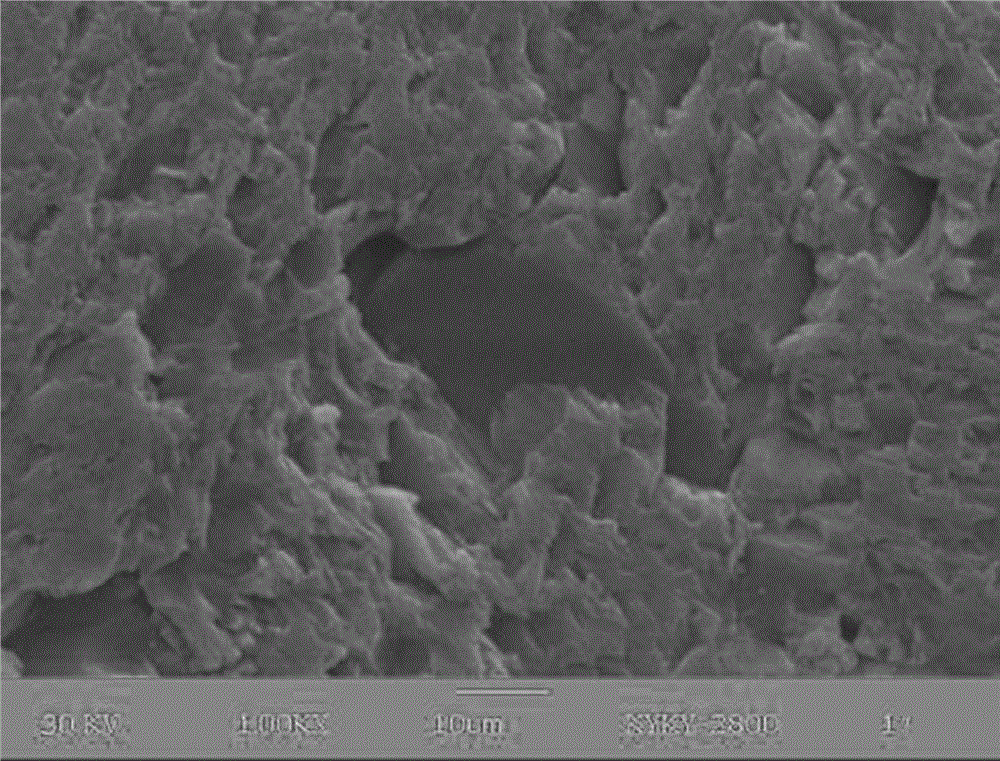
本发明属于冶金、有色、玻璃、水泥窑用高级耐火材料及其制备
技术领域:
,具体涉及一种微波干燥制备不烧改性高纯镁铝尖晶石复合砖的方法。
背景技术:
:《中国制造2025》重点目标:高效率、低成本洁净钢生产技术,先进钢铁成分组织设计,钢铁材料夹杂状态控制,炉外精炼过程模拟优化,炉外精炼装备设计优化,耐火材料制造配置优化,先进制造零部件用钢,高性能海工钢,新型钢强韧汽车钢,高速、重载轨道交通用钢,特种装备用超高强度不锈钢等。目前,申请公布号为CN106278324A的发明专利中公布了一种改性高纯镁铝尖晶石复合砖及其制备方法,虽然其在原料上选用国产高纯镁砂替代国外进口的海水镁砂节约了成本,高温热震稳定性好,取代钢包用镁碳和镁铬砖,实现无碳无铬排放,无污染,洁净钢水,改善了耐火材料制造中生产性能较好的原材料价格昂贵的问题并且性能优越,但是在其制备的过程中需要将成型的复合砖坯放入干燥窑进行干燥,干燥温度为90℃-150℃,干燥时间12-16小时;再将干燥后的复合砖坯送入1700℃-1800℃的窑中烧制7-8h进行烧结,因此需要大量能源提供热能,成本高并且生产周期长,生产效率低下。提供热能的常规方法有燃油燃烧提供热能、天然气燃烧提供热能、电能转化热能等,其中燃油燃烧虽然价格便宜、但是排放的污染气体危害较大;天然气燃烧虽然较为环保,但是价格昂贵,每吨砖烧成所需要的天然气的成本约为600-800元,同时天然气虽然是无色无味的,但是为了助于泄漏检测会在送到最终用户之前用硫醇来给天然气添加气味,硫醇也会产生一定的硫化物,并且在烧成过程中天然气的燃烧仍然产生一定量的温室气体CO2,对地球整体的温室效应会有影响,虽然天然气比空气轻而容易发散,但仍然存在致人窒息或死亡爆炸的安全隐患;电能转化热能是绿色清洁能源,但是上述专利的制备时间较长,烧结温度高,时间长,电能消耗大,综合成本也较高,同时生产效率低下。采用以上方式提供的热能是传统的环境传热给物料,由物料的外表面向内部阶梯式传热,存在物料受热不均匀,加热脱水或烧结速度慢等问题。因此,研制一种高效率、低成本洁净钢生产技术,无需高温烧成,受热均匀脱水速度快,原料成本低、性能优越、制备周期短,实现无碳无铬排放,无污染零排放的不烧改性高纯镁铝尖晶石复合砖的制备方法是非常重要的。技术实现要素:针对现有技术存在的问题,本发明的目的在于提供一种微波干燥制备不烧改性高纯镁铝尖晶石复合砖的方法。本发明微波干燥制备不烧改性高纯镁铝尖晶石复合砖的方法具有高效率、低成本洁净钢,无需高温烧成、受热均匀脱水速度快,原料成本低、性能优越、制备周期短,实现无碳无铬排放,无污染零排放等优点;运用本发明的制备方法生产的不烧改性高纯镁铝尖晶石复合砖具有纯度高、密度大、强度高、高温热震稳定性好、耐腐蚀性强且抗熔融金属和抗氧化能力强、无有害气体排放符合绿色耐材标准等优点。为解决上述技术问题,本发明采用的技术方案为。一种微波干燥制备不烧改性高纯镁铝尖晶石复合砖的方法,步骤如下:(1)按重量份数秤取高纯度镁砂(MgO≥99%)25-30份和高纯度镁铝尖晶石(MgO≥23%,Al2O3≥65%)10-30份,放入破碎机中进行破碎,破碎之后加入球磨机中进行粉碎,粉碎之后再用振动筛筛出粒度为5-150目的骨料;(2)按重量份数秤取电熔镁砂粉(MgO≥98%,粒度300-350目)20-35份、电熔镁铝尖晶石砂细粉(MgO含量23%-24%,Al2O3含量75%-76%)8-9份、电熔镁铝尖晶石砂超细粉(MgO含量23%-24%,Al2O3含量75%-76%)3-5份、脱硅氧化锆1-3份、氧化铈0.1-0.4份和活性氧化铝微粉1-3份,放入容器中混合配置成粉料;(3)混料:将配制的骨料放入泥料混炼机中,加入络合镁铝胶结剂2-5份,转速20-30r/min搅拌时间5-10分钟,在搅拌时加水1-3份至络合镁铝胶结剂形成浆料包裹在骨料表面,再加入上述步骤(2)制备的粉料继续混合搅拌,搅拌时间20-30分钟;(4)成型:称量5-10kg的混料放入压机中成型为复合砖坯,压机压力为800吨~1000吨;(5)微波干燥:将成型的复合砖坯放入微波干燥设备进行干燥,微波功率为250-500kW,干燥时间0.5-1h即得成品,所述成品的含水量为≤0.2%。本发明的一种优选方案,步骤(4)中的复合砖坯的厚度为50-100mm。进一步的,步骤(5)的微波干燥设备进行干燥分为两段式干燥,第一段为微波干燥,干燥时间为10-20min;第二段为微波和回收热风气流共同干燥,干燥时间为10-20min。进一步的,步骤(5)的微波功率为300kW。进一步的,步骤(2)中电熔镁铝尖晶石砂超细粉的粒度为2500-3000目。进一步的,步骤(2)中的粉料的粒度为300-350目。本发明的第二种优选方案,步骤(1)中的所述骨料的原料按重量份数秤取高纯度镁砂(MgO≥99%)30份、高纯度镁铝尖晶石(MgO≥23%,Al2O3≥65%)20份;步骤(2)中所述粉料的原料按重量份数秤取电熔镁砂粉(MgO≥98%,粒度300-350目)30份、电熔镁铝尖晶石砂细粉(MgO含量23%-24%,Al2O3含量75%-76%,粒度300-350目)10份、电熔镁铝尖晶石砂超细粉(MgO含量23%-24%,Al2O3含量75%-76%,粒度2500-3000目)3份、脱硅氧化锆(粒度300-350目)2份、稀土氧化物(粒度300-350目)0.1份、活性氧化铝微粉(粒度2000-3500目)2份、络合镁铝胶结剂3份和水2份。本发明的第三种优选方案,所述高纯度镁砂包括65%-75%的高纯度烧结镁砂和25%-35%的高纯度电熔镁砂;所述高纯度镁铝尖晶石包括60%-80%的高纯度烧结镁铝尖晶石和20%-40%的高纯度电熔镁铝尖晶石。本发明的第四种优选方案,所述高纯度镁砂包括72%的高纯度烧结镁砂和28%的高纯度电熔镁砂;所述高纯度镁铝尖晶石包括66%的高纯度烧结镁铝尖晶石和36%的高纯度电熔镁铝尖晶石。进一步的,所述稀土氧化物为氧化铈。本发明的有益效果。(1)生产效率高。本发明制备方法采用微波干燥设备进行干燥,采用两段控制,微波段利用微波内外同时加热的特点,快速脱除大量水分,后续的微波和回收热风气流干燥,用于干燥后期内部较低水分的快速烘干,干燥总时间在0.5-1h内就可以完成,成品的含水量为≤0.2%,克服了目前制备耐火砖的干燥时间长(一般需要10-20h,如对比例1-6所示)的问题,提高了生产效率。(2)克服微波缺点。微波干燥普遍存在边角效应,在食品领域尤为明显,但是由于本发明制备的不烧改性高纯镁铝尖晶石复合砖属于耐火材料领域,并且本身的高温热震稳定性好,将微波应用到本发明的配方中基本不会出现边角效应;本发明的砖坯厚度根据微波的穿透力设计为50-100mm,可以保证微波能够完全穿透砖坯,实现微波使砖坯内外同时均匀受热快速脱水的效果;本发明制备方法的微波干燥设计为两段控制,并且微波功率控制在250-500kw,在后段时砖坯的自由水已几乎蒸发,主要是对砖坯的一些结合水进行脱水,在后段采用微波配合热风不但节能,而且更好的避免了当砖坯在后段吸收微波时,出现温度高的地方,吸收微波更多,升温更快的现象,避免砖坯出现局部温度过高的情况。(3)性能优越。本发明制备方法制备的不烧改性高纯镁铝尖晶石复合砖采用镁含量99%的高纯度镁砂作为原料,首例采用络合镁铝胶结剂与稀土氧化物改性镁铝尖晶石复合砖,创造出镁铝尖晶石砖颜色为白色,由表4和表5对比可知本发明的性能远高于国外镁铝尖晶石砖性能标准;与申请公布号为CN106278324A的发明专利中的改性高纯镁铝尖晶石复合砖对比,再通过图1至图8和表2至表3所知,本发明具有与其相等的性能水平,具有纯度高,密度大,强度高、高温热震稳定性好、气孔率小,收缩率低、抗渣侵蚀性强、抗氧化能力强等优点。本发明采用的络合镁铝胶结剂是纳米技术制作的粉体,其主要成分是MgO和Al2O3,加水后形成的溶胶具有很好的胶结性,使泥料有着很好的可塑性,易于成型,用作本发明结合剂时,不会引入杂质成分,在常温下水化后具有胶结作用,干燥后,形成穿插式的结构镶嵌在颗粒与细粉之间,使本发明具有理想的结合强度,较好的荷重软化温度,热震稳定性、耐侵蚀性;同时,在高温下,这种络合镁胶结剂粉体还能起到促烧的作用,因此,该胶结剂在常高温下皆具有很好的强度,并且在使用过程中具有边运用边烧结的特点。其常温、中温、高温强度可达68-100MPa(对比例1-6所示)。(4)无需高温烧结,干燥步骤降低成本。本发明的制备方法在电加热干燥装置200℃以内烘烤进行对复合砖的干燥即得性能优越的成品,与申请公布号为CN106278324A的发明专利中的改性高纯镁铝尖晶石复合砖的制备方法的高温烧结相比,本发明的制备过程中的干燥利用微波,时间短,耗能低,成本降低(天燃气砖烧成成本600元/吨左右,免烧烘烤成本50-100元/吨。)每年中国的精炼钢钢包用无碳砖的产出大约为10万吨,可以节约大约几千万成本,为社会节约巨大的经济成本,同时创造出巨大的经济效益,影响巨大。(5)无污染零排放。本发明在冶金、玻璃及水泥窑应用中无有害气体排放,经国际耐火材料检测中心和国家建筑材料质量监督检验中心检测达到绿色耐材标准,解决了碳及铬污染的环保难题;络合镁铝胶结剂是采用先进科技,利用纳米技术在高温高压下络合而制成的新材料,其主要成分是MgO和Al2O3,无毒无味,节能环保;在制备过程中不采用天然气提供热能高温烧结,采用电能低温烘烤技术在200℃进行制备,克服了天然气的价格贵和天然气燃烧后的产生的CO2等一系列问题。(4)无安全隐患。本发明与传统镁铬砖相比,配料中不加入含碳和铬的原料,不污染环境,工人工作条件大为改善;并且不存在天然气会引发的任何安全隐患问题。附图说明图1为高纯度烧结镁砂(型号:MS99,MgO含量99.0%)抛光的标尺为100μm的扫描电镜图。图2为高纯度烧结镁砂(型号:MS99,MgO含量99.0%)抛光的标尺为10μm的扫描电镜图。图3为实施例1制备的不烧改性高纯镁铝尖晶石复合砖抛光的标尺为300μm的扫描电镜图。图4为对比例1制备的不烧改性高纯镁铝尖晶石复合砖抛光的标尺为100μm的扫描电镜图。图5为实施例2制备的不烧改性高纯镁铝尖晶石复合砖抛光的标尺为300μm的扫描电镜图。图6为对比例2制备的不烧改性高纯镁铝尖晶石复合砖抛光的标尺为100μm的扫描电镜图。图7为实施例1制备的不烧改性高纯镁铝尖晶石复合砖抛光的XRD图谱。图8为实施例2制备的不烧改性高纯镁铝尖晶石复合砖抛光的XRD图谱。具体实施方式为了进一步理解本发明,下面结合实施例对本发明优选实施方案进行描述,但是应当理解,这些描述只是为进一步说明本发明的特征和优点,而不是对本发明权利要求的限制。实施例1。分别按以下表1中指定的各组分秤取原料,制备方法如下。(1)按重量份数秤取高纯度镁砂和高纯度镁铝尖晶石,放入破碎机中进行破碎,破碎之后加入球磨机中进行粉碎,粉碎之后再用振动筛筛出粒度为5-150目的骨料。(2)按重量份数秤取电熔镁砂粉、电熔镁铝尖晶石砂细粉、电熔镁铝尖晶石砂超细粉、脱硅氧化锆、氧化铈和活性氧化铝微粉,放入容器中混合配置成粉料。(3)混料:将配制的骨料放入泥料混炼机中,加入络合镁铝胶结剂,转速20-30r/min搅拌时间5-10分钟,在搅拌时加水至结合剂形成浆料包裹在骨料表面,再加入上述步骤(2)制备的粉料继续混合搅拌,搅拌时间20-30分钟。(4)成型:称量5-10kg的混料放入压机中成型为复合砖坯,复合砖坯的厚度为50-100mm,压机压力为800吨~1000吨;(5)微波干燥:将成型的复合砖坯放入微波干燥设备进行干燥,微波功率为250-500kW,微波干燥设备进行干燥分为两段式干燥,第一段为微波干燥,干燥时间为10-20min;第二段为微波和回收热风气流共同干燥,干燥时间为10-20min,即得成品,所述成品的含水量为≤0.2%。本发明实施例1的制备成品对其进行物理力学性能指标检验。在表4中列出了测试结果。实施例2。按以下表1中指定的各组分含量重复实施例1的方法,在表4中列出了测试结果。实施例3。按以下表1中指定的各组分含量重复实施例1的方法,在表4中列出了测试结果。对比例1。按以下表1中指定的实施例1的各组分秤取原料,制备方法如下:(1)按重量份数秤取高纯度镁砂和高纯度镁铝尖晶石,放入破碎机中进行破碎,破碎之后加入球磨机中进行粉碎,粉碎之后再用振动筛筛出粒度为5-150目的骨料。(2)按重量份数秤取电熔镁砂粉、电熔镁铝尖晶石砂细粉、电熔镁铝尖晶石砂超细粉、脱硅氧化锆、氧化铈和活性氧化铝微粉,放入容器中混合配置成粉料。(3)混料:将配制的骨料放入泥料混炼机中,加入络合镁铝胶结剂,转速20-30r/min搅拌时间5-10分钟,在搅拌时加水至结合剂形成浆料包裹在骨料表面,再加入上述步骤(2)制备的粉料继续混合搅拌,搅拌时间20-30分钟。(4)成型:称量一定量的混料放入压机中成型,压机压力为700吨~1000吨。(5)干燥:将成型的复合砖坯放入电加热干燥装置进行干燥,干燥温度为90℃-150℃,干燥时间11-13小时,干燥温度升至200℃,继续干燥12-16小时,即得成品,所述成品的含水量为≤0.2%。在表4中列出了测试结果。对比例2。按以下表1中指定的实施例2的各组分秤取原料,重复对比例1的制备步骤(1)~(5),在表4中列出了测试结果。对比例3。按以下表1中指定的实施例3的各组分秤取原料,重复对比例1的制备步骤(1)~(5),在表4中列出了测试结果。对比例4。按以下表1中指定的实施例1的各组分秤取原料,重复对比例1的制备步骤(1)~(5),唯一不同的是在制备方法步骤5中的第二段干燥温度升至1000℃,取样测试,再继续升温至1750℃,取样测试,在表4中列出了测试结果。对比例5。按以下表1中指定的实施例2的各组分秤取原料,重复对比例1的制备步骤(1)~(5),唯一不同的是在制备方法步骤5中的第二段干燥温度升至1000℃,取样测试,再继续升温至1750℃,取样测试,在表4中列出了测试结果。对比例6。按以下表1中指定的实施例3的各组分秤取原料,重复对比例1的制备步骤(1)~(5),唯一不同的是在制备方法步骤5中的第二段干燥温度升至1000℃,取样测试,再继续升温至1750℃,取样测试,在表4中列出了测试结果。表1本发明实施例1-3的原料配比表。一、性能检测。1.对本发明的实施例随机选取进行电镜扫描、XRD检测,结果如图3至8、表2和表3所示。本发明随机选取实施例1制备的不烧改性高纯镁铝尖晶石复合砖进行抛光电镜扫描,如图3所示,实施例1制备的不烧改性高纯镁铝尖晶石复合砖抛光的扫描电镜图结果显示:标尺为300μm的扫描电镜图中均匀分部形成微裂纹有益于该产品的热震性提高,均匀分部骨料与细粉基质结合充分,对比例1制备的不烧改性高纯镁铝尖晶石复合砖抛光的扫描电镜图4结果显示:标尺为100μm的扫描电镜图中均匀分部骨料与细粉基质部分形成陶瓷烧结性能充分,说明本发明制备方法制备的不烧改性高纯镁铝尖晶石复合砖在高效率的同时保证了成品具有优良的热震稳定性。本发明随机选取实施例2制备的不烧改性高纯镁铝尖晶石复合砖进行抛光电镜扫描,如图5所示,实施例2制备的不烧改性高纯镁铝尖晶石复合砖抛光的扫描电镜图结果显示:标尺为300μm的扫描电镜图中均匀分部形成微裂纹有益于该产品的热震性提高,均匀分部骨料与细粉基质结合充分,对比例2制备的不烧改性高纯镁铝尖晶石复合砖抛光的扫描电镜图6结果显示:标尺为100μm的扫描电镜图中均匀分部骨料与细粉基质部分形成陶瓷烧结性能充分,说明本发明制备方法制备的不烧改性高纯镁铝尖晶石复合砖在高效率的同时保证了成品具有优良的热震稳定性。本发明随机选取实施例1和实施例2制备的不烧改性高纯镁铝尖晶石复合砖进行XRD检测,如图7和图8所示,对应的元素及含量如表2和表3所示,实施例1制备方法制备的不烧改性高纯镁铝尖晶石复合砖的XRD图谱结果显示:主要含有Mg元素(重量百分比为15.90%)、Al元素(重量百分比为28.90%)和O元素(重量百分比为55.20)的峰值,说明实施例1制备方法制备的不烧改性高纯镁铝尖晶石复合砖的MgO和Al2O3的含量高,几乎无杂质;实施例2制备方法制备的不烧改性高纯镁铝尖晶石复合砖抛光的XRD图谱结果显示:主要含有Mg元素(重量百分比为15.39%)、Al元素(重量百分比为27%)和O元素(重量百分比为44.14)的峰值,说明实施例1制备方法制备的不烧改性高纯镁铝尖晶石复合砖的MgO和Al2O3的含量高,纯度高,因此本发明制备方法制备的不烧改性高纯镁铝尖晶石复合砖具有纯度高的优点。表2为实施例1的不烧改性高纯镁铝尖晶石复合砖的XRD图谱对应的元素表。元素重量原子百分比百分比OK55.2066.65MgK15.9012.60AlK28.9020.75总量100.00表3为实施例2的不烧改性高纯镁铝尖晶石复合砖的XRD图谱对应的元素表。元素重量原子百分比百分比CK13.5020.40OK44.1049.98MgK15.3911.48AlK27.0018.14总量100.002.对实施例1-3制备的复合砖进行性能检测,结果如表4。表4不烧改性高纯镁铝尖晶石复合砖理化指标。3.国外烧成镁铝尖晶石性能见表5。表5国外烧成镁铝尖晶石砖性能。由表4和表5可知,本发明制备的不烧改性高纯镁铝尖晶石复合砖的体积密度>3.1g/cm3,气孔率<15%,国外镁铝尖晶石砖性能标准中体积密度在2.79g/cm3-3.0g/cm3之间,气孔率在15%-20%之间,由此可见,本发明制备方法制备的成品体积密度大于国外镁铝尖晶石砖性能标准中体积密度,气孔率小于国外镁铝尖晶石砖性能标准中气孔率,说明本发明制备方法制备的成品耐腐蚀性强且抗熔融金属和抗氧化能力强;本发明的200℃烘烤耐压强度为90Mpa以上,抗折强度为不低于12Mpa,国外镁铝尖晶石砖性能标准中高温烧后耐压强度在40Mpa-71Mpa之间,由此可见,本发明制备方法制备的成品的耐压强度70-90Mpa大于国外镁铝尖晶石砖性能标准中耐压强度;本发明制备方法制备的成品的热震稳定性在1100℃下冷水次数不低于20次会出现裂纹,国外镁铝尖晶石砖性能标准中水冷次数在10-15之间,由此可见,本发明制备方法制备的成品的抵抗高温应力的性能高,高温热震稳定性好;并且本发明的制备过程中无铬碳的添加,无有害气体排放符合绿色耐材标准。由表4可知,本发明微波脱水制备出的不烧改性高纯镁铝尖晶石复合砖的常温耐压强度为94-97Mpa,这是由于水化结合作用使本发明具有较高的常温耐压强度,对比例1-3在200℃传统烘烤的常温耐压强度为90-98,说明本发明制备方法不但大量的节约了干燥时间,提高效率同时具有较高的常温耐压强度;本发明制备方法制备的成品在1000℃是纳米陶瓷过渡烧结的作用使不烧改性高纯镁铝尖晶石复合砖的常温耐压强度为69-74Mpa;本发明制备方法制备的成品在1750℃是高温陶瓷烧结的作用使不烧改性高纯镁铝尖晶石复合砖的常温耐压强度为96-98Mpa,因此,本发明制备方法制备的成品在使用过程中具有边运用边烧结的特点。其常温、中温、高温强度可达69-100MPa(对比例1-6所示)。可以理解的是,以上关于本发明的具体描述,仅用于说明本发明而并非受限于本发明实施例所描述的技术方案,本领域的普通技术人员应当理解,仍然可以对本发明进行修改或等同替换,以达到相同的技术效果;只要满足使用需要,都在本发明的保护范围之内。当前第1页1 2 3