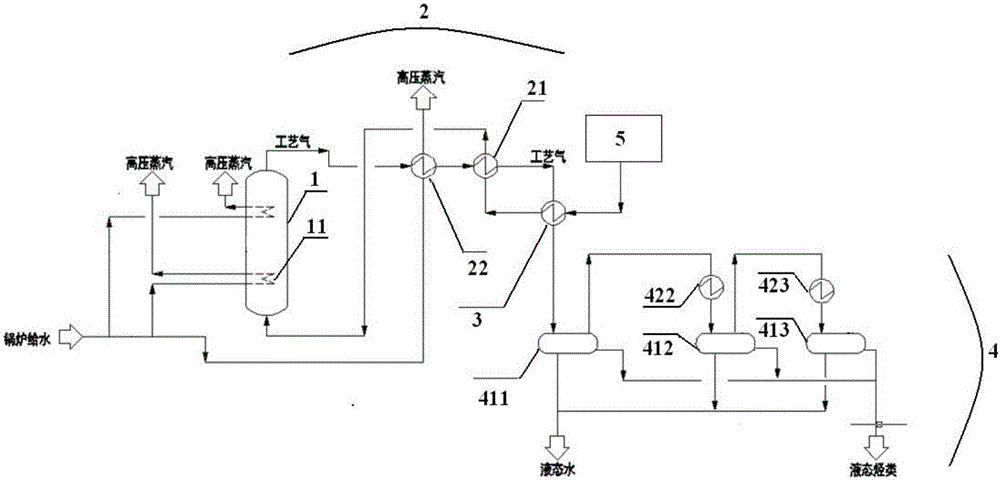
本实用新型涉及甲醇制烃领域,具体地,涉及一种甲醇制烃的系统。
背景技术:
:甲醇制烃类最早的报告出现在1880年,由LeBel、Greene提出,甲醇在熔融氯化锌中分解,得到六甲苯、轻质气体(主要为甲烷)和水。后人们尝试多种催化剂,包括硅胶、氧化铝、二氧化硅等。沸石是四面体多孔硅铝酸盐晶体,其独特的晶体结构可提供“择形催化”的功能,只允许特定尺寸的分子通过。沸石ZSM-5和ZSM-11,特别是ZSM-5在甲醇制烃上得到了广泛的研究,被公认为是这种反应的最有效催化剂。甲醇在ZSM-5上的转化,目前大部分研究人员认可的反应路径为:甲醇制烃类的反应,从反应原料与反应产物的焓值之差就可看出,该反应为强放热反应,以25℃甲醇计的反应放热达到1500-1800kJ/kg。如此强烈的放热可使反应物系温度迅速升高600℃以上。因此如何控制或移除如此多的反应热成为甲醇制烃反应器的关键。现有技术的反应器,不管是采用固定床,流化床,还是移动床,都是采用以下手段控制反应器温度:①向原料甲醇中加一定比例的水,利用水较大的热容吸收反应热;②部分原料液态甲醇不经过气化升温,直接喷入反应器,利用甲醇的气化吸收反应热;③大量气体在系统内循环,利用循环气体的热容缓和反应器温度的上升;④大量循环气体循环,其中部分轻质气体不经过预热就返回反应器,名曰冷激气,利用冷激气的较大的升温空间缓和反应器温度的上升。然而以上种种手段都有明显缺点:手段①:向系统中加入的水作为惰性组分,跟甲醇一样经历了整个气化-预热-吸热-降温-冷凝-气液液分离过程,增加了整套设备的运转负荷,或者说,降低了装置产能;由于反应也产生水分,随原料甲醇进入的水分抑制了反应向正方向进行,降低反应收率。手段②:不管对于固定床还是流化床,用甲醇气进料很容易布满整个空间或界面,反应均匀进行;甲醇液滴则不可均匀地与所有催化剂接触,而且液态密度大,会形成一个个反应剧烈的“热点”,局部温度急剧升高,反应产物分解碳化,催化剂迅速失活。手段③:不应忘记的是,甲醇制烃的反应条件有如下限制:反应初始温度不能过低,否则反应不易启活;反应终了温度不能过高,否则会出现副反应,还会损坏催化剂。所以循环气体必须预热后进入反应器,以满足反应初始要求。而循环气体的热容较小,为了吸收反应热,控制反应终了温度,需要很大的气量。由于该气体分子量小,密度小,在整个系统内循环,大大增加了全系统的体积流量。整套装置所有管道设备尺寸明显增大,投资增加。手段④:部分循环气体不经过预热,直接以冷激气的方式进入反应器降温,是手段③的改进版,可以使循环气量有所减少。但不管是固定床还是流化床,在反应中途额外引入大量气体,在有限的时间空间内,冷气和热工艺气难以混合均匀,必然扰乱原有的轴向或径向温度和组成分布,严重影响了后续反应的正常进行。例如,专利申请CN104818042A,涉及一种移动床甲醇制烃方法,包括烃合成、分离和后处理步骤,所述烃合成步骤中采用至少两个相互串联的反应器,反应原料与催化剂逆次序方向流过各反应器,分离步骤产生的含低碳烃的循环气返回烃合成步骤的不同进料位置,作为烃合成步骤的冷激气或原料补充气,利用原料甲醇对分离步骤产生的C1-C4轻组分进行洗涤吸收,并返回进料进行转化,从而将甲醇转化为高附加值的含有混合芳烃的稳定轻烃。由以上公开专利申请可知,其始端反应器温度370-550℃,末端反应器温度320-520℃,甲醇预热至250-480℃,循环气预热至320-480℃。也就是说,反应器进口物料温度与出口温度相差不大。因此,必然需要非常大的循环气倍率(5-10:1)来缓和反应放热温升。如此大的气量循环造成循环气压缩机能耗很高,而且全系统的气相管道直径明显增大,投资很高。技术实现要素:本实用新型的目的是为了克服现有技术中控制或移除反应热时对装置或对催化剂活性(导致烃收率降低)的影响,或者是对装置要求较高或是能耗大的缺陷,提供一种能够将甲醇制烃反应过程中生成的热量得到充分利用且不显著增加额外消耗,同时提高烃收率的甲醇制烃的系统。为了实现上述目的,本实用新型提供了一种该系统包括流化床反应器、换热装置和气化器,含液态甲醇的原料在所述气化器中与来自所述换热装置的工艺气进行热交换,由所述气化器产生的气化的含甲醇原料与来自所述流化床反应器的工艺气在所述换热装置中进行热交换,由所述换热装置产生的过热的含甲醇原料进入所述流化床反应器中进行反应,并且反应产生的含烃工艺气进入所述换热装置中进行热交换;其中,所述流化床反应器中设置有至少一个移热装置,所述反应过程中产生的部分热量通过所述的移热装置移出。优选的,所述流化床反应器为多层流化床反应器或循环流化床反应器。优选的,所述多层流化床反应器的每层中均设置有至少一个移热装置。优选的,所述换热装置包括第一预热器和废热锅炉:由所述气化器产生的气化的含甲醇原料与来自所述废热锅炉的工艺气在所述第一预热器中进行热交换;由所述第一预热器产生的第一过热含甲醇原料进入所述流化床反应器中进行反应,并且反应产生的含烃工艺气进入所述废热锅炉中以将其部分热量移出。优选的,所述换热装置包括第一预热器、废热锅炉和第二预热器:由所述气化器产生的气化的含甲醇原料与来自所述废热锅炉的工艺气在所述第一预热器中进行热交换;由所述第一预热器产生的第一过热含甲醇原料与来自所述流化床反应器的工艺气在所述第二预热器中进行热交换;由所述第二预热器产生的第二过热含甲醇原料进入所述流化床反应器中进行反应,反应产生的含烃工艺气进入所述第二预热器中进行热交换,并且在第二预热器中完成热交换的含烃工艺气进入所述废热锅炉中以将其部分热量移出。优选的,所述甲醇制烃系统还包括分离装置,来自所述气化器的由工艺气至少部分冷凝后得到的气液混合物在该分离装置中进行分离处理,以分离出液态水、液态烃和任选的气相。优选的,所述甲醇制烃系统还包括分离装置、循环气供给装置和液体甲醇供给装置,由所述分离装置分离出的气相经由所述循环气供给装置供给至与来自所述液体甲醇供给装置的液体甲醇混合,并作为所述含液态甲醇的原料供给至所述气化器。本实用新型采用流化床进行甲醇制烃,整个反应器内传质均匀无死角,反应物与催化剂全面接触,催化剂使用寿命一致;传热均匀迅速,传热系数大,再配合上换热装置,可以及时移走反应热,使反应器内温度平稳可控;当采用多层流化床时,在不同层分别设置换热装置,可精确控制反应不同阶段的温度,反应条件达到最优。同时,本实用新型在完全利用反应工艺气显热(物质不相变的前提下由于温度降低所释放的热量)的同时,进一步利用反应工艺气由气态冷凝为部分液态时放出的热量(潜热)对甲醇液体进行气化,充分利用了反应工艺气蕴藏的潜热,使得热量的利用更加充分。另外,本实用新型由于不需要大量气体去控制反应器温升,因此,需要返回的气体的倍率明显小于现有技术,本实用新型返回气体相对甲醇进料量的倍率可以在零到多倍之间随意调节。综上所述,本实用新型能够有效地提高蒸汽产出,反应过程中不需要额外的蒸汽消耗,也降低了电消耗。此外,采用本实用新型还提高了催化剂的活性,从而提高了烃收率。本实用新型的其它特征和优点将在随后的具体实施方式部分予以详细说明。附图说明附图是用来提供对本实用新型的进一步理解,并且构成说明书的一部分,与下面的具体实施方式一起用于解释本实用新型,但并不构成对本实用新型的限制。在附图中:图1是本实用新型一种具体实施方式的甲醇制烃系统。图2是本实用新型另一种具体实施方式的甲醇制烃系统。附图标记说明1流化床反应器2换热装置3气化器4分离装置5循环气供给装置6液体甲醇供给装置11移热装置21第一预热器22废热锅炉23第二预热器411一级分离器412二级分离器413三级分离器422二级冷凝器423三级冷凝器具体实施方式以下对本实用新型的具体实施方式进行详细说明。应当理解的是,此处所描述的具体实施方式仅用于说明和解释本实用新型,并不用于限制本实用新型。在本文中所披露的范围的端点和任何值都不限于该精确的范围或值,这些范围或值应当理解为包含接近这些范围或值的值。对于数值范围来说,各个范围的端点值之间、各个范围的端点值和单独的点值之间,以及单独的点值之间可以彼此组合而得到一个或多个新的数值范围,这些数值范围应被视为在本文中具体公开。本实用新型的发明人在研究的过程中发现,本实用新型采用流化床进行甲醇制烃,整个反应器内传质均匀无死角,反应物与催化剂全面接触,催化剂使用寿命一致;传热均匀迅速,传热系数大,再配合上换热装置,可以及时移走反应热,使反应器内温度平稳可控;当采用多层流化床时,在不同层分别设置换热装置,可精确控制反应不同阶段的温度,反应条件达到最优。并且本实用新型采用在反应器中设置移热装置,有效地避免了现有技术中向反应器中加入水、循环气或冷激气的操作,并且也不需要将未气化的甲醇直接注入反应器以进行制烃反应,因此,有效地提高了反应器的利用率,还提高了反应效率,并且节省了成本。基于如上发现,本实用新型提供了一种甲醇制烃的方法,其中,该方法在包括流化床反应器、换热装置和气化器的甲醇制烃系统中实施,所述方法包括:(1)将含液态甲醇的原料在所述气化器中与来自所述换热装置的工艺气进行热交换,使所述含液态甲醇的原料中的甲醇气化以获得气化的含甲醇原料;(2)将所述气化的含甲醇原料与来自所述流化床反应器的工艺气在所述换热装置中进行热交换,得到过热的含甲醇原料;以及(3)将所述过热的含甲醇原料注入所述流化床反应器中进行反应,并将反应产生的含烃工艺气注入所述换热装置中进行热交换;其中,所述反应过程中产生的部分热量通过设置在所述流化床反应器中的移热装置被移出。也就是说,在甲醇制烃过程中,含甲醇的原料和反应过程中生成的含烃工艺气在相互独立的管道中进行间接接触,在接触的过程中,含烃工艺气将其蕴含的热量(显热和潜热)传递给含甲醇的原料,自身温度得到降低,含甲醇的原料的温度得到升高,从而达到符合反应的需求。有效的利用了反应过程中发生的热量。根据本实用新型,如上所述的,甲醇制烃的反应为放热反应,因此,通过在流化床反应器中设置移热装置,及时将反应过程中的热量移出反应器,以将反应维持在稳定的温度和压力下。优选的,所述反应的条件包括:温度为250-450℃,优选为300-400℃(例如,300℃、310℃、320℃、330℃、340℃、350℃、370℃、380℃、390℃、400℃以及它们之间的任意数值),压力为0.1-1.5MPa,优选为0.2-1MPa(例如,0.2MPa、0.25MPa、0.3MPa、0.4MPa、0.5MPa、0.6MPa、0.7MPa、0.8MPa、0.9MPa、1.0MPa以及它们之间的任意数值)。根据本实用新型,所述移热装置优选通过热交换的形式将反应过程中产生的部分热量移出体系外,所述热交换的形式可以为本领域公知的任意形式,例如,所述移热装置可以为换热盘管设备,具体的,通过泵将水注入到反应器的换热盘管中(例如,将设定压力(比如4.0-12.0MPa,优选4.0-8.0MPa,更优选4.0MPA)的饱和液态水用泵送入换热盘管中,反应产生的热量与换热盘管中的水进行热交换,水气化后以高压蒸汽的形式离开反应器,一方面,使反应器的温度得到了维持,另一方面还可以产生生产上可用的高压蒸汽,例如,4.0-12.0MPa,优选4.0-8.0MPa,更优选为4.0MPa的高压蒸汽。根据本实用新型,所述移热装置的个数并没有特别的限制,只要满足甲醇制烃的生产温度需求即可,例如,可以为1个,也可以为多个,例如,2-5个,本领域技术人员可以根据实际的生产进行调整。根据本实用新型,所述流化床反应器可以为多层流化床反应器或循环流化床反应器,其中,当所述反应器为多层流化床反应器时,优选在所述多层流化床反应器中的每层均设置有移热装置,如此,可以有效控制反应不同阶段的温度,使得反应条件达到最优。进一步优选的情况下,所述流化床反应器为多层循环流化床反应器。根据本实用新型,在所述流化床反应器为多层流化床反应器的情况下,沿着含甲醇原料的流向,相邻两层之间,反应温度可以存在0-30℃,优选为5-30℃的温差,本领域技术人员可以根据实际的生产进行调整。根据本实用新型,为了充分将反应生成的含烃工艺气所蕴含的显热进行吸收,所述换热装置除了包括第一预热器以及可选的第二预热器,还优选包括废热锅炉。根据本实用新型一种具体的实施方式,所述换热装置包括第一预热器和废热锅炉,所述换热装置的换热过程包括:反应所得含烃工艺气先通过废热锅炉进行第一次降温,降温后的含烃工艺气进入第一预热器,并与进入第一预热器的由所述气化器产生的气化的含甲醇原料在相互独立空间内间接接触,以进行热交换,其中,所述经废热锅炉降温后的工艺气所蕴含的显热恰好能够使得所述气化的含甲醇原料过热至预定的温度,例如,200-400℃,优选为250-300℃(例如,250、255℃、260℃、265℃、270℃、275℃、280℃、285℃、290℃、295℃、300℃以及它们之间的任意数值)。其中,在所述第一预热器中进行热交换后得到的第一过热含甲醇原料可(直接)注入所述流化床反应器中进行反应,并将反应产生的含烃工艺气先注入所述废热锅炉移出部分热量再注入第一预热器中进行热交换。根据本实用新型另一种具体的实施方式,所述换热装置包括第一预热器、废热锅炉和第二预热器,所述换热装置的换热过程包括:由所述气化器产生的所述气化的含甲醇原料依次通过第一换热器和第二换热器,流化床反应器中反应产生的含烃工艺气依次通过第二预热器、废热锅炉和第一预热器,也即,由所述气化器产生的所述气化的含甲醇原料与来自所述废热锅炉的工艺气在所述第一预热器中进行热交换;经在所述第一预热器中进行热交换后得到的第一过热含甲醇原料与来自所述流化床反应器的工艺气在所述第二预热器中进行热交换。其中,在所述第二预热器中进行热交换后得到的第二过热含甲醇原料可(直接)注入所述流化床反应器中进行反应,并将反应产生的含烃工艺气依次注入所述第二预热器进行热量换、废热锅炉移出部分热量和第一预热器进行热交换。其中,所述废热锅炉对含烃工艺气移出的吸收优选恰好使得含甲醇的原料经过第一预热器和第二预热器后能够过热至预定的温度,例如,200-400℃,优选为250-300℃(例如,250、255℃、260℃、265℃、270℃、275℃、280℃、285℃、290℃、295℃、300℃以及它们之间的任意数值)。本实用新型反应器出口的工艺气,温度约250-450℃,优选为300-400℃。其中,从该温度降至冷凝点之前,放出的显热约140kcal/(kg工艺气)。经过如上的换热后,饱和气态工艺气的温度可以降低为80-180℃,优选100-180℃。根据本实用新型,流化床反应器出口的工艺气的温度高于进入流化床反应器入口的过热的含甲醇原料的温度;优选高50-150℃,优选70-130℃。根据本实用新型,当所述换热装置包括两级预热器时,优选通第一预热器后所述含烃工艺气的温度降低20-50℃,通过废热锅炉后温度再次降低30-60℃,通过第二预热器后温度降低至120-200℃。当所述换热装置包括一级预热器时,经过废热锅炉后温度降低50-120℃,通过预热器后温度再降低120-200℃。本实用新型需要说明的是,虽然如上的描述中规定了废热锅炉相对于第一预热器和第二预热器的位置,但这并不能够作为对本实用新型的限制,如上仅仅是为了描述方便而进行的设定。因此,所述废热锅炉可以置于第一预热器之前或之后,以及第二预热器之间或之后,只要能够与第一预热器和/或第二预热器配合以将所述含烃工艺气的显热全部吸收即可。其中,所述废热锅炉可用于产生4.0-12.0MPa,优选4.0-8.0MPa,更优选为4.0MPa的高压蒸汽。根据本实用新型,本实用新型的方法还包括将来自所述气化器的气液混合物进行一次或多次气液分离,分离出液态水、液态烃以及任选的气相。其中,所述气液分离器的方法可以为本领域常规的选择,例如,经一级或多级冷凝处理以及气-液-液分离,从而得到液态烃类和液态水,以及可选的气相,这些均是本领域技术人员所公知的,在此不再进行详细赘述。其中,在气-液-液平衡压力下,仍有少量物质留在气相中,以C1-C4烃类为主。可以根据需要调节冷凝温度,控制气量。该气体可以返回反应器,也可引出装置。本实用新型流化床反应器需要一定量的流化气体。可以单独拿进料甲醇气做流化气,也可用甲醇气和返回的循环气(如上所述气相)共同做流化气。根据本实用新型,反应器出口的工艺气温度一般会达到250-450℃,优选为300-400℃。需要降低到接近常温以得到液态烃类和水分;而原料甲醇需要气化和升温至接近反应温度,可能存在的循环气体(如上所述的气相)也需要从接近常温预热到接近反应温度,本领域的专业人员都会想到将冷热介质匹配,建立换热网络,以回收能量,降低系统运行费用。作为热源的工艺气降低温度,放出显热,将甲醇和/或循环气体分别预热至合适温度,本身仍为全气态(80-180℃,优选100-180℃),再用水冷器冷凝至30-60℃,以便分离产品烃类、水分和循环气体,这是现有技术的共同步骤。如专利申请CN104818042A可知,反应器出口工艺气与甲醇和循环气分别进行了换热,然后进入冷凝器,三相分离器。然而其工艺气的部分热量仅得到了回收,剩余热量全部在冷凝器处浪费。并且,在常规的甲醇进料压力(0.1-0.5MPa)下,甲醇的气化温度点高于工艺气冷凝点,使工艺气的冷凝热无法得到利用,只能用额外的冷却介质移走。然而,从物性上讲,80-180℃,优选100-180℃工艺气中水分和油品冷凝放出的潜热是非常可观的,用水冷器移走冷凝热,最终释放到大气是能量的巨大浪费。本领域技术人员要么没有意识到该潜热的巨大价值,要么不知如何利用如此低温的热源。本实用新型创造性地提出,将气液分离后的气相(循环气)与液态甲醇先混合,降低甲醇分压,即降低了甲醇气化温度,然后将工艺气与循环气-甲醇混合物进行换热,使工艺气的冷凝热(潜热)得到充分利用。因此,所述含液态甲醇的原料包括液态甲醇和所述气相。也即,工艺气冷凝相变与甲醇气化相变相匹配。根据本实用新型,当所述含液体甲醇的原料中含有所述气相时,通过所述换热装置后,所述含烃工艺气的温度可降低至100-150℃,当所述含液体甲醇的原料中不含有所述气相时,所述含烃工艺气的温度可降低至150-180℃。其中,所述循环气的加入量只要保证使得工艺气的部分潜热能够将液态甲醇进行气化即可。例如,返回的循环气质量流量为甲醇的0.1-3倍,优选0.5-2.5倍。根据本实用新型,所述甲醇制烃的反应在存在有催化剂的条件下进行,所述催化剂为本领域技术人员所熟知的各种甲醇制烃催化剂,其可以根据所要得到的目标产物进行适当的选择,例如,所述催化剂可以为氯化锌、硅胶、氧化铝、二氧化硅、沸石ZSM-5和ZSM-11中的一种或多种。根据本实用新型的第二方面,本实用新型还提供了一种实施上述方法的甲醇制烃系统,现结合图1和图2对本实用新型的提供了甲醇制烃系统进行具体的描述。如图1和图2所示的,该系统包括流化床反应器1、换热装置2和气化器3;其中,含液态甲醇的原料在所述气化器3中与来自所述换热装置2的工艺气进行热交换;由所述气化器3产生的气化的含甲醇原料与来自所述流化床反应器1的工艺气在所述换热装置2中进行热交换;由所述换热装置2产生的过热的含甲醇原料进入所述流化床反应器中1进行反应,并且反应产生的含烃工艺气进入所述换热装置2中进行热交换;其中,所述流化床反应器1中设置有至少一个移热装置11,所述反应过程中产生的部分热量通过所述的移热装置11被移出。根据本实用新型,在所述流化床反应器1的底部设置有过热的含甲醇原料入口,顶部设置有反应后形成的工艺气的出口,如此设置使得过热的含甲醇原料由下向上运动,进行不同阶段的反应,同时还作为流化床反应器的流化气体。根据本实用新型,如上的换热方式通过如下的设置实现:气化器3上设置有气化的含甲醇原料的出口,换热装置2上设置有气化的含甲醇原料入口,该出口-入口通过管路连通。其中,含液体甲醇的原料在气化器3中气化后经该出口排出,并通过管路由设置在换热装置2上的气化的含甲醇原料入口进入换热装置2,在所述换热装置2中对气化的含甲醇原料进行过热处理。另外,在所述换热装置2上还设置有过热含甲醇原料的出口,该出口与流化床反应器1上设置的过热的含甲醇原料入口通过管路相通,以使在所述换热装置2中进行过热处理的含甲醇原料离开换热装置2后可进入流化床反应器1进行制烃反应。同时,在沿着流化床反应器1、换热装置2和气化器3线路上还分别设置有与输送含甲醇原料管路相独立的含烃工艺气输送管路。具体的,在所述换装装置2上独立的设置有含烃工艺气入口,该入口与流化床反应器1上设置的含烃工艺气的出口通过管路相通,以便在流化床反应器1中形成的含烃工艺气进入所述换热装置2,与其中的气化的含甲醇原料在相互独立的空间内进行间接换热。另外,在所述换装装置2还独立设置有含烃工艺气的出口,该出口与设置在气化器3上的含烃工艺气的独立入口相通,以便换热后的工艺气进入所述气化器3并在与含液态甲醇独立的空间再次进行间接化热,从而实现含液体的甲醇原料的气化以及含烃工艺气的再次降温。根据本实用新型,所述移热装置11为一个或多个,优选为2-5个,所述移热装置11优选沿着甲醇物料的走向逐层排布,以更好的实现不同阶段反应对温度的需求。根据本实用新型,所述移热装置11可以为本领域常规的热量转换装置,例如,通过冷却介质,具体的,所述换热装置11上分别设置有冷却介质的入口和出口,以实现冷却介质的连续注入与换热。所述冷却介质可以为水。例如,所述移热装置11可以为换热盘管设备,具体的,通过泵将水注入到反应器的换热盘管中的饱和液态水用泵送入换热盘管中,反应产生的热量与换热盘管中的水进行热交换,水气化后以高压蒸汽的形式离开反应器。根据本实用新型,所述流化床反应器1可以为多层流化床反应器(例如,2-5层)或循环流化床反应器,其中,当所述流化床反应器1为多层流化床反应器时,优选在所述多层流化床反应器中的每层均设置有移热装置11,如此,可以有效控制反应不同阶段的温度,使得反应条件达到最优。进一步优选的情况下,所述流化床反应器为多层循环流化床反应器,例如,2-5层,优选为2层(如图2所示)或3层(如图1所示)。根据本实用新型一种具体的实施方式,如图2所示,所述换热装置2包括第一预热器21和废热锅炉22:其中,所述第一预热器21上设置有含甲醇原料的入口及出口,以及含烃工艺气的入口及出口,所述废热锅炉22上设置有含烃工艺气的入口及出口。所述含烃工艺气从流化床反应器1的出口排出后,通过废热锅炉的含烃工艺气入口进入废热锅炉22,在废热锅炉22中与冷却介质换热后从含烃工艺气出口排出,再通过连接的管路进入第一预热器21中;气化的含甲醇的原料经气化器3上设置的含甲醇原料出口通过相连的管路从第一预热器21的含甲醇原料入口进入,并在其中与第一预热器21中的含烃工艺在相互独立的空间进行间接换热,换热后的甲醇原料经第一预热器21的含甲醇原料出口通过相连的管路进入流化床反应器1进行反应。根据本实用新型另一种具体的实施方式,所述换热装置2包括第一预热器21、废热锅炉22和第二预热器23:其中,所述第一预热器21和第二预热器23上分别设置有含甲醇原料的入口及出口,以及含烃工艺气的入口及出口,所述废热锅炉22上设置有含烃工艺气的入口及出口。所述含烃工艺气从流化床反应器1的出口排出后,通过设置在第二预热器23上的含烃工艺气入口进入第二预热器23,在其中换热后从含烃工艺气出口排出,通过废热锅炉的含烃工艺气入口进入废热锅炉22,在废热锅炉22中与冷却介质换热后从含烃工艺气出口排出,再通过连接的管路进入第一预热器21中;气化的含甲醇的原料经气化器3上设置的含甲醇原料出口通过相连的管路进入第一预热器21的含甲醇原料入口,并在其中与第一预热器21中的含烃工艺在相互独立的空间进行间接换热,换热后的甲醇原料经第一预热器21的含甲醇原料出口通过相连的管路进入第二预热器23,在其中继续与进入其中的含烃工艺气在相互独立的空间进行间接换热,换热后的甲醇原料经第二预热器23的含甲醇原料出口通过相连的管路进入流化床反应器1进行反应。根据本实用新型,所述甲醇制烃系统还包括分离装置4,所述分离装置4上设置有接收气化器3中部分冷凝的作为气液混合物的工艺气,从而对所述气液混合物进行分离。所述分离装置4包括至少一级冷凝器和至少二级分离器(如图1所示)所述气液混合物先进入一级分离器411以对其进行初级分离,得到部分液态烃、液态水和气相,所述气相然后进入冷凝器421进行冷凝处理,然后在进入二级分离器412进行液态烃的分离和可选的气相的分离。另外,根据另一种具体的实施方式,如图2所示,所述分离装置4包括二级冷凝器和三级分离器,所述气液混合物先进入一级分离器411以对其进行初级分离,得到部分液态烃、液态水和气相,所述气相然后进入一级冷凝器421进行冷凝处理,然后在进入二级分离器412进行液态烃、液态水的分离和气相的分离;所述气相然后进入二级冷凝器422进行冷凝处理,然后在进入三级分离器413进行液态烃、液态水的分离和可选的气相的分离。根据本实用新型,所述甲醇制烃系统还包括循环气供给装置5和液体甲醇供给装置6,以将由所述分离装置4分离出的气相经由所述循环气供给装置5通过管路供给至所述气化器3以作为循环气,其中,所述液体甲醇供给装置6也通过管路供给至所述气化器3,其中,所述气相和所述液体甲醇优选在管路中相遇并混合后再进入至所述气化器3。其中,所述循环气供给装置5可以为循环风机。现结合图1对本实用新型的甲醇制烃系统和方法进行详细说明:常温新鲜甲醇液体由甲醇供给装置5送入通向气化器3的管路,返回的循环气质量流量为甲醇的2.5倍,液态甲醇与循环气在管路中混合后,进入气化器3,与工艺气换热后全部气化。混合气体分别进入一级预热器23和二级预热器21,并在其中分别与工艺气进行换热,并从底部进入流化床反应器1以在其中发生反应。反应器内设置三层移热装置,及时移出热量,其中,每层中均设置有将甲醇转化为烃类的催化剂。反应器出口工艺气在二级预热器中换热,进行一次降温,进入废热锅炉进行二次降温。在一级预热器内换热再次降温。通过气化器3,工艺气发生部分冷凝。在一级分离器411中分离出液态水和液态烃,气相进入二级冷凝器421,之后进入二级分离器412,分离出液态水和液态烃分离出的气相送循环风机作为循环气体与来自甲醇供给装置5的液态甲醇混合,之后一并进入气化器3进行气化。两级分离器的液态水和液态烃类分别合并,外送。以下将通过实施例对本实用新型进行详细描述。使用沸石ZSM-5作为催化剂以对甲醇进行制烃。实施例1本实施例用于说明本实用新型提供的甲醇制烃方法和系统如图1所示,常温新鲜甲醇液体由甲醇供给装置5送入通向气化器3的管路,返回的循环气质量流量为甲醇的2.5倍。液态甲醇与循环气在管路中混合后,进入气化器3,与含烃工艺气换热后全部气化,升温至80.5℃。气化气体分别进入一级预热器21和二级预热器23,在其中与工艺气相互独立的空间中分别进行间接换热,所述气化的含甲醇的气体通过两次加热后,升温至280℃,并从流化床反应器1底部进入其中向上流动并发生反应。反应压力0.28MPaG。所述流化床反应器为3层循环流化床反应器,内设置三层移热装置,及时移出热量,产生4.0MPaG蒸汽,控制三段反应温度沿着甲醇的流向分别为360℃、360℃、350℃(出口工艺气温度),其中每层中均设置有用于催化甲醇反应的沸石ZSM-5催化剂。反应器出口含烃工艺气进入二级预热器23,在二级预热器中与含甲醇原料在相互独立的空间内间接换热,进行第一次降温,降温至327℃,之后进入废热锅炉22产生4.0MPaG蒸汽,含烃工艺气第二次降温至280℃。二次降温后的工艺气进入一级预热器21,与含甲醇原料在相互独立的空间内换热,进行第三次降温,降至119℃,至此将含烃工艺气的显热在最大程度上得到了回收。第三次降温后的工艺气进入气化器3,与气化器3中的含液态甲醇的原料在相互独立的空间内间接换热,此时,工艺气发生部分冷凝,放出潜热,工艺气温度降至84.8℃。在一级分离器411中分离出液态水和液态烃,气相进入二级冷凝器421,冷至63.4℃进入二级分离器412,分离出液态水和液态烃,循环气体送循环风机。两级分离器的液态水和液态烃类分别合并,外送。循环风机对循环气加压后与来自甲醇供给装置5的液体甲醇原料混合。记录在整个过程中的蒸汽消耗、蒸汽产出以及电消耗,结果见表1所示。实施例2本实施例用于说明本实用新型提供的甲醇制烃方法和系统利用图1所示的设备且按照实施例1的方法进行甲醇制烃,所不同的是,(1)将甲醇与质量流量1.5倍的循环气混合;(2)经过两次加热后含甲醇气体升温至250℃;(3)反应压力为0.6MPa,三段反应温度沿着甲醇的流向分别为400℃、390℃、380℃;(4)含烃工艺气三次降温后的温度分别为360℃、300℃、130℃。记录在整个过程中的蒸汽消耗、蒸汽产出以及电消耗,结果见表1所示。实施例3本实施例用于说明本实用新型提供的甲醇制烃方法和系统利用图1所示的设备且按照实施例1的方法进行甲醇制烃,所不同的是,(1)将甲醇与质量流量0.5倍的循环气混合;(2)经过两次加热后含甲醇气体升温至300℃;(3)反应压力为1.0MPa,三段反应温度沿着甲醇的流向分别为390℃、385℃、375℃;(4)含烃工艺气三次降温后的温度分别为340℃、290℃、150℃。记录在整个过程中的蒸汽消耗、蒸汽产出以及电消耗,结果见表1所示。实施例4本实施例用于说明本实用新型提供甲醇制烃方法和系统如图2所示,常温新鲜甲醇液体由甲醇供给装置5送入气化器3,与含烃工艺气换热后全部气化,93.7℃,气化气体进入一级预热器21,在其中与工艺气相互独立的空间中进行间接换热,所述气化气体通过加热后升温至250℃,并从流化床反应器1底部进入其中向上流动并发生反应。反应压力0.2MPaG。所述流化床反应器为3层循环流化床反应器,内设置两层移热装置,及时移出热量,产生4.0MPaG蒸汽,沿着甲醇物料的流向,床层温度分别控制在400℃和380℃。其中每层中均设置有用于催化甲醇反应的沸石ZSM-5催化剂。出反应器的含烃工艺气进入废热锅炉降温至290℃,产出4.0MPaG蒸汽,之后进入一级预热器21,与含甲醇原料在相互独立的空间内换热,经过预热器降温至162℃,至此将含烃工艺气的显热在最大程度上得到了回收。经一级预热器降温后的工艺气进入气化器3,与气化器3中的含液态甲醇的原料进行换热,此时,工艺气发生部分冷凝,放出潜热,工艺气温度降至104℃。在一级气-液-液分离器411中分出液态水和液态烃,气相进入二级冷凝器421降至60℃,在二级分离器412中分出液态水、液态烃和气相。气相进入三级冷凝器423降至40℃,在二级分离器413中分出液态水和液态,三级分离器的液态水和液态烃类分别合并,外送。记录在整个过程中的蒸汽消耗、蒸汽产出以及电消耗,结果见表1所示。实施例5本实施例用于说明本实用新型提供甲醇制烃方法和系统利用图1所示的设备且按照实施例1的方法进行甲醇制烃,所不同的是,甲醇单独在气化器中气化后,再与循环气混合,再进行后续的预热处理。作为气化器热源的工艺气温度为174℃(通过调节废热锅炉的移热量进行控制),在气化器中换热后出口温度为98℃,通过冷凝装置先部分冷凝后再在分离装置中进行烃分离。记录在整个过程中的蒸汽消耗、蒸汽产出以及电消耗,结果见表1所示。对比例1本对比例用于说明参比的甲醇制烃方法和系统利用图1所示的设备且按照实施例1的方法进行甲醇制烃,所不同的是,流化床反应器中不设置移热装置,而是通过在系统中引入水作为惰性成分吸收反应热。记录在整个过程中的蒸汽消耗、蒸汽产出以及电消耗,结果见表1所示。对比例2本对比例用于说明参比的甲醇制烃方法和系统利用图1所示的设备且按照实施例1的方法进行甲醇制烃,所不同的是,循环气经过含烃工艺气的两级预热后被加热到340℃,液态甲醇预热至反应压力下的饱和液态进如流化床反应器。原气化器改为空冷器,仍将工艺气降至相应温度。记录在整个过程中的蒸汽消耗、蒸汽产出以及电消耗,结果见表1所示。对比例3本对比例用于说明参比的甲醇制烃方法和系统利用图1所示的设备且按照实施例1的方法进行甲醇制烃,所不同的是,反应器为三层固定床反应器,反应器内无移热装置,靠大倍率的循环气体控制反应器温度。记录在整个过程中的蒸汽消耗、蒸汽产出以及电消耗,结果见表1所示。表1每进料1吨甲醇蒸汽消耗t蒸汽产出t电消耗kw·h实施例100.837.3实施例200.755.3实施例300.953.9实施例400.912.1实施例500.67.3对比例100.2811.8对比例20.1015.9对比例300.6326.7CN104818042A0.1025注:CN104818042反应器进口温度480℃,出口温度控制在550℃,至少需要6.5倍循环气,循环压缩机电耗很高,空冷器和水冷器也需要额外冷却这部分循环气。反应产物在换热单元1和2中将甲醇和循环气加热到480℃,本身仍为100℃以上的气态,冷凝潜热不回收。大部分冷凝工作在空冷器内进行,空冷器负荷极重,电耗很高。水冷器第5换热单元和脱戊烷塔再沸器消耗蒸汽。本实用新型采用流化床进行甲醇制烃,整个反应器内传质均匀无死角,反应物与催化剂全面接触,催化剂使用寿命一致;传热均匀迅速,传热系数大,再配合上换热装置,可以及时移走反应热,使反应器内温度平稳可控;当采用多层流化床时,在不同层分别设置换热装置,可精确控制反应不同阶段的温度,反应条件达到最优。同时,本实用新型在完全利用反应显热(同相物质由于降温所释放出来的热量)的同时,利用反应工艺气由气态冷凝为部分液态时放出的热量对甲醇液体进行气化,充分利用了反应工艺气蕴藏的潜热,使得热量的利用更加充分。另外,本实用新型由于不需要大量气体去控制反应器温升,因此,需要的返回气体的倍率明显小于现有技术,本实用新型返回气体相对甲醇进料量的倍率可以在零到多倍之间随意调节。综上所述,本实用新型能够有效地提高蒸汽产出,反应过程中不需要额外的蒸汽消耗,也降低了电消耗。并且如上所述采用本实用新型,还能够提高了催化剂效率,从而可以提高烃收率。以上详细描述了本实用新型的优选实施方式,但是,本实用新型并不限于上述实施方式中的具体细节,在本实用新型的技术构思范围内,可以对本实用新型的技术方案进行多种简单变型,这些简单变型均属于本实用新型的保护范围。另外需要说明的是,在上述具体实施方式中所描述的各个具体技术特征,在不矛盾的情况下,可以通过任何合适的方式进行组合。为了避免不必要的重复,本实用新型对各种可能的组合方式不再另行说明。此外,本实用新型的各种不同的实施方式之间也可以进行任意组合,只要其不违背本实用新型的思想,其同样应当视为本实用新型所公开的内容。当前第1页1 2 3