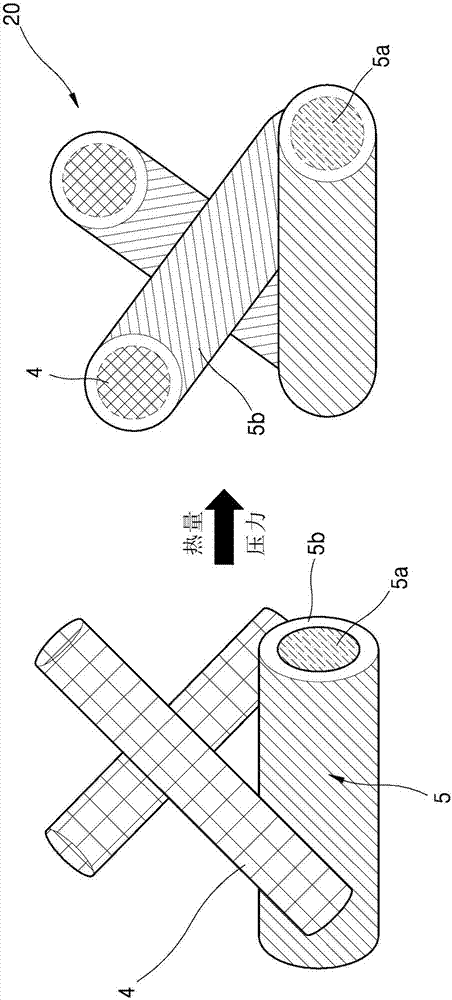
本发明涉及多孔性单一树脂纤维复合材料及多孔性单一树脂纤维复合材料的制备方法。
背景技术:
:以往的热塑性复合材料由呈现高刚性的玻璃纤维或碳纤维等高强度强化纤维和组成基质的热塑性树脂形成。由于这种热塑性复合材料比普通热塑性树脂产品呈现高机械物性,因而被广泛使用为汽车及建筑用材料。以往的热塑性复合材料的制备方式主要是在将强化纤维和热塑性树脂混合之后通过挤压和模压工序来成形的方式,最近,为了提高强度和生产性,首先通过采用干式针刺工序或湿式抄纸工序来优先制备包含强化纤维的垫形态的材料,之后通过将树脂浸渍于垫的方式来制备复合材料。就强化纤维和热塑性树脂的复合材料而言,由于强化纤维起到加固材料的作用,因而呈现优秀的机械强度。与普通的玻璃纤维及碳纤维等热塑性树脂不同,上述纤维强化复合材料使用具有高强度的纤维。在以如上所述的方式制备的复合材料中,热塑性树脂和强化纤维的成分互不相同,因而为了循环利用,必须额外实施对纤维和树脂进行分离的工序。并且,当玻璃纤维在被成形为复合材料之后露出于表面时,可能在环境方面或在处理性方面存在问题,因而需要进行涂敷膜或贴合无纺布等的额外的表面材料处理。并且,由于两种材料形成纤维-基质(Fiber-Matrix)结构,因而材料之间的互换性低,从而可能呈现出期待程度以下的强度。因此,当制备上述复合材料时,必须包含用于提高上述互换性的交联剂等添加剂。因这种额外的多个工序,从而存在使工序变得复杂且材料价格上升的问题。技术实现要素:本发明要解决的技术问题本发明的一实例提供不仅呈现优秀的机械强度、吸音性能、隔热性及实现轻量化还具有优秀的成形性的多孔性单一树脂纤维复合材料。本发明的另一实例提供上述多孔性单一树脂纤维复合材料的制备方法。技术方案在本发明的一实例中,提供一种多孔性单一树脂纤维复合材料,包括第一纤维状粒子、第二纤维状粒子以及用于使上述第一纤维状粒子与上述第二纤维状粒子相粘结的粘结材料,上述第一纤维状粒子与上述第二纤维状粒子借助上述粘结材料来相粘结,从而形成具有气孔的不规则的网眼结构,上述第一纤维状粒子为包含第一聚酯类树脂的聚酯类纤维,上述第二纤维状粒子为包含第二聚酯类树脂的聚酯类纤维,上述粘结材料包含第三聚酯类树脂,上述第一纤维状粒子的拉伸率高于上述第二纤维状粒子的拉伸率,上述第二聚酯类树脂的熔点高于上述第三聚酯类树脂的熔点。在本发明的另一实例中,提供一种多孔性单一树脂纤维复合材料的制备方法,包括:将强化纤维及双组分聚合物纤维分散于酸溶液中来准备浆料溶液的步骤;通过湿式抄纸工序由上述浆料溶液形成网的步骤;以及对所形成的上述网进行热处理及干燥来制备多孔性单一树脂纤维复合材料的步骤,上述强化纤维包含第一聚酯类树脂,上述双组分聚合物纤维包含芯(core)部和鞘(sheath)部,上述芯部包含第二聚酯类树脂,上述鞘部包含第三聚酯类树脂,上述粘结材料包含第三聚酯类树脂,上述第一纤维状粒子的拉伸率高于上述第二纤维状粒子的拉伸率,上述第二聚酯类树脂的熔点高于上述第三聚酯类树脂的熔点。有益效果上述多孔性单一树脂纤维复合材料呈现优秀的机械强度、吸音性能、隔热性及实现轻量化,并具有环保性以及易于循环利用,并且降低生产成本以及具有优秀的成形性。附图说明图1为本发明一实例的多孔性单一树脂纤维复合材料的简要示意图。图2为示出根据上述多孔性单一树脂纤维复合材料的制备方法向强化纤维和双组分聚合物施加热量和压力来制备本发明再一实例的多孔性单一树脂纤维复合材料的方式的图。图3为示意性地示出根据本发明另一实例来说明的多孔性单一树脂纤维复合材料板材的制备方法的图。图4为在实施例1中制备的板材的切割面的扫描电子显微镜(SEM)照片。图5为在实施例1中制备的板材的表面的光学显微镜图像。图6为在实施例1中制备的板材的表面的光学显微镜图像。图7为在实施例3中制备的板材的表面的光学显微镜图像。具体实施方式以下,对本发明的实例进行详细的说明。但,这些实例仅仅是作为例示所提出的,本发明并不局限于此,本发明仅由后述的发明要求保护范围的范畴所定义。在本发明的一实例中,提供一种多孔性单一树脂纤维复合材料,包括第一纤维状粒子、第二纤维状粒子以及用于使上述第一纤维状粒子与上述第二纤维状粒子相粘结的粘结材料,上述第一纤维状粒子与上述第二纤维状粒子借助上述粘结材料来相粘结,从而形成具有气孔的不规则的网眼结构,上述第一纤维状粒子为包含第一聚酯类树脂的聚酯类纤维,上述第二纤维状粒子为包含第二聚酯类树脂的聚酯类纤维,上述粘结材料包含第三聚酯类树脂,上述第一纤维状粒子的拉伸率高于上述第二纤维状粒子的拉伸率,上述第二聚酯类树脂的熔点高于上述第三聚酯类树脂的熔点。上述第一纤维状粒子可以为拉伸率为约300%至约600%的拉伸聚酯类纤维,上述第二纤维状粒子可以为0%未拉伸聚酯类纤维或拉伸率小于约300%的拉伸聚酯类纤维。上述聚酯类纤维可以为聚对苯二甲酸乙二酯(PET)纤维。例如,对于上述聚酯类纤维而言,可通过调节拉伸率来调节纤维自身的机械强度及刚性。例如,若向聚酯类纤维的长度方向提高拉伸率,则聚酯类纤维的结晶性上升,从而机械强度及刚性得以提高。可使用差示扫描量热仪(differentialscanningcalorimeter,DSC,Perkin-Elmer,DSC8000)来测定对聚酯类树脂的强度产生影响的结晶性。当利用差示扫描量热仪进行测定时,在结晶性相关分析中,若ΔH(J/g)值越高,则可判断为结晶性越高。如上所述,若拉伸率上升,则因结晶性上升而使基于差示扫描量热仪分析的ΔH值上升。由此,可根据拉伸率来对聚酯类树脂的结晶性进行分析。在上述多孔性单一树脂纤维复合材料中,包含拉伸率为约300%至约600%的拉伸聚酯类纤维作为上述第一纤维状粒子,从而可呈现优秀的机械强度及刚性,并可使热成形时的收缩最小化。在上述多孔性单一树脂纤维复合材料中,与上述第一纤维状粒子一同包含具有不同拉伸率的上述第二纤维状粒子来补充弹性,从而对于外部冲击可有效减弱冲击能量,由此可提高耐冲击性或冲击吸收能力。在上述第一纤维状粒子和上述第二纤维状粒子以一部分或整体涂敷有上述粘结材料成分的状态存在。即,在上述第一纤维状粒子及上述第二纤维状粒子的各个粒子表面形成由上述粘结材料形成的涂敷部。上述第一纤维状粒子及上述第二纤维状粒子的各个涂敷部被熔敷,从而可使上述第一纤维状粒子与上述第二纤维状粒子以不规则的方式相粘结。以如上所述的方式粘结的第一纤维状粒子及第二纤维状粒子可形成具有气孔的不规则的网眼结构。图1为包括本发明一实例的第一纤维状粒子1、第二纤维状粒子2及粘结材料3的多孔性单一树脂纤维复合材料10的简要示意图。上述多孔性单一树脂纤维复合材料为强度、吸音隔音性能及隔热性均优秀的复合材料。在上述多孔性单一树脂纤维复合材料中,上述第一纤维状粒子、上述第二纤维状粒子及上述粘结材料均使用同种单一树脂聚合物材料,因而树脂之间的互换性(compatibility)非常优秀,由此,上述多孔性单一树脂纤维复合材料可呈现非常优秀的强度。并且,上述多孔性单一树脂纤维复合材料仅由聚合物材料形成,因而具有优秀的成形性,并易于循环利用。上述多孔性单一树脂纤维复合材料可根据后述的上述多孔性单一树脂纤维复合材料的制备方法来制备,在以如上所述的方式制备的上述多孔性单一树脂纤维复合材料中,第一纤维状粒子及第二纤维状粒子分散均匀。像这样,若上述第一纤维状粒子及第二纤维状粒子均匀地分散于树脂中,则以粘结材料作为介质来使第一纤维状粒子与第二纤维状粒子相互之间的结合力得到上升,从而使多孔性单一树脂纤维复合材料呈现出更加优秀的强度。如上所述,上述多孔性单一树脂纤维复合材料不仅利用同种树脂来提高树脂之间的互换性,还基于所得出的分散性与强度之间的相关关系来提高第一纤维状粒子及第二纤维状粒子(出于方便,也称之为“多个纤维状粒子”)的分散性,从而获得协同效果,由此呈现出明显提高的强度特性。作为对包含于上述多孔性单一树脂纤维复合材料的多个纤维状粒子的分散性是否得到提高进行确认的间接方法,存在对强度进行比较的方法。若上述多个纤维状粒子的分散性得到提高,则最终使上述多孔性单一树脂纤维复合材料的强度得到提高,因而,在使包含于上述多孔性单一树脂纤维复合材料的第一纤维状粒子、第二纤维状粒子及粘结材料的种类及含量等不同条件维持恒定的情况下,可通过仅改变多个纤维状粒子的分散性,例如,可在通过变更制备方法等来制备上述多孔性单一树脂纤维复合材料之后,对强度进行比较。随着上述多孔性单一树脂纤维复合材料呈现出优秀的机械强度,可以成形为厚度薄的板材或薄片,从而可实现轻量化。在上述多孔性单一树脂纤维复合材料中,还可将上述第一纤维状粒子及上述第二纤维状粒子制备成具有单方向取向性的薄片。像这样,若向上述多孔性单一树脂纤维复合材料的薄片赋予单方向取向性,则薄片将沿着被赋予上述取向性的方向具有高机械物性。这种薄片适合用作可向特定方向承受很大力量的材料。在上述多孔性单一树脂纤维复合材料中,作为形成第一纤维状粒子及第二纤维状粒子的聚合物纤维,上述聚酯类纤维的强度或熔点互不相同,因而通过对它们之间的含量比、各自的强度或熔点的数值范围进行适当调节,来精确地调节如上所述的强度、吸音隔音性能、隔热性等所要达到的物性之间的关系,从而可以设计出整体上呈现优秀性能的多孔性单一树脂纤维复合材料。例如,由于上述粘结材料所包含的上述第三聚酯类树脂的熔点相对低,因而多孔性单一树脂纤维复合材料具有低温成形的特性。若要使上述第一纤维状粒子起到用于补充上述多孔性单一树脂纤维复合材料强度的强化纤维的作用,则用于形成上述第一纤维状粒子的第一聚酯类树脂的强度相对要高。若要使上述第二纤维状粒子起到提高上述多孔性单一树脂纤维复合材料的弹性和冲击吸收性的作用,用于形成上述第二纤维状粒子的第二聚酯类树脂的强度和熔点要相对低于上述第一聚酯类树脂的强度和熔点。若参照后述的多孔性单一树脂纤维复合材料的制备方法,则上述粘结材料相当于以上述第二纤维状粒子为芯的双组分纤维的鞘(sheath)部。上述双组分纤维的鞘部在低温下被熔融,从而一部分向上述第一纤维状粒子的表面转移,若要利用粘结材料来使上述第一纤维状粒子与上述第二纤维状粒子相粘结,上述粘结材料的熔点相对要低。上述聚酯类树脂的强度与拉伸率存在关联。若提高聚酯类树脂的拉伸率,则使强度上升,相反,若降低拉伸率,则使强度下降。在一实例中,上述第一聚酯类树脂的熔点可以为约200℃至约270℃。在再一实例中,上述第二聚酯类树脂的熔点可以为约200℃至约270℃。在另一实例中,上述第三聚酯类树脂的熔点可以为约100℃至约200℃。可使用热重分析(Thermogravimetricanalysis,TGA,Pyris1)设备来对聚酯类树脂的熔点进行测定。上述多孔性单一树脂纤维复合材料不使用玻璃纤维或碳纤维,而将聚合物纤维的多个纤维状粒子作为强化纤维来使用,从而无需额外的表面处理工序。不使用玻璃纤维或碳纤维的原因在于,在玻璃纤维或碳纤维露出于表面的情况下,会对人体有害,因而当制备复合材料时,需要通过表面处理工序来使玻璃纤维或碳纤维不露出于表面。相反,在上述多孔性单一树脂纤维复合材料使用聚合物纤维的情况下,若聚合物纤维露出于表面,则对人体无害,从而无需对表面进行处理。并且,上述多孔性单一树脂纤维复合材料使用聚合物纤维的多个纤维状粒子来代替玻璃纤维或碳纤维,并使用呈现出相对低热导率的作为热塑性聚合物纤维的聚酯类树脂,由此提高耐热性。并且,由于这种热塑性聚合物纤维相对于玻璃纤维或碳纤维具有低比重,因而当对相同重量复合材料实施成形时,可以包含更多数量的纤维状粒子,并使上述多孔性单一树脂纤维复合材料形成为低密度的多孔性材料。由于具有基于纤维振动而使通过上述多孔性单一树脂纤维复合材料的开放的气孔进入的声波减弱的效果,从而适合用作吸音隔音材料。在用作这种吸音隔音材料的情况下,若上述多孔性单一树脂纤维复合材料的气孔率越高,且所含有的纤维的数量越多,则能量减弱效果越优秀。如上所述,上述多孔性单一树脂纤维复合材料使用密度相对低于玻璃纤维或碳纤维密度的多个纤维状粒子,因而以相同重量的复合材料为基准,复合材料内的纤维状粒子的数量会增加,由此提高吸音隔音性能。尤其,相对于玻璃纤维或碳纤维等硬质的强化纤维,由于热塑性聚合物纤维的基于振动的自由度高,因而基于纤维振动的声能减弱效果优秀。因此,上述多孔性单一树脂纤维复合材料可具有更加优秀的吸音性能,并可有效地适用于要求优秀吸音性能的领域。相对于玻璃纤维及碳纤维,上述热塑性聚合物纤维的热导率处于25%以下水平,因而上述多孔性单一树脂纤维复合材料具有可使通过纤维传递的热传递达到最小化的优点。由此,上述单一树脂复合材料呈现出优秀的隔热性能。在一实例中,在上述多孔性单一树脂纤维复合材料中,第一纤维状粒子的含量与第二纤维状粒子和粘结材料的含量之和的重量比可以为约25:75至约60:40。第一纤维状粒子的含量越上升,强度越优秀,但若达到规定含量水平以上,则提高的程度可能下降。上述含量范围既有效确保基于第一纤维状粒子的含量增加的强度提高效果,同时也是适合从第二纤维状粒子获得效果的含量范围。当通过后述的多孔性单一树脂纤维复合材料的制备方法来制备多孔性单一树脂纤维复合材料时,第二纤维状粒子和粘结材料基于双组分聚合物纤维。因此,在后述的多孔性单一树脂纤维复合材料的制备方法中,可根据上述范围对第一纤维状粒子和双组分聚合物纤维的含量进行调节,来制备具有上述含量比的多孔性单一树脂纤维复合材料。在另一实例中,在上述多孔性单一树脂纤维复合材料中,相对于100重量份的第二纤维状粒子,可包含约40重量份至约250重量份的粘结材料。通过以上述含量比对第二纤维状粒子和粘结材料的含量比进行调节,来向上述第二纤维状粒子和粘结材料适当地赋予粘结力和弹性,并可使它们维持优秀的分散性。如上所述,在后述的多孔性单一树脂纤维复合材料的制备方法中,可通过调节双组分聚合物纤维的芯部与鞘部的含量比,来呈现上述第二纤维状粒子与上述粘结材料的含量比。上述多孔性单一树脂纤维复合材料的气孔率可以为约30体积百分比至约80体积百分比。如上所述,上述多孔性单一树脂纤维复合材料形成网眼结构,并形成开放的气孔。具有上述范围的气孔率的多孔性单一树脂纤维复合材料可维持强度,并可实现轻量化,并且,可以具有优秀的吸音隔音性能。上述多孔性单一树脂纤维复合材料可实现轻量化的相关内容如同上述,具体地,上述多孔性单一树脂纤维复合材料的密度可以为约0.1g/cm3至约1.6g/cm3。上述多孔性单一树脂纤维复合材料能够以符合所需用途的形态来制备,例如,可通过湿式抄纸工序等来制备成薄片。上述多孔性单一树脂纤维复合材料的薄片可制备成具有适合所需用途的重量,例如,可制备成具有约50g/m2至约1200g/m2重量的薄片。上述第一纤维状粒子的截面直径可以为约5μm至约40μm。具有上述范围粗细的第一纤维状粒子既可以适当地赋予强度,又可确保取向性及分散性。包含具有上述范围粗细的第一纤维状粒子的上述多孔性单一树脂纤维复合材料对外部冲击具有强承受力,在根据后述的上述多孔性单一树脂纤维复合材料的制备方法来制备上述多孔性单一树脂纤维复合材料的情况下,当使第一纤维状粒子分散于水溶液中时,使上述第一纤维状粒子在水溶液中具有适当的氢化性(Hydroentangleproperty),从而可易于形成薄片。上述第一纤维状粒子的长度可以为约6mm至约24mm,具体地,可以为约12mm至约24mm。具有上述范围长度的第一纤维状粒子既可以适当地赋予强度,又可以确保取向性及分散性,并且,通过适当地向多个纤维状粒子之间赋予结合力,从而使上述多孔性单一树脂纤维复合材料具有优秀的强度,并且在纤维过长的情况下,防止纤维在凝结的过程中分散性下降的现象,从而适合形成薄片。上述第二纤维状粒子的截面直径可以为约5μm至约30μm。具有上述范围粗细的第二纤维状粒子既可适当地赋予强度,又可确保取向性及分散性。包含具有上述范围粗细的第二纤维状粒子的上述多孔性单一树脂纤维复合材料具有优秀的强度特性,在根据后述的上述多孔性单一树脂纤维复合材料的制备方法来制备上述多孔性单一树脂纤维复合材料的情况下,当使第一纤维状粒子分散于水溶液中时,使上述第一纤维状粒子在水溶液中具有适当的氢化性,从而可易于形成薄片。上述第二纤维状粒子的长度可以为约3mm至约6mm。具有上述范围的长度的第二纤维状粒子既可以适当地赋予强度,又可以确保取向性及分散性,并且,通过适当地向多个纤维状粒子之间赋予结合力,从而使上述多孔性单一树脂纤维复合材料具有优秀的强度,并且在纤维过长的情况下,防止纤维因凝结成绳(rope)状而导致分散性下降的现象,因而适合形成薄片。纤维长度越短,水溶液中的分散性越提高,但具有强度下降的倾向。通过对具有上述长度范围的第一纤维状粒子和上述第二纤维状粒子进行组合,从而可呈现出优秀的分散性以及优秀的强度特性。由于上述第一纤维状粒子需要执行强化纤维的功能,从而可使用长度长于上述第二纤维状粒子长度的纤维。如上所述,当以如上述例示的方式选择第二聚酯类树脂及第三聚酯类树脂时,需要满足第二聚酯类树脂的熔点高于第三聚酯类树脂的熔点的条件。并且,为了使在后述的多孔性单一树脂纤维复合材料的制备方法中所使用的双组分聚合物纤维的芯部及鞘部材料满足上述条件,可以分别选择第二聚酯类树脂及第三聚酯类树脂。具体地,上述第二聚酯类树脂的熔点可以为约160℃以上。更加具体地,上述第二聚酯类树脂的熔点可以为约200℃至约400℃。通过使第二聚酯类树脂具有上述范围的熔点,从而当低温成形时,可使粘结材料即便在被熔融之后也维持纤维状。在上述第二聚酯类树脂的熔点小于160℃的情况下,为了维持纤维状而存在如下隐患,即,需要过于降低热成形温度,或者日后包含上述第二聚酯类树脂的上述多孔性单一树脂纤维复合材料的热稳定性下降而可能导致尺寸变形或聚合物变质等。并且,由于与第三聚酯类树脂的温差过小,因而可能难以控制成形温度。具体地,上述第三聚酯类树脂的熔点可小于约200℃。上述粘结材料起到捆绑第一纤维状粒子和第二纤维状粒子的作用,使形成上述粘结材料的上述第三聚酯类树脂的熔点低于第二聚酯类树脂的熔点,由于若具有比较低的熔点,则可在低温下被熔融,从而可确保低温成形性。因此,作为上述粘结材料,例如,可使用低熔点聚酯等。由于上述低熔点聚酯可在比普通聚酯低的温度下,即,在约100℃至约140℃之间的温度下被熔融,因而可根据所需的成形温度来选择低熔点聚酯,具体地,可选择低熔点聚对苯二甲酸乙二醇酯(PolyethyleneTerephthalate)。作为通过对聚对苯二甲酸乙二醇酯进行改性来获得低熔点聚对苯二甲酸乙二醇酯的方法之一,有一种向聚对苯二甲酸乙二醇酯追加共聚单体的方法。聚对苯二甲酸乙二醇酯包含邻苯二甲酸酯(phthalate)单位,在邻苯二甲酸酯单位中,苯环与酯形成1,4-(对位(para))键。若利用形成1,2-(邻位(ortho))键和/或1,3-(间位(meta))键的邻苯二甲酸(phthalic)单位和/或间苯二甲酸(isophthalic)单位来取代聚对苯二甲酸乙二醇酯中的形成上述1,4-(对位)键的邻苯二甲酸酯单位的一部分,则因结晶性下降而使熔点下降,从而可获得低熔点聚对苯二甲酸乙二醇酯。例如,上述粘结材料可以为聚对苯二甲酸乙二醇酯中的超过0至约50摩尔百分比的上述邻苯二甲酸酯单位被邻苯二甲酸(phthalic)单位和/或间苯二甲酸(isophthalic)单位所取代的低熔点聚对苯二甲酸乙二醇酯,具体地,上述粘结材料可以为约20摩尔百分比至约40摩尔百分比的上述邻苯二甲酸酯单位被邻苯二甲酸(phthalic)单位和/或间苯二甲酸(isophthalic)单位所取代的低熔点聚对苯二甲酸乙二醇酯。作为通过对聚对苯二甲酸乙二醇酯进行改性来获得低熔点聚对苯二甲酸乙二醇酯的另一种方法,可通过以高碳数链的甘醇(glycol)来代替作为形成聚对苯二甲酸乙二醇酯的乙烯单位的单体的乙二醇(ethyleneglycol)的一部分。例如,当合成聚酯树脂时,作为上述第三聚酯树脂可使用通过将环己烷二甲醇(cyclohexanedimethanol,CHDM)与乙二醇一同共聚来获得的改性的聚对苯二甲酸乙二醇酯(PET-G,Polyethyleneterephthalateglycol-modified)。在改性的聚对苯二甲酸乙二醇酯中,基于环己烷二甲醇的单位的长度与聚对苯二甲酸乙二醇酯中的相邻的乙烯单位的长度不一致,从而发生界面,这些界面妨碍结晶化,从而起到降低聚对苯二甲酸乙二酯的熔点的作用,并形成为非晶质。作为为了降低聚对苯二甲酸乙二醇酯的熔点而可与乙二醇一同使用的共聚单体,除了环己烷二甲醇之外,还可使用丙二醇(trimethyleneglycol)或2-甲基丙二醇(2-methyltrimethyleneglycol)等具有高碳数链的甘醇。在另一实例中,上述第二聚酯类树脂的比重约大于1。当根据多孔性单一树脂纤维复合材料的制备方法来制备多孔性单一树脂纤维复合材料时,使双组分聚合物分散于酸溶液中,此时,只有使用比重大于1的材料,才可提高分散性以及易于形成网状结构,其中,1为水的比重。因此,上述双组分聚合物纤维的芯部可以为比重大于1的聚酯类树脂。上述复合材料的多孔性单一树脂纤维可以制备成密度为约0.2g/cm3至约1.6g/cm3的板材。能够以将多孔性单一树脂纤维复合材料压缩到规定水平的状态来制备上述板材。例如,可在将通过湿式抄纸工序以单张薄片形态获得的上述多孔性单一树脂纤维复合材料薄片层叠多张之后,进行冲压成形来获得上述板材。上述冲压成形工序以多级工序来执行,通过以交替的方式执行热处理工序,从而可进一步提高粘结材料的分散性。例如,在对层叠多张的上述多孔性单一树脂纤维复合材料薄片进行冲压成形之后使其升温,之后重新在常温下进行冲压成形,最终获得板材。通过在冲压工序之间执行上述热处理工序,来使热量易于传递至板材的中心部,从而使粘结材料均匀地得到熔融,由此可形成均匀的分布。像这样,可通过使粘结材料均匀地分散,来使板材的物性整体上获得非常均匀的特性。上述冲压成形能够以80%至95%的压缩率来执行。通过上述冲压成形来调节纤维的压缩密度,从而可呈现出优秀的强度及吸音特性。上述板材包括气孔结构。通常,通过在混合原料后进行挤压并通过模压工序制备的复合材料难以形成气孔结构,相反,由于利用多孔性单一树脂纤维复合材料来制备上述板材,从而形成气孔结构。具体地,上述板材的气孔率可以为约40体积百分比至约80体积百分比。通过使上述多孔性单一树脂纤维复合材料的板材具有上述范围的气孔率,从而可以使上述多孔性单一树脂纤维复合材料的板材的强度、耐冲击性及吸音性的特性均达到优秀。上述多孔性单一树脂纤维复合材料的板材处于上述多孔性单一树脂纤维复合材料被压缩的状态,因此应理解成上述多孔性单一树脂纤维复合材料的板的结构在维持图1中的多孔性单一树脂纤维复合材料结构的状态下仅仅被压缩。具体地,能够执行冲压成形来使上述板材的密度达到约0.2g/cm3至约1.6g/cm3来制备板材。通过压接制备来使板材的密度在上述范围内,从而可呈现优秀的强度。在以如上所述的方式通过压缩制备的上述多孔性单一树脂纤维复合材料的板材中,多个纤维粒子具有优秀的分散率,从而可使板材整体上具有均匀的优秀的机械物性。例如,即使在多个位置对上述板材的冲击强度特性进行评价,也呈现出均匀的优秀的冲击强度结果。具体地,在针对上述板材执行基于美国材料与试验协会(ASTM)D3763基准的落球冲击试验后得出的冲击强度中,在一个板材中得出的冲击强度的最大值与最小值之差可以为约0.2J/mm以下。也就是说,这表示在上述板材中从任意2个位置测定出的基于美国材料与试验协会D3763的冲击强度之差可以为约0.2J/mm以下。上述板材为既可呈现出拉伸、弯曲及冲击强度等高机械强度,又因密度低而可实现轻量化的材料,从而可有效地应用到需要这种特性的汽车及建筑用材料。并且,上述板材可满足这种汽车及建筑用材料所需的优秀的吸音隔音性能条件。并且,上述板材为以单一聚合物为主要成分来组成的材料,因而在无需额外的双重分离工序的情况下容易循环利用,并且因未使用玻璃纤维而在作业时板材呈现出优秀的处理性。并且,如上所述,上述板材以被压缩的状态来制成,具有即使之后升温也不膨胀的特征。上述多孔性单一树脂纤维复合材料的板材可根据后述的上述多孔性单一树脂纤维复合材料的制备方法来制备,上述板材由第一纤维状粒子及第二纤维状粒子得到均匀分散的上述多孔性单一树脂纤维复合材料制备,因而多个纤维状粒子的分散性很优秀,并且,第一纤维状粒子、第二纤维状粒子及粘结材料均使用单一树脂,因而提高各成分之间的互换性,从而提高结合力。像这样,上述第一纤维状粒子及第二纤维状粒子得到均匀分散,且提高各种成分的结合力,因而提高多孔性单一树脂纤维复合材料的板材的强度。上述多孔性单一树脂纤维复合材料的板材根据以如上所述的方式得出的分散性或互换性与强度之间的相关关系,来提高多个纤维状粒子的分散及互换性,从而发挥优秀的强度特性。作为用于确认上述多孔性单一树脂纤维复合材料的板材所包含的多个纤维状粒子的分散性是否得到提高的方法,例如有利用色差计来对上述多孔性单一树脂纤维复合材料的板材的截面进行评价的方法。上述多个纤维状粒子的分散性越优秀,则因凝结的部分少而会更加均匀地呈现出白色,相反,在上述多个纤维状粒子的分散性下降的情况下,因上述多个纤维状粒子相互凝结而重叠的部分增多,从而使这些部分呈现出更深的颜色。可利用色差计来对这种差异进行评价。用于确认上述多孔性单一树脂纤维复合材料的板材所包含的多个纤维状粒子的分散性是否得到提高的间接方法有对强度进行比较的方法。若上述多个纤维状粒子的分散性得到提高,则最终会使上述多孔性单一树脂纤维复合材料的板材的强度得到提高,因而在使包含于上述多孔性单一树脂纤维复合材料的板材的第一纤维状粒子、第二纤维状粒子及粘结材料的种类及含量等不同条件维持恒定的情况下,通过仅改变多个纤维状粒子的分散性来对强度进行比较,例如,可在通过改变制备方法等来制备上述多孔性单一树脂纤维复合材料的板材之后,对强度进行比较。并且,如上所述,可由向多个纤维状粒子赋予单方向取向性来制备的多孔性单一树脂纤维复合材料制备上述多孔性单一树脂纤维复合材料的板材。首先,借助上述粘结材料使上述第一纤维状粒子与上述第二纤维状粒子相粘结,来制备形成具有气孔的不规则的网眼结构的复合材料薄片,之后使多张复合材料薄片层叠并通过冲压成形来制备上述多孔性单一树脂纤维复合材料板材,在此情况下,若向上述复合材料薄片的多个纤维状粒子赋予单方向取向性,则复合材料薄片沿着被赋予上述取向性的方向具有高机械物性。在使这种复合材料薄片单方向层叠之后经过冲压成形所获得的多孔性单一树脂纤维复合材料的板材可沿着特定方向承受很大的力量。可将上述多孔性单一树脂纤维复合材料的板材制成具有适合所需用途的重量,例如,可具有约600g/m2至约3000g/m2的定量,例如,可具有约900g/m2至约1400g/m2(修改)的定量。上述复合材料多孔性单一树脂纤维复合材料的板材的厚度可以为约2mm至约8mm。在本发明的另一实例中,提供一种多孔性单一树脂纤维复合材料的制备方法,包括:将强化纤维及双组分聚合物纤维分散于酸溶液中来准备浆料溶液的步骤;通过湿式抄纸工序由上述浆料溶液形成网的步骤;以及对所形成的上述网进行热处理及干燥来制备多孔性单一树脂纤维复合材料的步骤。上述强化纤维包含第一聚酯类树脂,上述双组分聚合物纤维包含芯部和鞘部,上述芯部包含第二聚酯类树脂,上述鞘部包含第三聚酯类树脂,上述第一聚酯类树脂的强度或熔点与上述第二聚酯类树脂的强度或熔点不同,上述第一聚酯类树脂的强度或熔点与上述第三聚酯类树脂的强度或熔点不同,上述第二聚酯类树脂的强度或熔点与上述第三聚酯类树脂的强度或熔点不同,其中,上述第二聚酯类树脂的熔点高于上述第三聚酯类树脂的熔点。可利用上述多孔性单一树脂纤维复合材料的制备方法来制备前述的上述多孔性单一树脂纤维复合材料。图2为示出根据上述多孔性单一树脂纤维复合材料的制备方法向强化纤维4和双组分聚合物纤维5加热和施加压力来制备多孔性单一树脂纤维复合材料20的方式的图。上述强化纤维4可以为前述的由上述第一聚酯类树脂形成的上述第一纤维状粒子。因此,对于上述强化纤维4的详细说明如同对上述第一纤维状粒子的说明。上述双组分聚合物纤维5包含芯部5a和鞘部5b,上述芯部5a包含第二聚酯类树脂,上述鞘部5b包含第三聚酯类树脂。对于上述第一聚酯类树脂、第二聚酯类树脂及第三聚酯类树脂的详细说明如同上述内容。在上述热处理及干燥步骤中,上述鞘部的第三聚酯树脂被熔融,从而以热熔敷的方式使上述强化纤维与上述双组分聚合物纤维相粘结,来形成具有气孔的不规则的网眼结构。上述鞘部的第三聚酯类树脂先涂敷于上述芯部的状态存在,之后在上述热处理及干燥步骤中得到熔融并转移到上述强化纤维,来对一部分或整个强化纤维进行涂敷,随着熔融状态得到固化,上述鞘部起到用于使上述双组分纤维的芯部及上述强化纤维相粘结的粘结材料的作用。像这样,由于上述鞘部起到粘结材料的作用,在上述多孔性单一树脂纤维复合材料的制备方法中可以无需另外使用额外的粘结材料。通过使形成上述双组分聚合物纤维的鞘部的热塑性树脂具有比较低的熔点,从而具有可以在低温下成形的优点。可通过改变上述双组分聚合物纤维中的芯部和鞘部的含量来对多孔性纤维强化复合材料的气孔率、向强化纤维转移的涂敷程度等进行调节。例如,在双组分聚合物纤维中,相对于100重量份的上述芯部,上述鞘部的重量可为约40重量份至约250重量份。在上述多孔性单一树脂纤维复合材料的制备方法中,使由作为呈现化学疏水性的热塑性树脂的聚酯类树脂制备的双组分聚合物纤维分散于酸溶液中,来制备上述多孔性单一树脂纤维复合材料,不仅如此,还使双组分聚合物纤维包含芯部和鞘部,并提高芯部的比重,从而可呈现出优秀的分散性。如上所述,若使上述双组分聚合物纤维的芯部的比重大于1,则在水溶液中进行搅拌过程中,可有效提高分散率。通过使用上述鞘部经过表面处理的上述强化纤维及上述双组分聚合物纤维,可进一步提高在酸溶液中的分散性,最终,可制备分散性更为优秀的多孔性单一树脂纤维复合材料板材。作为对上述强化纤维及上述双组分聚合物纤维的鞘部进行的表面处理方式,可向表面引入氟基(fluoro)、羟基(hydroxyl)、羧基(carboxyl)、烷基(alkyl)等官能团或可利用涂敷剂进行涂敷。例如,当制备强化纤维及双组分纤维聚合物纤维时,利用浸渍工序等,与上述强化纤维表面或者与上述双组分纤维的聚合物纤维的鞘部的表面相互作用来使可引入上述官能团的表面处理剂与纤维进行反应,由此可制备强化纤维及双组分纤维聚合物纤维。具体地,借助在制备上述强化纤维及上述双组分聚合物纤维时可使用的表面处理剂或涂敷剂来对上述强化纤维或双组分聚合物纤维进行硅烷处理,从而可提高纤维之间的结合力,或可经过碳化(Carbonization)来提高耐热性,或可经过水解(Hydrolysis)来提高亲水性,或可经过氧化(Oxidation)来提高水分散性。例如,可使用氟类蜡(例如,全氟辛酸(PFAO)等)、烃类蜡、硅类聚合物等来作为表面处理剂。根据成分,涂敷剂可以赋予亲水性/疏水性、拒水性、阻燃性、不燃性、耐热性、耐酸性、耐碱性、耐久性、耐污染性等特性。具体地,作为涂敷剂,可使用氟类蜡(例如,全氟辛酸等)、烃类蜡等拒水剂和硅类聚合物增容剂(Compatibilizer)等。可根据所要制备的多孔性单一树脂纤维复合材料所要达到的物性,来对强化纤维双组分聚合物成分的含量比进行调节。例如,上述强化纤维与上述双组分聚合物成分的重量比可以为约25:75至约60:40。具体地,在上述多孔性单一树脂纤维复合材料的制备方法中,可使在每1L的上述酸溶液混合的上述强化纤维及上述双组分聚合物纤维的含量总和达到约0.1g至约10g。通过将上述强化纤维及上述双组分聚合物纤维的纤维总量调节到上述含量范围,可以维持优秀的分散性,从而可制备成厚度均匀的薄片,并可基于优秀的分散性来确保物性。上述酸溶液的pH可以为约1至约4。通过以上述范围来对上述酸溶液的pH进行调节,从而使作为玻璃纤维组合物的二氧化硅(SiO2)或氧化铝(Al2O3)、氧化硼(B2O5)不被强酸化学分解,并使玻璃纤维表面发生电荷,从而可使分散性进一步得到提高。在上述多孔性单一树脂纤维复合材料的制备方法中,在使至少2张制备成薄片形状的上述复合材料薄片层叠之后,通过冲压成形来可将上述多孔性单一树脂纤维复合材料制备成板材。上述多孔性单一树脂纤维复合材料的制备方法还可包括搅拌上述浆料溶液的步骤。通过还执行搅拌上述浆料溶液的步骤,可进一步提高分散性。在上述多孔性单一树脂纤维复合材料的制备方法中,对所形成的上述网进行热处理及干燥的步骤可在约100℃至约180℃的温度下执行。上述温度范围以双组分纤维的鞘部开始被软化(Softening)或被熔融的温度为基准而定。在上述温度低于100℃的情况下,难以进行水分干燥,并且还无法使双组分聚合物纤维(鞘部)充分地得到软化,从而在以复合材料薄片的形状干燥之后,水分残留或导致复合材料薄片难以具有固定的性状。相反,在上述温度高于180℃的情况下,双组分聚合物纤维的鞘部完全被熔融,从而难以均匀地从双组分纤维向强化纤维转移。并且,在温度为熔融温度以上的情况下,还存在引起双组分聚合物纤维的鞘部聚合物变质的隐患。通过适当地调节双组分聚合物纤维的芯部截面直径,并在适当的热处理温度下进行热处理及干燥,从而可使双组分聚合物纤维的芯不被熔融,而包含于由纤维状粒子制备的多孔性单一树脂纤维复合材料的板材中。在执行上述湿式抄纸工序的过程中,在纤维均匀混合于浆料溶液之后,沿着随输送带移动的网眼形成水刺网(Hydro-entangledweb),在多个纤维沿着网眼上升的过程中,通过赋予倾斜度,从而使所制成的上述复合材料薄片具有取向性。像这样,通过使被赋予取向性的复合材料薄片层叠而获得的上述多孔性单一树脂纤维复合材料的板材向纤维成分赋予单方向取向性,从而可更加强化对其单方向的强度。像这样,能够以与所需的用途相符的方式选择性地向上述多孔性单一树脂纤维复合材料的板材赋予取向性。例如,当纤维从流浆箱向输送带移送并形成复合材料薄片时,能够以如下方式设计工序,即,通过向形成上述复合材料薄片的部分赋予倾斜度(inclinedwebformation),从而相对于具有平面性的输送带,可使纤维容易向纵向(MD,Machinedirection)卧倒。可将方向性分为纵向(Machinedirection)和横向(CD,Crossdirection)来赋予,相对于横向,更容易向纵向赋予方向性。上述浆料溶液还可包含交联剂或者额外的粘结剂等添加剂。上述交联剂起到强化强化纤维与双组分聚合物纤维之间的化学结合力的作用,例如,可使用硅烷类化合物、马来酸类化合物等。相对于100重量份的纤维(强化纤维和双组分聚合物纤维之和)总量,上述交联剂的含量可以为约0重量份至约5重量份。作为上述额外的粘结剂可使用:淀粉、酪蛋白、聚乙烯醇(PVA)、羧甲基纤维素钠(CMC)等水溶性聚合物;聚乙烯、聚丙烯、聚酰胺等乳剂类;水泥类、硫酸钙类黏土(Clay)、硅酸钠、硅氧化铝、硅酸钙的无机化合物等。相对于100重量份的纤维(强化纤维和双组分聚合物纤维之和)总量,上述额外的粘结剂的含量可以为约0重量份至约5重量份。上述多孔性单一树脂纤维复合材料的板材由至少2张以上的多张复合材料薄片经过压接而成,具体地,能够以与最终产品所要达到的单位面积重量相对应的方式确定层叠数量。例如,若使用上述复合材料薄片的产品的最终单位面积重量为1200g/m2,则在大致使2张至12张复合材料薄片层叠之后,通过加热和施加压力来进行热冲压成形,由此可制备多孔性单一树脂纤维复合材料的板材。可在可使上述双组分纤维的鞘部被熔融但不使芯部被熔融的温度下,执行上述热冲压成形。若在这种温度范围内执行上述冲压成形,则鞘部被熔融,从而可使上述复合材料薄片之间的接口得到熔敷。具体地,上述热冲压成形以如下方式进行,即,在约100℃至约180℃的温度下施加约1bar至约30bar的压力来对上述复合材料薄片实施叠压并成形,由此可制备多孔性单一树脂纤维复合材料的板材。借助双带冲压成形来以可连续制备多孔性单一树脂纤维复合材料的板材的方式执行上述热冲压成形。根据另一实例,能够以如下方式制备上述多孔性单一树脂纤维复合材料的板材。首先,在配合强化纤维及双组分聚合物纤维之后,在含有添加剂的水溶液中对经过配合的多个纤维进行搅拌,在经过搅拌过程之后,向可形成网的流浆箱(headbox)进行移送。流浆箱内的浆料在经过真空吸气系统的过程中形成水刺网,这在经过干燥器的过程中制备成薄片形态的复合材料薄片。为了日后容易实施热成形,将上述复合材料薄片的每平方米重量设定为约50g至约600g。为了可使双组分聚合物纤维的鞘部起到粘结剂的作用,根据鞘部材料,将干燥温度设定为约100℃至约180℃。在根据用途对制备的复合材料薄片进行切割之后,实施层叠并通过热压接冲压来制备厚度为约2mm至约8mm的板状多孔性单一树脂纤维复合材料的板材。例如,可在约200℃的温度下对上述多孔性单一树脂纤维复合材料的板材进行加热,之后重新向常温的冲压单元移送并进行冲压成形来制成厚度为2~4mm的板材。图3为示意性地示出根据上述一实例说明的多孔性单一树脂纤维复合材料的制备方法的图。以下,记载本发明的实施例及比较例。下述实施例仅仅为本发明的一实施例,而本发明并不局限于下述实施例。实施例实施例1作为双组分聚合物纤维,准备了聚对苯二甲酸乙二醇酯的芯部与低熔点聚对苯二甲酸乙二醇酯的鞘部的重量比为50:50且为了确保水分散性而使长度达到5mm、厚度达到4旦(denier)(约20μm的截面直径)的纤维。上述鞘部的聚对苯二甲酸乙二醇酯为聚对苯二甲酸乙二醇酯中的30摩尔百分比的邻苯二甲酸酯单位被间苯二甲酸单位所取代的熔点为110℃的低熔点聚对苯二甲酸乙二醇酯。作为强化纤维,准备了如下纤维,即,为了防止在进行干燥及预热时的收缩现象,使用了采用300%扁丝的聚对苯二甲酸乙二醇酯纤维,并以13mm的长度来对直径为13μm的聚对苯二甲酸乙二醇酯纤维进行了切割。在将40重量份的上述强化纤维及60重量份的上述双组分聚合物纤维进行配合之后,在以盐酸来调节成PH为2的水溶液中对上述配合纤维进行了1小时的搅拌。在此情况下,在每1L水中,强化纤维及双组分聚合物纤维的纤维总含量为2g。对以如上所述的方式经过搅拌的水溶液浆料执行了湿式抄纸工序,以在流浆箱内通过真空吸入装置形成网。在形成网之后使其经过140℃的箱型干燥机来对水分进行了彻底的干燥。由多孔性单一树脂纤维复合材料制备并经过干燥的复合材料薄片具有300g/m2的定量,并大致呈现出5mm的厚度。在通过使4张薄片层叠来使定量达到1200g/m2之后,在170℃的温度下通过热冲压(Hotpress)工序成形为厚度达5.0mm的板材。在红外线(IR)烤箱内,在200℃的温度下对上述板材进行了2分钟的热处理,并在向常温的冲压单元移送之后施加了压力。在此情况下,所施加的压力为100ton/m2,这相当于无法使板材从模具内部脱离的程度的压力,最终,成形出厚度达2.0mm的板材。在此情况下,压缩率为90%(由4张复合材料薄片层叠而成的复合材料薄片的总厚度从20.0mm被压缩至2.0mm),气孔率为56%。实施例2除了以使板材的定量达到1000g/m2的方式改变薄片的层叠数量之外,以与实施例1相同的方法成形出厚度达2.0mm的板材。在此情况下,压缩率为约87%。实施例3除了以使板材的定量达到1600g/m2的方式改变薄片的层叠数量之外,以与实施例1相同的方法成形出厚度达2.0mm的板材。在此情况下,压缩率为约92%。实施例4以使实施例1中的板材的最终厚度达到1.0mm的方式以95%的压缩率(由4张复合材料薄片层叠而成的复合材料薄片的总厚度从20.0mm被压缩至1.0mm)制备板材。板材的气孔率为13%。实施例5以使实施例1中的板材的最终厚度达到3.0mm的方式以71%的压缩率(由4张复合材料薄片层叠而成的复合材料薄片的总厚度从20.0mm被压缩至3.0mm)制备板材。板材的气孔率为71%。实施例6以使在实施例1的板材的最终厚度达到5.0mm的方式以75%的压缩率(由4张复合材料薄片层叠而成的复合材料薄片的总厚度从20.0mm被压缩至5.0mm)制备板材。板材的气孔率为82%。比较例1除了在实施例1中使用玻璃纤维来代替作为强化纤维来使用的聚酯纤维之外,以与实施例1相同的方式制备板材。比较例2除了在实施例1中使用玻璃纤维来代替作为强化纤维来使用的聚酯纤维中的一半来分别以20重量份的玻璃纤维、20重量份的强化纤维及60重量份的双组分聚合物纤维进行了配合之外,以与实施例1相同的方式制备板材。评价实验例1图4为在实施例1中制备的板材的切割面的扫描电子显微镜照片。如图所示,作为强化纤维的聚对苯二甲酸乙二酯纤维和作为双组分纤维的聚对苯二甲酸乙二酯纤维清楚地呈现于扫描电子显微镜照片中。即,可以确认到基于强化纤维及双组分纤维的各个第一纤维状粒子和第二纤维状粒子完整地形成在板材中。实验例2针对在实施例1至实施例6及比较例1至比较例2中制备的板材,对它们的机械物性进行了比较。首先,在分别将试片在常温下放置24小时之后测定出机械物性。并以美国材料与试验协会的D638为基准来对厚度为2mm的样本测定出拉伸强度和拉伸率,在常温下以美国材料与试验协会的D3763基准来实施了落球冲击试验并进行了测定。同样,以美国材料与试验协会的D256为基准来实施了缺口冲击试验(NotchedIZOD),并将结果记载于下表1中。表1与比较例1相比,实施例1中的作为强化纤维来使用的聚酯纤维相对于玻璃纤维呈现出低强度,但互换性得到提高,从而可确认到整体复合材料的拉伸强度提高了15%。并且,聚对苯二甲酸乙二酯纤维自身的拉伸率为约40%,玻璃纤维自身拉伸率为5%,因而聚对苯二甲酸乙二酯纤维的拉伸率达到玻璃纤维拉伸率的约8倍,从而整体复合材料的拉伸率达到了约10倍。由此,实施例1的多孔性单一树脂纤维复合材料的板材即使在外部的高强度和高变形条件下也具有低模量值,从而具有不断裂的性质。并且,实施例1中呈现出的落球冲击强度值和冲击能量的冲击强度值高于比较例1中的落球冲击强度值和冲击能量的冲击强度值,原因在于,模量相对低于玻璃纤维的复合材料中的聚酯纤维(强化纤维)使基于外部冲击的能量得到分散。并且,聚酯纤维的密度为约1.38g/cm3,玻璃纤维的密度为2.7g/cm3,聚酯纤维的密度比玻璃纤维的密度低约50%,因而即使在实施例1及比较例1中制备表面比重和重量相同的板材,但实施例1的板材的纤维数量更多。由此提高分散基于外部冲击而产生的能量的概率,因而可知冲击强度得到了提高。在以如同比较例2的方式通过混合聚合物纤维和玻璃纤维来用作强化纤维的情况下,相对于比较例1,拉伸率略微增加,但仍然低于实施例1,拉伸强度及冲击强度呈现出同等以下水平。其原因在于,在将复合材料制备成薄片或板材的情况下,若纤维种类增加,则纤维之间的斥力增加,从而使分散性下降,并且导致热成形之后的纤维之间的互换性(compatibility)下降。由此,在比较例1和比较例2中,由于将玻璃纤维用作强化纤维,从而使机械物性的提高效果下降,由单一树脂的纤维来组成复合材料的实施例1呈现出最高的机械物性。在实施例2至实施例3中,以在厚度与实施例1中的厚度相同的情况下使定量分别达到1000g/m2和1600g/m2的方式制备多孔性单一树脂纤维复合材料的板材。如表1所示,定量越增加,复合材料的密度增加,因而可知,具有虽然使拉伸强度增加但导致拉伸率减少的倾向。实验例3对实施例1至实施例3的板材比较了吸音性能方面的物性。以KS2816-2基准对各个板材测定出吸音性能。并将结果记载于表2中。表2在表2中,在实施例1至实施例3中均制备相同厚度的板材,由于以改变定量的方式制成,因而随着定量的增加,密度上升。随着定量的增加使板材的密度增加,则会使表面积增加,随着表面积的增加,会使借助板材振动的吸音效果增加,从而在低频区域中呈现出共振频率(Resonancefrequency)特性,由此可知,即使在低通气率特性下,也会对低频呈现出高吸音系数。另一方面,在高频区域中,借助纤维的振动而呈现出吸音效果,在实施例1中,因基于纤维振动的吸音效果优秀而使高频吸音性能最为优秀。在实施例3中,因包含高密度压缩的纤维而使气孔率下降,从而使基于聚对苯二甲酸乙二酯纤维的吸音效果下降,因而呈现出低吸音系数。相反,在实施例2中,纤维的压缩程度低于实施例1,因而在基于纤维振动的吸音性能方面比较有利,但是,由于纤维的含量下降,因而高频吸音性能反而更低于实施例1。因此,可知高频吸音性能需要通过将纤维的含量和气孔率调节到适当水平来实现。图5为在实施例1中制备的板材的表面的光学显微镜图像,图6为在实施例2中制备的板材的表面的光学显微镜图像,图7为在实施例3中制备的板材的表面的光学显微镜图像。依次对定量最低的实施例2的图6、实施例1的图5及定量最高的实施例3的图7进行观察可以确认到,因双组分纤维的鞘部被熔融,当形成板材中的粘结材料时,通过均匀的凝聚并经过膜化来形成平滑的表面。相反,若板材形成为更像膜的结构,则形成气孔闭合的结构,从而吸音性能反而下降。尽管如此,在所形成的开放气孔最多的实施例2中,由于纤维的含量下降,因而吸音性能反而低于比实施例1。实验例4对实施例1、实施例3至实施例6的板材评价了弯曲强度(破坏材料所需的压力)和弯曲刚性(使材料的变形达到规定程度所需的力量)。根据美国材料与试验协会D790来对三个位置测定弯曲强度和弯曲刚性,并将结果记载于下表3中。表3弯曲强度(MPa)弯曲刚性(N/mm)实施例1350.35实施例3500.43实施例4400.17实施例5280.70实施例6121.20随着压缩率的增加,气孔在材料内部中所占的比值减少,从而使弯曲强度得到提高,但由于材料的厚度下降,因而当施加规定力量时,因板材的弯曲性质增加而使弯曲强度和弯曲刚性具有相互权衡的性质。因此,根据用途,有必要以适当范围的厚度来成形。在实施例3中,若板材密度增加,则会使强化纤维自身的含量增加,从而使弯曲强度和弯曲刚性均得到增加。但是,在仅改变压缩率来对以相同密度制备的复合材料薄片进行比较的情况下,弯曲强度和弯曲刚性呈现出不同倾向性。相对于实施例1,在实施例4中,因压缩率增加而使弯曲强度得到提高,但可确认到弯曲刚性大幅度下降。相反,相对于实施例1,在实施例5中,因压缩率下降而使弯曲强度下降,但可确认到弯曲刚性提高到了2倍左右。如实施例6,在大幅度降低压缩率的情况下,可确认到,弯曲刚性得到增加,但弯曲强度却大幅度下降。从而可确认到弯曲强度和弯曲刚性的反比关系。在将多孔性单一树脂纤维复合材料用作汽车或建筑用材料的情况下,材料不应被从外部施加的力量所破坏,且材料的规定部分不应出现变形。可知,在为了符合特定用途而制备成板材的情况下,以具有适当压缩率(或者气孔率)的方式进行成形,从而可呈现出机械物性的最佳平衡。例如,当用作汽车或建筑用材料时,上述多孔性单一树脂纤维复合材料满足合适的弯曲强度和弯曲刚性的条件为压缩率为80~95%、气孔率(以体积比例为基准)在40~80%的范围内。实验例5在对实施例1及比较例1至比较例2中的板材分别制备200mm(横向)×200mm(纵向)×2mm(厚度)大小的样本之后,对热导率进行了测定。(请告知美国材料与试验协会的测定基准或设备。需告知设备的制备公司和型号。)并将测定结果记载于下表4中。表4热导率(W/mK)实施例10.03比较例10.035比较例20.035在表4中,在以如实施例1的方式仅由聚合物纤维组成复合材料的情况下,相对于比较例1中的作为强化纤维来使用玻璃纤维的复合材料,呈现出低热导率,因而可确认到具有优秀的隔热性能。原因在于,基于聚合物纤维的导热效果相对低于基于玻璃纤维的导热效果。在以如比较例2的方式使用玻璃纤维和聚合物纤维等两种纤维的情况下,与实施例1相比较,虽然部分使用了聚合物纤维,但热导率并未减少。原因在于,在比较例2中,纤维的分散性反而下降,从而使气孔率下降,由此使基于纤维的直接导热效果增加。因此,对于实施例1的板材,可期待其优秀的隔热效果,这适合用作汽车或建筑用材料。以上,对本发明的多个优选实施例进行了详细的说明,但本发明的权利范围并不局限于此,利用在以下发明要求保护范围中所定义的本发明的基本概念来由本发明所属
技术领域:
的普通技术人员实施的多种变形及改良形态也属于本发明的权利范围。附图标记的说明1:第一纤维状粒子2:第二纤维状粒子3:粘结材料4:强化纤维5:双组分聚合物纤维5a:芯部5b:鞘部10、20:多孔性单一树脂纤维复合材料当前第1页1 2 3