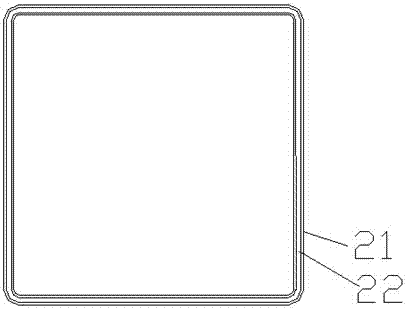
本发明涉及客车技术领域,具体涉及一种排气系统装置。
背景技术:随着客车排放标准的不断提高,客车排气系统越来越大,组合也越来越复杂。与此同时,随着排放标准的不断增高,客车排气系统产生的热源、噪音相对越来越大。目前,由于现有的客车排气系统安装机构不适用于针对欧六、京五等排放标准设计客车排气系统,使针对欧六、京五等排放标准设计的客车排气系统安装起来非常困难,存在安装误差,且无法对客车排气系统产生的热源及噪音进行隔绝,影响整车的舒适性。
技术实现要素:本发明的目的在于提供一种排气系统装置,该排气系统装置适用于针对欧六、京五等排放标准设计的客车排气系统,能够使上述客车排气系统快速准确地装配在客车车身上,且能够对客车排气系统产生的热源及噪音进行隔绝,提高整车的舒适性。为实现上述目的,本发明采用了以下技术方案:一种排气系统装置,包括隔热框架和嵌入设置在隔热框架内部的排气系统吊架与排气系统托架。所述隔热框架的上下两端分别通过悬置软垫及螺栓安装在车身底架上;所述排气系统吊架的顶部通过悬置软垫及螺栓安装在隔热框架顶部内侧;所述排气系统托架的底部通过悬置软垫及螺栓安装在隔热框架底部内侧。所述隔热框架包括中空的长方形框架和嵌入设置长方形框架内的隔热保护层。所述排气系统吊架包括吊架主体和焊接在吊架主体上的第一箍带;所述吊架主体包括对称设置的左吊架和右吊架;所述左吊架和右吊架的结构相同,均包括依次折弯相连的第一圆弧板、第一纵向板、横向板、第二纵向板和第二圆弧板;所述第一纵向板,其上端与横向板的内端垂直相连,其下端与第一圆弧板的上端相连;所述第二纵向板,其上端与横向板的外端垂直相连,其下端与第二圆弧板的上端相连;所述横向板上开设有第一腰形安装孔;所述第一圆弧板和第二圆弧板的内径与第一箍带的外径相等;所述第一箍带包括对称设置且螺栓配合的左半箍带和右半箍带;所述左半箍带,其中上部与左吊架的第一圆弧板的内侧焊接相连,其中下部与左吊架的第二圆弧板的内侧焊接相连;所述右半箍带,其中上部与右吊架的第一圆弧板的内侧焊接相连,其中下部与右吊架的第二圆弧板的内侧焊接相连。所述排气系统托架包括托架主体和焊接在托架主体顶部的第二箍带;所述托架主体包括托架安装板、垂直焊接在托架安装板左右两端顶部的第二箍带左侧连接板与第二箍带右侧连接板以及焊接在托架安装板中段顶部的第二箍带支撑板;所述第二箍带包括焊接在第二箍带左侧连接板、第二箍带支撑板和第二箍带右侧连接板顶部的第二下箍带以及与第二下箍带螺栓连接的第二上箍带;所述托架安装板的左右两端分别开设有第二左侧腰形安装孔和第二右侧腰形安装孔。所述悬置软垫包括依次设置的钢板、橡胶块主体和橡胶块凸起;所述钢板、橡胶块主体和橡胶块凸起上开设有依次相贯通的安装通孔。所述第二箍带支撑板为依次设置在托架安装板中段顶部前后两侧的两个;所述第二箍带左侧连接板、第二箍带右侧连接板以及第二箍带支撑板的顶部均为与箍带外周相适应的圆弧状。所述第二左侧腰形安装孔位于第二箍带左侧连接板的外侧,且在第二左侧腰形安装孔前后两侧的托架安装板上分别设有第一前侧加强筋和第一后侧加强筋;所述第一前侧加强筋和第一后侧加强筋,其内侧壁分别焊接在第二箍带左侧连接板外侧壁的前后两端,其底部分别焊接在托架安装板左端前后两侧的顶部。所述第二右侧腰形安装孔位于第二箍带右侧连接板的外侧,且在第二右侧腰形安装孔前后两侧的托架安装板上分别设有第二前侧加强筋和第二后侧加强筋;所述第二前侧加强筋和第二后侧加强筋,其内侧壁分别焊接在第二箍带右侧连接板外侧壁的前后两端,其底部分别焊接在托架安装板右端前后两侧的顶部。所述隔热保护层采用HKO硅胶高硅氧复合材料。由以上技术方案可知,本发明采用上吊下托的形式来固定安装客车排气系统,即采用排气系统吊架来固定安装催化消声器,采用排气系统托架来固定安装颗粒物捕集器,能够有效利用有限的客车空间,降低排气系统的装配难度,提高排气系统的装配精度;通过在排气系统吊架及排气系统托架的外侧设置隔热框架,既能够对排气系统吊架及托架起到良好的固定与支撑作用,又能够对发动机舱和发动机的排气系统进行有效的隔离,有效阻滞发动机排气系统的热量向发动机舱传递,避免排气系统产生的热量传递至发动机舱使发动机舱温度升高而影响整车发动机热平衡;通过在隔热框架上下两端与车身底架的连接处设置悬置软垫,并在排气系统托架、排气系统吊架与隔热框架之间分别设置悬置软垫,能够从上下两个方向防止隔热框架抖动,减小排气系统震动及噪声。本发明适用于针对欧六、京五等排放标准设计的客车排气系统,能够使上述客车排气系统快速准确地装配在客车车身上,且能够对客车排气系统产生的热源及噪音进行隔绝,提高整车的舒适性。附图说明图1是本发明的装配结构示意图;图2是隔热框架的结构示意图;图3是排气系统吊架的主视图;图4是左吊架的主视图;图5是左吊架的俯视图;图6是排气系统托架的主视图;图7是排气系统托架的侧视图;图8是托架主体的主视图;图9是托架主体的俯视图;图10是悬置软垫的结构示意图。其中:1、悬置软垫,11、钢板,12、橡胶块主体,13、橡胶块凸起,14、安装通孔,2、隔热框架,21、长方形框架,22、隔热保护层,3、排气系统吊架,31、左吊架,311、第一圆弧板,312、第一纵向板,313、横向板,314、第二纵向板,315、第二圆弧板,33、左半箍带,34、右半箍带,4、排气系统托架,41、托架主体,411、托架安装板,412、第二箍带左侧连接板,413、第二箍带支撑板,414、第二箍带右侧连接板,415、第一前侧加强筋,416、第二前侧加强筋,417、第二左侧腰形安装孔,418、第二右侧腰形安装孔,419、第一后侧加强筋,410、第二后侧加强筋,42、第二下箍带,43、第二上箍带,5、车身底架,6、催化消声器,7、颗粒物捕集器。具体实施方式下面结合附图对本发明做进一步说明:如图1-图10所示的一种排气系统装置,包括隔热框架2和嵌入设置在隔热框架2内部的排气系统吊架3与排气系统托架4。排气系统吊架用于固定安装催化消声器6,排气系统托架4用于固定安装颗粒物捕集器7。所述隔热框架2的上下两端分别通过悬置软垫1及螺栓安装在车身底架5上。所述排气系统吊架3的顶部通过悬置软垫1及螺栓安装在隔热框架2顶部内侧。所述排气系统托架4的底部通过悬置软垫1及螺栓安装在隔热框架2底部内侧。本发明通过在隔热框架的上、下两端与车身底架之间设置A悬置软垫,并同时在隔热框架与排气系统吊架、排气系统托架之间设置与A悬置软垫对置的B悬置软垫,能够从上下方向上对排气系统及隔热框架的震动起到良好的减震缓冲作用,对排气系统进行有效的保护。如图2所示,所述隔热框架1包括中空的长方形框架21和嵌入设置长方形框架21内的隔热保护层22。所述隔热框架的上、下两端分别开设有4个安装孔,每个安装孔对应着一对悬置软垫。隔热框架上端的4个安装孔,用于通过螺栓将车身底架5、隔热框架的上端及排气系统吊架连接为一体。以隔热框架上端的一个安装孔为例,在车身底架与隔热框架的顶部之间设有第一个悬置软垫,该悬置软垫的钢板位于上方,橡胶块凸起位于下方;在隔热框架顶部的内侧与排气系统吊架之间设有第二个悬置软垫,该悬置软垫的橡胶块凸起位于上方,钢板位于下方;将一根螺栓依次穿过车身底架,第一个悬置软垫的钢板、橡胶块主体、橡胶块凸起,隔热框架的顶部,第二个悬置软垫的橡胶块凸起、橡胶块主体、钢板,吊架安装板,从而将车身底架、第一个悬置软垫、隔热框架、第二个悬置软垫和排气系统吊架可拆卸连接为一体。其他隔热框架上的安装孔及其他悬置软垫同理。所述隔热保护层22采用HKO硅胶高硅氧复合材料,该材料耐温1000℃,隔热效果好,且不含石棉等有害物质。所述的隔热保护层22为导热系数极低的隔热材料,能够有效阻滞发动机排气系统的热量向发动机舱传递,避免排气系统产生的热量传递至发动机舱使发动机舱温度升高而影响整车发动机热平衡。如图3-图5所示,所述排气系统吊架3包括吊架主体和焊接在吊架主体上的第一箍带。所述吊架主体包括对称设置的左吊架31和右吊架32。所述左吊架31和右吊架32的结构相同,均采用一块钢板折弯而成。所述左吊架31和右吊架32均包括依次折弯相连的第一圆弧板311、第一纵向板312、横向板313、第二纵向板314和第二圆弧板315。所述第一纵向板312,其上端与横向板313的内端垂直相连,其下端与第一圆弧板311的上端相连。所述第二纵向板314,其上端与横向板313的外端垂直相连,其下端与第二圆弧板315的上端相连。所述横向板313上开设有第一腰形安装孔。所述第一圆弧板311和第二圆弧板315的内径与第一箍带的外径相等。所述第一箍带包括对称设置且螺栓配合的左半箍带33和右半箍带34。所述左半箍带33,其中上部与左吊架31的第一圆弧板的内侧焊接相连,其中下部与左吊架31的第二圆弧板的内侧焊接相连。所述右半箍带34,其中上部与右吊架32的第一圆弧板的内侧焊接相连,其中下部与右吊架32的第二圆弧板的内侧焊接相连。本发明使第一箍带的上下两端开口,左半箍带和右半箍带的上下两端通过螺栓相连,使第一箍带竖直安装,这样能够给排气系统安装预留更大的操纵空间,且由于左半箍带与右半箍带的连接螺栓位于整个箍带的上下两侧,能够避免对排气系统总成件造成干涉。本发明通过将吊架主体上设置与第一箍带外径相等的第一圆弧板与第二圆弧板,能够增加吊架主体与第一箍带的接触面积,使吊架主体与第一箍带连接的更加牢固,提高排气系统托架的结构强度,对催化消声器进行强有力的支撑。本发明通过设置长度方向为左右方向的第一腰形安装孔,能够对催化消声器的安装位置进行左右调节,保证客车排气系统上部分和下部分的相对位置,从而使催化消声器和颗粒物捕集器的安装位置最为合理,提高客车空间利用率和装配精度。如图6-图9所示,所述排气系统托架包括托架主体41和焊接在托架主体41顶部的第二箍带。所述托架主体包括托架安装板411、垂直焊接在托架安装板411左右两端顶部的第二箍带左侧连接板412与第二箍带右侧连接板414以及焊接在托架安装板411中段顶部的第二箍带支撑板413。所述第二箍带包括焊接在第二箍带左侧连接板412、第二箍带支撑板413和第二箍带右侧连接板414顶部的第二下箍带42以及与第二下箍带42螺栓连接的第二上箍带43;所述托架安装板411的左右两端分别开设有第二左侧腰形安装孔417和第二右侧腰形安装孔418。所述第二箍带支撑板413为依次设置在托架安装板中段顶部前后两侧的两个;所述第二箍带左侧连接板412、第二箍带右侧连接板414以及第二箍带支撑板413的顶部均为与第二下箍带外周相适应的圆弧状。所述第二左侧腰形安装孔417位于第二箍带左侧连接板412的外侧,且在第二左侧腰形安装孔417前后两侧的托架安装板411上分别设有第一前侧加强筋415和第一后侧加强筋419;所述第一前侧加强筋415和第一后侧加强筋419,其内侧壁分别焊接在第二箍带左侧连接板412外侧壁的前后两端,其底部分别焊接在托架安装板411左端前后两侧的顶部。所述第二右侧腰形安装孔418位于第二箍带右侧连接板414的外侧,且在第二右侧腰形安装孔418前后两侧的托架安装板411上分别设有第二前侧加强筋416和第二后侧加强筋410。所述第二前侧加强筋416和第二后侧加强筋410,其内侧壁分别焊接在第二箍带右侧连接板414外侧壁的前后两端,其底部分别焊接在托架安装板411右端前后两侧的顶部。本发明通过设置第二箍带左侧连接板、第二箍带支撑板和第二箍带右侧连接板,用于分别固定连接第二下箍带的左、中、右三端,能够使第二箍带的受力更加均匀,从而对颗粒物捕集器7进行有力且牢稳地固定。本发明通过将第二箍带左侧连接板、第二箍带支撑板和第二箍带右侧连接板的底部均设计为与第二下箍带半径相等的圆弧状,能够增加第二箍带左侧连接板、第二箍带支撑板和第二箍带右侧连接板与第二下箍带之间的焊接接触面积,增加焊接强度,提高排气系统托架的结构强度,对颗粒物捕集器进行强有力的支撑。本发明通过设置前后两个第二箍带支撑板,在保证结构强度的基础上,能够降低重量,从而避免自身重量过重而影响结构强度。本发明通过设置第一前侧加强筋、第一后侧加强筋、第二前侧加强筋和第二后侧加强筋,并将这四个加强筋设置为三进行,能够利用三角形的稳定性设计,增加排气系统托架的结构强度。本发明通过设置长度方向为左右方向的第二左侧腰形安装孔和第二右侧腰形安装孔,能够对颗粒物捕集器的安装位置进行左右调节,保证客车排气系统上部分和下部分的相对位置,从而使催化消声器和颗粒物捕集器的安装位置最为合理,提高客车空间利用率和装配精度。如图10所示,所述悬置软垫1包括依次设置的钢板11、与钢板硫化连接为一体的橡胶块主体12和设置在橡胶块主体底部的橡胶块凸起13上;橡胶块主体12和橡胶块凸起13上开设有依次相贯通的安装通孔14,该安装通孔用于螺栓通过。所述橡胶块凸起,用于减小悬置软垫与隔热框架的接触面积,使悬置软垫的压紧力更大,减震缓冲效果更好。以上所述的实施例仅仅是对本发明的优选实施方式进行描述,并非对本发明的范围进行限定,在不脱离本发明设计精神的前提下,本领域普通技术人员对本发明的技术方案作出的各种变形和改进,均应落入本发明权利要求书确定的保护范围内。