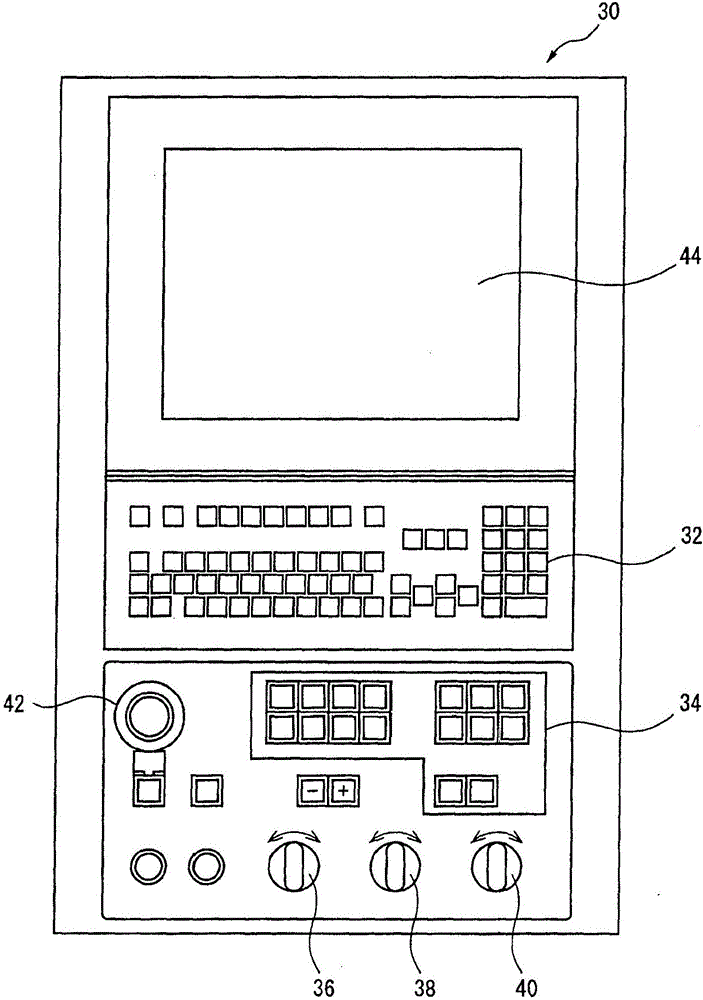
本发明涉及机床的操作人员能够容易地计算加工条件,防止由操作人员所致的计算错误和输入错误的机床的控制装置。
背景技术:
:在机床的进给轴装置中,将进给速度、主轴旋转速度等加工条件记载于加工程序,但实际上,操作人员有时必须在工厂等的现场基于经验等将进给速度、主轴旋转速度等直接输入到NC装置,或者在机床的附近制作或者编辑NC程序。这样,作为操作人员在工厂等的现场制作或者编辑NC程序时应输入到NC装置的数据,有操作人员必须使用台式计算器来计算数值的数据。另外,关于计算所需的数据、参数,操作人员还有时必须从规格书等通过目视来选择并输入到台式计算器等,作业烦杂且还成为向台式计算器的数据的输入错误的原因。另外,即使在将计算结果输入到NC装置时,也有产生输入错误的可能性。为了防止这样的人为的错误,在专利文献1中,记载有具备保持工具的直径或者半径、工具的刃数、工具长度等工具数据的工具数据库,根据当前的进给速度以及主轴旋转速度,计算并显示周速和每一刃的进给量的机床的NC装置。另外,在专利文献2中,记载有在设定显示装置中进行数据的设定、显示的数值控制装置中,使得在显示画面的窗口内具有台式计算器的功能的数值控制装置。专利文献1:日本特开平11-296214号公报专利文献2:日本实开平05-2207号公报技术实现要素:在专利文献1的发明中,能够计算工具的切刃的周速和每一刃的进给量,但作为加工条件,无法计算切削速度、进给速度、主轴旋转速度、尖端(cusp)高度、周期进给(pickfeed)量、切屑去除量,无法防止人为的输入错误、计算错误。在专利文献2的发明中,台式计算器显示于显示画面中,但操作人员必须通过手动操作来输入,所以仍无法防止人为的输入错误、计算错误。进而,在引用文献1、2的发明中,无法将机床的当前的坐标值作为输入数据取入、或者将计算结果作为自变量交接给加工程序,无法防止人为的输入错误。本发明将解决这样的以往技术的问题作为技术课题,其目的在于提供一种操作人员能够容易地计算加工条件,防止了操作人员所致的计算错误和输入错误的机床的控制装置。为了达成上述目的,根据本发明,提供一种机床的控制装置,根据加工程序加工工件,其特征在于包括:数据库,储存有与计算的种类对应的计算式和为了执行该计算而所需的参数的种类;输入部,选择计算的种类;以及显示部,根据通过所述输入部选择的计算的种类,显示应输入的参数。根据本发明,将与计算的种类对应的计算式和为了执行该计算而所需的参数的种类储存到数据库中,当操作人员通过输入部选择计算的种类后,根据选择的计算的种类,将应输入的参数显示于显示部中,所以能够防止操作人员所致的人为的输入错误、计算错误。附图说明图1是本发明的优选的实施方式的机床的控制装置的略示框图。图2是本发明的实施方式中的机床的操作盘的概略正面图。图3是示出在图2的操作盘的显示画面中显示的台式计算器的一个例子的图。图4是示出作为加工条件用于计算切削速度的在图2的操作盘的显示画面中显示的画面的一个例子的图。图5是示出作为加工条件用于计算每一刃的进给量的在图2的操作盘的显示画面中显示的画面的一个例子的图。图6是示出作为加工条件用于计算进给速度的在图2的操作盘的显示画面中显示的画面的一个例子的图。图7是示出作为加工条件用于计算主轴旋转速度的在图2的操作盘的显示画面中显示的画面的一个例子的图。图8是示出作为加工条件用于计算切削速度的在图2的操作盘的显示画面中显示的画面的一个例子的图。图9是示出作为加工条件用于计算尖端高度的在图2的操作盘的显示画面中显示的画面的一个例子的图。图10是示出作为加工条件用于计算周期进给量的在图2的操作盘的显示画面中显示的画面的一个例子的图。图11是示出作为加工条件用于计算尖端高度的在图2的操作盘的显示画面中显示的画面的其他例的图。图12是示出作为加工条件用于计算切屑去除量(从工件去除的材料的量)的在图2的操作盘的显示画面中显示的画面的一个例子的图。图13是示出用于计算坐标系的在图2的操作盘的显示画面中显示的画面的一个例子的图。图14是示出表示用于取入当前的X、Y坐标的命令的在图13的画面内显示的图标的一个例子的图。图15是示出表示用于取入当前的X、Y或者Z坐标的命令的在图13的画面内显示的图标的一个例子的图。图16是示出表示用于计算2点之间的中点的命令的在图13的画面内显示的图标的一个例子的图。图17是示出表示用于计算2点之间的斜率的命令的在图13的画面内显示的图标的一个例子的图。图18是示出表示用于计算2个直线的交点的命令的在图13的画面内显示的图标的一个例子的图。图19是示出表示用于计算旋转后的坐标的命令的在图13的画面内显示的图标的一个例子的图。图20是示出表示用于计算宽度的命令的在图13的画面内显示的图标的一个例子的图。(符号说明)10:控制装置;12:输入部;12a:输入框;12b:计算选择部;14:运算部;16:数据库;18:存储部;20:显示部。具体实施方式以下,参照附图,说明本发明的优选的实施方式。参照作为本发明的优选的实施方式的机床的控制装置的略示框图的图1,控制装置10具备输入部12、运算部14、数据库16、存储部18以及显示部20,作为主要的构成要素。输入部12通过在由触摸面板等形成的显示部20中显示的画面构成,如后所述,包括输入数值的输入框12a以及由下拉列表构成的计算选择部12b。在数据库16中,与计算的种类关联起来储存了各种计算式。进而,在数据库16中,将工具直径D、工具长度L、刃数N、每一刃的进给量fz、进给速度F、旋转速度S等参数与工具编号关联起来储存。当在计算选择部12b中选择计算的种类后,从数据库16读出对应的计算式、必要的参数并送出到运算部14,在该运算部14中进行计算。将计算结果储存到存储部18中,能够从该存储部18送出到例如NC装置(未图示)。图2示出在机床的控制装置中所配置的操作盘的正面图。参照图1、2,操作盘30包括形成图1的显示部20的显示面板44。本实施方式的显示面板44能够由可通过接触画面来选择期望的部分的触摸面板形成,在显示面板44中显示构成输入部12的画面。操作盘30包括键输入部32。在键输入部32中,配置有多个键开关。通过按压键输入部32的键开关,能够输入预定的数字、文字。另外,操作盘30包括进行预定的操作的选择的操作开关部34、进行覆写值的设定的覆写设定部36~40以及紧急停止按钮42。覆写设定部36~40例如能够设定主轴的旋转速度的覆写值、加工的进给速度的覆写值等。图3示出在显示部20(显示面板44)中显示的台式计算器。能够在该显示模式中,操作人员进行任意的计算。在图4中,作为计算的种类示出用于根据主轴旋转速度S(min-1)和工具直径(mm)计算切削速度∨(m/min)的画面100。当操作人员通过下拉列表98选择切削速度(m/min)后,显示计算式和作为计算所需的参数的工具直径以及主轴旋转速度。进而,在各参数下显示输入框102、104。当将适合的数值作为工具直径D(mm)以及主轴旋转速度S(min-1)输入到输入框102、104后,通过∨=(D×π×S)/1000的计算式,计算切削速度∨(m/min),在输出框94中显示计算结果。在图5中,作为计算的种类示出用于根据主轴旋转速度S(mim-1)、刃数Z以及进给速度F(mm/min)计算每一刃的进给量fz(mm/tooth)的画面110。当操作人员通过下拉列表98选择每一刃的进给量(mm/tooth)后,显示计算式和作为计算所需的参数的主轴旋转速度、刃数以及进给速度。进而,在各参数下显示输入框112、114、116。当将适合的数值作为进给速度F(mm/min)、刃数Z以及主轴旋转速度S(min-1)输入到输入框112、114、116后,通过fz=F/(Z×S)的计算式,计算每一刃的进给量fz(mm/tooth),在输出框94显示计算结果。在图6中,作为计算的种类示出用于根据每一刃的进给量(mm/tooth)、主轴旋转速度S(min-1)以及刃数Z计算进给速度F(mm/min)的画面120。当操作人员通过下拉列表98选择进给速度(mm/min)后,显示计算式和作为计算所需的参数的每一刃的进给量、主轴旋转速度以及刃数。进而,在各参数下显示输入框122、124、126。当将适合的数值作为每一刃的进给量(mm/tooth)、刃数Z以及主轴旋转速度S(min-1)输入到输入框122、124、126后,通过F=fz×Z×S的计算式,计算进给速度F(mm/min),在输出框94中显示计算结果。在图7中,作为计算的种类示出用于根据切削速度∨(m/min)以及工具直径D(mm)计算主轴旋转速度S(min-1)的画面130。当操作人员通过下拉列表98选择主轴旋转速度(min-1)后,显示计算式和作为计算所需的参数的切削速度以及工具直径。进而,在各参数下显示输入框132、134。将适合的数值作为切削速度∨(m/min)以及工具直径D(mm)输入到输入框132、134后,通过S=(1000×∨)/(D×π)的计算式计算主轴旋转速度S(min-1),在输出框94中显示计算结果。在图8中,作为计算的种类示出用于根据主轴旋转速度S(min-1)以及工具直径D(mm)计算切削速度∨(m/min)的画面140。当操作人员通过下拉列表98选择切削速度(m/min)后,则显示计算式和作为计算所需的参数的主轴旋转速度以及工具直径。进而,在各参数下显示输入框142、144。当将适合的数值作为工具直径D(mm)以及主轴旋转速度(min-1)输入到输入框142、144后,通过∨=(D×π×S)/1000的计算式,计算切削速度∨(m/min),在输出框94中显示计算结果。在图9中,作为计算的种类示出用于根据周期进给量P(mm)以及球头立铣刀的前端的球头半径R(mm)计算尖端高度H(mm)的画面150。当操作人员通过下拉列表98选择尖端高度(mm)后,显示计算式和作为计算所需的参数的周期进给量以及球头半径。进而,在各参数下显示输入框152、154。当将适合的数值作为周期进给量P(mm)以及球头半径R(mm)输入到输入框152、154后,通过H=(R2-P2/4)1/2的计算式,计算尖端高度H(mm),在输出框94中显示计算结果。在图10中,作为计算的种类示出用于根据尖端高度H(mm)以及球头半径R(mm)计算周期进给量P(mm)的画面160。当操作人员通过下拉列表98选择周期进给量P(mm)后,显示计算式和作为计算所需的参数的尖端高度以及球头半径。进而,在各参数下显示输入框162、164。当将适合的数值作为尖端高度(mm)以及球头半径R(mm)输入到输入框162、164后,通过P=(8×H×R-4H2)1/2的计算式,计算周期进给量P(mm),在输出框94中显示计算结果。在图11中,作为计算的种类示出用于根据每一刃的进给量fz(mm/tooth)以及球头半径R(mm)计算尖端高度H(mm)的画面170。当操作人员通过下拉列表98选择尖端高度(mm)后,显示计算式和作为计算所需的参数的每一刃的进给量以及球头半径。进而,在各参数下显示输入框172、174。当将适合的数值作为进给量fz(mm/tooth)以及球头半径R(mm)输入到输入框172、174后,通过H=R-(R2-fz2/4)1/2的计算式,计算尖端高度(mm),在输出框94中显示计算结果。在图12中,作为计算的种类示出有用于根据切削幅度W(mm)、切入深度DP(mm)以及进给速度F(mm/min)计算切屑去除量MRR(cm3/min)的画面180。当操作人员通过下拉列表98选择切屑去除量MRR(cm3/min)后,显示计算式和作为计算所需的参数的切削幅度、切入深度以及进给速度。进而,在各参数下显示输入框182、184、186。当将适合的数值作为切削幅度W(mm)、切入深度DP(mm)以及进给速度F(mm/min)输入到输入框182、184、186后,通过MRR=W×DP×F/1000的计算式,计算MRR(cm3/min),在输出框94中显示计算结果。将这样计算出的加工条件储存到控制装置10的存储部18中,例如,能够输出到NC装置或者在操作人员编辑加工程序时作为加工程序内的自变量交接。在作为自变量向加工程序交接时,能够在作为计算结果的数值中附加表示该数值的意义的字母(X、Y、Z、S、F等)或者根据需要附加小数点而调整有效位数。进而,能够用于切削阻力N(kgf)的计算那样的更复杂的计算。N=(1900×Ad×Rd×fz×Z×K)/D×Q其中,Ad:轴向的切入量(mm)Rd:半径方向的切入量(mm)fz:每一刃的进给量(mm/tooth)Z:刃数K:表1所示的材质系数D:工具直径(mm)Q:表2所示的切削效率[表1]材质JIS(ANSI)K镍铬合金181.7SKD61(H13)1.6~1.7NAK80(PrehardenedSteel)1.2~1.7NAK55(PrehardenedSteel)1.1~1.3SUS304(ASTM;S30300)1.0~1.1S55C(1055)1Ti-6AI-4V0.8~1.1FC25(ASTM;classNo.40)0.8~0.9A5052(5052)0.3~0.4[表2]fz(mm/tooth)Q0.1240.2310.3360.438将表1的材质系数、表2所示的针对每一刃的进给量fz的切削效率那样的数据储存到数据库16,通过运算部14适宜地调出,用于计算。操作人员能够决定加工条件以使这样计算出的切削阻力N进入到容许范围内。参照图13,其示出用于计算工件的坐标的画面。当打开设定机床的坐标系的画面后,在显示部20中显示在图13的上段所示那样的画面200。画面200在左侧配置图标,在各图标的右侧显示计算内容的简单说明。作为一个例子,图13的上段表示选择了计算通过2点的直线的斜率而取得的斜率取得的图标,下段表示通过图标的选择显示斜率取得画面210。斜率取得画面210包括用于选择成为所计算的斜率C的基准的轴的轴选择部212和输入2个点的XY坐标的坐标输入部214、216。当输入任意的2点的X、Y坐标后,通过C=ATAN(y2-y1)/(x2-x1)的计算式,计算通过该2点的直线的斜率C,显示计算结果。将该斜率C的值储存于存储部18中。图14示出取入当前的XY坐标的XY坐标取得图标220。当点击XY坐标取得图标220后,与图13的下段同样地显示坐标取得画面,在那里能够取入坐标。机床的X轴标尺、Y轴标尺等的位置传感器(未图示)的读取例如被取入到数据库16的预定的存储区域。图15示出选择并取入当前的X、Y或者Z坐标中的一个的一坐标取得图标230。当点击一坐标取得图标230后,与图13的下段同样地显示坐标取得画面,在那里能够取入坐标。机床的X轴标尺、Y轴标尺、Z轴标尺等位置传感器(未图示)中的相应的轴的读取例如被取入到数据库16的预定的存储区域。图16示出计算并取入2点之间的中点的中点取得图标240。图17示出在上述斜率取得画面210中显示的图标211。图18示出取得2个直线的交点的交点取得图标250。在XY平面内通过2点(x1、y1)、(x2、y2)的直线L1和通过其他2点(x3、y3)、(x4、y4)的直线L2的交点PC(X、Y),在设A1=(y2-y1)/(x2-x1)A3=(y4-y3)/(x4-x3)时,根据下式计算:X=(A1×x1-y3-A3×x3+y3)/(A1-A3)Y=A1×(X-x1)+y1例如,能够使在主轴前端安装的触摸传感器接触到工件的期望位置,来取入4点(x1、y1)、(x2、y2)、(x3、y3)、(x4、y4)的坐标值。图19示出取得使工件旋转之后的坐标的旋转后坐标取得图标260。根据下式,计算绕X轴旋转角度θ之后的坐标PR(X、Y、Z)。X=xY=cosθ×y-sinθ×zZ=sinθ×y+cosθ×z根据下式,计算绕Y轴旋转角度θ之后的坐标PR(X、Y、Z)。X=cosθ×x+sinθ×zY=yZ=-sinθ×x+cosθ×z根据下式,计算绕Z轴旋转角度θ之后的坐标PR(X、Y、Z)。X=cosθ×x-sinθ×yY=sinθ×x+cosθ×yZ=z能够使触摸传感器接触到工件的期望位置,而取入当前的坐标值(x、y、z)。图20示出取得工件的X轴向、Y轴向或者Z轴向的距离的宽度取得图标270。通过下式,计算宽度L。Lx=|x2+x1|Ly=|y2+y1|Lz=|z2+z1|能够使触摸传感器接触到工件的期望位置,而取入当前的坐标值(x、y)。当前第1页1 2 3