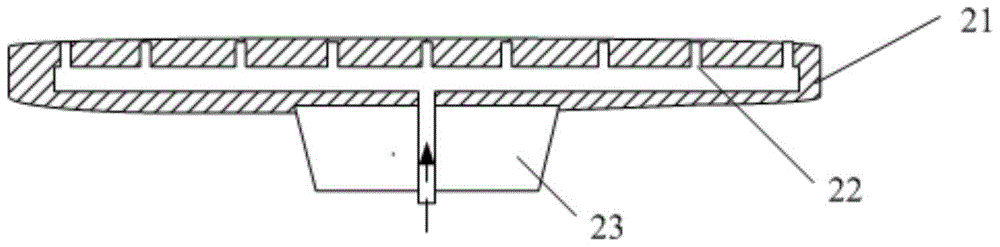
本发明属于显示技术领域,具体涉及一种输出装置和切割裂片系统。
背景技术:在显示技术领域,为提高生产效率,通常在大板(即母板)上制备形成单元显示面板的彩膜图形或阵列图形,显示面板母板成型后通过切割方式切割成小板,从而分离为多个独立的显示面板单元。现有技术中,如图1所示的切割裂片流程,其中的切割裂片工艺采用切割装置10、裂片装置11两部分,二者的承载平台(Stage)均为平面结构。基板母板31(Glass,可以由彩膜基板32和阵列基板33形成)先在切割装置10中切割(cut),此时刀轮切割后仅在基板母板31表面有切割凹槽101,即仅在切割位置的部分基板母板31表面形成切槽;接着借助特定的裂片装置11(通常包括裂片杆111)在其背面进行裂片(break),例如采用杆式裂片(bartypebreak)、滚轮式裂片(rollertypebreak)等裂片方式进行裂片,基板母板31随着表面切割凹槽101进一步渗裂,使得切割凹槽101贯穿整个基板母板31的厚度形成裂缝112;然后将裂片后的基板母板31通过传送装置12传送(transfer)到输出装置13,通过输出装置13的承载平台排出(output);最后通过剥片使基板母板31中的各显示基板彻底分离。若切割后不进行裂片,则由于切割不能完全自然开裂,基板母板31排出后,捡片、剥片时容易发生凸缘等切割不良;而增加特定的裂片机后,不仅占地面积增大,而且会增长切割过程整体循环周期(cycletime)。可见,设计一种同时兼具切割和裂片功能,缩短循环周期的切割裂片系统成为目前亟待解决的技术问题。
技术实现要素:本发明所要解决的技术问题是针对现有技术中存在的上述不足,提供一种输出装置和切割裂片系统,由于可在输出装置中实现裂片,相对现有技术中的切割裂片系统可省去其中的裂片装置,降低了生产成本,提高了生产效率和生产质量。解决本发明技术问题所采用的技术方案是该输出装置,包括承载平台,所述承载平台的上表面设置有用于放置待输出基板的承载区,其中,所述承载区为曲面结构。优选的是,所述承载平台的上表层为外凸的拱形结构。优选的是,所述承载平台的上表面设置有拱形的薄膜,所述薄膜具有高透气性。优选的是,所述薄膜通过贴附方式设置于所述承载平台的上表面。优选的是,所述曲面结构或所述拱形薄膜的曲率中心轴线与所述承载平台沿输出方向的中心轴线重合。优选的是,还包括真空机构,所述承载平台上表层开设有吸附孔,所述吸附孔与所述真空机构相连通。优选的是,还包括旋转马达,所述旋转马达用于对设置于所述承载区的待输出基板进行平面角度旋转。一种切割裂片系统,包括切割装置和传送装置,用于将具有多个单元显示基板的基板母板切割分离为独立的单元显示基板,其中,还包括上述的输出装置。优选的是,所述传送装置的下表层为内凹的拱形结构。优选的是,所述传送装置的下表面设置有内凹的薄膜,所述薄膜具有高透气性。本发明的有益效果是:该输出装置,通过将其承载平台的承载区设置为曲面结构,利用切割完毕的待输出基板的自身重力,产生向下的坠力,并结合承载平台的真空吸附力,实现待输出基板的裂片,提高了生产效率;采用该输出装置的切割裂片系统,可以省去裂片装置,缩短切割循环周期,减少承载平台的占地面积,降低承载平台成本;同时,待输出基板切裂程度大,便于后续的捡片、剥片、饵料掉落,降低凸缘等不良,提高了生产质量。附图说明图1为现有技术中切割裂片工艺的示意图;图2为本发明实施例1中输出装置的结构示意图;图3为本发明实施例2中输出装置的结构示意图;图4为本发明实施例2中传送装置的结构示意图;图5为本发明实施例3中切割裂片工艺的示意图;图中:10-切割装置;101-切割凹槽;11-裂片装置;111-裂片杆;112-裂缝;12-传送装置;13-输出装置;21-承载平台;22-吸附孔;23-旋转马达;24-薄膜;31-基板母板;32-彩膜基板;33-阵列基板。具体实施方式为使本领域技术人员更好地理解本发明的技术方案,下面结合附图和具体实施方式对本发明输出装置和切割裂片系统作进一步详细描述。实施例1:本实施例提供一种输出装置,该输出装置通过与待输出基板接触表面的结构的改进,在输出的同时实现裂片功能,不仅减小了设备占地面积,还缩短了切割的循环周期。通常情况下,待输出基板为可以切割裂片分离为多个单元板的母板。例如,母板可以为由彩膜基板32和阵列基板33形成的基板母板31。如图2所示,该输出装置包括承载平台21,承载平台21的上表面设置有用于放置待输出基板母板31的承载区,承载区为曲面结构。优选的是,承载平台21的上表层为外凸的拱形结构。在上述曲面结构的承载平台21表面条件下,当切割后的基板母板31放置于输出装置的承载平台21上方时,由于基板母板31与承载平台21为曲面接触(而不是现有技术中平面承载平台21表面条件下的平面接触),因此使得基板母板31未与承载平台21表面曲面接触部分受自身重力作用而产生向下的坠力,加剧切割凹槽101的开裂程度。进一步优选的是,曲面结构或拱形薄膜的曲率中心轴线与承载平台21沿输出方向的中心轴线重合。此时,基板母板31与承载平台21表面线接触部分为承载平台21的最高处,能获得较佳的切割凹槽101的开裂效果。本实施例的输出装置中,拱形结构可根据待输出基板母板31的尺寸、大小、重量和切割凹槽101部位设置不同的弧度或曲率。使得承载平台21拱形结构与基板母板31尺寸相匹配,能极大的提高开裂效果。优选的是,该输出装置还包括真空机构,承载平台21上表层开设有吸附孔22,吸附孔22与真空机构相连通。也即,本实施例中的输出装置,在对基板母板31输出的同时,除了依靠自身重力作用加剧切割凹槽101的开裂,还可以进一步通过真空吸附孔22将其吸附向承载平台21表面的吸附力的双重作用下,更好地实现裂片。另外,本实施例的输出装置还包括旋转马达23,旋转马达23用于对设置于承载区的待输出基板母板31进行平面角度旋转。例如,将基板母板31在承载区内进行90°旋转,便于单元显示基板在互相垂直的两个方向上的裂片。优选该旋转马达23设置于承载平台21下方,通过旋转马达23对待输出基板母板31进行90°或180°的旋转,从而实现沿着垂直的两个方向的裂片,达到0°或90°均可裂片的效果。实施例2:本实施例提供一种输出装置,该输出装置与实施例1中输出装置的区别在于,该承载平台21的上表面可以为平面,而在其上表面之上设置拱形的结构。优选的是,承载平台21的上表面设置有拱形的薄膜24,所述薄膜24具有高透气性。进一步优选的是,薄膜24通过贴附方式设置于承载平台21的上表面。本实施例中输出装置的其他结构与实施例1相同,例如,为了加强裂片效果,可以设置真空吸附孔22以及相应的真空机构(设置高透气性的拱形薄膜,不会影响吸附效果);为了实现基板母板31在两个垂直方向的裂片,可以设置用于转动的旋转马达23,这里不再详述。实施例1和实施例2中的输出装置,通过将其承载平台的承载区设置为曲面结构,利用切割完毕的待输出基板母板的自身重力,产生向下的坠力,并结合承载平台的真空吸附力,实现待输出基板母板的裂片。实施例3:本实施例提供一种切割裂片系统,包括切割装置11和传送装置12,用于将具有多个单元显示基板的基板母板切割分离为独立的单元显示基板,还包括实施例1或实施例2中的输出装置13。如图5所示,以采用实施例1中的输出装置13为例,该切割裂片系统的工作过程为:基板母板31(Glass)先在切割装置10中切割(cut),此时仅在切割位置的部分玻璃表面形成切槽(根据切割装置10中刀头的设置位置,可以在基板母板31的上表面形成切槽,或者在基板母板31的上表面和下表面均分别形成切槽);接着采用传送装置12传送(transfer)裂片后的基板母板31,在传送过程中,传送装置12通过旋转马达将基板母板31进行平面90°旋转;然后将基板母板31传送到输出装置13的承载平台21,进而通过输出装置13的拱形承载平台21排出(output),在排出的同时依靠基板母板31自身重力和真空吸附力进行裂片,使得切割位置的玻璃较大程度的渗透开裂,切槽贯穿整个基板母板31的厚度;最后通过剥片使基板母板31中的各单元显示基板彻底分离。在该切割裂片系统中,由于裂片可在输出装置13中实现自然裂片,相对现有技术中的切割裂片系统可省去其中的裂片装置。进一步优选的是,如图4所示,传送装置12的下表层为内凹的拱形结构;或者,传送装置13的下表面设置有内凹的薄膜,薄膜具有高透气性。这里的传送装置12采用与输出装置13相同的曲面结构的设计,能在将切割完毕后的基板母板31传送到输出装置13之前就进行预裂片,提升输出装置13的裂片效果。本实施例中的切割裂片系统,采用实施例1或实施例2中的输出装置,将用于输出切割后的基板母板的输出装置的承载平台设计为曲面拱形结构或者增加拱形的高透气膜,利用曲面拱形承载平台吸着弯曲(bending)及基板母板的自身重力和真空吸附力完成裂片,达到以下效果:1.可以省去裂片装置,减少承载平台的占地面积,降低了生产成本;2.可以省去裂片装置,缩短切割循环周期,提高了生产效率,3.待输出基板切裂程度大,便于后续的捡片、剥片、饵料掉落,降低凸缘等不良,提高了生产质量。可以理解的是,以上实施方式仅仅是为了说明本发明的原理而采用的示例性实施方式,然而本发明并不局限于此。对于本领域内的普通技术人员而言,在不脱离本发明的精神和实质的情况下,可以做出各种变型和改进,这些变型和改进也视为本发明的保护范围。