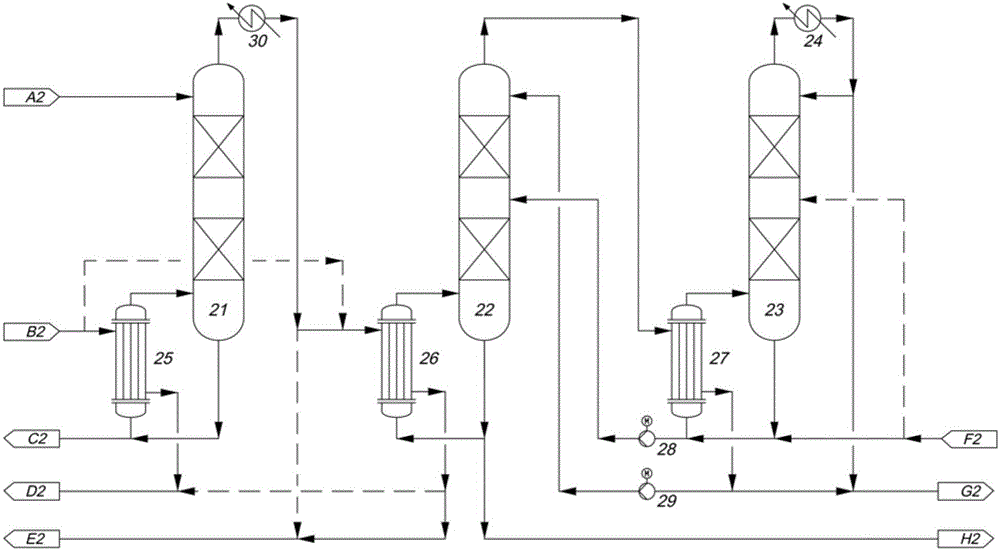
本实用新型属于精馏
技术领域:
,特别是涉及一种己内酰胺系统的节能装置。
背景技术:
:目前,国内己内酰胺装置一般采取氨肟化工艺,氨肟化工艺是近几年开发出来的一种环己酮肟生产的新工艺,它采用双氧水、液氨、环己酮为原料,一步反应直接生成环己酮肟,在发烟硫酸的作用下生产己内酰胺。改工艺有生产流程短,控制简便,设备、管线材质要求一般,三废排放量少等优点。对于以苯为原料的10万吨/年己内酰胺大型化工生产装置,一般包含的主要装置有环己酮、环己酮肟化、己内酰胺精制、硫铵装置、双氧水制备装置等。在环己酮肟化工段,为加快氨肟化反应的传质效果,在反应中引入叔丁醇作为环己酮肟的溶剂,使反应物及反应产物在反应器中达到均匀混合。反应液首先通过过滤将催化剂等不溶物与叔丁醇、水、环己酮肟分离,由于叔丁醇作为环己酮肟的有机溶剂,不参与反应,且对后续重排产生不利影响,为提高己内酰胺的收率及叔丁醇的利用率,需对其进行回收利用。由于叔丁醇-水-环己酮肟体系的沸点及相对挥发度相差较大,可采用传统的精馏技术进行分离,目前工业上的单塔精馏工艺存在蒸汽消耗较大的问题。在己内酰胺精制工段,为提纯己内酰胺需要用有机萃取剂对己内酰胺进行萃取,再用水对有机萃取剂中的己内酰胺进行反萃。萃取过程中,由于副产物在有机萃取剂中的累积,必须对有机萃取剂进行再生。目前,有机萃取剂再生全部采用蒸馏的方法,将有机萃取剂从塔顶蒸出来提纯,国内大都采用单塔蒸馏,能耗高,造成己内酰胺生产成本的增加。若能通过各种手段实现塔顶冷凝负荷和塔釜加热负荷消耗将至最小,实现生产过程的节能降耗,降低生产成本,可以提高己内酰胺生产工艺的竞争优势,具有重大的意义。技术实现要素:本实用新型的目的是克服现有技术的不足,提供一种己内酰胺系统的节能装置。本发明的第二个目的是提供另一种己内酰胺系统的节能装置。本实用新型的技术方案概述如下:第一种己内酰胺系统的节能装置,包括高压苯蒸馏塔1、低压有机溶剂精馏塔2、低压塔顶冷凝器3、高压塔釜再沸器4、第一低压塔釜再沸器5、第二低压塔釜再沸器6;粗苯原料罐区A通过管道与高压苯蒸馏塔1的上部连接,高压苯蒸馏塔1的顶部通过管道与第一低压塔釜再沸器5连接后再与精苯有机溶剂罐区E连接;高压苯蒸馏塔1的底部通过管道分别与高压塔釜再沸器4的底部和粗苯重组分分离装置C连接;高压塔釜再沸器4的顶部通过管道与高压苯蒸馏塔1的下部连接;有机溶剂进料罐区G通过管道与低压有机溶剂精馏塔2的中部连接,低压有机溶剂精馏塔2的顶部通过管道与低压塔顶冷凝器3连接后分两路,一路与低压有机溶剂精馏塔2的上部连接,另一路与有机溶剂罐区F连接;低压有机溶剂精馏塔2 的底部通过管道分别与第一低压塔釜再沸器5底部、第二低压塔釜再沸器6的底部和塔釜液罐区H连接,第一低压塔釜再沸器5和第二低压塔釜再沸器6的顶部分别通过管道与低压有机溶剂精馏塔2的下部连接;生蒸汽罐区B通过管道分别与高压塔釜再沸器4和第二低压塔釜再沸器6的壳程入口连接后再与生蒸汽冷凝水罐区D连接。第二种己内酰胺系统的节能装置,包括高压苯蒸馏塔21、中压有机溶剂精馏塔22、低压有机溶剂精馏塔23、低压塔顶冷凝器24、高压塔釜再沸器25、中压塔釜再沸器26、低压塔釜再沸器27、第一泵28、第二泵29、高压塔顶辅助冷凝器30;粗苯原料罐区A2通过管道与高压苯蒸馏塔21的上部连接,高压苯蒸馏塔21的顶部通过管道与高压塔顶辅助冷凝器30连接后分两路,一路与中压塔釜再沸器26连接后再与精苯有机溶剂罐区E2连接,另一路直接与精苯有机溶剂罐区E2连接;高压苯蒸馏塔21的底部通过管道分别与高压塔釜再沸器25的底部和粗苯重组分分离装置C2连接;高压塔釜再沸器25的顶部通过管道与高压苯蒸馏塔21的下部连接;有机溶剂进料罐区F2通过管道分别与低压有机溶剂精馏塔23的中部和低压有机溶剂精馏塔23的底部连接,低压有机溶剂精馏塔23的顶部通过管道与低压塔顶冷凝器24连接后分两路,一路与低压有机溶剂精馏塔23的上部连接,另一路与有机溶剂罐区G2连接;低压有机溶剂精馏塔23的底部通过管道分别与低压塔釜再沸器27的底部和第一泵28连接,第一泵28通过管道与中压有机溶剂精馏塔22的中部连接;低压塔釜再沸器27的顶部通过管道与低压有机溶剂精馏塔23的下部连接,中压有机溶剂精馏塔22的顶部通过管道与低压塔釜再沸器27连接后分两路,一路与第二泵29连接后再与中压有机溶剂精馏塔22上部连接,另一路通过管道与有机溶剂罐区G2连接;中压有机溶剂精馏塔22的底部通过管道分别与中压塔釜再沸器26的底部和塔釜液罐区H2连接;中压塔釜再沸器26的顶部通过管道与中压有机溶剂精馏塔22的下部连接;生蒸汽罐区B2通过管道分别与高压塔釜再沸器25和中压塔釜再沸器26的壳程入口连接后再与生蒸汽冷凝水罐区D2连接。本实用新型的优点:1.高压苯蒸馏塔的塔顶蒸汽用于加热有机溶剂精馏塔塔釜再沸器,实现了苯蒸馏塔的塔顶蒸汽潜热的回收利用。2.有机溶剂回收采用双效逆流精馏时,中压有机溶剂精馏塔塔顶冷凝负荷与低压有机溶剂精馏塔塔釜再沸器热负荷相匹配,实现热耦合精馏。3.有机溶剂回收采用双效逆流精馏时,保证了各塔较低的塔底温度,防止产品分解及副反应的发生。附图说明图1为一种己内酰胺系统的节能装置示意图。图2为另一种己内酰胺系统的节能装置示意图。具体实施方式下面结合附图通过具体实施例对本实用新型作进一步详述,但以下实施例只是描述性的,不是限定性的,不能以此限定本实用新型的保护范围。第一种己内酰胺系统的节能装置,见图1,包括高压苯蒸馏塔1、低压有机溶剂精馏塔2、 低压塔顶冷凝器3、高压塔釜再沸器4、第一低压塔釜再沸器5、第二低压塔釜再沸器6;粗苯原料罐区A通过管道与高压苯蒸馏塔1的上部连接,高压苯蒸馏塔1的顶部通过管道与第一低压塔釜再沸器5连接后再与精苯有机溶剂罐区E连接;高压苯蒸馏塔1的底部通过管道分别与高压塔釜再沸器4的底部和粗苯重组分分离装置C连接;高压塔釜再沸器4的顶部通过管道与高压苯蒸馏塔1的下部连接;有机溶剂进料罐区G通过管道与低压有机溶剂精馏塔2的中部连接,低压有机溶剂精馏塔2的顶部通过管道与低压塔顶冷凝器3连接后分两路,一路与低压有机溶剂精馏塔2的上部连接,另一路与有机溶剂罐区F连接;低压有机溶剂精馏塔2的底部通过管道分别与第一低压塔釜再沸器5底部、第二低压塔釜再沸器6的底部和塔釜液罐区H连接,第一低压塔釜再沸器5和第二低压塔釜再沸器6的顶部分别通过管道与低压有机溶剂精馏塔2的下部连接;生蒸汽罐区B通过管道分别与高压塔釜再沸器4和第二低压塔釜再沸器6的壳程入口连接后再与生蒸汽冷凝水罐区D连接。第二种己内酰胺系统的节能装置,见图2,包括高压苯蒸馏塔21、中压有机溶剂精馏塔22、低压有机溶剂精馏塔23、低压塔顶冷凝器24、高压塔釜再沸器25、中压塔釜再沸器26、低压塔釜再沸器27、第一泵28、第二泵29、高压塔顶辅助冷凝器30;粗苯原料罐区A2通过管道与高压苯蒸馏塔21的上部连接,高压苯蒸馏塔21的顶部通过管道与高压塔顶辅助冷凝器30连接后分两路,一路与中压塔釜再沸器26连接后再与精苯有机溶剂罐区E2连接,另一路直接与精苯有机溶剂罐区E2连接;高压苯蒸馏塔21的底部通过管道分别与高压塔釜再沸器25的底部和粗苯重组分分离装置C2连接;高压塔釜再沸器25的顶部通过管道与高压苯蒸馏塔21的下部连接;有机溶剂进料罐区F2通过管道分别与低压有机溶剂精馏塔23的中部和低压有机溶剂精馏塔23的底部连接,低压有机溶剂精馏塔23的顶部通过管道与低压塔顶冷凝器24连接后分两路,一路与低压有机溶剂精馏塔23的上部连接,另一路与有机溶剂罐区G2连接;低压有机溶剂精馏塔23的底部通过管道分别与低压塔釜再沸器27的底部和第一泵28连接,第一泵28通过管道与中压有机溶剂精馏塔22的中部连接;低压塔釜再沸器27的顶部通过管道与低压有机溶剂精馏塔23的下部连接,中压有机溶剂精馏塔22的顶部通过管道与低压塔釜再沸器27连接后分两路,一路与第二泵29连接后再与中压有机溶剂精馏塔22上部连接,另一路通过管道与有机溶剂罐区G2连接;中压有机溶剂精馏塔22的底部通过管道分别与中压塔釜再沸器26的底部和塔釜液罐区H2连接;中压塔釜再沸器26的顶部通过管道与中压有机溶剂精馏塔22的下部连接;生蒸汽罐区B2通过管道分别与高压塔釜再沸器25和中压塔釜再沸器26的壳程入口连接后再与生蒸汽冷凝水罐区D2连接。实施例1采用第一种装置的操作方法如下:来源于废水进料罐区A的废水原料进入高压苯蒸馏塔1进行汽提分离,高压苯蒸馏塔塔顶蒸汽经过第一低压塔釜再沸器5冷凝后采出至精苯有机溶剂罐区E;高压苯蒸馏塔1塔釜液相分为两股,一股通过高压塔釜再沸器4蒸发后返回高压苯蒸馏塔1,另一股排至粗苯重组分分离工段C;来自有机溶剂进料罐区G的有机溶剂进入低压有机溶剂精馏塔2中进行精馏,低压有机溶剂精馏塔2的塔顶蒸汽经低压塔顶冷凝器3冷凝后分两股,一股回流至低压 有机溶剂精馏塔2,另一股排至有机溶剂罐区F;低压有机溶剂精馏塔2塔釜液相分三股,前两股分别通过第一低压塔釜再沸器5和第二低压塔釜再沸器6蒸发后返回低压有机溶剂精馏塔2,另一股排至塔釜液罐区(H);来源于生蒸汽罐区B的生蒸汽作为高压塔釜再沸器4和第二低压塔釜再沸器6的热源,换热后通入生蒸汽冷凝液罐区D。对于山东某年产100kt的己内酰胺装置:环己酮肟化工段,有机溶剂进料罐区F的质量组成为:叔丁醇含量42.97%,环己酮肟含量19%、水含量35.3%、氨含量2.5%、环己酮含量0.1%、环己醇含量0.1%、甲苯含量0.1%、其它杂质含量0.2%。己内酰胺精制工段,粗苯进料罐区A的质量组成为:苯含量99.4%,水含量0.1%,环己酮含量0.1%,环己醇含量0.1%,苯胺含量0.1%,其它杂质含量0.2%。高压苯蒸馏塔操作压力为0.18MPaA,塔顶温度99.9℃,塔釜温度108.7℃,塔理论级数为8;低压有机溶剂精馏塔操作压力为0.09MPaA,塔顶温度46.5℃,塔釜温度81.7℃,塔理论级数为30,质量回流比为0.05。经上述过程,各塔顶塔釜出料到达该厂处理要求。由于该工艺考虑了充分的热耦合,各塔的负荷如表1(括号内为节省的加热或冷却热负荷):表1冷却负荷/KW加热负荷/KW合计/KW高压苯蒸馏塔(6538)68546854(13392)低压有机溶剂精馏塔141487599(6215)21747(27962)合计14148(20686)14453(20668)28601(41354)本实施例未耦合时,各塔总的加热负荷为20668KW,冷凝负荷为20686KW,总的热负荷为41354KW;耦合后,各塔总的加热负荷为14453KW,冷凝负荷为14148KW,总的热负荷为28601KW;加热负荷节能30.1%,冷凝负荷节能31.6%,总的热负荷节能30.8%。本实施例的环己酮肟化工段的溶剂回收塔的部分热量来源于己内酰胺精制工段的苯蒸馏塔的塔顶蒸汽冷凝,实现了己内酰胺系统的节能优化。实施例2采用第二种装置的操作方法如下:来源于废水进料罐区A2的废水原料进入高压苯蒸馏塔21进行汽提分离,高压苯蒸馏塔塔顶蒸汽经过高压塔顶辅助冷凝器30(该冷凝器不工作),通入中压塔釜再沸器26,冷凝后采出至精苯有机溶剂罐区E2;高压苯蒸馏塔21塔釜液相分为两股,一股通过高压塔釜再沸器25蒸发后返回高压苯蒸馏塔21,另一股排至粗苯重组分分离工段C2;来自有机溶剂进料罐区F2的有机溶剂进入低压有机溶剂精馏塔23中进行精馏,低压有机溶剂精馏塔23的塔顶蒸汽经低压塔顶冷凝器24冷凝后分两股,一股回流至低压有机溶剂精馏塔23,另一股排至有机溶剂罐区G2;低压有机溶剂精馏塔23塔釜液相分两股,一股通过低压塔釜再沸器27蒸发后返回低压有机溶剂精馏塔23,另一股通过第一泵28加压后进入中压有机溶剂精馏塔22中继续精馏;中压有机溶剂精馏塔22的塔顶蒸汽作为低压有机溶剂精馏塔23的热源,经低 压塔釜再沸器27冷凝后分两股,一股通过第二泵29回流至中压有机溶剂精馏塔,另一股排至有机溶剂罐区G2;中压有机溶剂精馏塔22塔釜液相分两股,一股通过中压塔釜再沸器26蒸发后返回中压有机溶剂精馏塔22,另一股排至塔釜液罐区H2。来源于生蒸汽罐区B2的生蒸汽作为高压塔釜再沸器25的热源,换热后通入生蒸汽冷凝液罐区D2。对于山东某年产100kt的己内酰胺装置:环己酮肟化工段,有机溶剂进料罐区F的质量组成为:叔丁醇含量42.97%,环己酮肟含量19%、水含量35.3%、氨含量2.5%、环己酮含量0.1%、环己醇含量0.1%、甲苯含量0.1%、其它杂质含量0.2%。己内酰胺精制工段,粗苯进料罐区A的质量组成为:苯含量99.4%,水含量0.1%,环己酮含量0.1%,环己醇含量0.1%,苯胺含量0.1%,其它反应副产物含量0.2%。高压苯蒸馏塔操作压力为0.15MPaA,塔顶温度126℃,塔釜温度126.8℃,塔理论级数为8;中压有机溶剂精馏塔操作压力为0.19MPaA,塔顶温度89.3℃,塔釜温度120℃,塔理论级数为15,质量回流比0.03;低压有机溶剂精馏塔操作压力为0.08MPaA,塔顶温度43.2℃,塔釜温度75.5℃,塔理论级数为30,质量回流比0.05。经上述过程,各塔顶塔釜出料到达该厂处理要求。由于该工艺考虑了充分的热耦合,各塔的负荷如表2(括号内为节省的加热或冷却热负荷):表2冷却负荷/KW加热负荷/KW合计/KW高压苯蒸馏塔(6538)68546854(13392)中压有机溶剂精馏塔(6190)(6215)(12405)低压有机溶剂精馏塔6275(5844)6275(12119)合计6275(19003)6854(18913)13129(37916)本实施例未耦合时,各塔总的加热负荷为18913KW,冷凝负荷为19003KW,总的热负荷为37916KW;耦合后,各塔总的加热负荷为6854KW,冷凝负荷为6275KW,总的热负荷为13129KW;加热负荷节能63.8%,冷凝负荷节能67.0%,总的热负荷节能65.4%。本实施例的环己酮肟化工段的溶剂回收塔采用双效逆流精馏,中压有机溶剂精馏塔的塔顶蒸汽作为低压有机溶剂精馏塔的热源,同时中压有机溶剂精馏塔的热源来源于己内酰胺精制工段的苯蒸馏塔的塔顶蒸汽冷凝,大大节省的己内酰胺系统的能耗,实现了己内酰胺系统的节能优化。实施例3采用第二种装置的另一种操作方法如下:来源于废水进料罐区A2的废水原料进入高压苯蒸馏塔21进行汽提分离,高压苯蒸馏塔塔顶蒸汽经过高压塔顶辅助冷凝器30冷凝后采出至精苯精苯有机溶剂罐区E2;高压苯蒸馏塔21塔釜液相分为两股,一股通过高压塔釜再沸器25蒸发后返回高压苯蒸馏塔21,另一股排至粗苯重组分分离工段C2;来自有机溶剂进料罐区F2的有机溶剂进入低压塔釜再沸器27中进行精馏,低压有机溶剂精馏塔23的塔顶蒸汽经低压塔顶冷凝器24冷凝后分两股,一股 回流至低压有机溶剂精馏塔23,另一股排至有机溶剂罐区G2;低压有机溶剂精馏塔23塔釜液相分两股,一股通过低压塔釜再沸器27蒸发后返回低压有机溶剂精馏塔23,另一股通过第一泵28加压后进入中压有机溶剂精馏塔22中继续精馏;中压有机溶剂精馏塔22的塔顶蒸汽作为低压有机溶剂精馏塔23的热源,经低压塔釜再沸器27冷凝后分两股,一股通过第二泵29回流至中压有机溶剂精馏塔,另一股排至有机溶剂罐区G2;中压有机溶剂精馏塔22塔釜液相分两股,一股通过中压塔釜再沸器26蒸发后返回中压有机溶剂精馏塔22,另一股排至塔釜液罐区H2。来源于生蒸汽罐区B2的生蒸汽作为高压塔釜再沸器25与中压塔釜再沸器26的热源,换热后通入生蒸汽冷凝液罐区D2。对于山东某年产100kt的己内酰胺装置:环己酮肟化工段,有机溶剂进料罐区F的质量组成为:叔丁醇含量42.97%,环己酮肟含量19%、水含量35.3%、氨含量2.5%、环己酮含量0.1%、环己醇含量0.1%、甲苯含量0.1%、其它杂质含量0.2%。己内酰胺精制工段,粗苯进料罐区A的质量组成为:苯含量99.4%,水含量0.1%,环己酮含量0.1%,环己醇含量0.1%,苯胺含量0.1%,其它反应副产物含量0.2%。高压苯蒸馏塔操作压力为0.1MPaA,塔顶温度79.6℃,塔釜温度87.3℃,塔理论级数为8;中压有机溶剂精馏塔操作压力为0.19MPaA,塔顶温度89.3℃,塔釜温度120℃,塔理论级数为15,质量回流比0.03;低压有机溶剂精馏塔操作压力为0.08MPaA,塔顶温度43.2℃,塔釜温度75.5℃,塔理论级数为30,质量回流比0.05。经上述过程,各塔顶塔釜出料到达该厂处理要求。由于该工艺考虑了充分的热耦合,各塔的负荷如表3(括号内为节省的加热或冷却热负荷):表3冷却负荷/KW加热负荷/KW合计/KW高压苯蒸馏塔6538685413392中压有机溶剂精馏塔(6190)62156215(12405)低压有机溶剂精馏塔6275(5844)6275(12119)合计6275(12465)6215(12059)12490(24524)本实施例的高压苯蒸馏塔与有机溶剂精馏塔单独运行,有机溶剂精馏塔采用中低压双效逆流精馏,未耦合时,其各塔总的加热负荷为12059KW,冷凝负荷为12465KW,总的热负荷为24524KW;耦合后,各塔总的加热负荷为6215KW,冷凝负荷为6275KW,总的热负荷为12490KW;加热负荷节能48.5%,冷凝负荷节能49.7%,总的热负荷节能49.1%。本实施例未进行完全耦合,只对环己酮肟化工段的溶剂回收塔采用双效逆流精馏耦合,中压有机溶剂精馏塔的塔顶蒸汽作为低压有机溶剂精馏塔的热源,实现了己内酰胺系统的节能优化。本实用新型提出的超低能耗回收己内酰胺有机萃取剂的装置,已通过较佳的实施例子进行了描述,相关技术人员能明显在不脱离本
实用新型内容、精神和范围内对本文所述方法及装置进行改动或适当变更组合来实现本实用新型技术。特别需要指出的是,所有相类似的替 换或改动对本领域的技术人员是显而易见的,都会被视为包在本实用新型精神、范围和内容中。当前第1页1 2 3