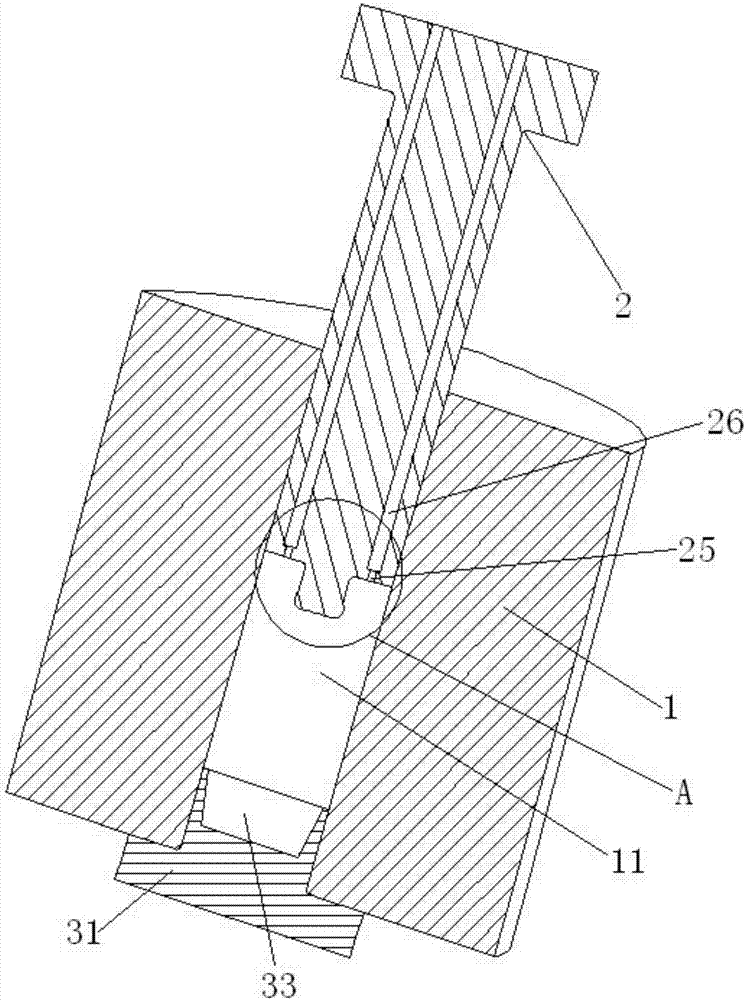
本发明涉及软钎焊料加工技术领域,尤其是涉及一种挤压模具。
背景技术:目前常规的软钎焊料丝材制造均采用正向挤压工艺,即金属流出模孔的方向与挤压力施加的方向相同的挤压方法,见示图1。其工艺为:挤压坯锭和模具达到一定的温度,挤压坯锭四周涂上少量润滑油送入模筒111,在挤压杆112的作用下,挤压坯锭填充模筒111内形成物料114,物料114经挤压模113缓慢从挤压口挤出形成线坯115,再经收线装置收线;挤压杆112快接近挤压模113时,停止挤压,模筒111内必须余留有30~50mm的物料114,退出挤压杆112,再放入第二颗挤压坯锭重复上述挤压过程,挤压过程中,后加入的挤压坯锭与前一颗挤压坯锭余留的物料114得到焊合。其具有设备简单,投资少;更换工模具简便,辅助时间短等优点。但也存在一些无法克服的不足,如挤压坯锭与模筒111内壁有相对滑动,造成模具磨损,有效挤压力仅为60~70%;在挤压过程中挤压力起伏变化,引起挤压速度的变化,造成挤压制品力学性能的变化;挤压制品极易混入润滑油、夹杂,造成表面气泡、毛刺,挤压坯锭之间的焊合处易混入挤压皮、油污等产生焊合不良的缺陷。反向挤压作为铜铝加工比较常见的技术,由于挤压筒壁与坯料表面之间无相对滑动,不产生摩擦损耗,因此模具损耗小,使用寿命长;同样的挤压比,所需的最大挤压力比正挤压可降低30~40%,因此可以实现近终型尺寸挤压制品;挤压过程压力稳定,挤压速度变化小,因此产品沿截面和长度上的组织与性能比较均匀;所需最大挤压力与挤压坯料长度无关,因而可采用长挤压坯料,提高生产效率;挤压皮、油污从挤压杆和模筒缝隙挤出,不会带入挤压制品中。因此反向挤压在降低消耗、提升产品质量和加工效率,具有明显的优势。但目前反向挤压主要用于铜铝等有色金属加工,其一个挤压坯锭挤压一根线坯,因此现有的反向挤压技术模具的结构无法达到多个挤压锭挤压成一根线坯的要求,因此并不适合软钎焊料的挤压。
技术实现要素:本发明的目的在于克服上述现有技术的不足,提供一种挤压模具,采用反向挤压技术,实现正向挤压软钎焊料线坯的效果,同时具备反向挤压的优点。为达到上述目的,本发明的技术方案是:一种挤压模具,包括模筒和挤压杆,所述模筒中心设有供挤压杆移动的挤压通道,所述挤压通道和挤压杆之间的配合间隙为0.05~0.5mm,挤压通道上与挤压杆所在侧相对的另一侧设有用来封堵挤压通道的顶端封件,所述挤压杆前端中心处设有凸出的圆柱形的挤压头,所述挤压头的长度为25~35mm,挤压头的直径为挤压杆的直径的30~50%,所述挤压杆上沿周向均布3~8个贯穿其长度方向的出丝口和出丝通道,所述出丝口和出丝通道连通且同心设置,出丝口的直径为2.5~4.5mm,出丝口的长度为出丝口的直径的0.5倍,所述出丝通道的直径是出丝口的直径的1.5倍,所述顶端封件包括配套伸入挤压通道的套接部和抵住模筒下端面的封堵部,所述套接部上与挤压头相近的端面上设有圆台形的凹槽,所述凹槽的直径从端面处往内部方向逐渐缩小,凹槽的锥度为20~25°,凹槽的最大直径比挤压杆的直径小2~6mm,凹槽的深度为30~40mm。所述挤压杆包括配套伸入挤压通道的杆体和抵住模筒上端面的杆头,所述出丝口贯穿杆体,所述出丝通道贯穿杆头,所述挤压头的直径为杆体的直径的30~50%,所述出丝口的中心线位于挤压头的外壁和杆体的外壁的中间。所述凹槽的锥度为22°,凹槽的最大直径比挤压杆的杆体的直径小4mm,凹槽的深度为35mm。所述挤压头的前端设有直径变大的扩径头,所述扩径头的直径比挤压头的直径大1~1.5mm。本发明的有益效果是:结构简单,使用方便,实现挤压锭挤压成单根线坯,线坯内在缺陷明显减少、力学性能稳定,且可以挤压近终型尺寸线坯,模具损耗较少。附图说明图1为现有技术的软钎焊料丝材制造示意图;图2为本发明的结构示意图;图3为图2中A处的放大图;图4为本发明的挤压杆的立体图;图5为本发明的顶端封件的立体图。具体实施方式下面通过实施例,并结合附图,对本发明的技术方案作进一步具体的说明。如图2~图5所示,一种挤压模具,包括模筒1和挤压杆2,所述模筒1中心设有供挤压杆2移动的挤压通道11,所述挤压通道11和挤压杆2之间的配合间隙为0.05~0.5mm,即挤压通道11和挤压杆2的杆体22之间的配合间隙为0.05~0.5mm,挤压通道11上与挤压杆2所在侧相对的另一侧设有用来封堵挤压通道11的顶端封件3,所述挤压杆2前端中心处设有凸出的圆柱形的挤压头23,所述挤压头23的长度为25~35mm,挤压头23的直径为挤压杆2的直径的30~50%,所述挤压杆2上沿周向均布3~8个贯穿其长度方向的出丝口25和出丝通道26,本发明中的出丝口25和出丝通道26均为7个,所述出丝口25和出丝通道26连通且同心设置,出丝口25的直径为2.5~4.5mm,出丝口25的长度为出丝口25的直径的0.5倍,出丝口25的长度较短,挤压锭直接从出丝口25快速挤出并沿着出丝通道26导出,所述出丝通道26的直径是出丝口25的直径的1.5倍,所述顶端封件3包括配套伸入挤压通道11的套接部32和抵住模筒1下端面的封堵部31,所述套接部32上与挤压头23相近的端面上设有圆台形的凹槽33,所述凹槽33的直径从端面处往内部方向逐渐缩小,凹槽33的锥度为20~25°,优选为22°,凹槽33的最大直径比挤压杆2的杆体22的直径小2~6mm,优选为4mm,凹槽33的深度为30~40mm,优选为35mm。所述挤压杆2包括配套伸入挤压通道11的杆体22和抵住模筒1上端面的杆头21,所述出丝口25贯穿杆体22,所述出丝通道26贯穿杆头21,最终锡基合金线坯从杆头21导出。所述挤压头23的直径为杆体22的直径的30~50%,所述出丝口25的中心线位于挤压头23的外壁和杆体22的外壁的中间。所述挤压头23的前端设有直径变大的扩径头24,所述扩径头24的直径比挤压头23的直径大1~1.5mm。本发明的工作原理是:挤压杆2沿着挤压通道11前进,由于挤压通道11和挤压杆2之间的配合间隙为0.05~0.5mm,因此在挤压过程中,挤压皮、油污等从该配合间隙挤出,不会带入挤压制品中,挤压杆2的杆体22的顶端在挤压通道11内推进到离顶端封件3的套接部32的上端面不大于1mm时停止,此时,凹槽33的底部形成一个高气压区,扩径头24的设置使得挤压头23可以带着凹槽33形状的剩余物料一起退出,该高气压区的存在使得挤压杆2上的剩余物料退出更为顺利,同时挤压杆2退出后高气压区中的气流也都泄掉,不会对下一个挤压过程造成影响,放入新的软钎焊料坯锭后再次挤压时,剩余物料与新软钎焊料坯锭可以更好的焊合形成的是同一根线坯。以上所述,仅为本发明较佳的具体实施方式,但本发明的保护范围并不局限于此,任何熟悉本技术领域的技术人员在本发明揭露的技术范围内,可轻易想到的变化或替换,都应涵盖在本发明的保护范围之内。