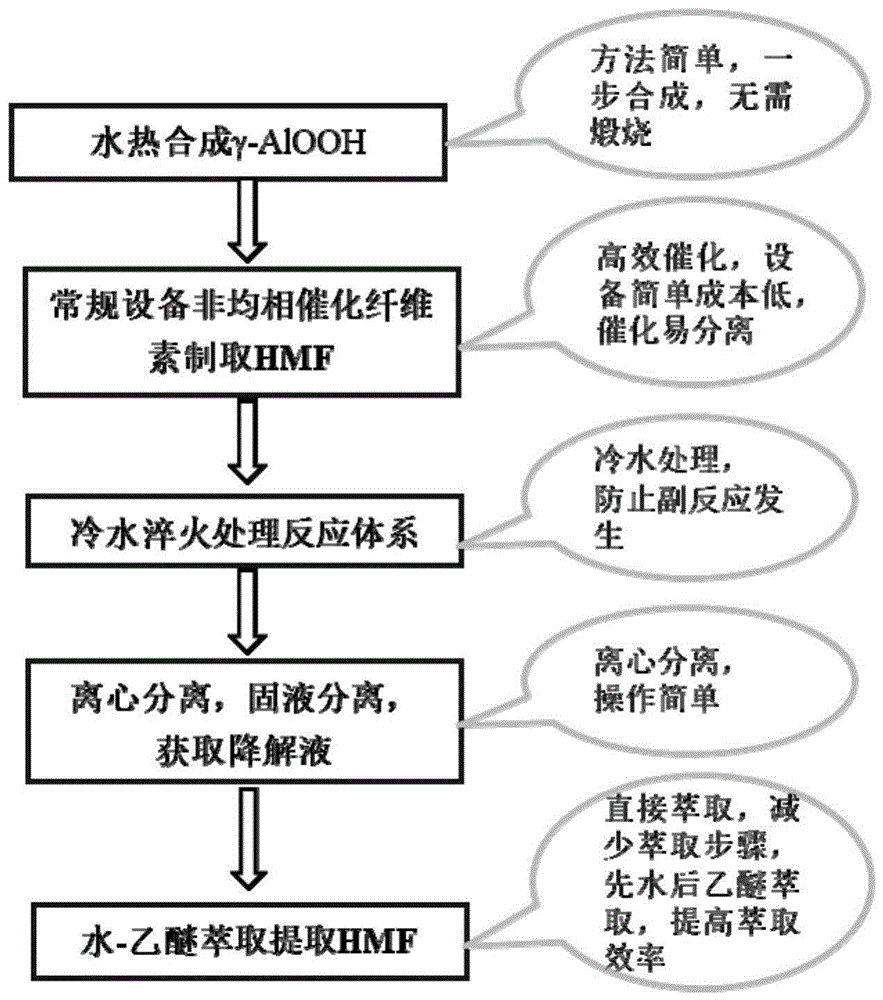
本发明属于催化剂
技术领域:
,具体涉及一种薄水铝石高效催化纤维素制备5-羟甲基糠醛的方法。
背景技术:
:随着石油资源日益枯竭及其人们对化工产品的需求量、对环境安全和可持续发展要求的不断提高,如何利用可再生的、可循环的和清洁的生物资源生产生物质平台化合物以减少或降低人们化石能源依赖,保护环境,是目前日益突出的问题。与其它的生物质平台化合物相比,5-羟甲基糠醛(hmf)被认为是一种具有较好发展前途的平台化合物,具备合成多种精细化学品、医药前驱体、生物燃料、高性能聚合物的能力,如2,5-二甲酰基呋喃(dff)、2,5-呋喃二羧酸(fda)、2,5-二羟甲基呋喃(bhmf)、2,5-二甲基呋喃(dmf)、乙酰丙酸(la)等,具有十分重要的研究和工业应用的价值,是目前研究的热点。与可食用的,价格较高的单糖相比如葡萄糖,果糖,木糖,纤维素具有非食用性,来源广泛,价格低廉等特点,是制备hmf的更加理想的原料。但是,由于纤维素是由葡萄糖单元通过β-1,4糖苷键和分子间和分子内氢键链接起来的紧密堆积的高分子化合物,具有高结晶度、低溶解度(水和常见有机溶剂)和难降解等特点,因此目前高效降解纤维素制取hmf的难度很大,存在很多的技术难题,具有较大挑战。目前研究表明酸性催化剂,包括均相和非均相相,均有利于催化纤维素降解。但与均相催化剂相比,非均相催化具有催化剂易回收、产物易分离、腐蚀性小、易实现工业化等优点,被认为更加理想制取hmf的方法,也是目前发展趋势和研究热点。近几十年,无数非均相催化剂被开发并应用到纤维素降解制取hmf的研究中,如金属氧化物、沸石分子筛、磺化炭基材料、掺杂材料、多功能聚合物、熔盐、金属有机框架化合物、树脂等。由于金属氧化物可以提供必要的酸性位点且价廉易得,因此,金属氧化物是目前研究最多、也最广泛和最具有工业应用前途的一种非均相催化剂,是目前研究热点和方向。氧化铝是其中一种常用金属氧化物,且由于其价格低廉,获取方面,常作为催化剂或者催化载体催化碳水化合物(葡萄糖、果糖、多糖)制取hmf。例如,sampath(appl.catal.a-gen.2017;533:75-80)以氧化铝为催化剂,辅以少量氯化铜,在二甲基亚砜(dmso)反应体系中,130℃下反应3h,催化葡萄糖获得56%hmf产率。garcía-sanchoa(appl.catal.b-environ.2017;206:617-625;appl.catal.b-environ.2014;152:1-10)调查以氧化铝为催化剂或者催化剂载体催化葡萄糖制取hmf的情况,同样表明氧化铝是一种具有良好催化葡萄糖、果糖等糖水化合物制取hmf能力的催化剂。但是氧化铝的水热稳定较差,在150℃的热水中,会缓慢地转化为其前驱体薄水铝石(γ-alooh)。同时,由于hmf是由果糖脱水生产的,因此,碳水化合物制取hmf的过程中必然有水参入。而对于纤维素降解制取hmf的过程中,除去上述过程产生的水外,由于纤维素降解第一部为水解反应,因此还需添加额外的水。同时,大多数纤维素降解反应的温度都大于150℃,因此氧化铝较差的水热稳定性势必影响其的催化性能,减低催化稳定性。正是基于这一观点考虑,takagaki(rscadv.2014:43785–43791)利用氧化铝的前驱体薄水铝石(γ-alooh)在水相中直接催化葡萄糖制取hmf,获取约18%hmf产率,说明γ-alooh具备催化葡萄糖、果糖等碳水化合物制取hmf的能力。但是目前,就我们所知,没有γ-alooh催化纤维素制取hmf的报道。同时与目前具有纤维素催化性能的催化剂相比,如磺化炭基材料、掺杂材料、多功能聚合物、金属有机框架化合物、树脂相比,γ-alooh制备简单、价格低廉、获取方便,是更加理想的hmf制取的催化剂。反应溶剂选择是影响纤维素制取hmf另一个关键因素。由于纤维素是紧密推挤的高分子化合物,难溶于常见有机溶剂和水。因此,如何有效溶解纤维素,促进纤维素与非均相催化剂有效接触,是提高纤维素降解效率关键因素之一。与其它常见溶剂相比(乙醇、丙酮),离子液体具有较强的纤维素溶解能力,在120℃以上纤维素可以有效溶于离子液体。虽然目前离子液体价格较高,但离子液体稳定性强,可以通过简单蒸馏、离子交换、萃取,实现离子液体循环使用,或者通过加入其它常见试剂降低其使用比例,来减少成本。因此,离子液体仍是目前降解纤维素的理想反应溶剂之一。因此,本发明公开了一种薄水铝石(γ-alooh)高效催化纤维素制取hmf的方法。技术实现要素:与葡萄糖,果糖,木糖等可食用的,价格较高的单糖相比,纤维素具有非食用性,来源广泛,价格低廉等特点,是制备hmf的更加理想的原料。但是,由于纤维素是由葡萄糖单元通过β-1,4糖苷键和分子间氢键链接起来的紧密堆积的高分子化合物,具有高结晶度、低溶解度(水和常见有机溶剂)和难降解等特点,因此目前高效降解纤维素制取hmf的难度很大,存在很多的技术难题,具有较大挑战。本发明的目的是解决常见氧化铝催化剂水热稳定性不强,和其它非均相催化剂制备复杂合不适合大范围制取hmf的问题,提供一种薄水铝石高效催化纤维素制备hmf的方法,该方法采用的催化剂薄水铝石性质稳定,原料价廉易得,催化效率高。为了实现上述发明目的,本发明采用以下技术方案:一种薄水铝石高效催化纤维素制备5-羟甲基糠醛的方法:将薄水铝石和纤维素加入到离子液体、二甲基亚砜和水的混合体系中,搅拌均匀后转移到反应器中,120~210℃条件下搅拌反应,反应结束后向反应液中加入去离子水进行淬火处理,离心,收集上层液体,得到包含5-羟甲基糠醛的降解液。进一步地,制备5-羟甲基糠醛的方法为:将纤维素先加入离子液体和二甲基亚砜的混合溶液中,搅拌至纤维素溶解,再加入薄水铝石和去离子水,搅拌均匀后转到到反应器中,120~210℃条件下搅拌反应,反应结束后向反应液中加入去离子水进行淬火处理,离心,收集上层液体,得到包含5-羟甲基糠醛的降解液。进一步地,薄水铝石和纤维素的质量比为0.05:1~5:1,优选为1:1。进一步地,纤维素与混合体系(离子液体、二甲基亚砜和水)的质量比为1:10~1:100,优选为1:60。进一步地,混合体系中离子液体和二甲基亚砜的质量比为6:0~2:4,优选为4:2。进一步地,混合体系中离子液体和水的质量比为4:2~4:0.5,优选为4:1。进一步地,所述离子液体为1-丁基-4-甲基氯化咪唑。进一步地,反应时间为0.5h~6h,优选为2h。进一步地,所述反应容器为常规玻璃反应器。进一步地,所述薄水铝石是通过以下方法制备得到的:将铝源、缓慢水解试剂加至去离子水中,搅拌均匀后,滴加沉淀剂,调节溶液ph值至9,然后将溶液转移至内衬聚四氟乙烯的反应釜中,将反应釜在100~300℃下反应5~60h,取出反应釜,自然冷却到室温,通过离心、洗涤收集反应后的固体,将固体在60~180℃下干燥8~48h,即获得固体催化剂薄水铝石。所述铝源为无机铝盐和/或异丙醇铝,缓慢水解试剂为碳酸氢铵,沉淀剂为氨水溶液。进一步地,所述铝源和缓慢水解试剂的摩尔比为1:2。进一步地,所述无机铝盐选自alcl3、al(no3)3、al2(so4)3、alcl3·6h2o、al(no3)3·9h2o、al2(so4)3·16h2o中的一种或几种,其中al(no3)3、al(no3)3·9h2o效果最佳。进一步地,从包含5-羟甲基糠醛的降解液萃取提纯5-羟甲基糠醛的方法为:在包含5-羟甲基糠醛的降解液中加入乙醚进行首次萃取分离,静置分层后,在上层液中加入去离子水,搅拌均匀后,再加入乙醚进行再次萃取分离,以此再进行2-3次萃取分离后,获取5-羟甲基糠醛-乙醚萃取液,将萃取液在冰水浴条件下进行减压蒸馏,分离乙醚,得到高浓度5-羟甲基糠醛。有益效果与现有技术相比,本发明具有如下优点:(1)本发明公开的非均相催化剂γ-alooh具有原料价格低廉易得、制备方法简单、催化剂性质稳定的特点,具有良好工业化应用前景。(2)采用本发明的方法催化纤维素制取hmf时,具有高效催化(hmf产率和选择性高)、催化剂易分离可重复使用、操作简单和成本较低(设备简单、催化剂和反应可循环利用)等特点,可避免大量副反应产生,提高产物选择性,降低产物分离成本,具有极高应用价值。(3)本发明利用直接一步法从离子液体(il)、dmso和水混合溶液中萃取hmf,减少操作步骤,避免了过多操作会导致hmf发生分解,提高hmf提取效率;且利用离子液体、dmso和hmf之间极性的不同,通过先加入水,充分利用水的极性,降低dmso和离子液体与hmf之间作用力;再借助乙醚对hmf的高萃取能力,可在保证hmf稳定性同时,提高hmf提取效率;实现了在高沸点强极性溶剂dmso和离子液体中一步萃取hmf的任务,可有效解决目前hmf在高沸点极性溶剂和离子液体混合溶液中提纯问题。附图说明图1为本发明的制备方法的流程示意图;图2为实施例1所制得的γ-alooh的xrd图;图3为实施例7中萃取剂中乙醚的体积分数对萃取效果的影响图;图4为实施例8中萃取次数对萃取效果的影响图;图5为实施例9中溶剂对催化效果的影响图;图6为实施例10中反应时间对催化效果的影响图;图7为实施例11中反应温度对催化效果的影响图;图8为实施例12中催化剂用量对催化效果的影响图;图9为实施例13中水添加量对催化效果的影响图;图10为实施例17中催化剂循环使用次数对催化效果的影响图。具体实施方式下面结合实施例对本发明进一步解释说明。下述实施例中的百分含量如无特殊说明均为质量百分含量。所用试剂或者仪器设备未注明生产厂商的,均视为可以通过市场购买的常规产品。实施例1在800转/分钟的磁力搅拌下,将40ml的0.75mol/l的nh4hco3溶液缓慢加入到10ml1.5mol/lal(no3)3溶液中。待其变成澄清透明溶液后,缓慢滴入25%的浓氨水溶液,调节ph至9。待其变成均匀的混合液后,将其转移到100ml内衬聚四氟乙烯的反应釜当中,在150℃下反应12h。当反应时间到达设定的时间时,取出反应釜。自然冷却到室温后,打开反应釜,进行催化剂的分离和洗涤工作,获取固体产物。最后,将此固体产物在150℃下干燥12h,即获得的固体催化剂γ-alooh。将此固体催化剂进行xrd分析。如图2所示,从图2中可以看出,样品的所有衍射峰与正交γ-alooh(jcpds021-1307)标志物衍射峰一致,同时没有观察到其它物质的衍射峰,说明合成的样品为高纯度的γ-alooh。在800转/分钟的磁力搅拌下,将0.1g纤维素加入到4.0g离子液体1-丁基-4-甲基氯化咪唑(bmimcl)和2.0g二甲基亚砜(dmso)的混合溶液中,搅拌直至纤维素完全溶解,形成均一的反应液。再将0.1g催化剂γ-alooh和1.0g去离子水加入到此反应液中,待其搅拌均匀后,将上述反应体系转移至160℃油浴埚中,800转/分钟磁力搅拌下反应2h。反应结束后,立即向反应液加入20ml冷的去离子水进行淬火处理。再用离心机以10000转/分钟的速度分离5min,收集上层液体,获得包含hmf的降解液。取出少许此降解液,用去离子水稀释200倍后,再利用高效液相色谱对降解液中的产物进行分析,计算得到此反应的hmf产率为58.4%和hmf选择性为60%,纤维素的转化率为97%。向上述离心分离后得到的降解液中,加入20ml乙醚进行萃取分离。静置10min后,取出上层液体。再向此上层液中加入20ml去离子水,搅拌均匀后,在向此均匀液中加入10ml乙醚进行萃取分离。静置10min后,取出上层溶液。与此,再重复此过程两次,取出上层液体,得到最终乙醚-hmf萃取溶液。同时,收集上述过程中所有的下层液体,80℃下进行旋转蒸馏,回收离子液体和dmso。紧接着,将此乙醚-hmf萃取溶液,在冰水浴中,进行减压蒸馏处理,回收乙醚溶液(做下一次的萃取剂),获得高浓度的hmf。取少许此hmf,用20ml去离子水稀释后,利用高效液相色谱分析hmf含量,计算得到hmf纯度为94%,萃取率为59%。实施例2γ-alooh制备方法和实施例1相同。纤维素降解制取hmf实验过程也如实施例1相同。在制备5-羟甲基糠醛的过程中,保持反应溶剂中离子液体和dmso比例不变,将反应溶剂(离子液体和dmso)增加至9.0g,考察反应物浓度对催化效果的影响。具体过程如下:在800转/分钟的磁力搅拌下,将0.1g纤维素加入到6.0g离子液体1-丁基-4-甲基氯化咪唑(bmimcl)和3.0g二甲基亚砜(dmso)的混合溶液中,搅拌直至纤维素完全溶解,形成均一的反应液。再将0.1g催化剂γ-alooh和1.0g去离子水加入到此反应液中。待其搅拌均匀后,将上述反应体系转移至160℃油浴埚中,800转/分钟磁力搅拌下反应2h。反应结束后,立即向反应液加入20ml冷的去离子水进行淬火处理。再用离心机以10000转/分钟的速度分离5min,收集上层液体,获得包含hmf的降解液。取出少许此降解液,用去离子水稀释200倍后,再利用高效液相色谱对降解液中的产物进行分析,计算得到此反应的hmf产率为60.3%和hmf选择性为61.4%,纤维素的转化率为98%。实施例3在制备5-羟甲基糠醛的过程中,保持反应溶剂中离子液体和dmso比例不变,将反应溶剂(离子液体和dmso)减少至3.0g,考察反应物浓度对催化效果的影响。具体过程如下:在800转/分钟的磁力搅拌下,将0.1g纤维素加入到2.0g离子液体1-丁基-4-甲基氯化咪唑(bmimcl)和1.0g二甲基亚砜(dmso)的混合溶液中,搅拌直至纤维素完全溶解,形成均一的反应液。再将0.1g催化剂γ-alooh和1.0g去离子水加入到此反应液中。待其搅拌均匀后,将上述反应体系转移至160℃油浴埚中,800转/分钟磁力搅拌下反应2h。反应结束后,立即向反应液加入20ml冷的去离子水进行淬火处理。再用离心机以10000转/分钟的速度分离5min,收集上层液体,获得包含hmf的降解液。取出少许此降解液,用去离子水稀释200倍后,再利用高效液相色谱对降解液中的产物进行分析,计算得到此反应的hmf产率为50.3%和hmf选择性为54.1%,纤维素的转化率为93%。从实施例1-3可以看出在离子液体和dmso的混合反应溶剂含量不低于6.0g,即纤维素含量不高于1.7%时,反应溶剂含量对hmf产率和选择性影响不大。但是一旦反应溶液含量低于6.0g,即葡萄糖含量高于1.7%时,反应溶剂含量对hmf产率和选择性有很大影响。反应溶剂的量越低,hmf产率和选择性越低,这可能与纤维素在离子液体溶解度有关,反应溶剂的含量越低,离子液体含量就越少,溶解纤维素的含量就越少,纤维素与催化剂接触几率随之降低,催化效果就越差。实施例4γ-alooh制备方法和制备条件、纤维素降解制取hmf的实验过程和原料加入量完全如实施例1相同。只是改变hmf萃取方法,考察不加入水对萃取结果的影响。具体过程如下:向离心分离后得到上层降解液中,加入20ml乙醚进行萃取分离。静置10min后,取出上层液体。再向此上层液中直接加入20ml乙醚进行萃取分离。静置10min后,取出上层溶液。与此在重复此过程2次,取出上层溶液,得到乙醚-hmf的萃取液。然后,将此乙醚-hmf的萃取液,在冰水浴中,进行减压蒸馏处理,回收乙醚溶液(做下次萃取剂),获得高浓度的hmf。取少量此hmf,用20ml去离子水稀释后,利用高效液相色谱分析hmf含量,计算得到hmf纯度为19%,萃取率为42%。此实验说明,加入水对萃取结果有很大影响,不加入水很难分离反应溶剂(离子液体与dmso混合溶液)与hmf,难以达到分离提纯的目的。实施例5γ-alooh制备方法和制备条件、纤维素降解制取hmf的实验过程和原料加入量完全如实施例1相同。只是改变hmf萃取方法,进行两步分离萃取方法。具体过程如下:将收集上层液,首先在150℃减压蒸馏,分离离子液体,获取dmso-水-hmf的降解液。将此收集降解液进行水-乙醚萃取分离,首先向此降解液加入10ml的乙醚,充分混合后,静置10min后,取出上层液体。再向此上层液中加入20ml去离子水,搅拌均匀后,在向此均匀液中加入10ml乙醚进行萃取分离。静置10min后,取出上层溶液。再重复此过程2次,取出上层液体,得到最终乙醚-hmf萃取液。然后,将此乙醚-hmf萃取液,在冰水浴中,进行减压蒸馏处理,回收乙醚溶液(做下一次的萃取剂),获得高浓度的hmf。取少许此hmf,用20ml去离子水稀释后,利用高效液相色谱分析hmf含量,计算得到hmf纯度为98%,萃取率为45%。对比实施例1,可以看出虽然两部萃取hmf纯度更高,但萃取率明显下降,整体效果不及一步萃取分离。实施例6γ-alooh制备方法和制备条件、纤维素降解制取hmf的实验过程和原料加入量完全如实施例1一样。考察hmf萃取剂的类型对萃取结果的影响,分别以甲苯、丙酮(acetone)、乙酸乙酯、甲基异丙酮、四氢呋喃(thf)和石油醚为萃取剂,萃取过程如实施例1一样。其萃取结果表1所示,从表1中可以得出乙醚作为萃取剂萃取效果最佳。表1不同萃取剂对hmf萃取结果的影响甲苯丙酮乙酸乙酯甲基异丙酮四氢呋喃石油醚乙醚hmf纯度(%)32586585867694hmf萃取率(%)51863520859实施例7γ-alooh制备方法和制备条件、纤维素降解制取hmf的实验过程和原料加入量完全如实施例1一样。在保持第一次萃取剂乙醚加入量不变前提下,即向离心分离后的上层液体中加入10ml乙醚条件下,考察从第二次开始萃取剂中乙醚的体积百分数对萃取结果的影响,保持乙醚与水总体积为30ml,考察乙醚体积分数分别为17%、20%、33%、50%、67%和80%时对萃取结果的影响,其实验过程去实施例1一样,其萃取结果如图3所示。从图3可知,在乙醚体积分数为33%,即乙醚/水的体积比为1:2时,萃取效果最佳。实施例8γ-alooh制备方法和制备条件以及纤维素降解制取hmf的实验过程和原料加入量完全如实施例1一样。考察萃取次数(1、2、3、4、5、6和7次)对萃取效果的影响,其实验过程去实施例1一样,其萃取结果如图4所示。从图可4知,萃取次数4次时,萃取效果最佳。实施例9γ-alooh制备方法和制备条件如实施例1一样。纤维素降解制取hmf实验过程也如实施例1相同,改变反应溶剂,考察反应溶剂的变化对催化效果影响。实验结果如图5所示,il为离子液体;dmso为二甲基亚砜;dmf为n’n-二甲基甲酰胺;thf为四氢呋喃;acetone为丙酮;xil指离子液体在混合溶剂中的质量分数。从图5中可以得出以离子液体和dmso混合液作为溶剂且二者质量比为4:2时,催化效果最佳。实施例10γ-alooh制备方法和制备条件如实施例1一样。纤维素降解制取hmf实验过程也如实施例1相同,只是调整催化反应的反应时间(0.5h到6h),考察反应时间对催化效果的影响。实验结果如图6所示。从图6中可以看出催化反应时间为2h,催化效果最佳。实施例11γ-alooh制备方法和制备条件如实施例1一样。纤维素降解制取hmf实验过程也如实施例1相同,只是调变催化反应的反应温度(120℃到210℃),考察反应温度对催化效果的影响。实验结果如图7所示。从图7中可以看出反应温度为160℃,催化效果最佳。实施例12γ-alooh制备方法和制备条件如实施例1一样。纤维素降解制取hmf实验过程也如实施例1相同,只是调变催化剂用量(0.05g到0.2g),考察催化剂的用量对催化效果的影响。实验结果如图8所示。从图8中可以看出催化剂用量为0.1g时,催化效果最佳。实施例13γ-alooh制备方法和制备条件如实施例1一样。纤维素降解制取hmf实验过程也如实施例1相同,只是调变水的添加量(0到4ml),考察水的添加量对催化效果的影响。实验结果如图9所示。从图9中可以看出水的添加量为1.0ml时,催化效果最佳。实施例14γ-alooh制备方法和制备过程如实施例1一样,调变铝源制备不同的γ-alooh,分别用al2(so4)3、alcl3和al(i-opr)3代替原有al(no3)3制备γ-alooh,并以此制备的γ-alooh作为催化剂催化纤维素水解制取hmf,其纤维素降解制备hmf过程如实施例1相同。具体实验结果如表2所示。表2不同铝源制备的γ-alooh催化纤维素降解制取hmf铝源al2(so4)3alcl3al(i-opr)3al(no3)3hmf(%)35.648.62058.4hmf选择性(%)45543460纤维素转化率(%)79895997从表2可以看出,以无机铝源为原料制备的γ-alooh比以有机铝源为铝源作为原料制备的γ-alooh,具有更好催化效果。而在无机铝源的中,以al(no3)3作为铝源制备的γ-alooh的催化效果最佳。实施例15γ-alooh制备方法和制备过程如实施例1一样,只是调变催化剂γ-alooh制备温度,将原有制备温度150℃调节至100℃、130℃、140℃、150℃、160℃、180℃或200℃中的任意一个,并以此制备的γ-alooh作为催化剂催化纤维素降解制备hmf。纤维素降解制备hmf过程如实施例1相同。其结果如表3所示。从表3中,可以得出制备温度为150℃时,制备的γ-alooh的催化效果最佳。表3不同温度制备的γ-alooh催化纤维素降解制取hmf制备温度(℃)100130150160180200hmf(%)44.352.558.455.650.246.8hmf选择性(%)535660595554纤维素转化率(%)839397959287实施例16γ-alooh制备方法和制备过程如实施例1一样,只是调变催化剂γ-alooh制备时间,将原有制备时间12h调节至2h、6h、12h、18h、24h、36h或48h中的任意一个,并以此制备的γ-alooh作为催化剂催化纤维素降解制备hmf。纤维素降解制备hmf过程如实施例1相同。其结果如表4所示。从表4中,可以得出制备时间为12h时,制备的γ-alooh的催化效果最佳。表4不同时间制备的γ-alooh催化纤维素降解制取hmf制备时间(h)261218243648hmf(%)11.340.358.457.356.354.652.6hmf选择性(%)25496060595756纤维素转化率(%)45829796959594实施例17催化剂循环重复使用实验。以实施例1中离心分离后烘干固体残渣作为下一次纤维素降解制取hmf实验的催化剂。具体过程如下:实验例1中离心分离得到首次使用γ-alooh的残渣,分别经过去离子水、乙醇和γ-戊内脂洗涤后,除去表面未反应纤维素和残留的反应物(如葡萄糖、果糖、hmf等),在100℃的真空干燥箱烘干,得到固体残渣,作为下次实验的催化剂,进行催化循环使用实验,考察催化剂的稳定性,纤维素水解制取实验过程过实验例1相同。其催化结果如图10所示。由图10可知,催化剂γ-alooh具有良好催化稳定性,5次重复使用后,催化剂的催化效率并未发生较大改变,hmf产率和纤维素转化率分别为47.8%和91%。本发明的保护内容不局限于以上实施例。在不背离发明构思的精神和范围下,本领域技术人员能够想到的变化和优点都被包括在本发明中,并且以所附的权利要求为保护范围。当前第1页12