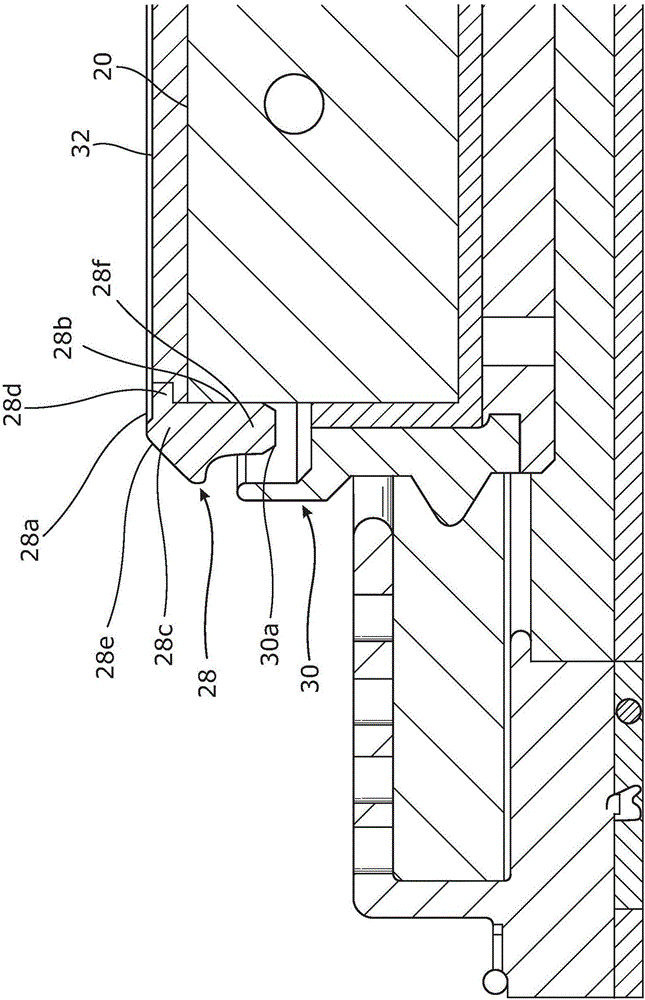
本发明涉及一种用于蚀刻基板的ICP等离子体蚀刻装置、降低污染的方法以及用于该类型等离子体蚀刻装置的保护结构。
背景技术:
:等离子体蚀刻广泛地用于处理各种基板,诸如半导体晶片。等离子体蚀刻工艺可为构成处理工序的一部分的一个步骤工艺。例如,在半导体工业中,熟知的是,在后续金属沉积步骤之前,通过溅射蚀刻工艺来去除晶片表面的材料。该溅射蚀刻工艺典型地利用氩等离子体来进行。目的是为了确保产生低接触电阻的高质量金属/金属界面。溅射蚀刻步骤典型地在预清洁的组件中进行。在操作中,据观察,延长的蚀刻可能导致再沉积的颗粒材料在溅射蚀刻腔室的内表面周围,诸如腔室盖和壁聚集。这是蚀刻可导致含碳材料的聚集或再沉积的有机材料,诸如聚酰亚胺(PI)和聚苯并噁唑(PBO)的一具体问题。该再沉积的颗粒材料可积聚至某一点,在该点处颗粒变得松散,并且它们可能掉落在晶片上而污染晶片。另一个问题与晶片相关:晶片包含强烈脱气的物质。该物质的实例为有机钝化层、粘合剂、光致抗蚀剂和旋涂材料。此外,PI和PBO是特别成问题的。当这些材料除气时,污染物被释放至腔室,该腔室压力升高。从而在对系列晶片处理期间,在将腔室恢复至可接受的真空水平时,可能导致显著的问题。对于这些问题,常规方案是频繁地进行维护工序。这最终使腔室与大气相通,从而能够进行机械清洁。这种停顿需要显著的成本以及工具停工时间。在生产环境下这不是可取的。相反,可取的是,降低维护停顿的频率。这将降低成本,同时增加工具的正常运行时间。还已知的是,对金属盘或镀金属膜的晶片进行周期性蚀刻,以延长腔室清洗之间的平均时间。腔室典型地包括陶瓷侧壁或石英侧壁,RF能量通过陶瓷侧壁或石英侧壁而感应耦合来在腔室中形成等离子体。重要的是,对腔室的该部分进行保护以免形成连续的金属沉积。否则,可能导致感应耦合的严重衰减。金属盘或镀金属膜的晶片的蚀刻导致在腔室的内表面上,蚀刻材料“粘结”任何松散的颗粒材料。这就防止了颗粒材料掉落到基板上。但是,必须中断正常的制造过程来进行金属盘或镀金属膜的蚀刻。因此,这些技术打断正常的制造过程,这将导致系统产出的损失以及增加的占有成本(COO)。技术实现要素:本发明在至少一些实施方式中解决了上述问题中的一个或多个。尽管本发明尤其适用于溅射蚀刻工艺,诸如在预清洁的组件中进行的溅射蚀刻工艺,但是本发明并不限于该方面。相反地,本发明可用于广泛的等离子体蚀刻工艺。根据本发明的第一个方面,提供了一种用于蚀刻基板的ICP(感应耦合等离子体)等离子体蚀刻装置,包括:至少一个腔室;放置在所述腔室内的基板支架;等离子体产生器件,产生用于蚀刻所述基板的等离子体;以及,保护结构,所述保护结构环绕所述基板支架,从而在使用中保护所述基板的外周部分免受不需要的材料沉积;其中,所述保护结构布置为被电偏压并且由金属材料形成,从而所述金属材料能够从所述保护结构溅射到所述腔室的内表面以使颗粒材料附着至所述内表面。以此方式,解决了颗粒沉积的问题。这可降低所需维护操作的频率。进而能够降低运行成本并且提高装置的正常工作时间。此外,本发明人实现了在蚀刻基板的同时,能够使保护结构溅射以使颗粒材料附着至腔室的内表面。这是极其便利的并且提高了系统的产出。所述金属材料可为金属或金属合金。所述金属材料可为铝、铝合金或铜。当所述金属材料为金属合金时,该合金可包括与一种或多种其它金属形成合金的金属,和/或与一种或多种非金属材料形成合金的金属。例如,所述保护结构可由铝合金来形成,该铝合金可包括铜、硅,或者同时包括铜和硅。典型地,铜和/或硅以小于5at.%的量存在。所述金属材料还可为吸气材料。所述吸气材料可为去除腔室中存在的一种或多种气态物质的材料。所述吸气材料可与腔室中存在的一种或多种气态物质反应或吸收腔室中存在的一种或多种气态物质。所述吸气材料可为钛或钽。以此方式,通过脱气,能够去除不需要的气态物质。典型地,所述保护结构为环状结构。所述环状结构可环绕所述基板和所述基板支架,从而保护所述基板的外周部分免受不需要的材料沉积。该被保护的部分可包括所述基板的下侧。该类型的环状结构通常被称为“反溅射环(backsputterring)”或“均匀环”。典型地,所述环状结构的一部分被配置为接收所述基板的外周部分。典型地,所述环状结构为连续的单个环状结构。然而,本文中所述的原理还扩展到其它形式的保护结构,如多个环状结构。所述保护结构可具有基板接收表面。所述保护结构可包括凹陷部,并且所述基板接收表面可形成所述凹陷部的一部分。所述保护结构在使用中邻近所述基板的区域可由介电材料形成。所述介电材料可在所述保护结构上以涂层的形式存在。所述保护结构可具有由介电材料形成的基板接收表面。所述保护结构可包括凹陷部,并且所述基板接收表面形成所述凹陷部的一部分。所述凹陷部可包括所述基板接收表面以及壁部分。所述基板接收表面和所述壁部分可由介电材料形成。所述介电材料可为氧化铝。所述保护结构可包括:远离基板支架的区域,所述远离基板支架的区域具有至少一个等离子体面向表面,所述至少一个等离子体面向表面远离所述基板支架倾斜。以此方式,可控制由所述保护结构溅射的金属材料的空间分布,以将溅射的金属材料最大限度地沉积在腔室内最有效沉积颗粒材料的区域中。进一步的优点是:能够最大限度地降低从保护结构溅射的金属材料沉积到基板上。所述远离基板支架的区域可具有单个等离子体面向表面,所述单个等离子体面向表面远离所述基板支架倾斜。所述远离基板支架的区域可为倒棱的形状、斜切的形状、拱形的形状或双弯曲线形状。该装置可进一步包括暗区屏蔽件。所述暗区屏蔽件可环绕所述基板支架并且具有用于接收所述保护结构的保护结构接收部。所述基板支架可包括用于接收所述基板的板台,所述板台限定一水平。所述保护结构接收部可布置在所述水平之下。常规地,暗区屏蔽件至少延伸至板台的水平,从而最大限度地降低在基板和基板支架的下部之间的间隙中形成等离子体。相反地,本发明所提供的暗区屏蔽件可配置为并不延伸至垂直进入腔室那么远。因此,等离子体可进一步围绕所述保护结构展开。这可增强从所述保护结构溅射金属材料。在使用中,所述基板支架被电偏压。所述保护结构可与所述基板支架电接触以在所述保护结构上提供电偏压。在实践中,这很可能是更便利的布置。但是在原理上,也可能独立地使所述保护结构电偏压。常规地,所述保护结构和/或所述基板支架利用RF电压来被电偏压。所述腔室可包括由介电材料形成的用于传递RF能量的区域。所述等离子体产生器件可导致所述RF能量通过所述区域耦合进入(coupledinto)所述腔室。形成所述区域的介电材料可为陶瓷或石英。所述区域可包括所述腔室的窗口或壁。所述等离子体蚀刻装置可为溅射蚀刻装置。所述等离子体蚀刻装置可为氩溅射蚀刻装置。所述等离子体产生器件可包括电感元件。典型地,所述电感元件被放置在所述腔室的外部。所述电感元件可为线圈。所述装置可进一步包括RF供电电源,用于将RF偏压电力供应至所述基板支架和所述保护结构中的一个或两个。典型地,所述等离子体蚀刻装置包括单个腔室。然而,多个腔室的装置也在本发明的范围内。所述等离子体蚀刻装置可为用在(多处理)组合工具中的预清洁模块。所述等离子体产生器件可包括发电机,优选RF发电机,其将电力供应至电感元件。通过供应至电感元件的电力的感应耦合,可产生等离子体。根据本发明的第二个方面,提供了一种用于降低蚀刻基板型等离子体蚀刻装置中的颗粒材料导致的污染的方法,包括以下步骤:提供根据本发明的第一方面的装置;以及,在所述腔室中产生等离子体,使金属材料从所述保护结构溅射到所述腔室的内表面上以使颗粒材料附着至所述腔室的内表面上。在对所述基板进行蚀刻的同时,可进行所述金属材料从所述保护结构的溅射。就产出而言,这就提供了相当大的优势。此外,其减少了对正常生产过程的中断。在所述腔室内产生等离子体期间,所述保护结构可被电偏压。根据本发明的第三个方面,提供了一种用于本发明的第一个方面的等离子体蚀刻装置的保护结构,所述保护结构被配置为环绕所述装置的所述基板支架,从而在使用中保护所述基板的外周部分免受不需要的材料沉积,其中,所述保护结构由金属材料形成,所述金属材料能够被溅射到所述装置的腔室的内表面以使颗粒材料附着至所述内表面。根据本发明的第四个方面,提供一种用于处理工件的组合工具,所述组合工具包括多个处理组件,其中,一个或多个组件为预清洁组件,所述预清洁组件包括本发明第一方面的等离子体蚀刻装置。尽管上文已经对本发明进行了描述,但是本发明可扩展至上文或下文、附图或权利要求中所述的特征的任意创造性组合。例如,针对本发明第一方面所述的任何特征被认为同样在针对本发明第二方面中公开,并且反之亦然。附图说明参照下列附图,现将对根据本发明的装置的实施方式、保护结构的实施方式和蚀刻方法的实施方式进行描述,其中:图1为等离子体蚀刻装置的剖视图;图2为图1装置的一部分的横截面图,该部分围绕板台和反溅射环的外周部分;图3示出了反溅射环的第二实施方式;图4示出了蚀刻的PBO涂覆的晶片上的污染物颗粒水平;图5示出了(a)尺寸小于0.2微米的颗粒在蚀刻的晶片上的颗粒水平;和(b)尺寸大于1.0微米的颗粒在蚀刻的晶片上的颗粒水平;以及,图6示出了在对晶片的蚀刻进行持久性测试(marathontest)期间测量的(a)蚀刻速度和(b)蚀刻均匀度。具体实施方式图1示出了本发明的等离子体蚀刻装置的实例,整体用10来表示。装置10包括腔室12,该腔室12具有布置在其顶部的合适的气体入口14。腔室12进一步包括晶片加载槽16和抽吸口18,该抽吸口18可与合适的抽吸布置,诸如导向涡轮泵的真空管线相连。腔室12的内部放置有工件(诸如晶片)可装载于其上的板台20。图1中实线示出的板台20处于降低的位置以接收工件。随后在开始蚀刻处理之前,使板台20升高至图1中虚线示出的位置。设置RF电源22,该RF电源22将RF偏压电力提供至板台20。为了方便起见,使用13.56MHz的RF信号频率,尽管在原理上,也可采用其他频率。腔室12环绕有感应线圈24。感应线圈24通过本领域熟知的阻抗匹配电路(未示出)与RF发电机(未示出)相连。腔室12的至少邻近感应线圈的壁由绝缘材料(诸如石英或陶瓷)制成,以最大限度地降低耦合至腔室12的RF功率的衰减。可将合适的一种工艺气体或多种工艺气体通过气体入口14供应至腔室12,并且可将RF电力供应至线圈24以在腔室12中产生等离子体26。在一个实施例中,通过质量流量控制器,在相对低压(典型地,1-10m托)将气体(典型为氩气)引入到腔室12中。随后使用至板台20的偏压电源来加速来自等离子体的离子朝向工件的运动,其中,离子轰击蚀刻工件的表面。装置10进一步包括反溅射环28形式的保护结构。该反溅射环28由金属或金属合金制成,该金属或金属合金可从反溅射环28的表面被溅射侵蚀。从反溅射环28溅射的材料随后涂覆在腔室12的内表面和组件上。已沉积在腔室12的内表面和组件上的颗粒材料通过从反溅射环28溅射的材料而“粘结”在恰当的位置。以此方式,颗粒材料通过从反溅射环28溅射的金属或金属合金材料而牢固地附着在腔室中的恰当位置。这至少降低了颗粒材料掉落在晶片上的风险。图2为腔室12围绕板台20的外周部分和反溅射环28的部分的横截面图。图2中使用了与图1中所使用的相同的附图标记来表示相同的特征。可以看出,装置10进一步包括非常规设计的暗区屏蔽件30。图2中示出的其它特征基本是常规类型,并且熟悉技术的读者熟知它们的操作。此外,图2示出了板台20的凹陷部32。该凹陷部32接收晶片(未示出)。反溅射环28包括凹陷部28a,其由水平基板接收表面28b和大致垂直的壁部分28c构成。晶片还被接收在凹陷部28a中。以此方式,反溅射环28用于保护晶片的边和表面免受等离子体的不期望的作用,诸如不需要的材料沉积。反溅射环28进一步包括圆形框(rim)28d,其被在板台20中形成的槽接收。这使得反溅射环28与板台20之间能够进行紧密接触,从而反溅射环28与板台20电接触。这就确保了板台20和反溅射环28均通过RF电源22而被电偏压。反溅射环28进一步包括等离子体面向表面28e。在图2示出的实施例中,等离子体面向表面28e远离板台20和晶片倾斜。从等离子体到达晶片和反溅射环28的离子通常沿垂直向下的方向移动。由等离子体面向表面28e提供的轮廓(profile)最大限度地增加了溅射材料从反溅射环28朝向腔室的易于被颗粒材料污染的部分的流量的空间分布。具体地,从反溅射环28溅射的材料基本上朝向靠近线圈24的位置的内腔室壁的区域。相关的优点是:其最大限度地降低了从反溅射环28溅射的材料流向晶片。由图2可以看出,等离子体面向表面28在其径向截面中是线性的。熟练技术的读者将知晓的是,也可使用许多其他轮廓以得到相似的结果。例如,等离子体面向表面可具有弯曲的径向横截面,或者也可使用倒棱的轮廓、斜切的轮廓、拱形的轮廓或双弯曲线轮廓。暗区屏蔽件30为非常规的设计。更具体地,传统上现有技术中的暗区屏蔽件通常被配置为向上延伸至板台的水平(至少至板台的下表面)。这是因为现有技术中的暗区屏蔽件用于减少等离子体进入板台和腔室底部之间的间隙区域的程度。与该传统类型的暗区屏蔽件相比,图2示出的暗区屏蔽件30为具有较短直立部的剖开设计(cut-offdesign)。由图2可以看出,暗区屏蔽件30的最上部始终位于板台20水平之下。暗区屏蔽件30包括相对浅的圆周槽30a,其接收反溅射环28的向下延伸的圆周壁28f。因此,等离子体26绕反溅射环28在板台20和晶片之间的间隙以及腔室的底部延伸。这就使得反溅射环28的溅射增强。图3示出了反溅射环28的第二实施方式。图3示出了与图1和图2中示出的元件基本相同的其它元件。使用相同的附图标记来表示这些相同的元件,即,板台20、晶片凹陷部32以及暗区屏蔽件30。反溅射环128具有凹陷部128a,该凹陷部128a包括壁部分和用于接收晶片的水平表面。在第二实施方式中,凹陷部128a涂覆有介电涂层,诸如氧化铝(Al2O3)。与铝相比,氧化铝具有低得多的溅射率(在600eV下,氧化铝溅射率=0.18;铝溅射率=1.24),并且从而与铝相比,其蚀刻要慢得多。因此,在涂覆的凹陷部128a中,发生降低量的溅射,并且进而降低了溅射到晶片边和背侧的材料量。熟悉技术的读者将知晓的是,可使用其它介电材料和除涂覆技术之外的其它技术,来生产在接近晶片处具有介电表面的背溅射晶片。尽管本发明并不限于该方面,据认为可取的是,相对于蚀刻的基板表面,利用具有相对较大表面积的反溅射环。在该情况下,从反溅射环溅射的材料与从基板释放的材料之比相对较大。例如,如果蚀刻300mm的晶片,据证实,在蚀刻100%PBO涂覆的晶片时,具有300mm内径和340mm外径的反溅射环能够有效地控制释放的颗粒材料。在该非限制性实施方式中,反溅射环具有的表面积约为晶片的表面积的30%。利用图2示出的反溅射环的第一实施方式与图1示出的装置的结合,可进行多种实验来蚀刻100%PBO涂覆的晶片。同时,利用现有技术中标准的蚀刻模式来进行实验。对蚀刻的晶片的VPDICPMS分析证实了:晶片的金属污染物能够被保持在标准蚀刻模式的典型值之下。表1示出了对于标准蚀刻和本发明的新的蚀刻装置的晶片的Al污染。对于本发明的装置,发现金属污染没有增加,并且实际上,示出的结果表明了更低水平的污染。Al(原子/cm2)标准蚀刻8.97E13新的蚀刻8.20E13表1图4示出了蚀刻的PBO涂覆的晶片上的污染物颗粒水平。检测大于1.0微米的颗粒。利用本发明的装置以及利用现有技术中的技术来进行对多个晶片蚀刻的实验,其中,通过以下来恢复颗粒水平:停止对晶片的蚀刻、将金属盘引入到腔室,以及进行粘结步骤(其中,金属盘被溅射蚀刻)。线40表示利用本发明的装置得到的结果,而线42表示利用现有技术金属盘粘结技术得到的结果。对于现有技术金属盘粘结技术,每次粘结导致颗粒水平的急剧下降。然而,利用现有技术观察的颗粒水平显著地高于利用本发明的装置观察的颗粒水平。尽管每个金属盘粘结步骤大幅度地降低了晶片上测得的颗粒数目,但是可以看出,即便是在金属盘粘结后得到的最低污染水平仍然高于利用本发明的装置观察到的污染物水平。此外,应注意的是,必须停止晶片蚀刻过程来进行金属盘粘结步骤,这就导致降低的产出。相反地是,通过反溅射环的溅射蚀刻实现的粘结在进行晶片蚀刻期间来实现。因此,利用本发明的装置不存在产出的损失。图5示出了本发明的装置蚀刻100%PBO涂覆的晶片的持久性测试的结果。图5示出了(a)在晶片上观察的尺寸大于0.2微米的颗粒水平和(b)在晶片上观察的尺寸大于1.0微米的颗粒水平。在这两种情况下,可以看出,在近2000张晶片上维持良好的颗粒性能。图6示出了在本发明的装置蚀刻100%PBO涂覆的晶片的持久性测试期间测量的(a)蚀刻速率(以A/分钟)和(b)蚀刻均匀度(1σ,3mm边界除外)。可以看出,实现了良好的蚀刻速率和均匀度可重复性。在以上提供的实施例中,反溅射环由铝来制备。如参照图3所述的,该反溅射环在邻近晶片处设置有氧化铝涂层。使用其它材料也在本发明的范围内。例如,可想到铝合金或铜。还能够想到使用诸如钛(更有效的“吸气”材料)的材料。使用吸气材料的优点是:能够从腔室的气氛中去除由不想要的脱气所产生的气态组分,从而得到更好的真空性能。当前第1页1 2 3