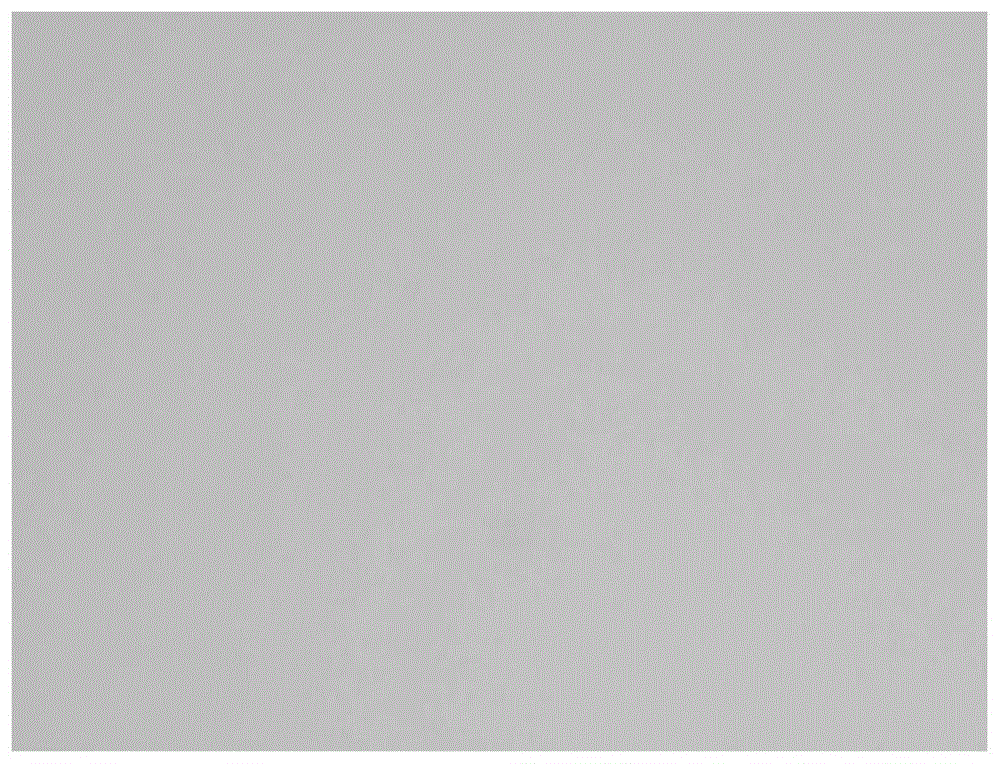
本发明涉及发光领域,尤其涉及一种发光器件、显示面板及制作方法。
背景技术:
:有机发光二极管(oled)显示因其高对比、广视角、快速响应等特点,被越来越多的人了解,但蒸镀法制程造价昂贵,使得应用oled面板的终端产品价格高昂,因此人们纷纷把目光投向了价廉的湿法制程,其中量子点发光二极管(qled)和聚合物有机发光二极管(poled)就是典型代表。与蒸镀法调控速率来控制膜层形貌不同,湿法制作的膜层粗糙度控制非常难,受很多方面影响,如墨水溶剂成分(挥发性)、成膜工艺、干燥烘烤工艺、制作时温湿度环境等,由于qled和poled都是多层堆叠结构,上述任何因素变动,批次之间的膜层质量差别就会很大;另一方面,湿法制作中,膜层的粗糙度会逐渐累积,在制作顶电极后点亮时,往往能观察到发光不均匀的现象,因此,亟需一种有效的手段来改善并提升器件性能。技术实现要素:为了克服现有技术的不足,本发明的目的在于提供一种发光器件,改善湿法制作器件的发光均匀性,提高器件的发光效率和寿命。为实现上述目的采用如下技术方案:根据本发明的一个方面,提供了一种发光器件,包括底电极、功能层和顶电极,上述功能层与上述顶电极相邻,还包括上述顶电极与上述功能层之间的平滑层,上述功能层包括发光层。进一步地,上述平滑层的材料包括聚合物或小分子化合物,上述聚合物为高聚物或齐聚物。进一步地,上述聚合物选自由pei、peie、pvb、pvp、peg组成的组中的一种或多种;上述小分子化合物选自由oled蒸镀材料、羟基醛、羟基酸组成的组中的一种或多种。进一步地,上述聚合物单体选自由丙烯酸酯类单体、乙烯基类单体、乙烯基醚类单体、环氧类单体组成的组中的一种或多种。进一步地,上述平滑层的厚度为3~20nm,优选为3~10nm。进一步地,上述底电极为反射电极,上述顶电极为半透明电极;或者上述底电极为半透明电极,上述顶电极为反射电极或半透明电极。进一步地,上述反射电极的材料为金属,上述反射电极的厚度为100~200nm;上述半透明电极的材料为金属或金属氧化物,当上述半透明电极的材料为金属时,上述半透明电极的厚度为10~25nm;当上述半透明电极为金属氧化物时,上述半透明电极的厚度为30~150nm。进一步地,上述发光器件还包括设置在上述反射电极上的功函数调节层;上述功函数调节厚度为5~20nm。根据本发明的一个方面,提供了一种上述发光器件的制备方法,包括以下步骤:在衬底基板上制作所述底电极;在所述底电极的远离所述衬底基板的一侧上制作所述功能层;在所述功能层的远离所述底电极的一侧上在制作所述平滑层;在所述平滑层的远离所述功能层的一侧上制作所述顶电极。进一步地,上述的功能层包括一层或多层,其中至少有一层采用湿法成膜工艺制作而成。进一步地,上述平滑层的材料为聚合物,上述平滑层采用湿法成膜工艺制作,形成上述平滑层的原料为聚合物溶液,上述聚合物溶液中聚合物的质量百分数为0.1~1wt%,上述聚合物溶液的溶剂选自酮类、醇类和水中的一种或多种;优选地,上述聚合物溶液中聚合物的质量百分数为0.1~0.5wt%。根据本发明的一个方面,提供了一种显示面板,包括上述的任一种发光器件。相比现有技术,湿法制作的各功能层会因受到制作工艺的限制造成膜层质量差别较大,每一层的粗糙度会逐渐累积,致使器件发光不均匀。应用本发明的技术方案,设置一层平滑层在顶电极和功能层之间,调整顶电极和功能层之间的接触面的形态,改善发光器件的发光均匀性,提高器件效率和寿命。附图说明图1为实施例1的器件点亮时发光面积部分区域的放大50倍的显微镜照片;图2为实施例2的器件点亮时发光面积部分区域的放大50倍的显微镜照片;图3为对比例1的器件点亮时发光面积部分区域的放大50倍的显微镜照片;图4为对比例2的器件点亮时发光面积部分区域的放大50倍的显微镜照片;图5为对比例3的器件点亮时发光面积部分区域的放大50倍的显微镜照片;以及图6为对比例4的器件点亮时发光面积部分区域的放大50倍的显微镜照片。具体实施方式下面,结合具体实施方式,对本发明做进一步描述,需要说明的是,在不相冲突的前提下,以下描述的各实施例之间或各技术特征之间可以任意组合形成新的实施例。在本发明的描述中,需要说明的是,对于方位词,如有术语“中心”,“横向”、“纵向”、“长度”、“宽度”、“厚度”、“上”、“下”、“前”、“后”、“左”、“右”、“竖直”、“水平”、“顶”、“底”、“内”、“外”、“顺时针”、“逆时针”等指示方位和位置关系为基于附图所示的方位或位置关系,仅是为了便于叙述本发明和简化描述,而不是指示或暗示所指的装置或元件必须具有特定的方位、以特定方位构造和操作,不能理解为限制本发明的具体保护范围。需要说明的是,本申请的说明书和权利要求书中的术语“第一”、“第二”等是用于区别类似的对象,而不必用于描述特定的顺序或先后次序。应该理解这样使用的数据在适当情况下可以互换,以便这里描述的本申请的实施例。此外,术语“包括”和“具有”以及他们的任何变形,意图在于覆盖不排他的包含,例如,包含了一系列步骤或单元的过程、方法、系统、产品或设备不必限于清楚地列出的那些步骤或单元,而是可包括没有清楚地列出的或对于这些过程、方法、产品或设备固有的其它步骤或单元。本申请提及的材料缩写除非特别说明,一般与oled或qled
技术领域:
的专业术语具有相同含义。在本发明一种典型的实施例中,提供一种发光器件,包括底电极、功能层和顶电极,功能层与顶电极相邻,还包括顶电极与功能层之间的平滑层,功能层包括发光层。通过设置一层平滑层在顶电极和功能层之间,调整顶电极和功能层之间的接触面的形态,改善发光器件的发光均匀性,提高器件效率和寿命。在一些实施例中,发光层为量子点发光层、有机小分子发光层、聚合物发光层中的一种或多种。在一些实施例中,量子点发光层中的量子点(qd)材料选自ⅱ-ⅵ族化合物、iii-v族化合物、iv族元素或化合物、iv-vi族化合物、ii-iii-v族化合物,或其组合任意组合而成的三元、四元化合物及核壳量子点,如cdse、cds、cdte、znse、zns、znte、inas、inp、gaas、gap、inp/zns、cds/znse、cds/zns、cdmns、innp组成的组中的一种或多种,但不限于此。在一些实施例中,有机小分子发光层可以是单一有机小分子发光材料,也可以是多种有机小分子材料的混合物,或是掺杂有磷光或荧光材料的混合物。有机小分子发光材料选自喹啉铝的衍生物、联苯二胺的衍生物、芳基取代三苯胺的衍生物、联噻吩的衍生物、二苯乙烯基芳基类衍生物、苝类衍生物、蒽类衍生物、螺芴、多芴类衍生物、有机硅类衍生物、有机硼类衍生物、邻菲罗林衍生物和联苯咔唑的衍生物,但不限于此。荧光或磷光材料可以选自苯乙烯基芳基类衍生物、喹吖啶酮类衍生物、苝类、芴类、螺芴类、香豆素类衍生物、铱、铂等的配合物、聚苯撑乙烯类衍生物、有机硅类、或有机硼类衍生物,但不限于此。在一些实施例中,聚合物发光层的材料包括可以是单一聚合物发光材料,或是掺杂有磷光或荧光材料的聚合物发光材料。聚合物发光材料包括但不限于:p-ppv、meh-ppv、pfb、pfs、f8bt等可溶液加工的聚合物发光材料。荧光或磷光染料选自苯乙烯基芳基类衍生物、喹吖啶酮类衍生物、苝类、芴类、螺芴类、香豆素类衍生物、铱、铂等的配合物、聚苯撑乙烯类衍生物、有机硅类、或有机硼类衍生物,但不限于此。在一些实施例中,平滑层的材料包括聚合物或小分子化合物,聚合物为高聚物或齐聚物。其中,高聚物分子量范围为大于10000;齐聚物范围的分子量为1000~10000;小分子化合物分子量的范围为小于1000。在一些实施例中,平滑层的材料可以是导电的也可以是绝缘的。在现有的发光器件制作过程中,各种功能层的材料种类通常是有限的,且为了确保上层功能层材料设置时不影响下层功能层材料,即不对其造成腐蚀或溶解,功能层溶剂的选择非常受限,另外,各个功能层的厚度通常有明确要求,因此各功能层原料的浓度也需要保持在一定范围内。上述原因都会使得成膜均匀性变差。而本申请中通过在顶电极和功能层之间设置平滑层,该平滑层的材料种类及浓度等的选择范围大很多,平滑层的成膜均匀性很容易好于各功能层,即容易获得表面平整的膜层,从而改善发光器件的发光均匀性。在一些实施例中,平滑层的粗糙度(ra)为小于等于1nm,优选平滑层的粗糙度(ra)小于等于0.5纳米。在一些实施例中,平滑层包括一层或多层,各层材料可以一样或不一样。在一些实施例中,聚合物选自由包括聚乙烯亚胺(pei)、聚乙氧基乙烯亚胺(peie)、聚乙烯醇缩丁醛(pvb)、聚乙烯吡咯烷酮(pvp)、聚乙二醇(peg)组成的组中的一种或多种;小分子化合物选自由包括oled蒸镀材料、羟基醛、羟基酸组成的组中的一种或多种。在一些实施例中,oled蒸镀(无机或有机)材料包括hnbphen、3tpymb、btb、pbd、bphen、bcp、tpbi、balq、bpy-oxd、bp-oxd-bpy、taz、ntaz、nbphen、zns、三(8-羟基喹啉)铝和bpy-foxd中的一种或多种,但不限于此。在一些实施例中,羟基醛包括3-羟基丙醛、二羟甲基乙醛、三羟甲基乙醛、2-羟甲基丙醛、2,2-二羟甲基丙醛、3-羟基-2-甲基丁醛、3-羟基戊醛和n-甲基-n-(2-羟乙基)-4-氨基苯甲醛中的一种或多种,但不限于此。在一些实施例中,羟基酸选自乳酸、柠檬酸、苹果酸和水杨酸中的一种或多种,但不限于此。在一些实施例中,聚合物通过聚合物单体聚合而成。在一些实施例中,聚合物单体选自由包括丙烯酸酯类单体、乙烯基类单体、乙烯基醚类单体、环氧类单体组成的组中的一种或多种。在一些实施例中,丙烯酸酯类单体包括丙烯酸甲酯、丙烯酸乙酯、丙烯酸丁酯、丙烯酸辛酯、甲基丙烯酸甲酯、甲基丙烯酸乙酯、甲基丙烯酸正丁酯、甲基丙烯酸异戊酯、甲基丙烯酸正己酯、甲基丙烯-2-乙基己酯、甲基丙烯酸异辛酯、甲基丙烯酸异壬酯、甲基丙烯酸癸酯、甲基丙烯酸十二烷醇酯、甲基丙烯酸异冰片酯、丙烯酸羟乙酯、丙烯酸羟丁酯、甲基丙烯酸羟乙酯、甲基丙烯酸羟丙酯、甲基丙烯酸苯氧乙酯、甲基丙烯酸甲氧基丙酯、甲基丙烯-2-甲氧基丁酯、丙烯酸n,n二甲氨基乙酯、甲基丙烯酸-n,n-二甲氨基乙酯和n,n-二甲氨基丙基丙烯酰胺,但不限于此。在一些实施例中,乙烯基类单体包括苯乙烯、n-乙烯基吡咯烷酮和乙酸乙烯酯,但不限于此。在一些实施例中,乙烯基醚类单体包括羟丁基乙烯基醚、羟甲基乙烯基醚、三乙二醇二乙烯基醚、1,4-环己基二甲醇二乙烯基醚和丁基乙烯基醚,但不限于此。在一些实施例中,环氧类单体包括环氧丙烷、环氧氯丙烷、3-羟基环氧丙烷、乙基缩水甘油醚、正丁基缩水甘油醚、甲基丙烯酸缩水甘油酯、丙烯酸缩水甘油酯、环氧溴丙烷、三羟甲基丙烷三缩水甘油醚、间苯二酚缩甲醛四缩水甘油醚,但不限于此。在一些实施例中,为了保证对粗糙度有较明显的改善,且避免不导电材料制备的平滑层过厚对发光器件导电性产生影响,平滑层的厚度为3~20nm,优选为3~10nm。在一些实施例中,底电极为反射电极,顶电极为半透明电极。在另一些实施例中,底电极为半透明电极,顶电极为反射电极或半透明电极。在一些实施例中,反射电极的材料为金属,该反射电极的厚度为100~200nm;半透明电极的材料为金属或金属氧化物。在一些实施例中,半透明电极的材料为金属,该半透明电极的厚度为10~25nm。在另一些实施例中,半透明电极为金属氧化物,该半透明电极的厚度为30~150nm。半透明电极的厚度主要考虑需要保证一定的导电性的前提下有尽可能高的可见光透过率,因此将该半透明电极做得比较薄。在一些实施例中,为了增强反射电极在衬底基板上的附着力,在衬底基板和反射电极之间还可以引入附着力改善层,比如金属氧化物膜层,如ito、al2o3等。在一些实施例中,发光器件还包括设置在反射电极上的功函数调节层,功函数调节层厚度为5~20nm,厚度太厚可能会吸光降低出光效率。功函数调节层的作用是确保电极的功函数与紧邻的功能层功函数匹配,提高发光效率。一般而言,反射电极一般都采用ag或al等金属,若直接在其表面施加空穴注入层如pedot:pss,显然两者的homo匹配性差,不利于空穴注入,此时,若在此反射电极表面添加如20nmito,ito与pedot:pss的homo较为匹配,显然利于空穴注入。功函数调节层可以是金属氧化物膜层。在一些实施例中,也可以不施加该功函数调节层,只通过改变器件结构来实现该效果,如,在反射电极上直接施加电子注入传输层,如zno纳米晶层,由于两者的lumo匹配性相对较好,电子的注入也不会受到影响,器件依然可以得到很好的效率。在一些实施例中,用作电极材料的金属包括但不限于ag、al、al/ag合金中任一种或其组合,用作电极材料的金属氧化物包括但不限于ito、zno(al)、zno中任一种或其组合。在一些实施例中,功能层包括一层或多层,其中,至少有一层采用湿法成膜工艺制作。功能层的层数越多,最终膜层累积的表面粗糙度越大,通过设置平滑层,器件的发光均匀性改善更为显著。在一些实施例中,功能层为多层,还可以包括空穴注入层、空穴传输层、电子传输层、电子注入层中至少一层,但不限于此。在一些实施例中,空穴注入层的材料选自pedot、氧化钼、氧化钒、氧化钨和氧化铬中的一种或多种,但不限于此。在一些实施例中,空穴传输层的材料选自poly-thx、poly-tpd、nio、tfb、pvk、cbp和tcta中的一种或多种,但不限于此。在一些实施例中,电子传输层的材料选自zno纳米晶、掺杂氧化锌纳米晶、tio2、sno、alzno、znsno和insno中的一种或多种,但不限于此。在一些实施例中,电子注入层的材料选自lif、cs2co3、csf、cscl、li、rb2co3和reo3中的一种或多种,但不限于此。在一些实施例中,平滑层的材料为聚合物,平滑层采用湿法成膜工艺制作。在另一些实施例中,平滑层的材料为小分子化合物,平滑层采用湿法成膜工艺或气相沉积法制作。在一些实施例中,湿法成膜工艺选自旋涂、喷墨打印、丝网印刷、狭缝涂布、喷涂和刮涂中任一种或多种的组合。在一些实施例中,平滑层的材料为聚合物,平滑层采用湿法成膜工艺制作,形成所述平滑层的原料为聚合物溶液,聚合物溶液中聚合物的质量分数为0.1~1wt%,聚合物溶液的溶剂选自酮类、醇类和水中的一种或多种。在一些优选的实施例中,聚合物溶液中聚合物的质量分数为0.10.5wt%。在本申请另一种典型的实施方式中,提供了前述任一种发光器件的制备方法,包括以下步骤:在衬底基板上制作底电极;在底电极的远离衬底基板的一侧上制作功能层;在功能层的远离底电极的一侧上在制作平滑层;在平滑层的远离功能层的一侧上制作顶电极。通过设置一层平滑层在顶电极和功能层之间,改善发光器件的发光均匀性,提高器件效率和寿命。在一些实施例中,功能层包括一层或多层,其中,至少有一层采用湿法成膜工艺制作而成。当功能层包括多层时,其粗糙度积累较大,在功能层和顶电极之间设置平滑层能一步到位解决粗糙度问题,提高发光性能。在一些实施例中,平滑层的材料为聚合物,平滑层采用湿法成膜工艺制作而成。在另一些实施例中,平滑层的材料为小分子化合物时,平滑层采用湿法成膜工艺或气相沉积法制作而成。在一些实施例中,湿法成膜工艺选自旋涂、喷墨打印、丝网印刷、狭缝涂布、喷涂和刮涂中任一种或多种的组合,但不限于此。在一些实施例中,平滑层的材料为聚合物,平滑层采用湿法成膜工艺制作,优选地,形成所述平滑层的原料为聚合物溶液,聚合物溶液中聚合物的质量分数不超过1wt%,聚合物溶液的溶剂选自酮类、醇类和水中的一种或多种。在一些优选的实施例中,聚合物溶液中聚合物的质量分数不超过0.5wt%。在一些实施例中,为了降低溶剂对相邻功能层的影响,聚合物溶液的溶剂酮类选自丙酮、丁酮、戊酮中的一种或多种,但不限于此。在一些实施例中,为了降低溶剂对相邻功能层的影响,聚合物溶液的溶剂醇类选自甲醇、乙醇、丙醇、异丙醇、丁醇中的一种或多种,但不限于此。在本申请又一种典型的实施方式中,提供了一种显示面板,该显示面板包括前述的发光器件。尽管在实施例中描述了本发明中制作方法的各个步骤,但是,这并非要求或者暗示必须按照该特定顺序来执行这些步骤,或是必须执行全部所示的步骤才能实现期望的结果。附加的或备选的,可以省略某些步骤,将多个步骤合并为一个步骤执行,以及/或者将一个步骤分解为多个步骤执行等。下面将结合实施例和对比例进一步说明本申请提供的发光器件、显示面板和制作方法。实施例1本实施例的发光器件为双面发射器件,发光器件从下至上依次包括衬底基板、底电极(ito)、空穴注入层(pedot)、空穴传输层(tfb)、发光层(红色量子点rqd)、电子传输层(zno纳米晶)、平滑层(pei)、顶电极(ag)。具体制作步骤可以包括:s1、依次用去离子水和乙醇对ito衬底基板作超声处理,待ito衬底基板表面干燥后,在氧气等离子体清洁处理15min,底电极ito的厚度为150nm,衬底基板尺寸为0.7*30*30mm;s2、在ito衬底基板上依次旋涂制作包含多层结构的功能层:40nmpedot空穴注入层、30nmtfb空穴传输层、30nmrqd发光层和50nmzno纳米晶电子传输层;s3、在zno电子传输层上旋涂0.5wt%的聚乙烯亚胺pei(数均分子量为1万)的异丙醇溶液,旋涂转速为2500rpm,之后在氮气氛围下,100℃烘烤30min制得平滑层。pei干膜厚度为10nm;s4、蒸镀20nmag顶电极层后封装,完成发光器件制作。其显微镜下的发光情况见图1。实施例2本实施例的发光器件为顶发射器件,与实施例1的区别在于,底电极为120nmag/20nmito,其中ito为功函调节层。其显微镜下的发光情况见图2。实施例3与实施例1的区别在于步骤s3,其中,旋涂所用的平滑层材料为分子量为2000的聚乙二醇的乙醇溶液,浓度为0.1wt%,聚乙二醇干膜厚度为5nm。实施例4与实施例1的区别在于步骤s3,其中,平滑层材料为npb(小分子化合物),利用真空热蒸镀在10-6torr的真空条件下制作而成,npb膜层厚度为8nm。实施例5与实施例1的区别在于步骤s3,其中,平滑层材料为zns,利用真空热蒸镀在10-6torr的真空条件下制作而成,zns膜层厚度为20nm。实施例6与实施例1的区别在于步骤s3,其中,旋涂的平滑层原料为丙烯酸月桂酯单体和引发剂,旋涂后在365nm的uv灯下固化而成,聚丙烯酸酯膜层的厚度为3nm。实施例7与实施例1的区别在于步骤s3,其中,平滑层材料聚乙烯缩丁醛pvb(数均分子量约3万)和水杨酸的乙醇溶液,总固含量为1wt%,聚乙烯缩丁醛与水杨酸的质量比为95:5,最终所得平滑层的厚度为15nm。对比例1在制作过程中未施加平滑层pei,其余步骤与实施例1相同。其显微镜下的发光情况见图3。对比例2在制作过程中未施加平滑层pei,其余步骤与实施例2相同。其显微镜下的发光情况见图4。对比例3s1、依次用去离子水和乙醇对ito衬底基板作超声处理,待ito衬底基板表面干燥后,在氧气等离子体清洁处理15min,底电极ito的厚度为150nm,衬底基板尺寸为0.7*30*30mm;s2、在ito衬底基板上依次旋涂制作包含多层结构的功能层:40nmpedot空穴注入层、30nmtfb空穴传输层、30nmrqd发光层,在rqd发光层上旋涂0.5wt%的聚乙烯亚胺pei(数均分子量为1万)的异丙醇溶液,旋涂转速为2500rpm,之后在氮气氛围下,100℃烘烤30min制得平滑层。pei干膜厚度为10nm;s3、在平滑层上旋涂制备50nm厚度的zno纳米晶电子传输层;s4、在电子传输层上蒸镀20nmag顶电极层后封装,完成发光器件制作。其显微镜下的发光情况见图5。对比例4与对比例3的区别在于,pei膜层的厚度为3nm,其余工艺均与对比例3一致。其显微镜下的发光情况见图6。上述各实施例和对比例中功能层(多层)中的各层的材料配方一致。衬底基板除非特别说明,也一致。各发光器件的发光面积均为3mm*3mm。利用photoresearch公司的pr670对上述各实施例和对比例得到的发光器件进行性能测试,在2ma/cm2的电流密度下测试器件的外量子效率(eqe),并利用显微镜对器件的发光均匀性进行表征,结果如下表所示:编号eqe(%)寿命(h)实施例113.5625实施例212.9621实施例312.5610实施例413.1601实施例512589实施例612.7598实施例712.1609对比例111319对比例210.3321对比例38.3256对比例410.5325从上表的测试结果及显微镜照片可以看出,实施例1~7在加入平滑层后,发光器件的发光均匀性得到了明显的改善,外量子效率也有不同程度的提高。由于顶电极很薄,器件各功能层膜层制作过程产生的粗糙度累积后,得到的发光面具有湿法工艺特有的射线条纹“缺陷”(参见图3和图4),尽管功能层墨水配方可以利用高沸点溶剂减缓这种射线条纹“缺陷”,但相邻功能层正交溶剂(防止溶解下层材料)的选择性本身就非常窄,改善的空间非常有限。通过引入平滑层,射线条纹基本观察不到,改善非常明显,并且平滑层不仅没有降低器件外量子效率,反而使外量子效率有比较明显的提升。上述器件在5000cd/m2的亮度条件下监测其亮度衰减到t95(即器件亮度由5000cd/m2衰减到该值95%时所花费的时间)所需的时间,实施例有平滑层的器件寿命几乎是对比例器件的两倍,可见其对顶电极和功能层界面搭接的改善是非常显著的。对比例3,发光均匀性有略微改善,但是相比对比例1~2,外量子效率和寿命都降了,其平滑层的膜厚有10nm,可能影响了红色量子点与zno纳米晶之间电子传输与注入。对比例4,平滑层的位置与对比例3相同,但平滑层厚度减薄到3nm,与对比例1~2相比,平滑层的加入对器件效率和寿命影响不大,但是射线条纹几乎没有改善,也即发光均匀性没有改善。从对比例3~4结果可以知晓,当功能层包括多层时,多层均是湿法制作时,如仅在功能层内部设置平滑层,则难以避免与顶电极相邻的功能层仍存在较大粗糙度。当功能层包括多层时,多层并非均是湿法制作时,在平滑层上继续设置功能层的其他层采用蒸镀、溅射等制作时,由于蒸镀、溅射工艺的成膜均匀性相对容易掌控,仍可能得到均匀发光的器件。但需要指出的是,由于平滑层位于功能层内部,将影响功能层内部多层之间的载流子的传输与复合,因此该平滑层的膜厚会非常苛刻,膜厚一般不宜超过5nm,不超过3nm更佳(超薄层膜的制作工艺难度极大),但当前期累积的粗糙度较大时,5nm、3nm或更薄的膜层能起到的平坦化效果非常有限,在这种情况下,得到的器件发光均匀性还是较差。当然,也可以在顶电极与紧邻的功能层间再加一层平滑层,但这样显然增加了工艺的复杂性。因此将平滑层设置在功能层和顶电极之间具有很大优势。上述实施方式仅为本发明的优选实施方式,不能以此来限定本发明保护的范围,本领域的技术人员在本发明的基础上所做的任何非实质性的变化及替换均属于本发明所要求保护的范围。当前第1页12