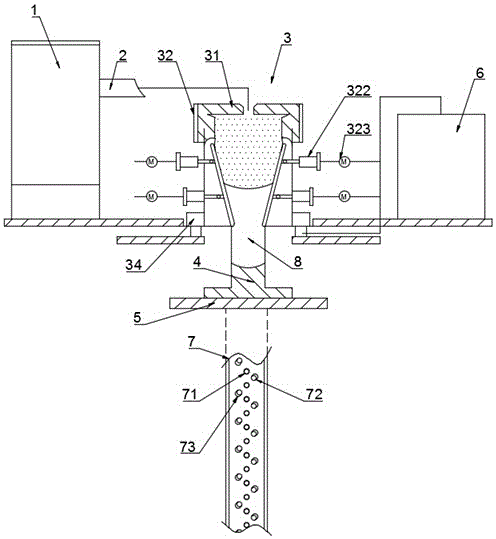
本发明涉及合金制备
技术领域:
,具体是涉及一种非真空下引半连铸铜锰合金扁锭的制备方法及其装置。
背景技术:
:铜锰合金是一种电阻材料,是用来制作电子仪器、测量仪表以及其他工业装置中电阻元件的一种基本材料。目前国内市场高端的锰铜合金都是进口的,国内生产工艺虽多采用非真空熔炼,但因为生产设备还不完善,生产的合金材料杂质含量高,成分组织不均匀,制成的贴片电阻电阻率、电阻温度系数不合格、无法形成规模化生产。本发明针对现有技术存在的不足,提供了一种非真空下引半连铸铜锰合金扁锭的生产工艺及其装置。技术实现要素:为了实现以上目的,本发明提供了一种非真空下引半连铸铜锰合金扁锭的生产工艺及其装置,针对实际生产中因结晶器内金属溶液与铜板粘连、导致的坯壳撕裂、引发漏液事故的问题,本发明重新设计了一种用于合金下引半连铸的结晶器;不仅如此,本发明还改进了对于铸锭的二次水冷装置,解决了因干涉喷泉导致的冷却不均匀、效率低的问题。本发明具体的技术方案如下:一、一种非真空下引半连铸铜锰合金扁锭的制备方法,具体包括以下步骤:s1、配料依照铜锰合金的组成配比,准备纯度99.9%的电解铜板、cumn90中间合金、mnni40中间合金、cusi16中间合金。s2、装炉依次向真空感应熔炼炉1的坩埚内装入电解铜板、mnni40中间合金,以及rj-2型覆盖剂。s3、熔炼在惰性气氛保护下,首先将坩埚温度升至1100℃,待电解铜板以及mnni40中间合金开始溶化时加入cumn90中间合金,随后补加cumn90中间合金和mnni40中间合金直至mn含量达到12.5~25.5%,ni含量达到2.1~10.1%。s4、精炼除气将坩埚温度缓慢升至1150℃,进行氩气除气和合金脱氧,出炉前加入cusi16中间合金并调整至si含量达到0.2~0.3%。s5、浇注s5-1、首先启动铸机,将底模的顶面升至感应器磁场强度最大位置处;接着启动冷却水系统;随后调整处于结晶器窄边的活动铜板的宽度以及锥度,调节感应器的电流强度为400~600a、频率为3hz,超声波发生器的纵振频率为20000~20200hz,输出振幅为16~20μm;最后将流槽预热至1200~1250℃、热顶预热至350~400℃。s5-2、使用色素炭黑覆盖结晶器,密封结晶器底部第一水冷机构。s5-3、将步骤s4中精炼后的合金液经流槽引入结晶器内进行浇注,合金液倒入流槽后及时打开燃气保护溜槽及结晶器入口,保证溜槽内液面平稳,不断流、不溢出。s6、铸造当浇注合金液流至底模,形成的半悬浮合金液柱体积占结晶器容积的70~85%时,使用第一水冷机构进行冷却,同时进行下引铸造,铸造速度缓慢由初始速度逐渐过渡到稳态速度50~80cm/min。s7、冷却s7-1、当铸造过程进入稳态阶段后,控制流槽中合金液液位,保持静压头和液位恒定,以及结晶器内合金液液面距结晶器顶部3~5mm;在此阶段,对结晶器水冷的同时,对牵引出的铸锭使用第二水冷机构进行二次水冷,水雾大小须保证铸锭从白亮将至暗红,不可直接冷至室温。s7-2、当坩埚内的合金液量降至埚容积的20%时,调小下引速度直至停止;待铸锭完全凝固后,关闭冷却水系统。二、一种非真空下引半连铸铜锰合金扁锭的制备装置本发明所使用到的装置,包括真空感应熔炼炉、结晶器、连接真空感应熔炼炉和结晶器的流槽、位于结晶器下方的底模以及与底模连接的铸机,具体的结构如下:所述结晶器包括结晶器外壳,所述结晶器外壳顶部套设有热顶,所述热顶外侧包裹有由不锈钢薄板制备的屏蔽罩。电磁铸造中,感应器产生的交流磁场同液体金属中的感生电流相互作用产生空间分布的电磁压力。由于电磁压力分布并不能很好地匹配液体金属的静压力分布,因此需要引入屏蔽罩改善磁场和电磁压力分布。屏蔽罩在交流磁场作用下产生与感应器电流反向的涡流,涡流同交变磁场相互作用,部分抵消了交变磁场,从而削弱了液柱的顶部磁场,抑制了电磁搅拌引起的熔体流动,形成比较稳定的金属液柱。本发明在屏蔽罩内用耐火材料制成热顶,约束金属液柱顶部熔体成型,即将热顶与屏蔽罩的功能合二为一。所述结晶器外壳窄边内侧设置有一对活动铜板,所述活动铜板靠近结晶器外壳侧连接有贯穿结晶器外壳的丝杠机构,所述丝杠机构与伺服电机连接。在实际生产中,有时一个浇次内有多个型号的订单,如果每个订单都停机更换结晶器显然是不经济的。为了提高铸机的作业率,本发明采用结晶器调宽技术来解决这一问题。结晶器采用伺服电机的电动调宽形式。电动调宽结构简单可靠,没有复杂的液压管路和部件,蜗轮蜗杆结构带有自锁特性,可以防止浇铸过程中结晶器的活动铜板的误动作。而结晶器的两个窄边各有上下两套丝杠机构,伺服电机的旋转通过蜗轮蜗杆机构传递为丝杠的平移运动,带动结晶器的活动铜板移动,这样结晶器的宽度和锥度就能够进行调节。所述结晶器外壳两个宽边外侧分别设置有感应器,所述感应器下方靠近结晶器外壳底部开口处设置有第一水冷机构。所述结晶器外壳底部设置有超声波发生器,所述超声波发生器是由波导座和设置在波导座下方的换能器组成。合金液在冷凝过程中很容易和结晶器的活动铜板发生粘结,一旦发生这种情况,会使拉矫阻力大大增加,并且铸坯的坯壳会被撕裂,发生漏液事故。倘若在浇铸过程中给结晶器施加一定的规律振动,合金液和结晶器内表面的润滑条件变好,摩擦力减小,即可防止粘结的发生,还可以使铸锭表面质量提高。进一步地,本发明还设置有用以冷却铸锭的第二水冷机构,所述第二水冷机构是由沿直线等间距排列的竖直喷嘴,以及分别设置在竖直喷嘴两侧的第一斜向喷嘴和第二斜向喷嘴组成。进一步地,所述第一斜向喷嘴和第二斜向喷嘴位于竖直喷嘴的间隔处,且二者间相互间隔。所述第一斜向喷嘴和第二斜向喷嘴的喷嘴斜向方向处于同一平面内,且朝向方向相对。第一水冷机构喷水孔直径为2.5mm,竖直喷嘴的冷却水喷射角(垂直射流与铸锭表面之间的夹角)为90°;第一斜向喷嘴和第二斜向喷嘴的的喷水孔直径为2mm,且斜向射流的喷射角均为60°。冷却水套采用厚6mm的环氧树脂板粘结组成,强度高、耐高温、不易变形,而且便于加工和改造。喷水孔的出口处与铸锭表面的水平间距为15mm。水冷却系统来提高电磁铸造过程的冷却效果。使用单排喷水冷却时,沿铸锭表面流动的水在两相邻的射流间相互冲击,会产生干涉喷泉。干涉喷泉使大量冷却水尚未吸收任何热量便离开了铸锭表面,因此冷却水溅射比较严重。垂直喷嘴沿铸锭表面喷出垂直射流,垂直射流朝相邻水流水平流动的冷却水在两相邻水流的中间相遇,形成干涉喷泉,在冷却水尚未离开铸锭表面之前,由第一斜向喷嘴和第二斜向喷嘴射出的斜向射流冲击在干涉喷泉上,使之又回到铸锭表面,且溅射水滴会相互碰撞融合,增大落回铸锭表面的概率。因此,采用本发明设计的水冷却机构不仅可以提高冷却水流量,能够改善冷却水的冷却效果,使耗水量下降,进而允许采用更高的水温而不使铸锭产生表面缺陷、裂纹、或翘曲现象。与现有的铸铜锰合金制备方法相比,本发明的有益效果是:(1)针对实际生产中因结晶器内铜锰溶液与铜板粘连、导致的坯壳撕裂、引发漏液事故的问题,本发明重新设计了一种具有超声波振荡结构的结晶器,配合能够调节宽度和锥度的活动铜板,能够有效防止粘结的发生,提高铸锭表面质量。(2)本发明设计的水冷却机构不仅可以提高冷却水流量,而且能够避免铸锭冷却常见的“干涉喷泉”现象,改善冷却水的冷却效果,使耗水量下降,进而允许采用更高的水温而不使铸锭产生表面缺陷、裂纹、或翘曲现象。附图说明图1是本发明的组装示意图;图2是本发明结晶器的结构示意图;图3是本发明第二水冷机构的结构意图;图4是本发明第二水冷机构进行冷却的原理示意图;图5是本发明结晶器的外观图;图6是本发明样片的低倍组织图图7是本发明样片的50倍金相图。图中:1-真空感应熔炼炉、2-流槽、3-结晶器、31-热顶、311-屏蔽罩、32-结晶器外壳、321-活动铜板、322-丝杠机构、323-伺服电机、33-感应器、34-超声波发生器、341-波导座、342-换能器、35-第一水冷机构、4-底模、5-铸机、6-电源、7-第二水冷机构、71-垂直喷嘴、72-第一斜向喷嘴、73-第二斜向喷嘴、74-干涉喷泉、75-垂直射流、76-斜向射流、8-铸锭。具体实施方式为更进一步阐述本发明所采取的方式和取得的效果,下面将结合附图对本发明的技术方案进行清楚和完整地描述。实施例一本实施例主要是对本发明使用的制备装置进行阐述,具体内容如下:如图1和图2所示,本发明所使用到的装置,包括真空感应熔炼炉1、结晶器3、连接真空感应熔炼炉1和结晶器3的流槽2、位于结晶器3下方的底模4以及与底模4连接的铸机5,具体的结构如下:所述结晶器3包括结晶器外壳32,所述结晶器外壳32顶部套设有热顶31,所述热顶31外侧包裹有由不锈钢薄板制备的屏蔽罩311。电磁铸造中,感应器33产生的交流磁场同液体金属中的感生电流相互作用产生空间分布的电磁压力。由于电磁压力分布并不能很好地匹配液体金属的静压力分布,因此需要引入屏蔽罩311改善磁场和电磁压力分布。屏蔽罩311在交流磁场作用下产生与感应器电流反向的涡流,涡流同交变磁场相互作用,部分抵消了交变磁场,从而削弱了液柱的顶部磁场,抑制了电磁搅拌引起的熔体流动,形成比较稳定的金属液柱。本发明在屏蔽罩311内用耐火材料制成热顶31,约束金属液柱顶部熔体成型,即将热顶31与屏蔽罩311的功能合二为一。所述结晶器外壳32窄边内侧设置有一对活动铜板321,所述活动铜板321靠近结晶器外壳32侧连接有贯穿结晶器外壳32的丝杠机构322,所述丝杠机构322与伺服电机323连接。在实际生产中,有时一个浇次内有多个型号的订单,如果每个订单都停机更换结晶器3显然是不经济的。为了提高铸机的作业率,本发明采用结晶器调宽技术来解决这一问题。结晶器3采用伺服电机的电动调宽形式。电动调宽结构简单可靠,没有复杂的液压管路和部件,蜗轮蜗杆结构带有自锁特性,可以防止浇铸过程中结晶器3的活动铜板321的误动作。而结晶器3的两个窄边各有上下两套丝杠机构322,伺服电机323的旋转通过蜗轮蜗杆机构传递为丝杠的平移运动,带动结晶器3的活动铜板321移动,这样结晶器的宽度和锥度就能够进行调节。所述结晶器外壳32两个宽边外侧分别设置有感应器33,所述感应器33下方靠近结晶器外壳32底部开口处设置有第一水冷机构35。所述结晶器外壳32底部设置有超声波发生器34,所述超声波发生器34是由波导座341和设置在波导座341下方的换能器342组成。合金液在冷凝过程中很容易和结晶器3的活动铜板321发生粘结,一旦发生这种情况,会使拉矫阻力大大增加,并且铸坯的坯壳会被撕裂,发生漏液事故。倘若在浇铸过程中给结晶器3施加一定的规律振动,合金液和结晶器3内表面的润滑条件变好,摩擦力减小,即可防止粘结的发生,还可以使板坯表面质量提高。如图3所示,本发明还设置有用以冷却铸锭8的第二水冷机构7,所述第二水冷机构7是由沿直线等间距排列的竖直喷嘴71,以及分别设置在竖直喷嘴71两侧的第一斜向喷嘴72和第二斜向喷嘴73组成。所述第一斜向喷嘴72和第二斜向喷嘴73位于竖直喷嘴71的间隔处,且二者间相互间隔。所述第一斜向喷嘴72和第二斜向喷嘴73的喷嘴斜向方向处于同一平面内,且朝向方向相对。第一水冷机构35喷水孔直径为2.5mm,竖直喷嘴71的冷却水喷射角(垂直射流75与铸锭表面之间的夹角)为90°;第一斜向喷嘴72和第二斜向喷嘴73的的喷水孔直径为2mm,且斜向射流76的喷射角均为60°。冷却水套采用厚6mm的环氧树脂板粘结组成,强度高、耐高温、不易变形,而且便于加工和改造。喷水孔的出口处与铸锭表面的水平间距为15mm。水冷却系统来提高电磁铸造过程的冷却效果。使用单排喷水冷却时,沿铸锭8表面流动的水在两相邻的射流间相互冲击,会产生干涉喷泉74。干涉喷泉74使大量冷却水尚未吸收任何热量便离开了铸锭8表面,因此冷却水溅射比较严重。如图4所示,垂直喷嘴71沿铸锭8表面喷出垂直射流75,垂直射流75朝相邻水流水平流动的冷却水在两相邻水流的中间相遇,形成干涉喷泉74,在冷却水尚未离开铸锭8表面之前,由第一斜向喷嘴72和第二斜向喷嘴73射出的斜向射流76冲击在干涉喷泉74上,使之又回到铸锭8表面,且溅射水滴会相互碰撞融合,增大落回铸锭8表面的概率。因此,采用本发明设计的三排水冷器不仅可以提高冷却水流量,还能够改善冷却水的冷却效果,使耗水量下降,允许采用更高的水温而不产生表面缺陷、裂纹、合金液泄漏或铸锭8翘曲现象。实施例二实施例二是以实施例一中的结构为基础进行叙述的,主要是对本发明的制备方法进行阐述,具体内容如下:s1、配料依照铜锰合金的组成配比,准备纯度99.9%的电解铜板、cumn90中间合金、mnni40中间合金、cusi16中间合金。s2、装炉依次向真空感应熔炼炉1的坩埚内装入电解铜板、mnni40中间合金,以及rj-2型覆盖剂。s3、熔炼在惰性气氛保护下,首先将坩埚温度升至1100℃,待电解铜板以及mnni40中间合金开始溶化时加入cumn90中间合金,随后补加cumn90中间合金和mnni40中间合金直至mn含量达到12.50%,ni含量达到2.10%。s4、精炼除气将坩埚温度缓慢升至1150℃,进行氩气除气和合金脱氧,出炉前加入cusi16中间合金并调整至si含量达到0.30%。s5、浇注s5-1、首先启动铸机5,将底模4的顶面升至感应器33磁场强度最大位置处;接着启动冷却水系统;随后调整处于结晶器3窄边的活动铜板321的宽度以及锥度,调节感应器33的电流强度为400a、频率为3hz,超声波发生器34的纵振频率为20000hz,输出振幅为16μm;最后将流槽2预热至1200℃、热顶31预热至350℃。s5-2、使用色素炭黑覆盖结晶器3,密封结晶器3底部第一水冷机构35。s5-3、将步骤s4中精炼后的合金液经流槽2引入结晶器3内进行浇注,合金液倒入流槽2后及时打开燃气保护溜槽及结晶器3入口,保证溜槽2内液面平稳,不断流、不溢出。s6、铸造当浇注合金液流至底模4,形成的半悬浮合金液柱体积占结晶器3容积的70%时,使用第一水冷机构35进行冷却,同时进行下引铸造,铸造速度缓慢由初始速度逐渐过渡到稳态速度50cm/min。s7、冷却s7-1、当铸造过程进入稳态阶段后,控制流槽2中合金液液位,保持静压头和液位恒定,以及结晶器3内合金液液面距结晶器3顶部3mm;在此阶段,对结晶器3水冷的同时,对牵引出的铸锭8使用第二水冷机构7进行二次水冷,水雾大小须保证铸锭8从白亮将至暗红,不可直接冷至室温。s7-2、当坩埚内的合金液量降至坩埚容积的20%时,调小下引速度直至停止;待铸锭8完全凝固后,关闭冷却水系统。实施例三实施例三是不同于实施例一的另一种参数设定的制备方法,具体内容如下:s1、配料依照铜锰合金的组成配比,准备纯度99.9%的电解铜板、cumn90中间合金、mnni40中间合金、cusi16中间合金。s2、装炉依次向真空感应熔炼炉1的坩埚内装入电解铜板、mnni40中间合金,以及rj-2型覆盖剂。s3、熔炼在惰性气氛保护下,首先将坩埚温度升至1100℃,待电解铜板以及mnni40中间合金开始溶化时加入cumn90中间合金,随后补加cumn90中间合金和mnni40中间合金直至mn含量达到12.50%,ni含量达到2.00%。s4、精炼除气将坩埚温度缓慢升至1150℃,进行氩气除气和合金脱氧,出炉前加入cusi16中间合金并调整至si含量达到0.30%。s5、浇注s5-1、首先启动铸机5,将底模4的顶面升至感应器33磁场强度最大位置处;接着启动冷却水系统;随后调整处于结晶器3窄边的活动铜板321的宽度以及锥度,调节感应器33的电流强度为500a、频率为3hz,超声波发生器34的纵振频率为20100hz,输出振幅为18μm;最后将流槽2预热至1230℃、热顶31预热至375℃。s5-2、使用色素炭黑覆盖结晶器3,密封结晶器3底部第一水冷机构35。s5-3、将步骤s4中精炼后的合金液经流槽2引入结晶器3内进行浇注,合金液倒入流槽2后及时打开燃气保护溜槽及结晶器3入口,保证溜槽2内液面平稳,不断流、不溢出。s6、铸造当浇注合金液流至底模4,形成的半悬浮合金液柱体积占结晶器3容积的80%时,使用第一水冷机构35进行冷却,同时进行下引铸造,铸造速度缓慢由初始速度逐渐过渡到稳态速度70cm/min。s7、冷却s7-1、当铸造过程进入稳态阶段后,控制流槽2中合金液液位,保持静压头和液位恒定,以及结晶器3内合金液液面距结晶器3顶部4mm;在此阶段,对结晶器3水冷的同时,对牵引出的铸锭8使用第二水冷机构7进行二次水冷,水雾大小须保证铸锭8从白亮将至暗红,不可直接冷至室温。。s7-2、当坩埚内的合金液量降至坩埚容积的20%时,调小下引速度直至停止;待铸锭8完全凝固后,关闭冷却水系统。实施例四实施例四是不同于实施例一的另一种参数设定的制备方法,具体内容如下:s1、配料依照铜锰合金的组成配比,准备纯度99.9%的电解铜板、cumn90中间合金、mnni40中间合金、cusi16中间合金。s2、装炉依次向真空感应熔炼炉1的坩埚内装入电解铜板、mnni40中间合金,以及rj-2型覆盖剂。s3、熔炼在惰性气氛保护下,首先将坩埚温度升至1100℃,待电解铜板以及mnni40中间合金开始溶化时加入cumn90中间合金,随后补加cumn90中间合金和mnni40中间合金直至mn含量达到25.50%,ni含量达到10.10%。s4、精炼除气将坩埚温度缓慢升至1150℃,进行氩气除气和合金脱氧,出炉前加入cusi16中间合金并调整至si含量达到0.20%。s5、浇注s5-1、首先启动铸机5,将底模4的顶面升至感应器33磁场强度最大位置处;接着启动冷却水系统;随后调整处于结晶器3窄边的活动铜板321的宽度以及锥度,调节感应器33的电流强度为600a、频率为3hz,超声波发生器34的纵振频率为20200hz,输出振幅为20μm;最后将流槽2预热至1250℃、热顶31预热至400℃。s5-2、使用色素炭黑覆盖结晶器3,密封结晶器3底部第一水冷机构35。s5-3、将步骤s4中精炼后的合金液经流槽2引入结晶器3内进行浇注,合金液倒入流槽2后及时打开燃气保护溜槽及结晶器3入口,保证溜槽2内液面平稳,不断流、不溢出。。s6、铸造当浇注合金液流至底模4,形成的半悬浮合金液柱体积占结晶器3容积的85%时,使用第一水冷机构35进行冷却,同时进行下引铸造,铸造速度缓慢由初始速度逐渐过渡到稳态速度80cm/min。s7、冷却s7-1、当铸造过程进入稳态阶段后,控制流槽2中合金液液位,保持静压头和液位恒定,以及结晶器3内合金液液面距结晶器3顶部5mm;在此阶段,对结晶器3水冷的同时,对牵引出的铸锭8使用第二水冷机构7进行二次水冷,水雾大小须保证铸锭8从白亮将至暗红,不可直接冷至室温。s7-2、当坩埚内的合金液量降至坩埚容积的20%时,调小下引速度直至停止;待铸锭8完全凝固后,关闭冷却水系统。实施例五实施例五是不同于实施例一的另一种参数设定的制备方法,具体内容如下:s1、配料依照铜锰合金的组成配比,准备纯度99.9%的电解铜板、cumn90中间合金、mnni40中间合金、cusi16中间合金。s2、装炉依次向真空感应熔炼炉1的坩埚内装入电解铜板、mnni40中间合金,以及rj-2型覆盖剂。s3、熔炼在惰性气氛保护下,首先将坩埚温度升至1100℃,待电解铜板以及mnni40中间合金开始溶化时加入cumn90中间合金,随后补加cumn90中间合金和mnni40中间合金直至mn含量达到25.50%,ni含量达到10.00%。s4、精炼除气将坩埚温度缓慢升至1150℃,进行氩气除气和合金脱氧,出炉前加入cusi16中间合金并调整至si含量达到0.20%。s5、浇注s5-1、首先启动铸机5,将底模4的顶面升至感应器33磁场强度最大位置处;接着启动冷却水系统;随后调整处于结晶器3窄边的活动铜板321的宽度以及锥度,调节感应器33的电流强度为600a、频率为3hz,超声波发生器34的纵振频率为20200hz,输出振幅为20μm;最后将流槽2预热至1250℃、热顶31预热至400℃。s5-2、使用色素炭黑覆盖结晶器3,密封结晶器3底部第一水冷机构35。s5-3、将步骤s4中精炼后的合金液经流槽2引入结晶器3内进行浇注,合金液倒入流槽2后及时打开燃气保护溜槽及结晶器3入口,保证溜槽2内液面平稳,不断流、不溢出。。s6、铸造当浇注合金液流至底模4,形成的半悬浮合金液柱体积占结晶器3容积的85%时,使用第一水冷机构35进行冷却,同时进行下引铸造,铸造速度缓慢由初始速度逐渐过渡到稳态速度80cm/min。s7、冷却s7-1、当铸造过程进入稳态阶段后,控制流槽2中合金液液位,保持静压头和液位恒定,以及结晶器3内合金液液面距结晶器3顶部5mm;在此阶段,对结晶器3水冷的同时,对牵引出的铸锭8使用第二水冷机构7进行二次水冷,水雾大小须保证铸锭8从白亮将至暗红,不可直接冷至室温。s7-2、当坩埚内的合金液量降至坩埚容积的20%时,调小下引速度直至停止;待铸锭8完全凝固后,关闭冷却水系统。实验例本实验例是以上述实施例中所描述的制备方法为基础进行设计的,主要是对不同方法制备的铸锭成品进行比较。本发明实施二至实施五的配料比例见表1,生产的铜锰合金扁锭成分见表2。表1实施二到实施五铜锰合金的配料比例配料比例(wt%)cumnnisi实施二85.1012.502.100.30实施三85.2012.502.000.30实施四64.2025.5010.100.20实施五64.3025.5010.000.20表2实施二到实施五铸锭成分铸锭成分(%)cumnnisio杂质实施二85.1012.192.180.2160.00070.038实施三85.2012.222.060.1880.00080.041实施四64.2025.1210.160.0960.00080.064实施五64.3025.1810.050.0840.00050.066结合表2、图6、图7可以看出,本发明制备的铸锭8化学成分均匀一致,杂质含量≤0.1wt%;且表面光洁,无积瘤、夹杂(渣)、冷隔、结疤、裂纹、裂边等缺陷,铸锭8内部组织致密,无气孔、夹杂、疏松、缩孔、偏析、内裂纹等缺陷。当前第1页12