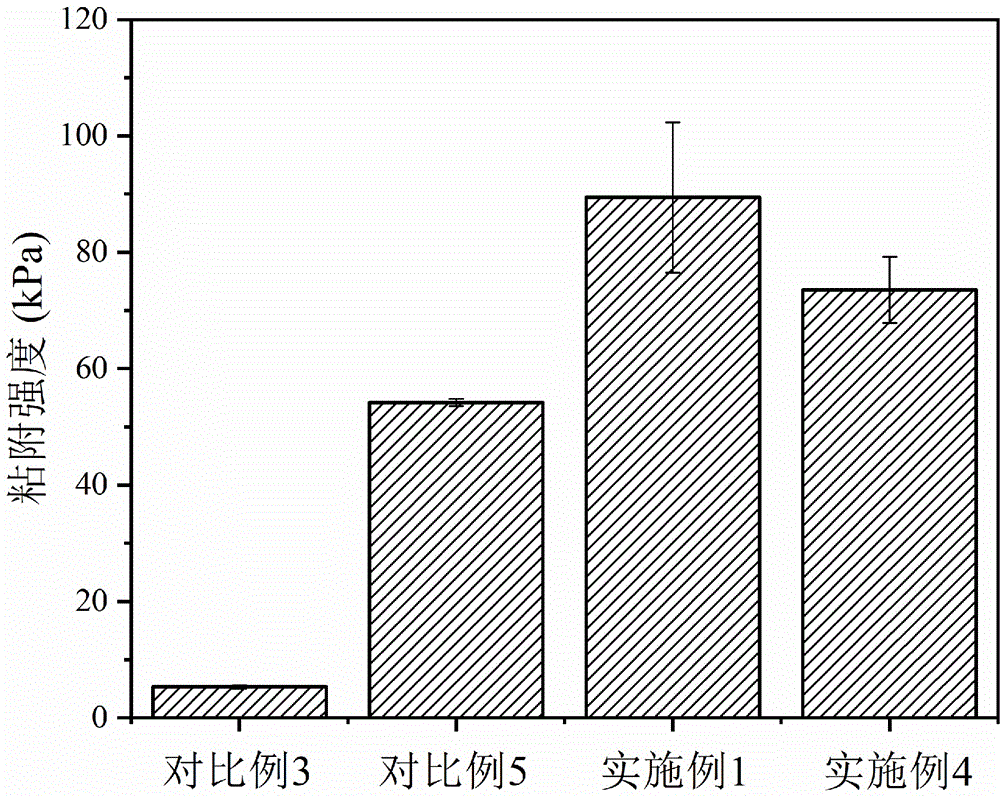
本发明属于仿生材料力学与纳米复合材料制备
技术领域:
,具体涉及一种兼具高强度和粘附性能的硅橡胶复合材料及其制备方法。
背景技术:
:硅橡胶是一类具有良好生理惰性、耐高低温性的特种橡胶材料,被广泛应用于建筑、医疗、航空航天等领域。纯硅橡胶的力学性能非常差,无法满足实际应用需求,通常需要添加补强填料进行增强。纳米二氧化硅(sio2)是硅橡胶最为常用的补强填料,具有与硅橡胶相容性好、增强效果突出、成本低等优势。另外,纳米sio2表面存在大量丰富的高活性羟基,容易通过表面改性接枝不同的化学官能团,调控sio2与硅橡胶分子之间的相互作用。因此,通过sio2的表面改性实现高强度硅橡胶复合材料的制备一直都是橡胶材料相关研究的热点。另一方面,在新兴的仿生科技领域,以硅橡胶为典型代表的超弹性材料柔软且易改变形状,能够与各种表面形成良好的接触,被广泛用于制造仿生壁虎刚毛微结构粘附表面,因此硅橡胶的粘附性也是一项重要的性能参数。在该研究领域,较为常用的方法是对硅橡胶表面进行亲水改性或者在其表面制备微纳结构的方式改善硅橡胶的粘附性。但此类方法制备过程往往较为复杂,不利于规模化制备,对硅橡胶的耐久性以及强度也有一定影响。因此,如何通过较为简单方式制备出兼具高强度和强粘附的硅橡胶复合材料显得尤为重要。高分子量的甲基乙烯基硅橡胶可通过sio2的补强获得较高的强度,但因其表面能较低,对物体的浸润性较差,导致其表面粘附性很弱。低分子量的液体硅橡胶虽具有杰出的粘附性,但力学强度往往提升有限。将两者的优势相结合,以甲基乙烯基硅橡胶为主体,液体硅橡胶为增粘剂,制备兼具高强度、强粘附的硅橡胶复合材料,在科研及生活中均具有突出的应用前景。技术实现要素:为了克服现有技术中的问题,本发明提供了一种兼具高强度和粘附性能的硅橡胶复合材料的制备方法。该方法以甲基乙烯基硅橡胶为主体,液体硅橡胶为增粘剂制备得到的硅橡胶复合材料兼具高强度、强粘附性能以及可反复粘附性。为实现上述目的,本发明的技术方案如下:一种兼具高强度和粘附性能的硅橡胶复合材料的制备方法,先将硅橡胶与纳米二氧化硅混炼均匀,得混炼胶;然后将混炼胶于100~200℃下热处理1~3h,冷却至室温后,再与液体硅橡胶增粘剂、硫化剂混炼均匀;最后经模压成型即得兼具高强度和粘附性能的硅橡胶复合材料。优选的,各物料的重量份数如下:硅橡胶100份,纳米二氧化硅40~60份,液体硅橡胶增粘剂1~7份,硫化剂0.5~1.5份;所述纳米二氧化硅为表面改性sio2。优选的,所述液体硅橡胶增粘剂通过下述方法制得:将聚硅氧烷单体在搅拌条件下升温至80-100℃,加入催化剂后升温至100~130℃,反应60~120min,然后加入表面改性sio2继续反应40~80min后,升温至130~150℃(使未反应催化剂分解),然后减压抽真空(去除未反应的单体及低沸点物质),经冷却后即得。进一步优选的,表面改性sio2表面修饰的反应性基团为甲基、乙基、环氧基、乙烯基、氨基和氢基中的一种,包括混炼胶和液体硅橡胶增粘剂中使用的表面改性sio2。进一步优选的,所述聚硅氧烷单体为二甲基环硅氧烷混合物;所述催化剂为碱性催化剂四甲基氢氧化铵,催化剂的用量为聚硅氧烷单体质量的0.01~0.02%;表面改性sio2的用量为聚硅氧烷单体质量的6~14wt%。具体的,聚硅氧烷单体中的八甲基环四硅氧烷(d4)含量>95%。优选的,所述硅橡胶为甲基乙烯基硅橡胶,分子量为60~80万,乙烯基含量为0.1~0.2wt%。优选的,所述硫化剂为过氧化物硫化剂;进一步的,过氧化物硫化剂为2,5-二甲基-2,5-二(叔丁基过氧基)己烷(双25)。通过上述方法制备得到的兼具高强度和粘附性能的硅橡胶复合材料,其在具备高拉伸强度、撕裂强度的同时,具备强粘附性和可反复粘附性。和现有技术相比,本发明的有益效果是:1.以表面改性纳米sio2作为补强填料,提高了sio2与硅橡胶的相互作用,改善了与硅橡胶之间的相容性,提高了硅橡胶的拉伸强度和撕裂强度,此外,所得到的硅橡胶还具有良好的柔韧性和粘附性;2.本发明采用的液体硅橡胶增粘剂与硅橡胶具有相同的主链结构,利于在硅橡胶基体中的分散,降低对硅橡胶强度的影响,而且液体硅橡胶增粘剂中所含有的羟基、环氧基等极性基团在硅橡胶复合材料具备高拉伸强度和撕裂强度的同时,进一步提高了硅橡胶复合材料的粘附性;3.本发明中使用的原料组分品类少,基本为普通市售产品,成本低;制备流程简单,可进一步进行规模化制备;4.通过本发明的方法制备得到的硅橡胶复合材料兼具高拉伸强度、撕裂强度和强粘附性,同时可反复粘附使用。附图说明图1为实施例1、实施例4与对比例3、对比例5制备的硅橡胶粘附性能;图2为实施例1制备的兼具高强度和粘附性能的硅橡胶复合材料的反复粘附性。具体实施方式下面结合实施例和附图对本发明进行进一步说明,但并不是对本发明的限制。本实施例使用的市售甲基乙烯基硅橡胶,分子量为62万,乙烯基含量0.164wt%。本实施例中的混炼是在室温下进行的。下述实施例中使用的液体硅橡胶增粘剂通过以下方法制得:将100gdmc在搅拌条件下升温至90℃后加入0.02gme4noh,并逐渐升温至105℃,反应80min(从加热至90℃起开始计算时间,最终温度保持在105℃,然后加入10g表面改性sio2(表面改性基团为环氧基),继续反应50min后,升温至130℃去除未反应的催化剂me4noh,减压蒸馏直至无馏分脱出,室温冷却后即得液体硅橡胶增粘剂(即sio2/pdms增粘剂)。需要说明的是:本实施例中使用的表面改性sio2是通过液相原位表面修饰法得到,具体可参见文献(lix,caoz,zhangz,dangh.surface-modificationinsituofnano-sio2anditsstructureandtribologicalproperties.appliedsurfacescience.2006;252:7856-7861.)或专利cn1666954a制备,得到表面含化学基团的改性纳米sio2;也可以在河南河大纳米材料工程研究中心有限公司购买获得。实施例1本实施例兼具高强度和粘附性能的硅橡胶复合材料的制备方法:将100份甲基乙烯基生胶与60份表面改性纳米sio2(表面修饰基团为乙烯基)在开炼机中混炼均匀(混炼时间30min),然后置于烘箱中200℃下热处理2h,取出后冷却至室温,依次加入3份液体硅橡胶增粘剂和0.5份2,5-二甲基-2,5-二(叔丁基过氧基)己烷(下述为双25)硫化剂,在开炼机中混炼均匀(混炼10min)后出片。最后通过平板硫化仪(硫化条件:170℃,20mpa,10min)硫化后得到样片。实施例2将100份甲基乙烯基生胶与50份表面改性纳米sio2(表面修饰基团为乙烯基)在开炼机中混炼均匀(混炼30min),然后置于烘箱中200℃下热处理2h,取出后冷却至室温,依次加入3份液体硅橡胶增粘剂和0.5份双25硫化剂,在开炼机中混炼均匀(混炼10min)后出片。最后通过平板硫化仪(硫化条件:170℃,20mpa,10min)硫化后得到样片。实施例3将100份甲基乙烯基生胶与55份表面改性纳米sio2(表面修饰基团为乙烯基)在开炼机中混炼均匀(混炼30min),然后置于烘箱中200℃下热处理2h,取出后冷却至室温,依次加入3份液体硅橡胶增粘剂和0.5份双25硫化剂,在开炼机中混炼均匀(混炼10min)后出片。最后通过平板硫化仪(硫化条件:170℃,20mpa,10min)硫化后得到样片。实施例4将100份甲基乙烯基生胶与60份表面改性纳米sio2(表面修饰基团为乙烯基)在开炼机中混炼均匀(混炼30min),然后置于烘箱中200℃下热处理2h,取出后冷却至室温,依次加入1份液体硅橡胶增粘剂和0.5份双25硫化剂,在开炼机中混炼均匀(混炼10min)后出片。最后通过平板硫化仪(硫化条件:170℃,20mpa,10min)硫化后得到样片。实施例5将100份甲基乙烯基生胶与40份表面改性纳米sio2(表面修饰基团为氨基)在开炼机中混炼均匀(混炼30min),然后置于烘箱中于150℃下热处理1h,取出后冷却至室温,依次加入7份液体硅橡胶增粘剂和0.5份双25硫化剂,在开炼机中混炼均匀(混炼10min)后出片。最后通过平板硫化仪(硫化条件:170℃,20mpa,10min)硫化后得到样片。实施例6将100份甲基乙烯基生胶与60份表面改性纳米sio2(表面修饰基团为环氧基)在开炼机中混炼均匀(混炼30min),然后置于烘箱中于100℃热处理3h,取出后冷却至室温,依次加入5份液体硅橡胶增粘剂和1.5份双25硫化剂,在开炼机中混炼均匀(混炼10min)后出片。最后通过平板硫化仪(硫化条件:170℃,20mpa,10min)硫化后得到样片。对比例1将100份甲基乙烯基生胶与57份市售气相sio2(hl-200)在开炼机中混炼均匀(混炼30min),混炼过程中加入7.5份市售羟基硅油,待混炼均匀后然后加入1.2份双25硫化剂,混炼均匀(混炼10min)后出片。最后通过平板硫化仪(硫化条件:170℃,20mpa,10min)硫化后得到样片。对比例2将100份甲基乙烯基生胶与57份市售进口气相sio2(r-106)在开炼机中混炼均匀(混炼30min),混炼过程中加入7.5份市售羟基硅油,待混炼均匀后然后加入1.2份双25硫化剂,混炼均匀(混炼10min)后出片。最后通过平板硫化仪(硫化条件:170℃,20mpa,10min)硫化后得到样片。对比例3将市售进口双组份硅橡胶(sylgard184)按固化比例a:b=10:1混合均匀,置于烘箱中固化(固化条件:100℃,30min),然后冷却至室温即得到样片。对比例4将100份甲基乙烯基生胶与57份表面改性纳米sio2(表面修饰基团为乙烯基)在开炼机中混炼均匀(混炼30min),然后加入1.2份双25硫化剂,混炼均匀(混炼10min)后出片。最后通过平板硫化仪(硫化条件:170℃,20mpa,10min)硫化后得到样片。对比例5本对比例是在实施例1的基础上作出的,与实施例1的区别在于本对比例没有使用液体硅橡胶增粘剂。将100份甲基乙烯基生胶与60份表面改性纳米sio2(表面修饰基团为乙烯基)在开炼机中混炼均匀(混炼30min),然后置于烘箱中于200℃下热处理2h,取出后冷却至室温,加入0.5份双25硫化剂,混炼均匀后出片。最后通过平板硫化仪(硫化条件:170℃,20mpa,10min)硫化后得到样片。性能测试拉伸强度和伸长率:按gb/t528-1998测试;撕裂强度:按gb/t529-1999测试;硬度:按gb/t531-1999测试;粘附强度:将试样裁剪成1cm×1cm×2mm的样片,然后将其粘附到玻璃上,并在其下悬挂重物,通过记录粘附失效前的最大重量得到其粘附强度。实施例1-3和对比例1-5制备的硅橡胶力学性能见表1。表1实施例1-3和对比例1-5制备硅橡胶的力学性能样品拉伸强度/mpa撕裂强度/kn·m-1断裂伸长率/%硬度实施例110.425.873460实施例210.123.855654实施例310.325.854057对比例17.119.657465对比例28.320.644864对比例35.757045对比例49.422.659155对比例510.324.455560从表1中可以看出,实施例1-3、对比例4-5的拉伸强度、撕裂强度要显著优于对比例1-3。对比例4与对比例1-2的制备过程基本相同,不同之处在于选用的sio2不同,对比例4中使用的为经过表面改性的纳米sio2(与实施例1-3相同),对比例1中使用的是市售国产气相sio2(宜昌汇富hl-200),对比例2中使用的是市售进口气相sio2(德固赛r106))。对比例1-2制备过程中均需要添加羟基硅油作为增容剂,改善气相sio2与硅橡胶之间的相容性,提高气相sio2的添加量,而对比例4和5中则不需要,说明表面改性纳米sio2与硅橡胶具有更好的相容性。在相同添加量情况下,对比例4与对比例1-2相比,采用表面改性sio2补强的硅橡胶在拉伸强度、撕裂强度以及断裂伸长率均优于采用气相法sio2补强的硅橡胶,说明表面改性sio2具有更佳的补强效果。另外,值得注意的是对比例4的硬度明显低于对比例1-2,通常情况下,硬度与强度往往呈正相关的关系,如何制备较低硬度,高强度的硅橡胶材料一直是行业中的难题,这里采用表面改性后的sio2得到了兼具柔性与强度的硅橡胶材料,为解决这一难题提供了新的途径。实施例1-3与对比例4-5相比,实施例1-3的拉伸强度和撕裂强度略高于对比例4-5,说明使用了液体硅橡胶增粘剂并没有影响表面改性的纳米sio2对硅橡胶基体的补强效果,这是由于采用的液体硅橡胶增粘剂与硅橡胶分子链结构相同,具有良好的相容性,因此并未影响硅橡胶的力学性能。对比例3为一种常用的市售进口硅橡胶基体材料,常用于硅橡胶粘附性的相关研究,因此将其作为对比例。实施例1、实施例4与对比例3、对比例5制备的硅橡胶的粘附强度见图1。由图1可得,对比例3、对比例5、实施例1和实施例4的粘附强度分别为:5.3kpa、54.2kpa、89.4kpa和73.5kpa。实施例1的粘附强度与对比例5相比,提高了64.9%,与对比例3相比,提高了1586.8%。可以看出,实施例1和实施例4的粘附强度远优于对比例3和对比例5,对比例5中虽然未添加液体硅橡胶增粘剂,但其粘附强度优于对比例3;而添加了液体硅橡胶增粘剂的实施例1和4则表现出更佳的粘附强度。从图1和表1中实施例1和对比例5的数据可以看出,实施例1中的硅橡胶复合材料在增加了液体硅橡胶增粘剂后,拉伸强度和撕裂强度并没有下降,粘接强度却得到了很大提升。一方面是由于液体硅橡胶与甲基乙烯基硅橡胶具有相同的主链结构,避免了相容性的问题,另一方面,液体硅橡胶本身具有优异的粘接性,引入到甲基乙烯基硅橡胶后同样赋予了甲基乙烯基硅橡胶较好的粘附性,从而制备得到本发明中兼具高拉伸强度和撕裂强度的同时还具有优良的粘接强度硅橡胶复合材料。采用实施例1制备的硅橡胶的反复粘附性能见图2。反复粘附性的测试方法:测试过程同粘附强度测试,在当样片撕脱后,再次粘附到玻璃上重复测试其粘附强度,反复测试20次。图2中的反复粘附性是将样片经过反复20次粘附-撕脱测试后得到的数据,由图2可见,实施例1的硅橡胶复合材料经过多次粘附-撕脱后仍具有很好的粘附性,表现出较为稳定反复粘附性。而现有的硅橡胶材料由于自身粘附强度较低,通常需要对其表面增加微结构或表面改性提升其粘附性,制备过程较为复杂,且在制备过程中又容易造成硅橡胶表面微裂纹的产生,影响使用寿命以及粘附稳定性。综上所述,经对比分析可发现,通过本发明的方法可制备得到兼具高强度和强粘附并且具有反复粘附性的硅橡胶复合材料,而且制备流程简单,成本低,可规模化生产。当前第1页12