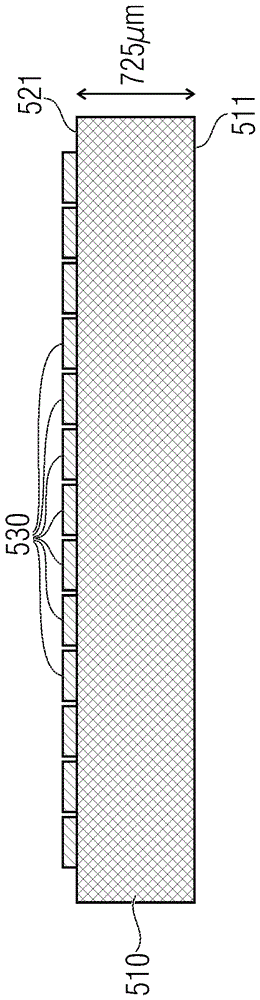
本发明的实施例涉及用于加工晶片的方法。本发明的另外的实施例涉及晶片。另外的实施例涉及用于硅扩音器的全表面(surface-wide)博世(Bosch)蚀刻(200μm)方法。
背景技术:当电子应用并且还有微机电系统(MEMS)在尺寸上缩小时,进行研究以减小用于各种电子和MEMS应用的电子部件和/或MEMS的占位空间(footprint)和厚度两者。对减小部件的尺寸的希望和/或需要有几个原因。为了在给定规模获得所需物理效果,部件需要具有合适的尺寸和比例。例如,减小加速度传感器的可移动元件的横向尺寸也可导致可移动元件的质量减少。为了维持加速度传感器的所需的灵敏性,可移动元件的悬架的刚性需要被减小,这会要求悬架机构的厚度的减小。简单地说,电子结构或MEMS结构的尺寸的减小通常可能会涉及在整个三维中尺寸的减小,以维持部件的比例并由此维持部件的所需的性能。从经济的观点来说,尺寸减小意味着更多的集成电路或MEMS器件可装配在给定尺寸的晶片上,从而导致每个电路或器件的减小的制造成本。一些MEMS器件不仅需要在晶片的前表面处加工,而且需要从晶片的后表面加工。通常,MEMS结构的主要部分被形成在前表面,使得从后表面一直通过晶片到前表面形成一个或多个腔体,以便便利需要从后表面被执行的制造步骤。所述一个或多个腔体可利用各种蚀刻工艺被形成,例如湿法蚀刻工艺或干法蚀刻工艺。利用湿法蚀刻工艺,通常可获得腔体的仅相对小的纵横比,即,为了达到所需的深度,腔体需要在后表面处相对宽。因此,MEMS结构不能被彼此放置得太近,这导致晶片产业(waferestate)的浪费。另一方面,干法蚀刻技术产生高纵横比,但是相对慢并且因此昂贵。特别地,干法蚀刻需要的设备通常是昂贵的,并且如果一批花费超过一整天的时间,当将达到所需的生产量或生产能力时,需要大量的干法蚀刻设备。尤其是结合薄晶片需要考虑的另一方面是一些用于晶片变薄的技术,尤其是例如研磨的机械技术,只能被使用下至特定最小晶片厚度。在这个最小晶片厚度以下,机械晶片变薄技术承受损坏晶片和/或形成在晶片的(前)表面处的MEMS结构的高风险。
技术实现要素:本发明的实施例提供用于加工具有第一主表面和第二主表面的晶片的方法。微机电系统结构被布置在第一主表面处。所述方法包括在第二主表面处施加掩蔽材料并且构造所述掩蔽材料以在第二主表面处得到多个掩蔽区域和多个未掩蔽区域。所述方法也包括在未掩蔽区域处从第二主表面各向异性地蚀刻所述晶片以形成多个凹进。此外,所述方法包括至少在其中一些掩蔽区域处去除掩蔽材料以得到预先掩蔽区域。所述方法也包括在未掩蔽区域和预先掩蔽区域处从第二主表面各向异性地蚀刻晶片以在预先掩蔽区域处增加凹进的深度并减小晶片的厚度。本发明的另外的实施例提供包括体材料和绝缘材料的堆叠、多个微机电系统结构、和多个凹进的晶片。所述绝缘材料形成晶片的第一主表面并且所述体材料形成晶片的第二主表面。所述堆叠具有从第一主表面延伸到第二主表面的在150μm和250μm之间的厚度。所述多个微机电系统结构被布置在第一主表面处。所述多个凹进的每个凹进从第二主表面穿过体材料和绝缘材料延伸到所述多个微机电系统结构的相应微机电系统结构。附图说明将使用附图来描述本发明的实施例,在附图中:图1是根据实施例的用于加工晶片的方法的示意流程图;图2是根据另外的实施例的用于加工晶片的方法的示意流程图;图3是根据另外的实施例的用于加工晶片的方法的示意流程图;图4A到4H示出根据实施例的在用于加工晶片的方法的不同阶段穿过晶片的示意截面;并且图5A到5D示出根据实施例的在用于加工晶片的方法的不同阶段期间晶片的示意截面。具体实施方式在本发明的实施例将在下面使用附图被详细地描述之前,将被指出的是相同的元件或具有相同功能的元件被提供有相同的参考数字或相似的参考数字,并且被提供有相同/相似的参考数字的元件的重复描述被省略了。因此,被提供用于具有相同/相似参考数字的元件的描述是相互可交换的。图1示出用于加工晶片的方法的示意流程图。所述方法开始于已经经历了几种加工的晶片,以致微机电系统结构被布置在晶片的第一主表面处。所述微机电系统(MEMS)结构可以是加工过的或半加工的。例如,半加工的MEMS结构仍可以包括在前面制造工艺期间已经被使用的牺牲材料,以便例如在MEMS结构内限定将来的腔体或开放空间。因此,这样的牺牲材料需要被去除以完成MEMS制造工艺。所述晶片也具有通常与第一主表面相对的第二主表面。如在图1的示意流程图中可看到的,所述方法包括在第二主表面处施加掩蔽材料的步骤102。所述掩蔽材料可以是光致抗蚀剂并且它到第二主表面的施加可以通过,例如旋涂工艺来实现。根据用来在第二主表面处施加掩蔽材料的方法,所述晶片可能必须被机械操作并且因而受到机械应力。在使用这样的掩蔽材料施加方法的情况下,晶片需要具有特定最小厚度,以减小晶片破裂或在第一主表面处对微机电系统结构的损坏的风险。在步骤104,所述掩蔽材料被构造来得到在第二主表面处的多个掩蔽区域和多个未掩蔽区域。构造掩蔽材料可以通过在晶片的第二主表面处执行光刻来被实现。如在图1的流程图中示意性地示出的方法的步骤106所示的,晶片在未掩蔽区域处从第二主表面被各向异性地蚀刻以形成多个凹进。所述凹进可以以后形成加工过的晶片或加工过的MEMS器件的孔、腔体、通道等,并且因而可在第一主表面处的微机电系统结构的制造和/或操作期间实现功能。在各向异性蚀刻步骤106期间,在第二主表面处的掩蔽区域基本上不受蚀刻工艺影响。然后至少在其中一些掩蔽区域处去除掩蔽材料以得到预先掩蔽区域,如在步骤108所示的。特别地,基本上全部掩蔽材料可从第二主表面被去除,使得整个第二主表面被暴露。此外,任何仍可存在于第一主表面处的残余掩蔽材料也可在步骤108期间被去除。去除掩蔽材料可能需要去除基本上所有的掩蔽材料,使得所有掩蔽区域被暴露,即在步骤108期间所有掩蔽区域变成预先掩蔽区域。在步骤110,晶片在未掩蔽区域处从第二主表面被(又一次)各向异性地蚀刻,并且这次也在预先掩蔽区域处被蚀刻以在预先掩蔽区域处增加凹进的深度并且减小晶片的厚度。在预先掩蔽区域构成基本上整个第二主表面(除了所述多个凹进以外)的情况下,整个晶片的厚度以基本均匀的方式减小。同时,凹进被进一步扩大并且可因此最终到达第一主表面附近的蚀刻停止层,或者它们可以直接到达第一主层。注意,一些各向异性蚀刻工艺可能会剩下晶片的边缘区域,使得在这个边缘区域处晶片厚度没有减少或者仅略微地被减少。所述边缘区域通常具有沿径向的在5mm和12mm之间的宽度。因为这个效果,在一些实施例中,术语“第二主表面的整个区域”可以排除边缘区域。注意,步骤106,108和110不需要晶片的机械加工步骤。因此,晶片厚度尤其在步骤110期间可被减小为远低于机械晶片变薄工艺所需的最小晶片厚度的阈值。步骤110合并两个任务,即直到凹进一直穿通基本上到达在第一主表面处的相应微机电系统结构为止的凹进的完成,以及晶片厚度的减小。因此,在步骤110期间的主要被执行来得到或完成凹进的蚀刻工艺也被用于减小晶片厚度。通常,不存在对在步骤110之后机械地加工晶片的需要,除了不引起晶片破裂或其它损伤的主要风险的晶片传送和运输以外。换句话说,在未掩蔽区域和预先掩蔽区域处各向异性地蚀刻晶片将在预先掩蔽区域处的晶片的厚度减小到最终晶片厚度。在实施例中,最终晶片厚度可以小于250μm。在用于加工晶片的方法的另外的实施例中,最终晶片厚度可以小于230μm,小于210μm,小于200μm,小于180μm,或者甚至小于170μm。用于最终晶片的在170μm和250μm之间的以1μm间隔隔开的中间值也被公开。相比之下,在步骤102之前并且在第二主表面处施加掩蔽材料之前,晶片可以具有在270μm和400μm之间的厚度。又一次地,以1μm间隔隔开的中间值也被公开。在作用于未掩蔽区域和预先掩蔽区域的各向异性蚀刻工艺期间,凹进的深度可以以在80μm和140μm之间的值被增加。同时,晶片的厚度可以以相同量(即在80μm和140μm之间)被减少。然而,注意,一旦到达蚀刻停止层,凹进深度的增加可以停止,而只要各向异性蚀刻工艺持续,晶片厚度的减小仍可继续。除了在图1中示意地示出的工艺步骤,用于加工晶片的方法可进一步包括在施加掩蔽材料之前,即在步骤102之前,在晶片的第二主表面处通过机械工艺来减小晶片的给定厚度的步骤。特别地,所述机械工艺可包括研磨第二主表面。机械工艺可特别地、进一步地、或替代地包括TAIKO工艺。根据TAIKO工艺,第二主表面的研磨并没有跨越第二主表面的整个区域发生,而只是在第二主表面的中心区域内发生。因此,TAIKO工艺留下边缘或边沿,在那里晶片基本上保持它的初始厚度。由于晶片的较厚的边缘区域,所述TAIKO工艺产生机械更稳定的晶片。所述TAIKO工艺可能具有来自日本词“taiko”的名称,该词意思是“鼓”。晶片可包括在第一主表面处邻近微机电系统结构的绝缘层(或隔绝层)。特别地,绝缘层可将微机电系统结构与晶片的体材料或衬底材料分离。绝缘层可用作MEMS结构之间的相对于衬底的电绝缘,而且(或可替代地)它可用作蚀刻停止层,使得当到达蚀刻停止层时凹进的蚀刻停止,其可发生在步骤110的各向异性蚀刻工艺期间。在步骤110的各向异性蚀刻工艺之后,所述绝缘层可通过不同蚀刻工艺被去除。特别地,该不同蚀刻工艺可以对于用于绝缘层的材料有选择性。所述用于加工晶片的方法可进一步包括通过去除微机电系统结构内的牺牲材料来释放微机电系统结构的一个或多个部件的可选步骤。该可选步骤可在未掩蔽区域和预先掩蔽区域处晶片的各向异性蚀刻之后被执行。牺牲材料可通过湿法蚀刻工艺或灰化工艺被去除。在牺牲材料和前面提到的绝缘层的材料以适当的方式被选择的情况下,可通过与用于去除微机电系统结构内的牺牲材料相同的工艺,去除至少在凹进内的绝缘层。步骤106和110,在其期间晶片从第二主表面被各向异性地蚀刻,可剩下晶片的边缘区域。这可能是由孔或者由用于各向异性蚀刻工艺的电场的结构导致的。特别地,在步骤110期间,在边缘区域中晶片的厚度可因此基本上没有减少。所得到的基本初始晶片厚度的边缘增强了晶片的机械稳定性并且可因此便于晶片的进一步传送。在这方面中,基于各向异性地蚀刻晶片的晶片变薄工艺展示了与上面提到的机械TAIKO工艺相似的性能。换句话说,这样的工艺步骤可被看作非机械TAIKO工艺或基于蚀刻的TAIKO工艺。在未掩蔽区域处从第二主表面各向异性地蚀刻晶片的步骤106可以是时间控制的工艺。所述晶片可以具有至少200mm的直径,其大约等于8英寸。相对大的晶片直径(例如200mm和更大)与越来越小的晶片厚度的结合对晶片需要经受住后面的制造步骤提出了挑战。此处公开的实施例提出了用于获得大直径、薄晶片的方法。根据一些实施例,微机电系统结构可以是声音换能器。例如,声音换能器可以是扩音器或扬声器。采用MEMS技术的声音换能器通常是静电扬声器,然而其它驱动原理当然是可能的和可想象的。静电MEMS声音换能器通常包括隔膜和一个或两个反电极。在声音换能器的工作期间,隔膜可在MEMS声音换能器的体积内振动。这个体积在所述MEMS声音换能器制造期间通常被牺牲材料填充。此外,MEMS声音换能器可以具有对隔膜的机械性能和声音换能器的谐振性能具有影响的背部体积或背部腔体。因此,根据声音换能器的所需性能来设计背部体积和给背部体积定尺寸通常是所希望的。背部体积的尺寸的好的设计和选择可改善例如声音换能器的信噪比(SNR)和/或效率。例如,MEMS声音换能器的一些应用可能需要大约200μm的背部体积的高度。背部体积可由MEMS声音换能器的第二主表面形成,使得在第二表面处它是开放的。在这些情况下,背部体积通常通过将MEMS声音换能器附着到另一衬底或芯片来被稍后闭合,所述另一衬底或芯片可包括用于MEMS声音换能器和/或其它信号处理电路的驱动电路。在这样的布置中,背部体积的高度基本上等于MEMS声音换能器的高度,并且因而等于最终晶片厚度。用于MEMS声音换能器的实际应用的实例是英飞凌(Infineon)的DSOUND产品系列。考虑到对于硅扩音器的背部体积的合适形状和尺寸的上面讨论的要求,大约200μm的部件高度将被实现用于所述DSOUND产品系列。然而,由于产品的特性,目前没有可行的或可用的支撑材料。此处提出的实施例的仿真和首次预试验表明在制造,加工,信噪比和/或成本方面的改进。除此以外,博世蚀刻设备(例如,Aviza博世蚀刻室)的处理能力的大约25%的容量增益看来似乎是可行的。在DSOUND产品系列内,以前没有产品可用,其已经被产生为具有200μm的部件高度。就发明人了解的,发明人是第一个能制造具有DSOUND扩音器的200μm厚,8英寸晶片。直至现在,由受让人使用制造工艺,根据其,晶片被蚀刻到400μm的厚度并且利用博世蚀刻工艺随后在背面(第二主表面)“被打孔”18,000个孔。根据提出的用于加工的方法,替代蚀刻晶片和给晶片打孔,在晶片上执行研磨以将晶片厚度减小了附加的100μm,即到大约300μm的厚度。然后时间控制的博世工艺被执行,使得该腔体或多个腔体延伸到晶片中仅200μm。随后晶片从光致抗蚀剂被完全剥离并且然后在Aviza博世蚀刻反应器中被全表面蚀刻了100μm。以这种方式,代替机械工艺,等离子体变薄工艺被提供。所述晶片以非常平缓的方式被加工。因为在前表面和后表面处没有光致抗蚀剂,晶片因而被直接带到释放蚀刻工艺,在其期间,扩音器的空隙被释放蚀刻。晶片的加工现在完成。请注意,上面的加工晶片的可能方法的描述只是一个实例,其不应当以任何方式被解释为限制性的。实施例提供将达到最终晶片厚度的四分之一以上的变薄工艺改变成机械研磨工艺,导致节省博世蚀刻所需的时间的25%。此外,在博世蚀刻工艺之后的刻印(lithography)工艺以及在晶片的200μm厚的状态的任何另外的光刻步骤可被省掉。当使用至少其中一些实施例时,增长的产量通常可以被预期。图2示出了根据另外的实施例的用于加工晶片的方法的示意流程图。所述方法开始于具有至少8英寸,或大约200mm的直径的晶片。所述晶片具有第一主表面和第二主表面。微机电系统结构(MEMS结构)被布置在第一主表面处。绝缘层将微机电系统结构与晶片的体材料分离。所述方法以步骤202开始,在其期间晶片的给定厚度通过在第二主表面处执行的机械工艺被减小。所述机械工艺生产具有在270μm和400μm之间(具有1μm间隔的中间值也被公开)的晶片厚度的晶片。如在步骤204示出的,掩蔽材料然后被施加在第二主表面处。掩蔽材料然后可以被构造以得到在第二主表面处的多个掩蔽区域和多个未掩蔽区域(步骤206)。根据步骤208,晶片在未掩蔽区域处从第二主表面被各向异性地蚀刻以形成具有在150μm和250μm之间(具有1μm间隔宽度的中间值也被公开)的深度的多个凹进(例如,腔体)。如在根据图2的流程图的用于加工晶片的方法的步骤210所示的,所述掩蔽材料然后至少在其中一些掩蔽区域处被去除以暴露(并且因而得到)预先掩蔽区域。步骤212表明晶片又一次从第二主表面被各向异性地蚀刻,然而这次不仅在凹进(其先前通过在未掩蔽区域处各向异性地蚀刻晶片已经(步骤208)被得到)的底部处,而且在预先掩蔽区域(其通过在步骤210期间至少在其中一些掩蔽区域处去除掩蔽材料已经被暴露)处。所述各向异性蚀刻至少持续到绝缘层(例如,氧化物、氮化物、碳化物、氧化硅、氮化硅、或碳化硅)被到达为止。同时,当凹进在深度上被扩大时,晶片的厚度在预先掩蔽区域处被减小。晶片的最终厚度小于250μm,可能小于220μm,可能小于200μm,并且可能甚至小于180μm。在步骤212的各向异性蚀刻工艺的目的是增加凹进的深度并在预先掩蔽区域处将晶片的厚度减小到所提到的最终厚度。根据步骤214,通过凹进可到达的部分绝缘层被去除。此外,微机电系统结构的一个或多个部件可在步骤214之前,在步骤214之后,或者与步骤214同时地通过除去微机电系统结构内的牺牲材料被释放。将被释放的所述一个或多个部件可以是,例如,声音换能器的隔膜或者加速度传感器的可移动的块。图3示出根据实施例的用于加工晶片的另外的方法的示意流程图。再一次,晶片具有第一主表面和第二主表面。微机电系统结构被布置在第一主表面处。所述方法包括在第二主表面处施加光致抗蚀剂的步骤302。所述光致抗蚀剂用作掩蔽材料并且在随后的步骤301期间被构造。光致抗蚀剂的构造产生了在晶片的第二主表面处的多个掩蔽区域和多个未掩蔽区域。根据步骤306,博世工艺在第二主表面处被执行以在未掩蔽区域处形成多个凹进(例如,腔体)。随后,如在步骤308所示的,光致抗蚀剂至少在其中一些掩蔽区域处被去除以得到预先掩蔽区域。根据一些实施例,不仅光致抗蚀剂的一部分被去除,而且基本上整个光致抗蚀剂被去除。而且,光致抗蚀剂的去除可不仅涉及晶片的第二主表面,而且涉及第一主表面。至少根据一些实施例,过了这个阶段之后,不需要进一步的光刻工艺,使得任何残留的光致抗蚀剂可从晶片被去除。如在步骤310所示的,博世工艺然后可在未掩蔽区域和预先掩蔽区域处被继续以增加凹进的深度并减小晶片在预先掩蔽区域处的厚度。如上面提到的,所述预先掩蔽区域可构成基本上整个第二主表面(由博世工艺剩下的凹进和/或边缘区域除外),使得基本上整个晶片被变薄直到达到所需的最终晶片厚度为止。上面在图1和2的情况下描述的用于加工晶片的方法的可选工艺步骤和可选结构也可适用于根据在图3中所示的流程图的用于加工晶片的方法。因此,这样的组合与此一起被公开。图4A到4H示出根据实施例的在加工晶片的不同阶段的晶片的示意截面。图4A示出根据实施例的晶片在它的初始状态(即在执行用于加工晶片的方法之前)的示意截面。所述晶片已经经历了一些预先加工,尤其为了在晶片的第一主表面421处形成微机电系统结构430。所述晶片主要由体材料或衬底410构成。所述绝缘层420将体材料或衬底410与微机电系统结构430分离。所述绝缘层420将在后面用作蚀刻停止层,这将在下面被解释。所述晶片进一步包括第二主表面411。如在图4A中可看到的,研磨工艺在第二主表面411处被执行,以减小晶片的厚度。在实施例中,研磨工艺可以是TAIKO工艺。代替机械加工第二主表面411,第二主表面411也可被蚀刻以减小晶片的厚度。在图4A到4H所示出的实施例中,所述晶片厚度被减小到大约300μm,如在图4B中所示的。然而,对于这个中间晶片厚度的其它值也是可想象的,例如,从270μm变动到400μm。图4B进一步示意性地示出将掩蔽材料,例如光致抗蚀剂施加到晶片的第二主表面411。如在图4C中示意性地示出的,在第二主表面处执行光刻以构造掩蔽材料440。构造掩蔽材料440的结果可在图4D中看到,其中三个未掩蔽区域442被形成在掩蔽材料440中。仍然存在于第二主表面411处的掩蔽材料440覆盖第二主表面411的掩蔽区域。图4D进一步示出晶片的体材料或衬底410的各向异性蚀刻。利用掩蔽材料440内的未掩蔽区域442,各向异性蚀刻以局部限制的方式作用于体材料410上。多个凹进因而被形成。图4E示出在图4D的各向异性蚀刻工艺之后穿过晶片的示意截面。图4D的各向异性蚀刻工艺基本上分别相应于在图1,2,或3中的流程图的方法步骤106,208,和306。多个凹进412已经被形成在晶片的体材料或衬底410内。在图4E所示的实例中,凹进412的深度从第二主表面411大约是200μm。所述多个凹进的每个具有相对大的纵横比,即凹进412的深度比凹进412的横向尺寸相对大。例如,每个凹进412的深度可以等于或大于凹进412的直径或宽度(纵横比≥1)。在实施例中,纵横比可以大于1,例如,纵横比=1.5,纵横比=2,或纵横比=3。图4E也示意性地示出去除掩蔽材料。这可以通过使用合适的溶剂或试剂溶解掩蔽材料来实现。如在图4F中示意性地示出的,进一步的各向异性蚀刻在晶片的第二主表面411处被执行。在图4E中示出的步骤期间掩蔽材料被去除,使得现在在图4D中示意性地示出的工艺步骤期间,预先掩蔽区域也受到各向异性蚀刻的影响。所述多个凹进412的深度被进一步增加,并且同时,在预先掩蔽区域处的晶片厚度被减小(参见图4F中的虚线)。各向异性蚀刻工艺至少持续到所述凹进412已经到达构成用于各向异性蚀刻工艺的蚀刻停止层的绝缘层420为止。在所示的实例中,各向异性蚀刻工艺将在预先掩蔽区域处的晶片厚度减小了大约100μm。在图4G中,以截面示意性地示出在图4F的各向异性蚀刻工艺完成之后的晶片。在图4G中,虚线表明在图4F的各向异性蚀刻工艺之前的晶片的结构。参考数字419表明体材料或衬底410的已经通过各向异性蚀刻工艺被蚀刻掉的那些部分。晶片现在具有大约200μm的晶片厚度。释放蚀刻可以现在被执行以去除至少在凹进412内的绝缘层420和/或去除在微机电系统结构430内的任何牺牲材料。释放蚀刻工艺可以是湿法蚀刻工艺。在替代方案中,牺牲材料可以是例如碳,其可以通过灰化工艺被去除。使用碳作为牺牲材料并且执行灰化工艺以便释放MEMS结构的一个或多个部件通常解决了与以前用以释放MEMS部件或子结构的湿法蚀刻工艺相关联的多个问题。图4H示出通常只是在将晶片单体化成多个MEMS器件之前在最终阶段的晶片的示意截面。图5A到5D示出根据实施例的在用于加工晶片的方法的不同加工阶段的晶片的示意截面。特别地,图5A到5D示出用于DSOUND和200μm晶片厚度的全区域或全表面回蚀工艺。图5A示意性地示出具有725μm的晶片厚度的晶片410的截面。所述厚度在第一主表面521和第二主表面511之间被测量。在第一主表面421处,布置多个微机电系统结构430(例如,SIMICDSOUND扩音器)。所述微机电系统结构530除了最终的释放蚀刻步骤外被完全加工。图5B示意性地示出已经利用研磨将晶片的厚度减小到300μm之后的晶片。图5C示意性地示出在用来在第二主表面(背部表面)处形成多个腔体或凹进的光刻工艺和时间控制的腔体蚀刻工艺之后的晶片。参考数字450表示被构造的光致抗蚀剂。凹进512借助通过光致抗蚀剂540的未掩蔽区域蚀刻晶片衬底510已经被形成。时间控制的腔体蚀刻产生具有大约200μm的深度的凹进或腔体512。图5D示意性地示出在没有光致抗蚀剂的全区域博世回蚀工艺被执行后的晶片。在图5D示出的实例中,100μm全区域回蚀被执行。结果,得到200μm晶片厚度的晶片。尽管在装置的情况下描述了一些方面,显然这些方面也代表了相应方法的描述,其中模块或器件相应于方法步骤或方法步骤的特征。类似地,在方法步骤的情况下描述的方面也代表相应模块或者相应装置的项或特征的描述。方法步骤的一些或全部可通过(或使用)硬件装置被执行,比如说例如,微处理器,可编程计算机或电子电路。在一些实施例中,最重要的方法步骤的某一个或多个可通过这样的装置被执行。上面描述的实施例对本发明的原理只是说明性的。应理解的是,此处描述的细节和布置的修改和变型对于本领域技术人员来说将是明显的。因此,其旨在仅被紧接着的专利权利要求的范围限制并且不被借助此处的实施例的描述和解释提供的特定细节限制。在前面的详细描述中,可看到各种特征在实施例中被分组在一起,用于简化本公开的目的。这种公开的方法不应被解释成反映一种意图,即所要求保护的实施例需要比在每个权利要求中明确陈述的特征更多的特征。相反,如下面的权利要求反映的,发明主题可在于少于单个公开的实施例的所有特征。因此,下面的权利要求在此被并入到详细描述中,其中每个权利要求可以独立作为单独的实施例。虽然每个权利要求可以独立作为单独的实施例,应该注意,尽管从属权利要求在权利要求中可以涉及与一个或多个其它权利要求的特定结合,但其它实施例也可以包括该从属权利要求与每个其它从属权利要求的主题的结合或者每个特征与其它从属权利要求或独立权利要求的结合。这种结合在此被提出,除非声明特定的结合不是预期的。此外,其旨在也将权利要求的特征包括到任何其它独立权利要求,即使这个权利要求没有被直接地从属于该独立权利要求。应进一步注意,在说明书或在权利要求中公开的方法可以通过具有用于执行这些方法的各自步骤的每个的装置的设备来实现。此外,在一些实施例中单个步骤可以包括或者可以被分解成多个子步骤。除非明确排除,这样的子步骤可以被包括并且是该单个步骤的公开的一部分。