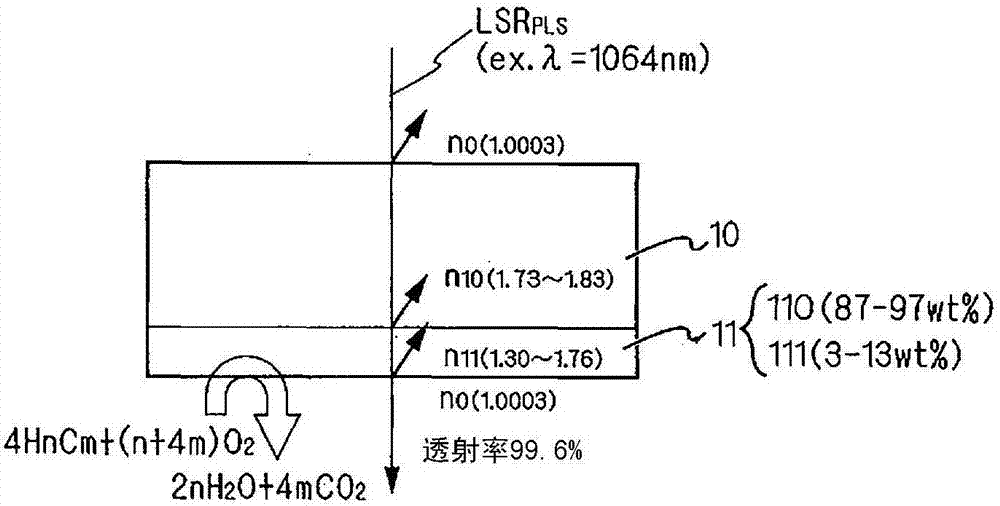
本发明涉及对导入内燃机的燃烧室内的混合气进行点火的点火装置,特别是涉及通过形成于火花塞表面上的超亲水膜来防止沉积物的堆积,实现稳定的发火的点火装置、以及其中所用的超亲水膜的制造方法。
背景技术:
:近年来,一直对作为废热发电用的气体燃料发动机、及稀薄混合气燃烧发动机等难发火性的内燃机的点火装置进行各种研究开发,上述点火装置是使用半导体激光器作为激发光源,向q开关式的激光谐振器照射从半导体激光器中起振的激发光,使能量密度高的脉冲激光起振,进而使用聚光部向导入燃烧室内的混合气中使脉冲激光聚光而进一步提高能量密度地进行点火的激光点火装置。在这样的激光点火装置中,为保护光学元件免受燃烧室内的高温、高压的影响,在与燃烧室的边界处设置具有耐热性光学窗的火花塞。而且,将经由光学窗而导入的脉冲激光聚光在内燃机的燃烧室中,进行导入燃烧室内的混合气的点火。另一方面,在内燃机中,为降低活塞的摩擦等而使用发动机油,成为雾状的油雾漂浮在燃烧室内。因此,如果油雾附着在光学窗的燃烧室侧表面上,其灰分及烟灰等堆积而形成沉积物,则脉冲激光的透射性下降,损害发火稳定性,所以,需要防止油雾附着在光学窗的燃烧室侧表面上。此外,即使在普通的火花点火装置中,例如在低温起动时等,如果因液体燃料的不完全燃烧而产生烟灰等,则附着在火花塞的绝缘子的表面上,形成沉积物。由于如此形成的沉积物以具有导电性的碳为主体,所以有使电极间的绝缘性下降、损害发火稳定性的顾虑。对于这样的问题,专利文献1中公开了在燃烧室窗的燃烧室侧的端部配设副室,并设置有使激光束通过而进入其内室的颈缩部的激光感应式外部点火装置。此外,专利文献2中公开了对绝缘子的外表面涂布含有硅酮树脂的涂料的火花塞。现有技术文献专利文献专利文献1:日本特开2013-527376号公报专利文献2:日本特表2013-545258号公报技术实现要素:发明要解决的问题可是,如专利文献1所示的那样仅通过颈缩部来限制朝向光学窗的气流,即使能够防止油雾在光学窗表面的直接附着,但也不能避免油雾附着在颈缩部的内周面上。因此,在长期间使用的情况下,附着在颈缩部内周壁上的油雾因暴露于燃烧室内的高温下,形成含有金属氧化物等不燃成分的沉积物。特别是,如果在开口径最细的颈缩部的顶端附近形成沉积物,则有招致激光束的衍射、或招致透光率的下降、不能维持稳定的发火的问题。另外,通过专利文献1那样的颈缩部,难以完全防止油雾附着在光学窗上,与此相对,通过在光学窗的燃烧室侧存在颈缩部,必然抑制颈缩部的内侧的流速。因此,在油雾从颈缩部挤过去而达到光学窗的表面的情况下,暂时附着的油雾不被燃烧室内的气流剥离而一度发生油雾堆积,则油雾重叠地堆积,反而还有颈缩部的存在导致相反效果的可能性。此外,即使通过专利文献2那样的涂料,也难完全防止包含碳的沉积物附着在绝缘子上。因此,本发明的目的在于,为解决上述以往的课题,提供能够促进附着在火花塞表面的油雾及碳的分解和剥离、防止沉积物的形成、实现稳定的发火、且具有简易的构成的激光点火装置、火花点火装置等点火装置。用于解决课题的手段本发明的点火装置(1、6),是具备安装在内燃机(5)的燃烧室(51)壁上的火花塞(4、60)、对导入所述燃烧室内的混合气进行发火的点火装置,其中,在构成所述火花塞的、面向所述燃烧室而配置的火花塞构成部件(10、7)的面向所述燃烧室的表面上,设有含有超亲水性粒子(110)和热激发催化剂粒子(111)的超亲水膜(11),而且,在将未设该超亲水膜时的所述火花塞构成部件和水的接触角设定为θw1、将设置有所述超亲水膜时的所述火花塞构成部件和水的接触角设定为θw2时,具有θw2<θw1的关系。所述点火装置是所述火花塞(4)经由设在与内燃机(5)的燃烧室(51)的边界处的作为火花塞构成部件的光学窗(10)而将能量密度高的脉冲激光(lsrpls)聚光在燃烧室内的焦点(fp)上,对导入所述燃烧室内的混合气进行发火的激光点火装置(1),在所述火花塞构成部件即所述光学窗的燃烧室侧表面上设置所述超亲水膜。或者,所述点火装置是所述火花塞(60)具备突出地位于所述内燃机的所述燃烧室内的中心电极(61)及接地电极(62)、和保持所述中心电极的外周的作为火花塞构成部件的绝缘子(7),在两电极间的间隙(g)中产生火花放电,对导入所述燃烧室内的混合气进行发火的火花点火装置(6),在所述火花塞构成部件即绝缘子(7)的面向所述燃烧室的表面上设置所述超亲水膜。再者,括号内的符号是为了参考而标注的,本发明并不受这些符号的限定。发明效果根据本发明涉及的点火装置的构成,即根据本发明涉及的激光点火装置或火花点火装置的构成,由于含在燃烧废气中的水分润湿铺展在所述超亲水膜的表面,所以具有即使所述燃烧室内浮游的油雾及碳附着在所述光学窗及所述绝缘子等火花塞构成部件上也容易剥离的效果。此外,通过燃烧时的热能量,激发含在所述超亲水膜中的热激发催化剂粒子的催化作用,能够对附着在所述光学窗表面上的油雾及碳进行氧化分解,能够使所述燃烧室窗长期维持清洁。进而,通过所述超亲水膜的疏油性,具有即使油雾及碳附着在所述光学窗表面也容易剥离的效果。附图说明图1是表示本发明的实施方式1中的激光点火装置的主要部位的纵向剖视图。图2a是表示本发明的主要部分即超亲水膜的功能的示意图。图2b是表示本发明的主要部分即超亲水膜的亲水性的示意图。图2c是表示本发明的主要部分即超亲水膜的疏油性的示意图。图3a是表示二氧化钛配合比率对于亲水性的效果的特性图。图3b是表示二氧化钛配合比率对于疏油性的效果的特性图。图4是表示本发明的实施方式2中的火花点火装置的主要部位的纵向剖视图。图5是表示二氧化钛配合比率对于亲水性的效果的特性图。图6是表示二氧化钛配合比率对于疏油性的效果的特性图。图7是表示变更了二氧化钛配合比率的超亲水膜的催化性能与温度的关系的特性图。图8是表示二氧化钛配合比率对于超亲水膜的催化性能的效果的特性图。图9是比较根据超亲水膜的有无而造成的火花点火塞冒烟试验结果的图示,是表示循环数和不发火率的关系的特性图。图10是将火花点火塞的冒烟试验中的构成超亲水膜的薄膜的表面状态与没有薄膜的状态进行比较而示出的照片。图11是表示二氧化钛配合比率对于直到发生不发火的循环数的效果的特性图。图12是表示超亲水膜厚对于直到发生不发火为止的循环数的效果的特性图。图13是表示本发明的实施方式3中的火花点火装置的主要部位的纵向剖视图。图14是表示本发明的实施方式4中的火花点火装置的主要部位的纵向剖视图。图15是表示本发明的实施方式5中的火花点火装置的主要部位的纵向剖视图。图16是表示本发明的实施方式6中的火花点火装置的主要部位的纵向剖视图。图17是表示本发明的实施方式7中的火花点火装置的主要部位的纵向剖视图。图18是表示本发明的实施方式8中的火花点火装置的主要部位的纵向剖视图。具体实施方式(实施方式1)参照图1对本发明的实施方式1中的点火装置进行说明。实施方式1中的点火装置为激光点火装置1,具备安装在内燃机5的燃烧室51壁上的作为火花塞的激光火花塞4。激光点火装置1可以适用的内燃机5是通过向由汽缸(未图示)和覆盖汽缸的上表面的发动机盖(燃烧室壁)50和沿汽缸内可升降地保持的活塞52划分而成的燃烧室51内导入混合气,使其在燃烧室51内燃烧膨胀,由此压下活塞52而产生动力的内燃机。再者,本发明中,作为形成被导入内燃机5的燃烧室内的混合气的燃料,也可以使用丙烷等气体燃料和汽油、轻油等液体燃料中的任一种。激光点火装置1是经由设在与内燃机5的燃烧室51的边界上的光学窗10(火花塞构成部件)将高能量密度的脉冲激光lsrpls聚光在设在燃烧室51内的规定位置上的焦点fp,对导入燃烧室51内的混合气进行发火的激光点火装置。激光点火装置1由激发光源13和激光火花塞4构成。在构成激光火花塞4的火花塞构成部件中,在面向燃烧室51的表面上设置超亲水膜11。如图2a所示的那样,超亲水膜11含有超亲水性粒子110和热激发催化剂粒子111。激光火花塞4由固定在作为燃烧室51的壁的发动机盖50上的筒状的外壳3、收容保持在外壳3内的光学元件12、在外壳3的顶端侧设在与燃烧室51的边界上的光学窗10构成。激光点火装置1中,在作为火花塞构成部件的光学窗10的燃烧室51侧表面上设有超亲水膜11,并且,在将未设超亲水膜11时的光学窗10与水的接触角设定为θw1、将设置有超亲水膜11时的光学窗10与水的接触角设定为θw2时,具有θw2<θw1的关系。再者,超亲水膜11含有按规定的配合比率混合的规定粒径以下的超亲水性粒子110和规定粒径以下的热激发催化剂粒子111,优选设置使光学窗10与水的接触角θw1减小至2/3以下的超亲水膜11。也就是说,未设超亲水膜11时和设置超亲水膜11时的与水的接触角的比即相对水接触角θw2/θw1优选为2/3以下。另外,超亲水膜11中,在将未设超亲水膜11时的光学窗10和油的接触角设定为θo1、将设置有超亲水膜11时的光学窗10和油的接触角设定为θo2时,具有θo2>θo1的关系。此外,优选超亲水膜11具备使光学窗10和油的接触角θo1增至1.5倍以上的疏油性。也就是说,未设超亲水膜11时和设置有超亲水膜11时的与油的接触角的比即相对油接触角θo2/θo1优选为1.5以上。超亲水膜11中,相对于超亲水性粒子110和热激发催化剂粒子的合计量,热激发催化剂粒子111的配合比率优选为47wt%以下,更优选为20wt%以下。此外,超亲水膜11含有超亲水性粒子110和热激发催化剂粒子111、粘合剂成分及固化材料等膜构成物质,该膜构成物质中,作为提高超亲水性粒子110和热激发催化剂粒子111的密合性的粘合剂成分,含有选自磷酸盐及金属氧化物中的1种以上。作为具体例子,超亲水膜11中,超亲水性粒子110含有二氧化硅(sio2),热激发催化剂粒子111含有选自过渡金属氧化物及氧化锡(sno2)中的1种以上。过渡金属氧化物包含选自tio2、zro2、cr2o3、y2o3、zno、ceo2、ta2o5、cuo2、cuo及wo3中的1种以上。作为一个例子,超亲水膜11通过按重量比以1比1的比例混合含有4~6wt%的磷酸铝(alpo4)、90~95wt%的二氧化硅(sio2)、1.0~1.5wt%的氧化铝(al2o3)、0.3~0.7wt%的氧化锌(zno)的主剂、和含有2.0wt%的氧化钠(na2o)、82.2wt%的氧化钾(k2o)和15.8wt%的硅酮(nsio2)的固化剂而形成。此外,按上述配合比混合在超亲水膜11中的热激发催化剂粒子111,优选含有选自二氧化钛(tio2)、二氧化铈(ceo2)、氧化锡(sno2)中的1种以上。本申请发明者等通过深入的研究试验,判明:在选择二氧化钛作为混合在超亲水膜11中的热激发催化剂粒子111时,在相对于超亲水膜11中的二氧化硅按3.0wt%~13.0wt%的配合比率混合时,尤其能够发挥效果。具体地讲,超亲水膜11最好含有87wt%~97wt%的粒径为450nm以下的超亲水性粒子110,含有3wt%~13wt%的粒径为450nm以下的热激发催化剂粒子111。本申请发明者通过使超亲水性粒子110和热激发催化剂粒子111的配合比率变化来形成超亲水膜11,观察了水及油的接触角的变化。得出如下判断:在将无膜时的与水的接触角设定为θw1、将有膜时的与水的接触角设定为θw2时,相对水接触角θw2/θw1为2/3以下的范围具有提高亲水性的效果。同样,得出如下判断:在将无膜时的与油的接触角设定为θo1、将有膜时的与油的接触角设定为θo2时,相对油接触角θo2/θo1为1.5倍以上的范围是具有提高疏油性的效果的范围。本申请发明者通过深入的研究试验,结果得出如下结论:作为满足两者的范围,在以粒径450nm以下的超亲水性粒子110为主成分的超亲水膜中,优选含有3wt%~13wt%的粒径为450nm以下的热激发催化剂粒子111。超亲水膜11可将设置超亲水膜11时的与水的接触角θw2减低至未形成膜的光学窗10与水的接触角θw1的2/3以下。由此,燃烧废气中存在的水分成为冷凝水,在附着在光学窗10的表面上时润湿铺展,能够使附着在光学窗10的表面上的油雾浮起。此外,关于热激发催化剂粒子111,即使存在于燃烧室51内的油雾附着在光学窗10的表面上,也发挥由燃烧时发生的热而激发的催化作用,能够将油雾的主成分即烃完全氧化分解。另外,即使在油雾中存在不燃的金属、生成金属氧化物时,由于超亲水膜11具有高的亲水性,所以通过润湿铺展在表面的水,可使金属氧化物浮起,容易剥离,因而可抑制堆积在光学窗10上。即使在使用液体燃料、因不完全燃烧而在燃烧废气中含有烟灰等的情况下,也可得到同样的效果,具有附着的烟灰等浮起、容易剥离的效果。此外,还具有通过燃料热激发催化剂粒子111的催化作用使烟灰的主成分即碳完全氧化分解的效果。激发光源13包含由公知的gaalas、ingaas等晶体材料形成的半导体激光二极管等,起振具有规定波长的激发激光lsrpmp。作为激发光源13,也能组合地使用多个半导体激光二极管。光学元件12由公知的准直透镜123、激光谐振器122、扩展透镜121、聚光透镜120构成,通过光学窗10保护免受燃烧室内的高温高压的影响。光学元件12也称为激光元件,扩展透镜121也称为光束扩展器。从激发光源13起振的激发激光lsrpmp通过准直透镜123准直成平行光,照射在激光谐振器122上。作为准直透镜123,使用光学玻璃、耐热玻璃、石英玻璃、蓝宝石玻璃等公知的光学材料。根据需要,对准直透镜123的表面实施公知的防反射膜。再者,准直透镜123可以是多个透镜组合而成的,也可以是一体地形成的。激光谐振器122可使用公知的从动q开关式的激光谐振器。激光谐振器122由激光器媒质、设在其入射侧的防反射膜、全反射镜、设在出射侧的可饱和吸收体、由部分反射膜形成的出光镜而构成。作为激光器媒质,可使用在yag单晶中掺杂了nd的nd∶yag等公知的激光器媒质。全反射镜以透射短波长的激发激光lpmp,全反射长波长的脉冲激光lsrpls的方式形成。可饱和吸收体可使用在yag单晶中掺杂了cr4+的cr∶yag等。激光谐振器122通过导入谐振器内的激发激光lpmp激发激光器媒质内的nd,例如放射1064nm的光,蓄积在激光器媒质内。如果激光器媒质内的能量水平达到一定水平,就从设在顶端侧的出光镜起振能量密度高的脉冲激光lsrpls。从激光谐振器122起振的脉冲激光lsrpls在暂时被扩展透镜121扩展后,通过聚光透镜120再次使其集光,由此提高在焦点fp即集光点上的能量密度,使存在于焦点fp周边的混合气等离子化,产生火焰核。再者,作为扩展透镜121、聚光透镜120,使用光学玻璃、耐热玻璃、石英玻璃、蓝宝石玻璃等公知的光学材料。外壳3可使用铁、镍、铁镍合金、不锈钢等耐热性金属材料,形成筒状,在内侧收容固定光学元件12,在顶端设有光学窗10。聚光透镜120被收容保持在形成为筒状的聚光透镜保持架23内。聚光透镜保持架23设置在元件收容部310内,元件收容部310被区划在外壳3的筒状部32的顶端侧,外壳3上设有螺纹部33,该螺纹部33用于将激光火花塞4螺合在发动机盖50上。由于不对聚光透镜保持架23作用由螺纹部33产生的紧固应力,所以聚光透镜120的光轴不会发生变形。作为光学窗10,可使用蓝宝石、石英玻璃等透明的耐热性玻璃材料。关于光学窗10,平行地形成与设在底端侧的聚光透镜120相对的入光面和与顶端侧的燃烧室51相对的出光面,在外周侧面设置朝顶端变得尖细的锥面。光学窗10被收容在底端侧形成为阶梯筒状的光学窗保持架22内,由密封部件21固定。另外,以覆盖设在光学窗10的顶端侧的锥面的方式,设有形成为圆环状的缓冲部件20。作为缓冲部件20,使用与外壳3所用的材料相比热膨胀率大的金属材料。光学窗10经由缓冲部件20通过设在外壳3的顶端的包铆接部30向轴向压紧,被弹性地保持。形成为筒状的聚光透镜保持架23的底端侧的平面与台阶部311搭接,聚光透镜保持架23的顶端侧的平面与形成为筒状的光学窗保持架22的底端侧的平面搭接,光学窗保持架22的顶端侧的平面与缓冲部件20的底端侧平面搭接。设在一轴上的聚光透镜保持架23、光学窗保持架22、缓冲部件20由台阶部311和包铆接部30夹持,通过设在外壳3的顶端的热铆接部31而产生的轴向力发挥作用,被弹性地保持。(制造方法)以下,对激光点火装置1、及后述的火花点火装置6中所用的超亲水膜11的制造方法进行简要的说明。超亲水膜11能够通过按重量比以1比1的比例混合表1所示那样的含有磷酸铝(alpo4)、二氧化硅(sio2)、蓝宝石(al2o3)、氧化锌(zno)的主剂、和表2所示那样的含有氧化钠(na2o)、氧化钾(k2o)、硅酮(nsio2)的固化剂而形成。主剂如表1所示的那样,作为主成分以90~95wt%的比例含有粒径450nm以下的二氧化硅。固化剂如表2所示的那样,作为主成分以80~85wt%的比例含有氧化钾。作为构成超亲水膜11的磷酸铝、二氧化硅、蓝宝石、氧化锌等超亲水性粒子110以外的粒子,使用粒径450nm以下的胶体粒子。另外,在超亲水膜11中,为了发挥催化作用,相对于超亲水性粒子110,按规定的比例混合热激发催化剂粒子111。作为热激发催化剂前体材料,可使用含有二氧化钛(tio2)、二氧化铈(ceo2)、氧化锡(sno2)中的至少1种的粒径450nm以下的胶体粒子。相对于按重量比计为87wt%~97wt%的超亲水性粒子110,作为热激发催化剂粒子111按3wt%~13wt%的比例混合热激发催化剂前体材料,并分散在水中而形成料浆。将得到的料浆滴在构成光学窗10的玻璃材料的表面上,然后以规定的转速(例如2000~2500rpm)使其高速旋转2分钟,进行薄膜化。接着,在自然干燥后,以规定的温度(例如350~500℃)进行烧成,由此形成为本发明要点的、按规定比例含有热激发催化剂粒子111的超亲水膜11。如图2a所示的那样,根据上述制造方法,形成在光学窗10表面上的超亲水膜11,由能按折射率n11(例如1.30~1.76)透射规定波长(例如nd∶yag激光器的基本波长λ=1064nm)的脉冲激光的薄膜(例如光学膜厚度n11d=λ/4nm=266nm、膜厚度d=151~240nm)构成。这里,空气的折射率n0为1.0003,光学窗10的折射率n10如果使用蓝宝石则为1.73~1.83。对该构成的光学窗10照射上述规定波长的脉冲激光,用于使其透过率达到最大(例如99.6%)的薄膜只要是上述光学膜厚度n11d=266nm以下的膜厚度即可,但如果考虑到加工时的误差及耐久性,膜厚度d优选为151~240nm。如果烃(4hncm)与该超亲水膜11接触,就通过热激发催化剂粒子111的作用与氧反应,分解成水和二氧化碳。水的一部分被超亲水膜11吸收,发挥疏油性。其结果是,能够降低附着在超亲水膜11上的烃的量,所以对于防止脉冲激光的透射率下降是有效的。再者,如表3所示的那样,作为主剂使用的各材料的混合比,容许有某种程度的范围。此外,作为热激发催化剂粒子111,能够使用表4所示的材料。对这些材料进行了研究,结果确认:特别是二氧化钛、二氧化铈、氧化锡,因耐酸性、耐碱性良好,能够形成可稳定地发挥超亲水性和热激发催化效果的薄膜。再者,表4中的氧化铬(cr2o3)的透射波长的评价是基于对例示的nd∶yag激光器的基本波长的可否的评价,在使用基本波长不同的脉冲激光的情况下,并不一定局限于此。表1表2表3主剂容许范围成分比率(wt%)下限上限alpo45.64.06.0sio292.690.095.0al2o31.31.01.5zno0.50.30.7合计100.00.00.0表4此外,如图2b所示的那样,通过形成超亲水膜11,能够使光学窗10和水的接触角θw1减小至2/3以下的接触角θw2,能够谋求提高亲水性的功能,由此,存在于燃烧室51内的水在附着在光学窗10的表面上时,润湿铺展,油雾难以附着。另外,如图2c所示的那样,通过形成超亲水膜11,能够使光学窗10和油的接触角θo1增加至1.5倍以上的接触角θo2,能够谋求提高疏油性,附着在光学窗10的表面上的油雾容易剥离。参照图3a、图3b,对使热激发催化剂即二氧化钛的配合比率变化时的超亲水膜11对亲水性的影响和对疏油性的影响进行说明。再者,二氧化钛的配合比以相对于超亲水膜的二氧化硅换算重量的重量%表示。如图3a所示的那样,判明:在将光学窗10的表面未设超亲水膜11时的与水的接触角设定为θw1,将光学窗10的表面设置有超亲水膜11时的与水的接触角设定为θw2时,相对于超亲水膜11中的与二氧化硅的合计量,在按重量比计以34%以下的范围混合二氧化钛的情况下,可以将θw2减低至θw1的2/3以下,随着二氧化钛的配合比率的提高,亲水性降低,如果二氧化钛的配合比超过47wt%,则形成比未设超亲水膜11时大的接触角。另外,判明了:在将光学窗10的表面未设超亲水膜11时的与油(发动机油)的接触角设定为θo1,将光学窗10的表面设置有超亲水膜11时的与油的接触角设定为θo2时,相对于超亲水膜11中的与二氧化硅的合计量,在按重量比以3%以上且13%以下的范围混合二氧化钛的情况下,可以将θo2增加至θo1的1.5以上,疏油性提高。随着二氧化钛的配合比率的提高,疏油性降低,如果二氧化钛的配合比超过20wt%地进一步增大,则在40wt%以上时,达到大致固定。从这些试验结果,判明了:关于作为热激发催化剂粒子111的二氧化钛的配合比,相对于超亲水性粒子110,优选设定为3wt%以上且20wt%以下,更优选设定为13wt%以下。通过减小与水的接触角、同时增大与油的接触角,附着在光学窗10的燃烧室侧表面上的油雾变得容易剥离。在上述的实施方式1涉及的激光点火装置1中,示出了光学窗10直接与内燃机5的燃烧室51相对配置的例子,但也可以按以下方式构成,即:在光学窗10与燃烧室51之间,划分具有与燃烧室连通的喷孔的副燃烧室,向副燃烧室内导入一部分混合气,在副燃烧室内使脉冲激光lsrpls聚光而对副燃烧室内的混合气进行发火,从副燃烧室向燃烧室内喷射燃烧火焰,进行内燃机的点火。另外,在上述实施方式中,示出了在光学窗10的燃烧室侧表面上直接形成超亲水膜11的例子,但也可以在光学窗10的表面与超亲水膜11之间形成防反射膜,来提高脉冲激光lsrpls的透射率。(实施方式2)以下,参照图4~图12对本发明的实施方式2涉及的点火装置进行说明。实施方式2涉及的点火装置为火花点火装置6,具备安装在内燃机5的燃烧室51壁上的作为火花塞的火花点火塞60。火花点火装置6所适用的内燃机5的构成与上述实施方式1所示的内燃机的构成同样,对于相同的构成的部位标注相同的符号,并将说明省略。以下,重点对不同之处进行说明。火花点火装置6由火花点火塞60和供给点火用电压的供电部8构成。而且,在突出地位于燃烧室51内的火花点火塞60的电极间形成规定的间隙g,对该间隙g导入高电压,产生火花放电,由此对导入燃烧室51内的混合气进行发火。关于构成火花点火塞60的火花塞构成部件,与实施方式1同样地设置覆盖面向燃烧室51的表面、且含有超亲水性粒子110和热激发催化剂粒子111的超亲水膜11(例如参照图2a)。火花点火塞60具有固定在作为燃烧室51壁的发动机盖50上的筒状的外壳63、保持中心电极61的外周的筒状的绝缘子7(火花塞构成部件)、固定在外壳63上的接地电极62。绝缘子7在向轴向x(即图的上下方向)延伸的轴孔71内同轴地收容棒状的中心电极61,以将底端侧气密封的状态收容保持在外壳63的筒内。接地电极62的顶端侧向径向内方弯曲成l字状,与中心电极61的顶端相对,形成火花放电用的间隙g。接地电极62的底端侧被焊接固定在外壳63的顶端面上。火花点火塞60的外壳63在外周侧具有安装用的螺纹部,在设于内周侧的台阶部64上支持绝缘子7的扩径而成的中间部72。外壳63的底端侧铆接固定在绝缘子7的外周,被气密封。在绝缘子7的底端侧,收容有未图示的密封材料及端子电极,经由端子电极从供电部8向中心电极61供电。在相比台阶部64的顶端侧,绝缘子7为朝着顶端侧而外径缓慢减小的尖细锥形状,在与位于外侧的外壳63之间具有空隙73。绝缘子7例如由氧化铝、二氧化硅等绝缘性陶瓷材料形成,外壳63例如由钢材等形成。中心电极61例如由镍合金等形成,在从绝缘子7突出的顶端部,例如焊接有含有铱等的合金片。接地电极62例如由镍合金等形成。图4所示的第2实施方式涉及的火花点火装置6中,将绝缘子7作为构成火花点火塞60的火花塞构成部件,在其位于燃烧室51内的表面上设有超亲水膜11。具体地讲,如图4中以粗虚线示出涂布范围那样,在相比台阶部64的顶端侧的绝缘子7的外表面的大致整面上设有超亲水膜11。超亲水膜11与实施方式1同样地构成,在将未设超亲水膜11时的绝缘子7和水的接触角设定为θw1,将设置有超亲水膜11时的绝缘子7和水的接触角设定为θw2时,具有θw2<θw1的关系。最好,未设超亲水膜11时与设置超亲水膜11时的与水的接触角的比即相对水接触角θw2/θw1为2/3以下(例如参照图2b)。另外,关于超亲水膜11,在将未设超亲水膜11时的绝缘子7和油的接触角设定为θo1,将设置有超亲水膜11时的绝缘子7和油的接触角设定为θo2时,具有θo2>θo1的关系。最好,超亲水膜11具备使绝缘子7和油的接触角θo1增大至1.5倍以上的疏油性。也就是说,未设超亲水膜11时与设置超亲水膜11时的与油的接触角的比即相对油接触角θo2/θo1为1.5以上(例如参照图2c)。此外,超亲水膜11中,热激发催化剂粒子111的配合比率相对于其与超亲水性粒子110的合计量为47wt%以下,最好为20wt%以下。此外,超亲水膜11含有超亲水性粒子110和热激发催化剂粒子111、粘合剂成分及固化材等膜构成物质。该膜构成物质中,作为提高超亲水性粒子110和热激发催化剂粒子111的密合性的粘合剂成分,含有选自磷酸盐及金属氧化物中的1种以上。作为具体例,超亲水膜11中,超亲水性粒子110含有二氧化硅(sio2),热激发催化剂粒子111含有选自过渡金属氧化物及氧化锡(sno2)中的1种以上。过渡金属氧化物包含选自tio2、zro2、cr2o3、y2o3、zno、ceo2、ta2o5、cuo2、cuo及wo3中的1种以上。最好,混合在超亲水膜11中的热激发催化剂粒子111含有选自二氧化钛(tio2)、二氧化铈(ceo2)、氧化锡(sno2)中的任1种以上。超亲水膜11中,主要是超亲水性粒子110对绝缘子7的表面赋予亲水性及疏油性和防静电作用,使油分及碳的附着量减小,同时使附着的油雾及碳容易剥离。另外,热激发催化剂粒子111具有催化作用,使含在附着的油雾中的烃及碳燃烧。亲水性及疏油性也根据超亲水性粒子110和热激发催化剂粒子111的配合比率而变化,为了发挥形成超亲水膜11所带来的效果,热激发催化剂粒子111的配合比率优选为47wt%以下,更优选为20wt%以下。作为一个例子,超亲水膜11通过以重量比按1比1的比例混合含有4~6wt%的磷酸铝(alpo4)、90~95wt%的二氧化硅(sio2)、1.0~1.5wt%的氧化铝(al2o3)、0.3~0.7wt%的氧化锌(zno)的主剂、和含有2.0wt%的氧化钠(na2o)、82.2wt%的氧化钾(k2o)、15.8wt%的硅酮(nsio2)的固化剂而形成。在该主剂和固化剂的混合物中,进而混合热激发催化剂粒子111,形成超亲水膜11。超亲水膜11中的超亲水性粒子110和热激发催化剂粒子111的配合比率及配合方法、超亲水膜11的制造方法等,可规定为与实施方式1中所示的制造方法相同。通过本申请发明者的深入研究试验,判明了:除了上述的亲水性及疏油性以外,进而,对于碳燃烧,在相对于超亲水膜11的二氧化硅换算重量按4wt%~40wt%的混合比率进行混合时,能够发挥效果。最好,在相对于超亲水膜11的二氧化硅换算重量,按7.5wt%~15wt%的混合比率进行混合的情况下,能够提高发火性,能够发挥高的发火性效果。(试验例)对于图4所示构成的火花点火装置6,按以下方式制作在绝缘子7的外表面设有超亲水膜11的火花点火塞60。超亲水膜11在从绝缘子7的相比中间部72的顶端侧的锥形状的外表面开始朝环状的顶端面连续地形成,将超亲水膜11的底端部处的绝缘子7的外径设定为φ6.4mm,将顶端部处的外径设定为φ4.2mm。此外,将超亲水膜11的轴向长度设定为13.2mm,将与超亲水膜11相对的外壳63的内径设定为φ7.3mm,将外壳63的螺纹部的公称径设定为m12。首先,调制用于形成超亲水膜11的涂料溶液。作为调制用的原料,使用含有作为超亲水性粒子110的二氧化硅的溶液a、含有作为热激发催化剂粒子111的二氧化钛的溶液b。其中,溶液a是在主成分即二氧化硅中配合了粘合剂等而成的,使用了含有上述表3所示组成的主剂及含有上述表2所示组成的固化剂的二氧化硅溶胶(即日本五合株式会社制造的zeroclea(注册商标))。此外,作为溶液b,使用了在水中分散有二氧化钛微粒的二氧化钛溶胶(即tio2的重量平均径为78mm、tio2浓度为17wt%、ph=7,tayca株式会社制造,商品名tkd-801)。对于溶液a和溶液b,以相对于二氧化硅和二氧化钛的合计量的二氧化钛的重量比率达到0.4、7.5、10、12.5、15、20、40、60、100(单位:wt%)的方式,基于各溶液a、b中的二氧化硅及二氧化钛的重量比率进行配合、混合,调制涂料溶液。将得到的各种配合比率的涂料溶液涂布在绝缘子7上,然后进行烧结,在图4内的粗虚线所示的规定的涂布范围形成超亲水膜11。烧结方法如下。首先,在绝缘子7的轴孔71内插入并固定中心电极61等。接着,对形成超亲水膜11的绝缘子7的外表面照射等离子。由此,将成为涂布涂料时使密合性下降的原因的油脂及尘埃等物质除去。进而,采用气压喷枪,对绝缘子7的外表面喷射涂料溶液,然后进行30分钟的自然干燥。在500℃的空气气氛中保持2小时,然后进行缓冷,在图4中的粗虚线所示的规定的涂布范围形成规定厚度(例如10μm)的超亲水膜11。在保持中心电极61的绝缘子7的外侧,安装焊接有接地电极62的外壳63,将外壳63的底端边缘部铆接固定,形成火花点火塞60。将该火花点火塞60经由未图示的密封垫圈而螺纹固定在设于燃烧室51壁上的安装孔上,将其与燃烧室51之间气密封。将火花点火塞60的中心电极61与供电部8连接,形成火花点火装置6。图5示出二氧化钛相对于二氧化硅的配合比率(即0~100wt%)和与水的接触角的关系,是用注射器一滴一滴地在超亲水膜11的表面滴下蒸馏水时的接触角的计测结果。与实施方式1所示的图3a时同样,将未设超亲水膜11时的与水的接触角设定为θw1,将设置有超亲水膜11时的与水的接触角设定为θw2,按相对水接触角θw2/θw1的值来评价亲水性。如图5所示的那样,在二氧化钛相对于二氧化硅的配合比率为47wt%以下时,与未设超亲水膜11时相比,亲水性提高(即θw2<θw1)。在此范围,具有通过燃烧而产生的水容易被绝缘子7表面的超亲水膜11吸附、通过该水分来提高疏油性的效果。另外,如果配合比率降低,则相对水接触角θw2/θw1也减小,在配合比率为20wt%左右至其以下的范围时,相对水接触角θw2/θw1最小。图6示出二氧化钛相对于二氧化硅的配合比率(即0~100wt%)和与油的接触角的关系,是用注射器一滴一滴地在超亲水膜11的表面滴下发动机油时的接触角的计测结果。与实施方式1所示的图3b时同样,将未设超亲水膜11时的与油的接触角设定为θo1,将设置有超亲水膜11时的与油的接触角设定为θo2,按相对油接触角θo2/θo1的值来评价疏油性。如图6所示的那样,通过设置超亲水膜11,与未设时相比疏油性提高(即θo2>θo1)。在二氧化钛相对于二氧化硅的配合比率为20wt%以下的范围时,疏油性更加提高。通过此特性,能够降低燃烧室51内浮游的物质例如发动机油、汽油、碳等的附着量。图7是通过变更二氧化钛相对于二氧化硅的配合比率(即4wt%~40wt%)而调查二氧化钛的催化特性的结果,示出火花塞使用条件下的碳沉积物的残留比例。具体地讲,准备多个按上述范围变更了二氧化钛的配合比率的超亲水膜11,在用乳钵将各个粉碎后,混合从火花塞表面采取的碳。对得到的多个试样进行加热,分段地变化温度,测定热重量,算出沉积物的残留比例。作为比较试样,图中示出对碳单质的试样进行同样的测定的结果。如图7所示的那样,通过按4wt%~40wt%的范围混合二氧化钛,多个试样都随着温度上升而使沉积物剧减。特别是,在350℃以上的温度时,与碳单质时的残留比例(例如60%左右)相比,残留比例降低至10%,在400℃以上的温度时,残留比例进一步减小。如此,得知:通过超亲水膜11的二氧化钛的催化作用,对碳的氧化燃烧具有良好的效果。图8是通过变更二氧化钛相对于二氧化硅的配合比率(即4wt%~40wt%)而测定350℃时的碳沉积物的残留比例的结果。如图8所示的那样,得知:即使在4wt%~40wt%的范围变更二氧化钛的配合比率,二氧化钛的催化作用也没有大的变化。如此,热激发催化剂粒子111即二氧化钛对超亲水膜11赋予催化特性,使附着在绝缘子7上的碳燃烧。由此,能够防止因在绝缘子7的表面附着高导电性的碳而产生的火花放电的内飞,因此具有可得到不易冒烟的火花点火塞60的效果。图9是使用设有图4所示构成的火花点火塞60的火花点火装置6进行以下冒烟试验的结果。超亲水膜11以将二氧化钛相对于二氧化硅的配合比率设定为10wt%、超亲水膜厚度达到10μm的方式而形成。在上述冒烟试验中,实行jis标准(即jisd1606)中规定的冒烟模式。此外,作为发动机诸要素,使用缸径φ80.5、冲程78.5mm、4气缸串联汽油发动机、dohc16阀、孔喷射系统。图9将在绝缘子7的表面设置有超亲水膜11的火花点火塞60的不发火率与未设超亲水膜11时比较而示出,在未设超亲水膜11时,从第3个循环开始不发火,7次就不能起动。与此相对照,在设置了超亲水膜11的火花点火塞60中,即使超过20个循环也能起动,未发生不发火。此时,如图10所示的那样,根据这些超亲水膜11的有无,火花点火塞60的顶端的碳附着状态大不相同。也就是说,如图中的右图所示的那样,在绝缘子7的表面设置了超亲水膜11的火花点火塞60中,中心电极61附近的碳的附着减少,设置超亲水膜11的表面露出。与此相对照,在未设超亲水膜11的左图的绝缘子7的表面,发现碳的堆积。也就是说,因通过碳而形成的导电通路而导致不发火,然而在设置超亲水膜11的情况下,因导电通路被切断,具有能够大幅度改善发火性的效果。图11是在按0~50wt%的范围变更二氧化钛的配合比率时,到开始不发火为止的试验循环数的测定结果,随着二氧化钛的配合比率的增加,到发生不发火为止的循环数也增加。二氧化钛的配合比率在10wt%左右时,到发生不发火为止的循环数达到最大,如果超过此值,则到发生不发火为止的循环数再次减少,如果超过30wt%,则与未设超亲水膜11时的大的差异消失。所以,为了提高火花点火塞60的发火性,最好将二氧化钛的配合比率设定为7.5wt%~15wt%的范围(即到发生不发火为止的循环数为10次以上)。图12是在二氧化钛的配合比率为10wt%的条件下,按0~50μm的范围变更超亲水膜厚度时,到开始不发火为止的试验循环数的测定结果,随着超亲水膜厚度的增加,到发生不发火为止的循环数也增加。在超亲水膜厚度为10μm左右时,到发生不发火为止的循环数达到最大,如果超过此值,则到发生不发火为止的循环数再次减少,在40μm左右时,与未设超亲水膜11时的差异消失。所以,优选将超亲水膜厚设定为3μm~30μm的范围,与未设超亲水膜11时相比,可提高火花点火塞60的发火性。(实施方式3)以下,参照图13对本发明的实施方式3涉及的火花点火装置中所用的火花点火塞60进行说明。如图13所示的那样,实施方式3涉及的火花点火装置的火花点火塞60中,也可对形成于绝缘子7上的超亲水膜11的涂布范围进行变更。本实施方式3中,如图示的那样,在绝缘子7的顶端侧的范围c1、底端侧的范围c3、它们之间的范围c2这3处,分别间隔地设有超亲水膜11。各范围c1~c3的轴向长度及它们的间隔可适宜选择。超亲水膜11的形成方法及其它火花点火装置6的构成因与上述实施方式时相同而这里将它们的说明省略。超亲水膜11不需要设在绝缘子7的外表面的整体上,这样,通过分割成绝缘子7的顶端侧和底端侧来设置超亲水膜11,可降低超亲水膜11的材料的使用量。最好,在将超亲水膜11设置在外表面的一部分上的情况下,至少在顶端部形成超亲水膜11。如低温起动时那样在燃烧室温度低的条件下,顶端部的温度容易上升,迅速达到含在范围c1中的二氧化钛等热激发催化剂粒子111的催化活性温度,因此附着在顶端部上的碳容易燃烧。底端侧与顶端部相比温度低,因此即使在范围c2、范围c3涂布超亲水膜11,也不燃而残留。附着在低温时没有燃烧的范围c2、范围c3上的碳,在随着发动机负载增加而火花塞温度上升、在达到二氧化钛的催化活性温度的时刻燃烧。(实施方式4)以下,参照图14对本发明的实施方式4涉及的火花点火装置中所用的火花点火塞60进行说明。如图14所示的那样,在实施方式2所示的火花点火塞60中,也能将绝缘子7的外表面形成具有凹凸的形状。在实施方式4涉及的火花点火装置的火花点火塞中,例如,将与配置在外壳63内的安装配件的内表面相对的绝缘子7的外侧面的大致整面设定为凹凸面74,在绝缘子7的包含顶端面的外表面上涂布涂料,形成超亲水膜11。这样,通过将与超亲水膜11相接的表面设定为凹凸面74,含在超亲水膜11中的二氧化钛等热激发催化剂粒子111与碳的接触面积增加,因此可促进碳的氧化燃烧。另外,还起到在附着的碳的层中发生裂纹、防止绝缘电阻下降的效果。此外,通过钉扎效果可提高超亲水膜11的密合性。可适宜地调整、设定凹凸面74的形成范围及凹凸形状。(实施方式5)以下,参照图15对本发明的实施方式5涉及的火花点火装置中所用的火花点火塞进行说明。在上述的实施方式2、3、4的火花点火装置的火花点火塞60中,示出了相比绝缘子7顶端面在外侧形成超亲水膜11的例子,但也能将超亲水膜11的涂布范围规定为包含绝缘子7的顶端面的内外表面。在此种情况下,也可得到将堆积在中心电极61与绝缘子7之间的碳烧碎的效果。此外,超亲水膜11的形成方法如上述那样,并不局限于通过涂布涂料溶液形成超亲水膜11的方法,可采用多种方法。例如,在构成绝缘子7的绝缘性陶瓷材料含有二氧化硅时,也能在该二氧化硅中配合二氧化钛等热激发催化剂粒子111,达到上述配合比率(例如10wt%)。此时,如图15所示的实施方式5涉及的火花点火装置中所用的火花点火塞60那样,通过至少在绝缘子7的顶端侧的表面部75中使用配合了二氧化钛等热激发催化剂粒子111的绝缘性陶瓷材料,可使其作为超亲水膜而发挥作用。根据这样的构成,只要预先将绝缘性陶瓷材料设定为规定的配合,按通常的工序进行烧成即可,因此可将形成超亲水膜11的工序省略。此外,通过形成于绝缘子7的内侧,容易得到使堆积在中心电极61与绝缘子7之间的碳氧化燃烧的效果。(实施方式6)以下,参照图16对本发明的实施方式6涉及的火花点火装置中所用的火花点火塞进行说明。也就是说,也能将实施方式2中的火花点火塞的基本结构变更为图16所示的结构。超亲水膜11的构成及形成方法、形成范围、其它的火花点火装置6的构成与上述的实施方式时相同,因此这里将它们的说明省略。实施方式6涉及的火花点火装置中,如图16所示的那样,形成在中心电极61的侧方相对地配置两个接地电极62、使其顶端部与中心电极61的顶端侧面部相对的2极型的电极结构。此外,使外壳63的顶端侧内周边部向内侧突出,设置辅助接地电极65。这样的2极型的火花点火塞60具有将附着在绝缘子7上的碳利用朝辅助接地电极65的跳火而烧碎的功能。在此种情况下,通过进而在绝缘子7的表面上形成上述超亲水膜11,具有可通过沿着绝缘子7表面流动的电流促进tio2的催化作用、使碳烧碎的效果增大的效果。(实施方式7)以下,参照图17对本发明的实施方式7涉及的火花点火装置中所用的火花点火塞进行说明。作为火花点火塞60的构成,并不局限于2极,也能够采用多极型的火花点火塞。图17所示的实施方式7涉及的火花点火装置的火花点火塞60形成为将辅助接地电极65配置在安装配件63的顶端面的3处、使其顶端部与中心电极61的顶端侧面部相对的3极型的电极结构,在绝缘子7的表面形成超亲水膜11,在这样的结构中,也能得到与上述各实施方式涉及的火花点火装置同样的效果。(实施方式8)以下,参照图18对本发明的实施方式8涉及的火花点火装置中所用的火花点火塞60进行说明。如图18所示的那样,在2极型的电极结构的火花点火塞60中,也可形成使相对的接地电极62的顶端部靠近绝缘子7的顶端面的沿面型的电极结构。在这样的火花点火塞60中,通过在绝缘子7的表面形成超亲水膜11,也可得到与上述实施方式涉及的火花点火装置同样的效果。以上,如详细说明的那样,通过超亲水膜11的亲水性及疏油性以及催化作用,能够降低绝缘子7的表面的沉积物,提高火花点火塞60的发火性、耐久性。火花点火装置6并不限定于上述的各实施方式的构成,在不脱离本发明的主旨的范围内,可以进行各种变更。此外,火花点火塞60的构成部件,例如端子金属零件的形状及材质、作为导电性密封层及电阻体的材料、及绝缘子7、安装金属零件的形状等可适宜变更。上述实施方式中,对使用火花点火装置6作为汽车发动机用途的例子进行了说明,但并不局限于汽车,也可以是废热发电、气体压力泵等中使用的内燃机用的闪光火花塞p。符号说明1-激光点火装置(点火装置),3-外壳,4-激光火花塞(火花塞),5-内燃机,10-光学窗(火花塞构成部件),11-超亲水膜,12-光学元件,20-缓冲部件,21-密封部件,22-光学窗保持架,23-聚光透镜保持架,30-包铆接部,31-热铆接部,32-筒状部,33-螺纹部,50-发动机盖(燃烧室壁),51-燃烧室,52-活塞,110-超亲水性粒子,111-热激发催化剂粒子,120-聚光透镜,121-扩展透镜,122-激光谐振器,123-准直透镜,124-激发光源,fp-焦点,lsrpmp-激发激光,lsrpls-脉冲激光。当前第1页12