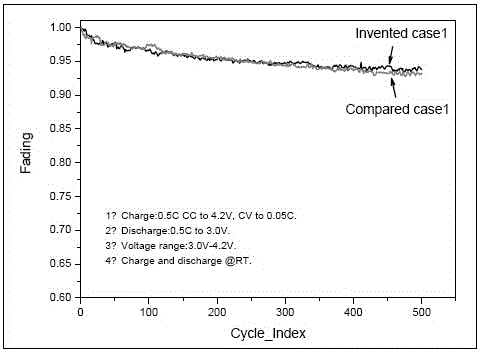
本发明涉及锂离子电池,尤其是一种导电剂组合型锂离子电池正极极片及其制作方法。
背景技术:
:锂离子电池是一种具有较高能量密度和电压的储能器件,该器件需要使用两种的电极材料一是锂离子活性物质组成的极片,称为正极,另一电极为炭材料组成的极片,称为负极,然后使用PE或PP材质隔离膜隔离这两个电极,电解质采用含有上述含锂离子的化合物。在充放电过程中,锂离子在正极电极活性物质晶格插入或脱出,对应电极的炭材料则发生脱出或插入。在锂离子从电极晶格插入脱出过程中,在正极和负极均发生电荷的转移,分别传导至各自集流体。而负极炭材料和正极锂离子材料电子电导性能有限,尤其是正极锂离子材料,在电极制作过程中需要添加导电剂,增加电导性,提高放电性能。目前,正极极片普遍使用CB和CNTs作为导电材料,GNPs作为导电剂在锂离子电池中的应用也有了阶段性进展,然而各自有优缺点:CB在结构上为初级粒子。具有良好的导电性、价格低廉、原料易得的诸多优点。然而,CB通常是以凝聚体形式存在,其本身作为零维球状的填料在颗粒间不易连接搭建形成导电网络,导电系数在10S/cm,因此,CB的添加量一般要求比较大,对于提高正极极片的能量密度是不利的。CNTs是一维纳米材料,具有优良的导电性能,导电系数达到1000S/cm,均匀分散在锂离子正极活性材料之间,可以形成较好的导电网络,但是其与正极活性材料,粘结剂之间形成的敷料在集流体上压实后,在之后装配成电池进行充电,锂离子脱出晶体过程中,容易产生比添加入CB导电剂更大的厚度膨胀率。总的说来,CNTs的刚性极高,且管状结构不容易被应力轻易破坏。当施加于CNTs表面的应力撤去,其结构会有逐渐恢复初始状态的趋势。GNPs是由单层或多层石墨组成的厚度为纳米级、直径为微米级的石墨薄片,属于二维纳米材料,比表面积大。在平行于碳原子层的方向具有良好的导电性能,导电系数可达到500S/cm以上。在正极活性物质之间容易搭载形成导电网络。网面可以有效扩大GNPs与正极活性材料颗粒的导电接触面积,从而有效提高了导电性能,减少电池内阻。在获得优异倍率和低温放电性能的同时,存在首次库伦效率较低,压实密度低,由于较强范德华力作用而易团聚的缺点。技术实现要素:本发明所要解决的技术问题是提供一种导电剂组合型锂离子电池正极极片及其制作方法,克服现有技术中导电剂CB、CNTs和GNPs在锂离子电池正极应用中各自存在的缺点与问题,提供的正极极片能量密度高,极片膨胀率低,库伦效率高,压实高。为解决上述技术问题,本发明的技术方案是:一种导电剂组合型锂离子电池正极极片,包括集流体及粘附在集流体上的正极涂膜,所述正极涂膜的组分包括正极活性材料、导电剂和粘结剂;所述导电剂为CB和CNTs组合、CB和GNPs组合、CNTs和GNPs组合或CB、CNTs和GNPs组合。制得的组合型导电剂分散在正极活性材料颗粒的间隙中形成三维复合导电网络结构,增强了活性物质之间的相互接触,提高了电极整体的电导性,同时,零维球状碳材料,一维纳米碳材料,二维纳米碳材料组合可以使各组分优势互补,发挥了协同效应。当把组合导电剂添加在正极活性物质中,CB可填充纳米级的空隙,CNTs可以实现活性物质间微米级的连接,GNPs可以使电极形成整体网络的连接,CB,CNTS和CNPs协同作用形成的导电网络,可以极大提升正极活性物质的导电性,提升电极压实密度,电导性,首次效率等性能,进而提升了电池的整体性能。作为改进,所述正极涂膜组成及质量比例为:正极活性材料92.0~99.3%,粘结剂0.5~4.0%,导电剂0.2~6.0%。作为改进,所述CB、CNTs和GNPs的状态均为粉末或已经分散均匀的分散浆料。作为改进,所述导电剂CB和CNTs组合中,CB与CNTs质量比例为(1:20)~(10:1),优选(1:5)~(5:1);所述导电剂CB和GNPs组合中,CB与GNPs质量比例为(1:20)~(10:1),优选(1:5)~(5:1);所述导电剂CNTs和GNPs组合中,CNTs与GNPs质量比例为(1:20)~(20:1),优选(1:1)~(5:1);所述导电剂CB、CNTs和GNPs组合中,CB与(CNTs+GNPs)质量比例为(1:20)~(10:1),其中CNTs与GNPs质量比例(1:20)~(20:1)。作为改进,所述正极活性材料为钴酸锂、镍钴锰酸锂、镍钴铝酸锂、锰酸锂、磷酸亚铁锂中的一种或两种。作为改进,所述粘结剂为聚偏氟乙烯;所述溶剂为N-甲基吡咯烷酮。作为改进,所述CB为乙炔黑、SuperP或科琴黑。作为改进,所述CNTs为单壁碳纳米管、双壁碳纳米管或多壁碳纳米管。作为改进,所述GNPs为单层石墨烯、双层石墨烯、少层石墨烯或多层石墨烯。为解决上述技术问题,本发明另一技术方案是:一种导电剂组合型锂离子电池正极极片制作方法,包括以下步骤:(1)将粘结剂加入溶剂中搅拌混合均匀;(2)向溶液中加入CB、CNTs、GNPs的两种或三种导电剂组合并搅拌混合均匀;(3)加入正极活性材料搅拌混合均匀,得到正极浆料;(4)将正极浆料涂覆于集流体上,经过烘烤、辊压后,制得锂离子电池所用正极极片。所述粘结剂不限于将粘结剂分散于溶剂之后再加入导电剂进行分散均匀,也可以提前分散于CB,CNTs,GNPs的至少一种导电剂分散浆料或者合浆中。附图说明图1为实施例1CB-CNTs组合导电剂正极极片与对比例1CNTs正极极片制作的电池倍率放电对比曲线图。图2为实施例1CB-CNTs组合导电剂正极极片与对比例1CNTs正极极片制作的电池循环曲线图。图3为实施例2CNTs-GNPs组合导电剂正极极片与对比例2GNPs正极极片制作的电池倍率放电对比曲线图。图4为实施例2CNTs-GNPs组合导电剂正极极片与对比例2GNPs正极极片制作的电池循环曲线图。图5a为实施例3CB-CNTs-GNPs组合导电剂正极极片电池倍率放电曲线图。图5b为对比例3CB-GNPs正极极片制作的电池倍率放电曲线图。图5c实施例3与对比例3电池倍率放电对比曲线图。图6为实施例3CB-CNTs-GNPs组合导电剂正极极片与对比例3CB-GNPs正极极片制作的电池循环曲线图。图7为实施例4CB-GNPs组合导电剂正极极片与对比例4CB正极极片制作的电池倍率放电对比曲线图。图8为实施例4CB-GNPs组合导电剂正极极片与对比例4CB正极极片制作的电池循环曲线图。具体实施方式下面结合说明书附图对本发明作进一步说明。实施例1一种导电剂组合型锂离子电池正极极片,包括集流体及粘附在集流体上的正极涂膜,所述正极涂膜的组分包括正极活性材料、导电剂和粘结剂。所述导电剂为CB和CNTs组合。所述正极活性材料为钴酸锂。所述粘结剂为聚偏氟乙烯。所述溶剂为N-甲基吡咯烷酮。所述CNTs为单壁碳纳米管。所述CB为SuperP。正极极片的制备方法:将8.7克聚偏氟乙烯(法国苏威5130)溶解在约150克N-甲基吡咯烷酮溶剂中制得粘结剂溶液;然后加入122.2克CNTs分散浆料(CNTs含量5%,镇江天奈)和3.6克SuperP,充分混合均匀;然后将1000克钴酸锂(天津巴莫)加入上述溶液中,充分搅拌混合均匀制得正极浆料;用涂布机将该浆料均匀涂布于16微米铝箔两面,经过通道烘烤,然后在辊压机器上压实,得到压实密度为4.15克/立方厘米的正极极片。锂离子电池的制备:正极使用本实施例制得的极片;负极使用上海杉杉MHE材料涂敷的极片,隔膜使用日本旭化成生产的16微米厚隔膜;电解液使用东莞杉杉生产的电解液;制备434369型号软包聚合物锂离子电池(设计电池容量1600mAh)。比较例1按照实施例1的方法制备正极极片,不同的是,不加入SuperP成分,选用194.2克CNTs分散浆料(CNTs含量5%,镇江天奈)加入粘结剂溶液中,充分混合均匀,然后将1000克钴酸锂(天津巴莫)加入上述溶液中,充分搅拌混合均匀制得正极浆料。锂离子电池的制备:正极使用本实施例制得的极片;负极使用上海杉杉MHE材料涂敷的极片,隔膜使用日本旭化成生产的16微米厚隔膜;电解液使用东莞杉杉生产的电解液;制备434369型号软包聚合物锂离子电池(设计电池容量1600mAh)。实施例1与比较例1制得的电池性能测试对比:①正极片厚度膨胀后压实密度,单位g/cm3辊压卷绕半电满电实施例14.154.124.003.93对比例14.154.073.803.71②倍率对比曲线如图1所示。③循环曲线如图2所示。实施例1通过添加0.35wt%的SuperP和0.6wt%的CNTs(不包含除CNTs外成分),形成CB-CNTs导电剂组合,与对比例1添加量0.95wt%的CNTs结果比较,发现实施例1有效提高正极片在卷绕,半电和满电阶段极片压实密度。倍率放电性能上,实施例1较对比例1稍差,如图1所示。循环性能上,实施例1较对比例1容量保持率稍高,如图2所示。实施例2一种导电剂组合型锂离子电池正极极片,包括集流体及粘附在集流体上的正极涂膜,所述正极涂膜的组分包括正极活性材料、导电剂和粘结剂。所述导电剂为CNTs和GNPs组合。所述正极活性材料为镍钴锰酸锂。所述粘结剂为聚偏氟乙烯。所述溶剂为N-甲基吡咯烷酮。所述CNTs为单壁碳纳米管。所述GNPs为双层石墨烯。正极极片的制备方法:将8.65克聚偏氟乙烯(苏威5130)溶解在约250克N-甲基吡咯烷酮溶剂中制得粘结剂溶液;然后加入111.9克CNTs分散浆料(CNTs含量5%,镇江天奈)和61.0克GNPs分散浆料(GNPs含量5%,宁波墨西),充分混合均匀;然后将1000克镍钴锰酸锂(深圳天骄)加入上述溶液中,充分搅拌混合均匀制得正极浆料;用涂布机将该浆料均匀涂布于16微米铝箔两面,经过通道烘烤,然后在辊压机器上压实,得到压实密度为3.72克/立方厘米的正极极片。锂离子电池的制备:正极使用本实施例制得的极片;负极使用上海杉杉FSN-1材料涂敷的极片,隔膜使用日本旭化成生产的16微米厚隔膜;电解液使用广州天赐生产的电解液;制备434369型号软包聚合物锂离子电池(设计电池容量1600mAh)。比较例2按照实施例2的方法制备正极极片,不同的是,不加入CNTs成分,选用172.9克GNPs分散浆料(GNPs含量5%,宁波墨西)加入粘结剂溶液中,充分混合均匀;然后将1000克镍钴锰酸锂(深圳天骄)加入上述溶液中,充分搅拌混合均匀制得正极浆料。锂离子电池的制备:正极使用本实施例制得的极片;负极使用上海杉杉FSN-1材料涂敷的极片,隔膜使用日本旭化成生产的16微米厚隔膜;电解液使用广州天赐生产的电解液;制备434369型号软包聚合物锂离子电池(设计电池容量1600mAh)。实施例2与比较例2制得的电池性能测试对比:①平均克容量与内阻平均正极活性物质克容量平均内阻实施例2156.7mAh/g27.8mΩ对比例2154.4mAh/g28.5mΩ②倍率对比曲线如图3所示。③循环曲线如图4所示。实施例2通过添加0.55wt%的CNTs(不包含除CNTs外成分)和0.3wt%的GNPs(不包含除GNPs外成分),形成CNTs-GNPs导电剂组合,与对比例2添加量0.85wt%的GNPs结果比较,发现实施例2平均正极活性物质克容量比对比例2的高,而电池平均内阻比对比例2低。倍率放电性能上,实施例2较对比例2放电率高,如图3所示。循环性能上,实施例2较对比例2容量保持率高,如图4所示。实施例3一种导电剂组合型锂离子电池正极极片,包括集流体及粘附在集流体上的正极涂膜,所述正极涂膜的组分包括正极活性材料、导电剂和粘结剂。所述导电剂为CB、CNTs和GNPs组合。所述正极活性材料为镍钴铝酸锂。所述粘结剂为聚偏氟乙烯。所述溶剂为N-甲基吡咯烷酮。所述CB为SuperP。所述CNTs为单壁碳纳米管。所述GNPs为多层石墨烯。正极极片的制备方法:将8.6克聚偏氟乙烯(苏威5130)溶解在约250克N-甲基吡咯烷酮溶剂中制得粘结剂溶液;然后加入1.5克SuperP,60.8克CNTs分散浆料(CNTs含量5%,镇江天奈),以及20.2克GNPs分散浆料(GNPs含量5%,宁波墨西),充分混合均匀;然后将1000克镍钴铝酸锂加入上述溶液中,充分搅拌混合均匀制得正极浆料;用涂布机将该浆料均匀涂布于16微米铝箔两面,经过通道烘烤,然后在辊压机器上压实,得到压实密度为3.5克/立方厘米的正极极片。锂离子电池的制备:正极使用本实施例制得的极片;负极使用上海杉杉MHE材料涂敷的极片,隔膜使用日本旭化成生产的16微米厚隔膜;电解液使用东莞杉杉生产的电解液;制备434369型号软包聚合物锂离子电池(设计电池容量1600mAh)。比较例3按照实施例3的方法制备正极极片,不同的是,不加入CNTs成分,选用1.5克SuperP,81.0克GNPs分散浆料(GNPs含量5%,宁波墨西)加入粘结剂溶液中,充分混合均匀;然后将1000克镍钴铝酸锂加入上述溶液中,充分搅拌混合均匀制得正极浆料;用涂布机将该浆料均匀涂布于16微米铝箔两面,经过通道烘烤,然后在辊压机器上压实,得到压实密度为3.5克/立方厘米的正极极片。锂离子电池的制备:正极使用本实施例制得的极片;负极使用上海杉杉MHE材料涂敷的极片,隔膜使用日本旭化成生产的16微米厚隔膜;电解液使用东莞杉杉生产的电解液;制备454093型号软包聚合物锂离子电池(设计电池容量2000mAh)。实施例3与比较例3制得的电池性能测试对比:①平均克容量与内阻平均正极活性物质克容量平均内阻实施例3182.5mAh/g24.1mΩ对比例3181.1mAh/g26.3mΩ②实施例3倍率放电曲线如图5a所示,对比例3倍率放电曲线如图5b所示,实施例3与对比例3倍率对比曲线如图5c所示。③循环曲线如图6所示。实施例3通过添加0.15wt%的SuperP和0.3wt%的CNTs(不包含除CNTs外成分)和0.1wt%的GNPs(不包含除GNPs外成分),形成CB-CNTs-GNPs导电剂组合,与对比例3添加量0.15wt%的SuperP和0.4wt%的GNPs结果比较,发现实施例3平均正极活性物质克容量比对比例3的高,而电池平均内阻比对比例3低。倍率放电性能上,实施例3较对比例3放电率高,如图5c所示。循环性能上,实施例3较对比例3容量保持率高,如图6所示。实施例4一种导电剂组合型锂离子电池正极极片,包括集流体及粘附在集流体上的正极涂膜,所述正极涂膜的组分包括正极活性材料、导电剂和粘结剂。所述导电剂为CB和GNPs组合。所述正极活性材料为镍钴锰酸锂与锰酸锂按照1比4质量比形成的混合剂。所述粘结剂为聚偏氟乙烯。所述溶剂为N-甲基吡咯烷酮。所述CB为SuperP。所述GNPs为双层石墨烯。正极极片的制备方法:将78.0克聚偏氟乙烯(苏威5130)溶解在约450克N-甲基吡咯烷酮溶剂中制得粘结剂溶液;然后加入366.6克GNPs分散浆料(GNPs含量5%,宁波墨西)和10.8克SuperP,充分混合均匀;然后将3000克镍钴锰酸锂和锰酸锂质量比为1比4的混合剂加入上述溶液中,充分搅拌混合均匀制得正极浆料;用涂布机将该浆料均匀涂布于16微米铝箔两面,经过通道烘烤,然后在辊压机器上压实,得到压实密度为3.1克/立方厘米的正极极片。锂离子电池的制备:正极使用本实施例制得的极片;负极使用上海杉杉MHE材料涂敷的极片,隔膜使用日本旭化成生产的16微米厚隔膜;电解液使用张家港国泰华荣生产的电解液;制备7570139型号软包聚合物锂离子电池(设计电池容量5000mAh)。比较例4按照实施例4的方法制备正极极片,不同的是,不加入GNPs成分;选用29.1克SuperP加入粘结剂溶液中,充分混合均匀;然后将3000克镍钴锰酸锂和锰酸锂质量比为1比4的混合剂加入上述溶液中,充分搅拌混合均匀制得正极浆料;用涂布机将该浆料均匀涂布于16微米铝箔两面,经过通道烘烤,然后在辊压机器上压实,得到压实密度为3.1克/立方厘米的正极极片。锂离子电池的制备:正极使用本实施例制得的极片;负极使用上海杉杉FSN-1材料涂敷的极片,隔膜使用日本旭化成生产的16微米厚隔膜;电解液使用张家港国泰华荣生产的电解液;制备7570139型号软包聚合物锂离子电池(设计电池容量5000mAh)。(2)实施例4与比较例4制得的电池性能测试对比:①平均克容量与内阻平均正极活性物质克容量平均内阻实施例4105.3mAh/g15.1mΩ对比例4106.1mAh/g16.2mΩ②倍率对比曲线如图7所示。③循环曲线如图8所示。实施例4通过添加0.35wt%的SuperP和0.59wt%的GNPs(不包含除GNPs外成分),形成CB-CNTs-GNPs导电剂组合,与对比例4添加量0.94wt%的SuperP结果比较,发现实施例4平均正极活性物质克容量比对比例4的低,但电池平均内阻比对比例4低。倍率放电性能上,实施例4较对比例4放电率高,如图7所示。循环性能上,实施例4较对比例4容量保持率高,如图8所示。当前第1页1 2 3