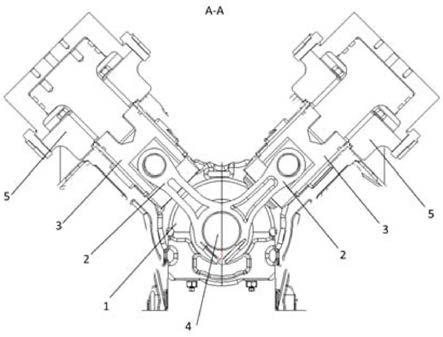
1.本发明涉及发动机试验技术领域,尤其是涉及一种精确模拟发动机主轴承孔载荷加载的机体部件试验方法。
背景技术:2.随着发动机爆发压力及功率密度不断提高,发动机零部件的可靠性面临着严酷的考验,机体作为发动机的骨架,可靠性尤其重要,在发动机研制阶段不仅需要对其进行计算分析评估,还必须通过实物应力测量及疲劳试验的验证才能保证其可靠性。
3.目前发动机机体部件试验一般采用将液压油注入燃烧室来模拟爆发压力的方法,可进行机体疲劳考核和动静态载荷下的机体应力测量。针对机体部件试验载荷的加载,是用液压油模拟发动机工作时的最高爆发压力,载荷通过连杆沿着气缸中心线传递到机体主轴承上,从而完成对机体的载荷施加。
4.但是由于目前发动机多为多缸机,轴承孔所受的真实载荷为各缸爆发压力作用下的合力,且通过发动机曲柄连杆机构运动学与动力学分析研究表明,轴承孔所受的最大载荷并非在沿气缸孔中心线方向上,所以传统的发动机机体试验载荷的施加与发动机真实工作状态下轴承孔载荷不一致,故而传统机体部件试验模拟不能反映发动机真实工作状态下机体的载荷特性。
技术实现要素:5.有鉴于此,本发明旨在提出一种精确模拟发动机主轴承孔载荷加载的机体部件试验方法,在发动机曲柄连杆机构运动学和动力学计算分析的基础上,获取曲轴不同转角下主轴承孔的载荷数据。
6.为达到上述目的,本发明的技术方案是这样实现的:
7.一种精确模拟发动机主轴承孔载荷加载的机体部件试验方法,采用机体部件疲劳试验装置对被试机体进行试验,所述机体部件疲劳试验装置包括左右两排载荷施加机构和一个非标曲轴,两排载荷施加机构的轴向中线之间呈一夹角,通过转动调节载荷施加机构来调节夹角的角度,每排载荷施加机构包括连杆、非标活塞和液压加载装置,每个液压加载装置通过非标活塞连接连杆的一端,两个连杆的另一端共同铰接于一个非标曲轴,非标曲轴轴连接于被试机体和主轴承隔板;
8.试验方法包括如下步骤:通过计算分析主轴承隔板主轴承孔最大轴承载荷方向与发动机垂向所呈角度以及载荷值f的数值,即被试机体主轴承孔最大轴承载荷方向与发动机垂向所呈角度以及载荷值f的数值。液压油由左、右排液压加载装置同时将计算所得的载荷f施加到左、右排非标活塞顶部,然后通过左、右排连杆将载荷合力传递到非标曲轴上,从而实现对被试机体的主轴承孔载荷的施加,同时主轴承隔板也受到相同载荷的施加。
9.相对于现有技术,本发明具有以下优势:
10.(1)该发动机机体部件疲劳试验方法能够准确模拟发动机真实工作状态下主轴承
孔的最大载荷。
11.(2)该发动机机体部件疲劳试验方法能够模拟发动机轴承孔不同方向和大小的的载荷。
附图说明
12.构成本发明的一部分的附图用来提供对本发明的进一步理解,本发明的示意性实施例及其说明用于解释本发明,并不构成对本发明的不当限定。在附图中:
13.图1为本发明实施例中的主轴承孔轴承载荷施加原理图;
14.图2为本发明实施例中的左右两排载荷施加机构的示意图;
15.图3为图2中a
‑
a剖视图(即本发明的结构示意图);
16.附图标记说明:
[0017]1‑
被试机体;2
‑
连杆;3
‑
非标活塞;4
‑
非标曲轴;5
‑
液压加载装置;6
‑
左3气缸;7
‑
右2气缸。
具体实施方式
[0018]
需要说明的是,在不冲突的情况下,本发明中的实施例及实施例中的特征可以相互组合。
[0019]
在本发明的描述中,需要理解的是,术语“中心”、“纵向”、“横向”、“上”、“下”、“前”、“后”、“左”、“右”、“竖直”、“水平”、“顶”、“底”、“内”、“外”等指示的方位或位置关系为基于附图所示的方位或位置关系,仅是为了便于描述本发明和简化描述,而不是指示或暗示所指的装置或元件必须具有特定的方位、以特定的方位构造和操作,因此不能理解为对本发明的限制。此外,术语“第一”、“第二”等仅用于描述目的,而不能理解为指示或暗示相对重要性或者隐含指明所指示的技术特征的数量。由此,限定有“第一”、“第二”等的特征可以明示或者隐含地包括一个或者更多个该特征。在本发明的描述中,除非另有说明,“多个”的含义是两个或两个以上。
[0020]
在本发明的描述中,需要说明的是,除非另有明确的规定和限定,术语“安装”、“相连”、“连接”应做广义理解,例如,可以是固定连接,也可以是可拆卸连接,或一体地连接;可以是机械连接,也可以是电连接;可以是直接相连,也可以通过中间媒介间接相连,可以是两个元件内部的连通。对于本领域的普通技术人员而言,可以通过具体情况理解上述术语在本发明中的具体含义。
[0021]
下面将参考附图并结合实施例来详细说明本发明。
[0022]
如图1
‑
3所示,一种精确模拟发动机主轴承孔载荷加载的机体部件试验方法,采用机体部件疲劳试验装置对被试机体1进行试验,所述机体部件疲劳试验装置包括左右两排载荷施加机构和一个非标曲轴4,两排载荷施加机构的轴向中线之间呈一夹角,通过转动调节载荷施加机构来调节夹角的角度,每排载荷施加机构包括连杆2、非标活塞3和液压加载装置5,每个液压加载装置5通过非标活塞3连接连杆2的一端,两个连杆的另一端共同铰接于一个非标曲轴4,非标曲轴4轴连接于被试机体1和主轴承隔板;
[0023]
试验方法包括如下步骤:通过计算分析主轴承隔板主轴承孔最大轴承载荷方向与发动机垂向所呈角度以及载荷值f的数值,即被试机体1主轴承孔最大轴承载荷方向与发动
机垂向所呈角度以及载荷值f的数值。液压油由左、右排液压加载装置5同时将计算所得的载荷f施加到左、右排非标活塞3顶部,然后通过左、右排连杆2将载荷合力传递到非标曲轴4上,从而实现对被试机体1的主轴承孔载荷的施加,同时主轴承隔板也受到相同载荷的施加。
[0024]
该试验方法也可通过控制左、右两缸载荷大小实现主轴承孔不同方向和大小的载荷施加。
[0025]
实施例:
[0026]
以某发动机机体为例,通过计算分析得到机体主轴承孔最大轴承载荷方向与发动机垂向呈22
°
角,载荷值为f。
[0027]
试验采用主隔板临近交错两缸同时加载的方式,加载缸为左3气缸6、右2气缸7,试验承载隔板为第二主轴承隔板,通过调节左3气缸载荷f2,右2气缸载荷f1,使加载在第二主隔板主轴承孔上的载荷方向为与发动机垂向22
°
角,载荷值为f,模拟发动机实际工作中主轴承孔承受的最大载荷,基本载荷施加原理见图1所示,具体试验装置组成见图2
‑
3所示。
[0028]
以上所述仅为本发明的较佳实施例而已,并不用以限制本发明,凡在本发明的精神和原则之内,所作的任何修改、等同替换、改进等,均应包含在本发明的保护范围之内。