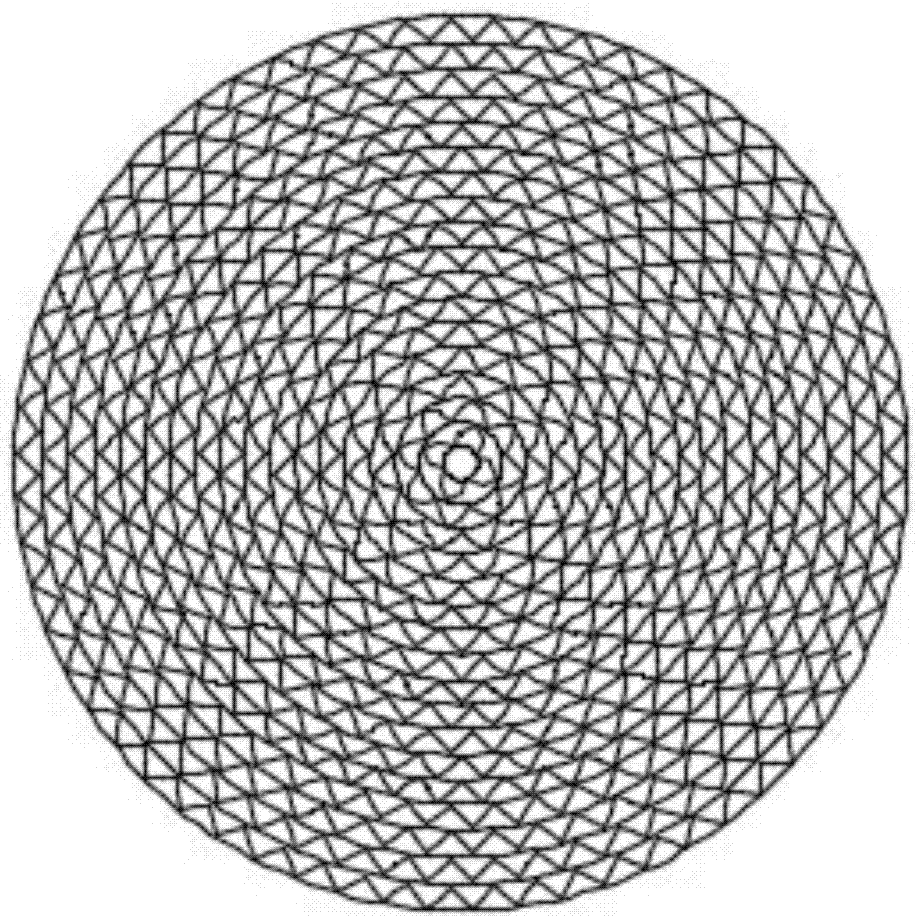
本发明涉及用于空气除湿的转轮除湿机的设备
技术领域:
,尤其涉及一种a型分子筛除湿载体及其制备方法。
背景技术:
:现有转轮除湿装置的除湿转轮一般选择硅胶、分子筛、氯化锂等做为除湿转轮的除湿剂,国内关于除湿转轮的申请专利中,多为转轮的结构和处理流程设计优化,来进行节能和提供更低露点的空气,包括合理划分处理区、分两级转轮进行处理、在两级处理之前分别增加降温处理提高除湿效果等等,而对除湿转轮的除湿剂选择及其担载过程优化的专利则很少,其中具有代表性的专利如下:cn200610162839.0公开了一种除湿转子及其制备方法,在除湿转子的纤维质载体上装载有两种以上的沸石的除湿转子,在该纤维质载体上形成有三层结构的除湿剂层,该三层结构的除湿剂层由含有氢离子交换沸石或第二金属离子交换沸石的第一层与含有原沸石并夹持该第一层的第二层构成;cn200710084129.5公开了一种即使加热器温度比以往低,除湿量仍多的除湿转子。该除湿转子使用于再生空气的入口侧的开口面的温度为250~500℃的除湿机中,其中,在除湿转子的纤维质载体上装载了第一除湿剂与第二除湿剂的混合物,该第一除湿剂为脱湿峰值温度为90~160℃的沸石,该第二除湿剂为脱湿峰值温度为40~100℃并且脱湿峰值温度比该沸石的脱湿峰值温度低5℃以上的非晶质无机多孔体;cn200910154107.0公开了一种氯化锂硅胶复合转轮的制备方法,该发明依次包括抄纸、上硅胶、轧制转轮体和转轮成型工序,其特征在于:轧制转轮体工序和转轮成型工序之间还依次包括浸渍硅酸盐溶液、酸化处理、煅烧和浸渍氯化锂溶液工序,浸渍硅酸盐溶液工序中,将转轮体浸到浓度为10-30%的硅酸盐水溶液中;酸化处理工序中,将转轮体浸泡到浓度为3-30%的酸溶液中;煅烧工序中,将转轮体置于400-500℃的高温下煅烧;浸渍氯化锂溶液工序中,将转轮体浸到浓度15-40%的氯化锂溶液中;以及cn201510779585.6公开了一种分子筛复合纤维型材的制备方法,该分子筛复合纤维型材为蜂窝状结构,该分子筛复合纤维型材可为mfi型、bea型或fau型,每个类型的分子筛复合纤维型材由若干个平行孔道组成,每个孔道的高度为1-30mm,每个孔道的宽度为2-60mm,分子筛复合纤维型材的比表面积为200-400m2/g,本发明制备得到的分子筛复合纤维型材由于具有丰富的纤维空隙和宏观孔道结构,有利于水蒸气的物质和热量传输,具备原位合成分子筛的空间条件;在纤维型材内部和表面原位合成分子筛,既实现了功能材料的用途转化,又保持了原有的基本结构和强度。本发明制备方法涉及的a型分子筛具有独特的生长机理,“在水热体系中,其晶体生长过程中存在着叠合生长的现象,即体系经过一个晶化诱导阶段后,大量的纳米晶形成,纳米晶作为生长基元,相互迅速聚集直接叠合演化为微米多晶体或微米单晶,叠合过程不同于邻位面生长所描述的生长基元一个个按次序嵌入晶面,而是许多纳米晶同时相互按一定方向接合而形成微晶。晶化中后期,纳米晶消耗殆尽,体系饱和度下降,叠合生长停止,晶体生长按线性规律进行(李酽《a型分子筛生长的理论模型》)”。技术实现要素:本发明旨在提供一种制作工艺简便,能够最大限度利用原料、节约成本并适合大量投入生产的a型分子筛除湿蜂窝载体及其制备方法,本发明的重点在于利用a型分子筛相对其它吸湿剂独特的生长机理,用无机纤维进行担载生长。为实现上述目的,本发明采用以下技术方案:本发明的第一个方面是提供一种a型分子筛除湿载体的制备方法,主要技术方案是先在无机纤维载体空隙间担载分子筛晶种,再通过原位水热合成反应在无机纤维载体表面和无机纤维载体空隙间合成分子筛,并使其负载于无机纤维载体上,担载完毕后即得a型分子筛除湿载体。进一步地,所述的a型分子筛除湿载体的制备方法,具体包括如下步骤:步骤1,将片状的无机纤维载体经过预处理后,在其间隙和表面利用物理方法形成一层配制的a型分子筛晶种悬浮液,于50~70℃烘干后制得晶种化载体;其中,所述a型分子筛晶种悬浮液的浓度为1.0-2.0wt%;步骤2,配制浓度为1.0-3.0wt%的a型分子筛母液,将步骤1制得的晶种化载体放入盛有所述a型分子筛母液的反应釜中,密封后置于80-120℃恒温烘箱下晶化1-5h,晶化结束即取出反应釜用自来水急速冷却,再取出担载完毕的无机纤维载体进行洗涤后,置于50-250℃的烘箱内烘干,即得a型分子筛除湿载体。进一步地,在所述的a型分子筛除湿载体的制备方法中,所述无机纤维载体选自玻璃纤维、陶瓷纤维、高硅氧纤维或氧化铝纤维中的一种或几种。更进一步地,在所述的a型分子筛除湿蜂窝载体的制备方法中,所述无机纤维选自玻璃纤维和高硅氧纤维,其中,将担载完毕的平坦型高硅氧纤维加工成波纹状,再将其与另外一片平坦型玻璃纤维叠合,形成一层载体,将该层加工卷绕成圆柱体,采用这种结构a型分子筛除湿蜂窝载体具有更为优异的吸湿性能。(删除原因:不清楚这一段用意)(此部分为对上述“无机纤维载体”的选择进一步扩展,建议保留)进一步地,在所述的a型分子筛除湿载体的制备方法中,所述无机纤维载体的预处理方法为:将无机纤维载体放入蒸馏水中采用超声洗涤,洗去无机纤维表面及内部空隙存在的颗粒杂质;所述超声波洗涤2次,每次2-4min。进一步地,在所述的a型分子筛除湿载体的制备方法中,所述a型分子筛除湿载体由无机纤维在进行分子筛担载完毕后再进行蜂窝结构加工制得。进一步地,在所述的a型分子筛除湿载体的制备方法中,所述a型分子筛除湿载体由无机纤维在进行蜂窝结构加工成型后再进行分子筛担载制得。进一步地,在所述的a型分子筛除湿载体的制备方法中,所述步骤(1)中a型分子筛晶种悬浮液的配制工艺为:先配制a型分子筛晶种液,置于超声波中震荡10-30min,使分子筛晶种分散均匀,再将一定量的水凝胶加入到a型分子筛晶种液中,得到浸渍用的浓度为1.0-2.0wt%的a型分子筛晶种悬浮液。、进一步地,在所述的a型分子筛除湿载体的制备方法中,所述步骤(1)中a型分子筛晶种悬浮液中晶种和水凝胶的质量比为(8-10):1;优选地,浸渍用的晶种悬浮液中晶种和凝胶的质量比为9:1。进一步地,在所述的a型分子筛除湿载体的制备方法中,所述a型分子筛晶种悬浮液的浓度为1.3-1.8wt%;优选为1.5wt%。(此部分为上述技术方案的进一步限定,建议保留)进一步地,在所述的a型分子筛除湿载体的制备方法中,所述步骤(1)中物理方法为浸渍、喷涂或淋洗工艺,优选为浸渍工艺。进一步地,在所述的a型分子筛除湿蜂窝载体的制备方法中,所述步骤(1)中烘干温度为50-70℃;优选地,烘干温度为55-65℃;更优选地,烘干温度为60℃。进一步地,在所述的a型分子筛除湿载体的制备方法中,所述步骤(2)中晶化温度为90-110℃,晶化时间为2~3h,烘干温度为140-160℃;优选地,所述晶化温度为95-100℃,晶化时间为2.5h,烘干温度为150-155℃。作为本发明的一个优选技术方案,所述的a型分子筛除湿蜂窝载体的制备方法,具体包括如下步骤:步骤1,片层无机纤维预处理:取两片片层平坦型的无机纤维,将其放入蒸馏水中采用超声洗涤,洗去无机纤维表面及内部空隙存在的颗粒杂质;步骤2,a型分子筛晶种液制备:配制浓度为1.0-2.0wt%的晶种液,置于超声波中震荡10-30min,使分子筛晶种分散均匀,再将一定量的水凝胶加入到晶种液中,得到浸渍用的晶种悬浮液;步骤3,无机纤维载体担载a型分子筛晶种:将步骤(2)制得的晶种悬浮液,通过物理方法在无机纤维载体间隙和表面形成一层a型分子筛晶种层,烘干,得晶种化载体;步骤4,二次原位水热合成:将步骤(3)制得的晶种化载体放入盛有浓度1.0-3.0wt%a型分子筛母液的反应釜中,将反应釜密封后置于80-120℃恒温烘箱下晶化1-5h,该晶种化载体利用步骤(3)中形成的a型分子筛晶种层做为生长中心或提供晶核,从分子筛母液中汲取所需要的原料,向各个方向生长填充无机纤维载体空隙;晶化结束后,取出反应釜,用自来水急速冷却反应釜,再取出担载完毕的无机纤维载体,用去离子水洗涤三次,洗涤完毕后置于50-250℃烘箱内烘干;步骤5,载体卷绕成蜂窝载体:将步骤(4)担载完毕的其中一片平坦型无机纤维加工成波纹状,再将其与另外一片平坦型无机纤维叠合,形成一层载体,将该层加工卷绕成圆柱体,即得a型分子筛除湿蜂窝载体。本发明的第二个方面是提供一种采用上述方法制备的a型分子筛除湿载体,所述a型分子筛除湿载体为蜂窝状的圆柱体结构,其由两层担载完毕的无机纤维经叠合、卷绕而成,其中一层为担载完毕的平坦型无机纤维,一层为担载完毕的平坦型无机纤维加工而成的波纹状无机纤维。本发明采用上述技术方案,与现有技术相比,具有如下技术效果:本发明a型分子筛除湿载体的制备方法,直接将分子筛种子分散于水后担载在载体上,理论上除了无机纤维载体,其余均为有用的分子筛;利用了无机纤维做为转轮基材,材料广泛,绿色环保,且可塑性极强,可根据需要制备成任意尺寸和形态的转轮型材;本发明分子筛担载于无机纤维载体的方法简单直接,比在铝源硅源混合溶液中使载体担载分子筛的方法成本低,且该方法消除了分子筛晶体生长所需要的晶核形成过程,有利于分子筛优先在支撑体上生长,从而更容易使其结合无机纤维自身内部骨架结构形成致密的分子筛晶体层。综上所述,采用本发明方法制备的a型分子筛除湿载体筛吸湿量大、稳定性好、解吸温度在80~100℃,节约大量能源;且制备工艺简便,能够最大限度利用原料,节约成本并适合大量投入生产,增强了市场竞争力。附图说明图1为本发明担载后的单层a型分子筛除湿载体的剖面结构示意图;图2为采用本发明a型分子筛除湿载体卷绕而成的圆柱体剖面结构示意图;图3为本发明实施例1-4的和比较例的分子筛负载量对比示意图。具体实施方式本发明提供了一种采用a型分子筛作为该除湿转轮主要吸湿剂制备a型分子筛除湿载体的方法,其主要技术原理是:通过在由无机纤维(玻璃纤维、陶瓷纤维、高硅氧纤维或氧化铝纤维等)制成的片状载体上担载一层a型分子筛晶种,利用a型分子筛相对其它吸湿剂独特的生长机理,使其于无机纤维上首先形成一层稳定的生长基元,再通过原位水热合成法对其继续进行a型分子筛晶种的生长,使a型分子筛晶种相互聚集,在无机纤维的空隙拼接成长为牢固的微米晶,一定时间后取出,150℃下烘干;将含有分子筛的片状平坦型无机纤维片状体2瓦楞成型加工成波纹状,其再与另外一片片状含有分子筛的平坦型无机纤维片状体1叠合,即得担载后的单层a型分子筛除湿载体,如图1所示结构;最后将该单层a型分子筛除湿载体卷绕成圆柱体,即得到a型分子筛除湿蜂窝载体(转轮),如图2所示结构。下面通过具体实施例对本发明进行详细和具体的介绍,以使更好的理解本发明,但是下述实施例并不限制本发明范围。实施例1a型分子筛除湿载体的制备(1)片层玻璃纤维预处理:取一片10㎝×60cm的片状平坦型玻璃纤维a及一片10cm×100cm的片状平坦型玻璃纤维b,将其放入蒸馏水中超声洗涤2min,重复洗涤2次,洗去玻璃纤维表面及内部空隙存在的颗粒杂质;(2)a型分子筛晶种液制备:配制浓度为1.0wt%的晶种液,超声波中震荡30min,使分子筛晶种分散均匀,再将一定量的水凝胶加入到浓度为3.0wt%的晶种悬浮液中,其中晶种悬浮液的晶种和凝胶的质量比为10:1,得到浸渍用的晶种悬浮液;(3)玻璃纤维载体担载a型分子筛晶种:通过浸渍方法在玻璃纤维载体表面形成一层a型分子筛晶种,于65℃烘干,得倒晶种化载体;(4)玻璃纤维载体上二次原位水热合成:将晶种化载体继续放入盛有1.0wt%a型分子筛母液的反应釜中,将反应釜密封后置于90℃恒温烘箱下晶化2h,然后将晶种化载体利用步骤(3)中形成的a型分子筛晶种层做为生长中心或提供晶核,从分子筛母液中汲取所需要的原料,向各个方向生长填充玻璃纤维载体空隙;晶化结束后取出反应釜,用自来水急速冷却反应釜,再取出担载完毕的玻璃纤维载体,用去离子水洗涤三次,洗涤完毕后置于140℃烘箱内烘干;(5)载体卷绕成转轮:将担载完毕的平坦型玻璃纤维b加工成波纹状,再将其与另一片担载完毕的平坦型玻璃纤维a叠合,形成一层载体,将该层加工卷绕成圆柱体,即得a型分子筛除湿蜂窝载体。实施例2a型分子筛除湿载体的制备(1)片层玻璃纤维预处理:取一片10㎝×60cm的片状平坦型玻璃纤维a及一片10cm×100cm的片状平坦型玻璃纤维b,将其放入蒸馏水中超声洗涤2min,重复洗涤2次,洗去玻璃纤维表面及内部空隙存在的颗粒杂质;(2)a型分子筛晶种液制备:配制浓度为1.5wt%的晶种液,超声波中震荡20min,使分子筛晶种分散均匀,再将一定量的水凝胶加入到浓度为1.0wt%的晶种悬浮液中,其中晶种悬浮液的晶种和凝胶的质量比为8:1,得到浸渍用的晶种悬浮液;(3)玻璃纤维载体担载a型分子筛晶种:通过浸渍、喷涂或淋洗方法在玻璃纤维载体表面形成一层a型分子筛晶种,于65℃烘干,得倒晶种化载体;(4)玻璃纤维载体上二次原位水热合成:将晶种化载体继续放入盛有2.0wt%a型分子筛母液的反应釜中,将反应釜密封后置于90℃恒温烘箱下晶化5h,然后将晶种化载体利用步骤(3)中形成的a型分子筛晶种层做为生长中心或提供晶核,从分子筛母液中汲取所需要的原料,向各个方向生长填充玻璃纤维载体空隙;晶化结束后取出反应釜,用自来水急速冷却反应釜,再取出担载完毕的玻璃纤维载体,用去离子水洗涤三次,洗涤完毕后置于140℃烘箱内烘干;(5)载体卷绕成转轮:将担载完毕的平坦型玻璃纤维b加工成波纹状,再将其与另一片平坦型玻璃纤维a叠合,形成一层载体,将该层加工卷绕成圆柱体,即得a型分子筛除湿蜂窝载体。实施例3a型分子筛除湿载体的制备(1)片层玻璃纤维预处理:取一片10㎝×60cm的片状平坦型陶瓷纤维a及一片10cm×100cm的片状平坦型陶瓷纤维b,将其放入蒸馏水中超声洗涤2min,重复洗涤2次,洗去陶瓷纤维表面及内部空隙存在的颗粒杂质;(2)a型分子筛晶种液制备:配制浓度为3.0wt%的晶种液,超声波中震荡10-30min,使分子筛晶种分散均匀,再将一定量的水凝胶加入到浓度为1.5wt%的晶种悬浮液中,其中晶种悬浮液的晶种和凝胶的质量比为9:1,得到浸渍用的晶种悬浮液;(3)纤维载体担载a型分子筛晶种:通过浸渍、喷涂或淋洗方法在纤维载体表面形成一层a型分子筛晶种,于60℃烘干,得倒晶种化载体;(4)纤维载体上二次原位水热合成:将晶种化载体继续放入盛有1.5wt%a型分子筛母液的反应釜中,将反应釜密封后置于100℃恒温烘箱下晶化1h,然后将晶种化载体利用步骤(3)中形成的a型分子筛晶种层做为生长中心或提供晶核,从分子筛母液中汲取所需要的原料,向各个方向生长填充纤维载体空隙;晶化结束后取出反应釜,用自来水急速冷却反应釜,再取出担载完毕的纤维载体,用去离子水洗涤三次,洗涤完毕后置于150℃烘箱内烘干;(5)载体卷绕成转轮:将担载完毕的平坦型陶瓷纤维b加工成波纹状,再将其与另一片平坦型陶瓷纤维a叠合,形成一层载体,将该层加工卷绕成圆柱体,即得a型分子筛除湿蜂窝载体。实施例4a型分子筛除湿载体的制备(1)片层纤维预处理:取一片10㎝×60cm的片状平坦型陶瓷纤维a和一片10㎝×100cm的片状平坦型高硅氧纤维b,均放入蒸馏水中超声洗涤4min,重复洗涤2次,洗去纤维表面及内部空隙存在的颗粒杂质;(2)a型分子筛晶种液制备:配制浓度为3.0wt%的晶种液,超声波中震荡10-30min,使分子筛晶种分散均匀,再将一定量的水凝胶加入到浓度为1.5wt%的晶种悬浮液中,其中晶种悬浮液的晶种和凝胶的质量比为9:1,得到浸渍用的晶种悬浮液;(3)纤维载体担载a型分子筛晶种:通过浸渍、喷涂或淋洗方法在纤维载体表面形成一层a型分子筛晶种,于60℃烘干,得倒晶种化载体;(4)纤维载体上二次原位水热合成:将晶种化载体继续放入盛有1.5wt%a型分子筛母液的反应釜中,将反应釜密封后置于100℃恒温烘箱下晶化1h,然后将晶种化载体利用步骤(3)中形成的a型分子筛晶种层做为生长中心或提供晶核,从分子筛母液中汲取所需要的原料,向各个方向生长填充纤维载体空隙;晶化结束后取出反应釜,用自来水急速冷却反应釜,再取出担载完毕的纤维载体,用去离子水洗涤三次,洗涤完毕后置于150℃烘箱内烘干;(5)载体卷绕成转轮:将担载完毕的平坦型高硅氧纤维b加工成波纹状,再将其与另外一片平坦型陶瓷纤维a叠合,形成一层载体,将该层加工卷绕成圆柱体,即得a型分子筛除湿蜂窝载体。性能测试:一、基础数据:1、实验无机纤维纸尺寸:a):10cm(宽)x60cm(长)x0.2mm(厚),1枚;b):10cm(宽)x100cm(长)x0.2mm(厚),1枚;2、无机纤维纸板坪重:40g/m2;二、a型分子筛除湿载体的制备方法:1、用以上尺寸的无机纤维纸进行晶种担载,水热合成,得到负载有a型分子筛的无机纤维纸板;2、将负载有a型分子的无机纤维纸板b)进行波纹成型加工,与负载有a型分子筛无机纤维纸板a)进行贴合,成卷,得到圆筒状吸湿蜂窝体c)。三、以上述本发明实施例1-4所制得的a型分子筛除湿载体为检测样,以现有技术中除湿转轮为对照样,该对照样是将分子筛浸渍担载在si系或al系无机粘接剂上,然后粘结在无机纤维载体制得的除湿载体。分别对本实施例1-4的吸湿蜂窝体c)和对照样的除湿转轮的吸湿能力进行测试,具体测试方法如下:1、将吸湿蜂窝体c)用180℃的热空气进行水分脱附干燥处理20min;2、测量干燥后的吸湿蜂窝体的重量,通过计算得到无机纤维纸板的分子筛负载量(g1);3、将干燥处理后的吸湿蜂窝体暴露于相对湿度80-90%,30℃的空气中,吸湿蜂窝体吸附空气中的水分,直至蜂窝体的重量达到平衡为止,记录重量(g2);4、计算方法:a、无机纤维纸板的分子筛负载量=(g1-(0.1x0.6+0.1x1)x40)/(0.1x0.6+0.1x1);b、吸湿蜂窝体的吸水量=g2-g1;5、具体测试测试结果如图3和下表一所示:表一:各性能检测数据样品分子筛负载量(g/m2)吸湿量(g)实施例1134.347实施例2163.859实施例398.834.8实施例4114.338.9比较例1*162.534.1四、对比分析:比较例的除湿转轮担载分子筛需要添加si系或al系无机粘接剂,占到总担载物重量的30%,这些粘接剂对水分的吸附是没有积极作用的,降低了整个转轮的吸水效率;而本发明中直接将分子筛种子分散于水后担载在载体上,理论上除了玻璃纤维载体,其余均为有用的分子筛。例如,转轮基材的担载量为200kg/m3,其中比较例中粘接剂占到60kg;而采用本发明方法实施例1-4制得的a型分子筛除湿载体,理论上200kg都可以是分子筛。此外,本发明采用无机纤维做为转轮基材,材料广泛,绿色环保,且可塑性极强,可根据需要制备成任意尺寸和形态的转轮型材。综上所述,本发明使用的分子筛担载于无机纤维载体的方法简单直接,比在铝源硅源混合溶液中使载体担载分子筛的方法成本低,且该方法消除了分子筛晶体生长所需要的晶核形成过程,有利于分子筛优先在支撑体上生长,从而更容易使其结合无机纤维自身内部骨架结构形成致密的分子筛晶体层。以上对本发明的具体实施例进行了详细描述,但其只是作为范例,本发明并不限制于以上描述的具体实施例。对于本领域技术人员而言,任何对本发明进行的等同修改和替代也都在本发明的范畴之中。因此,在不脱离本发明的精神和范围下所作的均等变换和修改,都应涵盖在本发明的范围内。当前第1页12