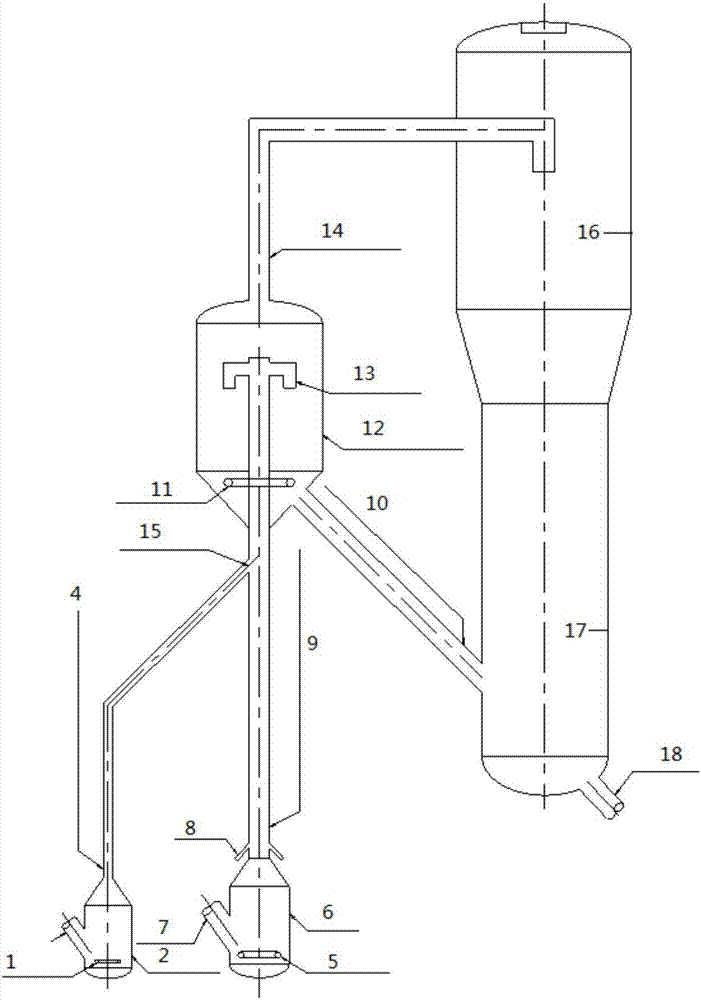
本发明涉及化工
技术领域:
,尤其是涉及一种提升管及其组成的流化催化裂化装置。
背景技术:
:随着原油资源的日益匮乏以及化工原料的多元化和规模化,原油加工少产气体多产轻质油已经成为一种长期趋势,而催化裂化作为主要的原油二次加工工艺,其技术发展适应这一趋势要求显得更为重要。目前,在石油化工行业,常规的提升管催化裂化装置普遍存在以下两方面的主要问题。(1)反应时间长、柴油产品质量差:提升管反应器的反应时间一般大于3秒(由提升管长度或工艺形式决定),过长的反应时间加剧了原料生成物的过裂化反应(即所谓的二次反应),导致裂化气产率高,汽、柴油馏分收率降低,生成的催化柴油质量也随着反应时间的延长逐渐变差。(2)再生催化剂温度高、剂油比低催化剂的再生温度一般在670~720℃。受装置热平衡限制,较高再生催化剂温度使重油提升管反应器的剂油比相对较低,一般为5~7;为此,国内外各大石油公司纷纷致力于新型的催化裂化工艺技术的研究与开发。中石化洛阳工程有限公司开发的fdfcc-ⅲ以及石油大学(北京)开发的mzcc工艺贯穿了“油剂低温接触、大剂油比”的技术理念。fdfcc-ⅲ工艺技术工业实施结果表明,“油剂低温接触、大剂油比”技术抑制了遵照自由基机理进行的热裂化反应,强化了正碳离子机理的催化裂化反应,使催化裂化产品选择性得到改善。uop与cepoc公司联合开发的milliscondcatalyticcrackingprocess(mscc)工艺技术,stone&webster,texco公司以及清华大学化工系曾经研究的气固超短接触下行床反应技术等。这些技术的共同点都是通过改变反应器的型式达到缩短反应时间(在1秒以内)的目的,从而减少反应器内油气的二次反应,降低焦炭、干气产率,提高轻质油收率。mscc工艺(美国专利usp5462652)的技术特点为:a.催化剂为常规fcc催化剂或专用催化剂。b.反应沉降器上部设置催化剂混合罐,混合罐采用水蒸汽进行催化剂的均匀混合;反应沉降器顶部设置混合催化剂室,催化剂由混合催化剂室中心开口进入反应沉降器。c.催化剂与原料的反应以及待生催化剂的汽提均在反应沉降器中进行,催化剂流动方向向下,原料喷射方向与催化剂流动方向成90度角,反应沉降器外挂旋风分离器。d.一部分待生催化剂由第一根提升管提升至再生器进行烧焦再生,另一部分待生催化剂由第二根提升管提升至催化剂混合罐,再生后的催化剂由第三根提升管提升至催化剂混合罐与待生催化剂混合来降低进入反应沉降器的混合催化剂温度。由于以上技术特征,mscc技术在反应沉降器中实现原料短反应时间、低油剂接触温度、大剂油比操作,使装置的干气、焦炭产率下降,液体收率大幅度提高,产品分布得到改善。目前,mscc工艺技术已成功进行了工业实施。与常规fcc相比,mscc的干气产率降低2%,汽柴油产率提高11v%。20世纪90年代初期,美国derby炼油厂将其50万t/afcc装置改造为mscc工业试验装置,原料油中掺有近20%的脱沥青油(dao),由于要求汽油的(r+m)/2不低于87,使得提升管裂化操作是在过裂化模式下运行。结果表明,由于mscc工艺的短油剂接触时间,使得干气的选择性大大改善,并且由于催化剂炭差下降,降低了再生温度而增加了剂油比。因此,原料油的转化率从60%~80%提高到70%~85%,特别是汽油选择性明显提高(汽油产率增加约13%),同时液体产品(包括液化气、汽油和柴油)总收率也增加。此外,其氢气产量和氢/甲烷比下降约25%,对ni的耐受性增强,并减少了补剂量。汽油辛烷值和柴油十六烷值也均有所提高。2002年,美国的flyingj炼油厂将其50万吨/年移动床催化裂化装置改造为mscc装置。目前mscc技术已有2套工业化装置正在运转。一套位于coastal公司的eaglepoint炼油厂,处理能力为280万吨/年;另一套建在tranamerican炼油公司,处理能力为500万吨/年。采用mscc技术改造前后的典型生产数据如下表1。表1产品常规fccmscc干气,%4.02.0烷基化原料,v%16.021.0汽油+轻循环油,v%74.085.0塔底重油,v%11.04.0尽管mscc工艺技术有诸多的优势,但仍存在以下不足:(1)在大剂油比操作中,参与反应的催化剂为再生催化剂和待生催化剂的混合物,该混合催化剂对原料的裂化活性较低,势必对产品分布带来不利影响。(2)工艺过程及操作复杂。在现有催化裂化工业装置上进行mscc工艺改造根本无法进行(除非新建装置)。使其难以推广、普及到各大炼厂。综上所述,通过对现有催化裂化装置的工艺设备加以改进,实现短反应时间、大剂油比操作,可降低裂化气和焦炭产率,提高轻质油收率,对以催化裂化工艺为主导的我国炼油工业具有重要的意义。为此中石化炼化工程(集团)股份有限公司洛阳技术研发中心开发的毫秒流化催化裂化(millisecondfluidcatalyticcracking,简称mfcc)工艺采用短反应时间(0.3~1.2秒)和大剂油比(7~12)的技术措施,与常规fcc相比可使干气产率降低40%左右,液化气降低2~5个百分点,轻油收率提高3~7个百分点,焦炭产率略有降低,产品性质明显改善,催化裂化装置的经济效益得到显著提高。该工艺技术与中国石化的主业发展密切相关,应具有广泛的应用前景。3、mfcc工艺的技术原理与技术特征(1)缩短反应时间,抑制二次反应。催化裂化为一典型的平行顺序反应过程。随着反应时间的延长,生成油气二次反应加剧,产品选择性恶化;若缩短反应时间,则可以减少二次反应,改善产品选择性;mfcc工艺采用新型反应器实现短反应时间(0.3~1.2秒)操作,最大程度的抑制生成油气二次反应。(2)进行大剂油比操作,确保原料的单程转化深度。大幅缩短反应时间会使原料的单程转化率下降,而提高反应温度、提高催化剂活性或剂油比均可以弥补由于反应时间缩短造成的原料转化率损失。提高反应温度会使热裂化反应加剧,采用高活性催化剂或提高装置催化剂的平衡活性则要付出高昂的代价,因此,宜选择适当提高装置操作剂油比,即提高催化剂的动态活性来确保原料的单程转化深度。mfcc工艺正是采用相对较高的剂油比(7~12)进行催化裂化操作以克服反应时间缩短对反应过程的负面影响。(3)采用催化剂二次注入提升管反应器的方法,实现提升管反应器催化剂接力反应。从而保证提升管反应器的单程转化率,消除提升管反应器反应时间短,单程转化率低的影响。虽然相比fcc工艺,mfcc工艺有诸多优点,但如何以较低的成本将fcc工艺替换为mfcc工艺是目前要解决的主要问题。有鉴于此,特提出本发明。技术实现要素:本发明的第一目的在于提供一种提升管,所述的提升管解决了常规fcc工艺替换为mfcc工艺需要全面更换设备导致成本极高的问题。本发明的第二目的在于提供一种流化催化裂化装置,该装置只需要在常规fcc装置的提升管的中间段增设沉降分离器即可,因此,更新工艺的成本低,极易推广。为了实现以上目的,本发明提供了以下技术方案:一种提升管,由下至上依次包括预提段、第一裂化反应段、第一沉降分离段、第二裂化反应段和第二沉降分离段;所述第一沉降分离段和所述第二沉降分离段内均设置沉降分离器。本发明的提升管能适用于mfcc工艺,即实现“油剂低温接触、大剂油比”的催化裂化技术,并且与传统的fcc提升管反应器相比,改动较小,只需要在现有的提升管中部(本发明所述的中部位置并非正中央,而是由裂化反应时间所决定)位置增设沉降分离器,以便预先对裂化反应产物进行油剂分离,从而达到终止催化裂化反应的目的。换言之,本发明的提升管是通过增设的沉降分离器(对应第一沉降分离段中的沉降分离器)将现有的提升管分为两个反应段,第一反应段(即第一裂化反应段)为重要的裂化反应段,由于空间长度缩短,反应时长也必然缩短,因此可实现短期反应的目的,避免过裂化反应。在第一沉降分离段,油剂分离后,待生催化剂回收,油气进入第二裂化反应段,在此反应段油气反应终止或者发生微弱的催化裂化反应,由于缺乏催化剂,因此此段内的催化裂化反应并非过裂化反应。之后物料进入第二沉降分离段,经过油剂分离,收集各种油气。综上可知,本发明的提升管与传统fcc工艺所用的提升管的反应结构以及长度差异不大,因此,将fcc工艺替换为mfcc工艺时,只需要在提升管的中间段增设沉降分离器即可,避免全面更换设备,因此,更新成本低,极易推广。以上提升管的结构还可以从以下方面改进,例如:优选地,所述第二沉降分离段远离所述第二裂化反应段的一端还连接有汽提段,所述第一沉降分离段的固体排出口通入所述汽提段。该汽提段与现有提升管中的汽提段作用相同,即用水蒸气脱除催化剂上吸附的油气及置换催化剂颗粒之间的油气,以免其被催化剂夹带至催化剂再生器,增加再生器的烧焦负荷。所述第一沉降分离段的固体排出口即为催化剂的排出口,该出口的位置优选高于所述汽提段中催化剂的入口位置,以便利用重力作用使催化剂自流入汽提段中,节省能耗,为此,汽提段可与第一沉降分离段平行并列设置。优选地,所述第二裂化反应段还设有催化剂注入口。在第二裂化反应段注入新鲜或再生的催化剂,通过调整低的剂油比,使油气在少量催化剂的作用下发生有益的裂化反应,而非过裂化反应,可在一定程度上提高汽、柴油馏分收率。换言之,在第二裂化反应段注入新鲜或再生的催化剂,能保证提升管反应器的单程转化率,消除第一段提升管反应器反应时间短,单程转化率低的影响。优选地,所述第一沉降分离段中在沉降器的底部还设有汽提分布环。该汽提分布环与传统汽提段的作用相同,可以脱除第一次沉降分离后催化剂上吸附的油气及置换催化剂颗粒之间的油气。优选地,所述第一裂化反应段的上部还设有催化剂注入口。同样,除了预提段供应的催化剂外,在第一裂化反应段的上部通过催化剂注入口注入新鲜或再生的催化剂,可以提高剂油比,从而提高裂化效果。优选地,所述第一沉降分离段和所述第二沉降分离段内中的沉降分离器为三叶槽快分头型或弹射分离快分头型。本发明对沉降分离器的型号不做限制,并且所述第一沉降分离段和所述第二沉降分离段内中的沉降分离器可采用相同或不同的类型。本发明的提升管用于流化催化裂化工艺时,还应当搭配其他的必要设备组成流化催化裂化整体装置,例如还包括催化剂再生器,所述汽提段与所述催化剂再生器连接。催化剂再生是催化裂化中很重要的一个流程,可以很大程度降低成本,延长装置寿命。优选地,还包括再生料仓。再生料仓可作为中转站,为提升管供应再生催化剂。优选地,所述第二裂化反应段设有催化剂注入口时,所述再生料仓与所述第二裂化反应段的所述催化剂注入口连接。即再生料仓为第二裂化反应段提供较少量的再生催化剂,促进有利于生成汽柴油的反应进行。优选地,所述第一裂化反应段设有催化剂注入口时,所述再生料仓与所述第一裂化反应段的所述催化剂注入口连接。随着反应的进行,第一裂化反应段的上部的催化剂活性降低,此时向其中步入催化剂,可保证第一裂化反应段内的催化剂活性一致,有利于提高汽柴油的收率。综上,与现有技术相比,本发明达到了以下技术效果:(1)本发明既可避免过裂化反应,又可以降低装置替换的难度,降低了工艺更新的门槛,使mfcc工艺更易推广;(2)通过设置催化剂的补充结构可以实现提升管内催化剂的接力反应,从而保证提升管反应器的单程转化率,消除第一段提升管反应器反应时间短,单程转化率低的影响。附图说明为了更清楚地说明本发明具体实施方式或现有技术中的技术方案,下面将对具体实施方式或现有技术描述中所需要使用的附图作简单地介绍,显而易见地,下面描述中的附图是本发明的一些实施方式,对于本领域普通技术人员来讲,在不付出创造性劳动的前提下,还可以根据这些附图获得其他的附图。图1为本发明实施例1提供的流化催化裂化装置的示意图;图2为本发明实施例2提供的流化催化裂化装置的示意图;图3为本发明实施例3提供的流化催化裂化装置的示意图;附图标记:1-气体分布环,2-再生剂料仓,3-再生剂管,4-再生剂输送提升管,5-预提段分布环,6-预提段,7-再生斜管,8-原料喷嘴,9-第一段提升管反应器,10-待生剂循环管,11-粗汽提分布环,12-油、剂分离沉降器,13-油、剂经快速分离器,14-第二段提升管反应器,15-再生剂注入口,16-沉降器,17-汽提段,18-待生斜管。具体实施方式下面将结合附图和具体实施方式对本发明的技术方案进行清楚、完整地描述,但是本领域技术人员将会理解,下列所描述的实施例是本发明一部分实施例,而不是全部的实施例,仅用于说明本发明,而不应视为限制本发明的范围。基于本发明中的实施例,本领域普通技术人员在没有做出创造性劳动前提下所获得的所有其他实施例,都属于本发明保护的范围。实施例中未注明具体条件者,按照常规条件或制造商建议的条件进行。所用试剂或仪器未注明生产厂商者,均为可以通过市售购买获得的常规产品。本发明的核心在于催化裂化装置中的提升管有如下结构改进:一种提升管,由下至上依次包括预提段、第一裂化反应段、第一沉降分离段、第二裂化反应段和第二沉降分离段;所述第一沉降分离段和所述第二沉降分离段内均设置沉降分离器;所述预提段、所述第一裂化反应段、所述第一沉降分离段和所述第二裂化反应段优选同轴设置。本发明的提升管能适用于mfcc工艺,即实现“油剂低温接触、大剂油比”的催化裂化技术,并且与传统的fcc提升管反应器相比,改动较小,只需要在现有的提升管中部(本发明所述的中部位置并非正中央,而是由裂化反应时间所决定)位置增设沉降分离器,以便预先对裂化反应产物进行油剂分离,从而达到终止催化裂化反应的目的。换言之,本发明的提升管是通过增设的沉降分离器(对应第一沉降分离段中的沉降分离器)将现有的提升管分为两个反应段,第一反应段(即第一裂化反应段)为重要的裂化反应段,由于空间长度缩短,反应时长也必然缩短,因此可实现短期反应的目的,避免过裂化反应。在第一沉降分离段,油剂分离后,待生催化剂回收,油气进入第二裂化反应段,在此反应段油气反应终止或者发生微弱的催化裂化反应,由于缺乏催化剂,因此此段内的催化裂化反应并非过裂化反应。之后物料进入第二沉降分离段,经过油剂分离,收集各种油气。不同实施例在此核心结构上做如下优化:优选地,所述第二沉降分离段远离所述第二裂化反应段的一端还连接有汽提段,所述第一沉降分离段的固体排出口通入所述汽提段。优选地,所述第二裂化反应段还设有催化剂注入口。优选地,所述第一沉降分离段中在沉降器的底部还设有汽提分布环。优选地,所述第一裂化反应段的上部还设有催化剂注入口。优选地,所述第一沉降分离段和所述第二沉降分离段内中的沉降分离器为三叶槽快分头型或弹射分离快分头型。实施例1流化催化裂化的装置如图1所示:来自再生器的再生催化剂(或者新鲜催化剂)首先进入预提段6,内设有预提段分布环5以使催化剂充分流化,预提段6内还设置再生斜管7,以通过再生催化剂。在预提升汽及经原料喷嘴8喷入的原料油双重作用下,催化剂与原料油一同进入第一段提升管反应器9,进行催化裂化反应。当达到mfcc工艺要求的反应时间后(即第一段反应的长度与所需的反应时间有关),油、剂经快速分离器13进入油、剂预分离沉降器12,并被迅速分离。分离后的待生催化剂被来自粗汽提分布环11的汽提蒸汽初步汽提后,经待生剂循环管10进入汽提段17;分离后油气进入第二段提升管反应器14。进入第二段提升管反应器14的油气与来自再生剂料仓2经再生剂输送提升管4、再生剂注入口15注入的再生剂继续进行催化裂化反应。从而保证提升管反应器的单程转化率,消除第一段提升管反应器反应时间短,单程转化率低的影响。反应完成后,油、剂一同进入沉降器16分离。分离出的油气从顶部引入分馏塔分馏出合格产品;待生剂经汽提段17充分汽提后经待生斜管18引入再生器烧焦。再生完成后的再生剂被重新引入再生剂料仓2和预提升段6,完成整个循环过程。再生剂料仓中设有气体分布环1,以便利用气体将再生催化剂提升至反应器中,还设有再生剂管3以接入再生器(图中未示出)中。从图1中可看出,预提段6、第一段提升管反应器9、快速分离器13和第二段提升管反应器为同轴设置,以便原料的高效运输,提高能源利用率。实施例2与实施例1的区别在于再生剂注入口的位置不同:在第一段提升管反应器9未完全完成反应之前,注入再生催化剂,增大第一段提升管反应器9反应的剂、油比,以这种形式来保证提升管反应器的单程转化率,消除第一段提升管反应器反应时间短,单程转化率低的影响。该实施例的其它工艺过程同实施例1。实施例3工艺过程与是附图1结构的工艺过程完全相同。其结构特征是:将实施例1的油、剂预分离沉降器中的快速分离器13结构由三叶槽快分头改变为弹射分离快分头。该实施例的其它工艺过程同实施例1。最后应说明的是:以上各实施例仅用以说明本发明的技术方案,而非对其限制;尽管参照前述各实施例对本发明进行了详细的说明,本领域的普通技术人员应当理解:其依然可以对前述各实施例所记载的技术方案进行修改,或者对其中部分或者全部技术特征进行等同替换;而这些修改或者替换,并不使相应技术方案的本质脱离本发明各实施例技术方案的范围。当前第1页12