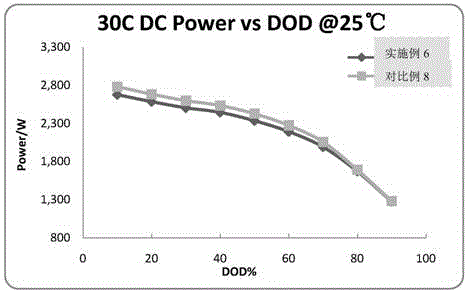
本发明涉及锂离子电池
技术领域:
,尤其涉及一种提高高功率动力锂离子电池负极极耳预焊质量的方法。
背景技术:
:锂离子动力电池作为电动车的重要组成部分,其性能直接影响电动车的正常使用。因其推广应用,其电性能和安全性能得到广泛关注。国内目前主要的两条技术路线分别高功率动力锂离子电池和纯电动用高能量型锂离子动力电池技术,其中纯电动高能量锂离子电池受电池原材料克容量的影响,能量密度大幅提升有一定的技术难度。对于高功率动力锂离子电池,主要考虑电池的功率性能,目前在用的市场应用的多为12v的车载启停电源和48v的轻混动力车载系统,市场需求逐渐增大。但高功率动力锂离子电池的功率密度的提升,除了与电池的正负极材料、工艺参数和电解液的电导率有关外,电池结构件的设计也至关重要。目前大多电池厂商通过两侧全极耳结构件的设计方式,提升电池的过流面积,从而提高电池的倍率和功率性能。高功率动力电池功率性能的一致性与极耳的焊接方式和质量存在密切的联系,焊接质量的不一致性严重影响了电池的功率性能发挥,并且因为高功率电池焊接面积的提升,极耳预焊相对于能量型电池的焊接更为复杂,导致过程中产生更多的金属屑,致使功率型电池的自放电较大,电芯短路率高于能量型电池。技术实现要素:基于
背景技术:
存在的技术问题,本发明提出了一种提高高功率动力锂离子电池负极极耳预焊质量的方法,通过二次焊接的方式,降低焊接时需要的能量值和焊接下压力,减少金属屑的产生,并提高焊接牢固度,提升电池的功率性能,降低生产过程的电芯的短路率,对高功率锂离子电池的功率一致性提升和工艺改进提供技术支持,提高成本电池直通率,降低企业生产成本。本发明提出的一种提高高功率动力锂离子电池负极极耳预焊质量的方法,包括如下步骤:将若干负极铜极耳进行整理使负极铜极耳的一端处于同一平面,采用超声波焊接机进行一次预焊,静置,接着进行二次预焊。优选地,负极铜极耳的尺寸为200mm×8mm×10mm。优选地,一次预焊与二次预焊的焊接参数相同。优选地,焊接参数如下:焊接能量为350-450j,焊接下压力为413.7-551.6kpa,焊接时间为0.5-1.5s。优选地,静置时间为1-3s。本发明通过对高功率动力锂离子电池制作过程中负极极耳预焊各参数的焊接牢固度和电芯短路率的实验,开发了新型的二次焊接的方法进行预焊,减少超声焊接设备的所需能量值和缩短焊接时间,提高焊接质量,减少因焊接过程中产生的金属屑造成的电芯微短路,提高工序的成品率,降低电池的生产成本,对高功率电池结构件的焊接提供技术支持,保证电池在生产过程中的一致性,减少整车运行过程存在的安全隐患,对实际生产有非常重要的指导意义。附图说明图1为采用实施例6和对比例8所得锂离子电池负极极耳制得的电池脉冲放电功率性能测试图。具体实施方式下面,通过具体实施例对本发明的技术方案进行详细说明。实施例一种提高高功率动力锂离子电池负极极耳预焊质量的方法,包括如下步骤:将5个尺寸为200mm×8mm×10mm的负极铜极耳进行整理使负极铜极耳的一端处于同一平面,采用超声波焊接机进行一次预焊,静置,接着进行二次预焊;其中一次预焊与二次预焊的焊接参数相同。通过调节焊接过程中焊接能量值、焊接下压力和焊接时间,实施例1-7的焊接参数如下表1所示:表1实施例1-7焊接参数焊接能量值/j焊接下压力/kpa焊接时间/s实施例1450551.601.5实施例2400551.601.5实施例3350551.601.5实施例4400482.651.5实施例5400413.701.5实施例6400413.701实施例7400413.700.5对比例一种高功率动力锂离子电池负极极耳预焊方法,包括如下步骤:将5个尺寸为200mm×8mm×10mm的负极铜极耳进行整理使负极铜极耳的一端处于同一平面,采用超声波焊接机进行一次预焊。通过调节焊接过程中焊接能量值、焊接下压力和焊接时间,对比例1-10的焊接参数如下表2所示:表2对比例1-10焊接参数焊接能量值/j焊接下压力/kpa焊接时间/s对比例1550551.602.5对比例2550620.552.5对比例3550482.652.5对比例4600551.602.5对比例5500551.602.5对比例6450551.602.5对比例7400551.602.5对比例8450551.602对比例9450551.601.5对比例10450551.601将实施例1-7所得锂离子电池负极极耳和对比例1-10所得锂离子电池负极极耳进行测试:i、进行重量拉力实验,若拉力大于300n则视为焊接牢固,记录焊接的牢固合格率;ii、选用热压后经短路测试仪测试合格的卷芯,经所得锂离子电池负极极耳组装,周边焊、入壳后,并用短路测试仪测试后入壳后的电芯短路率,短路测试仪型号为ss25-9920,测试电压为200mv,测试速度为100ms,统计入壳后电芯短路率;其结果如下表3所示:表3实施例1-7和对比例1-10测试结果预焊牢固率/%电芯短路率/%实施例110010实施例21008实施例3883实施例41008实施例51008实施例61003实施例7953对比例17520对比例27030对比例37318对比例45033对比例57020对比例67018对比例76518对比例88013对比例9735对比例10653由上表可知:本发明通过二次焊接方式,焊接牢固度明显提高,同时电芯短路率明显下降,对设备的负荷和损耗也相应降低;而对比例中调节超声焊接参数,对于提高焊接强度和降低短路率影响较小,焊接能量和焊接时间过长,产生的熔融的金属屑增多,焊接时间过短和能量值低,焊接牢固度下降。将实施例6和对比例8所得锂离子电池负极极耳经后续工序并分容后合格电池,电池额定容量为25ah,常温条件下进行脉冲放电功率性能测试:每隔10%soc进行30c脉冲放电10s、22.5c脉冲反馈10s测试,其结果如图1所示,根据图1可知:采用本发明所得锂离子电池负极极耳制得的电池脉冲功率值略高于对比例。以上所述,仅为本发明较佳的具体实施方式,但本发明的保护范围并不局限于此,任何熟悉本
技术领域:
的技术人员在本发明揭露的技术范围内,根据本发明的技术方案及其发明构思加以等同替换或改变,都应涵盖在本发明的保护范围之内。当前第1页12