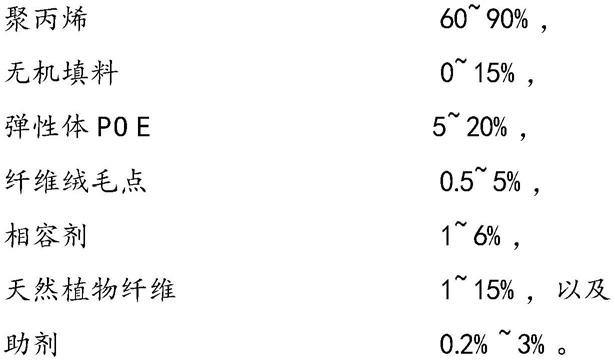
1.本发明涉及材料领域,尤其涉及一种适用于汽车内饰制件用的聚丙烯复合材料及其制备方法。
背景技术:2.聚丙烯作为一种通用塑料,由于其成本低、密度小、耐化学性能好、加工工艺性好、易回收利用等优点,广泛地应用于汽车的内外饰中,如汽车仪表板、立柱饰板、门内饰板、副仪表板等。然而聚丙烯也存在力学强度不高,冲击性能差,耐热性不好等性能问题,因此在实际使用过程中需要对其进行改性,以满足各类零部件的性能需求。
3.在汽车产品开发中,考虑到乘客的安全,对驾驶舱、副驾驶舱、立柱、甚至座椅都增加了安全气囊爆破配置。侧气帘通常是指从汽车立柱(a柱到c柱或d柱)与顶棚结合处安装的气囊,当汽车发生碰撞时,气囊弹出,保护驾驶员和乘客的安全。由于在爆破的瞬间,立柱受到气囊巨大的冲击力,但同时要求立柱不能有碎片飞出、不能脱离钣金件等影响司乘安全的因素发生。因此有侧气帘爆破需求的立柱材料要有十分高的韧性要求,尤其是低温情况下也要有较高的韧性要求。
4.另外,对于汽车产品,消费者已不再满足仅仅作为代步工具,在很大程度上就是一个可以移动的私人空间,因此消费者也越来越关注产品的品质感、科技感及人性化。基于此种需求,现有技术通过采用软质包覆或低压注塑等技术提高汽车内饰的感知品质。然而,由于这种技术成本昂贵、工艺复杂等原因限制了它的应用,因此开发低成本、良外观的材料来替代软质包覆或低压注塑,不仅能提升汽车内饰件的品质,同时还能有效的控制应用成本,提高产品的综合竞争力。
5.再者,车内空气质量强制性标准即将实施,因此车内空气质量也是各大主机厂和材料厂商研究的热点,聚丙烯材料作为内饰塑料件的主要原料,其气味必须严格控制,然而聚丙烯材料在高温(挤出和注塑)下都会散发出其特有的气味,是聚丙烯本身高温处理时散发出的气味,难以从材料本身改变。现有技术的气味解决方案是通过后续的热处理实现的,如在温度100℃~130℃条件下烘烤2h~10h,然而,热处理方法生产效率低,能源消耗巨大。
6.因此,有必要开发一种高抗冲、低成本、良外观且良气味的聚丙烯复合材料以满足汽车内饰制件尤其是汽车立柱的需求。
技术实现要素:7.本发明的一目的在于提供一种适用于汽车内饰制件用的聚丙烯复合材料,该聚丙烯复合材料具有高抗冲、低成本、良外观且良气味的优点。
8.本发明的另一目的在于提供一种制备适用于汽车内饰制件用的聚丙烯复合材料的方法,该方法制备的聚丙烯复合材料具有高抗冲、低成本、良外观且良气味的优点。
9.为实现上述目的,本发明提供了一种聚丙烯复合材料,所述聚丙烯复合材料适用于汽车内饰制件,按重量百分比计,所述聚丙烯复合材料包括:
[0010][0011]
例如,聚丙烯的重量百分比可为60%、61%、62%、63%、64%、65%、66%、67%、68%、69%、70%、71%、72%、73%、74%、75%、76%、77%、78%、79%、80%、81%、82%、83%、84%、85%、86%、87%、88%、89%或90%;无机填料的重量百分比可为0、1%、2%、3%、4%、5%、6%、7%、8%、9%、10%、11%、12%、13%、14%或15%;弹性体poe的重量百分比可为5%、6%、7%、8%、9%、10%、11%、12%、13%、14%、15%、16%、17%、18%、19%或20%;纤维绒毛点的重量百分比可为0.5%、0.6%、0.7%、0.8%、0.9%、1%、1.5%、2%、2.5%、3%、3.5%、4%、4.5%或5%;相容剂的重量百分比可为1%、2%、3%、4%、5%或6%;天然植物纤维的重量百分比可为1%、2%、3%、4%、5%、6%、7%、8%、9%、10%、11%、12%、13%、14%或15%。
[0012]
进一步地,所述聚丙烯为均聚聚丙烯或嵌段共聚聚丙烯,在测试温度为230℃、砝码为2.16kg的条件下,所述聚丙烯的熔融指数范围为15~60g/10min。
[0013]
进一步地,所述无机填料包括滑石粉,所述滑石粉的粒径范围均为1~5μm,所述无机填料可选择性地包括碳酸钙、硫酸钙和高岭土中的一种或几种。
[0014]
进一步地,所述弹性体poe是一类线性乙烯-辛烯共聚物,密度在0.88g/cm3~0.90g/cm3之间,在测试温度为190℃、砝码为2.16kg的条件下,所述弹性体poe的熔融指数范围为0.5~14g/10min。
[0015]
进一步地,所述纤维绒毛点为径长比≤1:12的碳纤维绒毛纤维,所述纤维绒毛点长度在1~4mm。具体地,纤维绒毛点可进行染色处理,颜色可调,可适用多种材料色系,可满足不同颜色的内饰方案应用,拓展了应用宽度。
[0016]
进一步地,所述相容剂为马来酸酐接枝聚丙烯树脂pp-g-mah,马来酸酐的接枝率为0.5~1.3%,在测试温度为190℃、砝码为2.16kg的条件下,所述相容剂的熔融指数为40~150g/10min。
[0017]
进一步地,所述天然植物纤维的纤维长度在1~10mm之间。
[0018]
进一步地,按重量百分比计,所述助剂包括抗氧剂0.1~2%以及光稳定剂0.1~1%。例如,抗氧剂为0.1%、0.2%、0.3%、0.4%、0.5%、0.6%、0.7%、0.8%、0.9%、1%、1.1%、1.2%、1.3%、1.4%、1.5%、1.6%、1.7%、1.8%、1.9%或2%;光稳定剂为0.1%、0.2%、0.3%、0.4%、0.5%、0.6%、0.7%、0.8%、0.9%或1%。
[0019]
进一步地,所述抗氧剂包括主抗氧剂和辅抗氧剂,主抗氧剂选用受阻酚和硫代酯类抗氧剂中的至少一种;辅抗氧剂选用亚磷酸盐和酯类抗氧剂中的至少一种;所述光稳定
剂选用三嗪类光稳定剂、苯并三唑光稳定剂、水杨酸酯类光稳定剂和受阻胺类光稳定剂中的一种或者几种的组合。例如,所述的主抗氧剂为3114、1010和dstp中的至少一种;辅抗氧剂为618和168中的至少一种。
[0020]
为实现上述目的,本发明还提供一种制备上述聚丙烯复合材料的方法,该制备方法包括步骤:
[0021]
(1)按照以下重量配比称取制备聚丙烯复合材料的原料,按重量百分比计,所述原料包括聚丙烯60~90%,无机填料0~15%,弹性体poe5~20%,纤维绒毛点0.5~5%,相容剂1~6%,天然植物纤维1~15%,以及助剂0.2%~3%;
[0022]
(2)将所述原料置于混合器中混合至均匀;所述混合器的转速为500~1800转/分钟,混合时间为3~5分钟;
[0023]
(3)将混合均匀的所述原料置于挤出机中,经熔融挤出后制得聚丙烯复合材料,整个挤出过程的停留时间为1~2分钟,挤出压力为12~18mpa,其中,螺杆各分区温度为:一区190~200℃、二区200~210℃、三区210~230℃、四区205~220℃。所述挤出机可选择为双螺杆挤出机,熔融挤出后一般还经过冷却、造粒、干燥处理等工序。
[0024]
与现有技术相比,本发明提供的适用于汽车内饰制件用的聚丙烯复合材料及其制备方法具有如下有益效果:
[0025]
(1)通过在聚丙烯体系中添加纤维绒毛点改进聚丙烯复合材料配方,使用该聚丙烯复合材料制得的立柱具备仿植绒效果,替代软质包覆或低压注塑技术,降低成本达50%;
[0026]
(2)相容剂改善纤维绒毛点与聚丙烯的界面,降低绒毛点对聚丙烯界面的破坏,从而不降低体系中滑石粉和弹性体poe的增韧增强效果,使制得的聚丙烯复合材料兼顾刚性和韧性,以满足汽车立柱侧气帘爆破的要求,不会出现碎裂,可通过汽车立柱侧气帘爆破验证;
[0027]
(3)在配方体系中添加天然植物纤维,使得制备的聚丙烯复合材料不仅具有仿植绒的效果,同时具有改善气味强度和类型的效果,且天然植物纤维的添加对纤维绒毛点的仿植绒效果具有协同增强作用;另不需要长时间的后续热处理,大幅度地提高了生产效率,降低能源能耗;
[0028]
(4)本发明所述的聚丙烯复合材料用于生产汽车立柱,制备工艺简单、合格率高、生产成本低。
[0029]
本发明的聚丙烯复合材料解决了汽车内饰“塑料感”、“高光泽”、“气味差”等消费者抱怨的问题,且具有高抗冲、低成本、良外观且良气味的优点。
具体实施方式
[0030]
本文所公开的“范围”以下限和上限的形式。可以分别为一个或多个下限,和一个或多个上限。给定范围是通过选定一个下限和一个上限进行限定的。选定的下限和上限限定了特别范围的边界。所有可以这种方式进行限定的范围是包含和可组合的,即任何下限可以与任何上限组合形成一个范围。例如,针对特定参数列出了60-120和80-110的范围,理解为60-110和80-120的范围也是预料到的。此外,如果列出的最小范围值1和2,和如果列出了最大范围值3,4和5,则下面的范围可全部预料到:1-3、1-4、1-5、2-3、2-4和2-5。在本发明中,如果没有特别的说明,本文所提到的所有实施方式以及优选实施方式可以
相互组合形成新的技术方案。
[0031]
在本发明中,如果没有特别的说明,本文所提到的所有技术特征以及优选特征可以相互组合形成新的技术方案。
[0032]
在本发明中,如果没有特别的说明,本文所提到的所有步骤可以顺序进行,也可以随机进行,但是优选是顺序进行的。
[0033]
在各实施例及对比例的聚丙烯复合材料配方中,聚丙烯为中沙(天津)石化生产的共聚聚丙烯,商品名为pp511mk40t,其熔体流动速率为29g/10min(测试条件:温度230℃,砝码2.16kg);无机填料为10000目滑石粉,平均粒径为1.3μm;弹性体poe为美国陶氏公司生产engage8180;纤维绒毛点为灰色市售产品,径长比≤1:12,长度1~4mm;主抗氧剂选用英国ice公司生产的dstp,化学名为硫代二丙酸十八酯,以及ciba公司生产的3114,化学名为3,5-二叔丁基-4-羟基苄基磷酸二乙酯,辅抗氧剂为ciba公司生产的168,化学名称为三(2,4-二叔丁基苄基)亚磷酸酯,天然植物纤维为市售的植物秸秆纤维。光稳定剂选用三嗪类光稳定剂、苯并三唑光稳定剂、水杨酸酯类光稳定剂和受阻胺类光稳定剂中的至少一种,在以下的各实施例及对比例中没有加入光稳定剂及其他助剂,并不影响聚丙烯复合材料的主要性能。
[0034]
聚丙烯复合材料的制备方法:
[0035]
(1)按照以下重量配比称取制备聚丙烯复合材料的原料,按重量百分比计,所述原料包括聚丙烯60~90%,无机填料0~15%,弹性体poe5~20%,纤维绒毛点0.5~5%,相容剂1~6%,天然植物纤维1~15%,以及助剂0.2%~3%;
[0036]
(2)将所述原料置于混合器中混合至均匀;所述混合器的转速为500~1800转/分钟,混合时间为3~5分钟;
[0037]
(3)将混合均匀的所述原料置于挤出机中,经熔融挤出后制得聚丙烯复合材料,螺杆转速为120~320转/分钟,整个挤出过程的停留时间为1~2分钟,挤出压力为12~18mpa,其中,螺杆各分区温度为:一区190~200℃、二区200~210℃、三区210~230℃、四区205~220℃。所述挤出机可选择为双螺杆挤出机。
[0038]
性能评价及实行标准:
[0039]
将按上述制备方法制造的塑料粒子材料置于100℃的鼓风干燥箱中干燥2~3小时,然后再将干燥好的粒料在注射成型机上进行注射成型制样。拉伸性能按照iso527进行,试样尺寸为170
×
10
×
4mm哑铃型样条,拉伸速度为50mm/min;弯曲性能测试按照iso178进行,试样尺寸为80
×
10
×
4mm,弯曲速度为2mm/min,跨距为64mm;简支梁缺口冲击强度按iso179进行,试样尺寸为80
×
10
×
4mm,缺口采用标准中a型,仿植绒效果及气味评价采用内部评价方法,气味评价样品取样量为50cm2。
[0040]
材料的综合性能通过测试所得的缺口冲击强度、拉伸强度、弯曲模量、仿植绒效果、气味强度和气味类型进行评判。实施例配方、对比例配方及各项性能测试结果见下列各表:
[0041]
表1实施例1~8及对比例1~3配方(单位:%)。
[0042][0043]
表2实施例1~8及对比例1~3测试结果
[0044][0045]“o”表示仿植绒效果,“o”越多表示仿植绒效果越好。
[0046]
从实施例1~8与对比例1的对比可以看出,通过添加纤维绒毛点和天然植物纤维所制备的聚丙烯复合材料具有良好的仿植绒效果,同时显著降低气味强度并改变气味类型。从实施案例1~3可以看出,纤维绒毛点的添加含量不一定是越高越好,绒毛含量越高,反而会降低材料的仿植绒效果;从实施例3~4可以看出相容剂的含量增加对材料冲击性能的提升不明显;从实施例2、5~6可以看出弹性体的添加量未影响材料的仿植绒效果,弹性体添加含量越高,材料缺口冲击强度越高,但材料的模量快速下降;从实施例8看出天然植物纤维添加量过多,气味太过浓烈,反而会导致材料气味变差;从实施例4与对比例2~3中可以看出,实施例4的植绒效果要优于对比例2,实施例4与对比例3气味效果相当;因为纤维绒毛点长度较小,难分散,致使外观易出现团聚点(缺陷),影响效果,由于天然植物纤维(长度较大)的加入,使得纤维绒毛点的分散更均匀,起到了协同增强作用,因此实施例4的植绒效果比单添加纤维绒毛点的对比例2更优。
[0047]
与现有技术相比,本发明提供的适用于汽车内饰制件用的聚丙烯复合材料及其制备方法具有如下有益效果:
[0048]
(1)通过在聚丙烯体系中添加纤维绒毛点改进聚丙烯复合材料配方,使用该聚丙烯复合材料制得的立柱饰板具备仿植绒效果,替代软质包覆或低压注塑技术,降低成本达50%;
[0049]
(2)相容剂改善纤维绒毛点与聚丙烯的界面,降低绒毛点对聚丙烯界面的破坏,从而不降低体系中滑石粉和弹性体poe的增韧增强效果,使制得的聚丙烯复合材料兼顾刚性和韧性,以满足汽车立柱饰板侧气帘爆破的要求,不会出现碎裂,可通过汽车立柱饰板侧气帘爆破验证;
[0050]
(3)在配方体系中添加天然植物纤维,使得制备的聚丙烯复合材料不仅具有仿植绒的效果,同时具有改善气味强度和类型的效果,且天然植物纤维的添加对纤维绒毛点的仿植绒效果具有协同增强作用;另不需要长时间的后续热处理,大幅度地提高了生产效率,降低能源能耗;
[0051]
(4)本发明所述的聚丙烯复合材料用于生产汽车立柱饰板,制备工艺简单、合格率高、生产成本低。
[0052]
本发明的聚丙烯复合材料解决了汽车内饰“塑料感”、“高光泽”、“气味差”等消费者抱怨的问题,且具有高抗冲、低成本、良外观且良气味的优点。
[0053]
以上所揭露的仅为本发明的优选实施例而已,当然不能以此来限定本发明之权利范围,因此依本发明申请专利范围所作的等同变化,仍属本发明所涵盖的范围。