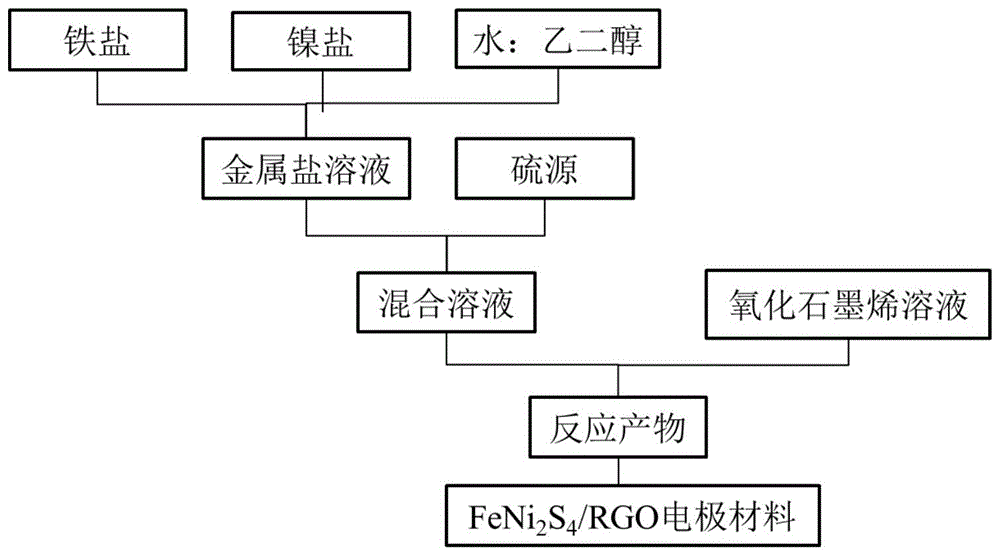
本发明属于电极材料
技术领域:
,具体涉及一种硫代尖晶石/石墨烯电极材料的制备方法及其电极材料。
背景技术:
:尖晶石型氧化物大多具有ab2o4通式,具有能够提供三维扩散路径的坚固的晶体结构。因为该结构在充放电过程中能够促进电子的转移和防止晶体结构的坍塌,所以尖晶石型氧化物具有较高的电化学性能,因此此类材料被广泛应用做电极材料。而硫代尖晶石材料硫替代了氧的位置,在保留尖晶石结构,且与对应金属氧化物相比电负性增强,比容量增加。目前,现有技术中硫代尖晶石/石墨烯复合材料的研究,大多是镍钴或者镍铜等硫代尖晶石与石墨烯复合,制备工艺繁杂,且金属硫化物电极材料虽然具有较高比容量,但在实际应用中,其电化学性能还是无法达到相关要求。因此,本领域亟需一种硫代尖晶石/石墨烯电极材料的制备方法,保证电极材料优良的电化学性能的同时,实现简易制备流程,工艺易调节,提高生产效率。技术实现要素:本部分的目的在于概述本发明的实施例的一些方面以及简要介绍一些较佳实施例。在本部分以及本申请的说明书摘要和发明名称中可能会做些简化或省略以避免使本部分、说明书摘要和发明名称的目的模糊,而这种简化或省略不能用于限制本发明的范围。鉴于上述的技术缺陷,提出了本发明。因此,作为本发明其中一个方面,本发明克服现有技术中存在的不足,提供硫代尖晶石/石墨烯基电极材料及其制备方法。为解决上述技术问题,本发明提供了如下技术方案:一种硫代尖晶石/石墨烯电极材料的制备方法,包括,将氧化石墨置于蒸馏水与乙二醇混合溶剂中超声分散均匀,制得氧化石墨烯溶液;将铁盐溶液和镍盐溶液混合,形成金属盐溶液,其中,所述铁盐溶液和所述镍盐溶液的中溶质的摩尔比为1:2;将硫源添加加到金属盐溶液中,搅拌均匀,形成混合溶液,所述硫源与所述镍盐溶液和所述锰盐溶液混合溶液中溶质的摩尔比为1:1~4;将混合溶液滴加到氧化石墨烯溶液中,搅拌;搅拌均匀后,60~180℃条件下水热反应6~18h,反应结束后冷却至室温,抽滤,收集沉淀物,洗涤,干燥,即得所述硫代尖晶石/石墨烯基电极材料,其中,氧化石墨烯质量分数为10~15%。作为本发明所述硫代尖晶石/石墨烯电极材料的制备方法的一种优选方案,其中:所述蒸馏水与乙二醇混合溶剂,其中,蒸馏水与乙二醇混合溶剂中蒸馏水与乙二醇的体积比为0.5~2。作为本发明所述硫代尖晶石/石墨烯电极材料的制备方法的一种优选方案,其中:所述将氧化石墨置于蒸馏水与乙二醇混合溶剂中超声分散均匀,其中,氧化石墨与所述蒸馏水与乙二醇混合溶剂的质量体积比以g:ml计为0.067~0.15:40。作为本发明所述硫代尖晶石/石墨烯电极材料的制备方法的一种优选方案,其中:所述超声分散,超声时间为30min,超声功率为250w,超声频率为40khz。作为本发明所述硫代尖晶石/石墨烯电极材料的制备方法的一种优选方案,其中:所述铁盐包括氯化铁、硝酸铁和硫酸亚铁中的一种或几种。作为本发明所述硫代尖晶石/石墨烯电极材料的制备方法的一种优选方案,其中:所述镍盐包括醋酸镍、氯化镍和醋酸镍中的一种或几种。作为本发明所述硫代尖晶石/石墨烯电极材料的制备方法的一种优选方案,其中:所述硫源包括l-半胱氨酸、硫脲和硫化钠中的一种或几种。作为本发明所述硫代尖晶石/石墨烯电极材料的制备方法的一种优选方案,其中:所述将混合盐溶液加入氧化石墨烯分散液中,搅拌,形成金属盐-氧化石墨烯混合液,其中,所述搅拌时间为30min。作为本发明所述硫代尖晶石/石墨烯电极材料的制备方法的一种优选方案,其中:所述收集沉淀物,洗涤,干燥,其中干燥温度是60~80℃,干燥时间是10~12h。作为本发明的另一个方面,本发明克服现有技术中存在的不足,提供所述的方法制得的硫代尖晶石/石墨烯基电极材料。为解决上述技术问题,本发明提供了如下技术方案:一种硫代尖晶石/石墨烯电极材料的制备方法制得的硫代尖晶石/石墨烯电极材料,所述硫代尖晶石/石墨烯电极材料为feni2s4-rgo复合物,其中,所述feni2s4颗粒生长在具有褶皱的rgo上,所述硫代尖晶石/石墨烯电极材料比电容可达1822.7f/g。本发明的有益效果:(1)本发明提供一种硫代尖晶石/石墨烯电极材料的制备方法,将铁镍硫代尖晶石与石墨烯进行复合,石墨烯的引入抑制了feni2s4的团聚,为feni2s4生长提供了成核位点,有利于增加feni2s4-rgo复合物与电解质的接触面积,更多的活性位点使材料的电化学性能得到提升,制备的feni2s4-rgo复合物电容可以达到1822.7f/g。(2)本发明优选l-半胱氨酸作为硫源,直接用水热去还原氧化石墨烯,不需要加入额外的还原剂,结合水热反应温度60~180℃,处理时间6~18h,并优选硫源的添加量以及铁盐溶液和所述镍盐溶液的中溶质的摩尔比为4:3,优选石墨烯质量分数为15%时,材料的电化学性能最佳,可能只有石墨烯添加量在此范围内,铁盐溶液和镍盐才能与石墨烯存在更佳的协同作用,制备的材料性能更佳,且本发明制得的硫代尖晶石/石墨烯电极材料不仅电化学性能得到提升,且实现简易制备流程,工艺容易调节,生产效率高。附图说明为了更清楚地说明本发明实施例的技术方案,下面将对实施例描述中所需要使用的附图作简单地介绍,显而易见地,下面描述中的附图仅仅是本发明的一些实施例,对于本领域普通技术人员来讲,在不付出创造性劳动性的前提下,还可以根据这些附图获得其它的附图。其中:图1为本发明实施例中硫代尖晶石/石墨烯基电极材料制备方法的工艺流程图。图2为实施例1制备的硫代尖晶石/石墨烯基电极材料电极材料xrd分析结果图。图3为实施例1制备的硫代尖晶石/石墨烯基电极材料及其制备方法在不同电流密度下的充放电时间对比图。图4为实施例中以硫化钠为硫源制得的产物、共沉淀工艺制得的xrd表征图。具体实施方式为使本发明的上述目的、特征和优点能够更加明显易懂,下面结合具体实施例对本发明的具体实施方式做详细的说明。在下面的描述中阐述了很多具体细节以便于充分理解本发明,但是本发明还可以采用其他不同于在此描述的其它方式来实施,本领域技术人员可以在不违背本发明内涵的情况下做类似推广,因此本发明不受下面公开的具体实施例的限制。其次,此处所称的“一个实施例”或“实施例”是指可包含于本发明至少一个实现方式中的特定特征、结构或特性。在本说明书中不同地方出现的“在一个实施例中”并非均指同一个实施例,也不是单独的或选择性的与其他实施例互相排斥的实施例。本发明中七水合硫酸亚铁(feso4〃7h2o)、四水合乙酸镍(ni(ch3coo)2〃4h2o)、l-半胱氨酸、硼氢化钠、氢氧化钾(koh)、硫脲、九水合硫化钠(na2s〃9h2o)、乙二醇((ch2oh)2)、无水乙醇(ch3ch2oh),无水甲醇、乙炔黑(cn2h4s)和聚四氟乙烯,分析纯(ar),国药集团化学试剂有限公司;氧化石墨(go)通过改进的hummer’s法制备。实施例1:本发明的硫代尖晶石/石墨烯基电极材料为feni2s4-rgo,由以下方法制得:(1)将6.115g的固含量为2.6%的氧化石墨置于40ml的蒸馏水:乙二醇(体积比为1:1)混合溶剂中超声分散均匀(超声时间为30min,超声功率为250w,超声频率为40khz),制得氧化石墨烯溶液;(2)将0.278g(1mmol)的硫酸亚铁和0.498g(2mmol)的醋酸镍溶于40ml的蒸馏水:乙二醇(体积比为1:1)混合溶剂中,加入0.121g(4mmol)的l-半胱氨酸混合均匀,形成混合盐溶液;(3)将混合盐溶液加入氧化石墨烯分散液中,搅拌30min,形成金属盐-氧化石墨烯混合液,拌均匀后160℃下进行水热反应12h,反应结束后冷却至室温,抽滤,收集沉淀物,洗涤,于60℃真空干燥12h,得到所述feni2s4-rgo电极材料。经检测,制备的feni2s4-rgo电极材料在0.5a/g的电流密度下,比电容高达1822.7f/g,这一效果较传统的材料feni2s4而言(传统的材料feni2s4的比电容691.25f/g),性能有了很大程度的提升。石墨烯的的加入使材料的比表面积增大,材料的活性位点增多,电极材料与电解质更易接触。本发明所述的硫代尖晶石/石墨烯基电极材料制备方法的工艺流程图见图1。xrd结果分析说明见如图2,从图2可以看出,材料出现的特征峰与feni2s4标准卡片(jcpdfno.47-1740)一一对应,说明feni2s4-rgo成功制备。图3为本实施例中制备的硫代尖晶石/石墨烯基电极材料电极材料及其制备方法在不同电流密度下的充放电时间对比图。从图3可以看出,材料显示较长放电时间,说明材料有很好的电容性能。实施例2:feni2s4电极材料的制备方法:(1)将0.278g(1mmol)的硫酸亚铁和0.498g(2mmol)的醋酸镍溶于40ml的蒸馏水:乙二醇(体积比为1:1)混合溶剂中,加入0.121g(4mmol)的l-半胱氨酸混合均匀。(2)拌均匀后160℃下进行水热反应12h,反应结束后冷却至室温,抽滤,收集沉淀物,洗涤,于60℃真空干燥12h,得到所述feni2s4电极材料。经检测feni2s4材料在0.5a/g的电流密度下,比电容有691.25f/g。这与feni2s4-rgo的测试结果相比,电容大幅下降,可能由于由于材料的团聚等原因导致电极材料无法与电解液充分接触,使材料电容性能不佳。实施例3:(1)将6.115g的固含量为2.6%的氧化石墨置于40ml的蒸馏水:乙二醇(体积比为1:1)混合溶剂中超声分散均匀,记为溶液a;(2)取0.278g(1mmol)的硫酸亚铁和0.498g(2mmol)的醋酸镍溶于40ml的蒸馏水:乙二醇(体积比1:1)混合溶剂中,加入2.410g(4mmol)的硫化钠混合均匀,记为溶液b;将溶液b滴加到溶液a中,搅拌均匀后160℃下进行水热反应12h,反应结束后冷却至室温,抽滤,收集沉淀物,洗涤,于60℃真空干燥12h,得到所述feni2s4-rgo电极材料。(3)经过检测,材料在0.5a/g的电流密度下,具有1022.5f/g的比电容。可能是由于产物中存在fe2o3的杂质所导致。发明人进一步分析发现,可能由于硫化钠溶于水中呈强碱性,会使fe2+在反应过程中生产fe(oh)2,经过高温水热后变为fe2o3杂质,如图4所示,当硫化钠做硫源是产物的xrd表征中还出现了其他杂质峰,说明硫化钠不适于用做镍铁硫代尖晶石/石墨烯复合材料的硫源。实施例4:(1)将0.1058g氧化石墨置于40ml的蒸馏水:乙二醇(1:1)混合溶剂中超声分散均匀;(2)0.278g的硫酸亚铁和0.4975的醋酸镍溶于40ml的蒸馏水:乙二醇(1:1)混合溶剂中,加入0.607g的l-半胱氨酸混合均匀。(3)将混合盐溶液加入氧化石墨烯分散液中,搅拌30min,形成金属盐-氧化石墨烯混合液。拌均匀后160℃下进行水热反应16h,反应结束后冷却至室温,抽滤,收集沉淀物,洗涤,于60℃真空干燥12h,得到产物材料。经测试材料在0.5a/g的电流密度下,具有1164.4f/g的比电容。与实施例1相比材料的比电容有明显下降,可能因为随着反应时间增长,产物中会生成其他杂质,从而影响材料的电化学性能。说明水热时间会有影响feni2s4-rgo的生成,因此水热的时间不宜过长。经过对比发现最佳反应时间为12h,温度为160℃。实施例5:(1)将质量为(0.067g~0.150g)的氧化石墨置于40ml的蒸馏水:乙二醇(体积比为1:1)混合溶剂中超声分散均匀(超声时间为30min,超声功率为250w,超声频率为40khz);(2)将0.278g的硫酸亚铁和0.497g的醋酸镍溶于40ml的蒸馏水:乙二醇(体积比为1:1)混合溶剂中,加入0.607g的l-半胱氨酸混合均匀。(3)将混合盐溶液加入氧化石墨烯分散液中,搅拌30min,形成金属盐-氧化石墨烯混合液。拌均匀后160℃下进行水热反应16h,反应结束后冷却至室温,抽滤,收集沉淀物,洗涤,于60℃真空干燥12h,得到所述材料,标记为feni2s4-rgox(x分别是5wt%、10wt%、15wt%、20wt%)。(4)经测试材料在0.5a/g的电流密度下,石墨烯质量分数为15%时材料的电化学性能最佳,具有1822.7f/g的比电容。feni2s4-rgox(x是氧化石墨烯质量分数)在0.5a/g的电流密度下的比电容测试结果如表1所示。表1从表1可以看出,引入石墨烯会提升材料的性能,但随着石墨烯质量分数的增加,可能由于石墨烯片层可能会堆叠或团聚,使活性位点无法暴露,造成材料性能下降。因此,本发明优选石墨烯质量分数为15%时,材料的电化学性能最佳,可能只有石墨烯添加量在此范围内,铁盐溶液和镍盐才能与石墨烯存在更佳的协同作用,制备的材料性能更佳。实施例6:(1)将6.115g的固含量为2.6%的氧化石墨置于40ml的蒸馏水:乙二醇(1:1)混合溶剂中超声分散均匀,记为溶液a;(2)取0.278g(1mmol)的硫酸亚铁和0.498g(2mmol)的醋酸镍溶于40ml的蒸馏水:乙二醇(体积比1:1)混合溶剂中,分别加入4mmol、6mmol、8mmol和12mmol不同摩尔量的l-半胱氨酸混合均匀,记为溶液b;将溶液b滴加到溶液a中,搅拌均匀后160℃下进行水热反应12h,反应结束后冷却至室温,抽滤,收集沉淀物,洗涤,于60℃真空干燥12h,得到不同硫源量的feni2s4-rgo电极材料。(3)经过检测,当硫源量3mmol、4mmol、8mmol和12mmol时,材料在0.5a/g的电流密度下,测定其比电容,见表2。表2从表2可以看出,硫源的添加量对比电容有较大影响,当硫源与铁源和镍源的比例为4:3时,制得的材料性能最佳,当超出此范围时,可能是由于硫过多导致影响了材料性能,电化学性能下降。实施例7:(1)将6.115g的固含量为2.6%的氧化石墨置于40ml的蒸馏水:乙二醇(1:1)混合溶剂中超声分散均匀,记为溶液a;(2)取0.278g(1mmol)的硫酸亚铁和0.498g(2mmol)的醋酸镍溶于40ml的蒸馏水:乙二醇(体积比1:1)混合溶剂中,加入2.410g(4mmol)的硫脲混合均匀,记为溶液b;将溶液b滴加到溶液a中,搅拌均匀后160℃下进行水热反应12h,反应结束后冷却至室温,抽滤,收集沉淀物,洗涤,于60℃真空干燥12h,得到所述feni2s4-rgo电极材料。(3)经过检测,材料在0.5a/g的电流密度下,具有620.5f/g的比电容。对比与实施例1中l-半胱氨酸做硫源制备出的材料,性能不佳。说明硫源的选择对材料的性能有存在影响。这可能是由于各个硫源的性质不同与金属盐结合能力不同导致的。通过对比发现,本发明优选的最佳硫源为l-半胱氨酸。实施例8:(1)将6.115g的固含量为2.6%的氧化石墨置于40ml的蒸馏水中,超声分散均匀,记为溶液a;(2)取0.278g(1mmol)的硫酸亚铁和0.498g(2mmol)的醋酸镍溶于40ml的蒸馏水中,加入2.410g(4mmol)的硫脲混合均匀,记为溶液b;将溶液b滴加到溶液a中,室温下通过共沉淀法搅拌均匀,抽滤,收集沉淀物,洗涤,于60℃真空干燥12h。经过检测,通过共沉淀方法制备的材料在0.5a/g的电流密度下,具有250f/g的比电容。与水热法相比电容性能不佳。这是因为材料经过煅烧后生成了其他杂质,无法合成纯的铁镍硫代尖晶石材料。如图4所示,共沉淀工艺制备材料有fe3s4等杂质生成。因此水热法为该材料最佳制备方法。实施例9:(1)将6.115g的固含量为2.6%的氧化石墨置于40ml的蒸馏水中,超声分散均匀,记为溶液a;(2)取0.278g(1mmol)的硫酸亚铁和0.498g(2mmol)的醋酸镍溶于40ml的蒸馏水中,加入2.410g(4mmol)的硫脲混合均匀,记为溶液b;将溶液b滴加到溶液a中,室温下搅拌均匀,抽滤,收集沉淀物,洗涤,于60℃真空干燥12h,得到前驱体。(3)将前驱体放于坩埚中,移至管式煅烧炉中在氮气气氛下于煅烧,其中升温速率为2.5℃/min,煅烧温度是500℃,煅烧时间是3h。经过检测,通过煅烧方法制备的材料在0.5a/g的电流密度下,具有550f/g的比电容。与水热法相比电容性能不佳。这是因为材料经过煅烧后生成了其他杂质,无法合成纯的铁镍硫代尖晶石材料。如图4所示,共沉淀工艺制备材料有fe3s4等杂质生成。因此水热法为该材料最佳制备方法。实施例1、实施例8~实施例10,测定其比电容,见表3。表3实施例1实施例7实施例8实施例9比电容(f/g)1822.7620.5250550从表3可以看出,说明硫源的选择对材料的性能有存在影响,这可能是由于各个硫源的性质不同与金属盐结合能力不同导致的,共沉淀法、煅烧方法与水热法相比电容性能不佳,可能由于材料经过煅烧后生成了其他杂质,无法合成纯的铁镍硫代尖晶石材料。本发明优选l-半胱氨酸作为硫源,直接用水热去还原氧化石墨烯,不需要加入额外的还原剂,结合水热反应温度60~180℃,处理时间6~18h,并优选硫源的添加量以及铁盐溶液和所述镍盐溶液的中溶质的摩尔比为4:3,各工艺条件共同作用,制得的硫代尖晶石/石墨烯电极材料不仅电化学性能得到提升,且实现简易制备流程,工艺容易调节,生产效率高。同时,本发明以铁与镍作为金属源,原料来源更广,价格便宜,其次二者的变价较多,导电性良好,更适合用于电极材料制备,因此我们制备的铁镍硫代尖晶石/石墨烯电极材料与一般的镍铜或者镍钴硫代尖晶石/石墨烯电化学性能更佳。本制备方法通过一次步溶剂热法就可以制备feni2s4-rgo,简化了制备流程,制备工艺容易调节,提高了生产效率;通过适度引入石墨烯来增加材料的表面积,抑制材料团聚,从而保证电极材料优良的电化学性能。应说明的是,以上实施例仅用以说明本发明的技术方案而非限制,尽管参照较佳实施例对本发明进行了详细说明,本领域的普通技术人员应当理解,可以对本发明的技术方案进行修改或者等同替换,而不脱离本发明技术方案的精神和范围,其均应涵盖在本发明的权利要求范围当中。当前第1页12