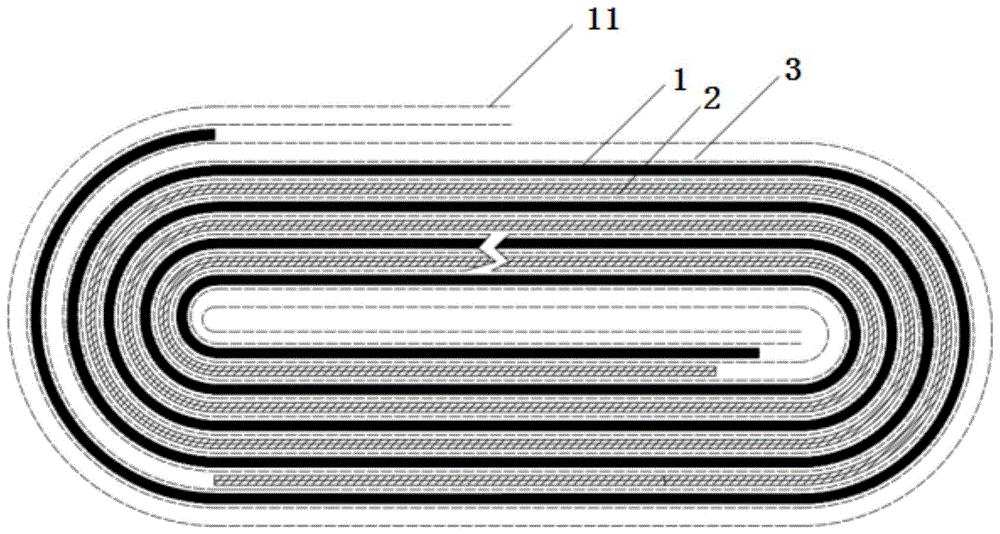
本发明涉及三元电池安全
技术领域:
,具体涉及一种高安全三元锂离子电池及其制备方法。
背景技术:
:高镍三元材料在合成过程中部分ni2+占据li+位,形成阳离子混排。另外在充电过程中,过渡金属层中的低价镍会迁移到锂层,占据锂空位,也会形成阳离子混排,随着三元电池镍含量提高,三元材料中的镍含量越高,热稳定性越差。2018年以来ncm811高镍电池推出,锂电池安全备受市场关注,特别是今年装载电车的自然事件,使得811电池的安全性问题推向了风口浪尖。各家锂电公司减慢了高镍的推出步伐,同时推出了新的替换方案,因此如何提高三元电芯体系安全性能是本行业研发领域重要研究方向,研究思路一方面从正极材料本身稳定性角度研究,另一方面从电芯设计角度。专利cn107579209a公开了一种高安全性三元聚合物锂离子电池,该技术是从改善电解液安全性能角度进行研究。专利cn102916164a,cn102315422a等提出的补锂方案,使用的是锂金属,由于锂金属非常活泼,所以该方案使用上受环境影响,操作过程复杂,且上述方案对锂离子电池的安全性没有改善。技术实现要素:本发明所要解决的技术问题在于解决现有技术对锂离子电池热失控的控制较弱的问题。本发明通过以下技术手段实现解决上述技术问题的:一种高安全三元锂离子电池,所述锂离子电池包括阴极、阳极、隔膜和电解液,用隔膜将阴极和阳极隔开,采用阴极包阳极的方式并绕卷形成电芯,将电芯封装进电池外壳中注入电解液并密封得到电池,所述阴极包括集流体、导热涂层、三元浆料涂层和多孔无机耐高温浆料涂层;所述集流体表面涂覆有导热涂层;位于所述集流体其中一面的导热涂层外部连续涂覆有三元浆料涂层,且位于所述集流体另一面的导热涂层外部间歇涂覆有三元浆料涂层;两面所述三元浆料涂层外部相应地涂覆有多孔无机耐高温浆料涂层,且所述多孔无机耐高温浆料涂层不与所述导热涂层接触;所述导热涂层的原料包括石墨烯、导电炭黑、纳米碳纤维、碳纳米管中的至少一种;所述电芯外侧设置有绝缘片,所述绝缘片为高硬度硅胶片绝缘保护袋。本发明通过对阴极的结构及电芯的设计上进行改进,采用阴极包阳极的方式并绕卷形成电芯,在阴极集流体与三元浆料涂层中间涂覆导热涂层,导热涂层的原料为不同结构碳材料,具有良好的传输电子及声子导热功能,当发生滥用时,阴极可以快速传输热量,同时,在三元浆料涂层表面涂敷多孔无机耐高温浆料涂层,一方面可以杜绝三元颗粒、粉尘、金属异物等尖端效应刺穿隔膜,另外一方面规避隔膜穿孔后铝箔与阳极石墨层的搭接;通过在电芯外侧设置有高硬度硅胶片绝缘保护袋,保障了电芯最大程度的散热。优选地,所述导热涂层涂覆的厚度为0.5-5um。优选地,所述三元浆料涂层的活性物质为li(ni(1-x-y)coymnx)o2,其中0≤x≤0.5,0≤y≤0.5。优选地,所述三元浆料涂层涂覆的密度为250-400g/m2。优选地,所述无机耐高温浆料涂层的原料包括二氧化硅、氧化铝、勃姆石中的一种。优选地,所述无机耐高温浆料涂层涂覆的厚度为1-4um。优选地,所述无机耐高温浆料涂层涂覆的宽度大于所述三元浆料涂层边缘1-6mm。优选地,所述电池为铝壳电池。本发明还提供上述的一种高安全三元锂离子电池的制备方法,包括以下步骤:(1)阴极的预处理:先在集流体表面涂覆导热涂层,然后在导热涂层的其中一面涂覆一层三元浆料涂层,并在导热涂层的另一面采用间隔涂覆的方式涂覆一层三元浆料涂层,烘干后,然后在两个三元材料涂层表面,对应地分别涂覆无机耐高温浆料涂层即可;(2)用隔膜将步骤(1)中预处理后的阴极和阳极隔开,按照阴极包阳极的方式并绕卷形成电芯,将电芯封装进电池外壳中注入电解液并密封得到电池。进一步地,所述步骤(1)中烘干的温度为80-105℃。本发明具有如下的有益效果:本发明通过对阴极的结构及电芯的设计上进行改进,采用阴极包阳极的方式并绕卷形成电芯,在阴极集流体与三元浆料涂层中间涂覆导热涂层,导热涂层的原料为不同结构碳材料,具有良好的传输电子及声子导热功能,当发生滥用时,阴极可以快速传输热量,同时,在三元浆料涂层表面涂敷多孔无机耐高温浆料涂层,一方面可以杜绝三元颗粒、粉尘、金属异物等尖端效应刺穿隔膜,另外一方面规避隔膜穿孔后铝箔与阳极石墨层的搭接;通过在电芯外侧设置有高硬度硅胶片绝缘保护袋,保障了电芯最大程度的散热。附图说明图1为本发明实施例1的电芯的结构示意图;图2为本发明实施例1的阴极的主视结构示意图;图3为本发明实施例1的阴极的侧视结构示意图。附图标号说明:1、阴极;2、阳极;3、隔膜;11、集流体;12、导热涂层;13、三元浆料涂层;14、多孔无机耐高温浆料涂层。具体实施方式为使本发明实施例的目的、技术方案和优点更加清楚,下面将结合本发明附图说明和实施例,对本发明实施例中的技术方案进行清楚、完整地描述,显然,所描述的实施例是本发明一部分实施例,而不是全部的实施例。基于本发明中的实施例,本领域普通技术人员在没有作出创造性劳动前提下所获得的所有其他实施例,都属于本发明保护的范围。下述实施例中所用的试验材料和试剂等,如无特殊说明,均可从商业途径获得。实施例中未注明具体技术或条件者,均可以按照本领域内的文献所描述的技术或条件或者按照产品说明书进行。实施例1如图1、图2所示,本实施例公开一种高安全三元锂离子电池,锂离子电池包括阴极1、阳极2、隔膜3和电解液,阴极1包括集流体11、导热涂层12、三元浆料涂层13和多孔无机耐高温浆料涂层14。如图2、图3所示,并具体以图2的方位为参照,集流体11表面涂覆有导热涂层12,在位于集流体11上面的导热涂层12的上面连续涂覆有三元浆料涂层13,且在该三元浆料涂层13的上面继续涂覆一层多孔无机耐高温浆料涂层14;在位于集流体11下面的导热涂层12的下面,采用间歇涂覆的方式涂覆一层三元浆料涂层13,对应地,在该三元浆料涂层13的下面采用间歇涂覆的方式涂覆一层多孔无机耐高温浆料涂层14。如图1所示,隔膜将阴极1和阳极2隔开,采用阴极1包阳极2的方式并绕卷形成电芯,将电芯封装进电池外壳中注入电解液并密封得到电池。一种高安全三元锂离子电池的制备,包括以下步骤:阴极1的预处理:先在集流体11的表面涂有厚度为2um的导电炭黑,在位于上面的和位于下面的两面导电炭黑上分别涂覆上密度为300g/m2的lini0.6co0.2mn0.2o2三元浆料,于100℃下烘干,然后在位于两面的三元浆料涂层13表面分别涂覆上厚度为2um的al2o3浆料;用隔膜3将预处理后的阴极1和阳极2隔开,按照阴极1包阳极2的方式并绕卷形成电芯,并在电芯外侧使用高硬度硅胶片绝缘保护袋,最后再将电芯封装进电池外壳中注入电解液并密封得到电池。对比例1-1本对比例与实施例1的区别在于:按照实施例1的涂覆方式,直接在集流体11的表面涂覆lini0.6co0.2mn0.2o2三元浆料和多孔无机耐高温浆料涂层14,三元浆料涂层13和集流体11之间不进行导热涂层12的涂覆。其他工艺与实施例1相同。对比例1-2本对比例与实施例1的区别在于:按照实施例1的涂覆方式,先在集流体11的表面涂有厚度为2um的导电炭黑,然后在位于上面的导电炭黑上面再涂覆上lini0.6co0.2mn0.2o2三元浆料,并在位于下面的导电炭黑下面涂覆上lini0.6co0.2mn0.2o2三元浆料,烘干即可。其他工艺与实施例1相同。对比例1-3本对比例与实施例1的区别在于:按照实施例1的涂覆方式,只在集流体11表面涂敷lini0.6co0.2mn0.2o2三元浆料。其他工艺与实施例1相同。对比例1-4本对比例与实施例1的区别在于:按照实施例1的涂覆方式,只在集流体11表面涂敷lini0.6co0.2mn0.2o2三元浆料,得到处理好的阴极1;且用隔膜3将预处理后的阴极1和阳极2隔开,按照阴极1包阳极2的方式并绕卷形成电芯,并在电芯外侧使用pet保护膜,最后再将电芯封装进电池外壳中注入电解液并密封得到电池。实施例2一种高安全三元锂离子电池的制备,包括以下步骤:阴极1的预处理:先在集流体11的表面涂有厚度为2um的导电炭黑,在位于上面的和位于下面的两面导电炭黑上分别涂覆上密度为300g/m2的lini0.6co0.2mn0.2o2三元浆料,于100℃下烘干,然后在位于两面的三元浆料涂层13表面分别涂覆上厚度为4um的al2o3浆料;用隔膜3将预处理后的阴极1和阳极2隔开,按照阴极1包阳极2的方式并绕卷形成电芯,并在电芯外侧使用高硬度硅胶片绝缘保护袋,最后再将电芯封装进电池外壳中注入电解液并密封得到电池。对比例2本对比例与实施例2的区别在于:按照实施例2的涂覆方式,只在集流体11表面涂敷lini0.83co0.07mn0.1o2三元浆料。其他工艺与实施例2相同。实施例3一种高安全三元锂离子电池的制备,包括以下步骤:阴极1的预处理:先在集流体11的表面涂有厚度为2um的导电炭黑,在位于上面的和位于下面的两面导电炭黑上分别涂覆上密度为300g/m2的lini0.6co0.2mn0.2o2三元浆料,于100℃下烘干,然后在位于两面的三元浆料涂层13表面分别涂覆上厚度为3um的al2o3浆料;用隔膜3将预处理后的阴极1和阳极2隔开,按照阴极1包阳极2的方式并绕卷形成电芯,并在电芯外侧使用高硬度硅胶片绝缘保护袋,最后再将电芯封装进电池外壳中注入电解液并密封得到电池。对比例3本对比例与实施例3的区别在于:按照实施例3的涂覆方式,只在集流体11表面涂敷lini0.6co0.2mn0.2o2三元浆料。其他工艺与实施例3相同。性能检测试验将上述实施例1和对比例1-4中的电芯制作成铝壳27148101a50ah电芯,电芯制作完成后用0.5c电流充电至满电,后放置于防爆箱体内,保持环境恒温,电池外接300w加热片,持续给电池加热至热失控,记录不同电芯热失控时间,结果如表1所示。表1为实施例1-3和对比例1-4检测结果组别热失控时间/s实施例13880对比例1-12062对比例1-22451对比例1-32334对比例1-41891实施例22321对比例21945实施例32894对比例32251由表1可以看出,实施例1与对比例1-1~1-4的热失控对比时间显示,对比例1-4采用传统电芯结构,电芯发生热失控时间最短1891s,即电芯内部散热效果最差,实施1与对比例1-3分别采用本发明的不同结构,结果显示,不同安全措施,对电芯散热均有一定帮助作用,实施例1效果最佳,能最大限度将电芯热滥用产生热量分散至电芯外部,热失控时间在3880s,而仅仅使用集流体涂层结构和表面涂绝缘层结构,电芯热失控时间分别在2451s和2062s,对电芯散热均仅起到一定辅助作用,且集流体涂导热层结构优于材料涂绝缘层。以上实施例仅用以说明本发明的技术方案,而非对其限制;尽管参照前述实施例对本发明进行了详细的说明,本领域的普通技术人员应当理解:其依然可以对前述各实施例所记载的技术方案进行修改,或者对其中部分技术特征进行等同替换;而这些修改或者替换,并不使相应技术方案的本质脱离本发明各实施例技术方案的精神和范围。当前第1页12