能够提供其中将耐磨元件的密度、硬度和断裂韧性中每个的离差抑制到±10%的范围内的耐磨元件,并且该耐磨元件具有优异的可靠性和低成本性能。此外,根据本发明,可以获得烧结的表面(烧结完成表面),其易于研磨。此外,根据该制造耐磨元件的方法,如下来制造该耐磨元件:制备一种材料粉末混合物,其含有氮化硅材料粉末、烧结剂粉末、10-3500ppm的按照fe元素计的fe成分、大于1000ppm至2000ppm的按照ca元素计的ca成分、和1-2000ppm的按照mg元素计的mg成分;模制该材料粉末混合物,由此来形成模制体;对该模制体进行初级烧结操作,由此来获得相对密度为80%或者更高且小于98%的初级烧结体;和对该初级烧结体进行次级烧结操作,由此来获得相对密度为98%或者更大的次级烧结体,使得这里能够容易的制造这样一种耐磨元件,其含有10-3500ppm的fe成分、大于1000ppm至2000ppm的ca成分、和1-2000ppm的mg成分,并且具有被抑制到±10%范围内的密度、硬度和断裂韧性。参考标记列表1…推力类型滚动磨损(磨损)测试设备,2…设备体,3…板形耐磨元件(或者suj2金属板),4…滚珠(或者球形耐磨元件),5…导板,6…驱动旋转轴,7…固定器,8…润滑油。当前第1页12