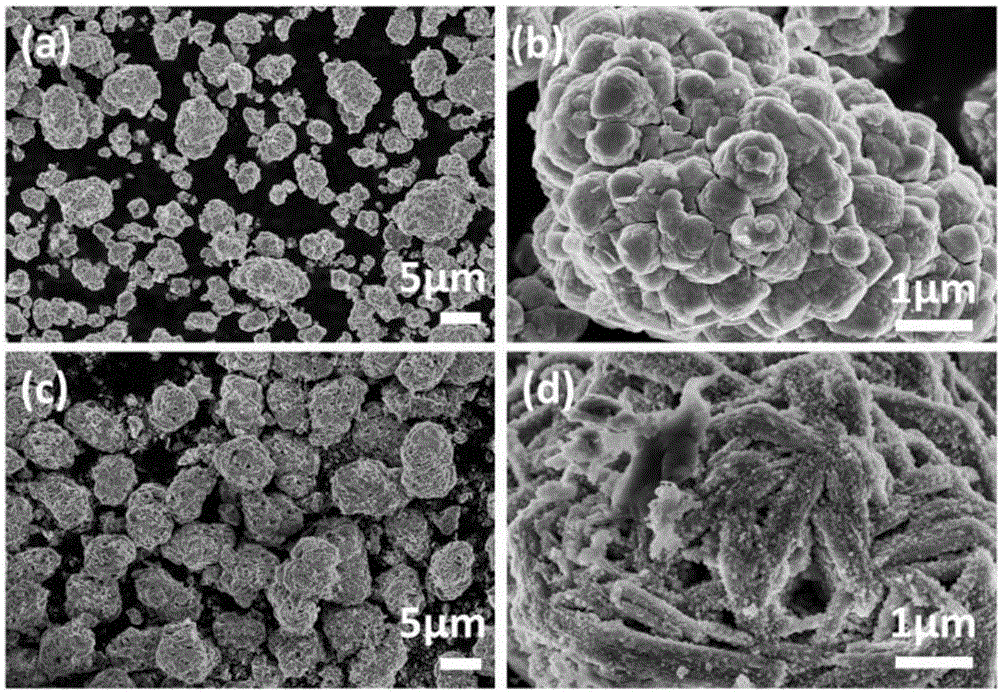
发明涉及锂离子电池正极材料领域,特别涉及一种高振实密度富锂锰基正极材料及其制备方法。
背景技术:
:锂离子电池由于其高能量密度、安全性能较佳和成本较低等优点,逐渐成为最重要的二次电化学电池。目前锂离子电池不但已成功应用手机、平板电脑等移动设备,而且,成功应用于混合电动汽车和纯电动汽车上。然而,在纯电动汽车应用领域,仍然需要进一步提高的锂离子电池能量密度,从而提升纯电动汽车续航里程。由于正极材料在锂离子电池中提供锂源,正极材料的性能对电池的性能起到关键作用,因此,采用能量密度高的正极材料为提升锂离子电池的能量密度有效手段。到目前为止,虽然以镍钴铝正极材料(LiNi0.8Co0.15Al0.05O2)为正极材料的锂离子动力电池能量密度高于180Wh/kg,然而,仍然难于满足《国家重点研发计划新能源汽车重点专项实施方案(征求意见稿)》的要求(2020年新能源汽车用电池能量密度达到300Wh/kg)。另外,目前商业化正极材料LiCoO2、LiMn2O4、LiMn1/3Ni1/3Co1/3O2、LiNi0.8Co0.15Al0.05O2、LiFePO4比容量均低于200mAh/g,且实际比容量提升空间狭小。为了进一步提升锂离子动力电池能量密度,开发出一种比容量大、放电电压高的正极材料成为必然选择。由Li2MnO3与LiMO2(B=Ni,Co,Mn,Fe,Cr)构成的富锂锰基正极材料xLi2MnO3·(1-x)LiMO2(x≥0.3)具有:(1)理论容量大于300mAh/g,实际容量大于250mAh/g;(2)放电平均电压高于3.5V;(3)稀贵元素成分含量少,原料成本低等优点,富锂锰基正极材料成为新一代商业化正极材料的最佳候选材料之一。然而,与目前已经商业化的球形三元正极材料LiNi0.8Co0.15Al0.05O2、LiMn1/3Ni1/3Co1/3O2等相比,富锂锰基正极材料还存在振实密度较低而引发的加工性能较差和对应电池极片压实密度较低的问题,最终导致电池制备成本较高和体积能量密度偏低的问题。现有文献表明(JournalofPowerSources,2012,203,115–120):富锂锰基正极材料的振实密度不高的问题主要是由材料中锰含量较高引发,即在采用共沉淀法制备二次颗粒为球形的前驱体过程中,由于生成的前驱体一次颗粒为大片状的形貌(如说明书附图2b),导致由一次颗粒堆积而成的球形二次颗粒(2a)中大孔多和孔隙率高,造成后续混锂煅烧之后的富锂锰基正极材料的空隙率高,因此,相比成分和结构相似的三元材料,富锂锰基正极材料的振实密度较低。另外,一次颗粒为大片状的形貌,{010}晶面面积较少,不利于锂离子的脱嵌,导致由大片状一次颗粒所组成的类球形二次颗粒的富锂锰基正极材料的电化学性能不佳,尤其是倍率性能较差。技术实现要素:本发明的目的在于克服现有富锂锰基正极材料存在的振实密度低、倍率性能差的不足,提供一种高振实密度富锂锰基正极材料及其制备方法;该富锂锰基正极材料孔隙率低,振实密度高且电化学性能和加工性能优异,从而提高了对应电池极片压实密度,降低电池制备成本,提升电池的体积能量密度;该方法无需添加络合剂(氨水)和氮气保护,直接通过共沉淀法制备得到由微米级类球形一次颗粒组成且粒径分布较宽的二次颗粒的前驱体,再将其与含锂化合物混合煅烧制备得到一次颗粒紧密堆积而成的富锂锰基正极材料二次颗粒,本发明制备方法工艺简单可靠,适合高振实密度富锂锰基正极材料的大规模、商业化生产。为了实现上述发明目的,本发明提供了一种高振实密度富锂锰基正极材料的制备方法,包括以下制备步骤:1、前驱体制备:在空气气氛中,将过渡金属盐溶液与氢氧化物溶液(沉淀剂)同时加入反应容器内进行共沉淀反应,反应结束后,将沉淀过滤并进行洗涤和干燥,得到前驱体;2、混合煅烧:将步骤1得到的前驱体与含锂化合物混合煅烧得到正极材料。上述一种高振实密度富锂锰基正极材料的制备方法中,步骤1中所述的过渡金属盐溶液为至少2种过渡金属盐的混合溶液,其中所述的过渡金属盐必定含锰盐;其中所述过渡金属盐为过渡金属硫酸盐、硝酸盐、氯化物中的一种;其中所述的过渡金属优选Ni、Mn、Co、Fe;最优选的,所述过渡金属盐溶液为Ni盐、Mn盐、Co盐的混合溶液,其中Mn︰Ni︰Co摩尔比为0.54︰0.13︰0.13,通过优选,富锂锰基正极材料的电化学性能最佳。其中所述的过渡金属盐溶液物质的量浓度为1.5-2.5mol/L,浓度过大(>2.5mol/L),过渡金属离子浓度大,溶液容易结晶析出,导致管道堵塞,工业化操作困难;浓度过小(<1.5mol/L),生产效率低,而且废水量大;优选的,所述的过渡金属盐溶液浓度为2.0mol/L。上述一种高振实密度富锂锰基正极材料的制备方法,步骤1中所述的氢氧化物为氢氧化钠、氢氧化钾中的一种或两种;其中所述的氢氧化物溶液物质的量浓度为2.0-8.0mol/L,浓度过大(>8.0mol/L),溶液容易结晶析出,导致管道堵塞,工业化操作困难;浓度过小(<2.0mol/L),生产效率低,而且废水量大。优选的,所述的氢氧化物溶液浓度为5.0mol/L。上述一种高振实密度富锂锰基正极材料的制备方法中,步骤1中所述的共沉淀反应的温度为30-70℃;在该温度范围内进行共沉淀反应,才能得到由微米级类球形一次颗粒组成且粒径分布较宽的二次颗粒的前驱体;优选的,共沉淀反应的温度为40-60℃;最优选的,共沉淀反应的温度为50℃。上述一种高振实密度富锂锰基正极材料的制备方法中,步骤1中所述的共沉淀反应的pH值控制在10,pH值过大或过小,都会影响共沉淀反应过程中颗粒成核和颗粒生长的速度,导致难于生成振实密度高的前驱体。上述一种高振实密度富锂锰基正极材料的制备方法中,步骤2中所述的含锂化合物为氢氧化锂、碳酸锂、醋酸锂、硝酸锂中的一种或多种。上述一种高振实密度富锂锰基正极材料的制备方法中,步骤2中所述的煅烧采用分段煅烧工艺,分段煅烧包括两段,其中第一段煅烧的温度为400-600℃,升温速度为2-10℃/min,保温时间为3-10h,升温速度太快(>10℃/min),前驱体里外受热不均,前驱体二次颗粒破裂,升温速度太慢(<2℃/min),加热时间长,能源浪费大,成本增加;第二段煅烧温度为700-1000℃,升温速度为2-10℃/min,煅烧保温时间为10-25h,升温速度太快(>10℃/min),导致正极材料晶体出现太多缺陷,升温速度太慢(<2℃/min),加热时间长,能源浪费大,成本增加。优选的,第一段煅烧的温度为500℃,升温速度为3℃/min,预煅烧保温时间为6h;第二段煅烧温度为900℃,升温速度为3℃/min,煅烧保温时间为15h;此条件下煅烧得到的富锂正极材料二次颗粒完整,烧结效果最好,能源消耗最少,成本最低。一种高振实密度富锂锰基正极材料的制备方法,通过控制共沉淀反应物的浓度和温度,不再需要添加络合剂和惰性气体保护,直接在空气气氛中生成由微米级类球形一次颗粒组成且粒径分布较宽的二次颗粒的前驱体,最后直接与锂源混合煅烧得到高振实密度富锂锰基正极材料,本发明制备方法工艺简单、可靠,适合富锂锰基正极材料的大规模、商业化生产。为了实现上述发明目的,进一步的,本发明提供了一种高振实密度富锂锰基正极材料,该材料是由上述制备方法制备得到的。一种高振实密度富锂锰基正极材料,由微米级类球形一次颗粒组成且粒径分布较宽的二次颗粒的前驱体与锂源混合煅烧得到,因此,该正极材料孔隙率低,振实密度高且电化学性能和加工性能优异,从而提高了对应电池极片压实密度,降低电池制备成本,提升电池的体积能量密度。与现有技术相比,本发明的有益效果:1、本发明方法能直接利用共沉淀法在空气气氛中制备得到由微米级类球形一次颗粒组成且粒径分布较宽的二次颗粒前驱体,从而制备得到高振实密度富锂锰基正极材料。2、本发明富锂锰基正极材料由微米级类球形一次颗粒组成且粒径分布较宽的二次颗粒的前驱体与锂源混合煅烧得到,孔隙率低,振实密度高且电化学性能优异。3、本发明方法所采用的共沉淀工艺无需N2为保护气氛,以及无需氨水作为络合剂,不但减少环境污染,而且降低工艺成本。4、本发明方法工艺简单、可靠,适合高振实密度富锂锰基正极材料的大规模、商业化生产。附图说明:图1为实施例1和对比例1工艺所制备的富锂锰基正极材料XRD图谱(图中I-OLO为实施例1,S-OLO为对比例1)。图2为实施例1和对比例1工艺所制备的前驱体SEM图(a、b为实施例1,c、d为对比例1)。图3为实施例1和对比例1工艺所制备的正极材料SEM图(a、b为实施例1,c、d为对比例1)。图4为实施例1和对比例1工艺所制备的正极材料的电性能对比图(a首次充放电曲线,b为倍率性能,c为循环性能,图中I-OLO为实施例1,S-OLO为对比例1)。具体实施方式下面结合对比例及具体实施方式对本发明作进一步的详细描述。但不应将此理解为本发明上述主题的范围仅限于以下的实施例,凡基于本
发明内容所实现的技术均属于本发明的范围。实施例1在空气气氛下,将2.0mol/L的MSO4(M=Mn、Ni、Co,其中Mn︰Ni︰Co摩尔比为0.54︰0.13︰0.13)溶液与5.0mol/L的NaOH溶液分别以0.5ml/min的速度逐滴加入反应容器,控制pH值为10.0,控制共沉淀反应温度为50℃,反应结束后,进行洗涤和干燥,获得由微米级类球形一次颗粒组成且粒径分布较宽的二次颗粒的前驱体(图2中a、b为所制备的前驱体XRD图谱),将干燥后的前驱体与LiOH·H2O混合均匀,然后放置于管式炉中,以3℃/min升温到500℃后保温6小时,再以3℃/min升温到900℃后保温15小时,获得高振实密度的锰基富锂正极材料(图1中I-OLO为所制备的正极材料XRD图谱,图3中a、b为所制备的正极材料的SEM图),以此材料组装成CR2032型扣式电池,测试电化学性能(图4中a、b、c中的I-OLO分别为所组装电池的首次充放电曲线,倍率性能,循环性能)。实施例2在空气气氛下,将1.5mol/L的MNO3(M=Mn、Ni、Co,其中Mn︰Ni︰Co摩尔比为0.5︰0.2︰0.1)溶液与5.0mol/L的NaOH溶液分别以0.5ml/min的速度逐滴加入反应容器,控制pH值为10.0,控制共沉淀反应温度为30℃,反应结束后,进行洗涤和干燥,获得由微米级类球形一次颗粒组成且粒径分布较宽的二次颗粒的前驱体,将干燥后的前驱体与Li2CO3混合均匀,然后放置于管式炉中,以3℃/min升温到600℃后保温5小时,再以5℃/min升温到900℃后保温15小时,获得高振实密度的锰基富锂正极材料,以此材料组装成CR2032型扣式电池,测试电化学性能。实施例3在空气气氛下,将2.5mol/L的MSO4(M=Mn、Ni,其中Mn︰Ni摩尔比为0.6︰0.2)溶液与2mol/L的KOH溶液分别以0.2ml/min的速度逐滴加入反应容器,控制pH值为10.0,控制共沉淀反应温度为60℃,反应结束后,进行洗涤和干燥,获得由微米级类球形一次颗粒组成且粒径分布较宽的二次颗粒的前驱体,将干燥后的前驱体与LiNO3混合均匀,然后放置于管式炉中,以5℃/min升温到600℃后保温4小时,再以3℃/min升温到850℃后保温18小时,获得高振实密度的锰基富锂正极材料,以此材料组装成CR2032型扣式电池,测试电化学性能。实施例4在空气气氛下,将2mol/L的MSO4(M=Mn、Co,其中Mn︰Co摩尔比为0.65︰0.15)溶液与8mol/L的NaOH和KOH的混合溶液分别以0.5ml/min的速度逐滴加入反应容器,控制pH值为10.0,控制共沉淀反应温度为40℃,反应结束后,进行洗涤和干燥,获得由微米级类球形一次颗粒组成且粒径分布较宽的二次颗粒的前驱体,将干燥后的前驱体与醋酸锂混合均匀,然后放置于管式炉中,以3℃/min升温到500℃后保温6小时,再以5℃/min升温到900℃后保温12小时,获得高振实密度的锰基富锂正极材料,以此材料组装成CR2032型扣式电池,测试电化学性能。对比例1在N2气氛下,将2mol/L的MSO4(M=Mn、Ni、Co,其中Mn︰Ni︰Co摩尔比为0.54︰0.13︰0.13)溶液、5.0mol/L的NaOH溶液和质量百分数为18%的氨水络合剂分别以0.5ml/min的速度逐滴加入反应容器,控制pH值为11.0,控制共沉淀反应为50℃,反应结束后,进行洗涤和干燥,将干燥后的类球形前驱体(图2中c、d为所制备的前驱体XRD图谱)与LiOH·H2O混合均匀,然后放置于管式炉中,以3℃/min升温到500℃后保温5小时,再以5℃/min升温到900℃后保温12小时,获得类球形的富锂锰基正极材料(图1中S-OLO为所制备的正极材料XRD图谱,图3中c、d为所制备的正极材料的SEM图),以此材料组装成CR2032型扣式电池,测试电化学性能(图4中a、b、c中的S-OLO分别为所组装电池的首次充放电曲线,倍率性能,循环性能)。对比例2在空气气氛下,将2mol/L的MSO4(M=Mn、Ni、Co,其中Mn︰Ni︰Co摩尔比为0.54︰0.13︰0.13)溶液、5.0mol/L的NaOH溶液和质量百分数为18%的氨水络合剂分别以0.5ml/min的速度逐滴加入反应容器,控制pH值为11.0,控制共沉淀反应温度为50℃,反应结束后,进行洗涤和干燥,将干燥后的前驱体(由片状一次颗粒堆叠而成的不规则二次颗粒)与LiOH·H2O混合均匀,然后放置于管式炉中,以3℃/min升温到500℃后保温5小时,再以5℃/min升温到900℃后保温12小时,获得富锂锰基正极材料(由片状一次颗粒堆叠而成的不规则二次颗粒,以此材料组装成CR2032型扣式电池,测试电化学性能。对比例3在N2气氛下,将2.0mol/L的MSO4(M=Mn、Ni、Co,其中Mn︰Ni︰Co摩尔比为0.54︰0.13︰0.13)溶液与5.0mol/L的NaOH溶液分别以0.5ml/min的速度逐滴加入反应容器,控制pH值为10.0,控制共沉淀反应温度为50℃,反应结束后,进行洗涤和干燥,获得由纳米级不规则一次颗粒堆叠而成类球形二次颗粒的前驱体,将干燥后的前驱体与LiOH·H2O混合均匀,然后放置于管式炉中,以3℃/min升温到500℃后保温6小时,再以3℃/min升温到900℃后保温15小时,获得锰基富锂正极材料(由亚微米级不规则一次颗粒堆叠而成类球形二次颗粒),以此材料组装成CR2032型扣式电池,测试电化学性能。对实施例1-4和对比例1-3进行振实密度及电化学性能测试结果如下表:组别振实密度(g/cm3)0.1C首次库伦效率(%)0.1C放电容量(mAh/g)1.0C循环100次放电容量(mAh/g)实施例12.1775.7259135实施例22.1173.2257130实施例32.1376.8262136实施例42.1274.6261134对比例12.0369.7232122对比例21.3182.3261135对比例31.6980.6260133通过对上述电化学性能结果分析可知:实施例1-4采用本发明方法制备得到的是由微米级类球形一次颗粒组成且粒径分布较宽的二次颗粒的富锂锰基材料,不但振实密度高,而且电化学性能优异,尤其是实施例1为最优选方案,得到高振实密度的富锂锰基正极材料,振实密度为2.17g/cm3,0.1C首次库伦效率为75.7%,0.1C放电容量259mAh/g,1.0C循环100次放电容量135mAh/g。对比例1采用常规共沉淀(既需要N2作为保护气氛,又需要氨水作为络合剂)制备得到的是类球形的富锂锰基正极材料,其振实密度和电化学性能与实施例1相比具有显著差异,振实密度为2.03g/cm3,0.1C首次库伦效率为69.7%,0.1C放电容量232mAh/g,1.0C循环100次放电容量122mAh/g;对比例2没有采用本发明方法,虽然前驱体合成过程在空气气氛下进行,但是添加了氨水作为络合剂,得到富锂锰基正极材料的振实密度与实施例1相比具有显著差异,振实密度仅为1.31g/cm3;对比例3没有采用本发明方法,虽然前驱体合成过程中没有添加氨水,但是在N2气氛下进行,得到富锂锰基正极材料的振实密度与实施例1相比具有显著差异,振实密度仅为1.69g/cm3。当前第1页1 2 3